Avançando compósitos termoplásticos e RTM para Clean Sky 2 na Espanha

O EURECAT Centro Tecnológico de Catalunya (Centro de Tecnologia EURECAT da Catalunha, Barcelona, Espanha) é uma organização privada de P&D sem fins lucrativos com 11 instalações, 650 funcionários e 50 milhões de euros em receitas anuais. “É o segundo maior centro de P&D da Espanha”, explica Angel Lagraña Hernandez, diretor do programa para o mercado aeronáutico e espacial da EURECAT. Ele explica que parte da receita da EURECAT é proveniente do governo catalão e do restante, metade deve vir de empresas privadas - em sua maioria pequenas e médias empresas (PMEs) - enquanto a outra metade pode ser pública, como financiada pela União Europeia Programa Clean Sky 2. “Agora temos 18 projetos Clean Sky”, observa Lagraña, “que foram premiados exclusivamente com base em inscrições competitivas em resposta a chamadas de propostas”.
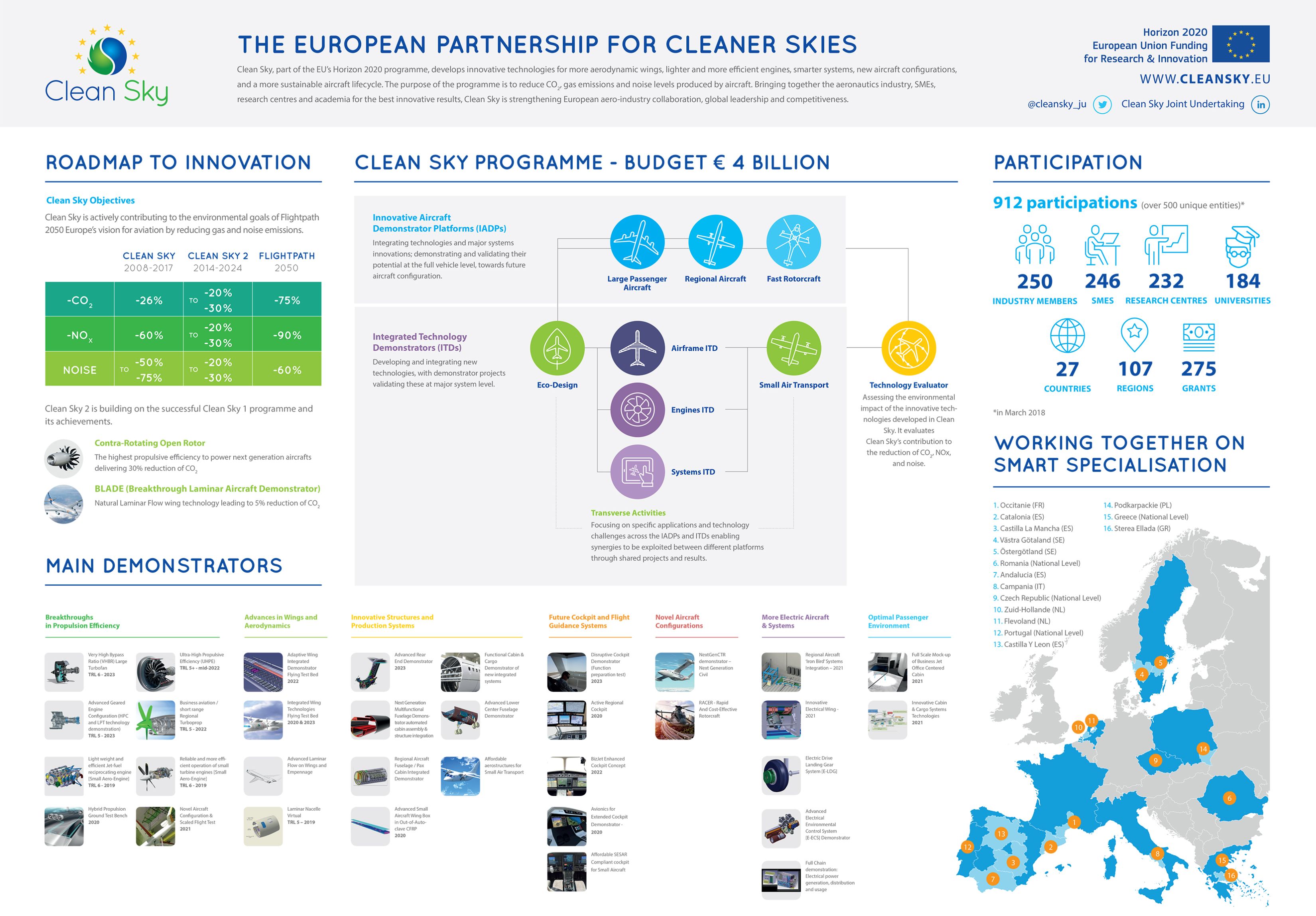
Exemplos de como os compostos aparecem nos diversos objetivos e demonstradores de tecnologia planejados da Clean Sky 2 incluem:
- Demonstrador de fuselagem multifuncional de última geração - aproveitando termoplásticos para céus mais limpos
- Economia circular:toma forma a fuselagem composta para aeronaves regionais
- Aproveitando a experiência em corridas de automóveis para o FastCan da Clean Sky
“EURECAT é altamente transversal, atuando nas indústrias automotiva, ferroviária e outras, além de sua atuação na indústria aeroespacial”, diz Lagraña. “Ele também tem muitas atividades em TI, como análise de dados e blockchain, etc. Composites 4.0 é uma de suas áreas estratégicas.” Em compósitos, ele observa que EURECAT funciona principalmente em tecnologias fora de autoclave (OOA). “Nós nos concentramos em termoplásticos e moldagem por compressão de líquido, incluindo monitoramento de processo em tempo real, incluindo monitoramento da temperatura de transição vítrea (Tg) da resina durante o processamento.” (Continue lendo a seção COFRARE, no final deste blog, para saber mais sobre esse monitoramento de Tg.)
Os projetos mais recentes relacionados a compósitos da EURECAT no Clean Sky 2 incluem:
- KEELBEMAN para demonstrar uma viga de quilha composta termoplástica (Este projeto recebeu financiamento da Empresa Comum Clean Sky 2 no âmbito do programa de pesquisa e inovação Horizon da União Europeia sob o GAP n ° 785435 KEELBEMAN) ;
- WINFRAME 4.0 construir caixilhos de janela de compósito termoplástico (TPC) para o demonstrador Green Regional Aircraft (GRA) na Clean Sky (2008-2017) e estendido para o Regional Aircraft IADP (Innovative Aircraft Demonstrator Platform) em Clean Sky 2 (2014-2024);
(Este projeto recebeu financiamento da Empresa Comum Clean Sky 2 no âmbito do programa de investigação e inovação Horizon da União Europeia ao abrigo do GAP n ° 821323 WINFRAME 4.0.) - COFRARE 2020 para armações de fuselagem termofixas feitas usando moldagem por transferência de resina (RTM) com laços de cisalhamento TPC.
(Este projeto recebeu financiamento da Empresa Comum Clean Sky 2 no âmbito do programa de investigação e inovação Horizon da União Europeia ao abrigo do GAP n ° 821261 COFRARE 2020.)
Viga de quilha composta termoplástica
Clean Sky 2 - JTI-CS2-2017-CFP06-LPA-02-20. Duração do projeto:março de 2018 a dezembro de 2019
O objetivo do projeto KEELBEMAN é desenvolver uma estrutura de quilha orientada para a fabricação para uma aeronave do tipo A320 que permita altas taxas de produção de aeronaves, mas a um custo acessível por meio de compostos termoplásticos. Além de EURECAT como coordenador do projeto, os parceiros incluem:
- Airbus (Toulouse, França) como gerente de tópico
- CETMA (Centro Europeu de Pesquisa para Design de Tecnologias e Materiais, Brindisi, Itália)
- Grupo de Engenharia CT (CT Ingenieros, Madrid, Espanha), uma empresa com vários escritórios globais que tem um contrato de vários anos com a Airbus para o desenvolvimento de aeronaves, como pesquisas na fuselagem, asas e traseira por meio de seu escritório em Hamburgo, Alemanha; pesquisa na extremidade traseira (Espanha); pesquisa sobre fuselagem e estruturas relacionadas à usina (Toulouse, França) e desenvolvimento de asas (Bristol, Reino Unido)
- Sofitec (Sevilla, Espanha), especialista em fabricação e montagem de aeroestruturas com expertise e capacidade de produção em compósitos.
O CT Engineering Group forneceu modelagem completa da geometria da viga da quilha por meio de seu escritório em Toulouse, enquanto a Sofitec desenvolveu a inspeção de teste não destrutivo (NDT). “Isso é muito desafiador com essa estrutura de caixa fechada”, destaca Lagraña.
