Estudo do Efeito da Direção de Impacto no Processo de Corte Nanométrico Abrasivo com Dinâmica Molecular
Resumo
O polimento de fluxo abrasivo desempenha um papel importante na usinagem moderna de ultraprecisão. Partículas ultrafinas suspensas no meio de fluxo abrasivo removem o material em nanoescala. Neste artigo, simulações de dinâmica molecular tridimensional (MD) são realizadas para investigar o efeito da direção de impacto no processo de corte abrasivo durante o polimento de fluxo abrasivo. O software de simulação de dinâmica molecular Lammps foi usado para simular o corte de cobre monocristalino com grãos abrasivos SiC em diferentes ângulos de corte (0 o –45 o ) Com um coeficiente de atrito constante, encontramos uma relação direta entre o ângulo de corte e a força de corte, o que acaba aumentando o número de deslocamentos durante a usinagem com fluxo abrasivo. Nosso estudo teórico revela que um pequeno ângulo de corte é benéfico para melhorar a qualidade da superfície e reduzir defeitos internos na peça de trabalho. No entanto, não existe uma relação óbvia entre o ângulo de corte e o coeficiente de atrito.
Histórico
Na moderna usinagem de ultraprecisão, as tecnologias de remoção de material desempenham um papel importante na microeletrônica, na fabricação de elementos micromecânicos e ópticos. A demanda por dispositivos miniaturizados com alta precisão dimensional e superfície de qualidade, tornando os processos de ultraprecisão a principal escolha na área citada [1]. Além disso, as mudanças nos componentes da superfície e na estrutura da subsuperfície estão na escala de comprimento nanométrico. A tecnologia de polimento de fluxo de partículas abrasivas desempenha um papel importante em muitos campos da usinagem de precisão e é como outras tecnologias de acabamento não tradicionais que melhoram a qualidade da superfície. Essa tecnologia tem atraído muitos pesquisadores devido ao seu papel significativo. E. Uhlmann e outros pesquisadores relataram a simulação de computador de superfícies de cerâmica de polimento de grãos abrasivos para os experimentos projetados para verificar o fluxo do fluido de moagem de vários fatores de processamento sobre o efeito dos materiais de corte [2]. Sehijpal Singh e outros pesquisadores usam a tecnologia de polimento de fluxo abrasivo para cortar materiais de cobre e alumínio. A partir da análise de microscopia eletrônica de varredura, eles encontraram uma superfície de ranhura profunda em sua peça de trabalho [3]. G. Venkatesh e outros pesquisadores relataram a tecnologia de polimento de grãos abrasivos assistidos por ultrassom para a engrenagem cônica na superfície complexa do processo de acabamento. Nesta técnica, a velocidade do grão abrasivo é maior do que o fluxo do grão abrasivo convencional para colidir com a superfície da peça, o que pode melhorar a eficiência do processamento. A partir de seus métodos experimentais e teóricos, eles descobriram que essa tecnologia é uma das melhores escolhas para o acabamento das lâminas de engrenagens [4, 5]. K. Kamal et al. estudaram as propriedades reológicas do líquido abrasivo na viscosidade do fluido abrasivo, taxa de cisalhamento e tempo de fluência [6]. No entanto, a maioria dos estudos de polimento de fluxo de abrasivo são baseados no nível macro e muito rara atenção tem sido dada ao nível micro. No processo de polimento por fluxo abrasivo, as partículas suspensas no meio fluirão ao longo do meio, a uma determinada velocidade com o impacto da superfície da peça de micro corte (Fig. 1).
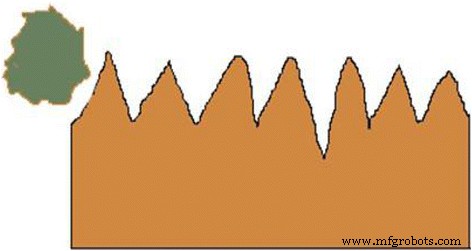
Esboço da peça de trabalho de corte abrasivo. Todos os números são sobre o efeito da direção de impacto no processo de corte nanométrico abrasivo com dinâmica molecular. A Figura 1 é o esboço da peça de trabalho de corte abrasivo. No processo de polimento de fluxo abrasivo, as partículas suspensas no meio fluirão ao longo do meio a uma certa velocidade com o impacto da superfície da peça de micro corte
Como o formato dos grãos abrasivos não é regular, apresentando certas arestas e cantos que atuam na superfície da peça de trabalho, semelhantes aos da ferramenta. Mas o processo de corte é na escala atômica que é obviamente diferente do processo de remoção de material. Um corte em nanoescala envolve poucos nanômetros ou menos da superfície do material, mas é muito difícil observar esse processo por meio de experimentos. Portanto, a simulação MD como método de investigação teórica é muito útil no estudo do processo de corte nanométrico. Dinâmica molecular como uma técnica de simulação por computador, que usa um método de mecânica estatística baseado no tempo para estudar a inter-relação de átomos para previsão e análise de condições. Esta também é uma ferramenta poderosa para simular e compreender os processos de remoção de materiais. Na literatura, existem inúmeros estudos a respeito do MD como uma ferramenta para investigar a usinagem de precisão. Oluwajobi e Chen realizaram um extenso trabalho em simulação MD de usinagem em nanoescala de cobre [7]. Em seus estudos, eles investigaram vários parâmetros para a nanomáquina, como profundidade mínima de corte, geometria e potencial interatômico [8]. Além disso, os resultados das simulações de MD também tiveram sucesso no passado para resolver vários problemas relativos ao processo de corte nanométrico de materiais frágeis como o silício [9]. Komanduri et al. conduziu uma simulação de MD para corte nanométrico de monocristal de silício puro livre de defeitos, usando o potencial de Tersoff. Eles estudaram os efeitos do ângulo de saída, largura de corte, profundidade de corte e ângulo de afastamento na remoção de material e geração de superfície [10]. Goel et al. investigou os aspectos atomísticos da resposta dúctil do SiC durante o processo de corte nanométrico. Eles descobriram a presença de uma transição ordem-desordem sp3-sp2 que finalmente resultou na grafitização do diamante [11]. Cai et al. usado MD para estudar o corte de modo dúctil em nanoescala de silício. Eles relataram a aresta de corte da ferramenta e seus efeitos sobre a tensão de cisalhamento no material da peça [12]. Arafin et al. discutiu o efeito do raio de ponta no corte em modo dúctil em nanoescala de wafer de silício [13]. Vários outros pesquisadores também destacaram as diferentes condições na nanomáquina de silício usando simulações de MD. As investigações consistem em forças de corte, profundidade de corte, temperatura, tensão de cisalhamento e outros parâmetros. No entanto, faltam validações experimentais adequadas nesta área. Qihong Fang et al. estudaram o mecanismo de interação dos deslocamentos em diferentes materiais heterogêneos com diferentes escalas, o deslocamento e a relação entre a tenacidade do material e o dano por fratura. Eles usam simulações de dinâmica molecular para estudar a nanoindentação em três estruturas cristalinas diferentes, incluindo o cobre monocristalino, policristalino e nanotwinned. Com o aumento da taxa de raspagem, a força de raspagem e a temperatura da peça aumentam continuamente devido à severa deformação plástica e grande volume de cavacos, resultando em deslizamento de deslocamento, deslizamento GB e geminação / detwinning [14, 15].
