Entrevista com especialista:Sintavia Presidente Doug Hedges sobre como alcançar a produção em série com impressão em Metal 3D
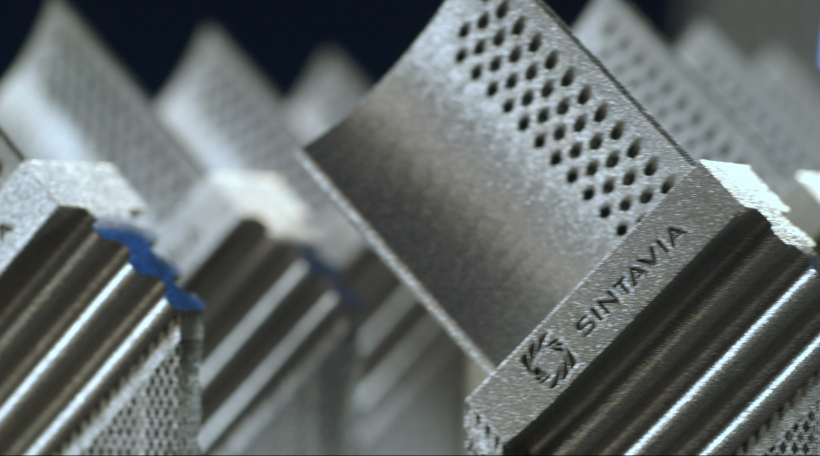
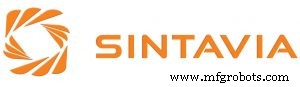
Com foco na produção em série de peças de metal por meio de manufatura aditiva, a empresa oferece um serviço exclusivo de ponta a ponta que abrange não apenas a produção e o pós-processamento, mas também os testes , metalurgia e caracterização de pós em seu laboratório interno.
Recentemente, Sintavia anunciou seus planos de expansão, mudando-se para uma nova instalação de 55.000 pés quadrados que tem uma ênfase distinta na produção.
Esta semana, temos o prazer de conversar com o presidente da Sintavia, Doug Hedges, para discutir como a empresa produz peças de metal certificadas de alta qualidade, por que a AM é perfeita para a indústria aeroespacial e o que a indústria de AM pode fazer para acelerar a adoção da tecnologia.
Você poderia nos contar um pouco sobre Sintavia?
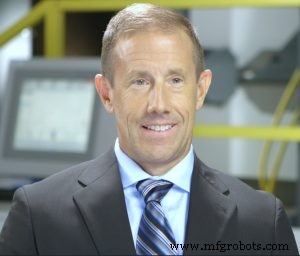
Sintavia foi fundada em 2012 por Brian Neff, CEO e presidente da empresa. A empresa foi fundada como um esforço interno de manufatura aditiva com uma empresa chamada CTS Engines, uma MRO independente para motores a jato com sede em Fort Lauderdale, Flórida.
A Sintavia se tornou uma empresa separada em 2015 e nos mudamos para Davie, Flórida, onde ainda estamos hoje.
Como empresa, temos uma vasta experiência na aviação. Vimos que havia uma oportunidade de usar esse histórico para criar uma empresa verticalmente integrada com uma série de ofertas diferentes. Para ser bom em aditivos, você também precisa ser bom em metrologia, metalurgia, usinagem, tratamentos térmicos, testes e assim por diante.
Portanto, embora nossa habilidade principal seja a manufatura aditiva, estamos usando nossa experiência em os campos de manufatura MRO e OEM para criar uma empresa nova e autônoma que se concentra em aeroespacial e defesa, bem como petróleo e gás.
O que é único em Sintavia é que a integração vertical sustenta tudo o que fazemos:desde o pós-processamento, qualidade, metalurgia, digitalização etc. Todos esses elementos estão localizados sob o mesmo teto em nossa unidade de produção aqui em Davie, Flórida.
Aeroespacial é um foco central para Sintavia. Você poderia nos apresentar alguns benefícios da manufatura aditiva para a indústria aeroespacial?
A manufatura aditiva funciona bem para a indústria aeroespacial por uma série de razões.
Primeiro, é importante observar que a tecnologia começou como uma ferramenta de desenvolvimento de protótipo para OEMs na indústria aeroespacial e de defesa para iterar rapidamente em projetos e testes os motores. Agora está evoluindo a um ponto em que as empresas estão construindo motores com peças aditivas.
