Automação na Siderurgia
Automação na indústria siderúrgica
O aço é uma liga de ferro geralmente contendo menos de 1% de carbono. Por suas propriedades versáteis e suas possibilidades de reciclagem, o aço é o material básico para o desenvolvimento sustentado na sociedade industrial moderna. Ele fornece uma ampla gama de usos em quase todos os setores importantes da indústria, como fabricação de aparelhos e máquinas, construção de pontes e edifícios, engenharia de energia e meio ambiente e indústrias automotiva e de transporte.
O aço é e continuará sendo o material de engenharia e construção mais importante da era moderna. A indústria siderúrgica é um setor industrial muito dinâmico. Outras medidas estão em andamento para aumentar a eficiência de recursos e energia, reduzir as emissões e fornecer ambientes de trabalho seguros e saudáveis. Para conseguir isso, a indústria siderúrgica deve se destacar no ambiente de hoje, que é um ambiente de negócios altamente dinâmico e interativo. Condições de mercado, novos requisitos de produtos, custos de matérias-primas e gerenciamento de processos, etc., todos afetam o desempenho da indústria siderúrgica.
A indústria siderúrgica é uma importante força motriz da economia e, portanto, deve ser gerida de forma eficiente. Além disso, precisa de investimentos pesados e, portanto, é essencial que opere economicamente para mantê-lo saudável. Seus produtos são indispensáveis para outras indústrias, como automotiva e construção. Qualidade, confiabilidade e eficiência econômica na produção de produtos siderúrgicos só podem ser garantidas por meio de instalações de fabricação automatizadas.
Os processos da indústria siderúrgica são altamente intensivos em energia e compostos por muitas operações unitárias complexas. O minério de ferro e o carvão precisam ser pré-processados antes de serem alimentados em um reator, e os metais líquidos de diferentes reatores precisam ser manuseados com cuidado. Além disso, o aço líquido deve ser convertido em forma sólida e depois laminado em produtos acabados. Cada uma dessas operações tem uma participação na qualidade do aço produzido, e também precisa de monitoramento constante. Existem muitos sistemas disponíveis para monitorar e controlar a operação de cada unidade. Os sistemas de controle de processo na indústria siderúrgica variam de controle manual a controles totalmente automatizados.
Os processos na indústria siderúrgica precisam ser equipados com dois tipos de tecnologias:(i) tecnologias básicas e (ii) tecnologias avançadas.
As tecnologias básicas são aquelas que são fundamentais para os processos de produção. Geralmente são as tecnologias tradicionais desenvolvidas com base em princípios científicos. São aquelas tecnologias que são necessárias para a produção do produto no nível de produtividade e eficiência necessários com baixo consumo específico de insumos. As tecnologias básicas normalmente consistem em tecnologias químicas, mecânicas, metalúrgicas ou de produção.
As tecnologias avançadas de fabricação de hoje usam as cinco ferramentas tecnológicas a seguir para ter o maior potencial de influenciar a qualidade dos produtos, além de influenciar na melhoria da produtividade e eficiência do processo.
- Automação – Uma nova geração de sistemas de automação são utilizados no processo de produção que vinculam o processo de fabricação com sistemas de controle remoto frequentemente através da tecnologia da informação. Esses novos sistemas de automação são equipados com sensores remotos de contato ou sem contato e interfaces padronizadas, e, em alguns casos, eliminam totalmente as interferências humanas. Isso ajuda a eliminar as deficiências de qualidade nos produtos introduzidos por meio de erros humanos. A automação também permite a fabricação do produto com melhores precisões e tolerâncias estreitas de maneira econômica.
- Engenharia de materiais computacionais integrada – Esta ferramenta cria modelos de computador para simular as propriedades dos produtos. Ao equipar os processos de produção com estes modelos, não só ajuda na produção de produtos que atendem aos requisitos de especificação, mas também reduz as taxas de rejeição de produtos. Esta ferramenta ajuda a estabilização do processo muito rapidamente durante o início do processo de fabricação. Também reduz a carga de teste do produto após sua fabricação. Isso também ajuda o processo de produção de produtos de maneira melhor, mais rápida e mais barata.
- Fabricação digital – A digitalização dos controles durante o processo de fabricação ajuda a identificar e corrigir automaticamente as falhas dos produtos em cada etapa do processo produtivo. Isso, por sua vez, melhora as taxas de aceitação do produto.
