Obra-prima com uso intensivo de compósitos:2020 Corvette, Parte 2
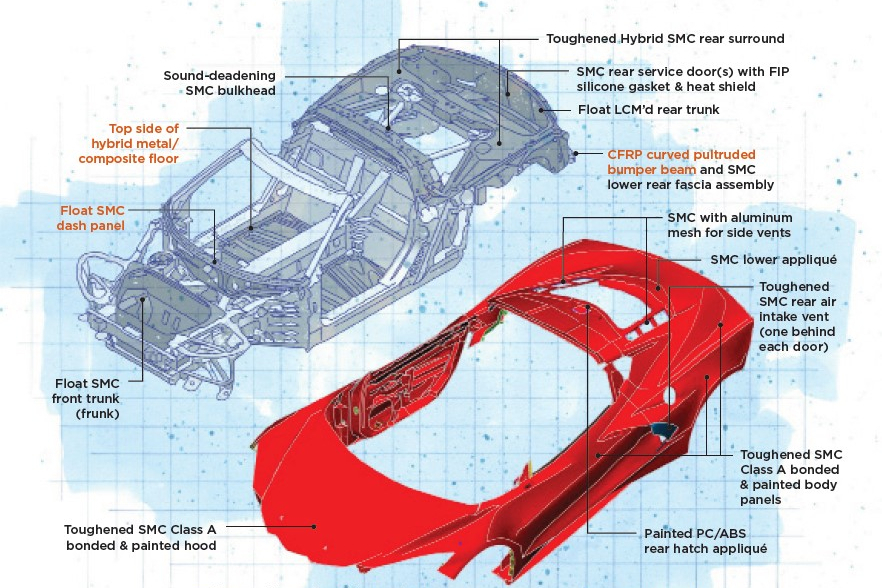

No início deste ano, a primeira parcela da oitava geração do Chevrolet Corvette carros esportivos (C8s) da General Motors Co. (GM, Detroit, Mich., EUA) saíram da linha de montagem de Bowling Green, Ky., EUA, da GM. Descrita como a “entrada mais rápida e poderosa do Corveta ”Nos 67 anos de história do modelo, é também o Corvette com maior uso de compósitos , e o primeiro a apresentar uma configuração de motor central. Não é apenas o 2020 Corvette Stingray bonito e rápido, mas é aprimorado com uma série de recursos de luxo. No entanto, não se deixe enganar pela beleza e pelos tempos rápidos:há muitas inovações em compósitos neste carro. CW A cobertura de duas partes do uso de compostos neste veículo começou na edição de julho de 2020. Esta é a parte 2.
Estrutura do corpo:parte B
O novo Corvette apresenta não um, mas dois baús que, combinados, comportam 12,6 pés cúbicos / 0,36 metros cúbicos de carga. Ambos os troncos são produzidos em 42% em peso de resina de poliéster insaturado de fibra de vidro / vinil éster (VE-UP), mas usam processos diferentes orientados por geometria e requisitos mecânicos. O porta-malas da frente ( frunk ) é um composto para moldagem de folha (SMC) moldado por compressão com gravidade específica 0,95 (SG), enquanto o tronco traseiro é formado por meio do processo proprietário PRiME (Reforço pré-posicionado garantindo Excelência de Fabricação), uma variante de moldagem por compressão de líquido (LCM). O SMC float e o processo PRiME foram desenvolvidos pela processadora Molded Fiber Glass Co. (MFG, Ashtabula, Ohio, EUA). A MFG produziu todas as peças estruturais SMC e LCM do carro.