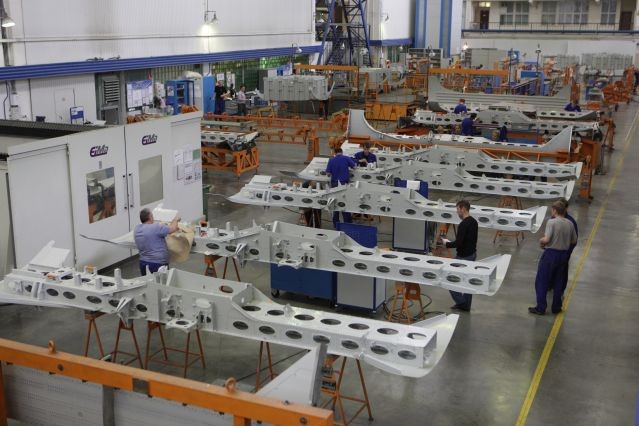
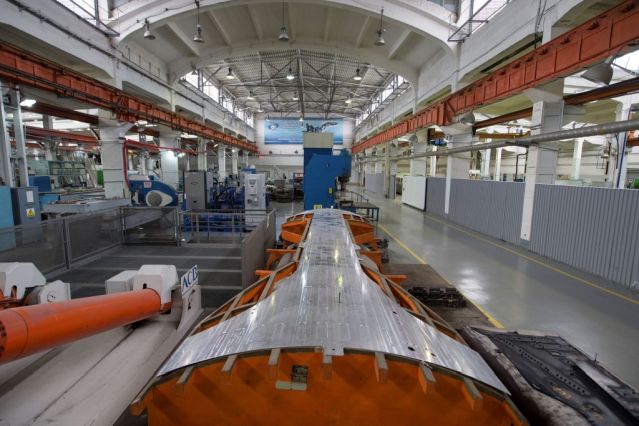
Aqui é mostrado o conjunto de viga de quilha A320, feito em metal pela Irkut Corporation (Moscou, Rússia). A Irkut supostamente assinou um contrato com a Airbus em 2004 para fornecer componentes, incluindo o compartimento do trem de pouso do nariz, a quilha e a pista do flap, que estão instalados, em média, em cada três aeronaves da família A320. FONTE | Irkut
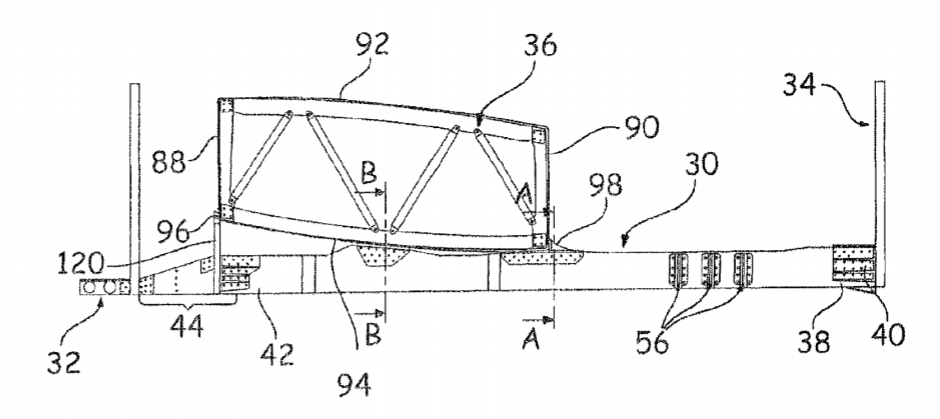
Desenvolvimento de estruturas de vigas de quilha
“Hoje, a maioria das vigas de quilha das aeronaves são feitas de metal, exceto para o Airbus
A350, que é um composto monolítico de fibra de carbono ”, diz Lagraña. “Isso requer um grande número de rebites e uma quantidade significativa de tempo para a montagem.” Ele explica que a viga da quilha é uma estrutura crítica na fuselagem, “Houve casos em que a viga da quilha quebrou durante o pouso, fazendo com que toda a fuselagem se partisse e se partisse.
De acordo com um artigo de 2011 de Steve Wilhelm, a viga de quilha do A350 é 70% composta, 54 pés (16,5 metros) de comprimento, junto com 10.000 fechos, pesa 1,2 toneladas e forma a espinha dorsal da aeronave. Wilhelm observa que a aeronave Boeing 787 competitiva "não depende de uma estrutura de quilha tão robusta, porque mais da resistência do casco vem de barris compostos que são presos juntos de ponta a ponta". O artigo então cita Michel Merluzeau, sócio-gerente da consultoria aeroespacial G2 Solutions LLC (Kirkland, Wash., EUA), que descreve o projeto do Airbus como "mais convencional" e "menos arriscado", mas aponta que a quilha é "essencial para o integridade estrutural dessa aeronave. ”
Na verdade, a Airbus foi pioneira em uma viga de quilha composta para o A340 em 2001. Mas, conforme descrito acima, o alto número de rebites necessários contraria a economia de peso possível com o uso de compostos. Assim, um objetivo importante no projeto KEELBEMAN é minimizar os fixadores usando componentes de compósitos termoplásticos que são soldados entre si.
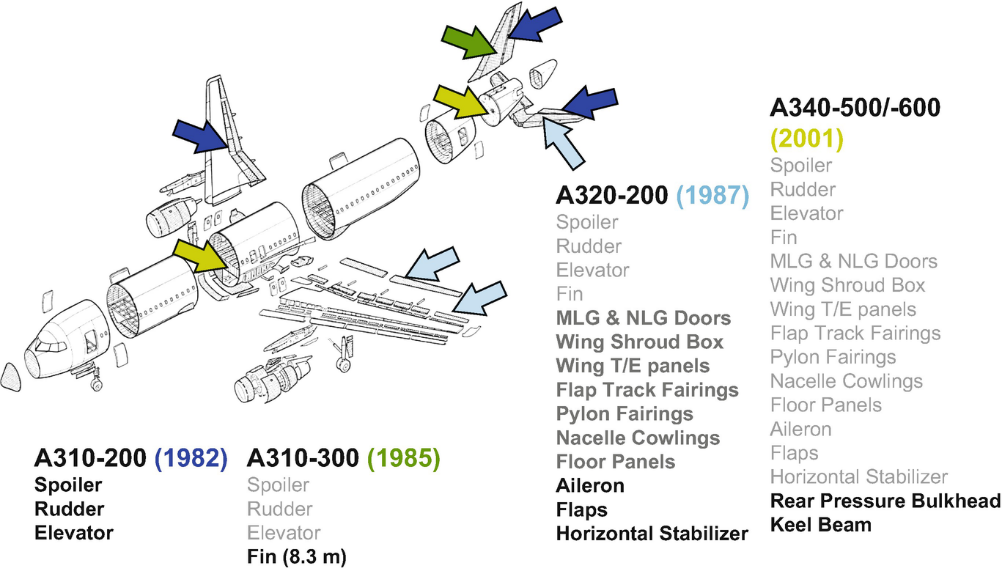
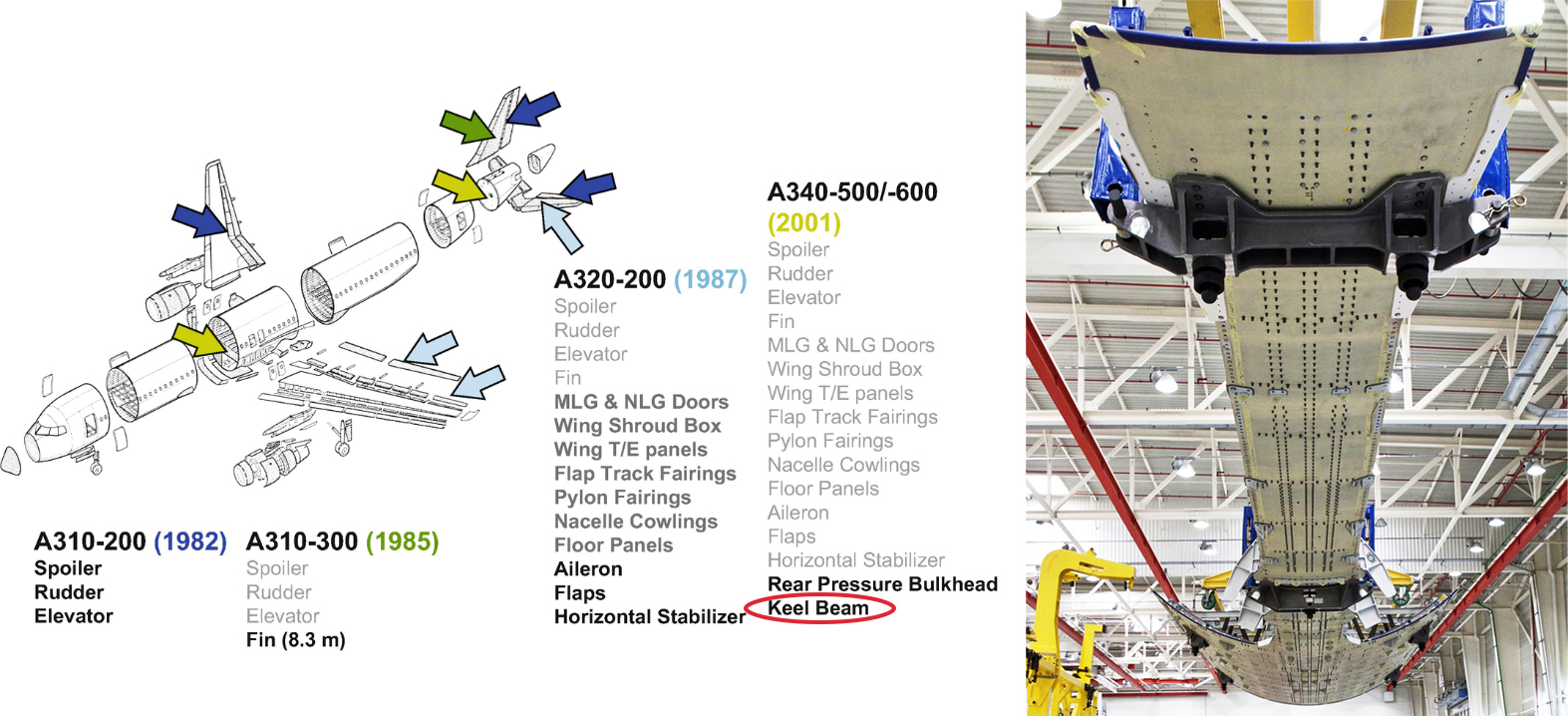
viga de quilha TPC
“O desenvolvimento de uma viga de quilha de composto termoplástico usando solda para montagem faz parte do desenvolvimento da Airbus da aeronave de amanhã, que inclui programas como Asa do Amanhã e Fuselagem do Amanhã”, diz Lagraña. “Dentro da KEELBEMAN, produzimos uma seção de demonstração de 250 milímetros por 500 milímetros por 1 metro de comprimento de uma viga de quilha com longarinas e demonstramos a viabilidade de soldar esta estrutura com o máximo de automação possível.”
