Cinco dicas de design para fundição de uretano
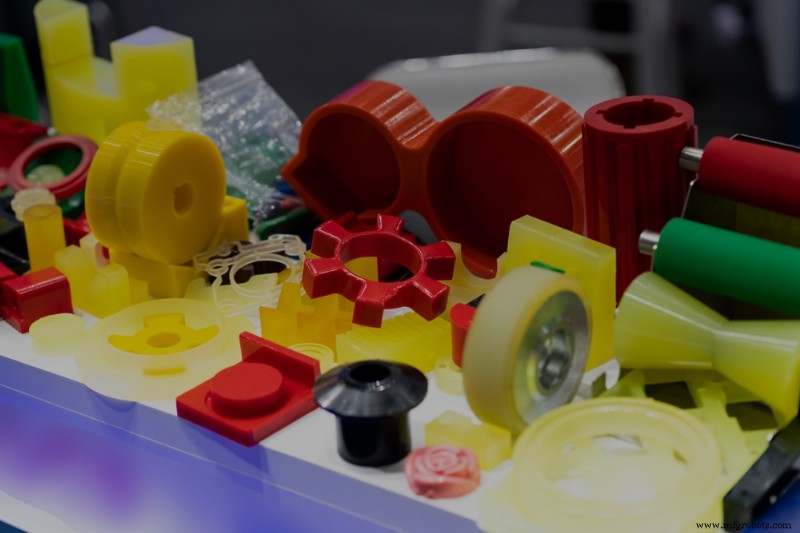
A fundição de uretano é um processo de fabricação tradicional versátil que usa um padrão mestre impresso em 3D e um molde de silicone para criar peças plásticas de uso final. Durante o processo de fundição de uretano, o padrão mestre é colocado dentro de uma caixa selada, coberto com silicone líquido e depois curado. Depois que o silicone endurece, um fabricante o corta ao meio para liberar o padrão mestre - neste ponto, o molde de uretano fundido está pronto para uso.
Para criar peças de uretano moldadas personalizadas, os engenheiros despejam resina de moldagem de uretano - normalmente um material de poliuretano que pode imitar as propriedades físicas do plástico usado na moldagem por injeção - no molde e o cura em um forno. A parte final geralmente requer pouco ou nenhum pós-processamento.
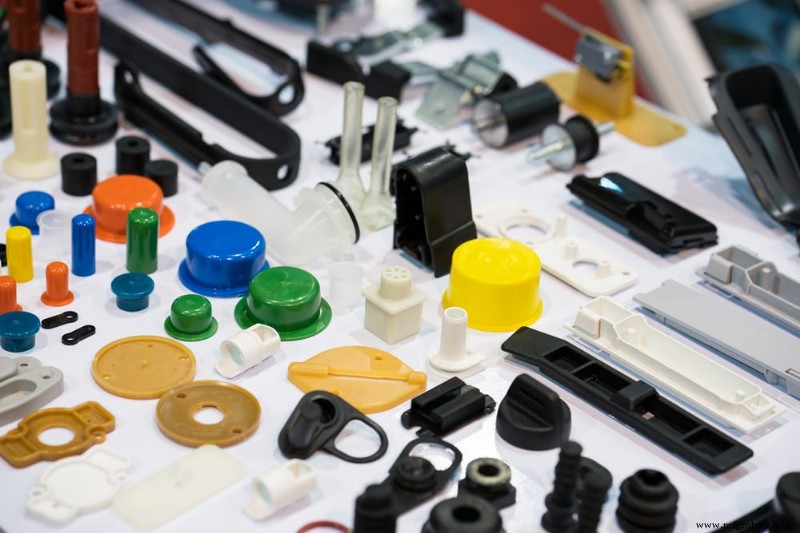
Menos caro e menos demorado do que ferramentas duras, a fundição de uretano é ideal para prototipagem rápida e execuções de produção de baixo a médio volume de construções complexas. Para tirar o máximo proveito desse processo de fabricação, as equipes de produto devem projetar para a fabricação e otimizar o projeto do molde desde o início para agilizar o processo de produção e manter os custos baixos. Aqui estão cinco dicas essenciais de design para criar peças de uretano fundido personalizadas limpas e funcionais:
5 dicas de design para fundição de uretano
1. Dê uma espessura de parede uniforme
Muitos engenheiros preferem a fundição de uretano à moldagem por injeção porque o processo anterior permite uma maior variação nas espessuras das paredes, mas ainda é importante garantir que um determinado projeto de molde de uretano tenha paredes uniformes. Paredes uniformes reduzem o risco de deformação durante a cura, garantem que o molde seja preenchido de forma completa e precisa e atenuam outros problemas de projeto.