Métodos / Experimental
No experimento de polimento de fluxo abrasivo, a peça de trabalho geralmente era cortada com abrasivo SiC. Após o estabelecimento do modelo de grãos abrasivos de SiC, a simulação da dinâmica molecular da peça foi realizada pelo software Lammps. Foi construído o modelo de dois abrasivos SiC para corte de cobre monocristalino com diferentes ângulos. Um modelo de simulação de um monocristal de cobre monocristal de corte de grãos abrasivos SiC é mostrado na Fig. 2.
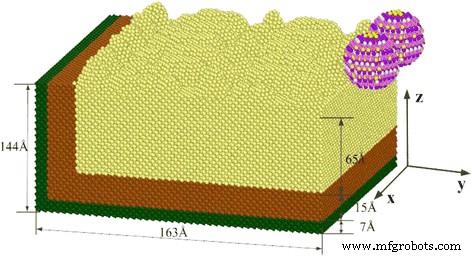
Modelo de simulação de abrasivo de SiC para corte de cobre monocristalino. A Figura 2 é sobre o modelo de simulação do corte abrasivo de SiC de cobre de cristal único; construímos dois abrasivos de SiC para cortar cobre de cristal único. No experimento de polimento de fluxo abrasivo, a peça de trabalho geralmente era cortada com abrasivo SiC. Após a construção do modelo do abrasivo SiC, foi realizada a simulação da dinâmica molecular da peça. O modelo de dois abrasivos SiC de corte de cobre monocristalino com diferentes ângulos foi construído
O tamanho do modelo é mostrado na Fig. 2, enquanto o número de átomos simulados era 159.020. O raio abrasivo é de 15 Å, o número total de átomos de C e átomos de Si nos grãos abrasivos são 1406. E os números de átomos de carbono e silício foram 681 e 725, respectivamente. O número da etapa de relaxamento é definido para 10.000 etapas para o conjunto de equilíbrio simulado, etapas de simulação de colisão para 100.000 etapas de corte, cada etapa da simulação foi 0,001 ps, simulação de corte, as partículas abrasivas de SiC na velocidade de direção de corte de 80 m / s. Grãos de valor de análise AFM colidem com a peça de trabalho de microusinagem durante o polimento, grãos abrasivos de SiC para explorar o processo de corte de diferentes ângulos de dinâmica de colisão molecular. No processo de corte com fluxo abrasivo, a força de corte aumenta à medida que a velocidade de corte aumenta e o tamanho da força de corte afeta diretamente o efeito de corte. Portanto, a escolha de uma velocidade de corte razoável tem um impacto importante na qualidade do corte. Para obter um corte de alta qualidade, escolhemos a velocidade de corte de 80 m / s, pois ela produz a força de corte que pode destruir rapidamente a interação entre os átomos da peça [16].
Em simulações de dinâmica molecular em baixa velocidade de corte, como 10 m / s, mapas de deslocamento atômico e o padrão de como a força de corte de partículas abrasivas de carboneto de silício e ângulos de corte variam com o tamanho da etapa de simulação, como mostrado nas Figs. 3 e 4. Como a velocidade de corte é muito pequena, a força de corte também é inadequada, resultando em muito menos deformação e deslocamento da rede. No geral, a eficiência de corte é baixa e a qualidade de corte é relativamente ruim. Por outro lado, quando a velocidade de corte é de até 80 m / s no experimento microscópico, as ligações químicas entre os átomos de cobre podem ser quebradas de forma rápida e eficaz, de modo a atingir a meta de corte instantâneo de alta qualidade. Portanto, após uma análise abrangente, a velocidade de corte de 80 m / s é razoável para a simulação.
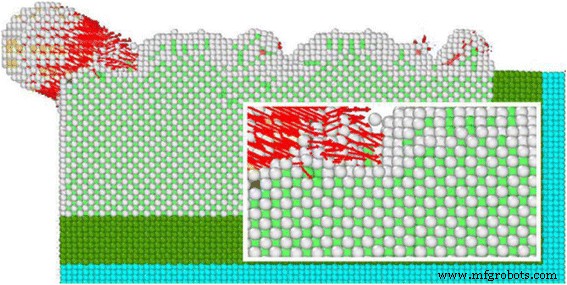
Deslocamento atômico de baixa velocidade
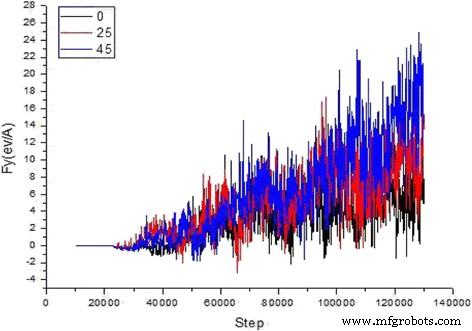
A relação entre a força de corte, o ângulo de corte e a etapa de simulação
Para simular a viabilidade e credibilidade, escolhemos uma função potencial empírica razoável para considerar os potenciais interatômicos dos átomos. De acordo com os diferentes objetos, podemos dividir a função potencial em função potencial de par e função potencial de muitos corpos. Os dois modelos entre cobre monocristalino e grãos abrasivos descrevem os potenciais interatômicos de átomos entre eles pelo potencial de Morse [17], o potencial EAM é usado para descrever os potenciais interatômicos de átomos entre átomos de cobre [18,19,20], e o a interação entre partículas de SiC é descrita usando o potencial de Tersoff [21].