“Embora ambos os espaços sejam caracterizados por paredes rasas e longas, o frunk é menor que o porta-malas traseiro e pode ser moldado por compressão ”, explica Chris Basela, Corvette engenheiro-chefe da estrutura corporal. “O porta-malas traseiro precisava de maior desempenho mecânico e era uma geometria difícil de preencher com uma carga SMC. Como o processo PRiME nos permite alterar o comprimento da fibra, poderíamos usar um reforço pré-posicionado mais longo em nossa pré-forma. O fluxo da resina [não do vidro] provou ser a melhor abordagem. ”
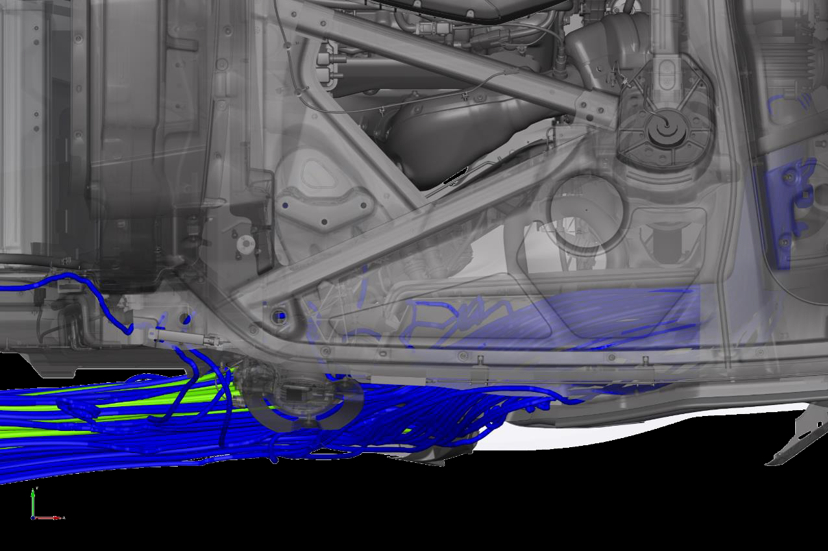
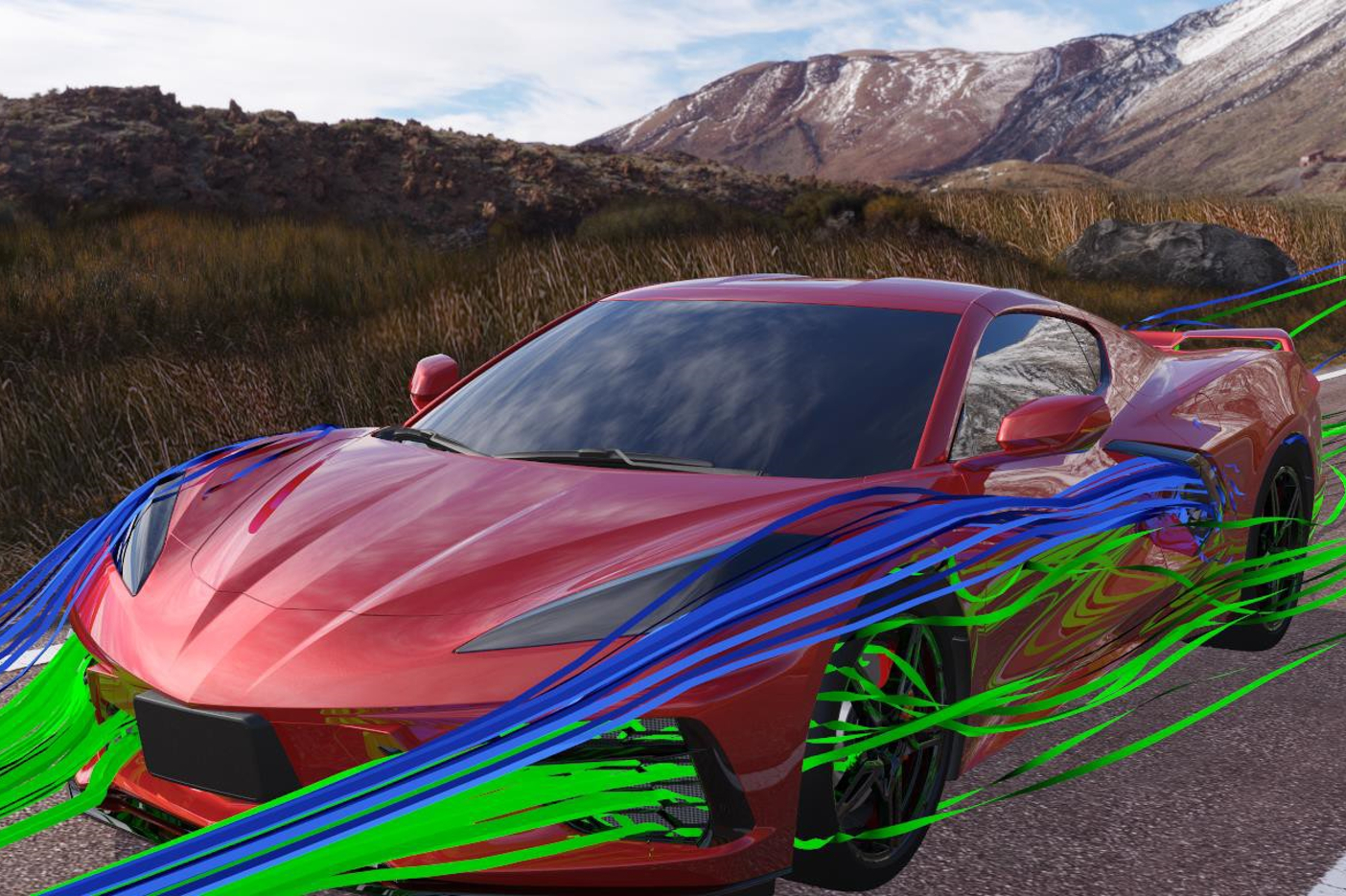
Engenharia inteligente e um novo material foram essenciais para resfriar o motor do C8. Múltiplos caminhos de resfriamento primários (entradas traseiras atrás de cada porta, aberturas da casa do leme dianteiras e entradas de resfriamento do motor de popa) alimentam dutos de indução altamente complexos que canalizam o ar através do veículo e através do motor, antes da ejeção através das aberturas de malha de alumínio e apliques SMC em ambos os lados do a divisória de vidro que mostra o Corvette motor. Os apliques são feitos com float MFG (0,95-SG) SMC (vidro picado / resina UP-VE). Com baixo teor de compostos orgânicos voláteis (VOCs), o material reduz as emissões e elimina a necessidade de ressonadores nos dutos de indução traseira, enquanto reduz o custo e a massa (2,4 kg) em comparação com tecnologias alternativas.
A enorme estrutura surround traseira visível para o cliente - 64 por 69 por 24 polegadas (163 por 175 por 61 centímetros) - que circunda a metade traseira do compartimento do passageiro é moldado por compressão em SMC 1.2-SG temperado. Este material híbrido reforçado apresenta fibra de carbono a 15% de fração de volume de fibra (FVF) e fibra de vidro a 30% FVF, com uma resina UP de baixo VOC, formulada para suportar o calor do compartimento do motor. A estrutura forma a base dimensional para todos os painéis externos e internos traseiros, mas o design flexível permite que ela seja usada para várias