- Internet industrial e automação flexível – Com a ajuda dessa automação, o hardware do processo pode ser conectado para que os equipamentos e as máquinas possam se comunicar entre si e ajustar automaticamente a qualidade do produto com base nos dados gerados pelos sensores. >
- Processo de manufatura aditiva – Esta é uma ferramenta muito avançada que cria objetos tridimensionais com base em modelos digitais depositando sucessivamente camadas finas de materiais. O uso desta ferramenta elimina totalmente a produção de produtos fora das tolerâncias dimensionais.
Automação, embora seja uma parte das tecnologias avançadas, mas muitas vezes os termos tecnologias avançadas e automação são usados de forma intercambiável. Neste artigo também ambos os termos são usados de forma intercambiável.
As tecnologias avançadas de fabricação ajudam a atender a várias necessidades da indústria siderúrgica. Essas novas tecnologias de processo aumentam a produtividade e a capacidade de resposta aos clientes, permitindo que as usinas de aço modifiquem e ajustem os processos de produção de forma rápida e fácil de acordo com os requisitos do cliente. Com isso, as siderúrgicas podem gerar uma maior diversidade de produtos a partir dos processos produtivos. Essas tecnologias avançadas combinam a eficiência da produção em massa com a fabricação personalizada com produtos feitos especificamente para atender às necessidades dos clientes. Isso é um pouco difícil e muitas vezes proibitivamente caro de se fazer usando tecnologias convencionais durante os processos de fabricação.
A aplicação de tecnologias avançadas às tecnologias básicas nos processos de fabricação é uma tendência recente. As aplicações de tecnologia de fabricação avançada têm um grande impacto na qualidade do produto. Os rápidos avanços na tecnologia da informação, sensores e nanomateriais estão reduzindo drasticamente não apenas os custos dos processos de fabricação de ponta, mas também melhorando seu desempenho em grande medida em relação à qualidade dos produtos. Lenta mas seguramente, a digitalização começou a permear todos os aspectos dos processos de produção, desde a engenharia até o gerenciamento da cadeia de suprimentos até o chão de fábrica, o que está tornando os sistemas de produção mais inteligentes e altamente conectados em rede e mais orientados para a qualidade do produto. Isso está ajudando a indústria siderúrgica não apenas a melhorar a produtividade, mas também a se tornar mais responsiva às mudanças nas necessidades dos clientes.
A palavra “Automação” é derivada das palavras gregas “Auto” (próprio) e “Matos” (movimento). A automação, portanto, é o mecanismo para sistemas que “se movem por si só”. No entanto, além desse sentido original da palavra, os sistemas automatizados também alcançam um desempenho significativamente superior ao que é possível com os sistemas manuais, em termos de potência, precisão e velocidade de operação. Assim, a automação é normalmente referida à substituição total ou parcial de uma função anteriormente realizada pelo operador humano.
Historicamente, a automação provou ser uma maneira eficiente de obter uma produção econômica na fabricação, bem como na indústria de processo, como a siderurgia. Em geral, a automação também aliviou os humanos de tarefas pesadas, perigosas, complexas, chatas e demoradas. A automação também tem sido extensiva não apenas no processo de produção real da indústria siderúrgica, mas também em tarefas de suporte (por exemplo, manuseio de materiais, transporte e armazenamento, etc.). Além disso, a automação pode fornecer soluções em situações altamente críticas em que não há tempo suficiente para um operador humano responder e tomar as medidas adequadas ou em outros tipos de situações em que o ser humano se mostra insuficiente em um ou mais aspectos.
Automação é definida como um conjunto de tecnologias que resulta na operação de máquinas e sistemas sem intervenção humana significativa e alcança desempenho superior à operação manual.
A automação consiste em tecnologias eletromecânicas (computadores) aplicadas aos sistemas de processo com a finalidade de controle dos processos de produção para aliviar ou substituir um operador humano. Essa definição é ampla na intenção de automação, mas focada em sua forma – computadores. Os computadores compõem a geração atual de sistemas de controle e serão cada vez mais confiáveis na próxima para realizar o processamento automático de dados e fornecer aos operadores informações cruciais para a tomada de decisão eficaz.
