Ganhando tração com Markforged:Moldagem e fundição de rodas impressas em 3D
Nota do Editor:esta postagem de convidado foi escrita por Charles Guan, um graduado em Engenharia Mecânica do MIT e ex-instrutor de oficina e design do MIT. Ele também é o construtor do robô Overhaul no BattleBots da ABC. Ele trabalha como consultor de engenharia em robótica e transporte e é patrocinado pela Markforged para competir em BattleBots e outras competições de robótica. Confira o site dele e Equals Zero Robotics para mais informações!
Design da roda
Rodas Com mais de 6.000 anos de história por trás deles, você imaginaria que já os teríamos tornado perfeitos. Como descobri da maneira mais difícil durante a 2ª temporada de BattleBots, isso está longe de ser verdade em muitos aspectos. Você pode realmente reinventar a roda e errar. Eu projetei o Overhaul 2.0 com uma plataforma quadrada poderosa e estável de 6 rodas com a intenção de usar a velocidade a meu favor para capturar oponentes em seu levantador de luta. Escolhi as rodas com base no que eu sabia:rodas de rodízio industrial de dureza média com degraus de elastômero termoplástico (TPE) que tinham sido usados em combate de robôs desde o início. Colocar motores de 16 cavalos de potência nessas rodas em um robô projetado para atingir 19 mph em 1 segundo era um território desconhecido.
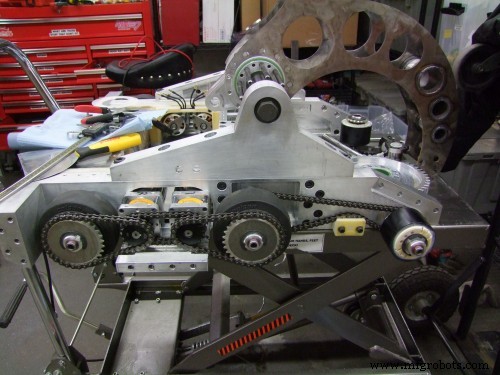
Isso não funcionou a meu favor na arena de forma alguma. As rodas do TPE começaram a se desfazer, literalmente derretendo com a energia que passava por elas. Seu piso escorregadio deslizou sobre os destroços e partículas soltas na caixa como se o robô estivesse dirigindo no gelo. Como resultado, meus motores de acionamento sem escovas de 16 cavalos de potência foram praticamente um desperdício total. Se você assistir a minha partida contra o Beta na temporada passada, verá que confundi BattleBots com o Grande Prêmio D1 em boa parte da partida.
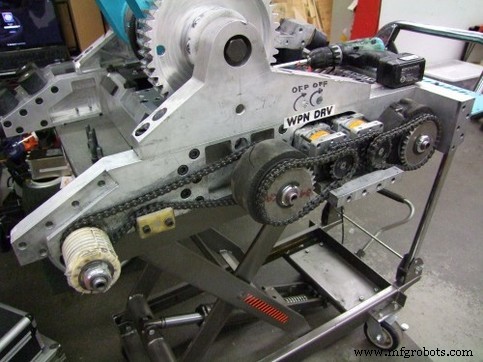
Após o torneio BattleBots Season 2, fiquei pensando nas próximas etapas. As rodas precisariam ser alteradas para colocar a potência do robô no solo. Foi aqui que comecei a pesquisar compostos de borracha moldáveis. Não me importei em fazer alguns moldes, despejar o material e, em seguida, trabalhar em outra coisa no tempo que leva para curar. Durante a 2ª temporada de BattleBots, observei alguns concorrentes - incluindo Beta - colocar suas próprias rodas de uretano no local.
Eu não sabia nada sobre desenho de pneus e rodas, nem sobre moldagem e fundição. Fale sobre um tiro no escuro! Felizmente, eu encurralei alguns representantes da empresa Smooth-On na Detroit Maker Faire durante o verão e conversei longamente com eles sobre quais produtos eram adequados para a fabricação de rodas de tração. Smooth-On é uma empresa voltada principalmente para a fabricação de moldes e fundição para efeitos especiais, fantasias e adereços - não para usos industriais. No entanto, seus distribuidores estão em todo o país, então seus materiais estão facilmente disponíveis para experimentação - a apenas 15 minutos de carro de Boston. A missão:aprender o fluxo de trabalho da fundição de resina, produzindo rodas personalizadas para um modelo em escala de 30 lb de Revisão que eu estava projetando na época para uma competição do outono de 2016.
