Manutenção baseada em condição:um guia completo
Condição- manutenção baseada (CBM) é uma estratégia de manutenção que monitora a condição em tempo real de um ativo para determinar qual manutenção precisa ser realizada.
O que é manutenção baseada em condição?
A manutenção baseada na condição (CBM) é uma estratégia de manutenção que monitora a condição em tempo real de um ativo para determinar qual manutenção precisa ser executada. Ao contrário da manutenção preventiva, que usa coisas como manutenção baseada no calendário ou outros meios para determinar quando agendar e realizar a manutenção, a manutenção baseada na condição determina que a manutenção só deve ser feita quando esses indicadores em tempo real mostrarem irregularidades ou sinais de desempenho decrescente.
O objetivo da manutenção baseada em condições é monitorar continuamente os ativos para detectar falhas iminentes, de forma que a manutenção possa ser programada de forma proativa antes que a falha ocorra. A ideia é que esse monitoramento em tempo real dê às equipes de manutenção tempo suficiente antes que ocorra uma falha ou o desempenho caia abaixo do nível ideal.
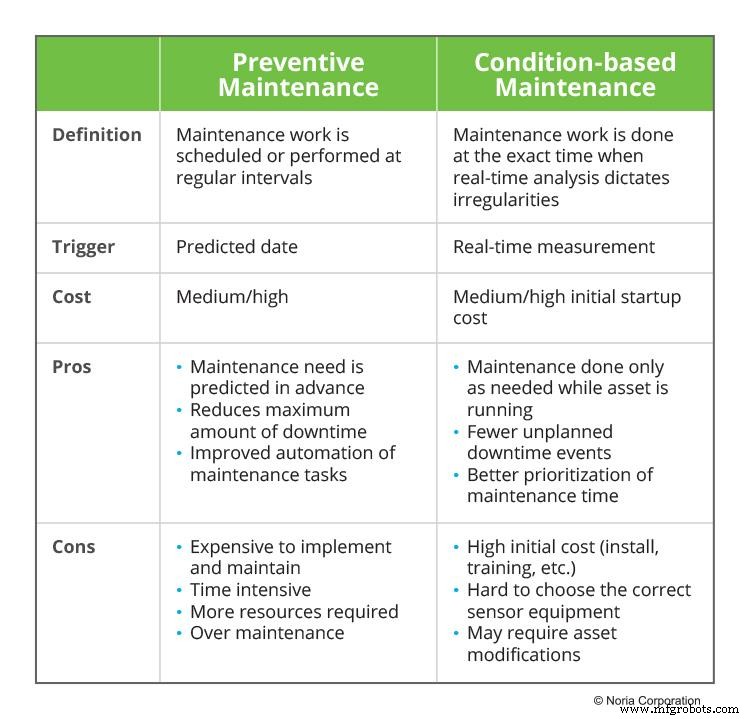
O uso de sensores e leituras pontuais são as formas mais comuns de coleta de dados em tempo real para análise. Por exemplo, sensores podem ser instalados em um equipamento rotativo para monitorar sua vibração. Com o tempo, conforme os componentes móveis se degradam e começam a sair do alinhamento, a vibração aumenta, que é captada pelos sensores. Os sensores instalados podem ser predefinidos para alertar a equipe de manutenção quando as vibrações atingirem um determinado limite.
Embora a manutenção baseada na condição possa ser usada na maioria dos equipamentos, esse equipamento deve atender a certos critérios para que o CBM seja eficaz. Primeiro, deve haver uma condição monitorável. Em outras palavras, se o desempenho da máquina não pode ser medido, como você pode saber se há uma mudança no desempenho? Você também precisa ser capaz de ver as mudanças no desempenho com antecedência suficiente, para que a manutenção possa ser realizada antes que o ativo falhe ou diminua na produção.
A criticidade do ativo é outro critério que você deve considerar antes de utilizar a manutenção baseada em condições. Você obterá o melhor retorno sobre o investimento (ROI) usando CBM em seus ativos mais críticos. Fazer uma análise de criticidade para classificar quais peças do equipamento têm maior probabilidade de falhar e o impacto que a falha terá em sua operação é uma etapa vital antes de realizar a manutenção baseada na condição. É importante dimensionar os ativos mais críticos para baixo.
