O controle conectado
A Internet e a computação baseada em nuvem estão mudando a forma como os fabricantes operam as máquinas-ferramentas CNC. Sua loja está pronta para isso?
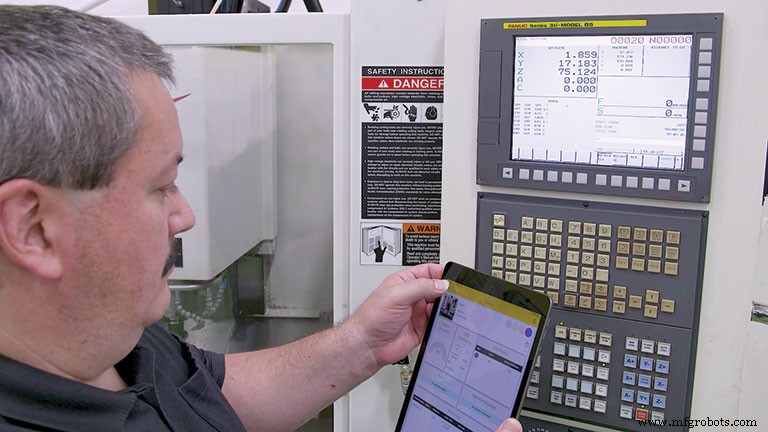
As portas Ethernet começaram a aparecer em tornos CNC e centros de usinagem há mais de 20 anos. O padrão de comunicação de máquinas-ferramenta MTConnect fez sua estreia oficial nos EUA no IMTS de 2010 em Chicago. Os fabricantes começaram a falar sobre computação em nuvem e Internet Industrial das Coisas (IIoT) pouco depois, termos que se tornariam populares quando o economista alemão Klaus Schwab publicou um artigo em 2015 afirmando que o mundo havia entrado em uma Quarta Revolução Industrial.
Bem-vindo a 2021. Já deve ser evidente para os proprietários de oficinas mecânicas, programadores CNC e engenheiros de fabricação que a indústria de usinagem mudou significativamente nas últimas duas décadas. As máquinas-ferramentas CNC são muito mais inteligentes do que antes, capazes de gerar quantidades significativas de dados sobre tudo o que está acontecendo por trás do vidro. O software de fabricação também ficou mais inteligente, oferecendo interoperabilidade e recursos baseados em nuvem com os quais só se sonhava na virada do século.
Se toda essa magia técnica é uma coisa boa ou não, está em debate. Alguns podem argumentar que a vida no chão de fábrica já é bastante desafiadora – quem precisa de Big Data e maquinário inteligente quando mal há horas no dia para colocar peças na porta? Outros veem a Indústria 4.0 e tudo o que ela implica como o caminho claro para os fabricantes, e quem não a adotar logo estará fora do negócio.
Ganhando FOCAS
A verdade está em algum lugar no meio. Paul Webster, diretor de engenharia da FANUC America Corp., com sede em Rochester Hills, Michigan, observou que as máquinas-ferramentas CNC estão prontas para rede e Internet desde antes do ano 2000. As lojas que optam por ignorar esse recurso ainda estão funcionando muito bem, obrigado, e continuarão a fazê-lo nos próximos anos. E, no entanto, poucos argumentariam que a conectividade da máquina-ferramenta e a maior visibilidade dos processos de usinagem assim habilitados nunca é uma coisa ruim e pode fazer a diferença entre um trabalho lucrativo e um que você logo esqueceria.
“Introduzimos nossa API FOCAS (interface de programação de aplicativos) no início dos anos 90, bem como portas de fibra ótica e Ethernet, portanto, conectar um CNC tem sido fácil há algum tempo”, disse ele. “A parte difícil sempre foi descobrir quais dados você precisa e o que você vai fazer com eles assim que os tiver.”