variantes de modelo. Graças à consolidação significativa de peças, os acessórios secundários foram eliminados, aumentando o espaço interno do pacote, reduzindo o ruído / vibração / aspereza (NVH), proporcionando melhor estrutura da carroceria e desempenho de vedação, melhorando a visibilidade da porta traseira e reduzindo a massa (15%) e o custo em relação ao quadro de saída. “Dado o tamanho desta peça, que tem quase 6 por 6 pés de altura e 2 pés de profundidade, tivemos que fazer o material fluir morro acima no molde, então estávamos todos um pouco preocupados na primeira foto”, lembra Basela.

Igualmente interessante é a antepara (moldura da janela intermediária), que foi formulada sob medida pela MFG para resolver os desafios de alto calor e ruído, uma vez que esta parte da cabine fica diretamente sobre o motor V8. O reforço de fibra de vidro combinado com enchimento de grafite de berílio em resina VE -UP de baixo VOC amortece a transmissão de som para o compartimento de passageiros de forma tão eficaz que eliminou a necessidade de contramedidas secundárias de amortecimento de som. Isso, por sua vez, reduziu os custos, aumentou o espaço interno do pacote e o conforto do passageiro, e melhorou a vedação da carroceria e o NVH. “Com uma gravidade específica de 2,2, esta é a primeira peça composta que me pediram para adicionar massa em vez de retirá-la , ”Ri Basela.
Fechamentos e cortes
Os painéis externos da carroceria são todos colados (interno / externo), pintados, temperados 1.2-SG SMC (22-28% de fibra de vidro FVF / resina UP, dependendo do componente) da Continental Structural Plastics (CSP), uma empresa do Teijin Group (Auburn Hills, Michigan, EUA). Ao aparafusar as tampas compostas, a GM atinge o estilo agressivo, a aerodinâmica e a integração de resfriamento funcional do C8, com redução de peso econômica em várias variantes de modelo usando peças comuns. Todos os painéis da carroceria são pintados em linha em um "sistema skuk" na posição do veículo, usando o inovador processo robótico de lixamento úmido de Bowling Green.
