Análise de criticidade:o que é e por que é importante
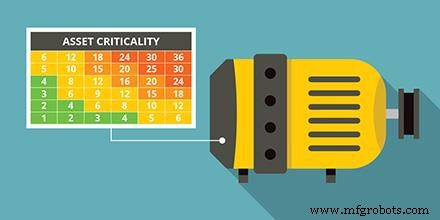
Análise de criticidade é definido como o processo de atribuição de uma classificação de criticidade aos ativos com base em seu risco potencial de falha.
O que é análise de criticidade?
A análise de criticidade é definida como o processo de atribuição de uma classificação de criticidade aos ativos com base em seu risco potencial. Risco é definido como "o efeito da incerteza sobre os objetivos", de acordo com a ISO 31000:2009 - Gestão de Risco - Princípios e Diretrizes . Uma vez que não pode ser verdadeiramente quantificado, o risco, neste caso, é considerado como todas as maneiras possíveis pelas quais os ativos podem falhar e os efeitos que a falha pode ter no sistema e na operação como um todo. Diante disso, a análise de criticidade está intimamente relacionada a uma análise de modos e efeitos de falha (FMEA) e a modos de falha, efeitos e análise de criticidade (FMECA), que serão discutidos posteriormente. Depois que uma análise de criticidade foi realizada, um FMEA normalmente é executado nos 20 por cento principais dos ativos mais críticos.
Qual é o objetivo da análise de criticidade?
Então, por que a análise de criticidade é importante? Você está sempre ouvindo sobre criticidade - fazendo uma análise de criticidade para priorizar ativos para um plano de manutenção produtiva total (TPM), um programa de monitoramento baseado em condições ou uma análise de causa raiz em equipamentos de alta prioridade. A criticidade desempenha um papel em quase todos os tipos de manutenção. Tudo se resume ao risco e ao que torna cada peça do equipamento crítica. A análise de criticidade permite compreender os riscos potenciais do ativo que podem impactar sua operação. Ele garante que a confiabilidade seja avaliada por uma lupa baseada em risco, e não pela opinião de cada pessoa.
De acordo com o Life Cycle Institute, um modelo de análise de criticidade deve abranger várias áreas da sua organização, incluindo:
- Impacto no cliente
- Impacto na segurança e no meio ambiente
- Capacidade de isolar falhas de ponto único
- Histórico de manutenção preventiva (PM)
- Histórico de manutenção corretiva
- Tempo médio entre falhas (MTBF)
- Prazo de entrega de peças sobressalentes
- Probabilidade de falha
Como o modelo de criticidade lida com várias áreas de uma organização, uma análise de criticidade deve ser um esforço de toda a empresa. Incluir departamentos que lidam com operações, engenharia, manutenção, compras e saúde e segurança garante que a análise considere todas as funções da operação como um todo. Você deve entender que o risco pode ser definido de forma diferente entre as várias equipes. Ter uma equipe diversificada fornecendo informações ajuda com a subjetividade da atribuição de risco.
A análise de criticidade também é importante porque pode ser usada em uma variedade de cenários dentro de uma organização. Alguns desses cenários podem ser assim:
- Uma pontuação de criticidade pode ser empregada como uma entrada para ajudar a determinar a classificação de prioridade final para tarefas de manutenção, que por sua vez pode ser usada junto com a prioridade da ordem de serviço.
- Pode ajudar a identificar estratégias de mitigação de risco de alto nível para equipamentos específicos. Por exemplo, isso pode envolver a aplicação de uma técnica de monitoramento de condição a ativos de alta criticidade.
- Pode ajudar a descobrir o número ideal de peças sobressalentes para cada peça do equipamento.
- Ele pode fornecer informações valiosas para discussões de orçamento, portanto, o equipamento de alta criticidade tem maior prioridade para atualizações ou substituição.
- A análise de criticidade ajuda os engenheiros de confiabilidade a concentrar seus esforços e energia nos ativos mais críticos.
Como realizar uma análise crítica
É importante observar que não existe uma abordagem definitiva para realizar uma análise de criticidade. A seguir estão dois métodos amplamente usados, uma abordagem simplista para começar e outro método aprofundado.
Então, por onde você deve começar? Muitas organizações querem apenas saber quais ativos devem ser incluídos em uma avaliação de criticidade. Em vez de presumir que todos os seus ativos são essenciais, faça uma lista dos principais ativos que sua equipe considera críticos e calcule o custo do tempo de inatividade e dos reparos. Você pode se surpreender com os resultados. Por exemplo, você pode ter centenas de motores em movimento constante, o que é bastante crítico, mas o ativo mais crítico é a caldeira que produz vapor para manter esses motores em movimento.