Os sistemas de automação utilizam instrumentos e sensores de campo para a coleta dos dados e sua transmissão para a unidade de processamento que após a análise dos dados envia sinais aos equipamentos de controle com a finalidade de controlar os parâmetros do processo para que estes sejam mantidos dentro dos limites aceitáveis.
Os objetivos da automação incluem o aumento da confiabilidade e disponibilidade operacional das linhas de produção. De fato, a automação é aplicada a sistemas homem-máquina (homem-computador) para diversos fins que incluem (i) melhor desempenho, (ii) maior segurança operacional e (iii) maior economia da força de trabalho. O desempenho dos sistemas pode ser melhorado alocando a um computador funções que os humanos não podem executar devido a limitações inerentes às capacidades físicas e mentais. Por exemplo, processos dinâmicos muito complexos para os operadores humanos responderem manualmente precisam ser realizados por meio do uso de automação. O desempenho do sistema também pode ser melhorado alocando a um computador funções que os operadores humanos podem realizar, mas são inadequadas ou que causam altos níveis de carga de trabalho e estresse.
O papel do sistema de automação na indústria siderúrgica inclui o funcionamento suave, preciso e estável dos processos de produção, basicamente empregados para produzir produtos acabados de aço a partir de matérias-primas/semi-acabados usando energia, mão de obra e equipamentos e infraestrutura. Sendo a indústria siderúrgica essencialmente uma “atividade econômica sistemática”, o objetivo fundamental da indústria é obter lucro que pode ser maximizado pela produção de produtos de qualidade em maiores volumes com menor custo e tempo de produção e, portanto, implantação de sistema de automação na indústria siderúrgica torna-se essencial.
As vantagens da automação incluem (i) controle do processo de produção, (ii) melhoria no processo de fabricação principalmente tornando o processo mais estável garantindo facilidade de operação, (iii) melhoria na produtividade, (iv) redução no ciclo de produção de matérias-primas ao produto, (iv) redução no consumo específico de materiais e energia, (v) melhoria na qualidade do produto, (vi) redução no custo de produção, (vii) melhoria na saúde dos equipamentos , (viii) gestão ambiental e (ix) segurança de operadores e equipamentos. A segurança operacional de sistemas tecnologicamente avançados, muito comuns na indústria siderúrgica moderna, pode ser aprimorada por meio da automação que visa remover erros humanos dos sistemas, substituindo os operadores por máquinas praticamente infalíveis. A automação resulta em maior capacidade e produtividade humana e redução da carga de trabalho e fadiga do operador.
As desvantagens do uso da automação na indústria siderúrgica incluem (i) baixa satisfação no trabalho do operador, (ii) falha do operador em atender a eventos críticos do sistema (vigilância), (iii) dependência excessiva do operador nos sistemas automatizados (complacência), (iv) baixa proficiência dos operadores em caso de emergências que exijam transferência manual (decaimento de habilidade) e (v) perda de conhecimento do sistema do operador. De fato, a administração de algumas siderúrgicas vê a automação como uma redução do status do papel do operador a um botão de pressão, privando-o de usar seu conhecimento e experiência no controle dos processos. Esta armadilha do operador passivo funcionando sob automação causa nos operadores (i) falta de vigilância, (ii) complacência e (iii) perdas em termos de habilidades (manuais) e consciência da situação.
Apesar dos avanços tecnológicos para desenvolver processos de produção automatizados que possam desempenhar funções com mais eficiência, confiabilidade ou precisão ou a um custo menor do que os operadores humanos na indústria siderúrgica, a automação ainda não substituiu os humanos nos processos de produção. Em termos leigos, no entanto, é fácil pensar em sistemas automatizados como não incluindo humanos. No entanto, a maioria desses sistemas “não tripulados”, como operações automáticas de montagem de placas de circuito, envolve operadores humanos em funções de supervisão ou monitoramento.
O controle supervisório que o humano como supervisor pode ser visto como uma ou mais das cinco funções genéricas e interligadas. Essas funções são as seguintes.
- A primeira função do supervisor é planejar o que precisa ser feito em algum período antes que qualquer automação seja ativada.
- A segunda função é ensinar (por exemplo, instruir, comandar, programar) o sistema automatizado com o que ele precisa saber para desempenhar sua função atribuída para esse período.
