Entrevista com especialista:Sistemas e componentes da Dunlop Mark Statham sobre a adoção da impressão 3D para ferramentas
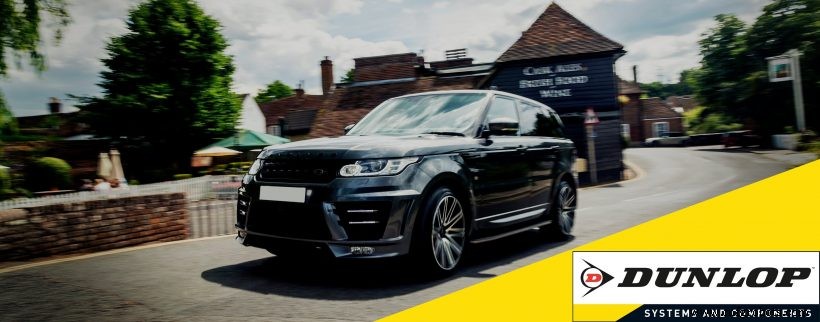
Gabaritos, acessórios e outros auxiliares de ferramentas formam a espinha dorsal de qualquer piso de produção. No entanto, não é incomum que essas ferramentas levem semanas para serem produzidas, causando gargalos no fluxo de trabalho de produção. Para superar isso, as empresas estão adotando cada vez mais a impressão 3D para acelerar a fabricação de ferramentas. A firma de fabricação automotiva do Reino Unido, Dunlop Systems and Components, é uma dessas empresas.
A Dunlop integrou a tecnologia de impressão 3D composta da Markforged em seus negócios no final de 2018. Nove meses depois, a empresa agora está imprimindo peças e protótipos em 3D em apenas alguns dias.
Na Entrevista com o Especialista desta semana, Mark Statham, Gerente de Produção e Engenharia da Dunlop, junta-se à AMFG para discutir o processo de adoção da impressão 3D e como a tecnologia está ajudando a otimizar áreas dos processos de produção da empresa.
Você poderia me falar um pouco sobre os sistemas e componentes da Dunlop?
A Dunlop Systems nasceu da empresa Dunlop original na década de 1960 e começou a produzir todos os tipos de sistemas de suspensão. Isso começou com o mini Metro e então, progressivamente ao longo das décadas, introduzimos a suspensão a ar em plataformas de fabricantes de veículos diferentes, incluindo caminhões Land Rover, GM, Isuzu e Renault, bem como veículos especializados.
Mais recentemente, entramos em mercados de nicho menores, por exemplo, entramos no mercado de ambulâncias (Renault, LDV) e no mercado de acesso para cadeiras de rodas, onde você tem veículos que podem acomodar cadeiras de rodas.
Em 2014, mudamos para uma instalação construída sob medida e isso criou uma oportunidade de nos lançarmos em novos mercados com a marca Dunlop Systems.
Que tipo de clientes e setores a Dunlop atende?
Atendemos principalmente a indústria automotiva. Por exemplo, fabricamos suspensões de veículos para todos os Land Rovers, Discoveries, etc. de alta qualidade e também fabricamos veículos especializados da Renault e Dennis.
Também atendemos a indústria ferroviária; A Bombardier é um de nossos clientes. Um dos produtos que produzimos para este setor são as válvulas.
Temos alguns clientes que compram nossos produtos e os utilizam em máquinas em movimento para que possam elevar máquinas no ar, em suspensão a ar e mova-o facilmente.
Nossos produtos também são usados no setor industrial para supressão de vibração e movimento. Uma aplicação incomum é o uso de foles convolutos para passeios em feiras - portanto, atendemos uma ampla variedade de setores.
O que levou a empresa a decidir considerar a manufatura aditiva?
A Dunlop recebe consultas e interesse de novos clientes em ter os nossos sistemas de suspensão pneumática (ECAS) instalados nos seus veículos. Os clientes estão precisando de prazos de entrega mais curtos, desde a concepção até o SOP e, como resultado, houve a necessidade de acelerar todas as partes do processo de design e fabricação.
