Obtenha o desempenho sem tempo de inatividade "testando o sangue da máquina"
Em meados dos anos 2000, o sistema de ar comprimido na fábrica da Toyota North America em Georgetown, KY, travava em média mais de uma vez por ano. Isso levou alguns na fábrica a se perguntarem se o aprendizado de máquina e a IA poderiam resolver esse problema, fornecendo detecção de anomalias, identificação de falhas e, o mais importante, previsão de falhas iminentes antes que elas ocorram.
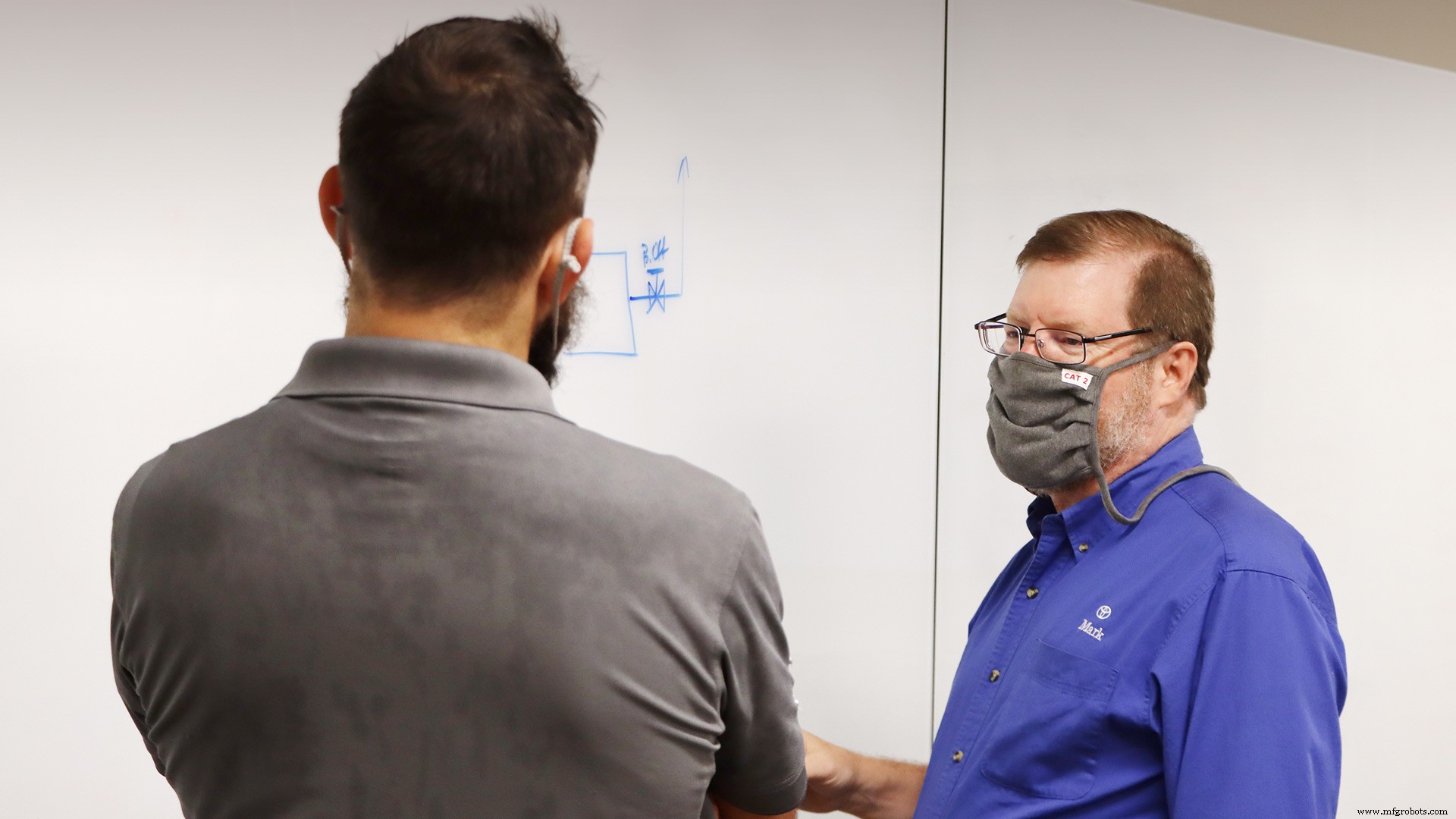
O tempo de inatividade não planejado do sistema de ar comprimido significava, é claro, que toda a fábrica tinha um problema. A oficina de pintura usou ar comprimido para pintar veículos novos com spray. O sistema deu vida às ferramentas pneumáticas e nada se compara ao ar comprimido para soprar lixas e outros resíduos.
