Principais características de um moderno laminador de tiras a quente
Principais características de um moderno laminador de tiras a quente
O objetivo de um laminador de tiras a quente (HSM) é reaquecer e laminar placas grossas em tiras finas com uma ampla faixa de espessura. Devido ao seu enorme tamanho e grande investimento, um laminador de tiras a quente precisa ter uma vida útil de várias décadas. A usina deve ser capaz de atender às demandas do mercado para uma ampla gama de tipos de aço, em particular, aços de alta resistência e aços avançados de alta resistência (AHSS) com boa conformabilidade a frio e com propriedades de tira superiores. O moinho deve ser capaz de atender ao seguinte requisito
- Alta disponibilidade do moinho, juntamente com alta produtividade e altos rendimentos.
- Atendendo à necessidade de baixa manutenção.
- Atendendo à necessidade de menor consumo de energia.
- Melhoria da qualidade do produto, atendendo às tolerâncias de espessura e perfil, conforme a necessidade dos clientes modernos, por meio de controles e ajustes poderosos. Essas tolerâncias podem ser muito mais próximas do que o especificado em vários padrões internacionais.
- Cronogramas de laminação mais flexíveis para garantir prazos de entrega curtos e laminação econômica de lotes menores.
Para atender a esses requisitos exigentes, muitos recursos importantes são incorporados nos modernos laminadores de tiras a quente convencionais. Alguns destes são descritos abaixo.
- Forno de reaquecimento – Os modernos laminadores de tiras a quente são equipados com fornos de feixe móvel com eficiência energética que normalmente são controlados por computador. Esses fornos de reaquecimento aquecem uniformemente as placas até as temperaturas desejadas nas taxas de produção necessárias e sem marcas de derrapagem e sem pontos frios. Esses fornos são capazes de receber placas frias ou quentes como material de carga no forno.
- Desincrustantes – Os descalcificadores são indispensáveis nos laminadores de tiras a quente para obter uma boa qualidade de superfície. Os descalcificadores atuais empregam tecnologia de ponta de bico com aplicação altamente eficaz de água de alta pressão (até 400 bar). Os descalcificadores geralmente são de design fechado para evitar que a água escape.
- Prensa de colagem de placas – Uma prensa de colagem de placas na área de desbaste tem a vantagem tecnológica sobre uma biseladora convencional. Além de grandes reduções de largura (até 350 mm), resulta em uma forma nitidamente melhor da laje ao centro. A prensa de dimensionamento de lajes produz ossos de cachorro mais planos, levando a uma redução de espalhamento e maior eficiência de dimensionamento. Um modo de operação especial de curso curto na cabeça e na cauda da laje resulta em menos perdas de colheita e maiores rendimentos. A prensa de colagem de placas permite que o número de tamanhos diferentes de lingotamento em máquinas de lingotamento contínuo seja reduzido a apenas algumas larguras padrão e, portanto, oferece mais flexibilidade na produção. A prensa de dimensionamento de lajes melhora a tolerância de largura ao longo de toda a tira.
- Sistema de ajuste hidráulico da biseladora – A largura da tira da cabeça à cauda é controlada por este sistema. A rápida resposta dinâmica deste sistema permite os movimentos corretivos rápidos na cabeça e na cauda do material para reduzir as perdas de colheita e no controle da largura ao longo do comprimento da tira. As biseladoras de última geração são instalações totalmente hidráulicas sem nenhum sistema de ajuste eletromecânico adicional.
- Caixa de bobinas – É instalada entre o moinho de desbaste e o moinho de acabamento para formar bobinas de barras de transferência, servindo assim como acumulador de material e calor. Durante o desenrolamento, a extremidade traseira da barra de transferência torna-se a extremidade superior da barra de transferência ao entrar na fresadora de acabamento. A caixa da bobina permite uma distância menor entre a fresa de desbaste e a fresa de acabamento. Também minimiza a queda de temperatura da barra de transferência que entra no laminador de acabamento. A caixa da bobina pode ser com mandril ou pode ser sem mandril. A caixa de bobina sem mandril contribui ainda mais para reduzir a queda de temperatura nos envoltórios internos da bobina em comparação com a caixa de bobina do tipo mandril. A caixa de bobina sem mandril também abre espaço para instalar os protetores térmicos laterais que contribuem para reduzir a queda de temperatura na borda da tira. A caixa da bobina é mostrada na Fig. 1.
