Os compostos agilizam a fabricação de fachada de concreto
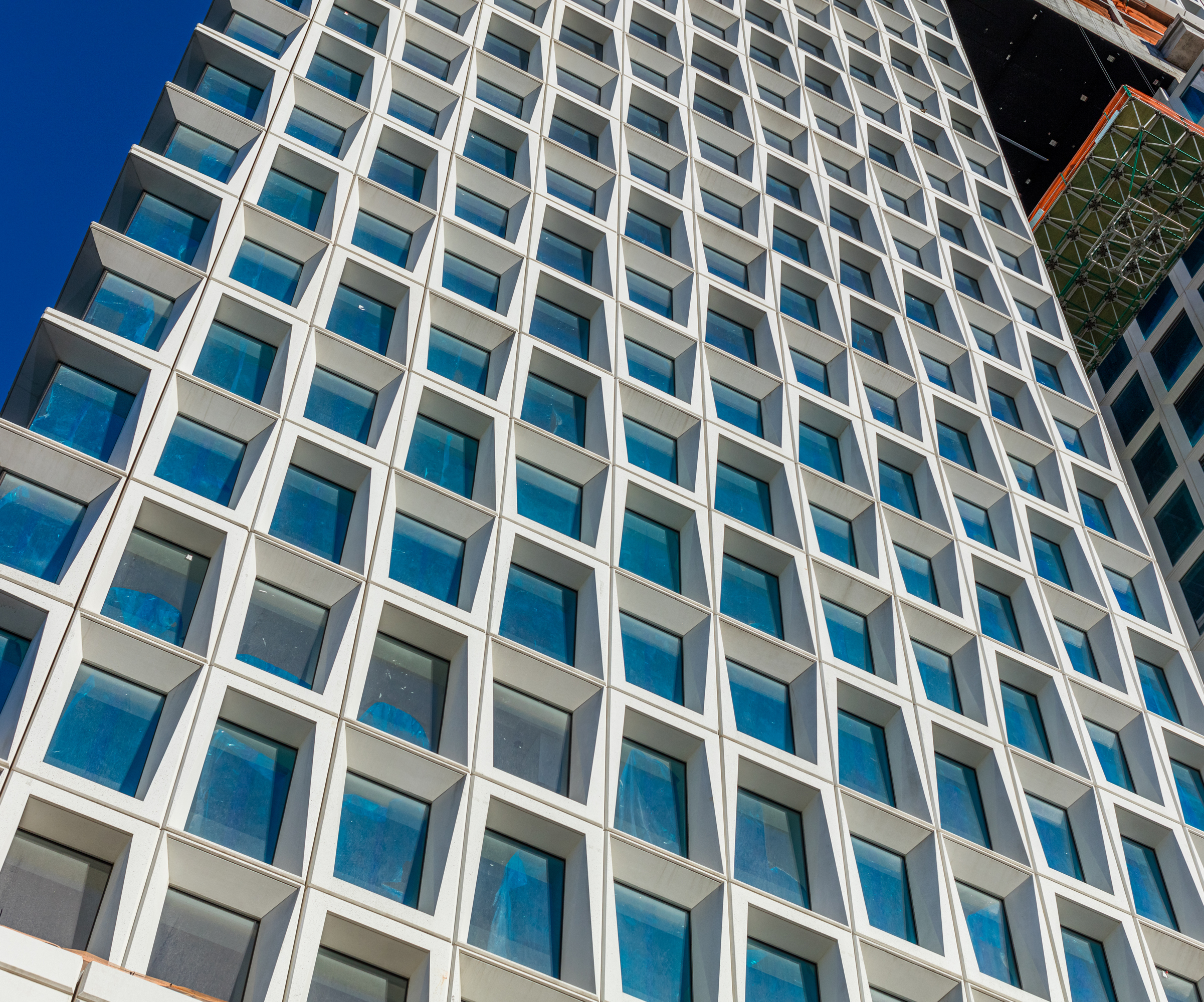
Cada edifício de vários andares construído hoje requer uma fachada. Derivado da palavra francesa fachada , que por sua vez veio do italiano facciata , significa "rosto". Em suma, a fachada é a estrutura exterior voltada para o público que confere ao edifício o seu carácter, cor e forma. Para os arquitetos, a fachada define o tom para o resto do edifício e diz muito sobre a intenção arquitetônica do designer.