Finalmente, a manutenção baseada em condições é tão eficaz quanto os processos e sistemas usados para analisar os dados. As equipes de manutenção devem ser capazes de coletar dados de desempenho e analisá-los adequadamente para tomar decisões inteligentes e oportunas com base nos resultados.
Tipos de manutenção baseada em condição
Uma das maiores vantagens da manutenção baseada em condições é que ela não é invasiva, o que significa que os dados em tempo real estão sendo coletados enquanto a máquina ainda está funcionando, sem ajustar a maneira como ela opera. Você pode escolher coletar dados em determinados intervalos ou continuamente por meio de coisas como sensores, inspeção visual ou testes programados. Vamos dar uma olhada em alguns dos tipos mais comuns de técnicas de monitoramento baseadas em condições usadas no CBM.
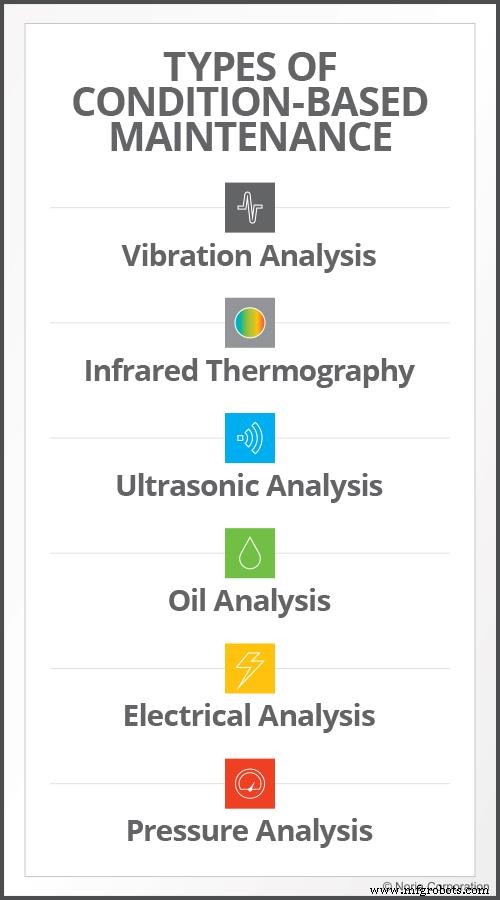
- Análise de vibração. A análise de vibração é definida como o processo para medir os níveis de vibração e frequências de máquinas e usar essas informações para analisar a integridade das máquinas e seus componentes. A análise de vibração pode ajudar a detectar problemas como desequilíbrio, falha de rolamento, folga mecânica, ressonância, eixos tortos e muito mais.
Um exemplo simples pode ser assim:Imagine que você tem um ventilador industrial. Você remove uma das pás da ventoinha e a liga. Como você pode esperar, o ventilador começa a vibrar devido ao desequilíbrio da roda do ventilador. Esta força desequilibrada acontecerá uma vez por revolução do ventilador, produzindo sinais de vibração aumentados. Você também pode ter uma pista de rolamento danificada, fazendo com que um rolo de rolamento gere vibração cada vez que entrar em contato com o estilhaçamento. Portanto, se três rolos de rolamento atingissem o estilhaço por revolução, você veria um sinal de vibração três vezes a velocidade de funcionamento do ventilador.
- Termografia infravermelha. A termografia infravermelha é o processo de usar um termovisor para detectar a radiação vinda de um objeto, convertendo-a em temperatura e exibindo uma imagem da distribuição da temperatura em tempo real. Frequentemente utilizadas com uma imagem de linha de base para comparação, as imagens termográficas infravermelhas podem mostrar de forma clara e fácil quando um ativo está ficando superaquecido. A termografia infravermelha é utilizada para monitorar as condições elétricas e mecânicas dos motores, inspecionar mancais e examinar o isolamento refratário, bem como para verificar os níveis de gases, líquidos e lamas.
As ferramentas de infravermelho incluem termógrafos de infravermelho spot, que são usados para medir a radiação térmica em ativos de difícil alcance ou ativos operando sob condições extremas; sistemas de varredura infravermelha, que examinam áreas ou objetos maiores em uma correia transportadora; e câmeras de imagem térmica infravermelha, que medem a temperatura em vários pontos em uma grande área e criam imagens termográficas bidimensionais.