Como o objetivo dessa abordagem é encontrar um bom ponto de partida, vamos dar uma olhada em algumas etapas de ação que você pode executar para iniciar um plano de criticidade.
- Compile uma lista de ativos a serem cortados que não exceda 20 por cento de todos os ativos. A prática recomendada para isso é uma proporção de 5 para 1 ou maior.
- Reúna uma equipe de funcionários das operações, manutenção, engenharia e aquisições da organização para conduzir uma pesquisa do equipamento da planta. Os operadores de equipamento também devem ser incluídos nesta equipe.
- Em seguida, classifique a criticidade dos ativos usando uma fórmula estabelecida. Lifetime Reliability Solutions usa a seguinte fórmula para determinar o impacto financeiro de um ativo: Criticidade do equipamento =Frequência de falha (por ano) x Consequência de custo ($) =Risco ($ por ano) . A consequência de custo nesta fórmula é o custo da produção perdida mais os custos de reparo. Por exemplo, se você tiver muitas máquinas idênticas, o tempo de inatividade da máquina pode ser $ 400 por hora, por máquina.
Agora que você tem uma ideia básica sobre como começar, vamos dar uma olhada em uma abordagem mais aprofundada e simplificada para a análise de criticidade. Este método inclui três etapas:chegar a um acordo sobre a matriz de risco a ser utilizada, montar a hierarquia de seu equipamento e avaliar os riscos de falha de cada ativo.
- Concorde com a matriz de risco. Isso se refere principalmente às matrizes de risco corporativo existentes e como a maioria dessas matrizes pode precisar ser ajustada para incluir uma avaliação de criticidade do equipamento. Duas áreas principais onde modificações podem ser necessárias são concordar sobre os níveis de risco de um nível corporativo e de equipamento e combinar as categorias de risco sobrepostas.
Em um nível corporativo, uma falha que leva a uma perda de $ 1 milhão em receita pode ser considerada pequena ou moderada , mas em um nível operacional de equipamento ou planta, pode ser visto como importante.
Em segundo lugar, as matrizes de risco que incluem categorias separadas para itens como saúde, segurança, meio ambiente e comunidade podem ser combinadas, porque se uma dessas categorias for afetada por uma falha, as outras também serão. A combinação de categorias irá acelerar a análise de criticidade.
- Monte sua hierarquia de ativos. Recomenda-se que seu equipamento ou hierarquia de ativos seja disposto ao longo de linhas funcionais, o que significa que seu chão de fábrica tem um certo número de unidades de processo, essas unidades de processo são compostas de seus próprios sistemas de equipamento e cada um desses sistemas é composto de peças de equipamento. Isso permite que você execute uma análise de criticidade muito mais rápido do que se sua hierarquia de ativos fosse organizada por linhas de classe de equipamento. Mesmo que seus ativos já estejam organizados ao longo de linhas funcionais, eles ainda devem ser revisados para garantir que nada esteja fora de linha. Ter uma hierarquia devidamente montada no início acelera a análise de criticidade posteriormente.
- Avalie os riscos de falha de cada ativo. Ao avaliar os riscos de falha para ajudar a determinar a criticidade do equipamento, considere os seguintes pontos:
- entender que o risco está relacionado a eventos, não a equipamentos;
- escolha apenas um evento - o evento de resultado máximo razoável (MRO);
- olhe apenas para a dimensão com o nível de risco mais alto; e
- comece no topo da hierarquia e vá descendo.
Em segundo lugar, cada peça do equipamento pode ter uma miríade de eventos de falha possíveis, e os riscos associados a cada um desses eventos são diferentes. Seria extremamente demorado tentar identificar todos esses eventos possíveis. Vários consultores e especialistas em confiabilidade recomendam a escolha de apenas um evento - aquele que melhor retrata o resultado máximo razoável (MRO) em termos de risco para aquele equipamento específico. Isso significa que você deve procurar um evento que seja mais provável e em que o risco geral seja determinado como o mais alto.
Essa determinação deve ocorrer em um ambiente do tipo workshop, já que indivíduos de diferentes departamentos terão opiniões diferentes sobre o evento de MRO. Incluídas nesta discussão devem estar as pessoas que conhecem melhor o equipamento e aquelas que entendem as consequências de uma falha de uma perspectiva de negócios.