Uma fachada também é funcional. Fornece a estrutura que envolve as janelas e portas, protege o edifício das intempéries e dos impactos e afeta a eficiência energética do edifício. Uma fachada pode ser construída com uma variedade de materiais, incluindo compostos, pedra, aço, vidro ou concreto. O concreto em uma fachada, em virtude de sua conformabilidade, pode ser usado para dar a um edifício uma aparência altamente dimensional e visualmente impactante, especialmente se as formas de concreto forem variadas.
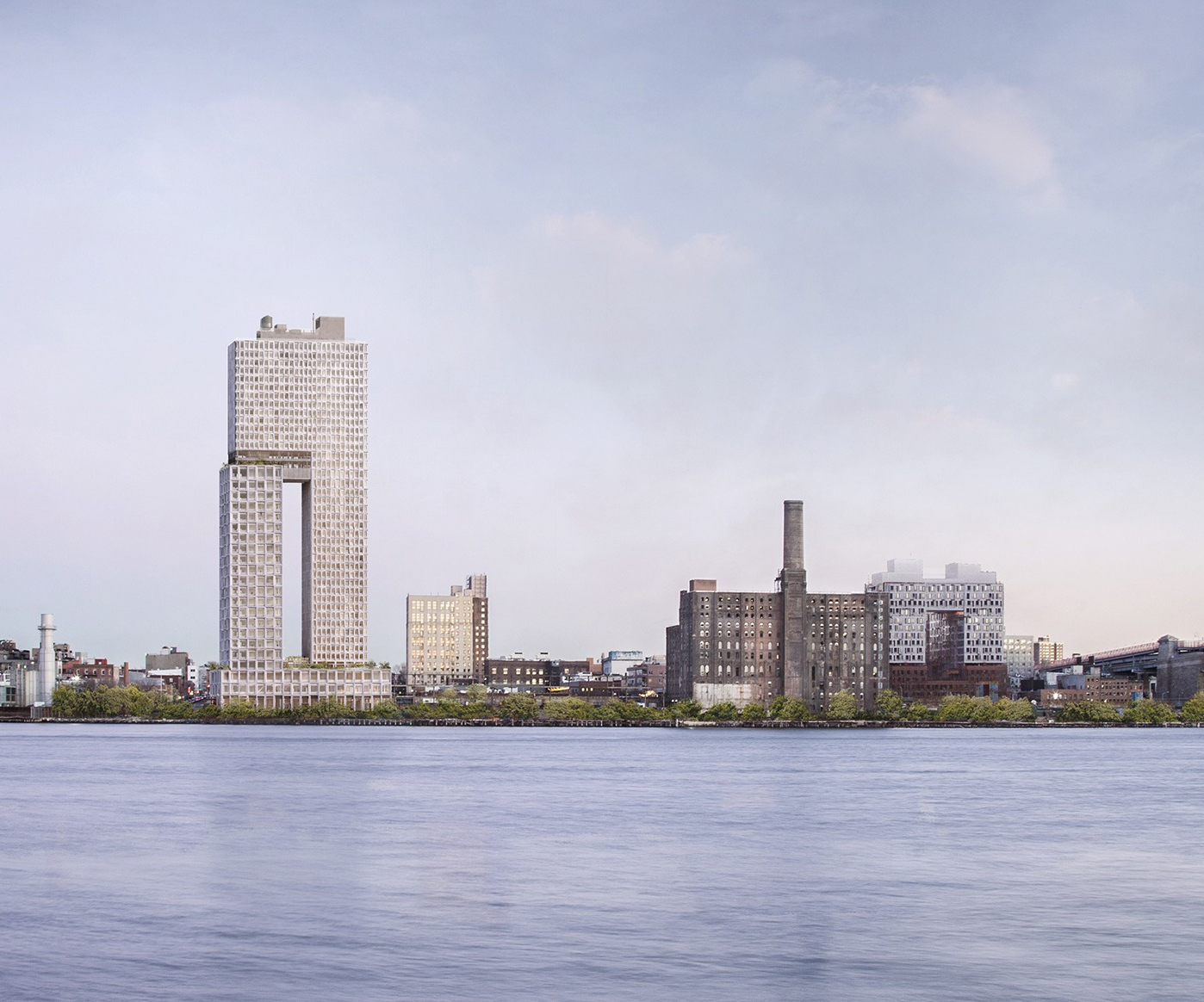
O açúcar é rei
Este foi o caso no Domino Park, um projeto de reconstrução de 4,5 hectares ao longo da orla de Williamsburg em Brooklyn, NY, EUA. No coração do Domino Park está a Refinaria de Açúcar Domino de 138 anos, que fechou em 2004 e agora está sendo reformada como escritório e espaço de varejo. Parte do Domino Park inclui vários novos edifícios, incluindo o One South First de 45 andares e o conjunto 10 Grand. Para esses edifícios, o arquiteto COOKFOX (New York, NY) decidiu usar uma fachada de concreto que apresenta vários ângulos de superfície, várias formas de moldura de janela e várias larguras de moldura de janela para, à distância, transmitir vagamente uma sensação de cristalinidade de açúcar, em mantendo a história do site.
