Máquinas internas:PC vs. PLC - Comparando opções de controle
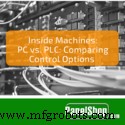
T A década de 1970 viu a introdução de PLCs ou controladores lógicos programáveis , o que mudaria para sempre a forma como a automação é alcançada em ambientes industriais. Conhecido por sua robustez de design e implementação escalável, o PLC foi adaptado por todos os principais fabricantes e até hoje é a norma para automação industrial. Allen-Bradley, Omron, Siemens, AEG, etc. tornaram-se líderes em PLC fabricação, e logo os controladores tinham a capacidade de processamento de um computador, resistindo a condições industriais adversas.
Não foi até a década de 1990, quando o interesse renovado em computadores pessoais começou a ganhar terreno. O principal motivo foi o aumento na velocidade do processador, a redução no tamanho e uma tendência de queda no custo. As indústrias também começaram a incorporar PCs em suas fábricas devido ao nível de controle de supervisão que ofereciam sobre outras máquinas, incluindo PLCs.
No entanto, hoje tanto os PLCs quanto os PCs desenvolveram recursos semelhantes, o que tornou bastante difícil para os engenheiros de controle decidirem qual produto usar. Vamos dar uma olhada nas principais funcionalidades desses dois produtos.
CLPs foram projetados como uma alternativa mais simplificada, reduzida, altamente flexível e robusta para painéis de relés e caixas de comutação. Geralmente eram atribuídas tarefas específicas, que eram pré-programadas e depois executadas. No entanto, a customização foi outro fator que os CPs tiveram que fornecer, portanto, uma linguagem e estrutura únicas foram selecionadas para todas as atividades de programação. Conhecida como "lógica de escada" , isso permitiu uma rápida customização no código de acordo com a situação. Além de tudo isso, os PLCs também tiveram que suportar o peso das radiações eletromagnéticas, vibrações e contaminação. Com o passar do tempo, os PLCs também tiveram que acompanhar o desenvolvimento de tecnologias. Em breve, conexões Ethernet, controles de processo PID e segurança integrada passaram a fazer parte dos PLCs, somando-se à sua longa lista de recursos.
Os PCs acabaram desenvolvendo recursos que os alinharam com os PLCs em termos de funcionalidade. Além disso, eles mantiveram sua robustez e personalização devido à disponibilidade de slots e portas de cartão. O poder de processamento dos PCs era muitas vezes maior do que os PLCs, pois continham kernel em tempo real, permitindo que ele executasse tarefas críticas e implementasse algoritmos de controle.
O objetivo final é um controle robusto, eficiente e confiável sobre os ativos industriais , e, portanto, cada credencial de PLCs e PCs deve ser colocada frente a frente para obter uma melhor compreensão e conclusão lógica.
Operação
Os PLCs padrão são incorporados a um sistema de operação em tempo real que usa um processador dedicado para garantir um alto grau de confiabilidade durante as operações de controle. O SO de um PLC é projetado especificamente para realizar tarefas relacionadas ao controle e, portanto, não há necessidade de utilitários como programas antivírus ou limpadores de registro. Isso, com efeito, aumenta a taxa de processamento do sistema, garantindo que mais ciclos de processamento sejam utilizados no monitoramento de parâmetros cruciais.
Os PCs também são projetados com kernel em tempo real e um sistema operacional associado, colocando-o lado a lado com os PLCs em termos de recursos de processamento. A confiabilidade dos PCs foi problemática, pois as experiências anteriores com falhas do sistema eram bastante comuns. No entanto, essa limitação foi logo eliminada com sistemas operacionais mais simples, especialmente construídos para uso em indústrias.
Portanto, PLCs e PCs estão atualmente no mesmo nível em termos de operação.
Integração de hardware
Os requisitos industriais de hoje não são mais semelhantes aos de 20 anos atrás. Ambos os PLCs e PCs são necessários para controlar uma série de dispositivos para comunicação, monitoramento e controle e, portanto, devem ter recursos de expansão suficientes. Protocolos de comunicação industrial bem conhecidos incluem Profbus, CANbus, Modbus, EtherCAT, EtherNET/IP, etc.
Embora tanto o PLC quanto o PC ofereçam essas opções de fieldbus, o PLC possui todos esses recursos integrados por padrão. Por outro lado, um PC pode exigir uma placa de expansão para suportar um protocolo específico. Mas o maior número de slots de expansão nos PCs significa que uma maior personalização é possível e uma ampla variedade de interfaces pode ser utilizada para operação.