- A terceira função é ativar a automação e monitorar a ação automática e detectar quaisquer desvios ou falhas.
- A quarta função do supervisor é intervir na ação automática, se necessário, e decidir sobre os ajustes necessários na automação.
- A quinta e última função é avaliar o desempenho e aprender com a experiência observada.
Com a automação, a função atribuída a um operador é a de monitor de sistema. Ele é obrigado a verificar os displays sem tomar nenhuma ação para alterar o estado do sistema, a menos que seja necessário. O único propósito desse monitoramento é determinar se um sistema está funcionando normalmente ou se é necessária a intervenção humana. A decisão de intervir no controle do processo é influenciada por (i) a precisão com que um operador deve perceber os valores das variáveis do sistema, (ii) a probabilidade de perder um evento crítico enquanto se concentra em outras informações, (iii) as recompensas e penalidades associadas a eventos críticos, (iv) a estratégia formulada por um operador, (v) a correlação entre eventos e (vi) o limite abaixo do qual um operador não aborda um evento crítico. Em caso de falha do controle de automação, torna-se necessário que o operador assuma os controles do processo para o qual o operador tem que ter habilidade e o sistema deve providenciar essa assunção do controle.
Sempre há situações na indústria siderúrgica em que o operador como componente do sistema de produção tem que estar envolvido para poder manusear máquinas e equipamentos em situações imprevistas. Consequentemente, tanto os sistemas automatizados avançados quanto os trabalhadores humanos qualificados que trabalham juntos são necessários para alcançar uma produção flexível e eficiente. Robustez e flexibilidade dos processos de produção são, portanto, as questões-chave para a automação. No entanto, como na indústria siderúrgica os processos são muito complexos e também porque a customização do produto aumentou essa complexidade, tornou-se uma exigência que a indústria siderúrgica adote como um maior nível e extensão de automação.
A automação está sempre associada ao controle que é um conjunto de tecnologias que atinge padrões desejados de variações de parâmetros operacionais e sequências para máquinas e sistemas fornecendo os sinais de entrada necessários. Existem algumas diferenças nos sentidos em que esses dois termos são geralmente interpretados em contextos técnicos. Estes são dados abaixo.
- Os sistemas de automação podem incluir sistemas de controle, mas o inverso não é verdadeiro. Os sistemas de controle podem ser partes de sistemas de automação.
- A principal função dos sistemas de controle é garantir que as saídas sigam os pontos de ajuste. No entanto, os sistemas de automação podem ter muito mais funcionalidades, como pontos de ajuste de computação para sistemas de controle, monitoramento do desempenho do sistema, inicialização ou desligamento da planta, agendamento de trabalhos e equipamentos etc.
Os sistemas de automação são essenciais para as siderúrgicas onde a maioria dos processos possui sequências complexas de muitas operações. Por isso, hoje, a automação na indústria siderúrgica tornou-se indispensável, pois desempenha um papel muito especial. Enquanto nos estágios iniciais era usado apenas para controle de processo, hoje ele fornece informações adicionais sobre as condições da planta que auxiliam no planejamento e preparação precisa da manutenção e reparo da planta e equipamentos. Hoje, a automação carrega funções de diagnóstico que são usadas para manutenção baseada em condições. Auxilia no aumento da confiabilidade dos equipamentos e sua disponibilidade para a produção.
A automação da indústria siderúrgica precisa de vários recursos que incluem (i) o rigor dos requisitos de precisão de controle, (ii) a confiabilidade para suportar operação contínua de 24 horas em uma planta onde as operações nunca param, (iii) processamento de informações em massa devido à grande escala de a operação, (iv) o rigor da exigência de alta resposta, e (v) a dificuldade de operações estáveis e “building-in”, devido à complexidade dos processos de fabricação.
A capacidade de um operador humano de controlar um sistema automatizado pode ser diretamente impactada pelo nível de planejamento de tarefas e interação de desempenho mantida com o controlador do computador. Por outro lado, a capacidade do operador de responder e tomar decisões com base nas informações do sistema é normalmente influenciada por vários níveis de automação. Nessas situações, o nível de automação na indústria siderúrgica pode ser (i) manual, que é o controle humano sem auxílio de computador, (ii) apoio à decisão, onde o controle do operador com entrada na forma de recomendações por computador, (iii) consensual, onde o controle por computador as ações, mas o consentimento do operador é necessário para realizar as ações, (iv) monitorado, caso em que o controle do computador é implementado automaticamente, a menos que haja vetos humanos, e (v) automação total onde há controle completo do computador sem interação do operador.
