5 dicas de design para peças moldadas por injeção com recursos complexos
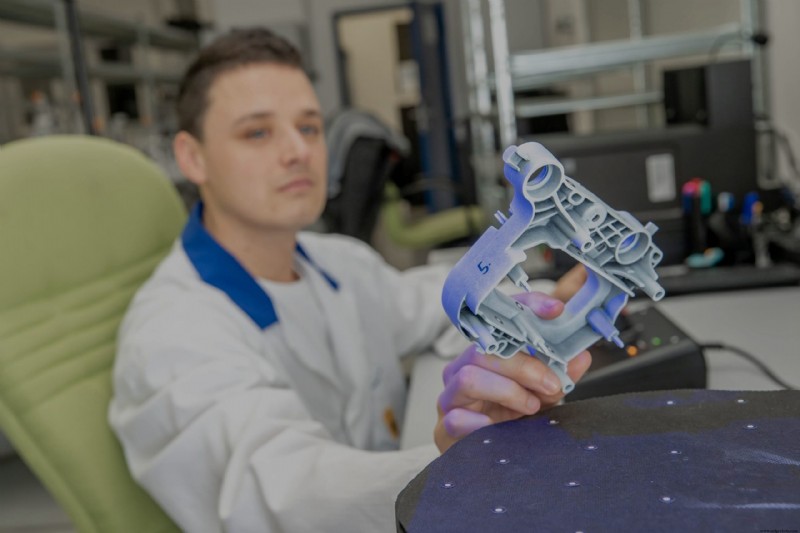
Design for manufacturability (DFM) é a prática geral de projetar peças para que também sejam eficientes para produzir. Embora as práticas recomendadas específicas variem de acordo com a tecnologia de fabricação, o objetivo final do DFM em geral é otimizar o projeto da peça para minimizar os custos de fabricação — sem sacrificar o desempenho ou a função. O DFM também ajuda a identificar possíveis problemas ou defeitos antecipadamente e evitar reprojetos disruptivos no futuro, e é por isso que avaliar possíveis métodos de fabricação é crucial durante as fases iniciais de projeto e prototipagem.
O design intencional e focado no método é especialmente importante ao tentar produzir peças com geometrias complexas ou recursos intrincados. E embora existam muitos métodos de fabricação viáveis para a produção de peças com geometrias complexas, a moldagem por injeção está entre os mais comuns.
O DFM é especialmente importante para peças moldadas por injeção, pois as ferramentas rígidas e os moldes usados para criar peças moldadas por injeção introduzem uma série de variáveis que podem afetar o projeto – incluindo temperatura do molde, temperatura do material e pressão do ar. Além disso, os moldes de injeção são caros e demorados para ferramentas, e o processo normalmente só se torna econômico ao produzir peças em grandes volumes, portanto, a consistência e a repetibilidade são críticas ao projetar peças com geometrias complexas ou recursos intrincados.
Aqui estão 5 dicas importantes sobre como projetar peças moldadas por injeção de plástico com recursos complexos.
1. Aproveite os fechamentos deslizantes para clipes e encaixes de encaixe
Clipes e encaixes são duas formas de mecanismos de fixação que podem ser incorporados diretamente no projeto do molde de injeção – alguns exemplos comuns são tampas de conjuntos de ferramentas e caixas de eletrônicos. Ambos funcionam de forma semelhante:em um lado do mecanismo, uma aba flexível de material prende-se em uma ranhura ou bolso na parte de acoplamento, prendendo assim os dois.
As tampas deslizantes ou telescópicas são componentes usinados em um lado do molde que se estendem até a outra metade, deslizando no lugar quando o molde é fechado. Isso evita que o material flua para áreas específicas, o que torna possível incorporar facilmente recursos como ganchos e furos (incluindo furos passantes longos) sem a necessidade de ações laterais caras, ressaltos, inserções e outros recursos que aumentam o custo e a complexidade do o projeto do molde.
As tampas deslizantes podem ser projetadas para ter a mesma aba e ranhura para combinar com os clipes e encaixes da peça, criando recursos que se encaixam com segurança e retêm flexibilidade suficiente para separar sem quebrar. Os fechamentos podem reduzir o projeto do molde e os custos operacionais e geralmente também podem ser usados como uma solução alternativa para rebaixos e recursos rebaixados.