Com um veículo acabado saindo de uma das três linhas na fábrica a cada 25 segundos durante dois turnos, as consequências eram significativas se o utilitário de ar comprimido falhasse.
“A despesa, se a linha cair, é enorme”, disse Mark Rucker, gerente de projeto e especialista em assuntos elétricos da fábrica. “Então, há um bom incentivo para ter uma utilidade boa, confiável e estável.”
O sistema de ar comprimido de vários milhões de dólares é composto por uma dúzia de compressores de ar centrífugos Ingersoll Rand, cada um do tamanho de um pequeno caminhão. As lâminas de estágio final de cada compressor giram a 20.000 rpm a uma fração de polegada de sua carcaça. Se uma lâmina operar um pouco fora das especificações e tocar na carcaça, é um caso perdido. A máquina inteira deve ser reconstruída a um custo de cerca de US$ 100.000.
A oscilação da lâmina não é a causa de um acidente; é o resultado.
O acidente - também conhecido como um surto ou fluxo reverso - acontece quando algo faz com que o fluxo normal de ar do compressor para um tubo tente se reverter e o ar no tubo empurra de volta.
A frequência, o custo e as consequências dos acidentes levaram a Toyota a chamar Jay Lee, diretor fundador da Intelligent Maintenance Systems, para obter ajuda.
Jay Lee estava à frente da curva da Indústria 4.0
No início do novo milênio, antes da ligação da Toyota, Lee era um professor de engenharia da Universidade de Cincinnati que imaginou todas as máquinas em uma fábrica conectadas e fornecendo dados para manutenção inteligente. Naquela época, porém, grande parte da tecnologia necessária para tornar a visão de Lee uma realidade ainda não existia.
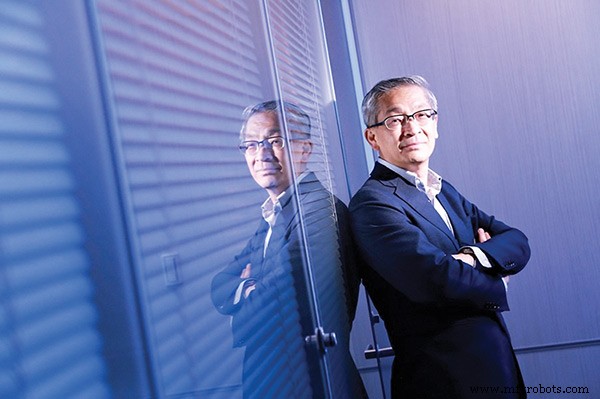
“Vinte anos atrás, muito poucas pessoas acreditavam que isso era possível”, disse Lee, que atualmente está de licença e é vice-presidente e membro do conselho do Foxconn Technology Group em Wisconsin.
Em sua visão industrial, as máquinas são como pacientes e os dados coletados de sensores que monitoram as máquinas fornecem informações sobre sua saúde. Os especialistas obtêm prognósticos interpretando os dados que coletam e analisam.
"Eu disse:'Por que não testar o sangue da máquina?' E qual é o sangue da máquina?" disse Lee. "Dados. A questão é:"Quais dados você deseja obter?" Depende do que você deseja analisar. Precisamos entender o contexto e o conteúdo e formular ainda mais um modelo de relacionamento entre os desconhecidos invisíveis”.
Oculto nos dados está o significado sobre o comportamento desviante de uma máquina ou processo. Desbloquear esse significado leva à previsão de qualidade, determinando a estabilidade da máquina ou processo e evitando possíveis falhas. “É exatamente disso que trata a Indústria 4.0 hoje”, disse Lee.