Os sistemas de automação podem ser categorizados com base na flexibilidade e no nível de integração nas operações do processo de fabricação. Vários sistemas de automação que são usados na indústria siderúrgica podem ser classificados da seguinte forma.
- Automação fixa – É normalmente um equipamento de engenharia personalizada e de finalidade especial para automatizar uma sequência fixa de operações. É utilizado na produção de alto volume com equipamentos dedicados, que possuem um conjunto fixo de operação e projetados para serem eficientes para este conjunto. Os sistemas de fluxo contínuo e produção em massa discreta usam essa automação. A automação fixa geralmente está associada a altas taxas de produção e design inflexível do produto de aço.
- Automação programável – Este sistema de automação é usado para uma sequência variável de operação e configuração das máquinas usando controles eletrônicos. No entanto, um esforço de programação não trivial pode ser necessário para reprogramar a máquina ou a sequência de operações. O investimento em equipamentos programáveis é menor, pois o processo de produção não é alterado com frequência. O sistema consiste em equipamentos projetados para acomodar uma classe específica de alterações de produtos. Esse tipo de automação é normalmente usado em processos em lote em que a variedade de tarefas é baixa e o volume do produto é médio a alto e, às vezes, também na produção em massa.
- Automação flexível – Este tipo de automação tem flexibilidade e é usado para fabricar uma variedade de produtos. Neste sistema de automação os operadores dão comandos de alto nível na forma de códigos inseridos no computador identificando o produto e sua localização na sequência e as alterações de nível inferior são feitas automaticamente. Cada máquina de produção recebe configurações/instruções do computador. As máquinas carregam/descarregam automaticamente as ferramentas necessárias e executam suas instruções de processamento. Após o processamento, os produtos são transferidos automaticamente para a próxima máquina. É normalmente usado em oficinas e processos em lote onde as variedades de produtos são altas e os volumes de trabalho são médios a baixos. No entanto, este tipo de automação está associado a menores taxas de produção e produtos que necessitam de trocas frequentes devido à sua dependência da demanda.
- Sistema de automação integrado – denota a automação completa de uma oficina de uma siderúrgica, com todos os processos funcionando sob controle computacional e coordenados por meio de processamento digital de informações. Inclui tecnologias como projeto e fabricação auxiliados por computador, planejamento de processo auxiliado por computador, máquinas-ferramentas de controle numérico computadorizado, sistemas de usinagem flexíveis, sistemas automatizados de armazenamento e recuperação, sistemas automatizados de manuseio de materiais, como robôs e guindastes e transportadores automatizados, programação e controle de produção. Também pode integrar um sistema de negócios por meio de um banco de dados comum. Em outras palavras, simboliza a integração total de processos e operações de gestão usando tecnologias de informação e comunicação.
A automação de usinas siderúrgicas faz uso extensivo de “Tecnologia da Informação” (TI). A Figura 1 abaixo mostra algumas das principais áreas de TI que são usadas no contexto da automação de usinas siderúrgicas.
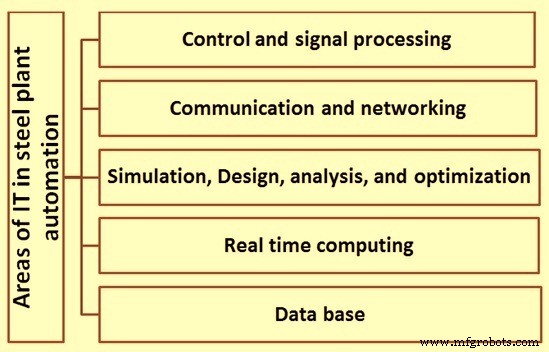
Fig 1 Áreas de TI na operação da siderúrgica
No entanto, a automação da usina siderúrgica é distinta da TI nos seguintes sentidos
- A automação de usinas siderúrgicas também envolve uma quantidade significativa de tecnologias de hardware, relacionadas a instrumentação e detecção, atuação e acionamentos, eletrônica para condicionamento de sinal, comunicação e exibição, sistemas de computação incorporados e autônomos, etc.