Lagraña observa que as placas de parede do demonstrador e longarinas foram feitas usando fita unidirecional (UD) de fibra de carbono / polietercetonecetona (PEKK) em um processo de moldagem por compressão contínua (CCM) desenvolvido pela CETMA (ver "Moldagem por compressão de grau aeroespacial" e "PEEK vs. PEKK vs. PAEK e moldagem por compressão contínua ”). “Também há nervuras para reforços transversais que foram feitas usando a moldagem por compressão não isotérmica tradicional da EURECAT”, acrescenta Lagraña.
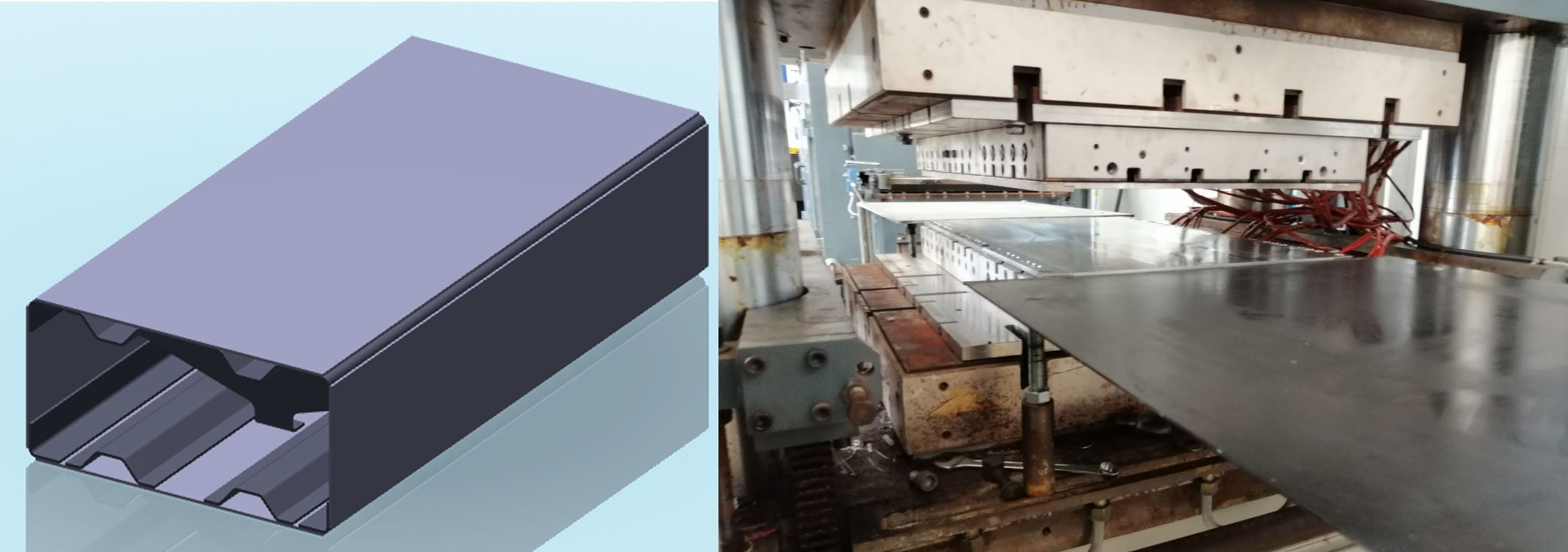
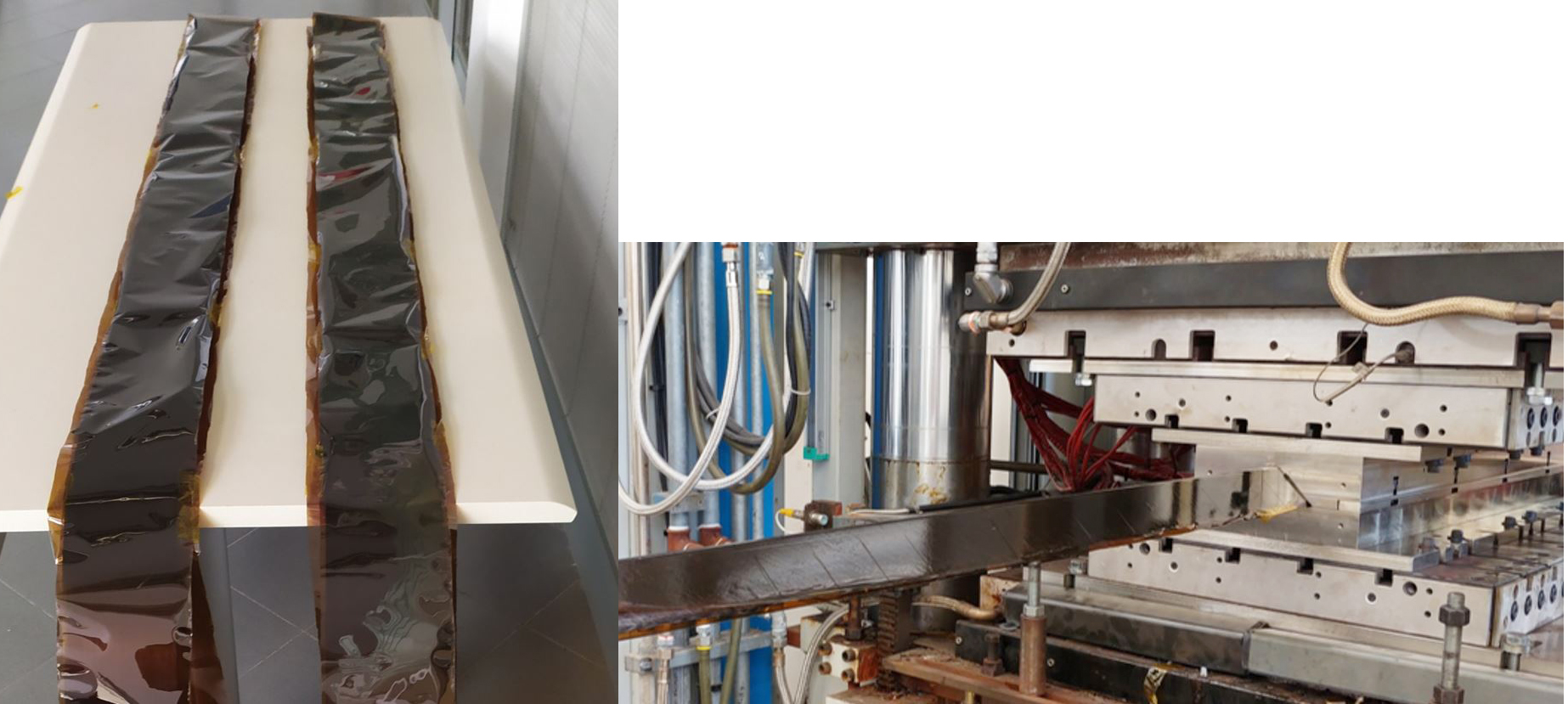
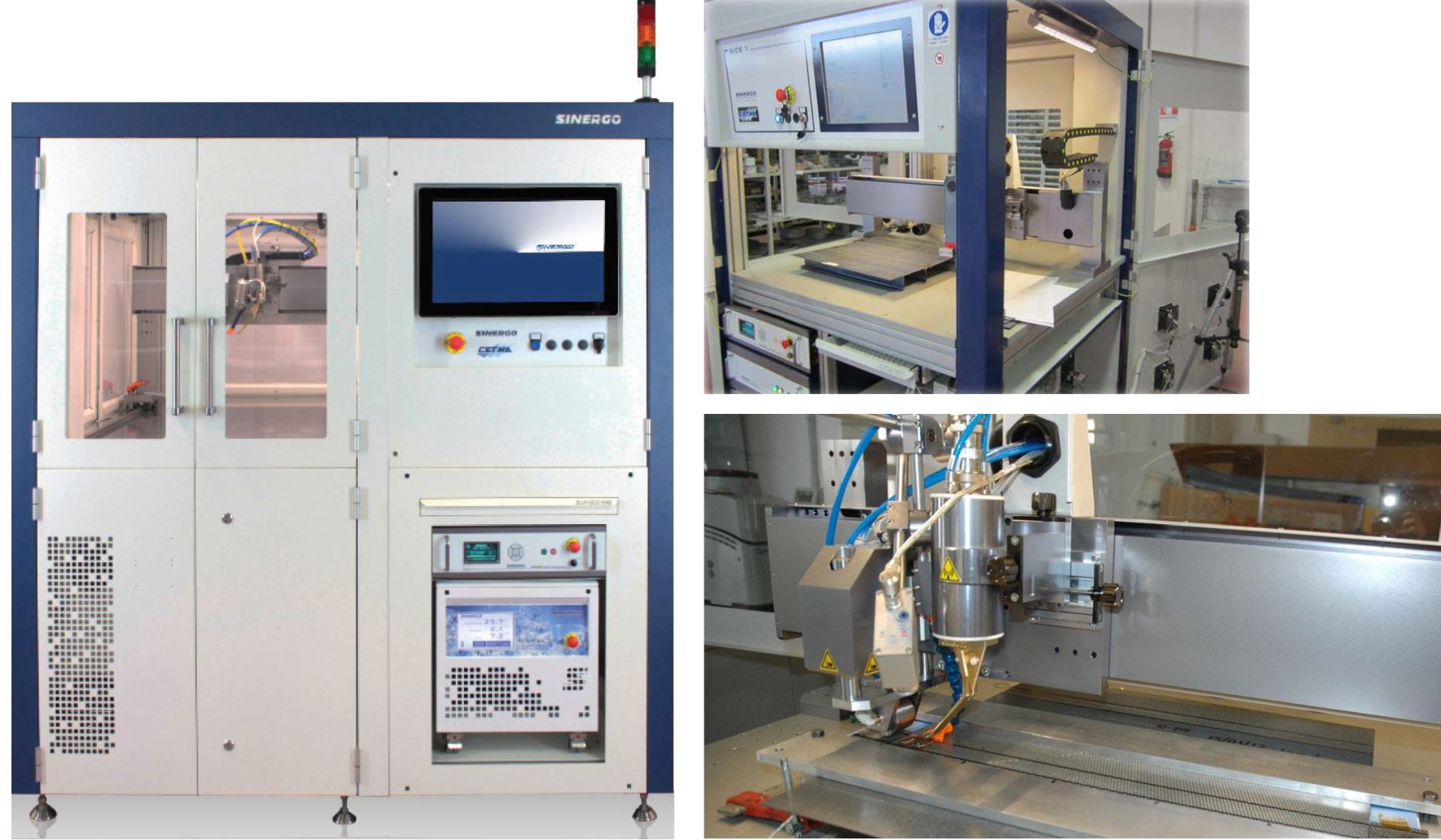
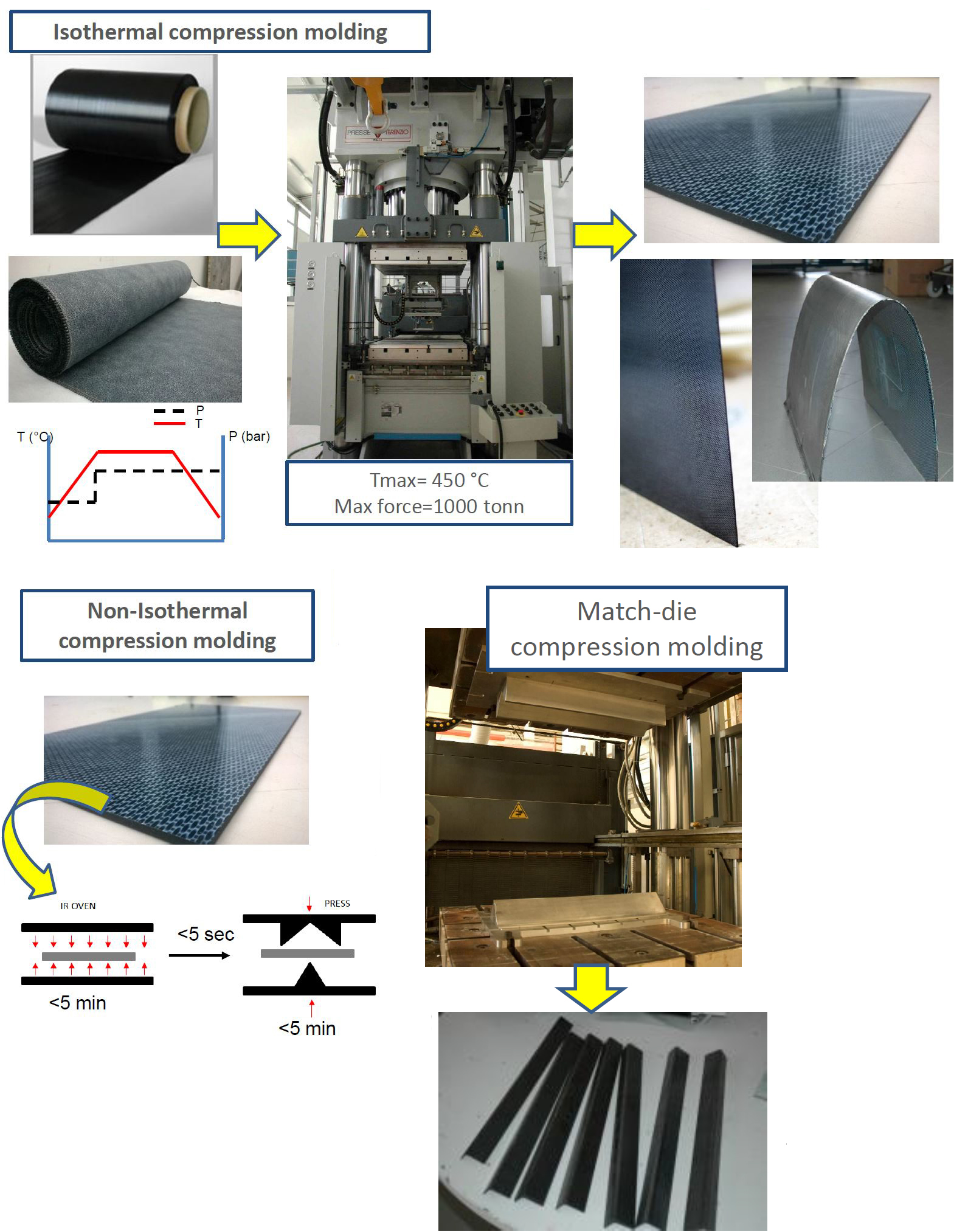
Soldagem por indução como principal habilitador
Lagraña observa que a CETMA desempenhou um papel fundamental não só na produção de peças para a KEELBEMAN, mas também na montagem do demonstrador usando sua máquina e tecnologia de solda por indução patenteada. Esta soldagem foi originalmente desenvolvida no projeto ECO FAIRS do primeiro programa Clean Sky (2011-2014), juntamente com a moldagem por compressão isotérmica e não isotérmica de estruturas TPC mostradas acima. Na ECO FAIRS, a CETMA usou todas essas tecnologias para produzir um demonstrador de protótipo baseado no painel superior existente (painel de pele endurecida com longarina) de uma cauda de helicóptero Agusta Westland, bem como um demonstrador de carenagem de patrocínio curvo. Embora estes tenham sido feitos usando CETEX (fornecido pela TenCate, agora Toray Advanced Composites) T300 3K 5HS têxtil de fibra de carbono com filme PPS (sulfeto de polifenileno) de dupla face, o CETMA também provou soldagem por indução com compósitos PEEK e PEI.
