Confiabilidade Orientada pelo Operador:Quem é o Proprietário dos Equipamentos de suas Plantas?
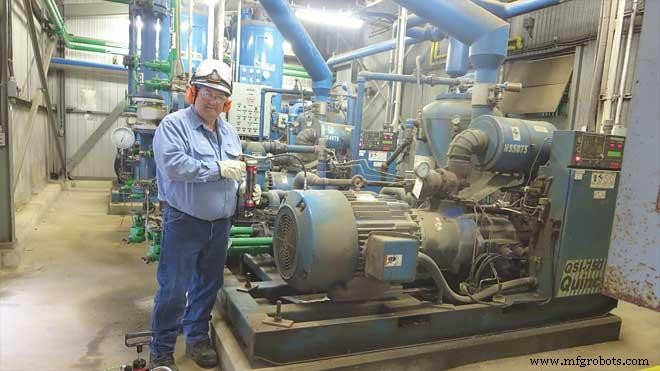
A indústria de papel de hoje é muito diferente da indústria que conhecíamos há cinco anos. O aumento da competição estrangeira e a desaceleração da economia doméstica alimentaram a consolidação da indústria de papel dos EUA.
O fechamento de instalações e a dispensa de funcionários se tornaram comuns e alimentam a mentalidade de “apenas os fortes sobrevivem”, o que forçou as usinas a buscar todas as formas de se manterem competitivas e economicamente viáveis. Como não podemos controlar o preço de mercado ou os custos das matérias-primas na fábrica, somos forçados a buscar internamente por maneiras de melhorar nossos resultados financeiros.
Ao restringir nosso foco às variáveis que estão sob nosso controle, a maioria das fábricas descobriu que a confiabilidade aprimorada é uma área-chave de melhoria de custo e produtividade. Ao longo dos anos, nossa busca por menores custos de produção por meio da tecnologia mudou drasticamente o papel do operador em nossas fábricas. Uma vez que um operador passava a maior parte do dia "no chão".
Isso proporcionou um conhecimento prático de como o equipamento funcionava e os sinais de que começava a falhar. No mundo de hoje, a maioria dos operadores opera a fábrica por meio de sistemas controlados por computador. Embora essa estratégia tenha obtido sucesso na redução dos custos de produção e, em alguns casos, no aumento da qualidade do produto, ela não incluiu uma estratégia de confiabilidade do equipamento. Na maioria dos casos, essa é uma responsabilidade que recai sobre o departamento de manutenção da fábrica.
Embora esse grupo esteja qualificado para cumprir a tarefa, eles são as pessoas certas para assumir a responsabilidade pela identificação inicial de falhas em potencial? O seu mecânico de automóveis é responsável por identificar falhas potenciais em seu automóvel?
Na International Paper, reconhecemos a confiabilidade como um grande potencial para economia de custos. Como uma empresa, decidimos nos concentrar em restaurar uma abordagem prática para a confiabilidade por meio de um projeto chamado Advantage. Neste projeto, nos concentramos na confiabilidade dirigida pelo operador, planejamento e programação, análise da causa raiz da falha e instalações de equipamentos de manutenção de precisão.
Embora os sistemas não fossem tão eficazes quanto poderiam, o planejamento e a programação, a análise da causa raiz da falha e as técnicas de manutenção de precisão já existiam na Usina Augusta. O planejamento e a programação eram vagos como uma expectativa de como o trabalho deveria ser realizado e um programa de análise da causa raiz da falha em papel existia em toda a fábrica.
Nossa análise de vibração, termografia infravermelha, programas de manutenção acústica e preventiva, todos usam ferramentas analíticas para identificar problemas e concentrar nossos esforços de manutenção antes de falhas catastróficas. A confiabilidade orientada pelo operador, por outro lado, não existia desde os dias do operador prático.
Tínhamos “rodadas de processo” em vigor que exigiam que os operadores olhassem para medidores e medidores para otimizar os parâmetros do processo, mas nenhuma verificação formal de confiabilidade foi incluída nesse sistema. Parecia que os dias em que um operador verificava um rolamento com um cabo de vassoura e o pegava um dia antes que ele nos fechasse já haviam passado por nós.
Isso nos levou à revelação de que a única maneira de mantermos nossa posição competitiva no mercado é tendo operadores que não apenas operam nosso equipamento, mas o POSSUEM. Assim como todos nós temos que assumir a responsabilidade de manter nossos carros funcionando, os operadores devem assumir a responsabilidade de manter o equipamento de processo funcionando em suas áreas.