- Análise ultrassônica. A análise ultrassônica usa som para identificar ativos potencialmente falhos, detectando sons de alta frequência e convertendo-os em áudio e dados digitais. Os métodos de coleta de dados determinam os tipos de falhas detectáveis quando se trata de ultrassom. Você pode ter métodos de contato (via estrutura) ou sem contato (via aérea). Os métodos de contato geralmente são usados para problemas mecânicos como falhas nos rolamentos, problemas de lubrificação, danos na engrenagem e cavitação da bomba. Todas essas falhas emitem um ruído de alta frequência. Os métodos de contato ultrassônico também são úteis para detectar falhas elétricas em motores, pois as barras do rotor soltas ou quebradas podem gerar um padrão rítmico de alta frequência. Por último, os purgadores que estão falhando podem ter vapor constantemente vazando pelas vedações internas, causando um ruído, que é captado pelo ultrassom.
Métodos sem contato (aerotransportados) de medições ultrassônicas incluem vazamentos de pressão e vácuo em sistemas de gás comprimido e uma série de aplicações elétricas. Pesquisas aéreas usam ultrassom para detectar vazamentos em sistemas de gás comprimido. Quando se trata de usar ultrassom aerotransportado para sistemas elétricos, os métodos ultrassônicos podem detectar arco voltaico e corona, mas a termografia não.
- Análise de óleo. A análise de óleo é uma atividade de rotina para analisar a saúde do óleo, contaminação e desgaste da máquina. Um programa de análise de óleo ajuda a verificar se uma máquina lubrificada está funcionando como deveria. A análise do óleo verifica as propriedades do fluido do óleo, respondendo a perguntas como os aditivos certos estão ativos. Os aditivos se esgotaram? A viscosidade está onde precisa estar? A análise de óleo também procura ver se há contaminantes destrutivos no óleo e, em caso afirmativo, ajuda a restringir a fonte provável. Por último, a análise de óleo permite que você analise a presença de partículas produzidas por desgaste mecânico, corrosão ou outra degradação da superfície da máquina.
- Análise elétrica. A análise elétrica é empregada para examinar a qualidade da energia de entrada dos ativos usando leituras de corrente do motor de amperímetros para medir a corrente em um circuito. Isso torna mais fácil para o pessoal de manutenção ver quando um ativo está recebendo uma quantidade anormal de eletricidade.
- Análise de pressão. É vital manter a pressão correta dentro do equipamento para permitir que o fluido, gás ou ar se movam através de uma tubulação ou mangueira hidráulica de maneira adequada. A análise de pressão pode monitorar continuamente os níveis de pressão em tempo real e alertar para quedas ou picos repentinos, permitindo que o pessoal de manutenção responda e corrija os problemas antes que um incidente mais sério ocorra.
Etapas a serem seguidas antes de implementar a manutenção baseada em condições
Conforme mencionado anteriormente, há certas coisas que você pode fazer para obter o máximo de um plano de manutenção baseado em condições.
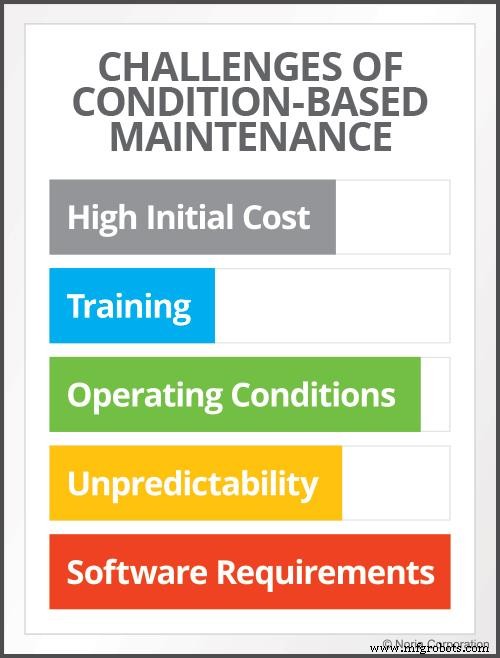
- Garanta uma base sólida. A manutenção baseada na condição anda de mãos dadas com a manutenção centrada na confiabilidade (RCM) porque o RCM ajuda a identificar problemas em potencial com seus ativos e determinar o que você deve fazer para garantir que esses ativos continuem produzindo na capacidade máxima. Ter um conhecimento sólido dos processos RCM ajuda a concentrar seus esforços de manutenção com base nas condições onde eles precisam estar. Na verdade, os especialistas em confiabilidade concordam que um dos maiores problemas que vem com a adoção de um programa de manutenção baseado em condições é a falta de compreensão dos princípios RCM.