Em geral, tanto a peça quanto o molde devem ter um mínimo de 3 graus de inclinação para evitar que o metal esfregue contra o metal, o que pode criar rebarbas e danificar o fechamento.
2. Escolha o material certo para as dobradiças vivas
As dobradiças vivas, outro recurso de tampa flexível, são uma excelente maneira de prender as duas metades dos componentes plásticos moldados por injeção (pense nas tampas dos recipientes individuais de um dispensador de vitaminas semanal, por exemplo).
Embora a consideração do material seja sempre uma consideração crítica no design e no desenvolvimento de produtos, deve ser sua principal preocupação ao projetar dobradiças vivas. O polipropileno, por exemplo, é mais adequado para esse recurso do que o policarbonato (que pode ser um excelente material para clipes e encaixes). Dependendo da amplitude de movimento esperada da tampa, pode ser necessário incorporar um raio no ponto médio da dobradiça para permitir que as duas partes fechem mais facilmente.
3. Fique de olho na espessura da parede
A espessura da parede deve permanecer uniforme sempre que possível, pois variações na espessura podem introduzir sérias complicações. Peças com espessura de parede não consistente correm o risco de empenamento (causado por diferentes seções da peça esfriando em taxas diferentes, o que cria tensão interna que dobra a peça permanentemente).
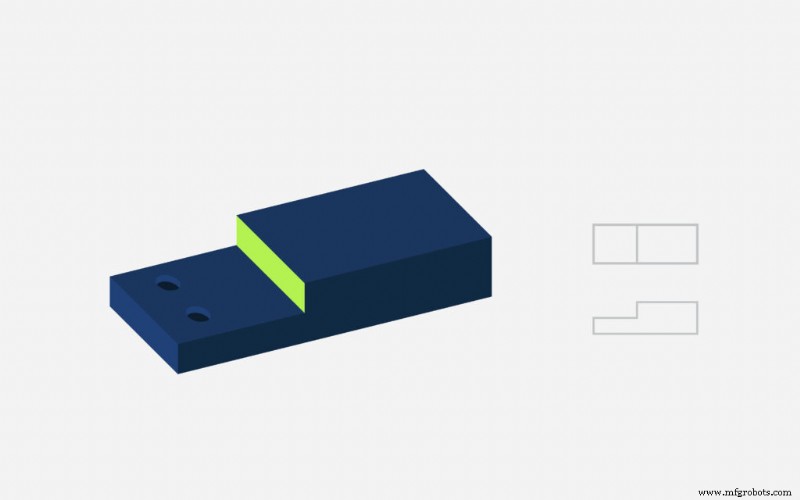
Além disso, se as paredes de uma peça forem muito grossas ou finas, podem surgir outros problemas. Por exemplo, paredes finas e nervuras de suporte mal projetadas podem impedir a fluidez, causando curtos curtos (ou preenchimentos incompletos do molde). Por outro lado, peças com paredes grossas e nervuras mal projetadas são propensas a desenvolver marcas de afundamento ou impressões na superfície da peça causadas pelo resfriamento da resina interna mais rápido que o material externo. Se você vir sinais de qualquer falha, talvez seja hora de reexaminar o design do molde.
4. Adicione rascunho e reduza a altura de recursos altos
Recursos altos como ressaltos, nervuras e espaçadores podem exigir que você incorpore maiores ângulos de inclinação (geralmente até 3°) para garantir que a peça saia do molde sem linhas de arrasto ou outros problemas de ejeção. Ressaltos e recursos altos permitem insertos rosqueados e resistência adicional da peça, mas aumentam o risco de desenvolver marcas de afundamento.
Além disso, aumentar a altura das nervuras e outros recursos também aumenta a profundidade do molde, aumentando a necessidade de fresas de topo mais longas, mais ventilação e taxas de corte mais lentas durante o processo de usinagem. Uma forma de contornar isso é apoiar os ressaltos com nervuras verticais periféricas, que possuem paredes mais finas, reduzindo a chance de sumidouros.