Durante o processo de polimento, a direção de colisão dos grãos abrasivos no meio é aleatória; suas trajetórias não são exatamente ao longo da superfície da peça. Durante o processo de micro-corte, a direção de corte dos grãos abrasivos nem sempre é ortogonal ao material da peça. O ângulo de corte refere-se ao grau do ângulo entre a direção de corte do grão abrasivo e o plano horizontal. É positivo quando as partículas se aproximam da superfície da peça. O esboço do ângulo de corte é mostrado na Fig. 5.
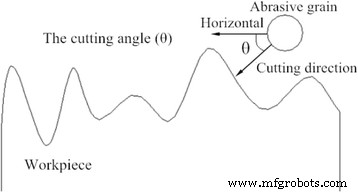
O esboço do ângulo de corte. A Figura 5 é o esboço dos diferentes ângulos de corte quando os grãos abrasivos são cortados. Grãos abrasivos de diferentes direções cortando o material da peça, o material terá o desempenho e a qualidade de processamento será diferente
Neste estudo, a simulação MD é empregada para simular multiabrasivos com diferentes direções de impacto do cobre monocristalino de corte. Conforme mostrado na Fig. 5, o ângulo de corte está entre 0 ° e 45 °, enquanto a superfície da peça de cobre é rugosa.
Resultados e discussão
Análise de colisão mecânica de corte abrasivo de SiC
O impacto do abrasivo de carboneto de silício no corte de material de cobre monocristalino é obtido destruindo a estrutura de rede de um único cristal de material de cobre. Durante a ruptura, as interações entre os átomos de cobre, a tensão de cisalhamento imposta pelos átomos de C, Si das partículas abrasivas de SiC nos átomos de Cu do material da peça foi identificada como sendo a força de corte, que é um parâmetro físico importante para o fato de que a força de corte reflete profundamente o processo de remoção do material da peça de trabalho de cobre de cristal único. Conforme discutido anteriormente, há uma grande diferença entre a força de corte micro e macro. Geralmente, a força de macro corte é a soma da força de corte e retificação, enquanto no micro corte, a força de corte é gerada pelas interações entre os grãos abrasivos e os átomos da peça de trabalho.
Na Fig. 6, mostramos as mudanças da tensão de cisalhamento de grãos abrasivos em várias direções, o efeito da tensão de cisalhamento em diferentes direções e a distribuição das forças de corte ao longo de diferentes ângulos de corte.
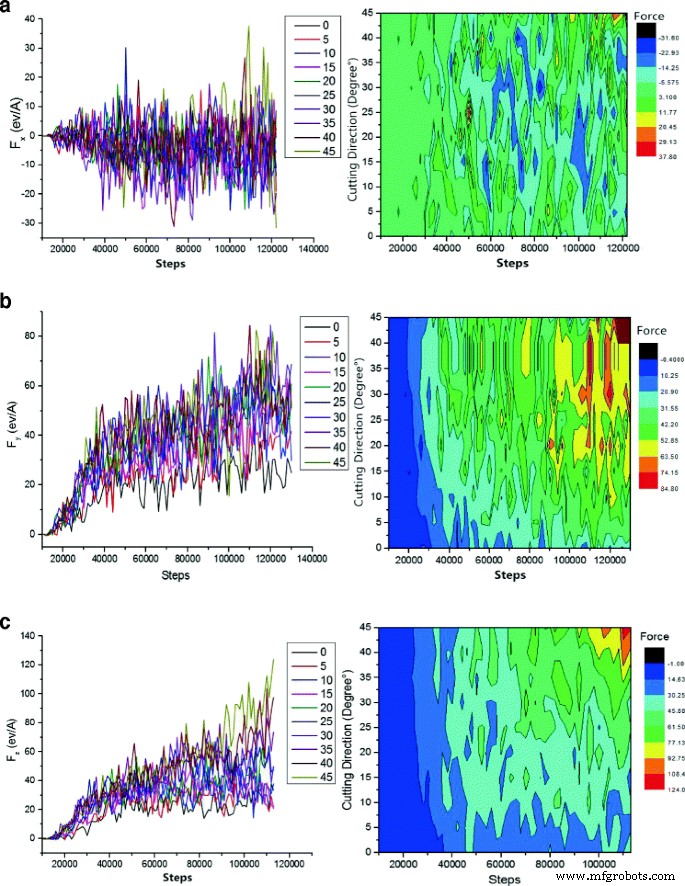
Como o ângulo de corte e o tamanho do passo da simulação afetam a força de corte. A Figura 6 mostra a força de corte abrasiva SiC e o ângulo de corte e o diagrama de etapas de simulação, com o aumento da profundidade de corte, o número da estrutura cristalina de destruição aumenta, o valor máximo da flutuação da força de corte também se torna maior. a [100] direção da força de corte. b [010] direção da força de corte. c [001] direção da força de corte
Os grãos abrasivos de carboneto de silício cortam e impactam no material de cobre de cristal único em diferentes ângulos de aresta, como [010] e [100]. As forças de corte ao longo das direções [001] e [010] eram forças de cisalhamento. Em simulação adicional, a profundidade de corte aumentou gradualmente, o que aumentou persistentemente as forças de corte ao longo das direções [001] e [010]. No entanto, até um certo limite, essas forças flutuaram, como pode ser visto na Fig. 6. Quando as partículas abrasivas se moveram em direção aos materiais da peça, isso mudou totalmente a interação (de atração para repulsão) entre os átomos de cobre mais externos e os átomos de SiC (Si e C). Inicialmente, durante a retificação do material da peça, as forças de corte eram inadequadas devido à presença de forças repulsivas de átomos de cobre. Para o processo de acabamento, as forças de corte devem ser suficientemente altas para que os grãos abrasivos possam facilmente quebrar as ligações químicas nos átomos de cobre para se moverem livremente. Além disso, o incremento da profundidade de corte tem relações diretas com as interações atômicas. Quando os átomos começam a se acumular, a força de corte aumenta consistentemente até que as partículas abrasivas entrem na peça de trabalho, o que requer uma força de corte estável. Neste estágio relativamente estável, a flutuação da força de corte foi sujeita ao grau de deformação da rede, reconstrução da rede, mudança de fase amorfa e geração de chips. À medida que os grãos abrasivos marchavam ao longo da direção do corte, uma força externa foi fornecida sobre o átomo de cobre na rede FCC, o que resultou no deslocamento dos átomos de cobre. Este deslocamento colapsa a rede FCC e a transforma em uma nova estrutura de rede com deslocamento. Uma situação semelhante também é observada na força de corte. Não há correlação linear positiva entre a força de corte ao longo da direção de [010] e o