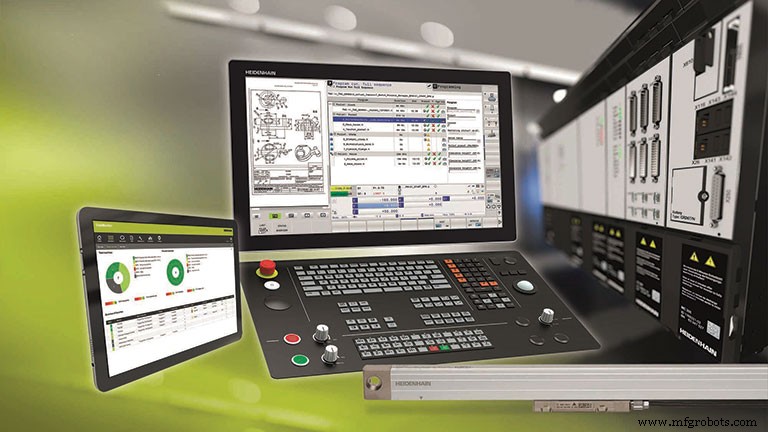
Esses dados incluem históricos de alarme, taxa de alimentação e configurações de substituição do fuso, servo motor e temperaturas do fuso, consumo de energia, variáveis macro e muito mais, todos os quais podem ser extraídos da máquina-ferramenta de forma contínua e automática. Adicione a isso várias entradas fornecidas pelo operador - número do trabalho, status da produção, consumo de ferramentas de corte e até informações sobre a qualidade da peça - e obter uma visão completa das atividades do chão de fábrica não se torna mais difícil do que olhar para o painel de qualquer software de monitoramento que coleta esses dados .
No caso da FANUC, trata-se do MT-LINKi, uma plataforma de análise independente da marca capaz de monitorar mais de 1.000 máquinas-ferramentas CNC de uma só vez, bem como o FASData, um programa de monitoramento de produção. Outros construtores de controle oferecem soluções semelhantes, assim como muitos construtores de máquinas-ferramenta, fornecedores de ferramentas de corte e desenvolvedores de software de terceiros. Todos fornecem os meios para reunir o que é reconhecidamente uma montanha de dados e apresentá-los de uma maneira que faça sentido para os seres humanos, dando-lhes a capacidade de reagir a tendências e problemas potenciais muito antes que possam afetar negativamente os níveis de produção.
O enigma da nuvem
A questão então se torna qual é o melhor lugar para armazenar esses dados e abrigar o software usado para analisá-los? Ambos devem estar localizados na nuvem em uma instalação de hospedagem externa e gerenciados por especialistas dedicados em hardware e software? Ou uma instalação “no local” é mais apropriada, usando qualquer talento interno de TI que a oficina possua?
Webster e os outros entrevistados para este artigo concordaram amplamente que, embora a primeira seja geralmente a abordagem mais segura e econômica, muitas oficinas permanecem apreensivas com programas de peças e dados de produção que saem de suas instalações. O mesmo acontece com Gisbert Ledvon, diretor de desenvolvimento de negócios para máquinas-ferramenta da Heidenhain Corp., com sede em Schaumburg, Illinois. Ele observou que os clientes podem instalar o software StateMonitor da empresa onde quiserem, mas promove instalações no local sempre que possível.
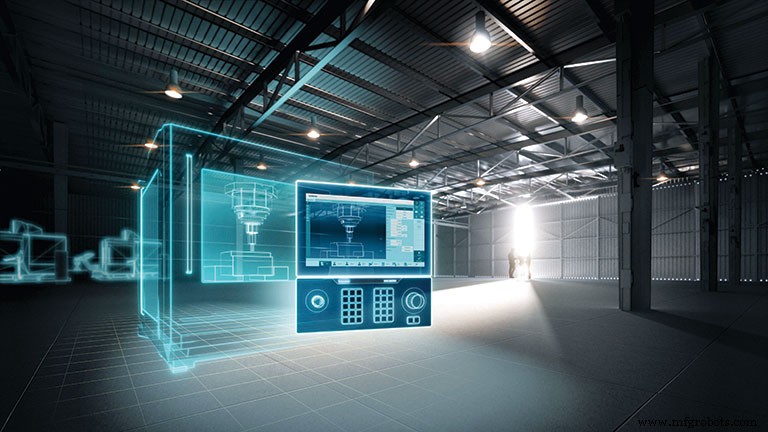
“Nossa filosofia é que os clientes devem proteger sua propriedade intelectual e, para nós, isso significa conectar suas máquinas-ferramentas e sistemas de software a uma rede corporativa devidamente protegida”, disse ele. “Houve muitos casos em que as lojas foram invadidas e forçadas a fazer pagamentos de resgate. É verdade que esses ataques geralmente são realizados por e-mail e não pelo controle da máquina-ferramenta, mas ainda assim é uma preocupação. É por isso que a NTMA (National Tooling and Machining Association) começou a oferecer seminários mostrando aos fabricantes como eles podem se proteger contra esses tipos de crimes cibernéticos.”