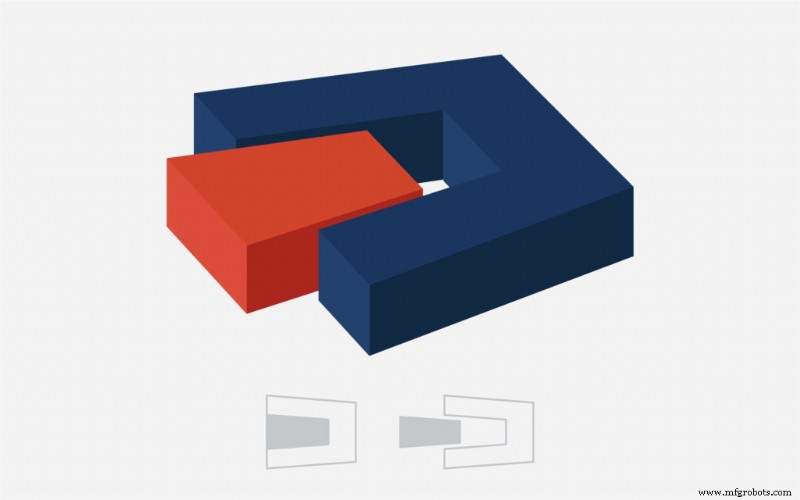
Os ressaltos angulares e outros recursos aumentam a complexidade da produção, pois o eixo do ressalto não se alinha mais com a linha de partição ou a linha de tração - o que praticamente exige que uma pastilha precise ser carregada manualmente no molde antes de cada disparo.
5. Seja estratégico com textos e logotipos
Texto (como o nome de um produto ou empresa) ou logotipos são comumente adicionados a produtos moldados por injeção. A boa notícia é que tamanhos de fonte pequenos são bastante fáceis de alcançar por meio de moldagem por injeção – contanto que você siga algumas diretrizes importantes.
Primeiro, o texto deve ser uma fonte sem serifa e o menor comprimento do traço (a barra transversal de um T ou A, por exemplo) deve ter pelo menos 0,020” de comprimento. O texto em relevo é mais fácil de ler e produzir do que o texto afundado na superfície de uma peça. A menos que o texto seja excessivamente grande, não deve ter mais de 0,015” de altura.
Por fim, a menos que você esteja trabalhando com materiais flexíveis, como borracha de silicone ou elastômero termoplástico (TPE), o texto deve estar voltado para a direção de tração, se possível – caso contrário, inserções carregadas manualmente ou ações laterais podem ser necessárias para garantir uma ejeção suave.
Comece a refinar seu projeto de moldagem por injeção hoje mesmo
Geometria complexa e um alto grau de complexidade de recursos não são o fim do mundo para peças moldadas por injeção. Ao prestar atenção aos principais fatores de design, como design de molde, seleção de material, orientação do ressalto e estilo e tamanho do texto, você poderá melhorar a capacidade de fabricação de sua peça (e, portanto, a relação custo-benefício) e a qualidade ao mesmo tempo.
É claro que a parceria com um fabricante experiente é outra maneira infalível de otimizar as fases de projeto e produção do desenvolvimento do produto. Fast Radius traz décadas de experiência em engenharia e design para a mesa, e trabalhamos diligentemente ao lado de cada cliente para garantir que suas peças não sejam apenas bem feitas, mas que sejam feitas da maneira mais eficiente e econômica possível. Entre em contato conosco hoje para descobrir como podemos tornar seus projetos uma realidade.
Tecnologia industrial
- Aprenda a projetar com E3.series para equipamentos industriais
- 5 dicas para design de chapas metálicas
- 5 dicas de design para RIM
- Dicas de design para moldagem por fundição
- Práticas e dicas de design para economia de custos para peças e gabinetes de chapa metálica personalizados
- Multitarefa para peças pequenas e complexas
- 5 dicas de segurança para trabalhar com máquinas
- 5 dicas para o projeto de circuitos automotivos derrotar a EMI
- Dicas de design para moldagem por injeção
- Dicas de design para impressão 3D de sinterização direta de metal a laser