ângulo de colisão das partículas. Na colisão com 0 °, 5 °, 10 ° e além, a força na direção [010] foi menor e menos flutuada do que nas outras direções de corte. Cortando em ângulos menores, basicamente remova as rebarbas, pois elas podem ser definidas na faixa de altura de 3,5 ~ 15 Å. Ao comparar essas direções umas com as outras, se a profundidade de corte for relativamente menor, o dano e a deformação da estrutura cristalina serão moderados. Portanto, em todo o processo de corte, a força de cisalhamento ao longo da direção [010] foi mantida menor, conforme mostrado no gráfico da curva da Fig. 6b. No estágio posterior da simulação, a força de corte atingiu o mínimo de 0 °. Verifica-se também que a força de corte tem relação direta com o ângulo conforme mostrado na Fig. 6c, o que pode ser atribuído ao fato de que quando a velocidade da partícula atinge 80 m / s, um ângulo de corte maior é alcançado. Por outro lado, na mesma etapa de simulação, quanto maior a velocidade do componente ao longo da direção [001], maior o ângulo, o corte de partículas mais profundo e mais redes atômicas foram destruídas. No entanto, houve uma correlação positiva entre o ângulo de corte e a força de corte. Quando os grãos se moviam ao longo da direção [100], os atritos entre os átomos de C, Si e Cu eram a fonte da força de corte. Portanto, a força de corte não apresentou tendência de aumento gradativo. Em outras simulações, no entanto, a força de corte aumentou e flutuou, o que estava intimamente relacionado à deformação e reconstrução da rede, bem como à geração de transição de fase estrutural amorfa. Antes que as partículas abrasivas pudessem ser destruídas, a interação entre os átomos da peça de trabalho é obtida para remover o material, o que acaba aumentando a força de corte de forma consistente. Ao aumentar a força de corte abrasivo, além do valor crítico (força de ligação do átomo), a rede atômica danificada e as ligações se dissociam resultando em uma estrutura amorfa. Ao conseguir isso, a força de corte caiu para um valor relativamente baixo. As flutuações da força de corte apareceram continuamente durante todo o processo de usinagem do fluxo abrasivo, o que se deve ao aumento da profundidade de corte, e mais destruição da estrutura cristalina ocorreu. Assim, conclui-se que nesta fase, o valor máximo da flutuação da força de corte foi maior. Conforme mostrado na Fig. 6b, a região vermelha ocupou uma área maior durante o estágio posterior da simulação, o que indica que a força de corte foi aumentada acentuadamente. No mesmo tempo de simulação, a força de corte era menor quando o ângulo de corte era menor que 15 °, o que significa que uma pequena parte da estrutura do cristal foi destruída.
Análise de energia para o processo de corte por impacto abrasivo SiC
A energia total da termodinâmica é a soma da energia potencial total e energia cinética total em um sistema, que revela o efeito do trabalho realizado na peça por grãos abrasivos. A influência do ângulo de corte no abrasivo de carboneto de silício na mudança de energia do sistema é mostrada na Fig. 7. No processo de corte, materiais de peça de cobre de cristal único com grãos abrasivos de carboneto de silício, o trabalho realizado por grãos abrasivos no material da peça atua de duas maneiras; uma parte é convertida em energia cinética que aumenta o calor dos átomos de cobre de cristal único em contato com as partículas de carboneto de silício funcionando no polimento, a outra parte é convertida em energia potencial que permite mudanças na estrutura interna da peça de cobre de cristal único, a deformação da rede e a liberação de energia da rede.
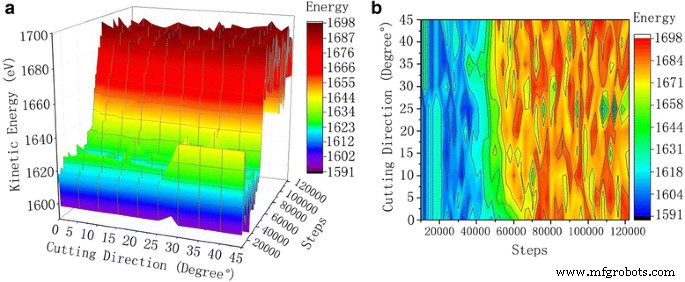
Curva de energia cinética dos átomos da peça. A Figura 7 é a curva de energia cinética dos diferentes ângulos de corte durante o processo de corte. Com o aumento do número de etapas de simulação, a energia cinética dos átomos oscila em uma faixa baixa e, a seguir, para uma faixa mais alta dentro das flutuações. a Curva 3D. b Contorno
No processo de corte de grãos abrasivos de peças de cobre de cristal único, a energia cinética do sistema está intimamente relacionada ao trabalho realizado no material da peça por abrasivos de SiC. Ao descobrir a velocidade das partículas no sistema a cada momento, a energia cinética total do sistema pode ser calculada:
$$ K =\ sum \ limits_ {i =1} ^ N \ frac {1} {2} {m} _i \ left ({v} _ {\ mathrm {ix}} ^ 2+ {v} _ {\ mathrm {iy}} ^ 2+ {v} _ {\ mathrm {iz}} ^ 2 \ right) $$ (1)
Na fórmula, \ ({v} _ {\ mathrm {ix}} ^ 2 \), \ ({v} _ {\ mathrm {iy}} ^ 2 \), e \ ({v} _ {\ mathrm {iz}} ^ 2 \) representam o componente de velocidade x , y , z átomos de direção, respectivamente.