A Gate Precast Co. (Jacksonville, Flórida, EUA) ganhou o contrato para construir a fachada de concreto - basicamente, uma série de caixilhos de janela - para o projeto One South First. A empresa iria, como é típico para uma fachada de concreto, fabricar as armações em suas próprias instalações e, em seguida, enviar as armações acabadas para o local de trabalho, onde seriam içadas no local para instalação por meio de um guindaste. Se a Gate tivesse decidido seguir a tradição, teria construído moldes de madeira para dar forma a todas as armações de concreto. Gate, no entanto, decidiu não seguir a tradição.
Para entender, volte a 2017, quando a Gate fez parceria com o Precast / Prestressed Concrete Institute (PCI, Chicago, Illinois, EUA) e o Oak Ridge National Laboratory (ORNL, Oak Ridge, Tenn., EUA) para realizar uma avaliação preliminar de o uso de manufatura aditiva de grande formato para construir moldes compostos para conformação de concreto pré-moldado na fábrica. Esta avaliação foi feita usando uma máquina BAAM (Big Area Additive Manufacturing) da ORNL. BAAM é uma máquina de manufatura aditiva de grande formato com um envelope de construção de 25 metros quadrados, co-desenvolvida por ORNL e Cincinnati Inc. (Harrison, Ohio, EUA) Gate comprometida em construir moldes compostos para a fachada One South First. O projeto exigiu um total de 80 moldes, dos quais 37 seriam impressos. Os 43 restantes seriam feitos de madeira. Quando essa decisão foi tomada, os prazos para entrega do molde eram apertados.