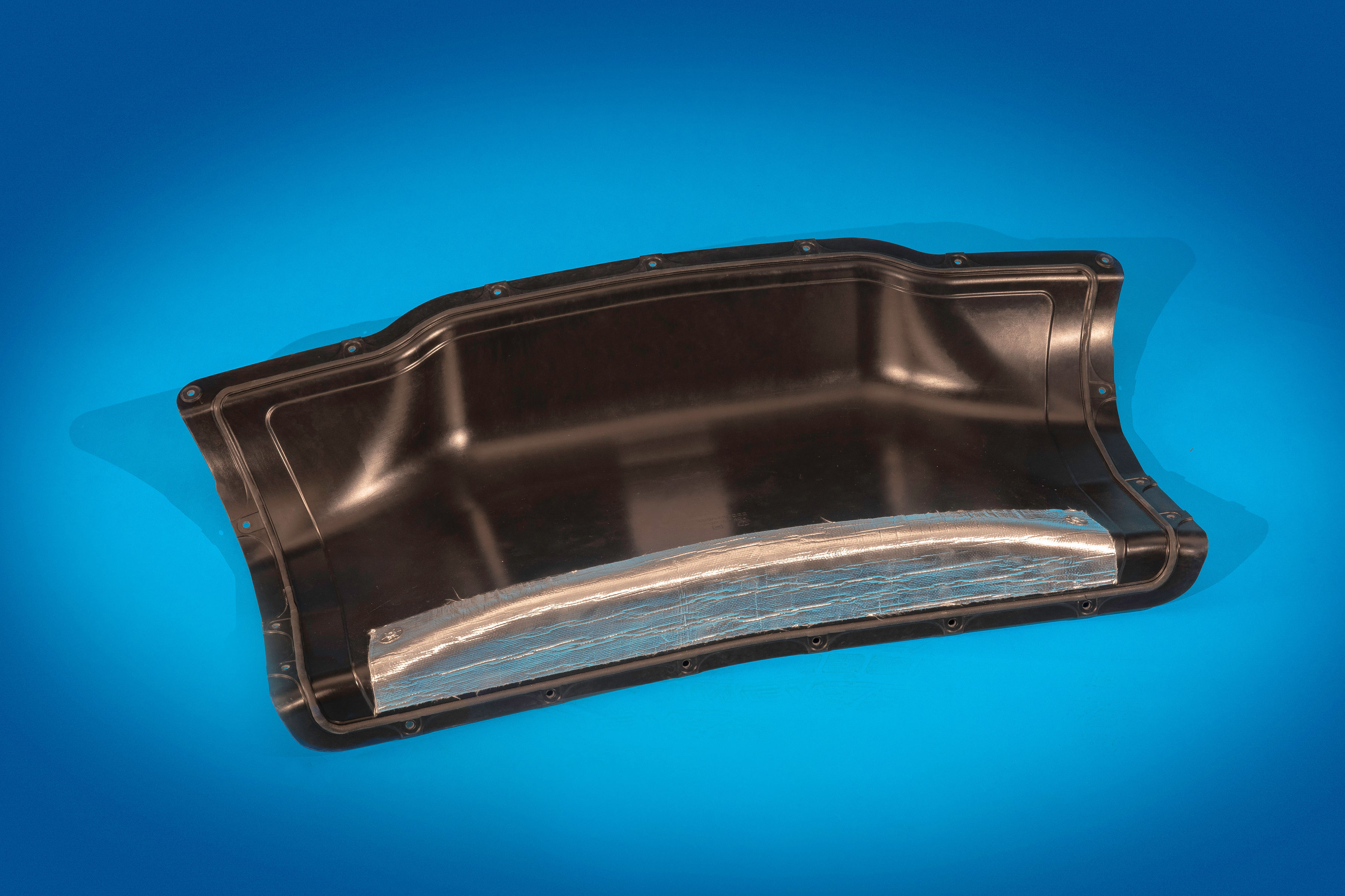
Outra inovação envolve o uso de uma junta de espuma elastomérica de silicone tixotrópica de uma parte aplicada na parte de trás das portas de serviço SMC, que estão localizadas no porta-malas traseiro (uma em coupés, duas em conversíveis), e permitem o acesso do cliente ao ar. sistema de filtro. Devido à proximidade com o compartimento do motor, o elastômero de espuma no local de alto desempenho (FIP) (Silastic 3-8186 da Dow, Inc., Midland, Michigan, EUA) foi especificado para sobreviver a temperaturas de uso contínuo de até 392 ° F / 200 ° C enquanto fornece uma vedação durável com excelente resistência à compressão, mesmo após ciclos repetidos de abrir / fechar. A GM relata que a maioria das outras espumas e gaxetas cortadas teria derretido ou quebrado sob exposição contínua a tais temperaturas. Após a dispensação, a gaxeta aplicada é tratada termicamente a 167 ° F / 75 ° C por 10 minutos para expandir a espuma, eliminando custos de corte e desperdício. As próprias portas são SMC temperadas (vidro 42% FVF em uma matriz VE-UP). Escudos térmicos, produzidos pela Gentex Corp. (Carbondale, Pa., US) usando tecidos de aramida Kevlar aluminizados resistentes ao calor e à abrasão (fibra de DuPont de Nemours, Inc., Wilmington, Del., US), fornecem interiores de porta com extras proteção térmica.

A GM também usou seu sistema de equilíbrio de roda de precisão totalmente automatizado de segunda geração no C8. Desenvolvido com a The 3M Co. (St. Paul, Minn., EUA) e a ESYS Automation (Auburn Hills, Michigan, EUA), os pesos de roda compostos de