Entrevista com especialista:CEO da PostProcess Technologies sobre como resolver o gargalo de pós-processamento para fabricação de aditivos
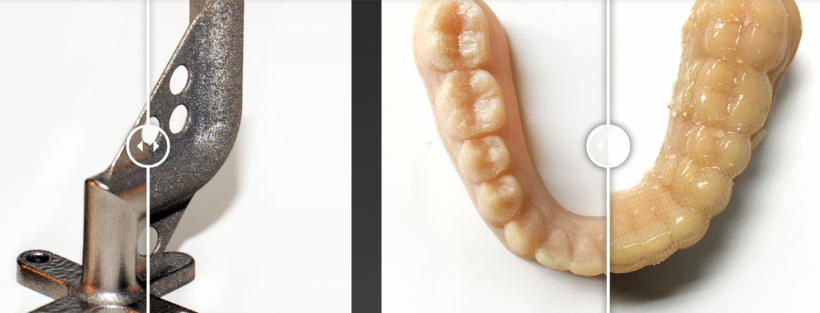
Antes e depois:peças impressas em 3D após o pós-processamento usando as soluções de automação da PostProcess Technologies. Crédito da imagem:PostProcess Technologies
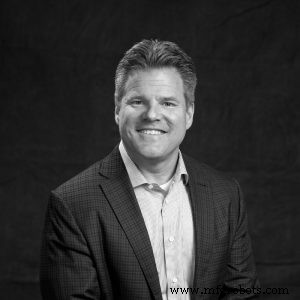
O pós-processamento é uma etapa vital do processo de manufatura aditiva - e talvez a mais demorada. De acordo com uma estatística, os métodos atuais de pós-processamento representam entre 30-60% do processo de fabricação de aditivos.
Um dos principais motivos para esse gargalo é que o pós-processamento ainda é principalmente um processo manual. Uma empresa que visa transformar isso é a PostProcess Technologies. Com sua sede principal em Buffalo, Nova York, PostProcess Technologies oferece soluções automatizadas para pós-processamento, incluindo remoção de suporte e acabamento de superfície.
Na Entrevista com Especialistas desta semana, a AMFG fala com o CEO da PostProcess Technologies, Jeff Mize, para saber mais sobre como a empresa está abrindo o caminho para o pós-processamento automatizado para manufatura aditiva e por que o pós-processamento automatizado é necessário para que a tecnologia seja escalonada.
Você poderia me falar um pouco sobre as tecnologias PostProcess e os problemas que está tentando resolver?
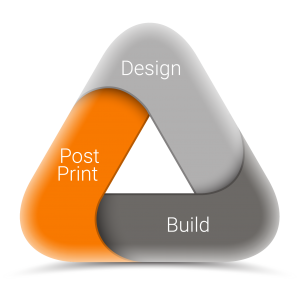
Estamos resolvendo dois desafios principais. O primeiro é automatizar a remoção do suporte. Hoje, ainda existe um componente pesado de trabalho manual quando se trata de remover suportes de peças aditivas. A manufatura aditiva é muito parecida com a natureza:conforme você está construindo uma peça no eixo Z, camada por camada, a força da gravidade significa que você precisará de suportes. Como a grande maioria das peças produzidas de forma aditiva tem algum tipo de suporte, a primeira área em que nos concentramos é a automação do processo de remoção de suporte.
Melhor acabamento de superfície para peças impressas em 3D é o nosso segundo foco. Dez ou até cinco anos atrás, a maior parte da atividade dentro da AM era para uma função adequada na engenharia - é claro que havia algumas exceções, mas de modo geral, essas partes realmente não viram a luz do dia. Mas, nos últimos dois anos, a indústria está vendo cada vez mais peças aditivas usadas para a função de forma / ajuste, o que levou a um aumento dramático na necessidade de um melhor acabamento superficial. Garantimos que a peça pode estar “pronta para o cliente” - que o cliente pode ser um cliente interno ou um cliente de nossos clientes.
Abordamos essas duas funções através da integração de software, hardware e química. Todo o nosso investimento, expertise e inovação estão voltados para o segmento industrial do mercado AM - e o software é o molho secreto. Isso controla a quantidade de energia que nossas soluções utilizam para finalizar essas peças aditivas delicadas, então podemos remover automaticamente os suportes e dar aos clientes um acabamento de superfície dramaticamente melhorado.