Apesar disso, Ledvon admite que a nuvem é uma tendência tecnológica que só vai ganhar força. O que é necessário para mitigar quaisquer riscos associados são boas práticas de manutenção de TI. Instale um firewall robusto entre a rede da loja e o mundo exterior. Evite conexões diretas do CNC para a nuvem baixando arquivos externos, programas de software e patches para um servidor interno seguro e, em seguida, verifique-os com software antivírus antes da distribuição. Treine todos os usuários de computador como gerenciar senhas, identificar e-mails e sites maliciosos e proteger informações corporativas. A lista continua.
“Considerando que o controle é o centro nervoso de qualquer máquina-ferramenta, não acho que a conveniência do acesso à nuvem valha o risco de exposição à Internet”, disse Ledvon. “Nada disso impede os fabricantes de implementar uma estratégia da Indústria 4.0, no entanto. De qualquer forma, eles devem conectar suas máquinas-ferramentas em rede e começar a coletar dados para análise. Isso dará a eles as informações necessárias para configurar as máquinas mais rapidamente, reduzir os tempos de ciclo, maximizar a vida útil da ferramenta e obter todas as outras vantagens oferecidas pelos controles CNC e sistemas de software atuais.”
Talento nativo
Outro componente da Indústria 4.0 é o gêmeo digital, que neste caso se refere a uma representação virtual, mas altamente precisa e abrangente de uma máquina-ferramenta CNC. De acordo com Vivek Furtado, chefe de digitalização – máquinas-ferramentas da Siemens Industry Inc., Elk Grove Village, Illinois, gêmeos digitais simplificam o projeto e a implantação de máquinas CNC, tornando os fabricantes mais eficientes.
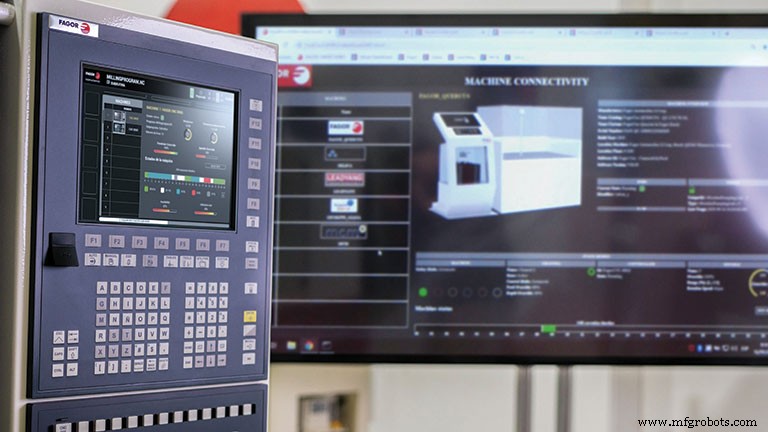
“Nosso controlador SINUMERIK One é conhecido como nativo digital, pois foi construído desde o início para suportar o gêmeo digital e outras tecnologias de habilitação”, disse ele. “Ele oferece aos fabricantes de máquinas-ferramenta CNC a capacidade de criar uma versão virtual de um torno ou centro de usinagem contendo todas as suas cinemáticas e características operacionais. Isso reduz muito o tempo de engenharia e os custos de desenvolvimento e garante que o produto atenda às necessidades dos usuários finais.”
Os controladores com capacidade para gêmeos digitais servem a outros propósitos. Eles aceleram o treinamento de novos funcionários e reduzem a chance de travar uma máquina-ferramenta cara. Eles permitem que os orçamentistas ordenem trabalhos com mais precisão, engenheiros desenvolvam processos de fabricação otimizados e programadores CNC validem o código G e a seleção de ferramentas de corte antes de enviar o trabalho para o chão de fábrica. Uma vez lá, eles facilitam a operação da máquina-ferramenta com gráficos aprimorados e maior usabilidade.