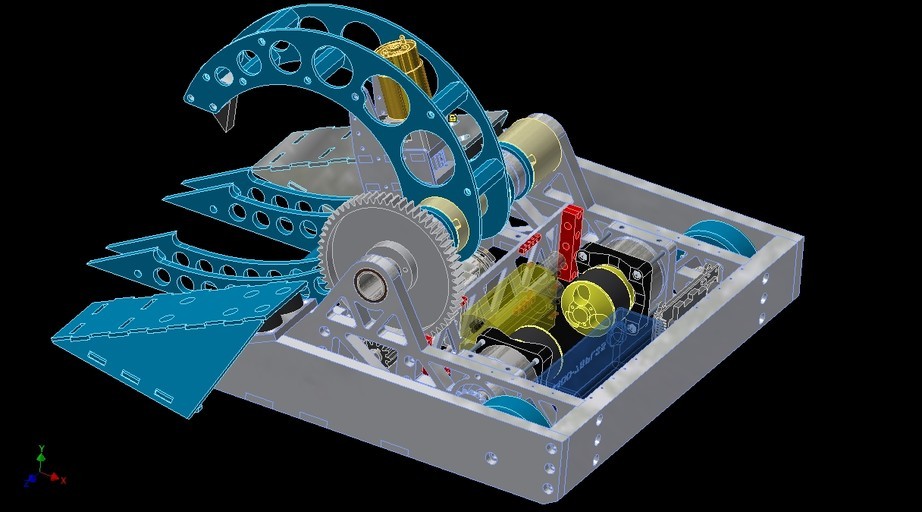
Projetando o molde
Os representantes me indicaram dois materiais com resistência ao rasgo e resistência à tração favoravelmente altas, as séries Reoflex e Simpact. Essas duas características são desejáveis em um composto de roda, onde a borracha é constantemente cortada através da espessura da banda de rodagem e arrastada ao longo do solo. Peguei uma amostra de ReoFlex 50 (para durômetro 50A, que é razoavelmente macio como a sola de um sapato) e comecei a projetar o molde e o cubo.
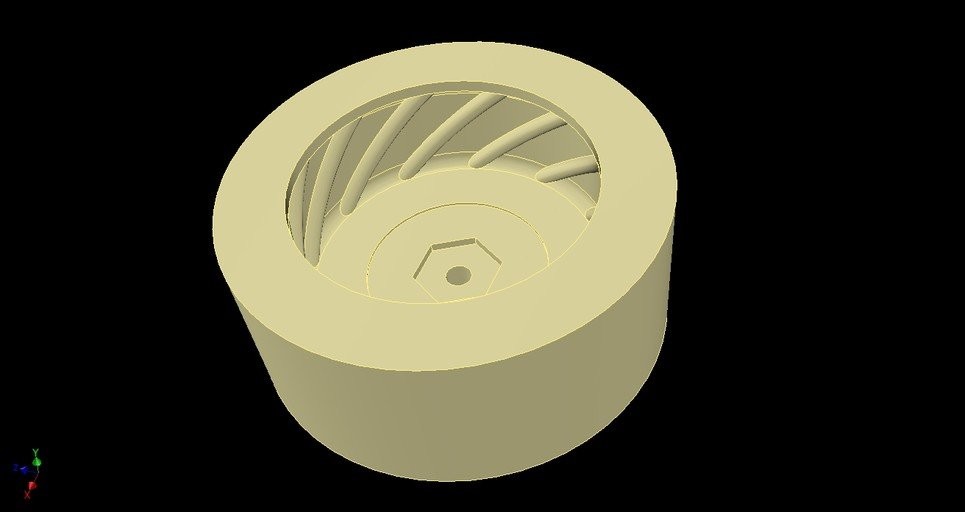
Após o desempenho da revisão na caixa, eu estava bastante convencido de que algum tipo de recurso de limpeza de detritos era necessário na superfície da roda. Embora não estejamos tentando canalizar água ou arranhar a lama como acontece com pneus de carro, ainda havia detritos soltos e flocos de tinta da própria arena para enfrentar. Para começar, fiz um padrão de piso em espiral simples. De forma alguma isso foi otimizado - eu só queria chegar rapidamente ao estágio de moldagem por enquanto. Achei que as ranhuras helicoidais tenderiam a empurrar os detritos para o lado, longe da área de contato. A orientação exata e o número de ranhuras obviamente ainda são uma ciência incerta, se você já foi comprar pneus.