A curva cinética da Fig. 7 nos levou a concluir que no incremento das etapas de simulação, inicialmente a energia cinética dos átomos flutua em uma faixa baixa e depois em uma faixa mais alta. Com o movimento dos grãos abrasivos, uma interação repulsiva de longo alcance é encontrada entre os átomos de cobre mais externos e os átomos de Si, C (SiC). Os átomos de cobre na peça de trabalho começam a receber energia cinética e se mover. Quando as partículas de carboneto de silício entram em contato com o único cristal de cobre, a temperatura atômica da região de contato aumenta, o que aumenta o movimento térmico atômico. Quando o corte é estável, a energia cinética dos átomos de cobre no material se transmite e se transforma em um padrão de equilíbrio dinâmico, e a energia cinética dos átomos flutua em uma faixa alta.
A análise da energia cinética nos levou a concluir que durante o processo de corte, quando as partículas começam a entrar em contato com a peça, os átomos da região extrudada sofrem deformação em rede, mudanças nas coordenadas atômicas e deslocamento com a energia cinética. Com as partículas abrasivas entrando no cobre de cristal único, o valor de pico da energia cinética da peça de cobre de cristal único aparece quando a peça entra completamente na peça de trabalho. Porque a energia cinética e a energia potencial das partículas abrasivas são meramente transformadas mutuamente. No entanto, a energia de todo o sistema não mudará, exceto para as partículas em movimento, que entram na peça de trabalho. Além disso, o movimento das partículas de carboneto de silício força os átomos da peça a se moverem simultaneamente com eles. O calor gerado durante o atrito atômico é liberado pela energia cinética e a energia de deformação liberada devido ao movimento de deslocamento.
A conversão entre calor e energia cinética é calculada pela seguinte fórmula:
$$ \ frac {1} {2} {\ sum} _i {m} _i {v} _i ^ 2 =\ frac {3} {2} {nk} _B {T} _i $$ (2)
Na fórmula, n é o número de átomos; vi representa a velocidade instantânea; k B é a constante de Boltzmann, e T i é a temperatura dos átomos.
A força de corte aumenta a temperatura atômica da área onde o abrasivo entra em contato com o material da peça. Ao considerar o movimento térmico do átomo e a energia cinética dos átomos, a energia cinética dos átomos de cobre aumenta parcialmente. O sistema simulado é definido para o conjunto canônico; a temperatura geral do sistema flutua em uma determinada faixa. O calor produzido durante o corte de partículas abrasivas é rapidamente transferido para a camada de átomos de temperatura constante, de modo que a energia cinética geral do sistema muda muito pouco.
Como pode ser visto na curva de energia potencial da Fig. 8, ao aumentar o número de etapas de simulação, a energia potencial entre o monocristal de átomos de cobre na peça de trabalho também tende a aumentar. Quando o abrasivo de carboneto de silício entra em contato com o cristal único da peça de cobre desde o início até o corte totalmente estável, o material da peça se deforma gradualmente e os átomos de cobre se deslocam, o que leva à distorção da estrutura do cristal no cristal. Isso também resulta em um campo de tensão elástica, onde a energia de deformação aumenta. Quando a energia de deformação não é suficiente para reorganizar os átomos materiais, ocorre o deslocamento dos átomos que aumenta a energia total do sistema. Em contraste com as curvas de potencial de 0 ° a 45 °, podemos ver uma consistência no movimento térmico dos átomos em temperatura constante. Não há relação significativa entre a energia cinética atômica e o ângulo de corte dos grãos abrasivos de SiC. A energia cinética dos átomos está intimamente relacionada ao movimento térmico dos átomos. No entanto, a mudança da energia potencial e da energia total está obviamente relacionada ao ângulo de corte das partículas abrasivas de SiC. A magnitude da energia potencial atômica aumenta com o aumento do ângulo de corte. Quando o ângulo de corte está entre 0 ° e 20 °, uma mudança óbvia na energia potencial é observada. No entanto, quando o ângulo de corte está entre 25 ° e 45 °, a energia potencial permanece como tal e as curvas de energia potencial geral são de ângulo de corte de 0 ° a 20 °. Conforme mostrado na Fig. 9, a tendência de energia total é semelhante à da curva de energia potencial. Os valores de energia total de todos os ângulos de corte são muito próximos uns dos outros. Isso ocorre porque a energia total é igual à energia potencial e à energia cinética do sistema, enquanto a energia cinética não muda em ritmo com o ângulo de corte, durante o processo de corte. A mudança na energia cinética da peça é muito baixa com diferentes ângulos de corte. Portanto, a curva de mudança da energia potencial é semelhante à curva da energia total. Comparando os diagramas de deslocamento atômico da Fig. 9, pode-se descobrir que sob a mesma condição de corte, a profundidade de corte na peça de cobre de cristal único é maior quando o ângulo de corte está entre 25 ° e 45 °, o que pode ser atribuído ao aumento do deslocamento de átomos de cobre. Ao longo da [001] direção das partículas de SiC, mais danos atômicos na rede e deslocamentos são gerados. A energia de deformação produzida durante este tempo é maior, o que resulta em uma curva de mudança de energia potencial alta e curva de mudança de energia total dos átomos da peça.