As restrições orçamentárias são bastante restritas porque estamos tentando apoiar nosso programa de cliente sem gastar demais. Também estávamos tentando financiar novos trabalhos de desenvolvimento para atrair mais novos clientes. Então, quando fui enviado para examinar a impressão 3D, pensei que isso nos ajudaria a economizar dinheiro e talvez também ajudasse a gerar novos negócios. Foi aí que entramos pela primeira vez na impressão 3D.
Quando se tratou de propor a ideia do aditivo, foi difícil conseguir adesão no início ou toda a empresa participou desde o início?
Os engenheiros de nosso departamento de engenharia de design já haviam examinado a impressão 3D alguns anos antes.
Temos nossas próprias instalações de teste, onde projetamos e construímos suspensões e depois as colocamos em um teste de resistência. Obviamente, essas suspensões devem durar um milhão de milhas. Eles são colocados em altas taxas de resistência em alta frequência e alta velocidade e ficam lá por cerca de duas semanas, o que simula a vida útil da unidade de suspensão.
Quando nossos engenheiros olharam pela primeira vez para a impressão 3D, eles descobriram que não poderiam alcançar esse tipo de vida útil com os materiais que estavam disponíveis. Mas não descartamos a tecnologia.
No ano passado, meu diretor me abordou e perguntou se eu participaria de um seminário online para ver se, e como, poderíamos usar a impressão 3D. O seminário, conduzido pela Markforged, mostrou a tecnologia e os materiais que eles tinham e, mais importante, como outros os usaram. Foi quando pensei que a impressão 3D poderia ser benéfica para nós também.
Mas para realmente fazer um caso de negócios para isso, tive que examinar quais peças estavam para conserto, o que precisava de uma revisão ou substituir e depois montar uma planilha com o que nos custaria.
Algumas peças são substituídas anualmente, outras são substituídas quando se quebram. Ficou claro que ter uma impressora 3D a bordo não substituiria completamente todas as ferramentas porque temos algumas ferramentas de alto uso, alta temperatura e alto impacto.
Mas isso nos forneceria a opção de substituição. Considerando os custos de aquisição da impressora e os custos mensais de funcionamento, calculei que veríamos facilmente o retorno do investimento em dois anos.
Eu compilei uma lista de cerca de 100 peças de ferramentas, que pensei que poderíamos substituir e que precisavam ser substituídas, ou que não tínhamos recursos para substituir. Com base nisso, pudemos justificar as despesas.
Cerca de três semanas depois, recebemos nossa impressora e recebemos o retorno em seis meses.
Como era o processo de implantação da tecnologia nos primeiros dias?
Quando a impressora 3D chegou, estávamos funcionando em cerca de uma hora. Começamos examinando a lista de nossos critérios mais importantes.
Não queríamos que rodasse durante a noite naquele ponto. Queríamos manter as coisas simples e focar nas ferramentas simples que estavam na lista de prioridades.
Por exemplo, temos itens de suspensão de alta qualidade que vão em veículos de alta qualidade como Bentleys, Audis e Porsches. Um de nossos principais clientes compra nossos módulos e adiciona seus próprios componentes para criar um amortecedor pneumático completo. Por serem componentes de veículos de alta qualidade, temos ferramentas de nylon para mantê-los no lugar durante o processo de proteção das peças. Essas ferramentas de náilon se desgastam, ficam sujas e não são muito atraentes, então as peças de náilon de reposição foram os primeiros itens que imprimimos. Substituímos o náilon branco pelo Black Onyx da Markforged.
Isso foi bem recebido porque estávamos recebendo as peças imediatamente. Normalmente, se precisarmos substituir uma peça, devemos primeiro localizar o desenho, enviar para cotação e aguardar a volta da cotação do ferramenteiro, o que pode levar dias.
O simples fato de receber a papelada para levantar o pedido demorou cerca de uma a duas semanas. Então, para eles fazerem a peça, dependendo de quão complexo era, pode levar mais uma semana.
Você está olhando para um retorno de no mínimo duas semanas, enquanto estávamos imprimindo peças diariamente. Foi quando nossos colegas do chão de fábrica realmente viram os benefícios da impressão 3D.