Isso coloca os PCs à frente dos PLCs quando se trata de lidar com tarefas como imagens avançadas de alta resolução ou outras com vários requisitos de processamento inesperados. Além disso, se as tarefas que exigem memória devem ser realizadas usando um PLC, um PLC industrial suplementar deve ser instalado para acompanhar os parâmetros dinâmicos e as conexões.
Segurança
A ciberespionagem sempre esteve em alta devido ao aumento da conectividade entre os dispositivos. A segurança industrial é fundamental para garantir tempo de atividade contínuo e produtividade máxima. Existem duas dimensões básicas de segurança com as quais um CLP/PC deve se preocupar:
- Bloqueando o acesso não autorizado de ataques externos
- Limitando o acesso do usuário de acordo com seus direitos/designação
Tradicionalmente, os PLCs são considerados imunes a ataques de malware e isso é verdade até certo ponto. Os PLCs têm SO dedicado e funcionalidade limitada, colocando-os em menor risco de ataques em comparação com os PCs. No entanto, episódios recentes como o do “Stuxnet”, um malware direcionado aos PLCs da Siemens, prejudicaram a reputação do PLC como imune a vírus. Ainda assim, os casos registrados de tais ataques são extremamente limitados. Em comparação, os PCs são extremamente vulneráveis a ataques de malware e exigem proteção e monitoramento antivírus de primeira linha.
Programação
O ambiente e a linguagem de programação são cruciais para obter a máxima eficiência, seja de um PLC ou PC. Uma das principais diferenças entre um PLC e um PC é a forma como os programas são desenvolvidos e executados. Um PLC geralmente segue a execução de um programa baseado em varredura, enquanto o software de PC geralmente é orientado a eventos. Os diferentes estilos de execução, por sua vez, se traduzem em diferentes filosofias de programação.
Os CLPs são programados usando linguagens especificadas no padrão IEC 61131-3 , ou seja, lógica ladder ou linguagem proprietária do fornecedor. Em comparação, os programas baseados em PC usam linguagens como C/C++/.NET. Nenhuma linguagem pode ser considerada melhor que a outra, pois depende apenas da experiência do programador. Mas devido à tendência crescente de soluções e cursos baseados em PC, é mais provável que um programador ache C/C++/.NET mais flexível em comparação com a lógica ladder.
Discussões de custo
Este pode ser o último tópico em discussão, mas é um dos mais importantes. Os problemas de automação e controle de hoje são multidimensionais e podem ser resolvidos de mais de uma maneira. Ambas as soluções baseadas em PC ou baseadas em PLC são elegíveis para algumas aplicações, no entanto, a principal restrição que se mostra prejudicial é o custo associado a essas soluções.
- Desempenho x Custo
O custo inicial de uma solução baseada em PC pode ser maior do que um PLC, mas sempre que cálculos exigentes e cargas de rede complexas precisam ser processadas, um programa baseado em PC é mais caro -eficaz. Em comparação, os CLPs podem ser inicialmente baratos, mas à medida que o poder de processamento aumenta, seu custo segue uma tendência exponencial.
- Expansibilidade x custo
Os PCs têm um custo mais alto do que os PLCs quando nenhum periférico externo precisa ser adicionado, pois os PLCs geralmente suportam equipamentos industriais padrão. No entanto, quando uma solução requer uma infinidade de controles externos, uma solução baseada em PC é muito mais adequada do que uma baseada em CLP.
- Robustez x Custo
Os CLPs não requerem excesso de equipamentos de proteção para aumentar sua robustez e blindagem. Em comparação, um PC pode exigir um investimento considerável para protegê-lo dos efeitos do ambiente hostil para que o tempo de atividade máximo possa ser garantido.
Interessado em saber mais? Entre em contato com um especialista ou visite nosso site:PanelShop.com .
Sistema de controle de automação
- Renesas expande opções de microcontrolador para controle de servo em robôs industriais
- A digitalização bem-sucedida começa com PLCs modernos
- Comparação de diferentes tipos de máquinas CNC
- O que você deve saber sobre controladores lógicos programáveis
- Dicas para solucionar problemas de PLCs problemáticos
- Este controle ABB pode ser reparado? O que há dentro de um controle?
- Bright Machines lança 'Microfactory-as-a-Service'
- Yaskawa e Phoenix Contact fazem parceria para desenvolver nova plataforma PLC
- PLC vs DCS
- Benefícios da convergência de controle industrial