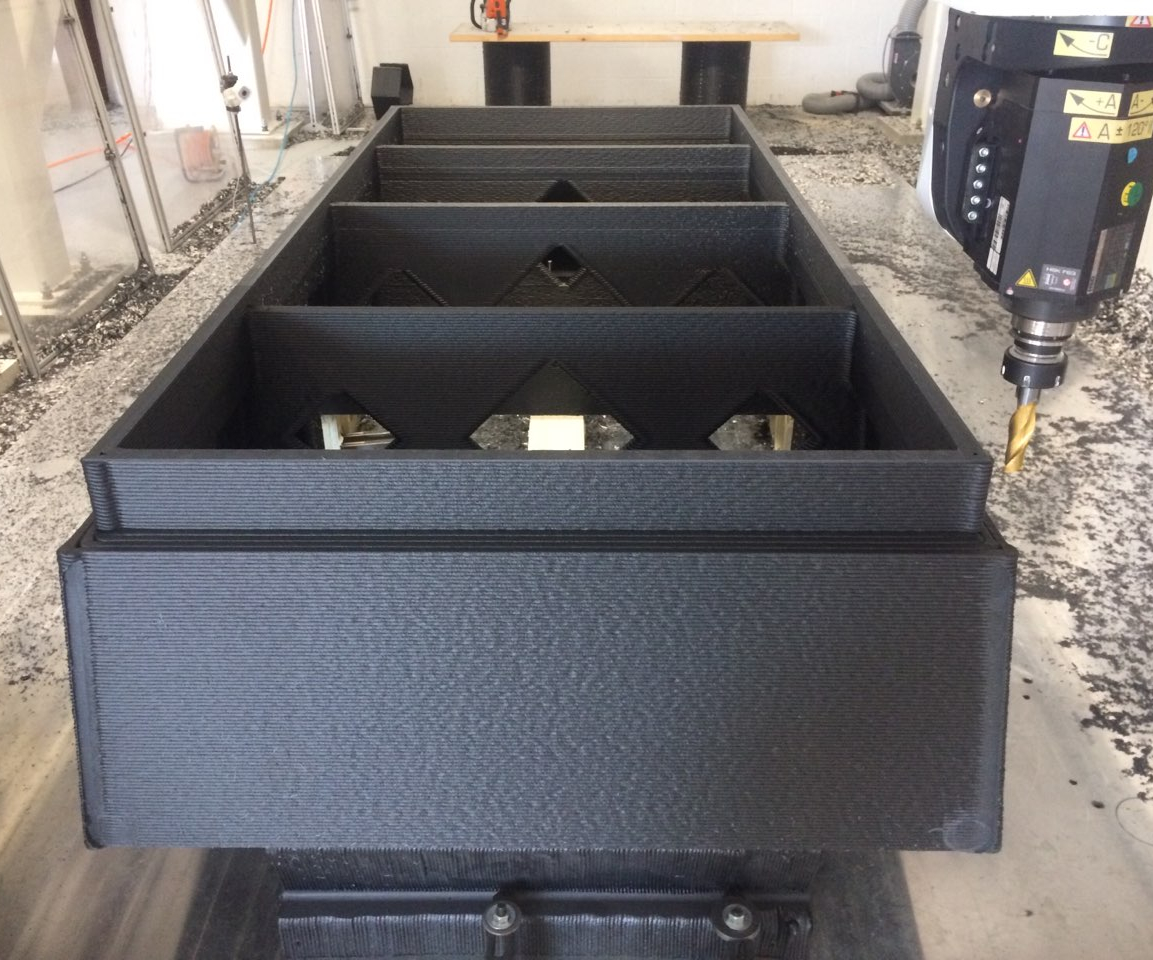
Em 2016, a Additive Engineering Solutions (AES, Akron, OH) adquiriu sua primeira máquina BAAM da Cincinnati Inc. Por causa disso, a ORNL e a Gate Precast recorreram à AES para obter ajuda. Andrew Bader, VP e cofundador da AES, diz que sua empresa e a ORNL dividiram o pacote de trabalho, com a AES produzindo 18 dos 37 moldes. Bader diz que cada molde de moldura de janela mede cerca de 5-6 pés de largura, 9-10 pés de altura e 16 polegadas de profundidade e pesa cerca de 500 libras.
Bader afirma que o interior da geometria dos moldes, por serem projetados para produzir esquadrias que circundam as janelas retangulares, era relativamente simples. No entanto, o desenho das superfícies externas das esquadrias, como se observou, era mais complexo, com profundidades e ângulos variados integrados em cada molde. Uma forma impressa substituiu a forma de madeira composta de muitas peças cortadas individualmente e pregadas juntas. “A geometria era simples, mas complicada”, diz Bader. “O projeto exigia vários designs de estrutura exclusivos, dependendo da localização da estrutura.”