O termo “Indústria 4.0”, é claro, não foi popularizado até a época da iniciativa do governo alemão em 2013.
Nenhuma falha desde 2006
Uma vez na Toyota, Lee e sua equipe de analistas de dados se juntaram a Rucker e um grupo de trabalhadores de manutenção qualificados e engenheiros de fábrica para resolver o problema do sistema de ar comprimido.
A simplicidade de suas perguntas desmentia a complexidade da tarefa à frente.
“Podemos prever um problema de fluxo reverso antes que ele cause uma falha?” disse Rucker. “Podemos ver algo se desenvolvendo a tempo de fazer algo a respeito?”
Durante meses de tentativa e erro em 2005, a equipe coletou e analisou dados de alta fidelidade de um dos compressores e procurou por anomalias. Às vezes, a equipe criava uma condição de surto ou abordagem de surto para forçar a máquina a começar a exibir um comportamento desviante e ver como isso se parecia no conjunto de dados.
Eventualmente, o trabalho da equipe valeu a pena. Seus membros viram que o melhor preditor de uma condição de surto incipiente ocorreu no estágio dois (dos quatro estágios em que o compressor percorre esse progresso da pressão normal para 120 libras de pressão por polegada quadrada, ou PSI).
“Qual é a física por trás disso, por que isso é o preditor?” disse Rucker. “Não sei, não me importo. Acabamos de ver que isso prevê com segurança um aumento futuro e o prevê com segundos de aviso. ”
O próximo passo foi colocar um sensor diferencial em cada compressor e criar um algoritmo de aprendizado de máquina para a unidade de controle central. Os testes confirmaram que assim que o estágio dois começasse a “balançar”, o compressor começaria a recuar.
“Toda vez que testávamos, isso nos mantinha longe de problemas”, disse ele. “Não tivemos acidentes desde 2006.”
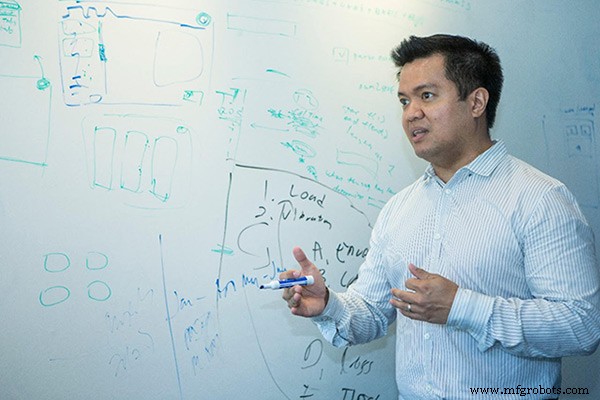
Embora o projeto do compressor tenha sido um sucesso, outro que se concentrou em tentar prever a vida útil dos rolamentos nos gigantes do ar comprimido falhou. A equipe não conseguiu encontrar dados de manutenção confiáveis suficientes e combiná-los com dados operacionais da máquina para traçar correlações úteis, disse Rucker.
“Isso provavelmente é a mistura certa de P&D”, disse ele. “Você tenta coisas e não sabe se vai funcionar ou não. E se metade das vezes você receber seu dinheiro de volta, isso é uma vitória. E de vez em quando você encontra aquele que paga por todo o resto – como o controle de surto.”
Flexibilidade é fundamental
Lee posteriormente publicou um artigo sobre o projeto da Toyota e, em 2013, ajudou a cofundar a Predictronics com Patrick Brown, funcionário da Intelligent Maintenance Systems, e dois de seus estudantes universitários, David Siegel e Edzel Lapira. Marrom. Lapira e Siegel formam a suíte Predictronics C.
Assim como Rucker, da Toyota, pediu ajuda de IA a Lee, as empresas procuram a Predictronics para obter ajuda com suas aspirações de tempo de inatividade zero.
“Diferentes clientes geralmente estão em diferentes níveis de maturidade”, disse Lapira, que é CEO. “Temos alguns clientes que já possuem uma estrutura de coleta de dados:eles têm um data lake, mas não sabem o que fazer com os dados. Também temos alguns clientes que precisam começar do zero.”
Clientes com ativos de 50 ou 60 anos devem começar ainda mais cedo.