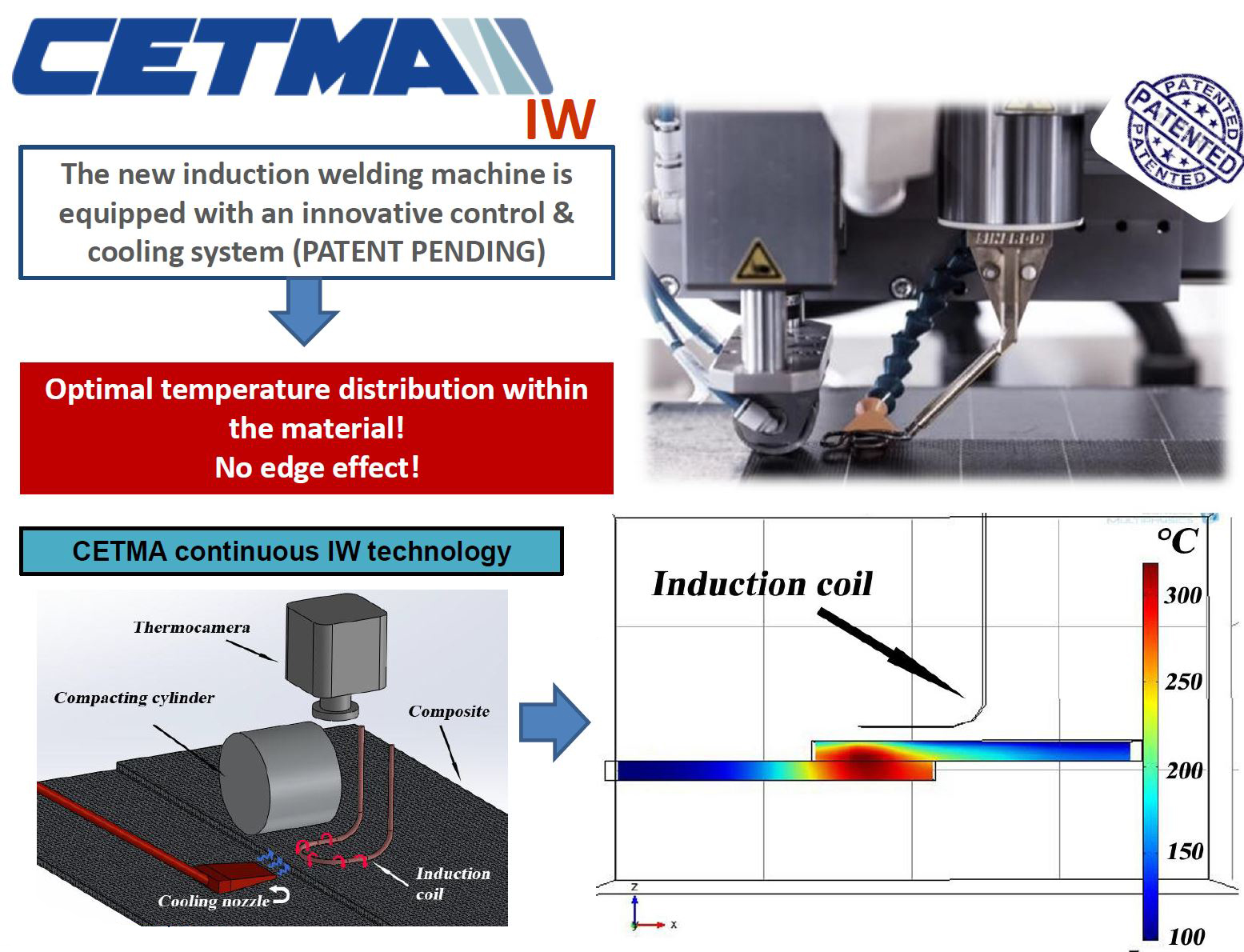
O CETMA selecionou a soldagem por indução (IW) como a mais promissora das técnicas de soldagem de compósitos termoplásticos e trabalhou com o especialista em soldagem e engenharia eletrônica SINERGO srl (Valdobbiadene, Treviso, Itália) para desenvolver uma nova máquina de soldagem por indução. A máquina SICE 1 WIDE com base em pórtico oferecida pela SINERGO (ver imagem abaixo) é capaz de soldar continuamente peças de qualidade aeroespacial de até 1 metro por 1 metro. Inclui um sistema de controle robusto para garantir que as distribuições de temperatura otimizadas sejam obtidas dentro dos materiais que estão sendo soldados. A máquina é equipada com um cilindro resfriado para aplicar pressão de consolidação e com um sistema de resfriamento a ar para remover o calor quando necessário, como nas bordas, onde o fluxo das correntes parasitas elétricas induzidas é restringido, resultando em alta densidade de corrente e superaquecimento . Também é possível instalar a cabeça de soldagem por indução CETMA em um braço robótico de 6 eixos para soldar formas geometricamente complexas.
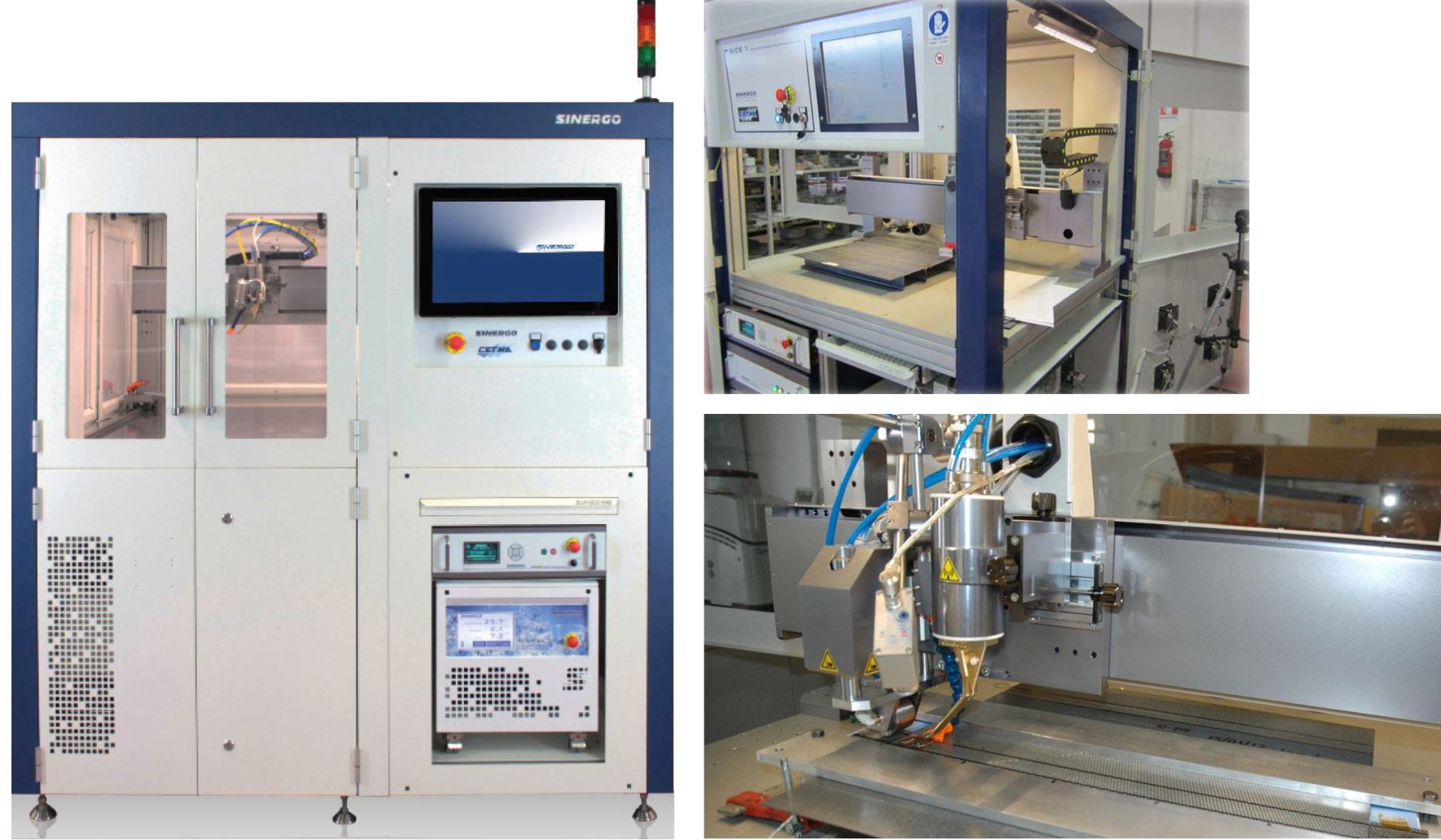
O CETMA também desenvolveu a capacidade de otimizar seu processo de soldagem por indução usando ferramentas de simulação, realizando análises numéricas usando o software de modelagem de elementos finitos (FEM) COMSOL Multiphysics (COMSOL Inc., Burlington, Mass, EUA). Ele verificou esses modelos por meio de um grande número de testes físicos. O CETMA confirmou seus parâmetros de processo otimizados por meio de ensaios de volta única em cupons soldados, nos quais os valores de resistência ao cisalhamento ficaram muito próximos do máximo relatado na literatura. Notavelmente, estes também eram muito maiores do que os valores máximos ao usar adesivos estruturais, diz CETMA.