Então esse ainda é um grande motivador. Mas há todos os outros benefícios típicos que tornam o AM uma grande tecnologia. Aqui, estou me referindo à consolidação de soldagens, fundições complexas, peso leve, design sem ferramentas. Claro, a complexidade não é gratuita - mas é amplamente expandida com o uso de aditivos.
Como exemplo, um foco principal para nós em termos de seleção de peças são os corpos de válvula externos no lado de fora dos motores a jato e dutos. Também vemos um mercado emergente para chassis e trocadores de calor na indústria aeroespacial.
Uma das tecnologias de impressão 3D de metal que você usa é o Powder Bed Fusion. Quais são os benefícios desta tecnologia para aplicações aeroespaciais?
Bem, a impressão 3D de metal em geral realmente se presta a designs únicos.
O estágio inicial do que estamos fazendo é usar a fusão do leito de pó com lasers e feixes de elétrons para construir dutos e componentes de alta pressão, camada por camada. Obviamente, há o benefício de usar a tecnologia como ferramenta de substituição para peças soldadas e fundidas já utilizadas na indústria.
Mas o poder do aditivo vai muito além disso:você é capaz de fazer peças que são melhores, mais leves e mais fortes - essencialmente facilitando um desempenho aprimorado. Em última análise, para realmente utilizar o poder do AM, os componentes precisam ser projetados para manufatura aditiva.
Você pode usar a manufatura aditiva - estou falando principalmente sobre lasers aqui - para componentes como trocadores de calor e chassis para fazer geometrias que antes eram impossíveis de fabricar.
Você também tem, por exemplo, corpos de fluxo ou conjuntos de válvula que você pode tornar mais rápido e consolidar usando AM. Isso permite que nossos clientes não apenas otimizem suas cadeias de suprimentos existentes, mas também façam produtos melhores e aproveitem os pontos fortes do mercado de defesa e aeroespacial OEM.
Pegue os trocadores de calor como um exemplo:a manufatura aditiva permite que você para fazer paredes muito finas e geometrias pequenas e intrincadas dentro do componente. Portanto, você pode ter uma parede de 200 mícrons ou menos. Além disso, com a manufatura aditiva, agora você tem uma maneira melhor de conduzir o calor para fora do componente. Isso é ótimo porque o objetivo do jogo final com trocadores de calor é tirar o calor do componente para que você possa colocar mais eletrônicos nele.
Usamos a manufatura aditiva de metal para melhorar seus produtos. Qualquer coisa, desde corpos de válvulas, componentes externos de motores a jato, dutos e trocadores de calor a chassis e diferentes tipos de estruturas de tubos que foram feitos por soldagens com muitos gabaritos complexos e acessórios para soldá-los juntos.
Dito isso , também fazemos muito mais do que isso. Por exemplo, trabalhamos com o que está dentro do equipamento da turbomaquinaria, desde um impulsor menor que poderia estar dentro de um compressor até um impulsor maior que poderia estar dentro de um foguete.
Temos um foco dentro da indústria aeroespacial comercial - motores a jato essencialmente - e outro foco na propulsão, que seriam peças de foguetes.
Temos então o "meio-termo" dentro da indústria aeroespacial e de defesa, pelo que me refiro aos componentes obscuros que antes eram feitos de 10 a 100 peças, mas agora podemos fazer em uma única peça usando manufatura aditiva.
Você poderia expandir alguns dos desafios de design associados a esses aplicativos?
AM é um processo relativamente novo na fabricação. Estamos usando lasers ou feixes de elétrons para derreter o pó em camadas. Essencialmente, o que estamos realmente fazendo é fazer soldagens de pequeno a médio porte, ou "micro-soldagem".
Neste processo de micro solda, há um resfriamento rápido onde o laser expõe o pó de metal. Você tem um caso de dois extremos:um processo de impressão muito quente, com resfriamento rápido ocorrendo ao lado.
Devido a essas diferenças extremas de temperatura, sua peça está sujeita a distorções. Portanto, essas peças não são como as soldagens tradicionais feitas com peças fundidas; eles são itens únicos em si mesmos.
Um dos principais desafios é ser capaz de prever como essas peças se moverão dentro do processo de manufatura aditiva. Uma parte fundamental deste desafio é usar esta tecnologia muito moderna e ferramentas de alta tecnologia para fazer a previsão no início, para ajudar em toda a coordenação do processo.