Quais os benefícios que suas soluções oferecem?
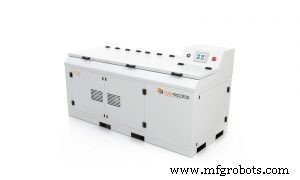
Existem três benefícios principais que oferecemos aos nossos clientes. Um é a consistência - muitas vezes há mais arte do que ciência quando se trata de pós-impressão de aditivos hoje. Nossas máquinas funcionam 24 horas por dia e oferecem uma consistência que você não obtém com métodos manuais.
O segundo benefício é o rendimento . À medida que cada um de nossos clientes dimensiona suas operações de AM, eles estão percebendo cada vez mais um gargalo no que chamamos de terceira etapa do processo aditivo:pós-impressão. Com nossas soluções, eles são capazes de automatizar esse processo e remover esse gargalo.
O terceiro é o retorno do investimento . Conseguimos reduzir significativamente a quantidade de tempo do técnico atendido - em muitos casos, podemos reduzir isso em pelo menos 90%. Como resultado, nossos clientes obtêm um retorno do investimento muito rápido, normalmente dentro de um período de 10-30 semanas.
Estamos vendo que os volumes de prototipagem estão crescendo rapidamente. As empresas que produziam mil protótipos em seus laboratórios há um ou dois anos estão agora produzindo de 10.000 a 30.000 protótipos no mesmo laboratório. Mesmo que ainda sejam considerados protótipos, ouvimos clientes querendo encontrar uma maneira de obter peças mais consistentes. Usar métodos manuais consome muito tempo e é difícil encontrar o técnico certo. Portanto, nossa solução é absolutamente crítica para que esses volumes de protótipo continuem a aumentar e isso é absolutamente essencial para entrar em volumes de produção.
Você poderia explicar um pouco mais sobre como você integra software, hardware e química?
Nosso foco na integração de software, hardware e química realmente oferece um valor único para o estágio de pós-impressão. Além de descobrir o software e desenvolver o hardware, também estamos gastando muito tempo otimizando a química para as tecnologias de maior volume, como PolyJet, FDM, SLA e DMLS no lado metálico, junto com MJF da HP, CLIP da Carbon - e temos mais de 500.000 benchmarks.
Temos nossos codificadores sentados ao lado de nossos químicos e engenheiros de desenvolvimento, e os três grupos de engenheiros estão constantemente trabalhando juntos para que possamos otimizar continuamente os resultados finais para o cliente. Essa é uma abordagem única e inovadora que ninguém mais está fazendo hoje. Isso nos dá uma posição de liderança significativa no mercado de pós-impressão automatizada para aditivos.
Então, essa integração de três vias é um diferencial importante entre você e soluções semelhantes no mercado hoje?
Sim. E o elemento de software é crítico. Dentro desse elemento de software, existe um componente de análise de dados. Estamos otimizando esse software para otimizar ainda mais o processo. Quer seja o algoritmo de agitação utilizado para remoção de suporte ou a frequência e amplitude que estamos usando em nossas soluções de acabamento de superfície, o componente de software ou análise de dados é outra área de investimento significativo para nós à medida que avançamos.
Pense assim:a peça de software é o cérebro do que estamos fazendo aqui. E então a integração de software, hardware e química nos permite oferecer consistentemente os três benefícios aos clientes finais:peças consistentes, rendimento ilimitado e rápido ROI.
Existem setores específicos que você está segmentando?
Os três maiores mercados que vemos emergir são o aeroespacial, médico e automotivo. Atualmente, nossa base de clientes cobre praticamente todas as verticais, mas com o tempo, acreditamos que veremos a maior parte de nossa receita proveniente dos setores aeroespacial, médico, odontológico e automotivo.
Quais são os principais desafios que a manufatura aditiva ainda enfrenta?
Velocidade e redução dos custos gerais são desafios importantes que ainda enfrentamos hoje. A velocidade com a qual você pode imprimir peças é crítica, e é por isso que vemos empresas como a HP e a Stratasys fazendo muito trabalho nessa área, para que você possa realmente imprimir mais rápido. O custo é outro problema - mas acredito que continuaremos vendo o custo das soluções cair, não apenas no lado do polímero, mas também no lado do metal.