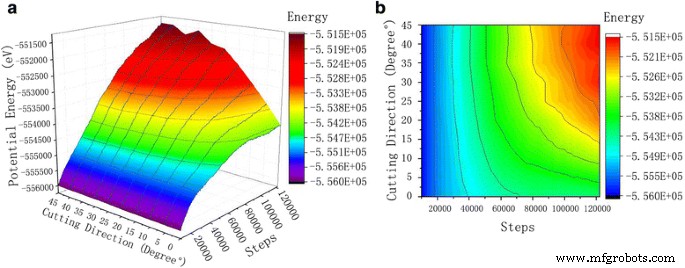
Curva de energia potencial da peça. A Figura 8 é um gráfico de variações de energia potencial em diferentes ângulos de corte durante o processo de corte. Com o aumento do número de etapas para simulação, o potencial entre os átomos monocristais de cobre em exibição na peça tende a aumentar. a Curva 3D. b Contorno
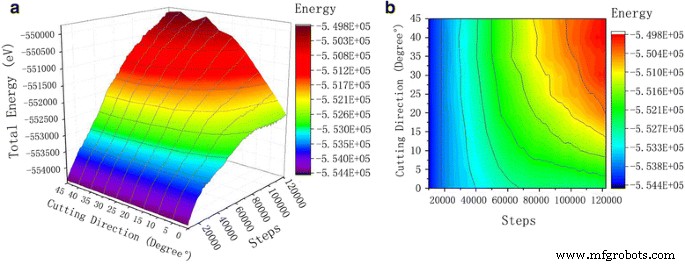
Curva de energia total. A Figura 9 mostra a curva de energia total. Durante o processo de corte de SiC da peça de cobre de cristal único, o efeito dos grãos abrasivos na peça de trabalho se manifesta em duas formas:parte da qual é convertida em energia cinética, o calor atômico é aumentado e a energia cinética local torna-se maior durante o polimento a área de junção da peça de trabalho de cobre de cristal único e as partículas SIC; a outra parte é convertida em energia potencial, a estrutura interna da peça monocristal de cobre é alterada, a rede é deformada e a energia da rede é liberada e transformada em energia potencial. a Curva 3D. b Contorno
Análise de deslocamento atômico no processo de corte por colisão de partículas abrasivas de SiC
No processo de corte do material da peça em vários ângulos, os grãos abrasivos se movem ao longo da direção do corte, forçando os átomos de cobre da peça a se moverem. A partir da análise da direção do movimento da peça de trabalho, o efeito dos grãos abrasivos no material da peça, como a forma do cavaco e a remoção do material são completamente esclarecidos. De acordo com o método de análise do ângulo de ligação, proposto por Ackland-Jones, as diferentes estruturas da rede atômica são marcadas por cores diversificadas, para fins de observação e análise. O plano ZOY é selecionado para observar o processo de corte de uma partícula individual de SiC, e o diagrama de deslocamento atômico da área de corte é ampliado, como pode ser visto na Fig. 10.
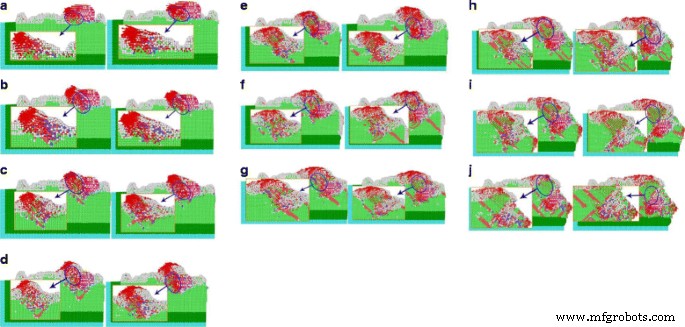
Diferentes ângulos de corte causam deslocamentos atômicos. A Figura 10 descreve deslocamentos atômicos de diferentes ângulos de corte. Quando as partículas abrasivas de SiC de cristal único colidem com a peça de trabalho cortando cobre em diferentes direções, com grãos abrasivos de SiC sendo cortados, a profundidade de corte aumenta, uma vez que a velocidade da direção de corte é de 80 m / s, a direção [001] é v z =0,8 ∗ sen θ , com o aumento da profundidade de corte do ângulo de corte, [001] nas mesmas etapas de simulação de aumento do ângulo de corte, a profundidade de corte é grande ao mesmo tempo. a Deslocamento de 0 °. b Deslocamentos de 5 °. c Deslocamento de 10 °. d Deslocamento de 15 °. e Deslocamento de 20 °. f Deslocamento de 25 °. g Deslocamento de 30 °. h Deslocamento de 35 °. eu Deslocamento de 40 °. j Deslocamento de 45 °. (cor atômica:



Quando as partículas abrasivas de SiC de cristal único colidem com a peça de trabalho cortando o cobre em diferentes direções, a profundidade de corte aumenta ao longo do processo. A velocidade da direção de corte é de 80 m / s, onde a velocidade do componente na direção [001] é v z =0.8 ∗ sin θ . Na mesma etapa de simulação, a profundidade de corte aumenta com o aumento do ângulo de corte. As shown in Fig. 10, there is an atomic position shift in both of the surface and interior of the workpiece material, contacting with the abrasive grains, where atoms of different lattice types are arranged and doped with each other. Due to the movement of these abrasive particles, the copper atoms accumulated at the tip of the abrasive grains, which results no cracks during abrasive particles cutting. It can be seen that the material removal mode of the abrasive particles is plastic deformation. At the same time, due to abrasive cutting, the atoms displacement in single crystal copper increases from 15° to 45°.
The number of the workpiece atoms along the abrasive grain motion direction also increases, and the atomic displacement is perpendicular to the direction of abrasive cutting. This part of the atomic displacement is due to that of the abrasive particles, change the cutting action to the extrusion upon the workpiece atoms. At cutting angle, the abrasive particles is between 0° and 10°, while the cutting depth is smaller than those of the 15° to 45°. Abrasive particles are performing mainly the cutting function, the extrusion of the workpiece atoms is marginal, and the number of atoms is small whose displacement direction is perpendicular to the direction of the abrasive grain motion. With the repeated cutting on the workpiece surface by numerous abrasive particles, the abrasive particles having large cutting angle produce deep pits on the workpiece material during the whole cutting process, while ones following smaller cutting angles will continue cutting along the cutting mark produced by the former. Under the combined action, the workpiece material is cut to a certain depth (micro-cutting) followed by whole abrasive flow polishing.
Dislocation Collision Analysis for SiC Abrasive Cutting
Dislocation is a special arrangement of atoms in crystal along certain crystal surface and crystal direction, or a boundary between the slip zone and the non-slip zone on the slip surface. Dislocation can be divided into edge dislocation, spiral dislocation, and mixed dislocation, among which mixed dislocation is most common. In the process of abrasive particle cutting, the single crystal copper workpiece is plastically deformed, the atoms move, and the crystal lattice breaks and reconstructs, which results in a large number of dislocations. The analysis for dislocation and bond angles at different incidence angles is shown in Fig. 10. In the simulation model of abrasive flow simulation, two abrasive particles are used for cutting the workpiece material. For ease of analysis, the generation and change of different dislocation lines in single crystal copper material, during cutting process and the different lattice structures in the cutting part are analyzed in the view of one single SiC particle on the YOZ surface, as shown in Fig. 11.