Recomenda-se uma espessura mínima de parede de 0,040” (1 mm), mas há casos em que as paredes podem ser tão finas quanto 0,020” (0,5 mm) em peças pequenas. Para peças maiores, a espessura da parede deve sempre aumentar proporcionalmente ao tamanho da peça para garantir que as paredes possam fornecer suporte adequado.
2. Conta para redução
Quando duas paredes com espessuras diferentes se cruzam em um projeto de molde de uretano, pode ocorrer encolhimento. Como as paredes mais grossas solidificam mais lentamente do que as paredes mais finas, a área à qual elas estão presas na parede nominal encolherá à medida que a projeção - uma nervura ou uma saliência - encolhe. Isso causa uma área rebaixada na parede nominal. Para minimizar o encolhimento e evitar áreas afundadas, os engenheiros devem garantir que a espessura das nervuras caia entre 50% e 60% das paredes às quais estão presas.
Ainda assim, às vezes as peças fundidas de uretano encolhem por outros motivos que não uma falha no projeto do molde de uretano. As dimensões finais de uma peça fundida de uretano dependem da precisão do padrão mestre e do molde, da geometria da peça, bem como dos materiais de fundição de uretano. Uma taxa de encolhimento de 0,15% é considerada aceitável, mas os engenheiros devem rever o projeto do molde de uretano se a taxa de encolhimento ultrapassar esse limite.
3. Empregar costelas
Adicionar nervuras a um projeto de molde de uretano pode aumentar a resistência e a rigidez da peça final sem adicionar espessura. Para usar as nervuras corretamente, os engenheiros devem seguir as seguintes diretrizes:
Altura
As nervuras mais longas fornecem maior reforço, mas a fundição de uma nervura longa pode dificultar a moldagem da peça. Por esta razão, uma costela não deve exceder uma altura três vezes a sua espessura. Para evitar completamente o problema da altura, os engenheiros podem usar várias nervuras curtas em vez de uma longa nervura para aumentar a rigidez da peça.
Largura
A largura da nervura na interseção da peça deve ser de 40% a 60% da espessura da peça. Se um raio de filete estiver incluído no projeto, ele deve ser de pelo menos 25% da espessura da peça. Esses parâmetros ajudam a tornar a costela o mais forte possível.
Ângulo de rascunho
Os engenheiros devem esboçar uma nervura projetada para reduzir a possibilidade de afundamento. Os ângulos de inclinação para cada lado devem estar entre 0,25 e 0,5 graus e o ângulo de inclinação de cada lado deve ser igual. Para superfícies texturizadas, adicione uma inclinação adicional de 1,0 grau para cada 0,025 (0,001 polegada) de profundidade de textura.
Espaçamento
Os engenheiros devem definir nervuras consecutivas com pelo menos duas vezes a espessura umas das outras para distribuir uniformemente o peso da peça em todas as nervuras.
Orientação
A orientação das nervuras determina como e onde a peça sofre tensão, portanto, os engenheiros devem ter o cuidado de organizar as nervuras de uma maneira que maximize a rigidez à flexão da peça. Se as nervuras forem colocadas na posição errada, elas não terão nenhum impacto positivo na resistência da peça.
As equipes de produto também devem estar atentas às interseções e afundamentos ao trabalhar com nervuras. No ponto em que uma nervura se cruza com a peça, uma nervura pesada pode fazer com que a peça mergulhe. Para evitar o afundamento na interseção da nervura, os engenheiros podem usar filetes para aliviar a tensão na superfície da peça e reduzir o afundamento no lado oposto da peça. Os raios dos filetes devem ser pelo menos um quarto da espessura da peça. Além disso, retirar o testemunho ou reduzir o peso da peça reduz a quantidade de material usado e ajuda a manter uma espessura de parede uniforme em toda a peça.
As nervuras podem melhorar drasticamente o desempenho de uma peça final, mas os engenheiros e as equipes de produto não devem se empolgar. As nervuras só são úteis quando a peça requer reforço extra. Em situações em que este não é o caso, as nervuras geralmente são colocadas incorretamente e fazem pouco para melhorar a resistência ou rigidez da peça. Além disso, nervuras desnecessárias aumentam o peso e o preço da peça, causam problemas de moldagem e contribuem para o desperdício de material. Engenheiros e equipes de produto devem manter essas considerações em mente ao decidir se o projeto do molde de uretano requer ou não uma nervura.