Quanto a onde o PostProcess entra:acreditamos que nossas soluções automatizadas irão remover um dos maiores problemas do momento, que é permitir maior rendimento com saída consistente da função de pós-impressão.
Como você vê a evolução da manufatura aditiva nos próximos cinco anos?
Acho que a AM valerá de 3 a 4% da manufatura tradicional, ou seja, um mercado de 3 a 400 bilhões de dólares nos próximos cinco anos. Um dos maiores mercados será o médico, onde a customização em massa é tão importante.
Portanto, vejo o aditivo se tornando a tecnologia de manufatura dominante na área médica nos próximos anos - é projetado para ser o segundo maior mercado depois do aeroespacial.
A capacidade de construir geometrias exclusivas com materiais que pesam muito menos para aplicações aeroespaciais e automotivas aumentará rapidamente. Atualmente, estamos no ponto de inflexão, onde veremos taxas médias de crescimento de 40% + em setores específicos.
Também há cada vez mais clientes entrando em produção. Recentemente, estávamos conversando com uma empresa de cosméticos que planeja produzir 50 milhões de peças aditivas por ano nos próximos dois a três anos.
Vemos empresas automotivas planejando produzir milhares de peças aditivas para entrar em produção veículos. Portanto, em um nível mais alto, veremos mais empresas buscando maiores volumes de produção. Automatizar a terceira etapa desse processo será essencial para essa consistência, rendimento e rastreabilidade.
PostProcess anunciou recentemente sua expansão na Europa. Por que você tomou essa decisão - e você tem outros planos para a expansão no futuro?
A demanda por aditivos é global e não para de crescer - mais de 2.000 empresas em todo o mundo questionaram nossas soluções. Sem surpresa, grande parte dessa demanda vem da Europa, e é por isso que agora abrimos nossa sede na Europa em Sophia-Antipolis, nos arredores de Nice, França.
O mercado europeu é quase do mesmo tamanho que o mercado norte-americano em termos de potencial. Eu até diria que a Europa está à frente, principalmente no lado dos metais, com empresas como EOS, SLM e Renishaw.
Fora da França, acreditamos que a Alemanha será nosso maior mercado e, recentemente, anunciamos nossa parceria com a Rösler Mass Finishing, fornecedora líder mundial de tecnologias de acabamento de superfície. A Rösler será nosso braço de distribuição na Europa. Com a Rösler, teremos uma forte presença na Alemanha e seremos capazes de cobrir rapidamente todos os principais países industriais, da Alemanha à França, à Espanha, ao Reino Unido, à Polônia e à Itália.
Então, para responder à sua pergunta, foi um alinhamento de vários fatores - também temos planos de lançar na Ásia, embora provavelmente seja no final de 2019/2020.
Você poderia compartilhar o que está por vir para as tecnologias PostProcess?

Há alguns outros problemas que vemos se tornarem mais agudos na pós-impressão, que iremos abordar daqui para frente. Neste ponto, não estamos divulgando publicamente o que estamos fazendo lá, mas definitivamente vai além da remoção do suporte e acabamento superficial. Estaremos trazendo algumas soluções adicionais para o mercado - uma em 2019 e outra em 2020. Elas oferecerão um pacote de produtos pós-acabamento de ponta a ponta que, acreditamos, atenderá à grande maioria das necessidades de aditivos dos clientes .
Saiba mais sobre tecnologias PostProcess aqui .
impressao 3D
- Reconsiderando o processo de integração de software para operações de manufatura aditiva
- Entrevista com especialista:Pat Warner, especialista em fabricação de aditivos da equipe Renault de Fórmula 1
- A verdade sobre economias de escala para processos de manufatura aditiva
- Entrevista com especialista:Felix Ewald, CEO da DyeMansion
- Tecnologias de manufatura aditivas:A empresa de pós-processamento que molda o futuro da manufatura
- O que é a ‘Internet das coisas’ e o que ela significa para a manufatura aditiva?
- A próxima fronteira para a fabricação de aditivos escaláveis? Software Aditivo MES
- Entrevista com especialista:Nanoe CEO Guillaume de Calan sobre o futuro da impressão 3D em cerâmica
- Como a Ford Motor Company está inovando a impressão 3D para a indústria automotiva:Entrevista de especialista com Harold Sears
- O caso da impressão 3D na manufatura