Manutenção autônoma:o que é e por que é importante
Manutenção autônoma aumenta a eficiência treinando os operadores para realizar pequenas tarefas de manutenção. Abaixo, discutimos a implementação da manutenção autônoma, sustentando-a e muito mais.
O que é manutenção autônoma?
A manutenção autônoma é definida como uma estratégia de manutenção em que os operadores de máquinas monitoram continuamente seus equipamentos, fazem ajustes e realizam pequenas tarefas de manutenção em suas máquinas. Isso é feito em vez de atribuir um técnico de manutenção dedicado para realizar a manutenção e a manutenção programada regularmente.
A manutenção autônoma é o primeiro pilar da estratégia de manutenção produtiva total. Um operador treinado em manutenção autônoma significa que ele ou ela tem total conhecimento das tarefas de rotina, como limpeza, lubrificação e inspeção. Exige que os operadores se apropriem de seus equipamentos e da área circundante. Isso começa ao colocar a máquina em um padrão "como novo" de limpeza e mantê-la lá, garantindo que os operadores sejam treinados nas habilidades técnicas adequadas para a realização de inspeções de rotina e padronizando um cronograma de inspeção autônomo.
A manutenção autônoma segue dois princípios fundamentais:
- Para evitar a deterioração do equipamento por meio de operação adequada, e;
- Trazendo e mantendo o equipamento no status "como novo" por meio da restauração e gerenciamento adequado.
Muito disso depende de os operadores saberem quando uma atualização da máquina é necessária ou quando uma simples correção pode fazer a máquina voltar a funcionar rapidamente. A manutenção autônoma exige que os operadores dominem habilidades como detecção de anormalidades por meio da compreensão dos componentes da máquina, fazendo melhorias, identificando possíveis problemas de qualidade e determinando suas causas.
Com o objetivo final de uma manutenção produtiva total melhorar a eficácia geral do equipamento de sua organização, há uma razão para isso começar com a manutenção autônoma. Ele libera a equipe de manutenção qualificada de ter que se preocupar com as tarefas de manutenção simples e rotineiras, para que possam se concentrar em projetos de manutenção especializados. Isso leva a várias vantagens, como:
- Aumentar o conhecimento do operador sobre seus equipamentos
- Manter os equipamentos "como novos", garantindo que estejam limpos e lubrificados
- A capacidade de perceber problemas emergentes antes que se tornem falhas
Ao permitir que os operadores da máquina lidem com essas tarefas e inspeções de manutenção de rotina, o OEE é ainda mais maximizado por meio da redução de quebras e deterioração do equipamento.
Como implementar manutenção autônoma
A implementação da manutenção autônoma pode variar um pouco dependendo da operação de cada planta, mas normalmente é dividida em sete etapas.
- Aumente o conhecimento do operador. Os operadores podem ser os mestres em operar sua máquina até a capacidade máxima, mas para que a manutenção autônoma seja eficaz, eles precisam conhecer os meandros de sua máquina. Isso envolve o treinamento de técnicos de manutenção sobre os detalhes técnicos de como os componentes da máquina funcionam e sua finalidade, bem como treinamento em habilidades de resolução de problemas. Em suma, os operadores devem ter quatro habilidades relacionadas ao equipamento:
- Detecção de anormalidades
- Correção e restauração de anormalidades
- Definir as condições ideais do equipamento
- Manter essas condições ideais do equipamento
Uma vez que essas habilidades são revisadas em um ambiente de sala de aula, os operadores podem realizar tarefas básicas de manutenção em suas máquinas enquanto os técnicos de manutenção observam para garantir que tudo seja coberto.
- Limpeza e inspeção inicial da máquina. Esta etapa é onde o equipamento retorna a um estado de "linha de base" com o objetivo de colocá-lo de volta em uma condição de "como novo". Todas as mãos estão disponíveis para esta tarefa, incluindo membros da produção, manutenção, engenharia e operadores. Não apenas o equipamento é completamente revisado e limpo, mas a área circundante também é limpa. O objetivo é restaurar totalmente o desempenho total de cada peça do equipamento, identificando e eliminando sinais de deterioração. As equipes devem procurar e corrigir coisas como:
- Vazamentos
- Parafusos soltos
- Lubrificação adequada
- Rachaduras - aparentes e não aparentes
- Taxas de contaminação de fluidos
- Remoção de material de água e óleo
- Remoção de poeira e sujeira
- Restrição de condutibilidade na fabricação elétrica devido a depósitos de óleo e / ou poeira
- Eliminação de paradas devido ao acúmulo de poeira
É uma boa ideia documentar o protocolo durante a realização dessa limpeza completa para que os problemas possam ser facilmente rastreados e os operadores tenham algo para acessar que contenha etapas fáceis de seguir.
- Remova a causa da contaminação e melhore o acesso. Agora que a limpeza inicial foi feita e todo o equipamento foi restaurado, certifique-se de que ele não volte a ficar em mau estado. Isso pode ser alcançado eliminando todas as fontes possíveis de contaminação e melhorando a acessibilidade para limpeza e manutenção.