Assim que sua organização vir a lâmpada acender, a parte mais difícil de iniciar um programa de confiabilidade orientado pelo operador como este ficará para trás. Com recursos dedicados e um cronograma bem definido, esse programa pode fornecer os resultados financeiros que todos buscamos.
Planejamento estratégico
Então, agora que decidimos desenvolver este programa de confiabilidade orientado pelo operador, o que fazemos primeiro? O componente mais crítico de um programa de confiabilidade orientado pelo operador bem-sucedido é a adesão da administração. Sem o apoio dos níveis mais altos da organização, o programa nunca receberá o tempo, dinheiro e apoio necessários para ver resultados positivos.
A primeira etapa na implementação do programa de confiabilidade orientado pelo operador é o desenvolvimento da declaração de missão e metas de confiabilidade orientada pelo operador da fábrica. Desenvolvido pela equipe de liderança da fábrica, deve incluir métricas do programa, marcos, orçamentos e funções e responsabilidades em toda a fábrica.
Em seguida, a equipe de liderança deve selecionar um campeão para supervisionar a implementação do programa. A pessoa selecionada deve ser um indivíduo respeitado de uma posição altamente visível. Eles deverão ter fortes habilidades de liderança e facilitador de equipe, uma vez que gerenciarão em grande parte por meio da influência.
Essa pessoa deve ser rapidamente selecionada e promovida na fábrica como responsável pela implementação do programa. Isso tornará mais fácil para eles navegar nas águas políticas específicas da área. A equipe de liderança deve garantir que o campeão esteja ciente da função que está sendo solicitada a preencher e dos limites que ele deve navegar na implementação bem-sucedida do programa.
Como regra prática, essa pessoa é responsável por identificar e retificar bloqueios na fábrica, manter a equipe de liderança da fábrica informada sobre o andamento, selecionar uma equipe da fábrica para implementar o programa e manter a visibilidade e as expectativas do programa.
Em seguida, o campeão da confiabilidade conduzida pelo operador precisará identificar as principais áreas operacionais da fábrica e selecionar um membro da equipe para representar cada área na equipe de confiabilidade conduzida pelo operador da fábrica. Em Augusta, identificamos seis áreas operacionais críticas - pátio de madeira, fábrica de celulose, casa de força, fábrica de papel, acabamento e transporte e água e resíduos, e selecionamos um membro da equipe para cada uma.
O membro da equipe é responsável por identificar os equipamentos que serão colocados nas rotas das operadoras, desenvolver a ordem de caminhada das rotas e, em seguida, definir a frequência das inspeções. Eles também são responsáveis pelas métricas da área, plano de comunicação da área, identificação das necessidades de ferramentas analíticas e um plano de reconhecimento do departamento. Assim como o campeão do programa, os membros da equipe devem ser bem respeitados em sua área, automotivados e ter a capacidade de trabalhar em várias tarefas ao mesmo tempo.
Os membros finais da equipe de desenvolvimento devem ser um grupo adicional de funcionários assalariados ou horistas selecionados para desenvolver as rotas. Na Augusta, utilizamos duas estratégias diferentes para o desenvolvimento da rota. Começamos a implantação com foco em nosso pátio de madeira.
Para esta fase, selecionamos dois funcionários de operações horistas para o desenvolvimento da rota. Sentimos que eles teriam um melhor conhecimento da perspectiva dos equipamentos e dos operadores e ao mesmo tempo darão mais credibilidade às rotas para os demais operadores da área. Embora esta tenha se mostrado uma maneira bem-sucedida de implementar as rotas do pátio de madeira, tem sido muito demorada. Os funcionários horistas tinham o desejo de fazer o programa funcionar, mas não tinham conhecimentos de informática e um forte senso de resolução de problemas.
Desenvolvemos uma nova estratégia para as áreas subsequentes. Pegamos quatro engenheiros recém-contratados e os configuramos para concluir o desenvolvimento do restante da fábrica. Isso acabou trazendo dois benefícios principais. Eles nos ajudaram a desenvolver as rotas rapidamente com seus conhecimentos de informática e treinamento para resolução de problemas, e isso os ajudou a aprender as áreas e o pessoal da fábrica.