- Inclua o pessoal afetado. Depois de estabelecer que todo o pessoal de manutenção possui as habilidades necessárias, inclua-os na análise de criticidade. Incorporar suas informações os torna participantes ativos e lhes dá a oportunidade de usar seus fundamentos RCM de forma eficaz, contribuindo para a implementação da manutenção baseada em condições. Também os ajudará a identificar, mitigar e eliminar os modos de falha.
- Realize uma análise de criticidade. Conforme mencionado brevemente, uma avaliação de criticidade garante que seu programa de manutenção com base na condição seja eficaz. A identificação precisa de ativos como críticos, semicríticos e não críticos pode diminuir a manutenção desnecessária baseada em rota. Em outras palavras, a equipe de manutenção saberá quais ativos são mais críticos e pode realizar verificações nesses ativos primeiro ou com mais frequência do que os ativos não críticos, sem fazer rotas desnecessárias por toda a planta.
A análise de criticidade também ajuda a determinar quais ativos se beneficiarão mais das técnicas de monitoramento baseadas em condições, como vibrações remotas ou sensores acústicos que produzem dados em tempo real que podem ser analisados de outro local. Esses ativos mais críticos são chamados de "atores mal-intencionados" ou os infratores reincidentes em sua lista de ativos. Esses malfeitores se beneficiam mais com o monitoramento contínuo, pois tendem a ter problemas frequentes. Lembre-se de que, depois de concluir uma análise de criticidade, não é incomum descobrir que os ativos que você já considerou críticos não são tão críticos quanto você pensava anteriormente.
- Acompanhamento. Depois de terminar sua avaliação de criticidade, é uma boa ideia implementar um sistema de relatório de falha, análise e ação corretiva (FRACAS) para garantir que sua análise esteja correta e que os ativos mais críticos estejam se beneficiando ao máximo de seu programa de manutenção com base na condição.
Implementando a manutenção baseada em condições:Exemplo da IAEA
Em maio de 2007, a Agência Internacional de Energia Atômica (IAEA) reconheceu a necessidade de começar a mover usinas nucleares de um programa de manutenção preventiva (com base no tempo) para um programa de manutenção com base nas condições, dependendo das condições da planta e dos componentes. Ao reconhecer esta necessidade, a agência desenvolveu e padronizou como implementar um programa CBM em uma publicação intitulada, Estratégias de Implementação para Manutenção Baseada em Condições em Usinas Nucleares . As estratégias descritas usam várias técnicas de monitoramento de condição online e offline para definir como selecionar componentes e parâmetros para monitoramento, quais técnicas de monitoramento e diagnóstico devem ser empregadas, como incorporar critérios de aceitação e muito mais.
Os principais objetivos da IAEA para essa estratégia de manutenção baseada em condições incluem melhorar a disponibilidade por meio da redução das interrupções forçadas; aumentando a vida útil do equipamento, diminuindo o desgaste da reconstrução frequente; detectar problemas à medida que ocorrem; minimizar o potencial de problemas na desmontagem e remontagem; e economia em custos de manutenção, reduzindo custos de reparo, horas extras e peças em estoque.
A estratégia de manutenção baseada em condições da IAEA consiste em uma combinação de inspeção visual e técnicas de monitoramento contínuo em coisas como componentes de limite de pressão, estruturas de contenção, geradores de turbina principal e bombas de refrigeração do reator. Por exemplo, isso poderia envolver diagnósticos online usados no monitoramento do desgaste do mancal de impulso do gerador de turbina. As tecnologias sugeridas de manutenção com base na condição incluem monitoramento de vibração, análise acústica, análise de motor, teste de válvula operada por motor, termografia, tribologia e monitoramento de parâmetro de processo, tudo junto com inspeções visuais.
A IAEA descobriu que o desafio de mudar para um programa de manutenção baseado em condições não estava na falta de conhecimento sobre métodos tecnológicos avançados, mas sim na vontade de mudar a cultura e a gestão para colocá-los a bordo. Compreendendo esse desafio, ele concentrou seu processo de implementação de CBM em torno de quatro elementos:
- Compromisso - A equipe de manutenção deve se comprometer com o processo e sua nova tecnologia. Ela tem que confiar no treinamento e na tecnologia, enquanto a administração precisa se comprometer a adquirir o equipamento e o treinamento adequados para todos os funcionários.