4. Considere rascunhos e cortes
Rascunhos e rebaixos não são uma preocupação com a fundição de uretano porque o silicone líquido pode assumir a forma de qualquer molde. No entanto, se um engenheiro estiver usando fundição de uretano para construir um protótipo que eventualmente será fabricado usando um processo diferente, como moldagem por injeção, ele deverá criar o projeto conforme pretendido para a produção de uso final. Isso pode incluir a incorporação de rascunhos e cortes inferiores. Recursos longos de rascunho zero vêm com um pequeno risco de quebra da peça ao extrair a peça do molde, portanto, um pequeno ângulo pode ser útil, especialmente para tiragens de produção maiores.
5. Inclua espaçamento suficiente entre letras e logotipos
Com a fundição de uretano, é fácil para os designers moldarem letras e logotipos em relevo ou embutidos de alta qualidade em peças personalizadas de uretano fundido. Para garantir que as letras sejam tão bonitas e legíveis quanto possível, os designers devem manter em mente a altura ou a profundidade do recurso, a largura do recurso, os raios do recurso e o espaço entre os recursos.
As equipes de produto devem deixar pelo menos 0,050” entre os recursos, embora isso possa variar dependendo das particularidades do design. Todos os raios devem ser pelo menos iguais à metade da altura do recurso, mas raios maiores são ainda melhores. Finalmente, a largura de todos os logotipos ou letras deve ser o dobro da altura.
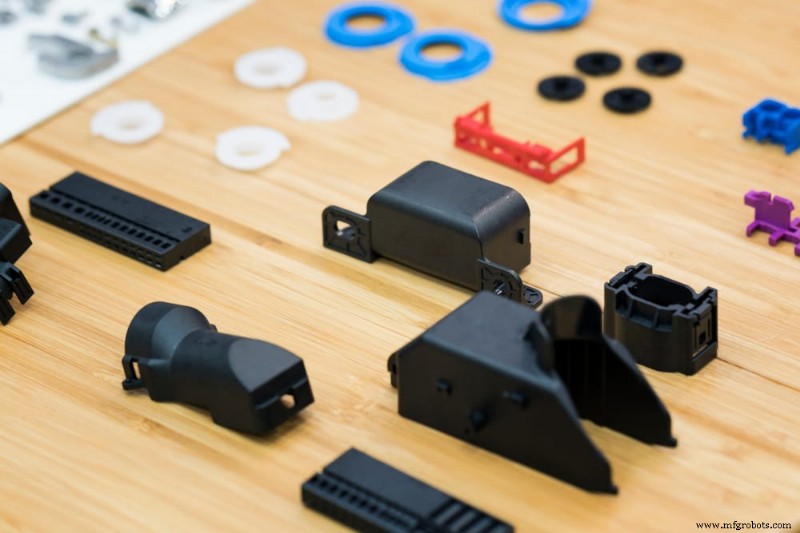
Otimize suas peças fundidas em uretano
Com a fundição de uretano e o design para fabricação, algumas pequenas alterações no design ajudam bastante. Engenheiros e projetistas devem procurar manter espessuras de parede uniformes, levar em conta o encolhimento e garantir que estejam usando nervuras de forma eficaz. As equipes de produto podem otimizar ainda mais a capacidade de fabricação criando designs que se destinam à produção de uso final e certificando-se de que deixem espaço suficiente entre letras e logotipos para aumentar a estética.
Um parceiro de fabricação experiente como a Fast Radius pode ajudar as equipes de produto a simplificar o projeto para a fabricação. Somos apaixonados por desenvolver produtos que antes eram considerados impossíveis de fabricar, e fazemos questão de acompanhar as mais recentes tecnologias de design digital.
As equipes de produtos que buscam desenvolver uma aplicação inovadora ou otimizar um projeto de molde de uretano existente podem se beneficiar dos anos de experiência de nossa equipe de projeto em todos os processos de fabricação. Entre em contato conosco hoje para começar suas peças personalizadas de uretano fundido.
Para obter mais dicas de design e informações sobre fundição de uretano, confira os artigos relacionados no centro de aprendizado Fast Radius.
Pronto para fazer suas peças com Fast Radius?
Comece sua cotaçãoTecnologia industrial
- Cinco dicas para otimizar cadeias de suprimentos de saúde
- Cinco dicas para criar um processo eficiente de integração de fornecedores
- Envio da loja no mesmo dia? Cinco dicas para entrega mais rápida
- 5 dicas para design de chapas metálicas
- 6 dicas para otimizar seu projeto para um projeto de fabricação de metal
- 5 dicas de design para RIM
- Dicas de design para moldagem por fundição
- Dicas de design de fundição de poliuretano
- 5 dicas para o projeto de circuitos automotivos derrotar a EMI
- Dicas de design para moldagem por injeção