- Como os sistemas de automação das siderúrgicas estão cada vez mais sofisticados em termos de conhecimento e algoritmos que utilizam, eles abrangem áreas de operação maiores, abrangendo várias unidades ou toda a siderúrgica, e integram a produção com outras áreas do funcionamento da siderurgia, como gerenciamento de materiais, gerenciamento de relacionamento com o cliente, gerenciamento financeiro, gerenciamento de qualidade do produto, gerenciamento de controle de custos e gerenciamento de vendas etc., o uso de TI aumentou drasticamente na automação da siderúrgica.
Quando comparada às indústrias de mão-de-obra intensiva, a indústria siderúrgica pode ser considerada muito intensiva em capital, portanto, o papel e as aplicações da automação são muitas vezes diferentes. Em vez de linhas de produção totalmente automatizadas, a automação é amplamente utilizada para melhorar a controlabilidade dos processos, qualidade dos produtos e tarefas auxiliares automatizadas, como manuseio de materiais. As características distintivas do sistema de automação da usina siderúrgica incluem o seguinte.
- O sistema de automação do aço é geralmente reativo no sentido de que recebe estímulos do ambiente em que está funcionando e, por sua vez, produz respostas que estimulam o ambiente. Naturalmente, um componente crucial do sistema de automação da usina siderúrgica é sua interface com o meio ambiente.
- O sistema de automação da usina siderúrgica deve ser em tempo real. Com isso quer-se dizer que a computação não só tem que ser correta, mas também deve ser produzida a tempo. Um resultado preciso, que não é oportuno, pode ser menos preferível do que um resultado menos preciso produzido a tempo. Portanto, o sistema de automação deve ser projetado com considerações explícitas sobre o cumprimento dos prazos de tempo de computação.
- O sistema de automação da usina siderúrgica deve ser de missão crítica, no sentido de que o mau funcionamento de qualquer componente do sistema de automação pode trazer consequências catastróficas em termos de perda de equipamentos e até perdas humanas. Portanto, é necessário um cuidado extraordinário durante seu projeto para torná-lo impecável. Apesar disso, mecanismos elaborados são frequentemente implantados para garantir que quaisquer circunstâncias imprevistas também possam ser tratadas de maneira previsível. A tolerância a falhas para emergências devido a falhas de hardware e software é frequentemente incorporada ao sistema de automação.
Níveis de automação
Existem cinco níveis de automações que são comumente empregados na indústria siderúrgica. Esses níveis são dados abaixo.
- Nível 0 – Nesse nível, praticamente não há automação e todo controle dos equipamentos e processos consiste em controle manual.
- Nível 1 – A automação do nível I é restrita aos processos produtivos. Inclui controle de equipamentos e processos de produção. Inclui controlador digital dedicado (DDC). Não inclui rede. A automação de nível 1 utiliza instrumentos de campo cada vez mais modernos, E/S remotas, barramentos de campo e interfaces gráficas. Em diferentes oficinas de aço, os modernos acionamentos CA fornecem novas ferramentas para controle avançado de velocidade e torque. Além disso, a utilização de servo-hidráulicos forneceu novas possibilidades aprimoradas para controlar a produção de aço em uma ampla gama de máquinas de lingotamento contínuo a pequenos manipuladores. Geralmente, os sistemas de controle de nível 1 atuais são capazes de lidar com sistemas MIMO (multientradas e saídas múltiplas) cada vez mais complexos e sistemas em cascata com maior precisão.