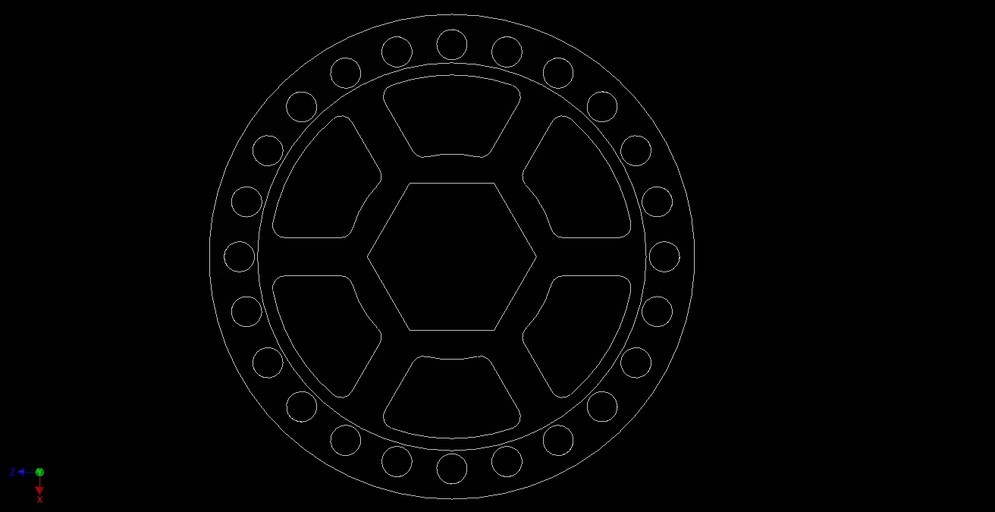
Em seguida, fui confrontado com a tarefa de projetar o cubo da roda. Dei uma olhada em minha caixa de scooter e rodas de skate para me inspirar. Todos eles tinham uma característica comum:orifícios ou fendas pelas quais o uretano fluía ao redor e para dentro. Eu estava muito interessado em garantir que o material do piso pudesse permanecer no cubo, mesmo com falha de aderência. Eu modelei um cubo cilíndrico bastante básico, mas com muitos recursos de orifício em uma nervura central cônica para dar área e seção transversal máximas para o uretano aderir. Escolhi Onyx em vez de Nylon regular para o cubo devido à sua maior rigidez e resistência, fatorado com propriedades de adesão. O aumento da rigidez me permitiria tornar o cubo da roda mais leve, enquanto a resina aderia melhor à textura microscopicamente áspera do Onyx sobre o náilon brilhante.
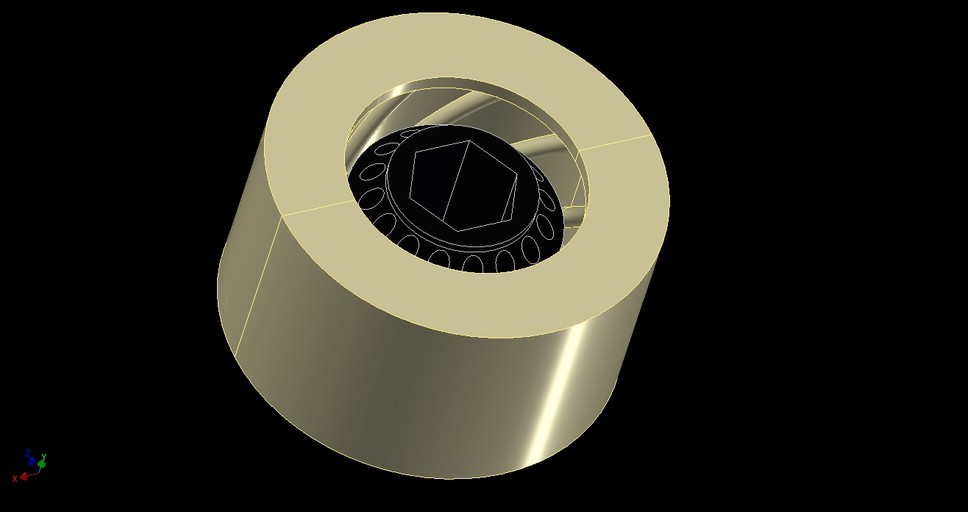
Como a revisão minúscula também precisaria de algumas rodas dianteiras menores, usei os recursos paramétricos do Autodesk Inventor para gerar rapidamente um modelo de 2 polegadas. Este molde tinha uma área bastante restrita para vazar, então eu estava interessado em como o material se comportaria.