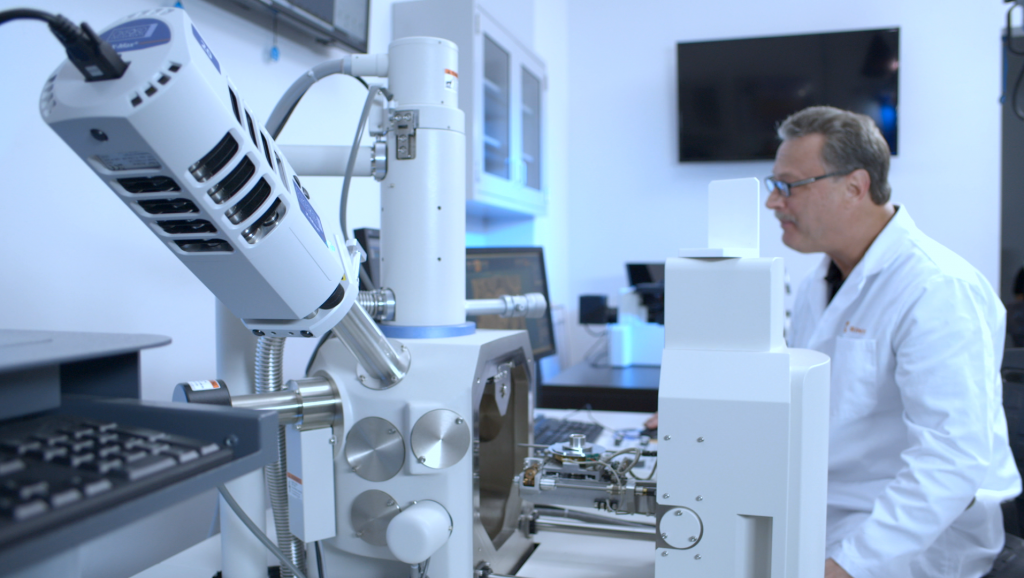
Na Sintavia, usamos a Análise de Elementos Finitos (FEA) no início do ciclo de projeto. Os engenheiros da Sintavia obtêm os dados iniciais dos nossos clientes na forma de modelos CAD, desenhos e especificações. Nossos engenheiros trabalham com nossos clientes para definir parâmetros-chave como orientar uma peça na placa de construção, em que ângulo uma peça será criada e como os suportes serão usados, seja para segurar a peça ou tirar o calor do parte.
Estamos usando matemática para prever como a parte vai distorcer e minimizar essa distorção para fazer uma parte de alta fidelidade. Precisamos saber como essa peça vai se mover e se deslocar sobre nós, para que possamos adicionar estoque a flanges, orifícios, orifícios, etc, para garantir que haja estoque suficiente para limpar no final do processo. Usando essa abordagem, também podemos contabilizar o pós-processamento dessa peça em um momento posterior.
Uma coisa a ter em mente é que a manufatura aditiva é um processo tremendamente poderoso para criar peças complexas, mas deve ser usado em coordenação com os processos tradicionais. A coordenação do processo aditivo com o processo subtrativo é crítica.
Ouvimos falar muito sobre os desafios do pós-processamento de peças metálicas, e esse é um dos serviços que a Sintavia oferece. Você poderia nos mostrar alguns dos maiores desafios do pós-processamento e sua abordagem?
O pós-processamento precisa ser um esforço coordenado entre o próprio processo de impressão e o pós-processamento que acompanha essa peça após a produção.
Um desafio comum que a maioria das pessoas não vê é a remoção do pó após o processo. Após a impressão, todo o pó deve ser retirado da peça. Como algumas dessas peças têm geometrias muito complexas, fazemos máquinas personalizadas - ultrassônicas ou sistemas de vibração tradicionais - para remover o pó.
É normal remover o pó da peça antes da próxima etapa, o que quase sempre é o alívio do estresse. Estamos aliviando o estresse internamente com um forno a vácuo ou um forno de caixa para remover a tensão residual do processo de construção do aditivo.
A partir daí, você vai até um eletroerosão ou uma serra de fita para retirar a peça da chapa. Então, é claro, você precisa remover os suportes. Esses suportes podem ser qualquer coisa, desde simples suportes de treliça até algo muito sólido, usado para segurar a peça e produzir peças muito grandes de superligas de níquel. Estes estão sujeitos a muito estresse térmico.
