Implementando Manutenção Baseada em Risco (RbM) | Dividido em Termos do Layman
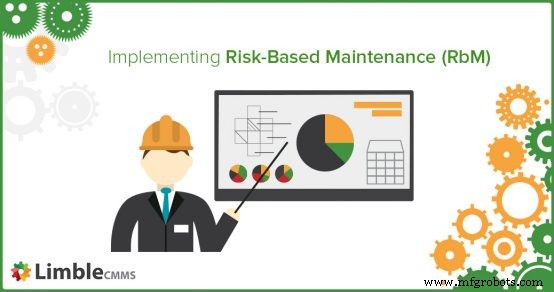
Você já se perguntou se seria capaz de economizar tempo e recursos não gastando seus recursos já limitados em ativos que não precisam deles?
Você se pergunta se economizaria tempo e dinheiro criando uma estratégia de manutenção para o gerenciamento de ativos?
Nosso guia para manutenção baseada em risco (RbM) irá mostrar passo a passo em termos leigos como analisar rapidamente a maneira mais eficiente de usar seus recursos de manutenção enquanto melhora a confiabilidade, reduz custos e aumenta o ciclo de vida e integridade do equipamento de forma econômica.
Um estudo da Universidade de Aalborg na Dinamarca sobre estruturas de aço offshore descreveu como uma empresa conseguiu economizar mais de 80% nos custos totais de reparo!
O que é manutenção baseada em risco e por que ela é importante?
A manutenção baseada em risco pode se tornar bastante robusta e complexa, mas em poucas palavras - ela ajuda a determinar o uso mais econômico de seus recursos de manutenção. Qual é a diferença entre manutenção baseada em risco e manutenção centrada em confiabilidade?
Isso pode parecer complicado, mas o processo pode ser relativamente simples. Vamos mergulhar nos detalhes básicos de como a seguir, mas a essência da manutenção corretiva baseada em risco é encontrar os ativos críticos / problemáticos e dedicar seus recursos de manutenção a eles enquanto desvia recursos de ativos não críticos.
Quando bem feito, as recompensas são grandes. Uma empresa de petróleo e gás na Europa conseguiu economizar mais de US $ 15 milhões por ano utilizando a manutenção baseada em risco.
Como você implementa a manutenção baseada em risco?
Com a manutenção baseada em risco, temos a missão de analisar duas medidas principais:prevenção (probabilidade de falha) e recuperação (consequências da falha).
Para começar, primeiro precisamos entender o que essas duas frases significam:
A Probabilidade de Falha significa simplesmente, “qual é a probabilidade de que este equipamento falhe?”
Freqüentemente, a Probabilidade de Falha (PoF) se correlaciona com a idade (tempo de execução) do equipamento.
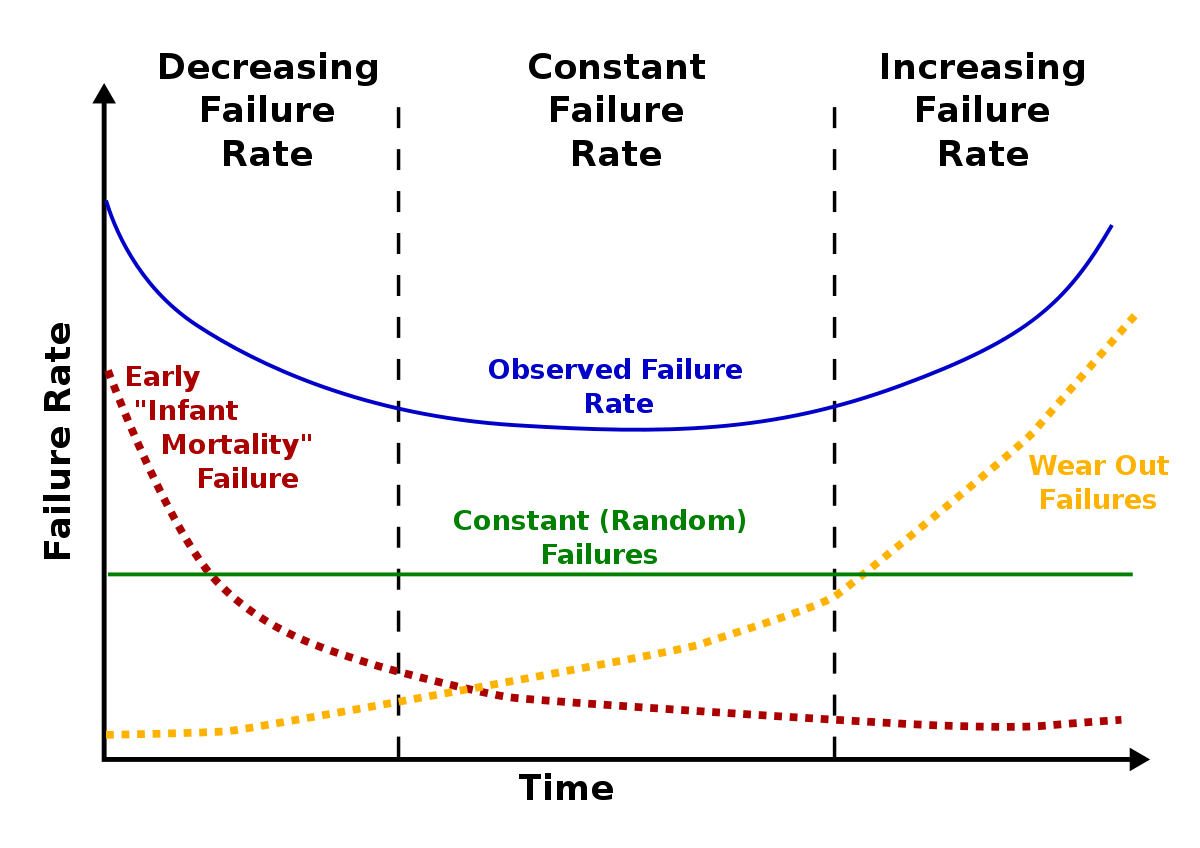
No entanto, o tempo não deve ser sua única consideração. As condições de trabalho são importantes no que diz respeito à tomada de decisões e à probabilidade de fracasso.