- Participação - Para alcançar o sucesso, é necessária 100 por cento de participação no programa CBM de todos os grupos. Essa expectativa deve ser reforçada pela gerência.
- Abordagem holística - Isso se aplica a todos os sistemas em toda a planta, sem exceções.
- Sustentabilidade - O programa CBM, equipe e equipamentos devem ser mantidos ao longo do tempo para colher os benefícios de longo prazo. Conforme as pessoas entram e saem da organização, o treinamento e os recursos adequados precisam estar disponíveis.
Para garantir que a implementação do CBM fosse retratada de maneira adequada ao pessoal de manutenção, a IAEA reconheceu a necessidade de comunicação e treinamento eficazes. Ele delineou o seguinte processo de pensamento para educar uma usina nuclear e explicando os fundamentos do processo CBM:condições analisadas, métodos escolhidos, métodos implementados e avaliação do projeto. Cada um deles pode ser dividido perguntando "o quê", "por que", "como" e quem ".
- Condições analisadas: Isso inclui a análise de criticidade.
- O quê? - Assegurar o comprometimento da gestão, identificar necessidades, olhar para ambições e expectativas, identificar recursos disponíveis, etc.
- Por quê? - Compreenda a visão geral do que é necessário.
- Como? - Visitas ao local, avaliação do desempenho da empresa.
- Quem? - Especialistas e figuras de autoridade / proprietários.
- Métodos escolhidos: É aqui que os métodos e funções do CBM são decididos.
- O quê? - Escolher as funções e necessidades da equipe CBM; identificar e selecionar métodos.
- Por quê? - Para selecionar métodos que atendam a todas as necessidades encontradas na análise inicial.
- Como? - Consenso dos líderes e equipe de manutenção.
- Quem? - Qualquer pessoa afetada pela implementação do CBM.
- Métodos implementados: É aqui que a discussão é posta em ação.
- O quê? - As funções são desenvolvidas. Certifique-se de que todos os planos e projetos sejam comunicados e compreendidos por meio da realização de treinamento, obtenção de suporte de TI, etc. Crie benchmarks.
- Por quê? - Para melhorar a manutenção e a confiabilidade o mais rápido possível.
- Como? - Treinamento on-the-job, reuniões de projeto de coaching e acompanhamento.
- Quem? - Gerente de projeto, equipe de manutenção e qualquer outra pessoa afetada.
- Projeto avaliado: Isso inclui a análise do processo CBM recém-implementado para garantir que tudo esteja funcionando conforme planejado.
- O quê? - Acompanhar as metas do plano de CBM, discutir experiências e traçar um plano de administração e desenvolvimento.
- Por quê? - Para garantir que o CBM está funcionando conforme o planejado.
- Como? - Auditoria e reunião para acompanhamento e planejamento.
- Quem? - Proprietários, gerentes e líderes de processos.
Desafios da manutenção baseada em condições
Então, qual é o truque? Como acontece com qualquer mudança de processo ou implementação de novo processo, a manutenção baseada em condições apresenta alguns desafios.
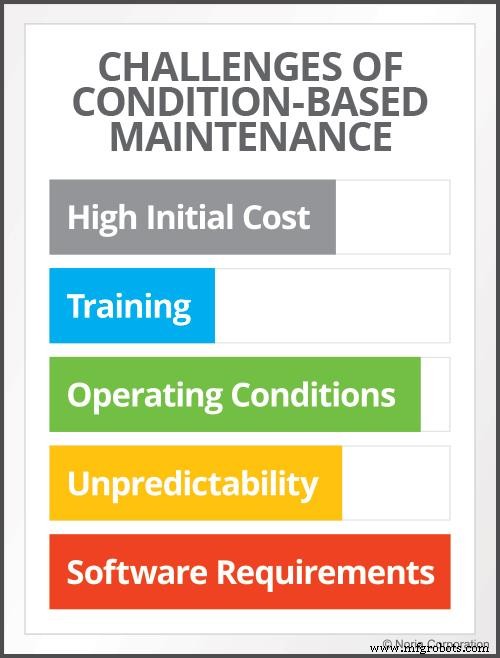
- Custo inicial significativo. Os custos iniciais associados ao CBM tendem a aumentar conforme você executa uma análise de criticidade e descobre onde precisa colocar os sensores. Isso pode ser ainda mais caro se você precisar adaptá-los em ativos mais antigos. Em parte, é por isso que sua análise de criticidade é tão importante, porque ela determina qual equipamento dará o maior ROI. Plantas mais novas ou menores podem não ter o conhecimento local para realizar esse tipo de análise, portanto, é aconselhável trazer um especialista para conduzir uma análise de modo de falha e efeitos (FMEA) e uma análise de RCM, o que terá um custo adicional.