Por isso, pode ser necessário um processo de máquina muito robusto para remover os suportes dessas peças. Pode haver um trabalho considerável envolvido nisso. E quando digo "processo de máquina", isso pode significar muitas coisas diferentes. Pode significar algo tão fácil quanto quebrá-los com um alicate em uma máquina-ferramenta de cinco eixos muito rígida para remover esses suportes da peça.
A partir deste ponto, você tem várias opções. Por exemplo, você pode ir para HIP, que apresentamos no local, ou usamos usinagem. Neste caso, quando digo usinagem, quero dizer usinar para imprimir. Portanto, isso não é realmente diferente do que você veria em uma oficina mecânica.
Na maior parte do tempo, temos um desenho 2D com muitos controles e usinamos essa parte para que fique de acordo com as especificações.
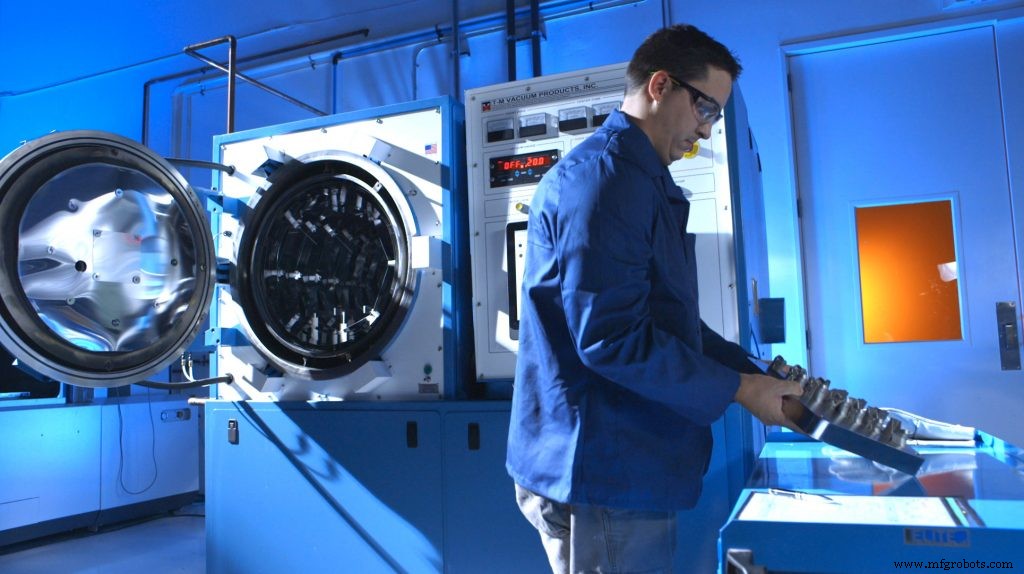
Passando para os próprios pós metálicos, qual é o processo de desenvolvimento de pós metálicos em Sintavia?
Para ser claro, nós realmente não desenvolvemos pós per se. Mas temos estado envolvidos em ajudar empresas a desenvolver ligas que não estavam disponíveis comercialmente no passado.
Temos empresas com as quais trabalhamos que possuem, digamos, uma variante de um aço para ferramentas ou uma variante de aço inoxidável. Normalmente, são ligas especiais que desenvolveram para serem usadas para algum tipo de vantagem de desempenho no futuro.
O que temos são soluções em pó aprovadas para voos para a indústria aeroespacial. Nós obtemos o pó, trazemos para nosso laboratório e o executamos em uma série de testes antes de iniciar a compilação.
Um dos nossos pontos fortes na Sintavia é que temos a caracterização completa do nosso pó no local, em nosso laboratório. Isso nos permite provar e entender o que está acontecendo com o pó. Normalmente, outras empresas terceirizam esse processo. Portanto, embora possamos adquirir materiais de nosso fornecedor de pó, fazemos o teste de fluxo, morfologia, distribuição de tamanho de partícula, análise de gás, ICP para química etc.
Realizamos cerca de oito ou nove testes para garantir que os pós atendem aos requisitos de fabricação de nossos clientes. Em seguida, conforme o pó é usado, coletamos e arquivamos essas amostras de pó para entender o que acontece com o pó conforme a construção continua. Isso significa que somos capazes de entender exatamente o que acontece com o pó conforme ele é usado progressivamente.