Em terceiro lugar, considere avaliar apenas uma dimensão de risco - aquela com o nível de risco mais alto - para evitar perda de tempo. Conforme mencionado anteriormente, olhar cada evento individualmente geralmente acaba sendo uma perda de tempo, pois muitos afetam diretamente os outros. Freqüentemente, é bastante óbvio qual dimensão de risco vem com o maior nível de risco. Por exemplo, se você está avaliando a criticidade de uma válvula de alívio de pressão em uma usina de gás natural, os riscos associados à segurança são o que você examinará (incluindo o impacto ambiental e na comunidade). Se você estiver avaliando um componente que fornece eletricidade para operar os equipamentos da planta, provavelmente considerará o impacto econômico dessa falha.
Finalmente, para garantir que sua abordagem de análise de criticidade seja simplificada e eficiente, comece no topo da hierarquia do equipamento e vá descendo. A melhor coisa sobre essa abordagem é, pela lógica, qualquer ativo ou equipamento no nível inferior da hierarquia não pode ter uma classificação de criticidade mais alta do que o ativo acima dele. Em outras palavras, assim que você identificou um equipamento em uma das categorias mais baixas de sua hierarquia, onde as classificações de criticidade são baixas, qualquer item abaixo deste equipamento também deve pertencer à mesma categoria, eliminando a necessidade de análise sua criticidade. Como você pode imaginar, isso enfatiza a importância de construir sua hierarquia corretamente desde o início.
Visualização da análise crítica
Quando se trata de definir visualmente as classificações de criticidade, você descobrirá que existem muitas teorias sobre a melhor maneira de fazer isso. Uma das abordagens mais comuns é usar uma grade de 6x6, que representa a probabilidade de uma falha em relação à gravidade da falha, resultando em um número de prioridade de risco (RPN).
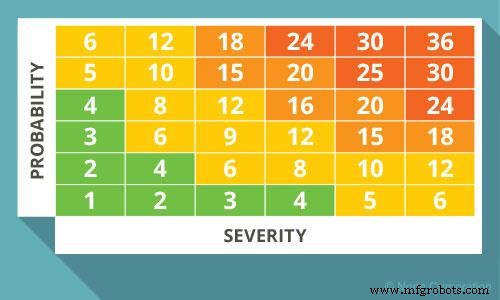
Talvez uma abordagem mais comum seja avaliar todas as categorias principais (operacional, saúde, segurança e meio ambiente, confiabilidade, etc.) individualmente para descobrir o pior caso de falha. Este tipo de análise fará com que os membros da equipe atribuam a cada consequência um número de risco, que é então adicionado ou multiplicado contra cada um, dando um RPN final. A maioria das organizações usa uma pontuação de criticidade derivada de uma classificação definida de 0-6 a 0-10 para cada categoria, com 0 sem impacto e 6 (ou 10) com maior impacto. Por exemplo, se você está classificando o risco de impacto de segurança, saúde e meio ambiente de um ativo, pode definir o impacto que uma falha teria com base no seguinte:
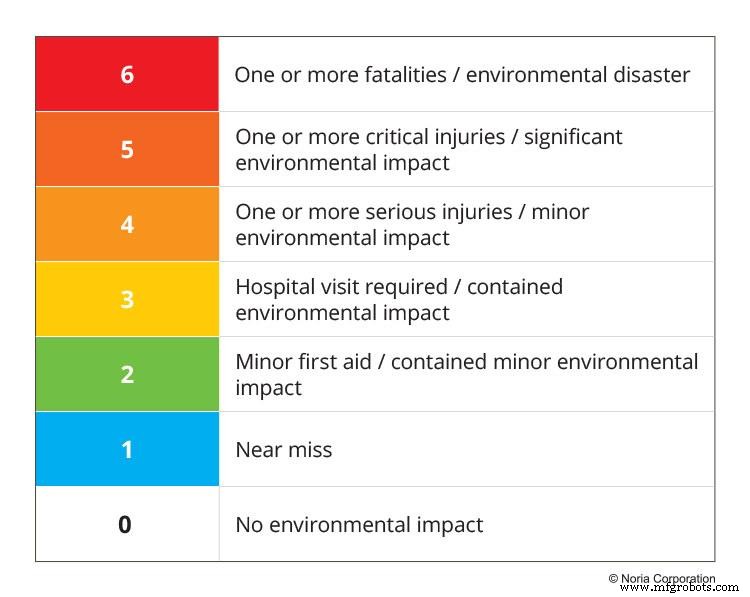
Essa forma de realizar e visualizar uma análise de criticidade deve ser feita em duas fases. A primeira fase é a análise inicial de uma equipe multifuncional com informações das operações; manutenção; aquisição de engenharia; e meio ambiente, saúde e segurança (EH&S). A segunda fase é manter o processo de análise perene ou manter o processo de análise de criticidade ao longo do ciclo de vida do ativo. Isso ajuda a descobrir quando o risco foi mitigado ou se há alguma mudança significativa em cada ativo.