alta densidade (5,8-SG) com propriedades magnéticas personalizadas substituíram os pesos metálicos estampados tradicionais em aço pintado, zinco ou chumbo que possuem massa específica e devem ser aplicados manualmente sobre rodas. O novo sistema usa grandes carretéis de fita extrudada com adesivo que contém 67% em volume de liga de aço pós-industrial, resistente à corrosão e totalmente reciclável em uma base de fluoropolímero. O sistema automatizado examina cada roda e, em seguida, corta e aplica segmentos de fita de peso personalizado em incrementos menores e mais precisos para melhorar a direção e reduzir o desgaste dos pneus. Ele também reduz o tempo e o custo de montagem, simplifica o estoque, elimina sucata e mão de obra e é oferecido em mais cores do que pesos de metal.
Os tetos Coupé estão disponíveis em três níveis de acabamento:pintado, SMC temperado de baixa densidade (da CSP); policarbonato transparente com revestimento rígido (PC); e compósito de fibra de carbono com revestimento transparente / tecido exposto com bordas pintadas (da deBotech Inc., Mooresville, N.C.). A CSP também fornece vários painéis SMC 1.2-SG reforçados Classe A para sistemas de teto retrátil de modelo conversível.
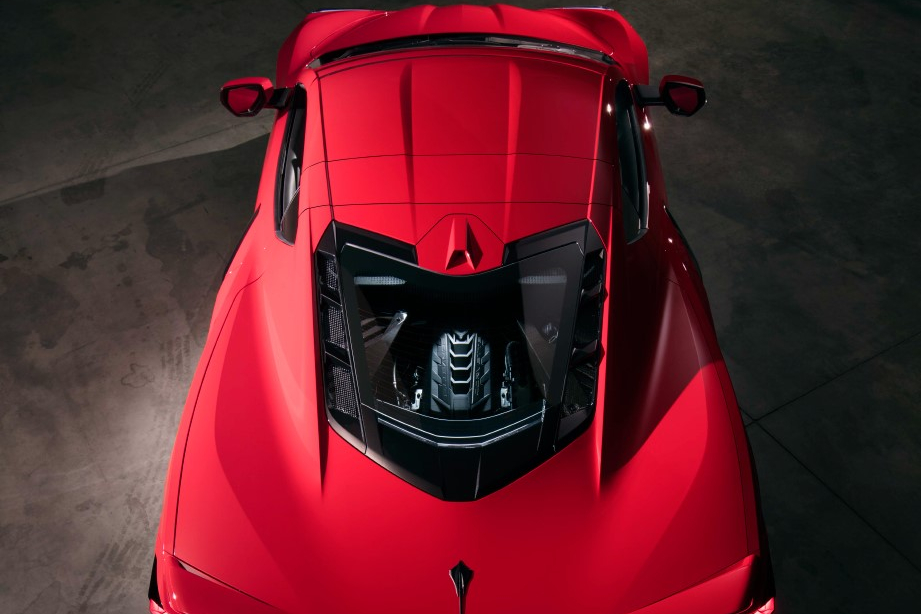
Outros painéis externos incluem painel frontal superior e inferior de poliolefina termoplástica pintada (TPO), o último com dutos integrados para direcionar o ar para os freios (pacote Z51 apenas) e trocadores de calor externos. A grade externa e as aberturas de resfriamento do freio são pintadas com acrilonitrila butadieno estireno (ABS).