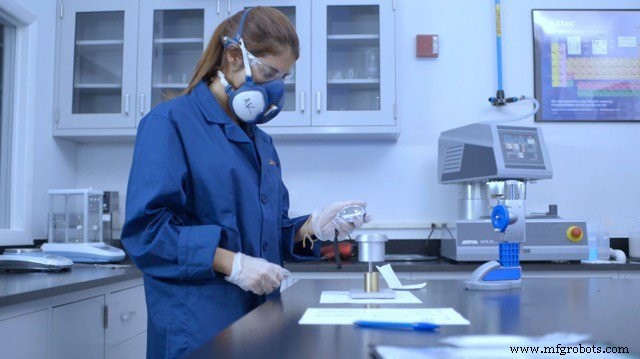
Sintavia anunciou que planeja abrir uma nova unidade com aumento de máquinas este mês. Você poderia compartilhar a visão por trás desta nova instalação?
Estamos muito entusiasmados com a inauguração de nossas novas instalações neste mês.
As novas instalações terão 55.000 pés quadrados e vamos basear essas instalações em nosso sucesso anterior.
Um ponto-chave é que será significativamente baseado na produção. Vamos abrigar mais de $ 30 milhões em novas máquinas, equipamentos AM modernos maiores, sistemas de manuseio de pó, geradores de backup, fontes de alimentação, gás inerte. Prevemos que vamos agregar mais de 135 novos empregos para Sintavia e Sul da Flórida.
A nova instalação é realmente a visão de pegar o que fizemos em uma escala menor, operando 12 máquinas aqui em nossa instalação atual, e escalando para uma instalação de 55.000 pés quadrados com até 65 máquinas.
Haverá um grande esforço na manufatura aditiva, nos tratamentos térmicos. pós-processamento, acabamento, limpeza, etc.
Basicamente, estamos procurando controlar o processo de aditivos em uma única instalação. Esse é realmente o modelo de negócios:queremos expandir o que fizemos e trazer isso para um processo de fabricação que tenha qualidade garantida e repetibilidade para nossos clientes OEM.
Você consideraria expandir para outros setores no futuro, como automotivo ou médico, onde também há uma grande demanda por peças de metal impressas em 3D?
Sim, absolutamente. Temos algumas coisas acontecendo tanto no setor automotivo quanto no médico. E há outras indústrias para as quais o aditivo também faz sentido.
Por exemplo, estamos envolvidos em turbinas industriais a gás. Embora nosso histórico sejam turbinas a gás, as turbinas a gás baseadas no solo para energia são basicamente ampliadas e os motores de turbina aero diferentes são ligeiramente diferentes.
A tecnologia também se aplica muito bem ao setor biomédico.
Sintavia é credenciada pelo AS9100 - AS9100 é um sistema de gerenciamento de qualidade para a indústria aeroespacial. Nosso laboratório é certificado pela ISO 17025 para medições mecânicas, o que pode significar qualquer coisa, desde caracterização de pó e química até testes de tração e testes de fadiga.
A indústria biomédica possui uma agência de credenciamento diferente; a maior parte disso é reduzida para ISO 13485. Depois de ter AS9100, você pode passar para ISO 13485. Não é um grande salto ir entre essas diferentes indústrias. Afinal:qualidade é qualidade e processos são processos. Se você pode fazer aeroespacial, pode fazer essa transição para outros mercados.
Além de tudo o que mencionei, o controle de qualidade é o aspecto mais importante.
Desde o primeiro dia, nos concentramos no desenvolvimento de nosso sistema de qualidade com AS9100, Certificações ISO e Nadcap. Tudo isso é muito benéfico para nossos clientes OEM e pode definitivamente ser um recurso para outras indústrias também.