Ambas as táticas podem ser muito eficazes, mas variam de fábrica para fábrica com base no pessoal. Esta é uma excelente decisão para deixar a equipe do projeto discutir. Eles não apenas levarão o conhecimento de todo o pessoal da área operacional para a decisão, mas também formarão uma forte participação no projeto ao poderem expressar suas opiniões.
Ferramentas analíticas
Muitos programas de confiabilidade orientados pelo operador param por causa da questão das ferramentas analíticas e dos custos e treinamento associados. Há muitos benefícios em usar um conjunto completo de ferramentas analíticas. Você pode fornecer leituras mais precisas, melhores meios de relatório de exceção, tendência de dados em tempo real no campo, minimizar a capacidade de rotas de "ponta de lápis" e dar um senso de credibilidade a um novo programa.
Embora todos esses sejam “agradáveis de ter”, eles não são, de forma alguma, empecilhos quando se trata de implementar um programa ODR e podem ser facilmente adicionados a um programa conforme ele amadurece.
Dito isso, há uma variedade de equipamentos disponíveis para ajudar a refinar sua coleta de dados.
· Pistolas infravermelhas de temperatura: Eles fornecem a temperatura exata com maior segurança, pois fornecem aos operadores uma leitura precisa sem entrar em contato com equipamentos potencialmente quentes.
· Estroboscópios: Eles são usados para procurar acoplamentos ou correias soltas, encontrar parafusos faltando ou defeitos de material em equipamentos rotativos em serviço. Eles exigem acesso aos pares ou cintos, tendo portas de inspeção nas proteções ou nas proteções de metal expandido.
· Canetas de vibração: Eles verificam a condição e a tendência dos níveis de vibração do rolamento. Eles requerem o uso do mesmo ponto e ângulo para que as leituras forneçam tendências precisas.
· Assistentes pessoais digitais (PDAs): Estas são unidades portáteis para rotas eletrônicas. Eles fornecem tendências de campo, leitura de código de barras para garantir que as verificações corretas do equipamento sejam concluídas, conformidade de rota eletrônica e registro de exceção com um botão. As desvantagens incluem custo, treinamento extensivo necessário e possível desculpa para rotas incompletas.
A fábrica Augusta implementou o programa de confiabilidade orientado pelo operador apenas com pistolas de temperatura e rotas de papel. Esta decisão foi tomada com os riscos de segurança envolvidos em tocar em equipamentos potencialmente quentes e o conhecimento de que avançaremos para ferramentas mais analíticas conforme o programa amadurece e os preços continuam a cair.
Comunicação
Como acontece com qualquer programa que envolva um grande número de funcionários, a comunicação é fundamental para sustentá-lo até que ele se torne parte da cultura. Se os funcionários não receberem um feedback consistente sobre suas rotas, eles presumirão que as rotas são um item de baixa prioridade e rapidamente começarão a "revirar o caminho" nas rotas. Se continuarem a não receber feedback, acabarão por parar de executá-los completamente. Portanto, é fundamental ter um plano de comunicação e reconhecimento por escrito em vigor para a fábrica.
Em Augusta, descobrimos que cada departamento tinha veículos de comunicação maduros que já usavam para repassar feedback e informações. Algumas áreas usaram conversas pessoais com os capatazes, enquanto outras usaram um quadro de avisos e atualizações semanais. Permitir que ajudassem a desenvolver o plano com o gerente de comunicação da fábrica aumentou sua participação no programa e trouxe à luz a melhor alternativa para cada área.
Independentemente do método usado, um plano de comunicação de confiabilidade orientado pelo operador deve incluir:funções e responsabilidades do departamento, tempo de rotas e papelada de acompanhamento, sistema de feedback, expectativas, treinamento e como o reconhecimento será tratado na área.
Desenvolvimento de rota
A carne do programa é baseada no desenvolvimento de rotas. Existem muitas filosofias diferentes de desenvolvimento de rota, que vão desde a inclusão apenas de equipamentos críticos até a inclusão de todos os equipamentos e tudo o mais. Na realidade, os líderes de confiabilidade orientados por operadores de área terão que determinar quanto tempo seus operadores têm para examinar as condições do equipamento e desenvolver suas rotas para utilizar totalmente esse tempo. Muitas vezes as pessoas esquecem o tempo necessário para passar de um equipamento a outro.