O painel frontal superior traseiro é moldado em cor (MIC) TPO, mas o conjunto do painel frontal traseiro inferior é pintado de Classe A, 1.2-SG SMC (vidro / resina UP), devido à proximidade da peça com as pontas de exaustão quentes. O excelente desempenho mecânico da SMC permitiu à GM projetar uma saliência traseira curta sem suporte e use espaçamentos maiores entre os acessórios sem flacidez. O SMC também distribui cargas de maneira eficiente por uma área maior durante colisões traseiras de baixa velocidade do que os termoplásticos. Suportes e sensores traseiros de auxílio ao estacionamento são colados ao SMC. Esta é considerada a primeira vez que os pára-choques SMC são usados em veículos de alto volume.
Os apliques da porta traseira apresentam PC / ABS pintado para o painel superior, SMC com malha de alumínio para as aberturas laterais e um aplique inferior SMC para acomodar a carga térmica diretamente sobre o motor. Esses painéis SMC são produzidos pela Quantum Composites Inc. da LyondellBasell (Bay City, Mich., EUA). Os interruptores de liberação da maçaneta da porta são PC / ABS, enquanto a entrada de ar traseira é SMC. O carro básico ostenta um spoiler de ABS pintado e moldado por sopro e a grade de saída de ar traseira é moldado por injeção em ABS pintado. Os apliques do pilar A e do cabeçalho são pintados de ABS, assim como as tampas dos espelhos retrovisores externos e as grades de entrada do radiador. Dependendo do pacote opcional, um SMC reforçado na parte inferior da asa e um divisor / difusor dianteiro de TPO moldado por sopro ou composto de fibra de carbono - carbono / epóxi com revestimento transparente / tecido visível produzido por deBotech usando prepreg da Solvay Composite Materials (Alpharetta, Ga., US) - contribui para a estabilidade aerodinâmica adicional. Um difusor traseiro em SMC temperado combina com o painel traseiro inferior do SMC no SMC pintado de Classe A da MFG.
O pacote de acabamento de fibra de carbono premium apresenta vários acentos de fibra de carbono transparentes / trama visível por dentro e por fora, incluindo tampas de espelho, inserção da grade frontal, divisor dianteiro, asa de acessórios, tampas do compartimento do motor, placas de interruptor de porta interna, molduras de balancim, instrumentos moldura do painel do cluster, tampas das maçanetas, apliques de quarto e placa de controle de condução. Estes componentes são produzidos por deBotech, SMI Composites LLC (Comer, Ga., U.S.) e Plasan Carbon Composites (Wixom, Mich., U.S.).