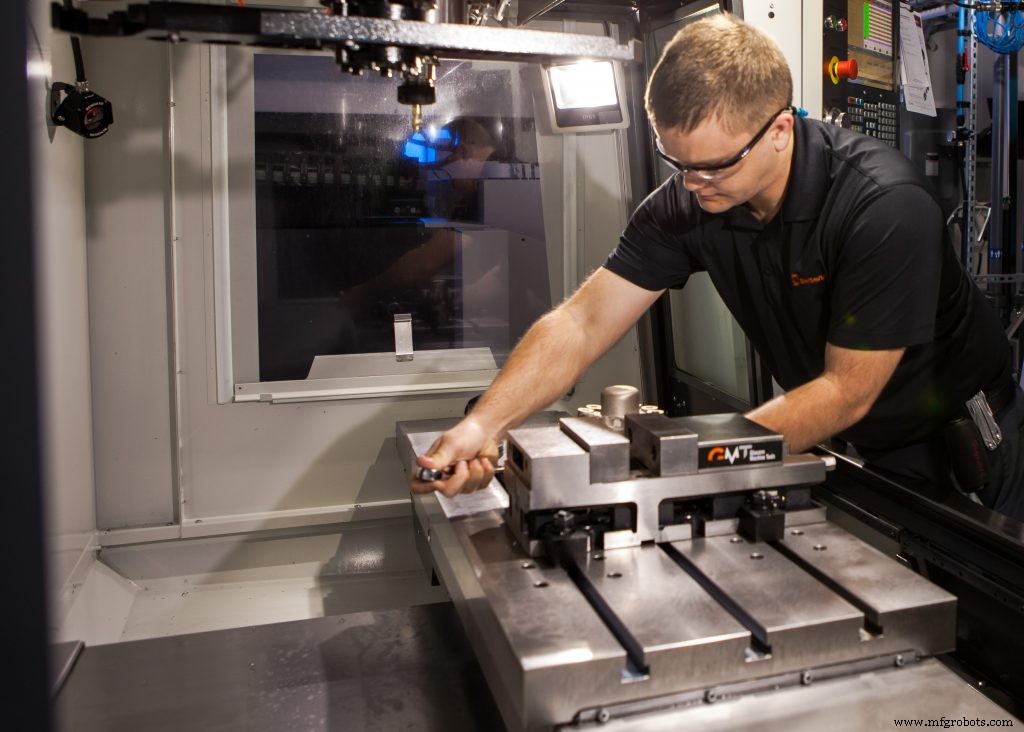
Na sua opinião, quais são algumas das coisas necessárias para acelerar a adoção da impressão 3D em metal?
Apesar de toda a nossa tecnologia e habilidade que temos em análise, devemos realmente nos concentrar no que impulsiona os negócios. Os negócios são movidos por dinheiro e velocidade. Isso significa que a tecnologia precisa se tornar mais rápida, mais barata e mais estabelecida.
Dito isso, estamos vendo como as coisas estão mudando. Durante nosso tempo aqui na Sintavia, vimos como o metal AM evoluiu. Por exemplo, em um ponto no tempo, o alumínio era um material relativamente difícil de imprimir na manufatura aditiva, mas agora é quase comum. À medida que vemos lasers adicionais, à medida que vemos a experiência e peças de design para aditivos, isso vai oferecer aos nossos clientes velocidade mais rápida e economia de custos.
Tudo isso surgiu historicamente da indústria de prototipagem e queremos passar para a produção em série. Há certas coisas que precisamos fazer para torná-lo mais rápido e barato, fornecer qualidade e também oferecer as vantagens que todos sabem que o aditivo de metal pode oferecer.
Como você vê a evolução da manufatura aditiva de metal nos próximos cinco anos, e como a Sintavia se encaixa nessa visão?
O que realmente precisamos fazer é começar a fabricar as peças em modo de produção. Para indústrias críticas, precisamos garantir que estamos produzindo peças de metal reais que são totalmente funcionais.
Sabemos que essas peças competem extremamente bem com as fundições em propriedades mecânicas. Com o processo e os controles corretos, eles também podem competir com produtos crus e, em alguns casos, até com produtos forjados.
Controle de qualidade, ou seja, entender os requisitos de qualidade e ser capaz de validar sua peça vai realmente fazer a diferença daqui para frente.
Mas também não podemos perder de vista o fato de que a tecnologia ainda é relativamente nova. Como uma indústria, estamos fazendo muitas coisas pela primeira vez.
Isso significa que o front-end do processo precisa ser aprendido em primeiro lugar.
Por exemplo, no início do processo, os engenheiros precisarão entender as estratégias de suporte e passar algum tempo aprendendo a melhor forma de otimizar a geometria da peça e a geometria do suporte, o que por sua vez ajudará a produzir peças melhores e garantir que os suportes saiam com relativa facilidade.
Graças a este trabalho realizado no começar, você terá realizado o que era uma etapa cara e demorada de remoção de suporte e a tornou significativamente mais barata. O esforço de engenharia para fazer as peças é realmente fundamental para chegar a um ponto maduro e fazer produtos um após o outro.