Isso é crítico, especialmente em áreas remotas onde o tempo entre os equipamentos pode ser mais que o dobro do tempo gasto para completar a rota. Em última análise, cada rota deve ser cronometrada para garantir que os operadores possam concluir suas rotas atribuídas, mantendo suas funções atuais. Você também deve estar ciente do tempo adicional que pode ser necessário para usar ferramentas analíticas. No início, o uso das ferramentas pode aumentar significativamente o tempo, mas diminuirá à medida que os funcionários se familiarizarem com os equipamentos e ferramentas.
Em Augusta, definimos 20 minutos como regra geral para a extensão da rota, embora a extensão variasse de acordo com a posição ao longo da fábrica. Em seguida, usamos o membro da equipe de área para identificar o equipamento “certo” a ser incluído nas rotas. Com base na mão de obra atual da fábrica, algumas áreas verificam apenas equipamentos críticos que podem causar tempo de inatividade do processo da área, enquanto outras também incluem alto custo e equipamentos de reparo repetitivo.
A frequência da rota é outro fator a considerar no desenvolvimento. Idealmente, usaríamos o período de desenvolvimento de falha de todas as falhas que podemos detectar com confiabilidade orientada pelo operador e definir nossas frequências de inspeção na metade desse intervalo de tempo para garantir que detectemos as falhas antes que ocorram. Embora essa seja uma boa meta, a mão de obra da maioria das usinas hoje só nos permitirá nos concentrar no que é mais provável de acontecer e, em seguida, ajustar se encontrarmos uma responsabilidade inaceitável no futuro.
As rotas também são substancialmente mais fáceis de gerenciar se todos os equipamentos forem verificados ao mesmo tempo, em vez de frequências de rota diferentes para vários equipamentos dentro de uma área. Na Augusta, decidimos fazer crescer a história da frequência através da experiência. As rotas foram desenvolvidas para serem executadas semanalmente e usaremos o programa de falha de causa raiz para identificar quando uma inspeção foi deixada de fora da rota que deveria ser concluída.
Treinamento
Este é outro componente que é amplamente esquecido ao iniciar um programa de confiabilidade orientado pelo operador. Muitas vezes, sentimos que os operadores já conhecem seus equipamentos e, desde que os cheques estejam na rota do papel, eles não precisarão de nenhum treinamento adicional. Em Augusta, descobrimos que isso está longe de ser verdade. Descobrimos que os operadores conheciam os equipamentos por nomes completamente diferentes dos identificados no sistema de gerenciamento de manutenção computadorizado.
Isso tornava muito difícil identificar exatamente quais reparos precisavam ser feitos sem percorrer a rota com o operador que os identificou. Com a programação de turnos de 12 horas de Augusta, isso pode significar esperar quase um mês para ter aquele funcionário de volta em dias durante a semana. Também descobrimos que apenas alguns operadores sabiam como o equipamento funcionava e por que era importante fazer as verificações que eles deveriam realizar. O porquê e o como do treinamento são críticos para que o operador se aproprie do programa e do equipamento de sua área.
Dois grupos distintos devem ser treinados para implementar e sustentar com sucesso seu programa de confiabilidade orientado pelo operador - gerentes e operadores. Os gerentes devem entender os objetivos do programa, como ele é configurado e as expectativas deles para fazer o programa funcionar. Os operadores precisam ser treinados em:
- o que é uma rota
- como usar as ferramentas analíticas
- como realizar verificações de maneira adequada
- como preencher a documentação adequada
- plano de comunicação da área
Para nossos funcionários horistas, desenvolvemos um curso de quatro horas em Augusta utilizando os padrões de monitoramento de condição do IDCON como base. Isso fornece:
- o que um equipamento é projetado para fazer
- quais verificações devem ser feitas em um determinado equipamento
- como fazer as verificações
- por que as verificações são importantes
O treinamento também incluiu uma caminhada prática de uma rota e tempo depois para fazer perguntas e discutir o que eles vivenciaram.
Para os gerentes, conduzimos sessões individuais com o membro da equipe de sua área. Isso incluiu o equipamento da rota, o fluxo do processo, o plano de comunicação e reconhecimento e sua função e responsabilidade como gerente do programa.
Sustentabilidade
O programa de confiabilidade orientado pelo operador deve se tornar parte da cultura da fábrica para ser sustentável. Deve se tornar a maneira mais fácil para um operador fazer o equipamento trabalhar em sua área. O feedback constante é fundamental para ajudá-los a entender o trabalho que está sendo feito, quando e por quê. Também ajuda a garantir que as rotas sejam as melhores para a área.