Qualquer pessoa com um sistema CAM de ponta ou software PLM pode dizer que pode realizar a maior parte disso sem um controle CNC avançado. E embora não haja argumentos de que as capacidades dessas e de outras plataformas de software aumentaram drasticamente nos últimos anos, as máquinas-ferramentas que participam do segmento digital fornecem às oficinas uma ferramenta importante, que aprimora a troca de dados e fecha o ciclo da interoperabilidade.
Adaptar e superar
Além da geminação digital, Furtado sugeriu que os controladores CNC estão se tornando muito mais inteligentes e fáceis de usar, com funções e recursos que qualquer usuário de smartphone reconhecerá. “A maioria de nós lembra que uma vez usávamos nossos telefones para ligar para as pessoas”, disse ele. “Hoje, eles permitem monitorar sua saúde, buscar informações, fazer pedidos de produtos e assim por diante. As gerações mais recentes de controladores oferecem funcionalidade semelhante. Eles são capazes de processar informações e preparar dados de maneira a permitir que sejam utilizados de forma mais eficaz por seus operadores humanos ou por outros sistemas.”
Essa inteligência também se estende ao processo de usinagem. Siemens, FANUC e fornecedores de soluções de terceiros, como a Caron Engineering, oferecem recursos de controle adaptativo que monitoram continuamente as cargas do eixo e do eixo, vibração da máquina e fatores semelhantes que afetam a vida útil da ferramenta de corte e a qualidade da peça. Esses sistemas inteligentes ajustam os parâmetros de usinagem em tempo real, otimizando a remoção de material e eliminando possíveis problemas.
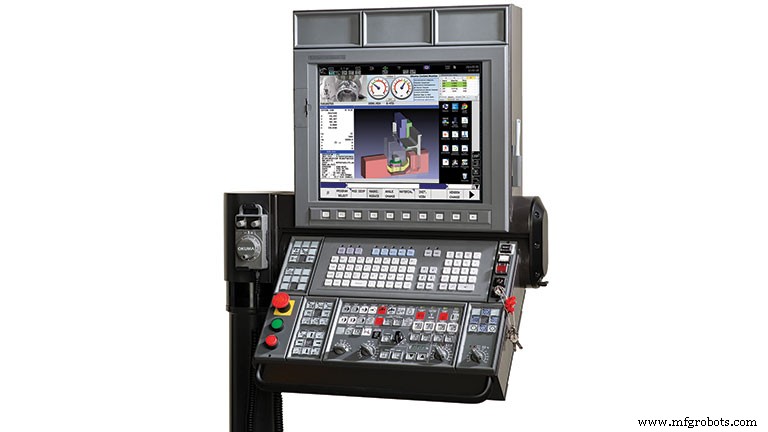
A Fagor Automation Corp., Elk Grove Village, Illinois, é outro fornecedor de controle de olho no prêmio Industry 4.0. Harsh Bibra, gerente geral para a América do Norte da Fagor, explicou que seu controle ARFS (Adaptive Real-time Feed and Speed) faz tudo isso e muito mais, mas observou que esse tipo de tecnologia baseada em sensores também pode ser usada para manutenção preditiva.
“Também oferecemos nosso pacote de conectividade i4.0”, disse ele. “Isso permite que os usuários coletem dados de usinagem, é claro, mas também façam coisas como enviar alertas baseados em condições, ajustar a máquina-ferramenta e atualizar seu firmware, alterar configurações de parâmetros e assim por diante, tudo a partir de um dispositivo móvel ou computador remoto.”
O maior gargalo
Bibra vê grandes mudanças pela frente. Além do aumento do uso de sensores e acelerômetros compatíveis com IIoT em máquinas-ferramentas, juntamente com controladores mais inteligentes, as próprias fábricas se tornarão mais inteligentes. A inteligência artificial (IA) muito além das capacidades adaptativas mencionadas acima se tornará predominante, abrindo portas para a tomada de decisão automatizada necessária para a fabricação generalizada de luzes apagadas.