Como será o futuro de Sintavia?
Parece muito emocionante! Claro, também parece bastante desafiador conforme nos mudamos para nossas novas instalações. Vamos implementar manufatura enxuta. Temos a primeira instalação de manufatura de aditivos enxutos em grande escala desenvolvida propositalmente para nosso alinhamento com OEMs e a cadeia de suprimentos.
Em 2019 continuaremos muito do trabalho que temos feito nos últimos anos, na qualificação e desenvolvimento de peças para nossos clientes.
Não vou citar nomes, mas se você olhar para as principais empresas aeroespaciais globalmente, há uma grande probabilidade de que estejamos fazendo negócios para elas.
Em algumas casos, como nosso relacionamento com a Honeywell, em que somos o primeiro fornecedor de AM aprovado para fabricar peças prontas para voo para a Honeywell Aerospace. Nós nos alinhamos com a Honeywell para usar nossa instalação atual e nossa próxima instalação para trazer isso para fora e fazer peças de produção para a Honeywell.
A Honeywell é um adotante relativamente rápido da tecnologia e eles têm muitas e muitas aplicações. But if you go outside of Honeywell, there’s a good chance, whether it’s an airframer or engine power plant, whether it’s an aerospace and defence provider, that we’re doing work for them now.
We look at 2019 and 2020 as being relatively big years for us, as far as the adoption of metal additive is concerned. It’s really exciting that Honeywell is here today, but we’re going to see that we’ll have more customers doing serial production in the coming years.
We’re aligning our company to provide that resource for the OEMs of the world so they can have a one-stop shop, vertically integrated partner for producing these parts with additive manufacturing.
Any final thoughts?
I’d like to reiterate that quality is our focus.
Our customers are, without doubt, the most risk-averse customers in the world. In order for them to feel comfortable flying these critical components made by additive manufacturing, quality is paramount to this.
At the end of the day, we want to conform products to engineering drawings and specifications, to use them in real-world applications. To do that, it takes a focus on conformance.
Also, today AM is where all of the media attention is and where a lot of time and money is being spent. But ultimately, it should be about taking the part that you made by additive manufacturing and conforming that to the engineering requirements of your customers.
So yes, we do like to talk about additive manufacturing. But I also like to think about it as advanced manufacturing. I’d like to move away from the additive manufacturing buzzwords to say we’re an advanced manufacturer of precision aerospace parts. We want to make advanced parts to ensure our customers can significantly improve their current designs.
To learn more about Sintavia, visit: https://sintavia.com/
About Doug Hedges
Doug Hedges has over 20 years’ experience in the aerospace industry, from OEM experimental component design to FAA-approved repairs, alterations and component development based on industry standard specifications and controls.
Prior to Sintavia, he served as Senior Engineer at CTS Engines, developing repairs and processes for General Electric jet engine overhaul, Lead Project Engineer for HEICO Aerospace, Senior PMA Engineer for Kapco Global, and Design Engineer for Rolls-Royce. Doug has a BSME degree in Mechanical Engineering from the University of Minnesota.
Expert Interviews
AMFG’s Expert Interviews series showcases innovative companies and individuals helping to shape the future of additive manufacturing. For more information about participating in the series, please contact [email protected].
impressao 3D
- Como você pode dimensionar para a produção aditiva em série com MES aditivo?
- Entrevista com um especialista:Professor Neil Hopkinson, Diretor de Impressão 3D da Xaar
- Entrevista com um especialista:Philip Cotton, fundador do 3Dfilemarket.com
- Entrevista com um especialista:Dr. Alvaro Goyanes da FabRx
- Entrevista com especialista:Ultimaker Presidente John Kawola sobre o futuro da impressão 3D
- Entrevista com especialista:Sintavia Presidente Doug Hedges sobre como alcançar a produção em série com impressão em Metal 3D
- Entrevista com especialista:Brian Alexander da Solvay sobre o desenvolvimento de polímeros de alto desempenho para impressão 3D
- Entrevista com especialista:Co-fundador da Carbon, Philip DeSimone, sobre como avançar para a produção de alto volume com impressão 3D
- 4 Desafios de fabricação de aditivos que podem ser resolvidos com software
- Entrevista com especialista:Jabil’s Rush LaSelle sobre o futuro da fabricação de aditivos