Para parte de sua produção, a AES escolheu um composto LNP THERMOCOMP AM, um material de alto módulo e baixo empenamento baseado em ABS com 20% de reforço de fibra de carbono picada fornecido pela SABIC (Houston, Tex., EUA). Bader diz que a máquina BAAM levou de 8 a 10 horas para construir cada molde monolítico, seguido por 4-8 horas de usinagem e acabamento em uma máquina CNC Quintax (Stow, Ohio, EUA). Ele relata que os moldes foram lixados nas dimensões exigidas, mas não selados.
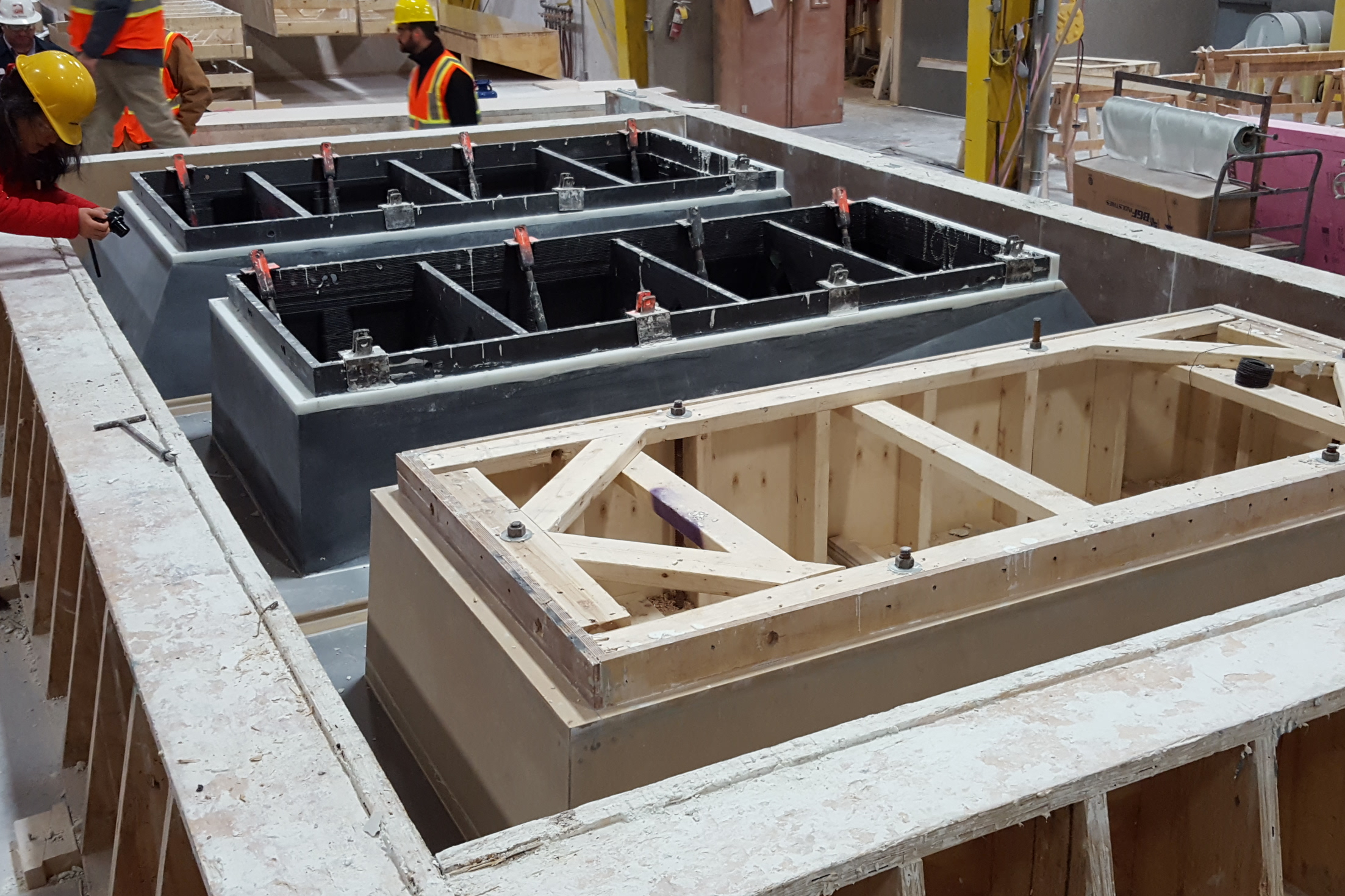
Fabricação de caixilhos de janelas
Os moldes foram entregues na instalação da Gate Winchester, Ky., EUA, onde foram usados junto com os 43 moldes de madeira tradicionais que a Gate construiu para o projeto. Os moldes de madeira foram montados manualmente pelos funcionários da Gate, em seguida, uma esteira de fibra de vidro e uma camada de resina foram aplicadas, com óleo de fôrma pulverizado para facilitar a liberação da estrutura de concreto formado. O óleo da forma também foi pulverizado nos moldes de compósitos para facilitar a liberação.