Ativos localizados em locais úmidos ou empoeirados podem exigir mais manutenção e têm maior probabilidade de falhar. Como você pode imaginar, fatores como geografia, clima e outras condições ambientais desempenham um papel importante na determinação da PoF.
A Consequência da Falha significa, “quanto custará a falha desta máquina?”
Você deve considerar tantos fatores quanto possível para determinar a Consequência da Falha (CoF). Você vai querer se fazer perguntas como:
- Quanto custa o conserto médio?
- Quanto estou perdendo a cada ano no tempo de inatividade (perda de produção) porque esta máquina não está funcionando corretamente?
- Existem acidentes relacionados à falha deste equipamento? O processo de manutenção desta máquina está retardando outras áreas de produção?
- Existem riscos de segurança relacionados com a abordagem de manutenção desta máquina ou falta de manutenção?
Como você pode ver, há mais a considerar do que apenas custos de reparo.
Agora que entendemos a terminologia, vamos iniciar o processo.
1. Colete seus dados de manutenção
Antes de qualquer coisa, precisamos coletar e analisar seus dados de manutenção atuais. O objetivo aqui é utilizar os dados disponíveis para identificar as áreas problemáticas.
Você precisará obter um inventário decente de seus ativos e o que eles estão custando a você. Para fazer isso, consulte seu CMMS e outros registros de manutenção. Para uma visão aprofundada do que é um CMMS, confira nosso guia O que é um sistema CMMS e como funciona.
A partir desses registros, você vai querer saber o seguinte para cada peça de equipamento em sua instalação:
- Quantos anos tem este equipamento?
- Com que frequência o equipamento falha? (MTBF)
- Quanto tempo leva para restaurar o funcionamento do equipamento? (MTTR)
- Quanto custa quando este equipamento falha? (Interrupção na produção, custo de peças, custo de mão de obra, etc.)
- Com que frequência você faz manutenção neste equipamento?
Depois de obter os dados de todos os seus equipamentos, você vai querer identificar quais ativos precisam de sua atenção.
Existem vários métodos excelentes para fazer isso, mas neste post, usaremos a Matriz de Criticidade como exemplo.
Se você for um dos poucos sortudos com um ótimo CMMS, ele informará automaticamente seus ativos problemáticos. Por exemplo, no Limble CMMS, criamos uma poderosa seção de relatórios onde os ativos problemáticos chegam ao topo da lista, permitindo que você veja rapidamente qual ativo está custando mais e por quê.