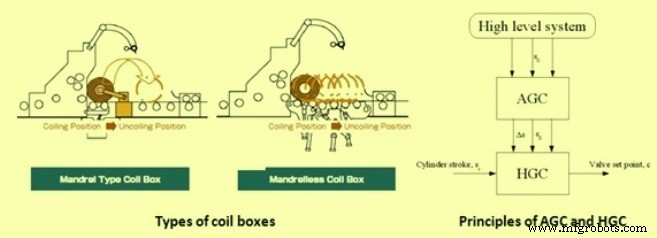
Fig 1 Tipos de caixas de bobinas e princípios de AGC e HGC
- Controle automático de bitola (AGC) e controle hidráulico de folga (HGC) – O controle da folga entre os cilindros de trabalho, ou seja, da espessura da tira, é feito em duas etapas com dois módulos de controle (Fig 1). O primeiro módulo é chamado AGC enquanto o segundo módulo é conhecido como HGC. O AGC recebe pontos de ajuste de espessura de um sistema de nível superior. Ele calcula e compensa coisas como desgaste do rolo, expansão térmica nos rolos, estiramento do cordão e outras quantidades imensuráveis que afetam a folga. Uma medição de espessura é feita durante os passes, que é usada pelo AGC. O feedback de espessura é passado através de um controlador PI e adicionado ao desvio total da folga. Pode ser visto como compensação de erro do modelo. Esta compensação altera a referência de posição do cilindro no HGC. Não há controle de feedback de espessura no HGC. HGC controla a folga entre os dois rolos de trabalho. O HGC usa os pontos de ajuste de nível mais alto como valores de referência de intervalo de rolagem. As medições dos transdutores de posição nos cilindros e a compensação de corrente são usadas para calcular a folga do rolo. O HGC é controlado por posição e usa a referência e a folga real para controlar a espessura da tira.
- Controle automático de largura (AWC) – Excelente precisão de largura pode ser alcançada fornecendo o sistema AWC hidráulico na biseladora vertical da extremidade da cabeça à extremidade da tira. O sistema de controle de largura operado por cilindro hidráulico é usado. Este sistema funciona como controle de curso curto para a extremidade dianteira e traseira da tira e como um sistema AWC para o resto da tira. As servoválvulas eletromecânicas controlam com precisão a posição do ceylinder hidráulico.
- Dobragem do rolo de trabalho – Em um laminador de tiras a quente, os rolos de apoio têm um diâmetro grande para suportar o rolo de trabalho e evitar que ele dobre. Mas, na prática, até mesmo os rolos de apoio são dobrados quando a força na caixa do mancal se torna maior. Isso faz com que a força aplicada no rolo de trabalho seja maior perto do alojamento do mancal e menor no meio do rolo. A tira, por outro lado, opera com uma força reativa. Isso atua no meio do rolo. Isso, por sua vez, dobra o rolo de trabalho e afeta o perfil da tira (Fig 2). O sistema de dobragem do rolo de trabalho permite a modelagem do perfil da tira aplicando uma força contrária no alojamento do rolamento do rolo de trabalho. A aplicação de uma grande força de flexão torna a tira mais plana. A força de flexão muda constantemente e a força de referência é calculada em função da força de rolamento. Quatro cilindros hidráulicos de cada lado geram a força.
- Coroa de variação contínua (CVC) – Outra maneira de alterar o perfil da tira é usar rolo com perfil. A folga entre os rolos pode ser alterada pelo deslocamento axial dos rolos (Fig 2). A técnica CVC também é conhecida como técnica de deslocamento de rolo. A técnica CVC tem uma dinâmica mais lenta, mas um alcance mais amplo do que a flexão do rolo de trabalho. Como o CVC e a dobra de cilindros de trabalho se complementam, ambas as técnicas são normalmente usadas nos modernos laminadores de tiras a quente.