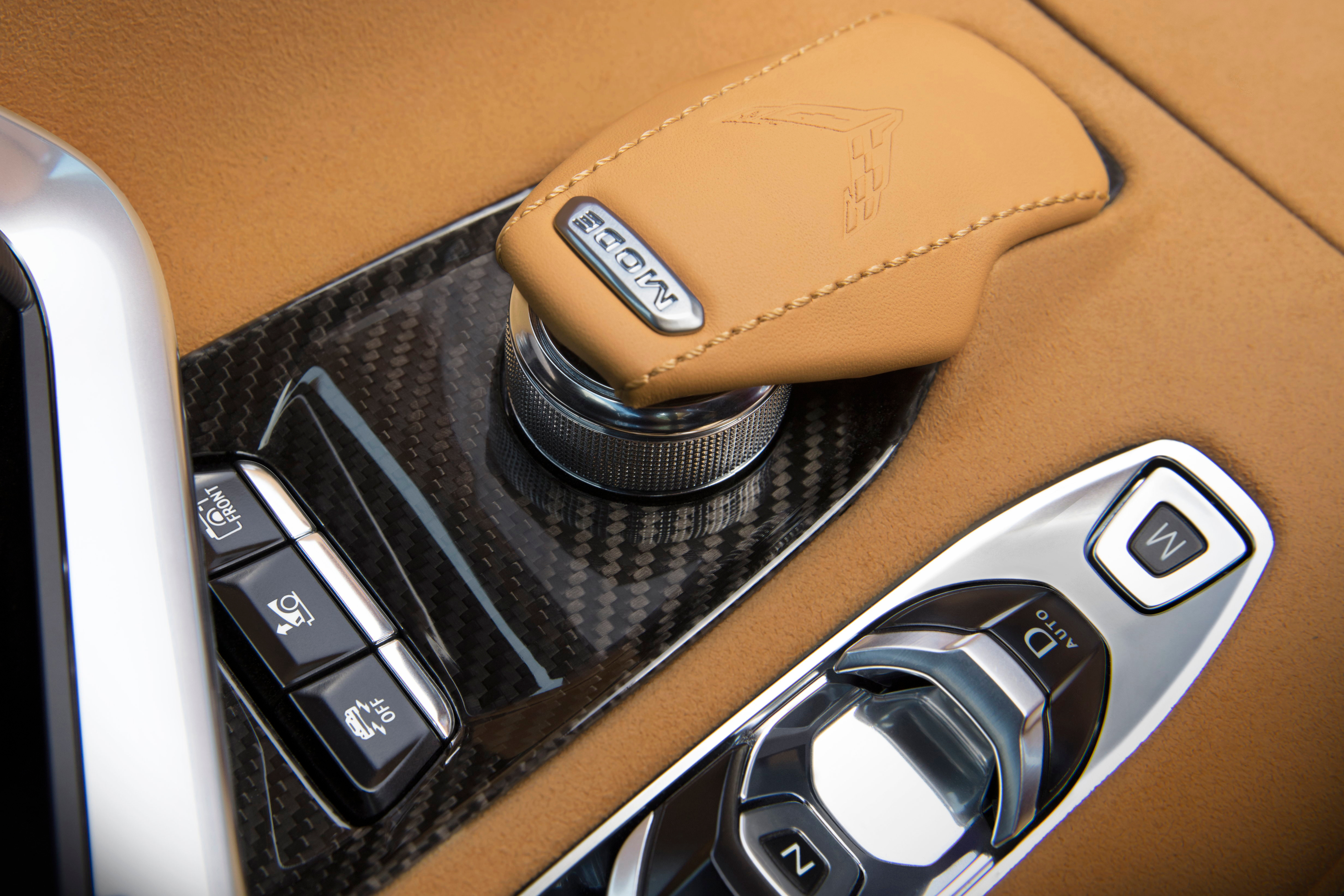
Tecnologia avançada
O Corveta 2020 já ganhou muitos prêmios da indústria de prestígio, incluindo 2020 MotorTrend Car of the Year, 2020 Automotive News PACE (Premier Automotive Supplier Contributions to Excellence) Prêmio de Parceria e vários prêmios da Society of Plastics Engineers (SPE), incluindo 2019 Vehicle Engineering Team Award . “Embora o novo Stingray’s arquitetura de motor intermediário tem dominado as manchetes, não importa onde o motor esteja - na frente ou atrás do motorista - por oito gerações, Corvetas sempre avançaram o estado da arte em tecnologia de materiais automotivos ”, acrescenta Tadge Juechter, engenheiro-chefe executivo da Global Corvette. “O avanço da tecnologia está no cerne do que fazemos.”
Resina
- 10 vantagens da computação em nuvem em 2020
- O futuro da impressão 3D:12 principais conclusões da AM Landscape Digital Conference 2020 da AMFG (Parte 1)
- Liderança de manutenção, Parte 3
- Introdução aos harmônicos:parte 1
- Sustentabilidade na fabricação - Parte 3
- Tendências e desafios de 2020 impactados pelo Covid-19:Parte I
- O giro é opcional
- O que é um número de peça?
- Usinagem de peças pequenas
- Cilindricidade em GD&T