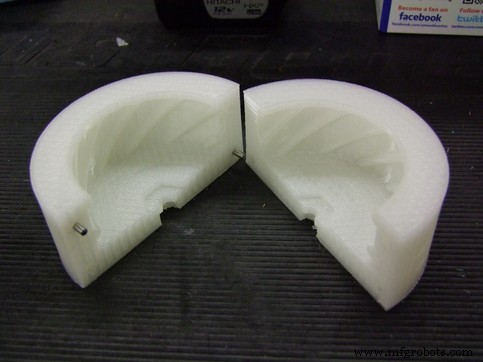
Eu imprimi um molde de teste usando Náilon simples não reforçado no Mark Two. O molde era muito esparso - 4 paredes e 4 camadas de telhado e piso, mas apenas 25% de preenchimento, impresso na configuração da camada mais grossa de 0,2 mm. Eu modelei os orifícios dos pinos de registro nas metades para garantir o alinhamento.
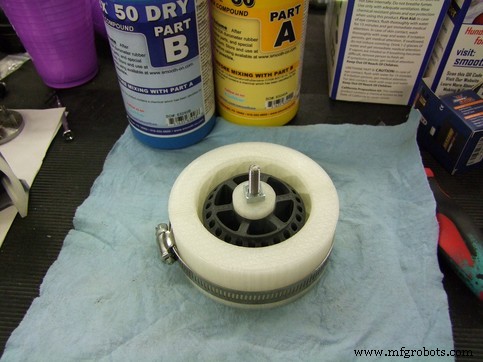
Derramando o Molde
As metades do molde são projetadas para serem mantidas juntas com uma única braçadeira de mangueira regular. No interior, o cubo da roda fica em uma bucha adaptadora para mantê-lo centralizado no molde, e esta bucha adaptadora tem um orifício na parte inferior das metades do molde para que eu pudesse passar uma porca de retenção e parafuso verticalmente para vedar a face inferior do o cubo da roda contra o molde. Antes de montar isso, eu revesti as metades do molde com desmoldante por spray.

Seguindo o conselho de amigos que tinham mais experiência em moldagem e fundição, peguei emprestado um pote a vácuo para retirar todas as bolhas de ar da resina misturada. Smooth-on anuncia suas resinas como “minimizando o ar aprisionado”, mas observar a mistura ferver me mostrou que isso era menos do que eficaz. O aprisionamento de bolhas de ar reduziria a integridade da banda de rodagem, pois apresentaria muitas interrupções no material. Eu desgaseifiquei o copo de material misturado em vez de colocar todo o molde com resina líquida na câmara, uma vez que todo o ar dentro das metades do molde sendo impresso oco provavelmente iria deformá-las ou mesmo vazar e borbulhar lentamente.
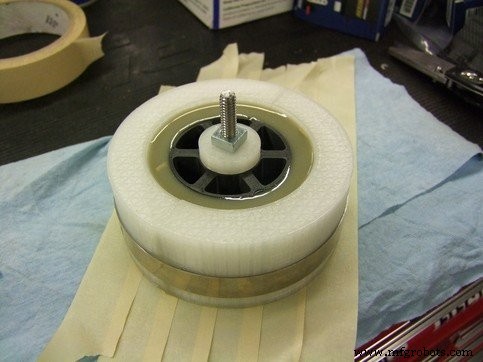
Demorou cerca de 2 minutos para despejar o molde de roda de 3 polegadas - inclinei o copo de mistura apenas o suficiente para manter o fluxo contínuo do líquido, deixando a resina assentar no fundo e não empilhar ou formar crista no molde. Deixar a resina “encontrar sua linha de água” é como evitar o aprisionamento de grandes bolhas de ar na peça.
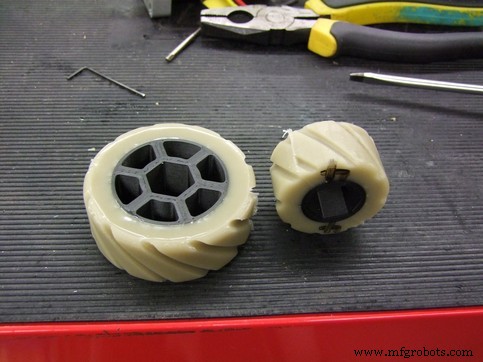
Eu derramei uma roda de 3 "e uma roda de 2" como lote inicial. Depois que pelo menos as duas primeiras rodas ficaram sólidas, era hora de iniciar a produção. Eu imprimi moldes adicionais para que pudesse derramar 4 ou mais rodas de uma vez - um dos meus copos de mistura era perfeito para duas rodas de 3 ″ e duas rodas de 2 ″, então isso se tornou o padrão.