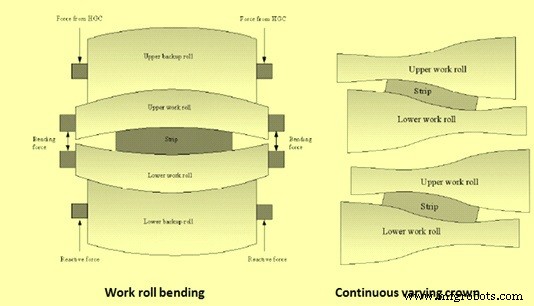
Fig 2 flexão do rolo de trabalho e coroa variável contínua
- Compensação de excentricidade do rolo – A excentricidade do rolo é um distúrbio periódico causado por uma estrutura de rolos de apoio em laminadores e afeta a precisão da espessura do produto. Ele não pode ser medido diretamente por sensores, portanto, deve ser identificado pela espessura medida ou força de rolo medida. Quando há uma grande diferença de diâmetros entre o rolo de apoio superior e inferior, o desempenho do controle de excentricidade do rolo usando sinais de feedback de força ou espessura do rolo não tem sido tão bom. Também tem sido difícil para o controle ser aplicado a partir da extremidade da cabeça porque é necessário identificar a excentricidade do rolo durante a laminação. O controle de compensação de excentricidade de rolagem identifica a excentricidade de rolagem superior e inferior, respectivamente, a partir de um sinal de força de rolagem e inicia o controle da extremidade da cabeça.
- Lubrificação do cilindro de trabalho – Ao lubrificar o cilindro dos cilindros de trabalho, os defeitos da superfície são evitados e o desgaste do cilindro é reduzido. As vantagens de aplicar meios de lubrificação nos cilindros de trabalho incluem evitar o acúmulo de incrustações e o descascamento da superfície do cilindro de trabalho com um mínimo de óleo de laminação, melhor qualidade da tira, custos operacionais reduzidos, tempos de utilização estendidos do moinho, limites estendidos do moinho e consumo de energia reduzido.
- Sistema de resfriamento intensivo e mascaramento de bordas – O sistema de resfriamento de tiras resfria a tira laminada pelo laminador de acabamento e está localizado na mesa de saída entre o laminador de acabamento e o rebobinador. O sistema de resfriamento é projetado como um sistema de fluxo laminar na parte superior e inferior, incorporando um sistema de tanque principal do lado da linha. A zona de resfriamento é dividida nos bancos de resfriamento necessários, que consistem em bancos de resfriamento intensivo para resfriamento mais rápido, bancos de resfriamento normais para resfriamento regular e bancos de resfriamento para controle preciso da temperatura para atingir os padrões de resfriamento desejados e temperaturas de bobinagem para fase dupla e aços de viagem. A combinação de resfriamento laminar e sistema de mascaramento de bordas evita o resfriamento excessivo das bordas da tira, minimizando assim as diferenças de tensão ao longo da largura da tira.
- Enroladores de descida avançados – Uma guia de entrada ajustável hidraulicamente é fornecida na extremidade terminal da mesa de outroler de corrida serve para centralizar o estribo antes de entrar no bobinador de descida. A tira, rodando na velocidade de laminação final, é seguramente agarrada pela unidade de rolo de pressão e direcionada para o mandril da bobina. As características da bobinadeira descendente incluem rolos de empacotamento operados hidraulicamente, espalhamento hidráulico controlado do mandril, calibração automática e ajuste hidráulico exato da folga e dos rolos do mandril, limitação controlada das forças do rolo de empacotamento em função das dimensões da tira e material e tira tensão na cabeça da tira acumulada após dois a três enrolamentos.
Processo de manufatura
- Cachorro-quente
- Balão de ar quente
- Arco de violino
- Sprout:Moderna plantadeira autorregulada interna
- Como fazer uma matriz NeoPixel
- Jukebox moderna
- Têmpera a Seco de Coca-Cola Quente
- Decapagem de tiras laminadas a quente de aço carbono em linhas de decapagem
- Uma introdução à bomba de água quente
- O que é uma broca de moinho de bancada?