A criação de um visual para o seu processo de realizar uma análise de criticidade e determinar as classificações finais de criticidade pode ser feita em 10 etapas:
- Etapa 1: Escolha as características pelas quais você deseja avaliar cada ativo. Essas características devem abranger vários aspectos do negócio, como o impacto sobre os clientes, o impacto EH&S, a capacidade de isolar e se recuperar de falhas de ponto único, histórico de manutenção preventiva, histórico de manutenção corretiva, etc.
- Etapa 2: Pese cada característica usando uma escala de 0 a 10 para retratar a importância para o negócio. Você também pode usar uma escala maior (quanto maior a escala, mais fácil será identificar ativos críticos), mas a escala não deve exceder 100.
- Etapa 3: Defina cada descrição de característica na escala para precisão.
- Etapa 4: Liste (ou importe) sua hierarquia de ativos.
- Etapa 5: Defina a função principal de cada ativo para identificar uma falha de ponto único.
- Etapa 6: Analise o efeito que uma falha de ponto único teria para cada ativo em todas as características.
- Etapa 7: Calcule a classificação de criticidade para cada ativo dividindo a pontuação bruta (soma de todas as características) pelo total de pontos ponderados possíveis, multiplicado por 100.
- Etapa 8: Identifique os 10-20 por cento principais dos ativos críticos.
- Etapa 9: Revise sua análise e encontre as características que tornam cada ativo crítico.
- Etapa 10: Finalmente, identifique os ativos que são mais significativos para áreas importantes do negócio, como confiabilidade, custo, valor de reposição, desenvolvimento de plano de manutenção, etc.
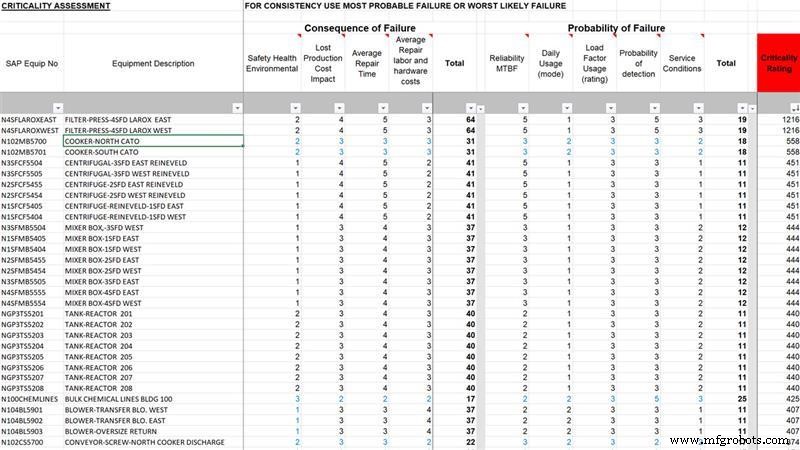
Análise de criticidade:a abordagem FMECA
Modos de falha, efeitos e análise de criticidade (FMECA) foi desenvolvido no final dos anos 1940 pelos militares dos Estados Unidos para fazer a transição de uma abordagem de "identificar a falha e corrigi-la" para uma abordagem de "antecipar a falha e evitá-la". Esta metodologia foi posteriormente padronizada e publicada como um padrão militar:MIL-STD_ 1629A. O FMECA envolve análise quantitativa de falhas, o que significa que usa quantidades e números para avaliar o risco e o potencial de falha.
FMECA e FMEA são ferramentas intimamente relacionadas usadas para realizar uma análise de criticidade; um é uma ferramenta qualitativa (FMEA) que analisa cenários "e se", enquanto o outro (FMECA) é a ferramenta quantitativa que considera RPNs. Utilizando FMEA com FMECA, você pode realizar uma análise de criticidade para garantir que certas áreas do negócio, como design, operações e custos, sejam otimizados.