Para realizar um vazamento de concreto, vários moldes foram colocados em uma mesa de fundição de madeira de 12 a 50 pés de comprimento. Os moldes foram agrupados para produzir uma única moldura, uma moldura dupla ou uma moldura tripla. O vergalhão de aço foi posicionado dentro de cada molde e o concreto foi derramado ao redor do vergalhão. A mesa de fundição foi então vibrada para consolidar o concreto. Após 14-20 horas de cura, os caixilhos das janelas foram desmoldados, lavados com ácido e polidos. Em seguida, as janelas foram instaladas e todo o pacote foi enviado de caminhão até o canteiro de obras no Brooklyn.
Bader diz que os moldes de compósito AES, trabalhando lado a lado com os moldes de madeira tradicionais, revelaram rapidamente suas vantagens. Primeiro, diz ele, um molde de madeira permite apenas 15-20 vazamentos de concreto antes de precisar ser retirado de serviço e reformado ou substituído. Os moldes AES, por outro lado, permitiam 200 vazamentos de concreto com reforma mínima ou tempo fora de serviço. E os 200 derramamentos, diz Bader, representaram o fim do projeto, não o fim da vida útil do molde. “É exatamente aí que eles pararam”, diz ele. “Se os nossos moldes forem bem cuidados, pensamos que podem ser usados centenas e centenas de vezes.”