- Nível 2 – Este nível de automação inclui o controle supervisório. O controle de supervisão combina as funções de programação de produção e informações de gerenciamento com as funções de controle de processo para formar um sistema de controle hierárquico. Também inclui modelos de processo, manuseio automático de materiais, configuração de ferramentas, embalagem e outros sistemas auxiliares. Ele utiliza modelos de processo físico para complementar o controle de nível 1, fornecendo valores definidos calculados para o controle de processo de nível 1. O monitoramento e diagnóstico de processos também desempenham um papel importante em sistemas de nível 2. Em sistemas grandes, um computador separado pode ser necessário para lidar com cada nível, mas em sistemas pequenos, dois ou mais níveis operacionais podem ser reduzidos em um nível de computador. Os controladores digitais dedicados no nível 1 não requerem intervenção humana, pois suas tarefas funcionais são completamente fixadas pelo projeto dos sistemas e não são interagidas on-line pelos operadores. Todos os outros níveis têm interfaces humanas conforme indicado. Os sistemas de automação de nível 2 oferecem dois recursos principais, a saber (i) controle otimizado rígido de cada unidade operacional da planta com base nos níveis de produção e restrições definidas pelo sistema de planejamento e controle de produção (PPC) de nível 3, fornecendo pontos de ajuste operacionais ideais para o processos de fabricação com esse controle reagindo diretamente a quaisquer emergências que ocorram em sua própria unidade e (ii) melhor confiabilidade e disponibilidade geral do sistema de controle total por meio de detecção de falhas, tolerância a falhas, redundância e outras técnicas aplicáveis incorporadas na especificação do sistema e operação.
- Nível 3 – O sistema de automação de nível 3 contém recursos de monitoramento de status de agendamento e entrega. Inclui funções de planejamento e controle da produção. As funções de planejamento de produção e controle de produção estão incluídas neste nível. Também inclui planejamento de manutenção e análise de dados. Este sistema é um sistema de automação totalmente integrado. Com este nível de automação, o responsável pela operação remota pode visualizar todos os dados. O planejamento de recursos empresariais (ERP) é uma tecnologia popular baseada em software relacionada à automação de nível 3.
- Nível 4 – É como os controles de nível 3, mas sob este nível é possível o controle por satélite de uma área remota. O nível 4 conecta os pedidos dos clientes e o material e faz a alocação de capacidade à produção. Este complexo sistema ERP é usado para gerenciar todo o acompanhamento e documentação da cadeia de suprimentos de pedidos.
A Fig. 2 mostra a hierarquia funcional de um sistema de controle nos diferentes níveis de automação.
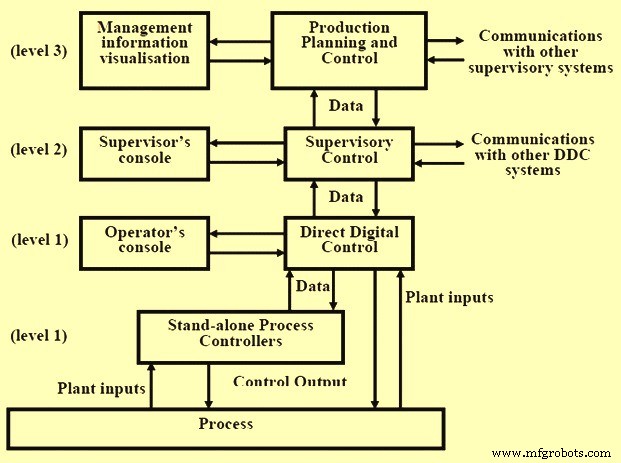
Fig 2 Hierarquia funcional de um sistema de controle nos diferentes níveis de automação
Sistema de controle distribuído
O sistema de controle distribuído (DCS) é a plataforma tecnológica que realiza as automações de nível 1 e nível 2. Os controles de nível 1 e nível 2 podem ser alcançados normalmente por meio de controladores lógicos programáveis (CLPs), sistemas baseados em microprocessadores, bem como controladores programáveis (PCs)/estações de trabalho, conforme necessário. No DCS, cada um dos sistemas de automação da oficina é subdividido de acordo com os requisitos funcionais e abrange as funções de controle de malha aberta e malha fechada das diferentes seções da oficina de produção.
O sistema de controle distribuído vem evoluindo rapidamente desde meados da década de 1980, deixando de ser essencialmente uma substituição de painéis de painel em seu início para se tornar uma informação abrangente da planta, computação e redes de controle totalmente integradas ao fluxo principal das operações da planta. Este progresso foi impulsionado em parte pela revolução tecnológica na tecnologia de microprocessadores e software, bem como pela necessidade econômica.