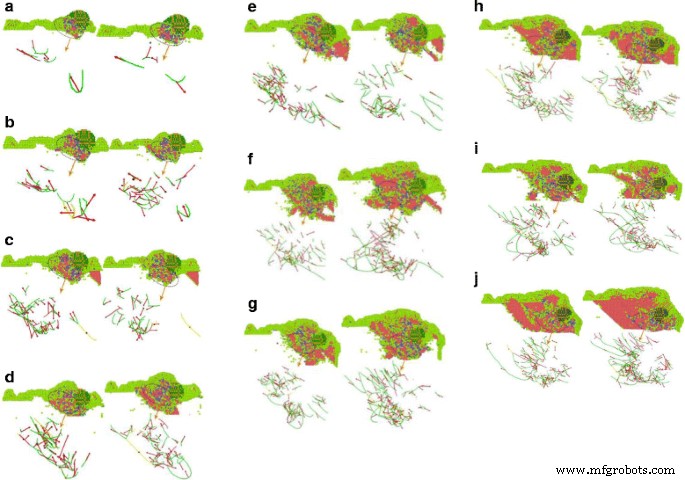
Different angles-bond angle dislocation line charts. Figure 11 represents the cutting dislocation line and the bond angle. As the repeated cuttings on the workpiece surface are done by the numerous abrasive particles during the polishing process, in the entire cutting process, the abrasive particles with larger cutting angle produce bigger pits, while the following abrasive particles with smaller cutting angles continue to polish along the cutting trace. Therefore, certain depth is done on the workpiece material and the whole micro-cutting of abrasive flow polishing is achieved. a Dislocation lines with 0° cutting angles. b Dislocation lines with 5° cutting angles. c Dislocation lines with 10° cutting angles. d Dislocation lines with 15° cutting angles. e Dislocation lines with 20° cutting angles. f Dislocation lines with 25° cutting angles. g Dislocation lines with 30° cutting angles. h Dislocation lines with 35° cutting angles. i Dislocation lines with 40° cutting angles. j Dislocation lines with 45° cutting angles. (Note:the upper part of the key angle analysis, the figure in the atomic color:










Key angle analysis diagram of each cutting angle is shown in Fig. 11, where the sample from the interior workpiece simulation at time 60 and 70 ps, the atoms are colored individually according to different arrangement of atoms through BAD technology. To facilitate the analysis of the lattice changes in the cutting part, atoms of the FCC structure in the workpiece material are removed. By DXA techniques, different types of dislocations are marked in diverse colors:red arrow indicates the Burgers vector (Burgers vectors), green for Shockley partial dislocations (Shockley), light blue for the Frank partial dislocations (Frank), pink pole position for the pressure error (Stair-rod), and blue for the whole dislocation (Perfect).
As can be observed from the analysis of the bond angle portion in Fig. 11, a large number of dislocations and lattice deformations occurred under the impact of external cutting forces. The bond angle analysis shows that the internal HCP structure of the workpiece appears more clearly with increasing of cutting angle. On further simulations, the structure of HCP increases gradually. The silicon carbide particles continuously cut and squeeze the workpiece material at 80 m/s speed, resulting in a phase transition from the FCC structure to the HCP structure. During this phase transition, the atomic strain of the workpiece continues to increase. However, when the stress state of atoms of the workpiece has exceeded the threshold of thermodynamic phase transition, it turns to metastable state. As the strain increases, the HCP phase begins to nucleate and grow spontaneously, and the FCC lattice of copper undergoes absolute destabilization, which induces a sudden change in mechanical quantities. As the kinetic energy of the atom is directly related to the atomic temperature (formula 1), there is a saltatory augment in the kinetic energy change curve, as can be seen from Fig. 7. This is due to high strain energy, accumulated in the single crystal copper workpiece before the nucleation of HCP. The HCP structure increases the system temperature through metastable nucleation and partial stress release. Due to the abrasive cutting and extrusion, bonds of copper atoms in workpiece material break down which results in disorder. The original regular lattice structure is broken, where the partial copper atoms gradually change into disorder and form an amorphous structure. It can be seen from the bond angle analysis diagram that (Fig. 11) atoms with relatively disordered displacement tend to form amorphous structures at 60 and 70 ps, which is because of silicon carbide abrasive particles. At the same time, many atoms with the same displacement direction are transformed into HCP structures. Meanwhile, the particles shear downward and the atomic structure is rearranged due to the displacement of atoms in the original amorphous structure, results an amorphous structure of HCP. Atoms that have already been transformed into HCP structures, even before the next cut stage, change back into amorphous structure. As the cutting depth increases, the number of amorphous atoms near the abrasive particles also increases.
When the FCC crystal structure undergoes cutting by abrasive particles, a shear stress generates in atoms, which results in the displacement of atoms in the lattice and the arrangement of various lattice structures. In moving the atoms of workpiece, the rigid displacements of the atoms produce dislocations, also called as dislocation lines (Fig. 11). Dislocation line can be termed as the boundary between the slip zone and the non-slip zone, on the slip surface. According to the relation between the dislocation and the PATS vector, dislocation is parallel to the PATS vector, called the screw dislocations. The vertical ones are edge dislocations, and the mixed dislocations are neither parallel nor vertical. In Fig. 11, most of the dislocation lines are neither parallel nor vertical to PATS vectors, which are typical mixed dislocations. In the cutting process of abrasive particles, the dislocation line changes, moves and grows around the abrasive particles. The closer the particle, the greater the density of the dislocation line. Dislocation lines are also very dense, when the arrangement of atoms is complicated. The abrasive particles marked as orange, produce a large amount of HCP, BCC, and amorphous structures around them, which interlace and blend with each other to form dislocations that increases the internal energy of the crystals. When atoms arrange their self just like shown in Fig. 12b, possess maximum potential energy. While for the arrangement, shown in Fig. 12a–b, the atoms situate at the lowest potential energy position. The number of dislocation lines is directly related to the magnitude of strain energy of the crystal. The total strain energy of the unit length dislocation can be measured with the given formula:
$$ W=\alpha {Gb}^2 $$ (3)

Schematic view of dislocation changes. Dislocation is a special arrangement of atoms in crystals. It is the crystal in the atomic arrangement along a certain crystal face and crystal orientation occurred in a certain wrong line, and it is the boundary of the slip surface within the area where the slip has occurred and the area with no slip has occurred. In Fig. 12a - c , the relative displacement of the rigidity of the upper atom and the underlying atom produce dislocations, the upper atom belongs to the sliding region, and the lower atoms belong to the non-slip region, they are in the slip surface of the intersection line which is called dislocation line, that is, dislocation. Figure 12 is the process of dislocation generation and development
Where, α is the geometric factor (type dislocations, dislocation density) parameter related to, and generally 0.5 ~ 1.0; G is the shear modulus, and b is the slippage distance.