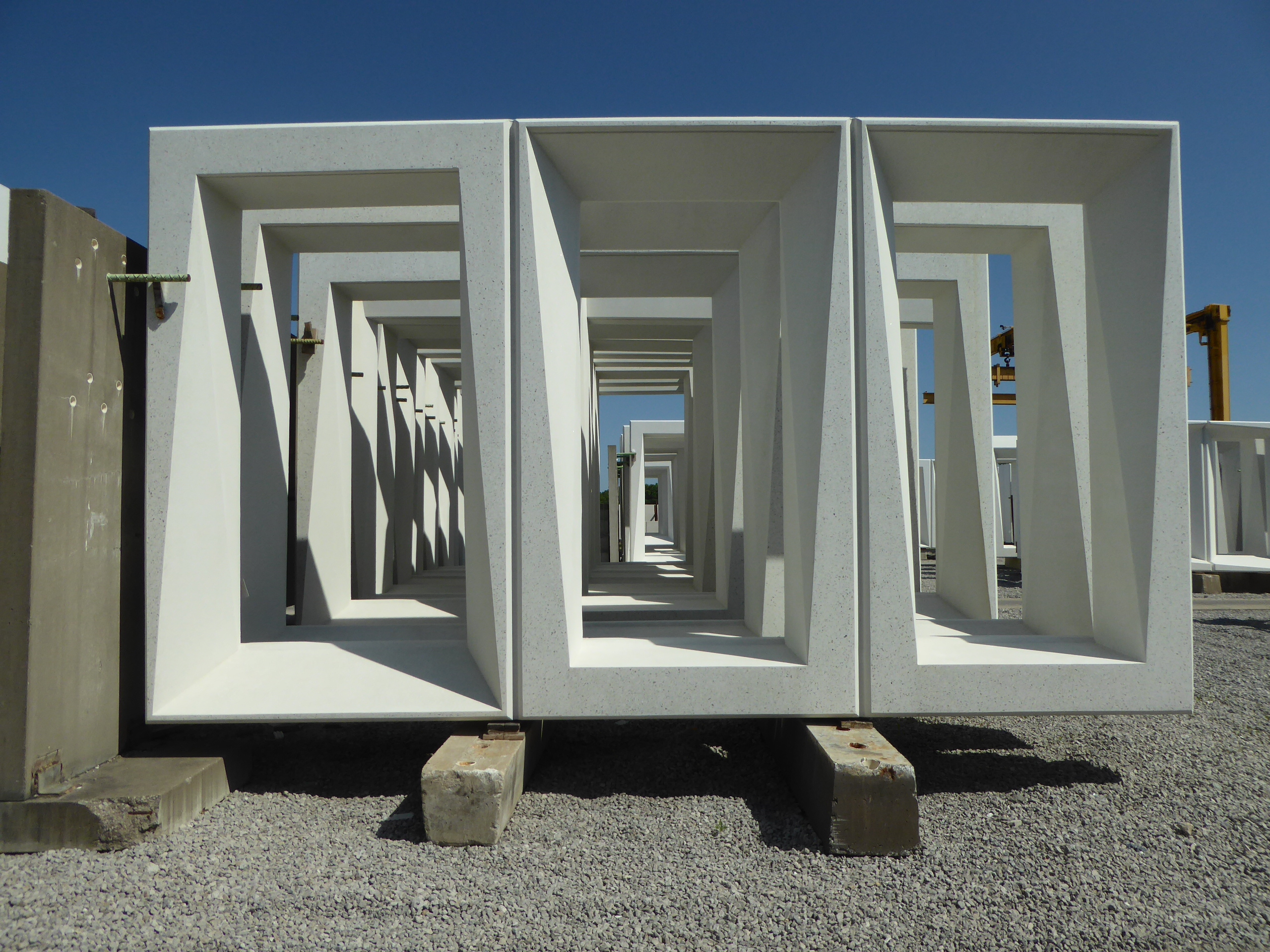
Além disso, para o uso de 150 doses ou mais, Gate calcula que seriam necessários até 10 moldes de madeira para atender ao desempenho de um molde AES. Além disso, dado que a Gate 40 horas-homem para produzir um molde de madeira, sem os 37 moldes de compósito a empresa não teria cumprido os requisitos de cronograma do projeto One South First.
Bader admite que um molde de composto AES custa quatro vezes mais que um molde de madeira, mas é pelo menos 10 vezes mais durável. “A forma como as formas pré-moldadas foram construídas permaneceu relativamente inalterada por décadas”, afirma Bader. “De repente, um dia, estávamos fazendo formas 3D de 500 libras e todos ficaram chocados.” Dito isso, ele reconhece que a fabricação aditiva de tais moldes é a mais econômico em aplicações onde as formas de concreto têm geometria complicada ou alta repetição - a mesma forma muitas vezes.
AES, relata Bader, agora possui e opera quatro máquinas BAAM e pode produzir peças de até 2,5 metros de altura. Peças muito maiores foram construídas pela união de várias peças.