Esta etapa também leva a segurança em consideração. Manter uma máquina em funcionamento é perigoso, portanto, melhorar a segurança e a visibilidade por meio de melhores pontos de acesso é fundamental. Uma maneira comum de fazer isso é substituindo as tampas opacas por transparentes para uma visualização rápida e fácil das peças em movimento. A remoção da causa da contaminação pode ser feita por:
- Estabelecer e seguir padrões de limpeza.
- Evitando sujar. Selagem de qualidade e tampas de máquina são bons lugares para começar, mas alguma contaminação só pode ser contida investindo em coisas como bombas ou despoeiramento - pneumaticamente ou por peneiramento a seco.
- Promover a limpeza. Reitere continuamente a limpeza durante as inspeções e manutenção.
- Promoção da organização. Garantir que as ferramentas tenham seu lugar e permaneçam lá aumenta a eficiência.
- Desenvolva padrões para lubrificação e inspeção. Esta etapa pode ser ajustada conforme necessário com base em cada peça do equipamento e seu operador. O estabelecimento de padrões para os operadores sobre limpeza, inspeção e lubrificação deve começar com a documentação atual arquivada e terminar com maneiras aprimoradas de realizar esses procedimentos. Os padrões devem indicar quais componentes devem ser limpos e lubrificados, como eles devem ser limpos e lubrificados e todas as outras responsabilidades de manutenção a serem atribuídas. Os padrões variam com base em se a máquina é considerada não crítica ou crítica.
- Para máquinas não críticas, os operadores são treinados por um engenheiro de manutenção experiente para seguir os padrões estabelecidos. Os operadores podem então estabelecer sua própria rotina.
- Para máquinas críticas, uma equipe de engenheiros de manutenção dedicada aos métodos de manutenção pode ser criada para desenvolver padrões.
Uma vez finalizados, todos os padrões devem ser documentados e disponibilizados para os operadores.
- Inspeção e monitoramento. Agora que eles têm um conjunto de padrões a seguir, os operadores podem modificar sua rotina de manutenção básica para agilizar e melhorar as tarefas. As tarefas de manutenção do operador são rastreadas e comparadas com as programações do próprio departamento de manutenção (geralmente por meio de um sistema de gerenciamento de manutenção computadorizado) para garantir que a duplicação de tarefas não seja um problema. Os operadores realizam as tarefas de manutenção básicas, muitas vezes esquecidas, como verificar os níveis de lubrificação, localizar vazamentos, apertar os parafusos, procurar problemas mecânicos iminentes, como rachaduras e desgaste, e realizar ajustes mecânicos como medições de tensão, regulação do sensor, etc.
- Padronize a manutenção visual. Padronizar a manutenção autônoma e tornar o equipamento "visual" é uma etapa importante para manter a integridade de cada máquina. Como você torna o equipamento visual? Os exemplos incluem a identificação do fluxo de fluidos através de tubos, substituindo coberturas opacas por transparentes sempre que possível, rotulando a direção de abertura / fechamento de válvulas e alavancas e marcando valores operacionais "seguros" ou "normais" em medidores e visores em verde com perigosos níveis em vermelho. Em suma, torne as coisas na máquina o mais óbvias possível.
- Melhoria contínua. Periodicamente, reservar um tempo para recuar e dissecar processos padronizados para ver onde há espaço para melhorias é importante para garantir que você esteja operando com eficiência. Manter bons registros de falhas é vital para fornecer dados que os engenheiros de manutenção possam usar ao projetar máquinas futuras, tornando-as ainda mais fáceis de acessar e manter.
A melhoria contínua também pode resultar de líderes de equipe e técnicos de manutenção que auditam regularmente o trabalho dos operadores. Isso não apenas permite que eles apontem áreas de melhoria, mas também lhes dá a chance de parabenizar os operadores por fazerem um bom trabalho.
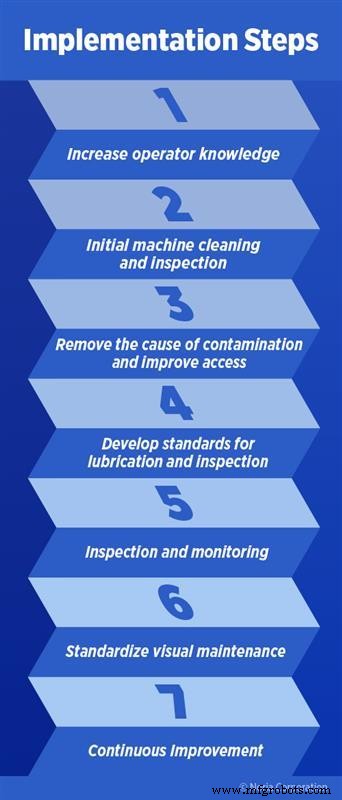
Sustentando a manutenção autônoma
Depois que seus operadores estão devidamente treinados em manutenção autônoma, os procedimentos são padronizados e um sistema de auditoria está implementado, é hora de focar na sustentação desse processo. Existem algumas ferramentas simples que você pode incorporar em sua rotina diária para ajudar a sustentar o processo de manutenção autônomo.