Cada vez mais, a Predictronics é abordada por clientes com máquinas legadas. Lapira e seus colegas os mandam comprar componentes como acelerômetros e transdutores.
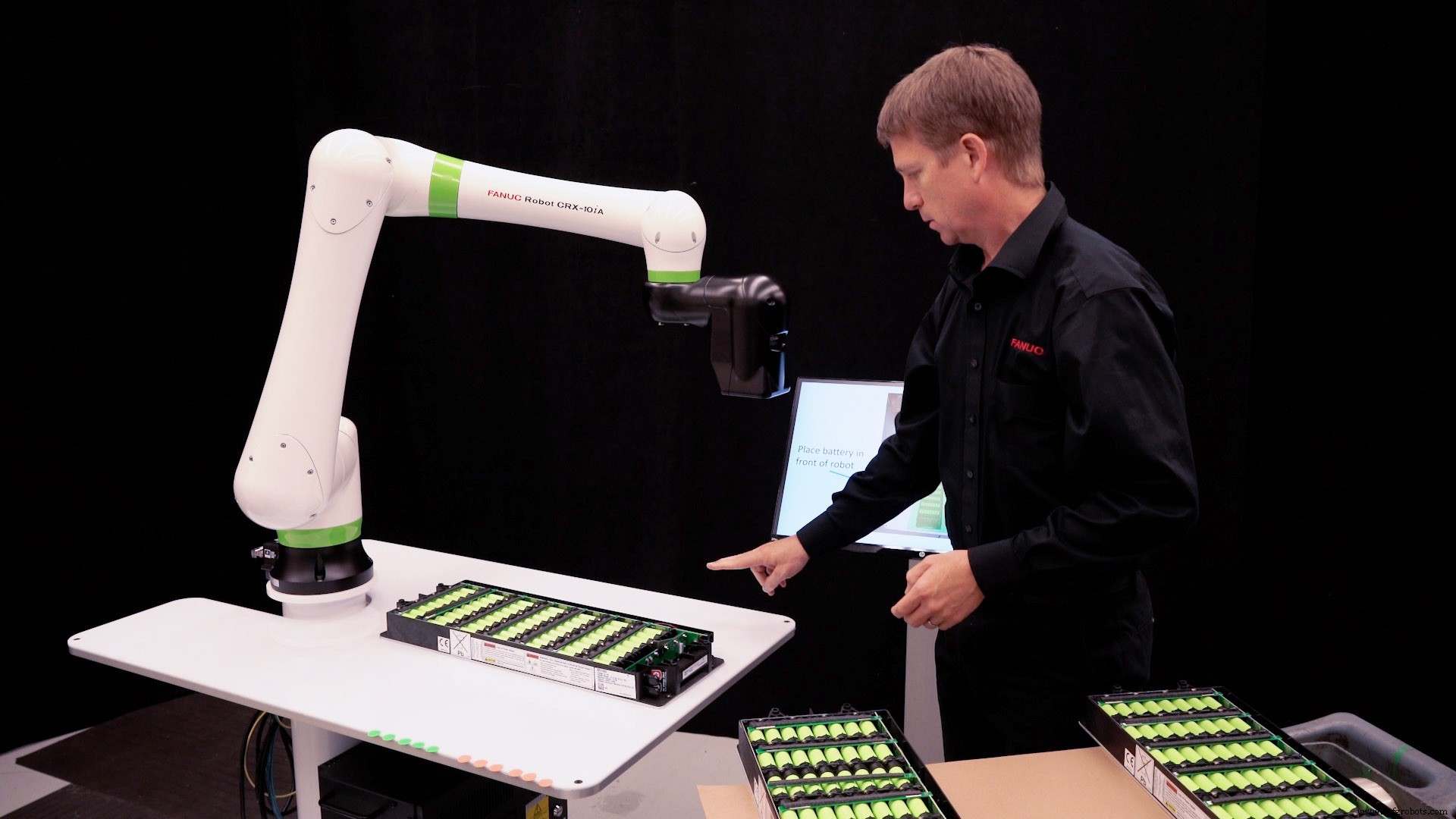
“Estes são os diferentes conversores analógico-digitais de que precisamos para obter esses dados”, disse ele.