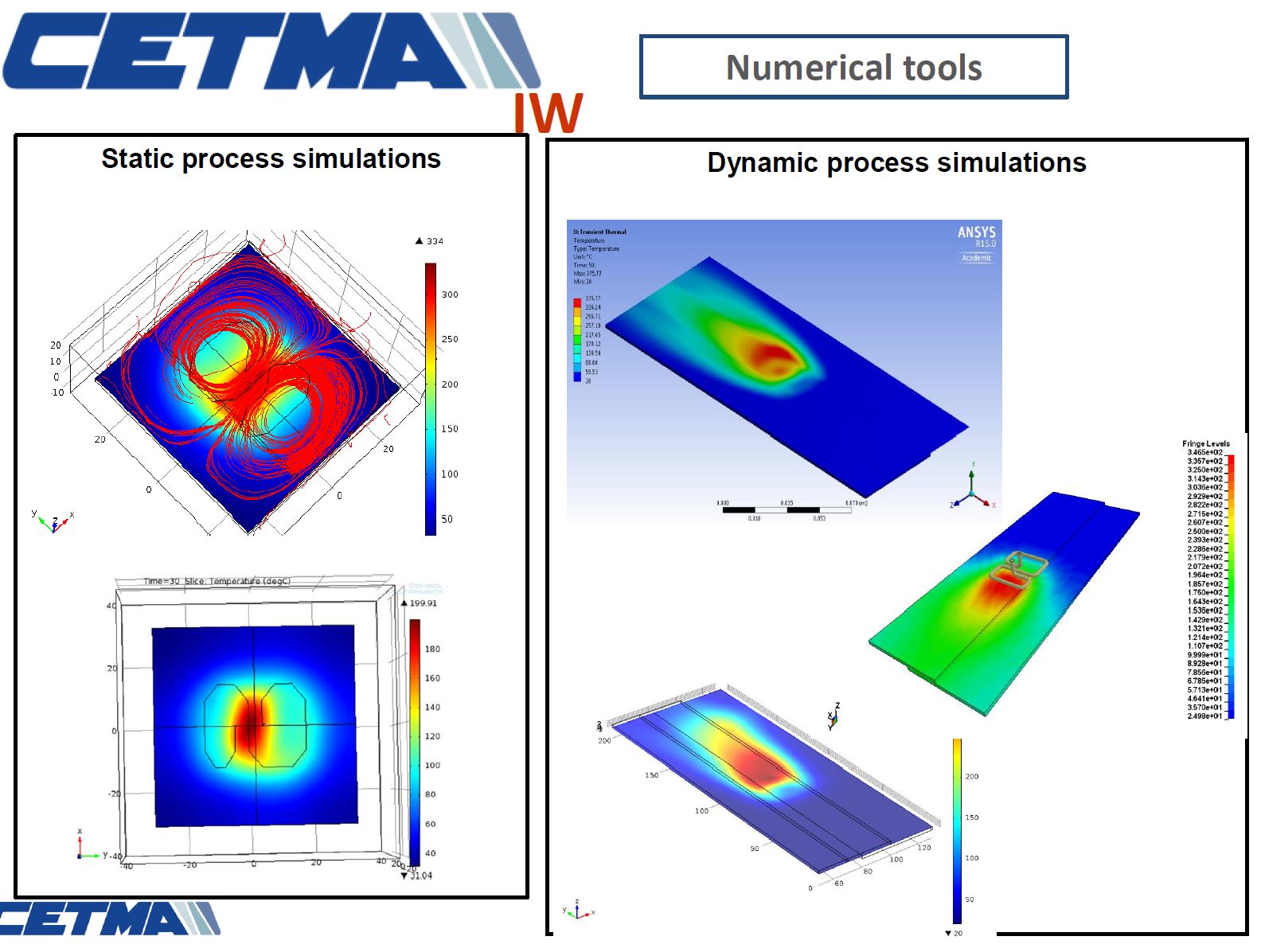
CETMA provou sua capacidade de soldagem para uma ampla variedade de materiais, incluindo tecido e fibra de carbono UD, bem como PEEK, PEI, PEKK, PP, PA6, PA12 e até soldagem em CF / epóxi usando um híbrido de PVB termoplástico (polivinil butiral) camada de transição do substrato termofixo para a face termoplástica para soldagem. (Muitos dos detalhes desta seção foram extraídos da apresentação de competências CETMA e da Relatório final CORDIS para ECO FAIRS.) O CETMA solicitou uma patente europeia em 2014 e os inventores Silvio Pappada e Andrea Salomi foram premiados com a patente EP2801472A1 em 2016. O CETMA publicou vários artigos e apresentações sobre esta tecnologia, incluindo:
- “Simulações de elementos finitos para apoiar o desenvolvimento de tecnologias fora de autoclave”, A&D, 11-12 de outubro de 2012
- “Simulações de elementos finitos para apoiar a soldagem por indução contínua de compósitos de PPS-Carbono”, SEICO 13, 11-13 de março de 2013 “Paris”
- “Desenvolvimento de uma nova máquina de solda por indução para compósitos termoplásticos no setor aeroespacial”, Conferência italiana de Aeronáutica e Astronáutica XXII Conferência de Napoli, 9 a 12 de setembro de 2013
- “Soldagem por indução no setor aeroespacial”, TPRC, Thermoplastic Composites European Consortium, Web-meeting, dezembro de 2013.
- “Testes em escala real em componentes termoplásticos para o setor aeroespacial”, SEICO 14, 10-11 de março de 2014 “Paris”
- “Novo equipamento de soldagem por indução para o setor aeroespacial”, revista JEC, nº 87, março de 2014, pp. 89-91.
Status do KEELBEMAN e caminho a seguir
A Airbus visitou a CETMA em dezembro para ver a soldagem final da seção do demonstrador de 1 metro, e a equipe da KEELBEMAN também realizou uma revisão final do nível de preparação da tecnologia (TRL). “Estamos obtendo bons resultados e amadurecendo a tecnologia do TRL 3 ao TRL 4”, diz Lagraña. As próximas etapas podem incluir o desenvolvimento do TRL 6 e a produção de uma viga de quilha em escala real a ser instalada em um dos demonstradores do Clean Sky 2, como a fuselagem central inferior de tamanho real WP 2.3.2, mas isso ainda não foi decidiu.
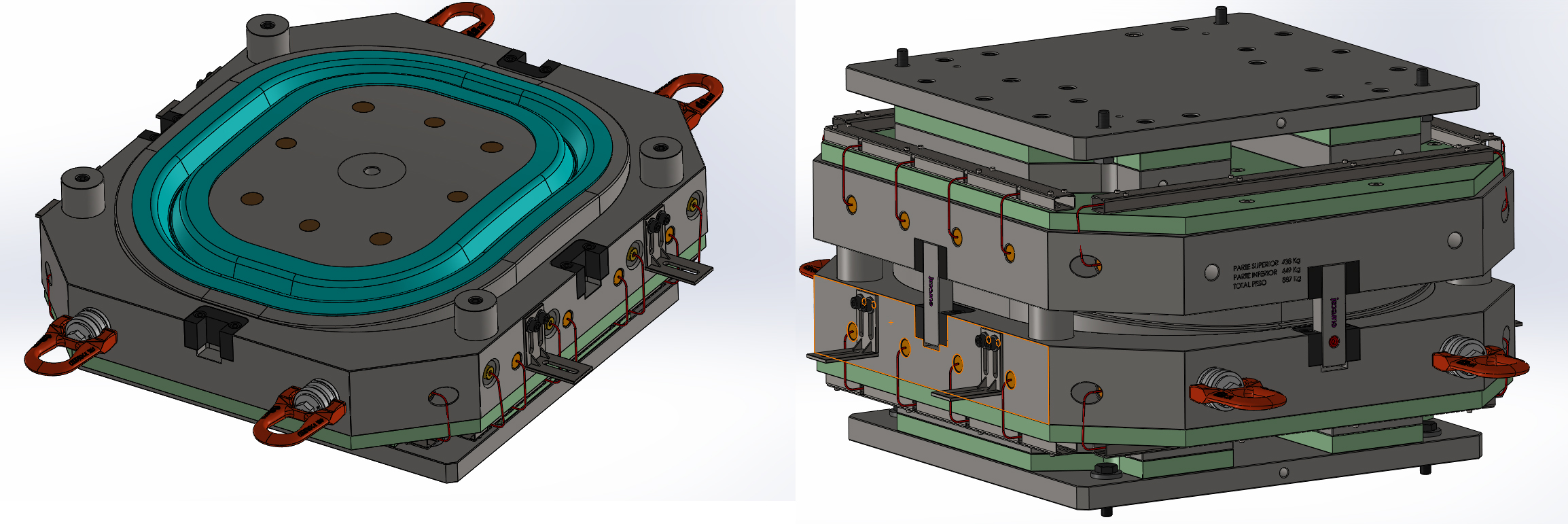
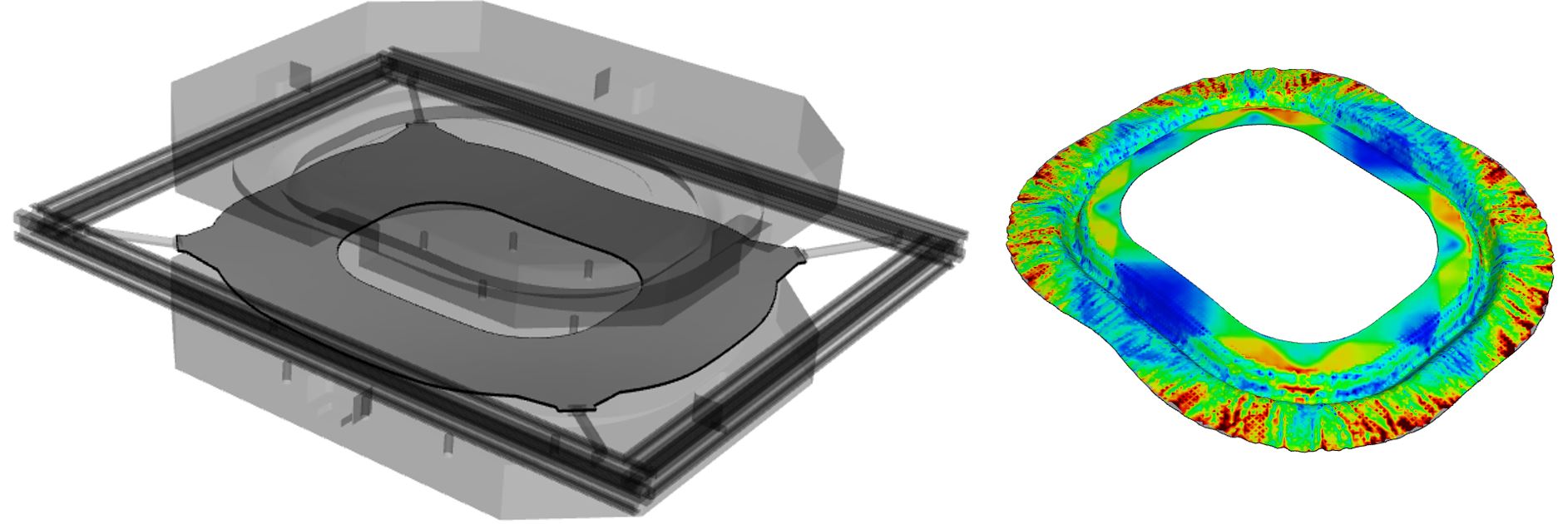
Projeto WINFRAME 4.0 para frames de janelas TPC
Outro programa de composto termoplástico (TPC) para EURECAT é WINFRAME 4.0, com o objetivo de desenvolver e fabricar 24 esquadrias para um demonstrador terrestre integrado fuselagem / cabine de aeronave regional (ver explicação dos desenvolvimentos do Clean Sky 2 para Aeronaves Regionais e o Completo - Demonstrador inovador de fuselagem e cabine de passageiros em escala abaixo). Os parceiros WINFRAME 4.0 incluem:
- Empresa aeroespacial multinacional Leonardo (Roma, Itália) como gerente de tópico
- EURECAT
- Sofitec.