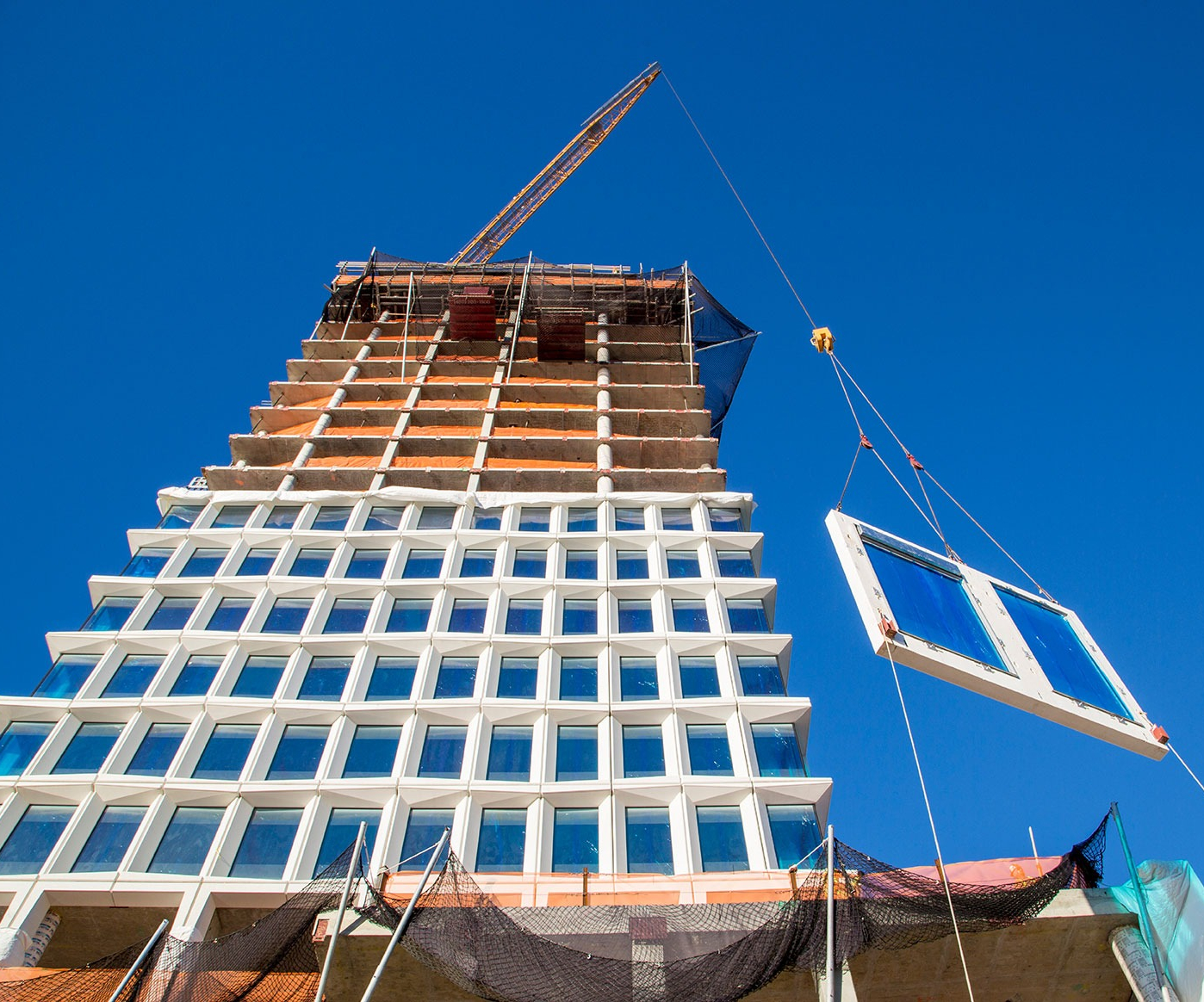
Resina
- Velocímetro
- Concreto
- CompositesWorld SourceBook 2022
- Resolução de problemas de termoformação de compósitos termoplásticos
- A evolução dos compostos aditivos
- Compostos termoplásticos:Suporte de pára-choque estrutural
- ATL Composites contribui para o projeto de remediação do pilar de concreto
- RS Electric Boats seleciona Norco para a fabricação de compostos
- Compósitos termoplásticos de soldagem
- Compostos de alto desempenho em Israel