2. Visualize com uma matriz de criticidade
Uma matriz de criticidade (isso parece super nerd e complexo, mas não é) é simplesmente um gráfico onde a Probabilidade de Falha é traçada no eixo X (horizontalmente) e a Consequência da Falha é traçada no eixo Y ( verticalmente). Como isso:
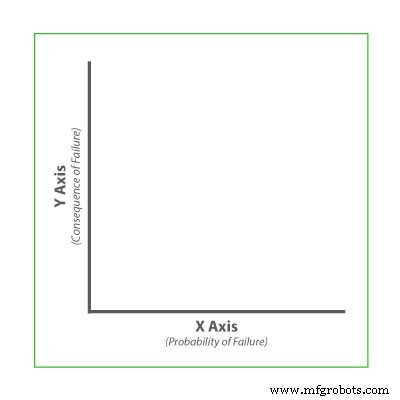
Para mostrar como criar o gráfico, vamos dividi-lo um pouco com um exemplo.
Digamos que tenhamos inventariado os seguintes equipamentos: Geradores 11, 12 e 13 .
Vimos os registros de manutenção de cada equipamento e temos os dados necessários para determinar o PoF e o CoF de cada um.
Para fazer um gráfico disso, precisamos pontuar a Probabilidade de Falha (PoF) dos geradores 11, 12 e 13 atribuindo uma pontuação que representa a probabilidade de que cada gerador possa falhar.
O intervalo de pontuação pode ser parecido com isto:
1 =falha altamente improvável ocorrerá dentro de três anos
2 =falha improvável ocorrerá dentro de três anos
3 =falha não é provável ou improvável
4 =falha é provável
5 =falha é altamente provável
DICA # 1:você pode usar qualquer tipo de sistema de pontuação que desejar. Se for mais fácil para você pensar em porcentagens (ou seja, 10% de chance de falha, 20% de chance de falha, etc.), então, por favor, vá em frente!
Agora que configuramos nossa estrutura de pontuação, vamos fazer a pontuação.
Nossos dados nos dizem que nos últimos 3 anos o Gerador 11 quebrou 5 vezes, o Gerador 12 quebrou 2 vezes e o Gerador 13 quebrou 3 vezes. Com base nesses números, vamos dar as seguintes pontuações:
Escala de probabilidade de falha
Gerador 11 - pontuação 5
Gerador 12 - pontuação 2
Gerador 13 - pontuação 3
Em seguida, é hora de atribuir a cada gerador uma pontuação de Consequência de Falha. Novamente, precisamos criar um sistema de pontuação que represente o nível de consequência de cada ativo. (Você também pode pontuar seu CoF da maneira que desejar).
Vamos medir o impacto da falha:
Gerador 11 - Este gerador é usado pela equipe noturna móvel para fornecer eletricidade para iluminação. Se ele quebrar, a equipe não poderá continuar seu trabalho, que custa $ 5.000 em tempo perdido, atrasos no projeto de mão de obra, etc. Os custos de reparo são normalmente $ 300 por quebra.
Gerador 12 - Este é um gerador antigo que raramente é usado. A falha deste gerador não tem um grande impacto. Trabalhos de reparo, perda de tempo, mão de obra etc. custam apenas $ 500. Os custos de reparo são normalmente de $ 300 por avaria.
Gerador 13 - Esta máquina é usada para exercícios aleatórios no quintal. O trabalho aleatório no quintal não é urgente, mas custa dinheiro quando não pode ser concluído. A perda estimada em tempo perdido, trabalho, etc. é de $ 2.500. Os custos de reparo são normalmente de $ 200 por avaria.
Escala de conseqüência da falha
1 =Menos de $ 2.500 custos anuais
2 =Entre $ 2.500 e $ 5.000 custos anuais
3 =Mais de $ 5.000 custos anuais
E então, atribuiríamos a cada gerador uma pontuação com base nas consequências (custos) particulares de cada máquina. Igual a:
Gerador 11 =3
Gerador 12 =1
Gerador 13 =2
DICA 2:A melhor maneira de descobrir as consequências do fracasso é conversar com sua equipe. Pergunte a eles o que acontece se uma determinada peça do equipamento não funcionar e o que isso lhes custa. Olhe para o seu CMMS ou registros de manutenção para ver os custos de reparo. Essas ações lhe darão grandes percepções sobre o verdadeiro custo da falha do equipamento.
Agora que temos as pontuações de Probabilidade de Falha e Consequência de Falha, é hora de plotar nossos dados. Este gráfico seria mais ou menos assim:
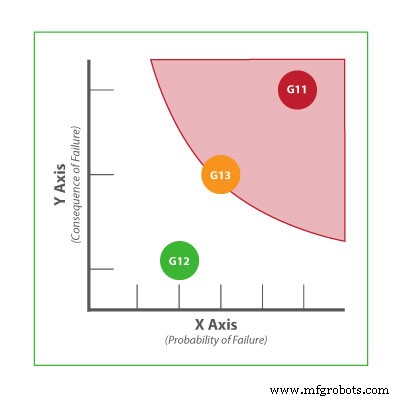
Os geradores que estão na fronteira ou dentro da área vermelha (números 11 e 13) têm um nível de risco muito maior do que o equipamento na parte inferior esquerda do gráfico (número 12). Nesse caso, podemos considerar novas estratégias de manutenção para os geradores 11 e 13.