When the workpiece material is being cut, particles break the atomic arrangement and the lattice reconstructs, which constitutes, macroscopically, the plastic deformation of the workpiece material. In the process of plastic deformation, the dislocation was supposed to escape from the crystal and decrease the dislocation density. However, this dislocation density increases due to dislocation propagation. There are many ways of dislocation multiplication and the main one is the Frank–Reed dislocation source theory, of which the growth mechanism is shown in Fig. 11. As illustrated in Fig. 11, the density of the dislocation line increases markedly from 60 to 70 ps when the cutting simulation proceeds, change both the number and shape of dislocation lines in accordance with Frank–Reed dislocation source theory. At simulation time of 60 ps, there are many long Shockley dislocations. But after another 10 ps simulating, the long Shockley dislocation line becomes less and shorter. The original straight dislocation lines turn into bent, which is especially evident near the abrasive grains. From formula 3, the strain energy of the dislocation is proportional to b 2 . From the viewpoint of energy, the dislocations with the smallest b in the crystal should be most stable with low energy; however, dislocations with larger b will break down into ones. In addition, the energy of the dislocation is valued by the unit length of the dislocation line. Given the shortest line between two points is the straight, the strain energy of straight dislocation is lower than that of the bent one, means straight dislocations are more stable. Frank–Reed dislocation source theory argued that the long dislocation line becomes shorter and breaks down into smaller dislocations, thus decreasing the strain energy of the crystal.
Analysis for Friction Coefficient Between Workpiece Surface and Abrasive Particles
To quantitatively disclose mechanical properties and surface effect of SiC abrasive cutting single crystal copper material, the tangential force ([010] direction) and normal force ([001]direction) on the cutting surface are further analyzed. The friction coefficient can be defined as the ratio of the tangential force to the normal force, with the formula below:
$$ f=\frac{F_y}{F_z} $$ (4)
Figure 13 shows the variation of friction coefficient along different cutting angles during abrasive cutting. The change of friction coefficient can be divided into two periods. Period I, when the cutting distance is less than half of the size of the abrasive particle, the friction coefficient fluctuates violently in certain range due to surface effect of the material; while in period II, all the friction coefficients fluctuate in very small range, and the friction coefficients remains steady state at different angles. However, at cutting angle of 5°, there is a small amount of abnormal fluctuation at the end of simulation. Moreover, in period I, abrasive particles contact the workpiece atoms to the abrasive grains enter into the workpiece of half abrasive diameter (shown in Fig. 13b), the cutting movement distance reaches 7.5 Å. In Fig. 6, the cutting force change curve shows that the tangential force and normal force are in an oscillating phase during period I. Since the friction coefficient can be characterized as the adhesion among atoms in the contact surface and is related to the two atoms contacting with each other, regardless of the cutting mode, which can interpret the phenomenon that change of cutting angle does not cause significant change of friction coefficient, as shown in Fig. 13a.
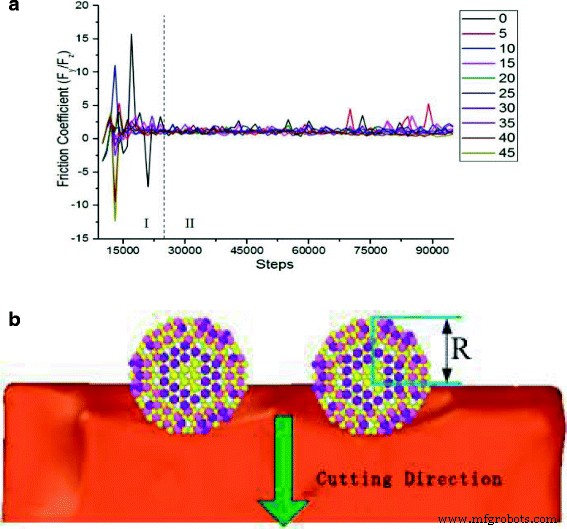
Friction coefficients of different cutting angles. Figure 13 is the changes of the frictional coefficients during SIC particles cutting single crystal copper from different angles. The change in cutting angle did not cause significant changes in friction coefficient. It described two kinds of coefficient of friction in contact with the relevant atoms in the cutting process, regardless of the cutting mode. a Friction coefficient variation curve with cutting angle. b Instantaneous structure when SiC abrasive grains move 7.5 Å
Conclusões
The micro cutting simulation of single crystal copper by SiC abrasive particles is achieved during abrasive flow polishing. Comprehensive analysis of the SiC abrasive cutting reveals that when SiC abrasive particles cut at angle from 0° to 15°, cutting forces in along Y and Z direction are relatively small and tend to stay steady. A larger cutting angle results more dislocations, which brings about larger grooves damaging of the workpiece material. In the process of cutting, it is necessary to avoid more dislocations, which has an immediate adverse effect on the performance of all aspects of crystal material. Therefore, a cutting angle of 0° is better than other angles. Considering the amount of dislocation produced, or the change of cutting force and energy in the cutting process; cutting with small or medium angles is not only beneficial for improving surface quality but reduce the internal defects.
Nanomateriais
- Efeito de superfície no transporte de petróleo em nanocanais:um estudo de dinâmica molecular
- Modelagem de Dinâmica Molecular e Simulação de Corte de Cério com Diamante
- Toxicidade de nanopartículas de CoFe2O4 revestidas com PEG com efeito de tratamento da curcumina
- Estudo de comportamentos de atrito em nanoescala de grafeno em substratos de ouro usando dinâmica molecular
- Dependências de temperatura e pressão das propriedades elásticas de cristais simples de tântalo sob carga de tração <100>:um estudo de dinâmica molecular
- Síntese e estudo in vitro de uma sonda de modo duplo que direciona a integrina αvβ3
- Condutividade térmica de dois tipos de alótropos de carbono 2D:um estudo de dinâmica molecular
- Usinagem e corte com jato de água abrasivo
- Benefícios do processo de corte a laser
- Prós e contras do corte abrasivo