Desde sua fundação em 2013, a Predictronics ajudou mais de 70 fábricas com soluções de IA, muitas delas empresas da Fortune 500.
A Predictronics trabalhou com um cliente, um fabricante de semicondutores, para estabelecer uma solução preditiva de metrologia virtual capaz de aprender a relação entre o sensor e as variáveis de medição.
O projeto foi desafiador devido às centenas de sinais medidos emitidos pelo equipamento semicondutor.
Mas existem métodos estatísticos bem conhecidos para diminuir o número de possibilidades, disse Siegel.
“Além desses métodos, nos últimos anos tem sido mais da comunidade de aprendizado de máquina que desenvolveu métodos que incorporam um algoritmo de regressão de classificação que possui uma parte de seleção de variável integrada”, disse ele. “Então, isso reduz as 10 principais, ou 20 ou 30 variáveis. Então você trabalha com o cliente ou usa seu próprio conhecimento para determinar o que faz mais sentido incluir no software e no modelo de análise.”
Se a Predictronics aplica o conhecimento adquirido com a experiência anterior em sua abordagem baseada em modelos, que ajuda a manter os custos baixos, ou uma solução formulada em uma parte de uma empresa que pode ser dimensionada internamente, “encontrar uma solução que aborde diretamente os problemas mais críticos questões, mas também é flexível o suficiente para ser aplicado a outros problemas”, disse Brown.
AI de due diligence
As fábricas que estão procurando um fornecedor de soluções de IA como a Toyota fez para seu problema de ar comprimido devem fazer a devida diligência para encontrar o ajuste certo.
Ajuda saber as perguntas certas a serem feitas, disseram os especialistas da Predictronics:
Onde seus serviços foram usados antes?
Sua solução demonstrou uma melhoria clara nas operações de negócios em termos de redução do tempo de inatividade ou aumento da qualidade?
A sua solução foi utilizada na minha indústria?
Sua equipe tem conhecimento do domínio industrial?
Sua solução funciona com equipamentos legados?
Sua solução funciona com uma variedade de sensores?
Sua solução usa aprendizado de máquina?
Quantos dados são necessários para treinar o modelo?
Ele precisa apenas de dados de uma máquina saudável ou dados de uma máquina degradada ou defeituosa também para aprender?
Os robôs também querem IA
Embora as máquinas-ferramentas em uma oficina tenham um desempenho melhor sob a influência da IA, não há razão para que os robôs não possam fazer o mesmo.
A Fanuc America adicionou recentemente “AI Error Proofing” ao seu controlador de robô e à função de visão dos robôs, iRVision, que usa aprendizado de máquina (ML) para inspeção de peças.
Com o recurso à prova de erros, um operador usa imagens para treinar o ML para verificar duas situações distintas - se uma porca soldada estiver presente ou ausente, por exemplo - e aceitar ou rejeitar uma peça.
Como o iRVision pode suportar até 27 câmeras, a função à prova de erros pode atuar em vários pontos do processo de fabricação.
“Você quer identificar rejeições ou erros antes de continuar agregando valor a uma peça ruim”, disse Josh Person, engenheiro de equipe do grupo de visão de máquina da Fanuc.
“Muitas vezes, você pode ver um erro em um estágio e o próximo o encobriria”, acrescentou.
Durante a configuração, o operador pode apresentar vários exemplos de peças de trabalho e classificá-las em duas categorias:boas e ruins. Se o exemplo não se enquadrar em nenhuma das classes, ele produzirá “indeterminado”. Exemplos indeterminados podem então ser adicionados para melhorar o modelo aprendido.
Sistema de controle de automação
- VISÃO:Para cegos
- Avaliando as vantagens do DevOps para testes de desempenho de IoT
- Automação:o que significa para o futuro dos negócios
- O futuro da entrega sem contato
- Obrigado pelas lembranças!
- Os benefícios da automação para sua empresa
- Como escolher o filtro certo para seu aplicativo
- Cinco maneiras de encontrar o compressor certo para o hobby doméstico
- Diretrizes para selecionar o provedor de serviço de ar comprimido certo
- Dando as boas-vindas a Dorothy Parnell como autora do blog The Compressed Air Blog