Esta é uma versão extremamente simples de uma Matriz de Criticidade, pois apenas traçamos alguns ativos e mantivemos nossa pontuação de PoF e CoF muito básica. Mas, você ainda tem uma excelente visão de quais ativos se beneficiariam mais com um plano de manutenção. Quanto mais ativos, mais benéfico será este gráfico na seleção rápida de ativos para programas de manutenção.
Reduz a manutenção reativa em 73,2%
Veja os resultados que Red Hawk aprecia com Limble
Leia nosso
Estudo de caso
Como você sabe qual tipo de manutenção implementar?
Agora que você sabe quais ativos exigem planos de manutenção, como escolher o plano certo para cada máquina?
Odiamos quebrar isso para você, mas não existe uma estratégia padrão pré-determinada que funcione melhor para sua empresa automaticamente. Cada instalação é diferente, cheia de equipamentos diferentes, fazendo produtos diferentes, com pessoas diferentes operando os equipamentos.
Dito isso, aqui estão algumas perguntas que você achará úteis ao determinar quais estratégias de manutenção implementar.
Quanto e quais são os meus recursos de manutenção?
Infelizmente, no mundo da manutenção, espera-se que você faça mais a cada ano com um pool de recursos cada vez menor. Em um mundo perfeito, sua equipe de manutenção seria grande o suficiente para fazer o trabalho direito, mas raramente é o caso. Ao considerar as estratégias de manutenção, você precisa considerar os recursos.
Por exemplo, um plano de manutenção preventiva não adiantará muito se você não tiver mão de obra para realizar os PMs quando eles forem programados.
O que o fabricante recomenda?
O fabricante deve ser sua fonte de informações de referência. Freqüentemente, um manual do equipamento fornecerá um esboço detalhado do trabalho que precisa ser feito para mantê-lo devidamente mantido. Dito isso, lembre-se de que essas são orientações gerais e, dependendo da sua situação, você pode querer aumentar ou diminuir a frequência.
Quanto custa cada ativo para substituir e qual é sua vida útil restante esperada?
Em situações com ativos muito antigos que têm uma vida curta restante, pode ser melhor executar o ativo até a falha e, em seguida, comprar um substituto. Isso pode não ser verdade se o ativo tiver um CoF muito alto, mas felizmente agora você sabe como encontrar essa resposta 🙂
Onde foi parar na sua matriz de criticidade?
Se um ativo pousou no canto superior direito (área super arriscada) de sua matriz, então você precisa de ALGUM tipo de estratégia no lugar. Você pode atribuir inspeções de rotina ou implementar um plano de manutenção preditiva que permitirá que você conserte o equipamento apenas quando for absolutamente necessário consertá-lo.
Antes de tomar grandes decisões, certifique-se de conhecer todas as suas opções. Confira nossa comparação detalhada de estratégias de manutenção para aprender os prós e os contras de cada abordagem.
Reduza o risco começando pequeno e, em seguida, dimensione
Depois de identificar quais métodos de manutenção podem funcionar para seus ativos, você pode aumentar suas chances de sucesso começando aos poucos. Ou seja, coloque seu plano em ação com apenas alguns equipamentos para começar. Monitore o progresso e dimensione sua estratégia a partir desse ponto, se ela for bem-sucedida.
Se você decidiu implementar um plano de manutenção, então você deve considerar investir em uma solução CMMS (se você não tiver uma ou estiver usando um pacote antigo e desatualizado).
Com o Limble CMMS, você pode agilizar seu fluxo de trabalho, reunir dados de qualidade e rapidamente tomar decisões importantes para otimizar a produção da sua empresa na palma da sua mão.
Manutenção e reparo de equipamentos
- A Evolução da Manutenção Industrial
- Propriedade de equipamento para técnicos de manutenção
- Como implementar a manutenção produtiva total
- Participe da pesquisa de benchmark de manutenção de equipamentos
- 5 Chaves para Manter a Confiabilidade do Equipamento
- 5 Benefícios a longo prazo da manutenção preventiva
- O papel das inspeções de equipamentos na manutenção
- Instalação e manutenção industrial
- Manutenção de equipamentos de construção
- Manutenção de equipamentos pesados nos meses de inverno