“O método que usamos pode produzir uma moldura de janela a cada 10 minutos”, diz Lagraña. As etapas de produção incluem:aquecer os blanks laminados TPC em um forno, converter em um molde, fechar o molde em uma prensa, aplicar calor e pressão por 10-20 minutos e desmoldar a (s) peça (s) acabada (s). “Essa abordagem não apenas alcança ciclos mais curtos do que a moldagem por líquido, mas também ferramentas muito menos caras”, acrescenta. “O processo é bastante conhecido na indústria automotiva, é a moldagem por compressão em uma configuração altamente automatizada que aumenta a qualidade da peça, mas os materiais aeroespaciais usados são diferentes, neste caso um PPS reforçado com fibra de carbono e fibra de carbono da Toray Compostos avançados (anteriormente TenCate). Ao final desse projeto, teremos alcançado um TRL 6 para essas tecnologias ”, afirma Lagraña.
Projeto COFRARE:RTM C-frames e laços de cisalhamento termoplástico
O projeto COFRARE 2020 é uma extensão do projeto COFRARE 2.0 inicial:
Clean Sky 2 - JTI-CS2-2015-CFP02-AIR-02-16. “Desenvolvimento de processos para fabricação de molduras compostas com alta taxa de produção e baixo custo” Duração do projeto:2016 a 2018.
O objetivo do projeto Clean Sky 2 COFRARE 2.0 era desenvolver um processo de fabricação competitivo e viável para estruturas compostas de fibra de carbono a serem usadas em uma fuselagem baseada em painel composto para aeronaves regionais. Parceiros incluídos:
- Fornecedor aeroespacial de Nível 1 com sede em Nápoles e empresa de engenharia / industrialização DEMA (Design Manufacturing SpA, Somma Vesuviana, Itália)
- EURECAT
- LGAI Technological Center S.A., uma divisão da Applus + Laboratories em Barcelona, a Espanha forneceu testes.
O objetivo da próxima geração do projeto COFRARE 2020 é fabricar estruturas compostas em escala real e tirantes de cisalhamento para serem usados no demonstrador de solo integrado de fuselagem / cabine Clean Sky 2. Este demonstrador é organizado no IADP (Plataforma de Demonstração de Aeronave Inovadora) da Clean Sky 2 e detalhado na Seção 5.2.2 do documento do Programa Técnico Conjunto de março de 2015:
“ Aeronaves regionais são um elemento-chave da Clean Sky por meio de um ITD (Demonstrador de Tecnologia Integrado) dedicado - Aeronave Regional Verde (GRA) , fornecendo blocos de construção essenciais para um sistema de transporte aéreo que respeita o meio ambiente, garante uma mobilidade segura e contínua e constrói a liderança industrial na Europa. In Clean Sky 2 , … Os objetivos de demonstração da Aeronave Regional IADP são muito mais complexos, abrangentes e desafiadores do que os do atual Clean Sky Projeto GRA , que foi forçada a trabalhar dentro das restrições de orçamento e tempo. … ”
O Programa Técnico Conjunto de 2015 descreve o desenvolvimento de Aeronaves Regionais para incluir dois bancos de teste de voo e cinco grandes demonstradores terrestres integrados. Este último inclui o Demonstrador Inovador de Fuselagem e Cabine de Passageiros em Grande Escala :“A fuselagem será uma demonstração em grande escala de tecnologias para materiais, estruturas e manufatura compósitos objetivou [alcançar] redução de peso e custo e minimizar o impacto ambiental por meio de eco-design e otimização do consumo de energia ao longo do ciclo de vida (em direção a um impacto zero). ”
Os parceiros do projeto COFRARE 2020 incluem:
- Leonardo como gerente de tópico
- EURECAT
- DEMA
- Fabricação de componentes e conjuntos de aeronaves A. Abete (Nola / Marigliano, Itália).
“No COFRARE 2020, estamos fazendo armações de fuselagem usando RTM (moldagem por transferência de resina), que será integrado ao demonstrador de fuselagem”, explica Lagraña. “Estamos usando a tecnologia Ziplus de Shikibo (Osaka, Japão), que produz pré-formas adequadas para injeção de resina.” A Shikibo Ltd. faz parte da Composite Alliance Corp. (Dallas, Texas, EUA) e oferece uma variedade de tecnologias de pré-formação de têxteis.
Um aspecto interessante deste programa é o uso de sensores da Synthesites (Uccle, Bélgica) para monitoramento em tempo real da chegada da resina, temperatura, pressão, Tg e cura. “Os sensores estão localizados em áreas específicas da parte composta e da ferramenta RTM para otimizar a estratégia de injeção de resina”, observa Lagraña. A injeção é realizada por meio de um sistema altamente automatizado fornecido pela ISOJET (Corba, França), que também faz parte da Composite Alliance Corp. Os sensores Synthesites são sensores dielétricos, mas ao contrário da maioria da análise dielétrica (DEA), que é baseada em corrente alternada (AC) , Synthesites usa corrente contínua (DC). “Nossos sensores funcionam bem com materiais de alta resistividade como resinas e como estamos aplicando uma única voltagem, não temos que analisar múltiplas frequências, mas alcançamos uma alta precisão, mesmo no final da cura”, explica o diretor da Synthesites, Dr. Nikos Pantelelis.