DCSs baseados em microprocessadores fizeram sua estréia em meados da década de 1970. Inicialmente, eles foram concebidos como substitutos funcionais para a instrumentação do painel eletrônico e foram embalados de acordo. Os sistemas iniciais utilizavam telas de painel discreto semelhantes às suas contrapartes de instrumentação eletrônica. Esses sistemas evoluíram rapidamente, adicionando estações de trabalho baseadas em vídeo e controladores compartilhados capazes de expressar estratégias complexas de controle regulatório e de sequência orientadas a operações unitárias contendo dezenas de elementos funcionais, como PID (proportional-integral-derivative), lad /lag/totalizers, elementos de tempo morto, temporizador decorrido, circuitos lógicos e calculadoras de uso geral
Do início a meados da década de 1980, a indústria de computadores pessoais amadureceu com o sistema operacional de disco IBM PC (DOS) como padrão. Isso deu origem à indústria de software que forneceu pacotes de software baratos de alta qualidade e carregados de recursos. Com isso, tornou-se possível desenvolver um pacote de alarme de controle de varredura e aquisição de dados (SCADA) relativamente barato para uma plataforma de computador pessoal e integrá-lo a esses pacotes de software de embalagem retrátil de uso geral, como planilhas, editoração eletrônica ou gerenciamento de banco de dados e pode-se ter uma alternativa muito econômica para DCS. Devido ao desempenho e às limitações gerais de adequação dessas ofertas de PC, essa abordagem era atraente principalmente em aplicativos não críticos de custo-benefício e onde existia um baixo risco de segurança ou perigo. Este conceito, no entanto, criou uma expectativa e visão de futuro, ou seja, arquiteturas abertas.
O DCS foi desenvolvido ainda mais e agora inclui ferramentas para lidar com aplicações de controle de processo em tempo real, incorporando os pacotes termoencolhíveis de baixo custo em seus sistemas. Such packages include (i) relational database management, (ii) spreadsheet packages, (iii) statistical process control capabilities, (iv) expert systems, (v) computer-based process simulation, (vi) computer-aided design and drafting, (desktop publishing, (vii) object-oriented display management, (viii) windows-oriented display management, and (ix) information exchange with other plant systems.
During the last 1980s and early 1990s the computer industry continued its transformation. Networking of systems into a cohesive whole promised to (again) revolutionize the steel industry, which has barely absorbed the impact of the PC revolution. Software and communications standard began to take hold, making interoperability among disparate computing platforms and application software a near-term reality. The steel organization, including the factory floor, could be moulded into a cohesive whole by making the various departmental systems work cooperatively at an acceptable integration cost. These added new technological features to DCS including (i) open operating system standards, such as UNIXC or POSIX etc., (ii) open system interconnect (OSI) communications model, (iii) client server cooperative computing model, (iv) X-window protocols for workstation communications, (v) distributed relational database management systems, (vi) SQL (Structured query language) access to distributed relational databases, (vii) object oriented programming and platform independent languages , and (viii) computer-aided software engineering.
These characterize the modern DCS technology. DCSs today are distributed computing platforms with sufficient performance to support large-scale real-time process applications. Structurally DCSs traditionally are organized into five major subsystems, namely (i) operations workstations which act as the MMI (machine man interface) and provide visualization capability, (ii) controller subsystems which perform direct digital control, (iii) data collection subsystems, (iv) process computing subsystems for process optimization and supervision, and (v) communication networks. Open system communication standards are enabling DCSs to receive information from a set of similar compatible computing platforms, including business, laboratory information, maintenance, and other plant systems as well as to provide informations in support of applications, such as given below.
- Automated warehousing and packaging line systems so that a complete order can be coordinated from the receipt of raw materials to the shipment of the final product.
- Laboratory information management systems (LIMs), which perform in-process analysis as well as quality assurance inspections.
- Automated production scheduling for a plant accessing the business system and tying into manufacturing resource planning systems and finite-capacity scheduling packages.
Application of DCS systems can be found in some areas of operations in large integrated steel plants.
Processo de manufatura
- Usos do molibdênio na indústria do aço
- Aplicação do Nióbio na Siderurgia
- Tendências em sistemas de E / S de automação de processos
- Importância do Níquel na Indústria de Aço Inoxidável?
- É possível usar a automação de processos para promover o Instagram?
- Como a automação afeta a indústria de manufatura
- Um processo de cinco eixos, 10 elementos de automação
- Adote a automação de processos de fabricação em seu negócio
- Automação na indústria 4.0
- Processo de tratamento térmico do aço