Além disso, a escolha do sensor adequado é crítica. Considere fatores como condições de operação, já que os sensores construídos para resistir a ambientes operacionais adversos geralmente custam mais.
- Treinamento. Agora que você tem sensores para fornecer dados em tempo real e informações sobre as condições do equipamento, deve ter uma equipe que possa analisar esses dados de maneira adequada e rápida. Para cada detecção de falha ou alerta produzido por um sensor, surgem várias perguntas. Uma peça precisa ser substituída? A peça está em estoque? Quanto tempo temos antes que o ativo falhe? Precisamos que o fornecedor faça a substituição?
Lembre-se de que o treinamento é outra despesa e envolve afastar os operadores e outras equipes de manutenção de suas funções operacionais normais. O treinamento também envolve a integração de todos com a mudança e o gerenciamento eficaz da mudança. Conforme aprendido com a IAEA, esta é uma das partes mais difíceis da implementação de um programa de manutenção baseado em condições.
- Condições operacionais. A precisão e o desempenho de seus sensores dependem parcialmente do ambiente em que estão funcionando. Condições operacionais adversas podem causar mau funcionamento ou sensores danificados. Por exemplo, alto calor e umidade podem afetar os eletrônicos, enquanto produtos químicos corrosivos podem danificar sensores e produzir leituras imprecisas.
- Imprevisibilidade. Ao contrário da manutenção programada, o trabalho de manutenção baseado em um programa de monitoramento baseado em condições é imprevisível. Por exemplo, você pode realizar manutenção quando um sensor o alertar. Isso pode causar irregularidades na forma como os custos aparecem em seu orçamento. Por exemplo, se um punhado de ativos exigir manutenção ao mesmo tempo, sua equipe de manutenção deve ser capaz de gerenciar os reparos rapidamente.
- Requisitos de software. Cada sensor instalado coleta grandes quantidades de dados continuamente, por isso é importante ter um moderno sistema de gerenciamento de manutenção computadorizado (CMMS) ou outro software que possa organizar, rastrear, coletar e analisar esses dados. Além de ter o software certo, você precisará considerar a contratação de um terceiro para ajudar a analisar os resultados até que sua equipe esteja totalmente treinada.
Além disso, certifique-se de que sua conexão Wi-Fi pode lidar com a quantidade de dados que está sendo usada e seu plano de armazenamento em nuvem é grande o suficiente para conter os dados armazenados.
Benefícios do monitoramento baseado em condição
Com todos os desafios que vêm com a implementação de um programa de manutenção baseado em condições, você pode estar se perguntando se vale a pena. Embora um programa CBM não seja barato inicialmente e possa levar algum tempo para ser instalado e executado, você pode eventualmente receber muito valor dele. Uma vez implementado corretamente e executado por uma equipe bem treinada, pode levar a muitos benefícios, tais como:
- confiabilidade do sistema aprimorada,
- aumento de produtividade,
- menores custos de manutenção,
- uma diminuição no tempo de inatividade,
- diagnóstico mais rápido de problemas e
- uma redução no tempo entre as manutenções.
O potencial de um programa CBM para um alto ROI atrai muitas organizações devido ao fato de que pode ajudá-las a se manterem competitivas e a operar da maneira mais enxuta possível.
Manutenção e reparo de equipamentos
- Um guia para implementação da manutenção produtiva total
- Guia para KPIs de Fabricação
- O futuro da manutenção:um guia prático para a Indústria 4.0
- Um guia simples para construir um programa de manutenção preditiva
- Como tornar a manutenção baseada na condição mais eficaz
- GE, Boeing implementa o padrão de manutenção com base na condição
- O guia completo para impressão 3D
- Um guia simples para benchmark de manutenção
- Seu guia para gerenciamento de manutenção
- Guia básico para manutenção de minicarregadeiras