A parte FMEA desta abordagem de criticidade envolve a definição do sistema, construção de limites do sistema e diagramas de parâmetros, identificação de modos de falha, análise de efeitos de falha, determinação da causa raiz dos modos de falha e fornecimento dos resultados para a equipe de projeto. A porção FMECA inclui a transferência de tudo o que foi aprendido do FMEA para o FMECA, classificando os efeitos da falha por gravidade, realizando cálculos de criticidade, classificando a criticidade do modo de falha e determinando os itens de maior risco, tomando ações para mitigar a falha e documentando o risco restante e acompanhando a eficácia da ação de correção .
A realização de uma análise de criticidade usando a metodologia FMECA fornece valor no departamento de design e desenvolvimento, operações e benefícios de custo, incluindo:
- Benefícios de design e desenvolvimento incluem maior confiabilidade dos ativos, melhor qualidade do equipamento, maiores margens de segurança e uma diminuição no tempo de desenvolvimento e redesenho.
- Benefícios operacionais incluem uma maneira mais eficaz de reduzir custos, programas de manutenção preventiva e preditiva otimizada (PdM), análise de crescimento da confiabilidade durante o desenvolvimento do produto e uma diminuição no desperdício e operações sem valor agregado ou aumento dos princípios de manufatura enxuta.
- Custo benefício incluem a capacidade de mitigar ou reconhecer falhas antes que elas aconteçam, quando são mais baratas de consertar, custos de garantia minimizados e vendas aumentadas devido à satisfação do cliente.
Por ser bastante demorado para ser colocado em prática, a abordagem FMECA geralmente não é o método "básico" para conduzir uma análise de criticidade; no entanto, alguns grupos de consultoria de confiabilidade têm recursos para ajudá-lo, caso sua organização escolha esse método.
Análise de criticidade:o resultado final
A análise de criticidade é uma ótima ferramenta para identificar a prioridade das tarefas de manutenção. Uma boa maneira de ver isso é que a prioridade da tarefa de manutenção deve ser estabelecida pelo nível de risco que vem com a não execução dessa tarefa. Coincidentemente, este nível de risco associado a não realizar uma tarefa de manutenção particular é determinado pelas consequências da falha potencial que poderia acontecer se a tarefa não fosse concluída e a probabilidade de que a falha ocorra se a tarefa não for realizada em um determinado Tempo.
Depois de obter suas classificações de criticidade, uma análise de criticidade pode ajudá-lo a escolher uma estratégia de mitigação de risco adequada que pode ser aplicada a cada ativo. Por exemplo:
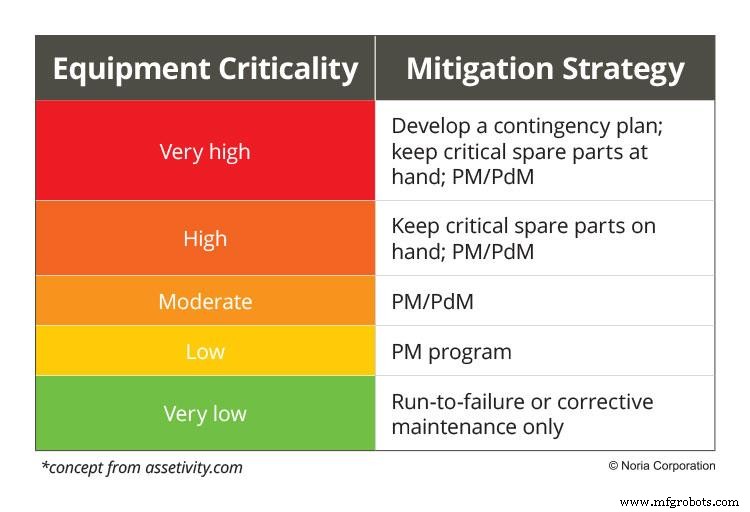
Manutenção e reparo de equipamentos
- Manutenção autônoma:o que é e por que é importante
- O quê, por quê e como usar a chave inglesa
- Análise de criticidade:O que é e como é feito?
- Limitador de torque:o que é e por que é importante para equipamentos mecânicos?
- O que é otimização de armazém, por que é importante?
- O que é manutenção sustentável e por que é importante?
- O que é certificado ISO e por que é importante?
- O que é o GBA? E por que isto é importante?
- O que é retificação de superfície e por que é importante?
- O que é potência e por que ela é importante?