O processo de cura
A maioria dos fabricantes de resina recomenda uma cura lenta inicial à temperatura ambiente, e depois aquecendo o material para fortalecer mais as reticulações do polímero. Por exemplo, a folha de dados do Reoflex 50 diz para aquecer o material a 65 Celsius por 4 a 8 horas. Usei uma câmara aquecida a aproximadamente 70 graus Celsius:as novas rodas que emergiram dessa cura acelerada pelo calor eram definitivamente mais resistentes e resistentes ao toque.
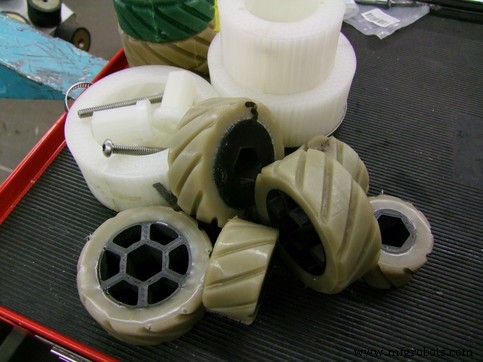
O resultado após uma semana de experimentação foi cerca de meia dúzia de cada tamanho de roda. Eu examinei meu suprimento de ReoFlex 50, então determinei que este era um bom lugar para parar e ter certeza de que as rodas realmente funcionavam na competição antes de gastar mais dinheiro com o material. Entrei em um bom ciclo nos últimos dias antes - despejava os moldes como a última coisa que fiz à noite antes de sair, desmoldava-os pela manhã e, em seguida, as assava ao longo do dia.
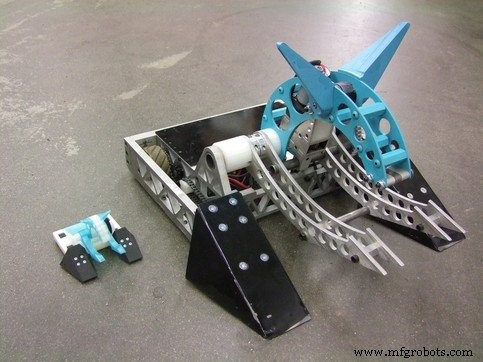
E é assim que eles se parecem instalados no bot. Se você estiver interessado no desenvolvimento de “30-Haul” como o apelidamos, você pode verificar seu tópico de construção em meu site.
Então o que vem depois? Agora que tenho o processo de produção explorado e um design básico na minha frente, é hora de a ciência real começar. Fique ligado na Parte II desta série, onde tento fazer rodas de diferentes compostos e testar sua tração em um piso de aço pintado. Por enquanto, aqui está a aparência dessas rodas depois de algumas lutas difíceis!
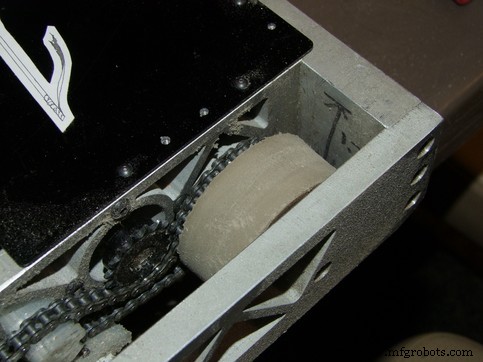
Saiba mais sobre as impressoras Markforged e como elas podem se adequar às suas aplicações!
impressao 3D
- Entrevista com um especialista:Spencer Wright de pencerw.com e nTopology
- Concluindo as peças impressas em 3D com… giz de cera?
- Entrevista com um especialista:Ibraheem Khadar de Markforged
- Stratasys faz parceria com GrabCAD e e-Xstream
- Stratasys revive MakerBot com o método
- Fundição em areia com tecnologia FDM
- Melhor controle de qualidade com peças impressas em 3D
- Amarre-se com peças impressas em 3D funcionais!
- Re-imaginando o Go Kart com peças impressas em 3D
- Prototipagem e produção de curta duração com fundição sob pressão