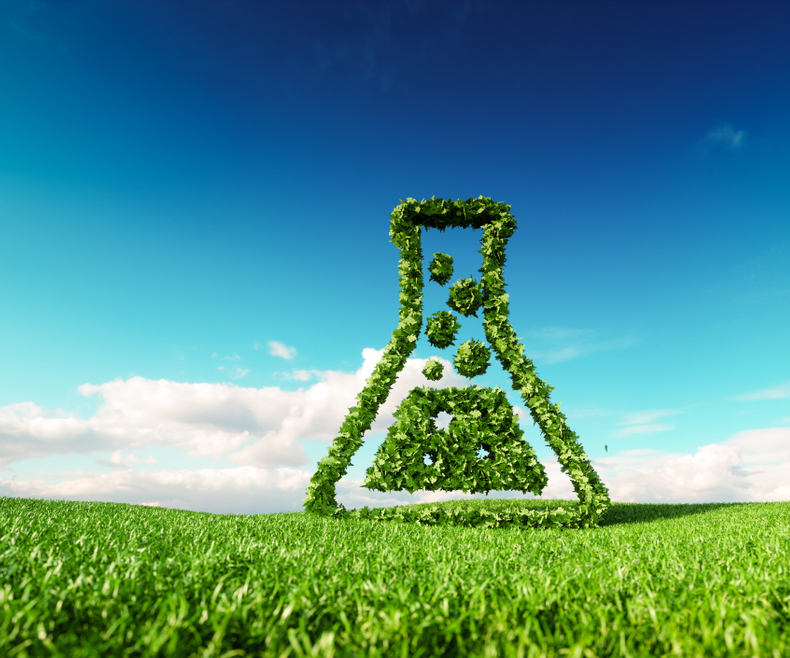
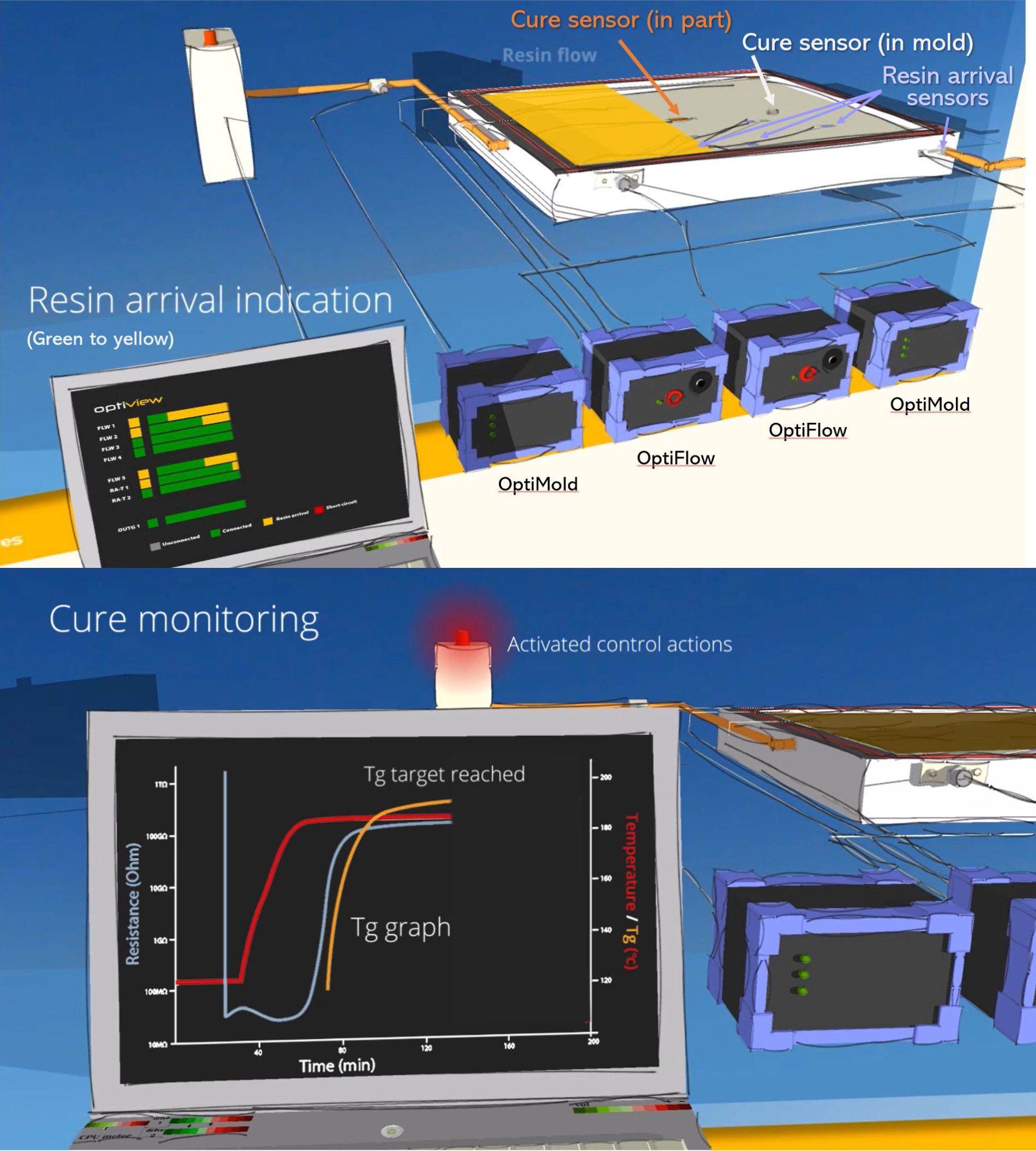
“Conhecemos os Synthesites em uma conferência SAMPE em 2011”, lembra Lagraña. “Eles falaram sobre sensores para encurtar o ciclo de cura. Estamos explorando como automatizar pré-formas para as estruturas da fuselagem e até mesmo usar um processamento mais rápido com HP-RTM (RTM de alta pressão), mas ainda assim você está com 3-4 horas de tempo de processamento. No entanto, com os Synthesites, cortamos o ciclo de cura em 50 por cento monitorando a Tg. Agora estamos testando propriedades. Esses sensores podem trabalhar em alta pressão, mas em nosso processamento RTM, estamos usando apenas 8 bar de pressão. ”
Os sensores dielétricos Synthesites DC, o sistema de monitoramento de fluxo de resina líquida OptiFlow e o sistema de monitoramento de cura OptiMold foram demonstrados em produção por vários fabricantes de pás eólicas. Eles também são usados pela Bombardier Aerospace (Belfast, Reino Unido) para produzir a asa moldada de compósito líquido para o C-Series agora Airbus 220. O Centro Aeroespacial Alemão (DLR, Stade, Alemanha) demonstrou redução do ciclo de cura de até 50% com ambos autoclave prepreg e RTM, enquanto o National Composites Centre (NCC, Bristol, UK) demonstrou que mesmo para resinas altamente reativas, os cálculos de Tg em tempo real feitos a partir de medições de sensor de temperatura e resistividade da resina são tão precisos quanto a Tg medida de painéis curados usando calorimetria de varredura diferencial (DSC).
Armações de união com laços de cisalhamento TPC
Outra parte importante do COFRARE 2020 é um método de produção de alto volume para produzir as centenas de amarras e suportes de cisalhamento necessários para unir as armações C da fuselagem RTM aos painéis compostos da fuselagem. “Estamos desenvolvendo 255 geometrias diferentes para braquetes de compósitos termoplásticos produzidos por moldagem por compressão”, diz Lagraña. (Nota, GKN Fokker tem vários projetos Clean Sky 2 onde produzirá suportes TPC para o Demonstrador de Fuselagem Multifuncional em Aeronaves de Passageiros Grandes IADP; este trabalho no COFRARE 2020 é para aeronaves regionais menores.) O método básico é mostrado abaixo, usando ferramentas de aço combinadas e uma prensa aquecida. “O custo dessas ferramentas de moldagem por compressão é de apenas 2.000 euros, o que é muito acessível em comparação com as ferramentas RTM”, acrescenta. “A estampagem também atinge tempos de ciclo muito curtos.”
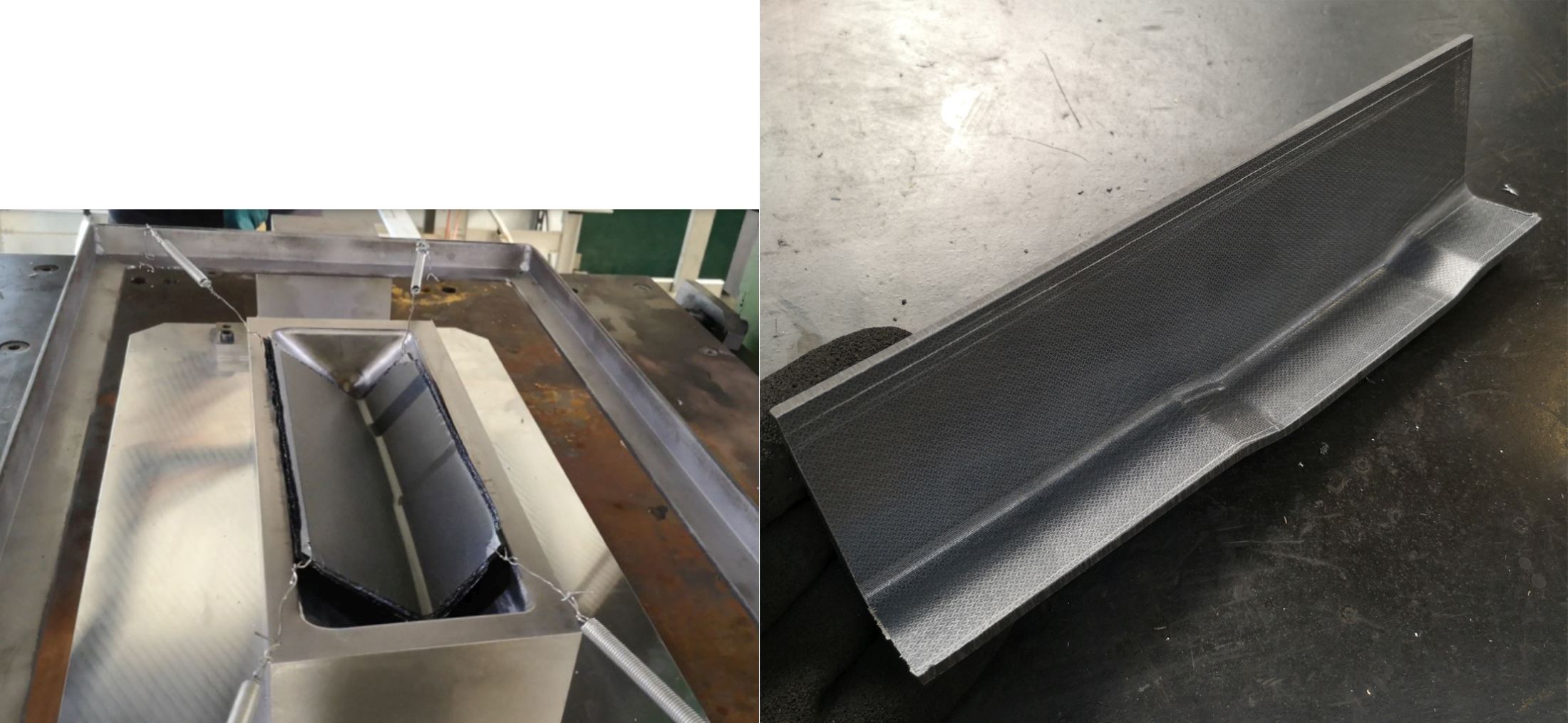
EURECAT está investido para permanecer na vanguarda do desenvolvimento de tecnologia de compósitos, diz Lagraña. “Acreditamos que a pressão por um ambiente limpo aumentará drasticamente o uso de compósitos em todos os transportes, e que o preço acessível e o desempenho irão juntos. É por isso que nos concentramos em tecnologias automatizadas fora da autoclave para oferecer aos nossos clientes. ”
Fique ligado no meu próximo blog sobre os projetos Clean Sky 2 STUNNING e MECATESTERS, que discutirá o desenvolvimento de suportes TPC soldados para o Demonstrador de Fuselagem Multifuncional e uma caracterização completa do PAEK para este projeto. Também farei um blog sobre Synthesites com mais detalhes, bem como mais sobre os desenvolvimentos da CETMA em compósitos. 2020 vai ser um ano muito interessante para os compósitos!
Resina
- Sanduíche termoplástico de favo de mel para sobremoldagem em compósitos leves mais finos
- Personalização de sensores ultrassônicos para otimização e controle de processos compostos
- Resinas epóxi reprocessáveis, reparáveis e recicláveis para compósitos
- Combinação de medições dielétricas AC e DC para monitoramento de cura de compósitos
- Solvay, Leonardo lança laboratório conjunto de pesquisa para compósitos termoplásticos
- Porta termoplástica a primeira para compósitos automotivos
- LANXESS expande capacidade de produção de compósitos termoplásticos reforçados com fibra contínua
- TPAC e TPRC desenvolvem processo de reciclagem de compósitos termoplásticos
- Compósitos termoplásticos de soldagem
- Consórcio de compósitos termoplásticos visa produção de alto volume para automotivo e aeroespacial