Por fim, os recursos dedicados no início do programa serão reatribuídos e o programa deve ter impulso suficiente para fazer o departamento assumir a responsabilidade de sustentar as rotas de confiabilidade conduzidas pelo operador.
Incluímos um cronograma para o desenvolvimento de um programa de sustentabilidade da fábrica em Augusta, com o objetivo de garantir que o trabalho realizado pela equipe de confiabilidade acionada pelo operador seja retomado e assumido pelas áreas. O reconhecimento é um aspecto importante da nossa sustentabilidade. Um vale-presente de US $ 5 para o refeitório para cada funcionário de ODR do departamento do mês ajudará a manter a visibilidade do programa e reforçar os esforços da área para incutir propriedade nos operadores. Com menos de $ 500 por ano para manter, é um programa de reconhecimento atraente para reforçar o ODR.
Manutenção
Housekeeping é o “bloqueio e combate” do mundo da confiabilidade do equipamento. Sem equipamentos limpos, as temperaturas sobem, vazamentos passam despercebidos e pequenas falhas de equipamentos tornam-se dispendiosas falhas de equipamentos. Para algumas usinas, isso não é problema. Eles já têm uma expectativa e uma cultura de arrumação no local.
Para outros, isso pode ser um obstáculo considerável que tem o potencial de fazer até mesmo um sistema bem desenvolvido falhar. Se a limpeza for um problema em sua fábrica, não se esqueça disso. Deve ser discutido e um plano formulado sobre como lidar com questões reais. Infelizmente, a limpeza é uma questão muito emocional. Temos a tendência de apontar o dedo para outra pessoa ou inventar um motivo pelo qual isso "não pode" ser feito.
Na Augusta, reconhecemos a limpeza como um problema com o qual precisávamos lidar. Integramos a limpeza ao treinamento e enfatizamos a importância de manter os equipamentos limpos. Escovas de arame, trapos e uma lanterna estão incluídos nos kits de confiabilidade acionados pelo operador em um esforço para ajudar a tornar a limpeza uma parte da cultura da fábrica. Algumas áreas já estão assumindo esse aspecto, tirando fotos digitais de questões de limpeza na área e discutindo e tratando delas nas reuniões semanais da equipe.
Este é definitivamente um problema do tamanho de um elefante:você tem que comê-lo um pedaço de cada vez. Em nosso treinamento, dissemos a eles para gastar tempo para realmente limpar a última peça do equipamento em suas rotas. Once that piece of equipment is cleaned, clean up the second-to-last on the next round, and so on. With four different crews running routes, it shouldn’t take long to get them all in decent shape.
Our mill trainers did an experiment and went out and thoroughly cleaned one motor and pump set. They said it took them about a half-hour to complete. So far, it has stayed relatively clean over the last four months. There will be some pieces of equipment that will get covered in stock regularly due to some other issue (for example, a hole in a chute or a chest that runs over). These should be written up on their routes in an attempt to justify fixing them. Nothing will get buy-in quicker from your hourly employees than seeing operator-driven reliability fix something that has bothered them for years.
Conclusion
Market pressures show no sign of receding, and we must explore all avenues to provide the highest quality product at the lowest cost. Equipment reliability has already been identified as a key component of the cost equation and it is easy to see that operator-driven reliability must be part of the mill reliability strategy. Without the ownership of your mill equipment in the operator’s hands, you cannot hope to be reliable. Using a well-planned approach involving all mill employees, equipment reliability will have a direct, positive impact on your bottom line.
About the author:
Chris Hykin is the director of operator-driven reliability for International Paper in Augusta, Ga.
Manutenção e reparo de equipamentos
- Função da proteção contra surtos na confiabilidade do equipamento
- Os adesivos garantem a confiabilidade do fixador
- Fabricação flexível e confiabilidade podem coexistir
- 5 Chaves para Manter a Confiabilidade do Equipamento
- Como escolher o fornecedor certo de equipamento industrial pode ajudar sua empresa a crescer
- Por que seu equipamento de teste precisa ser consertado
- Canja de Galinha para Seu Equipamento Eletrônico Quebrado
- Como manter seu equipamento de fabricação industrial
- Conheça seu equipamento agrícola
- 6 dicas valiosas para melhorar a confiabilidade do seu equipamento