Tudo isso literalmente ganhará velocidade devido ao desenvolvimento e subsequente implantação das redes celulares 5G, sugeriu Bibra. Isso não apenas aumentará a largura de banda da Internet e reduzirá a latência, mas possivelmente aliviará os medos de hackers mencionados anteriormente. “Os controles do futuro serão equipados com 5G, e os dados que eles gerarem poderão ser enviados sem fio a velocidades de até 10 gigabits por segundo (Gbit/s) para os chamados dispositivos de borda”, disse ele. “Esperamos que dentro de alguns anos, essa tecnologia transforme fundamentalmente a forma como os fabricantes coletam informações do chão de fábrica.”
A desvantagem da Indústria 4.0 é a falta de trabalhadores qualificados capazes de entender e trabalhar com tecnologia avançada. Bibra disse que o retreinamento será necessário à medida que os fabricantes se tornarem mais experientes em tecnologia. No entanto, quaisquer preocupações sobre o conhecimento tribal e a perda de experiência devido ao desgaste e aposentadoria de funcionários devem se tornar história antiga.
Visitando a Loja
Jim Kosmala, vice-presidente de engenharia e tecnologia da Okuma America Corp., Charlotte, N.C., atribui muito do aumento da conectividade de hoje ao uso de controles baseados em PC. “Muitas pessoas esquecem que a Okuma não é apenas uma fabricante de máquinas-ferramenta, mas também faz seus próprios sistemas servo e controladores. Eles rodam no Microsoft Windows e usam um chip Intel, ambos fornecem conectividade fácil.”
Os controles baseados em PC também facilitam a instalação de vários programas de software no controle - no início da pandemia de COVID, por exemplo, os clientes da Okuma podiam colaborar com outras pessoas usando o Microsoft Teams, compartilhando telas ou dando a outras pessoas controle remoto conforme necessário. “Essa é a ideia por trás da nossa App Store”, disse Kosmala. “Os usuários podem baixar e instalar o que precisarem diretamente no controle OSP, eliminando a necessidade de um PC separado. Representa possibilidades inteiramente novas de colaboração e conectividade.”
Um desses aplicativos é o Connect Plan da Okuma, que permite aos usuários monitorar máquinas-ferramentas CNC e coletar dados operacionais. Funciona com quase todas as marcas ou vintages de máquinas-ferramenta, bem como com robôs e outras formas de automação. De acordo com Kosmala, no entanto, o Connect Plan usa um algoritmo de IA para analisar as informações disponíveis e identificar tendências que um humano pode perder.
Considere o gerente de um departamento de torneamento, que percebe depois de semanas analisando relatórios de coleta de dados e painéis que um determinado torno sempre inicia 10 minutos de atraso todas as manhãs graças ao hábito de café do operador, ou que a temperatura do fuso no moedor mais próximo do departamento de expedição cai cada vez que abrem a porta de carregamento. Kosmala explicou que a IA capta essas tendências muito mais rapidamente do que um ser humano, dando aos supervisores a capacidade de abordar possíveis áreas problemáticas mais cedo. Além disso, essas informações são armazenadas em um banco de dados, de modo que quando o supervisor sai da empresa, não há perda de conhecimento.
“Deming nos disse que, sem dados, você é apenas mais uma pessoa com uma opinião”, disse Kosmala. “A IIoT e a Indústria 4.0 tratam de coletar esses dados e fazer uso deles, transformando-os em conhecimento. Esse é o primeiro passo para quem está nessa jornada. Agora temos conferência virtual e a capacidade de verificar o status da máquina ou os níveis de produção de qualquer lugar e acesso a ferramentas remotas que simplificam a automação. Se você puder fazer isso sem ter que entrar na fábrica, tanto melhor. Trata-se de aumentar a eficiência e o tempo de atividade da máquina, ambos mais facilmente realizados usando controladores CNC modernos.”
Sistema de controle de automação
- O que eu faço com os dados ?!
- Democratizando a IoT
- O futuro dos data centers
- Noções básicas de painéis de controle elétrico
- Aprendizado de máquina em campo
- Integração industrial da Internet das Coisas
- A nuvem na IoT
- No Limite da Glória:Habilitando uma Nova Era da Máquina da Internet
- O decodificador permite o monitoramento conectado de dados de cada máquina
- Os muitos benefícios das fábricas inteligentes conectadas à IIoT