Uma reunião stand-up diária é uma ótima maneira para os operadores e seus gerentes diretos se reunirem todas as manhãs para discutir como as coisas estão indo. Essas reuniões funcionam circulando o círculo e permitindo que cada pessoa discuta o que está funcionando bem e mencione quaisquer problemas que tenham encontrado. Outros itens da agenda incluem lições aprendidas, status da mão de obra, atualizações de gerenciamento e metas e ações do dia. As reuniões diárias podem destacar as dificuldades que os operadores estão enfrentando ou introduzir mudanças da alta administração que precisam ser incorporadas.
Aulas de ponto único são excelentes para auxiliar os membros da equipe a implementar mudanças, ajudando-os a não negligenciar uma etapa da qual estão lutando para lembrar ou comunicar problemas que ocorreram no passado para evitar que ocorram novamente. As aulas de um ponto geralmente são focadas em subsistemas de equipamentos, pontos de segurança e informações operacionais básicas. Um exemplo de lição de um ponto seria a criação de uma etiqueta adesiva a ser colocada diretamente em uma alavanca ou proteção para lembrar um operador que está lutando para se lembrar de girar a alavanca ou uma proteção de volta para a posição de segurança antes de continuar para o próximo procedimento.
Outras etapas para sustentar a manutenção autônoma incluem:
- Rastreie os dados de falha e decomposição: Esses dados são essenciais quando você começa a formar seus procedimentos de manutenção autônoma. Ele não apenas orienta seus operadores sobre quais equipamentos precisam de mais atenção, mas o acompanhamento desses dados ao longo do tempo permite que você acompanhe as melhorias.
- Use métricas: As métricas estabelecidas são a chave para monitorar e rastrear a eficácia geral do equipamento em relação a reparos e desempenho. Analisar padrões de coisas como tempo médio entre falhas e tempo médio para reparo ajuda você a aprender a prever e até mesmo prevenir falhas futuras.
- Desgaste do componente do documento: Use outros meios para controlar o desgaste dos componentes. As tecnologias de manutenção, como análise de óleo, análise de vibração e termografia infravermelha, podem fornecer informações adicionais sobre as falhas do equipamento.
- Padronizar a criação de ordens de serviço: O uso do software de ordens de serviço ajuda a automatizar e controlar a criação de ordens de serviço e os dados de manutenção. O software que está integrado a um sistema de gerenciamento de manutenção computadorizado (CMMS) permite que você crie uma folha de registro de manutenção para cada peça do equipamento em sua planta. Aqui, você pode registrar todas as ocorrências de falha, substituições e quando a condição dos componentes muda.
Benefícios da manutenção autônoma
A maioria das organizações investe pesadamente na contratação, treinamento e desenvolvimento de uma equipe de manutenção altamente qualificada para determinar por que os ativos críticos falham e, em seguida, repará-los. A manutenção autônoma visa liberar esses técnicos da execução de tarefas de baixa qualificação, como inspeções, lubrificação e pequenos ajustes. Entre outros, existem três benefícios principais que a manutenção autônoma traz para uma organização.
O maior benefício é a redução dos custos de mão de obra. Isso inclui a diminuição das ineficiências relacionadas ao tempo de viagem e à espera pela disponibilidade. Por ter um operador sempre próximo a uma máquina, esses tipos de problemas são bastante reduzidos.
Outro benefício da manutenção autônoma é aumentar a disponibilidade de pessoal de manutenção altamente qualificado para que possam atender às necessidades mais críticas. Empregar a manutenção autônoma permite que até mesmo os departamentos de manutenção com equipe mais restrita atendam às questões críticas sem sacrificar a manutenção de rotina.
Por fim, a manutenção autônoma melhora a coesão da equipe, eliminando a mentalidade "nós / eles". Tradicionalmente, o operador tem uma mentalidade "Eu uso", enquanto o técnico de manutenção mantém uma mentalidade "Eu mantenho e conserto". A manutenção autônoma muda isso para uma atitude mais coesa de "nós mantemos" que se encaixa diretamente nos pilares da manutenção produtiva total.
Manutenção e reparo de equipamentos
- A fábrica digital:o que é e por que é importante
- O que é confiabilidade?
- O que é manutenção de fábrica?
- O que é Manutenção de Fábrica?
- O que é Manutenção de Emergência?
- O que é Manutenção Preditiva?
- O que é Manutenção Preventiva?
- O que é manutenção preditiva para guindastes e por que isso é importante?
- O que é um diretor de manutenção e o que ele faz?
- O que é manutenção sustentável e por que é importante?