As primeiras peças impressas eram peças muito simples. Então começamos a percorrer as peças e aprendemos como eram leves, mas ao mesmo tempo como eram fortes as peças impressas em 3D. Isso abriu uma ampla gama de ferramentas que poderíamos substituir.
Foi muito bem recebido na primeira semana; o chão de fábrica estava recebendo peças em dias e horas, em vez de semanas. E porque somos o padrão IATS, leva mais tempo para o departamento de qualidade inspecionar a peça do que para nós para imprimi-la.
Você disse que começou de forma simples. O uso da impressão 3D evoluiu ao longo dos nove meses em que você teve a impressora 3D?
sim. Agora podemos fazer peças e ferramentas muito complexas e desenvolvemos métodos de fixação de duas peças impressas em 3D juntas.
Temos muitos clientes de pequeno nicho que produzem veículos com acesso para cadeiras de rodas. Desenvolvemos parcerias com essas empresas e parte disso é para apoiar seus orçamentos relativamente pequenos. Outros clientes menores estavam recebendo ferramentas que utilizamos de ferramentas obsoletas; não parecia atraente, mas ainda funcionava.
Agora, para esses clientes, podemos imprimir em 3D trabalhos muito complexos segurando peças que se ajustam perfeitamente às suas peças e as protegem melhor do que antes. Isso também significa que podemos entregar a peça a eles mais rapidamente, com menos risco de danificá-la, porque agora é uma ferramenta de engenharia adequada.
Também estamos experimentando diferentes técnicas de junção. Por exemplo, porque moldamos todos os nossos produtos internamente, nosso produto precisa ser expandido antes de entrar no processo de moldagem.
Temos uma máquina de expansão no chão de fábrica que nos custou cerca de £ 14.000 para desenvolver internamente. Nós o chamamos de "foguete" porque tem cerca de dois metros de comprimento e cerca de dois metros de altura. Ele aponta em um ângulo em direção ao operador, para que o operador possa carregar e descarregar o produto com bastante facilidade. Mas a área de trabalho real tem apenas meio metro de comprimento. Mas é todo o acionamento dessa máquina que faz o produto se expandir.
Para a área de trabalho, agora imprimimos em 3D um tubo de meio metro e ele é impresso em seis partes diferentes que unimos.
Fizemos o primeiro teste de expansão de um produto neste tubo de meio metro em vez de na máquina maior. Mas este protótipo de fixação custa apenas £ 600, uma fração do custo.
Como agora somos fornecedores de um novo fabricante automotivo, provavelmente precisaremos de cerca de seis dessas máquinas. Se funcionar, podemos economizar muito dinheiro.
Uma das coisas que as empresas costumam nos dizer é que precisam ter experiência interna em AM para poder adotar a tecnologia com sucesso. Este foi um problema que você enfrentou?
Temos cinco pessoas em minha equipe e nosso departamento administra e faz a manutenção da impressora 3D. Todos em nosso departamento aprenderam rapidamente a tecnologia e estamos tentando coisas diferentes.
Outros departamentos estão lentamente se acostumando com a tecnologia. Por exemplo, imprimimos alguns medidores para nosso departamento de qualidade. O departamento de qualidade precisa verificar se certas peças estão dentro da tolerância. Como eles não são altamente críticos, imprimimos em 3D alguns medidores para eles. Portanto, nosso departamento de qualidade aceitou algumas dessas ferramentas impressas em 3D.
Também produzimos algumas peças de protótipo para nossa equipe de design. As peças do protótipo são normalmente muito caras porque você deve usiná-las de aço ou alumínio sólido.
Na suspensão a ar de um veículo, você normalmente tem polainas, que evitam que as pedras atinjam a suspensão e rompam o air bag. Esta polaina é apoiada nas escoras por meio de um colar de plástico. Por ser um protótipo, não poderia ser moldado porque ninguém projetaria um molde para um protótipo. Ele poderia ter sido usinado a partir de um sólido, mas o design é tão complexo que provavelmente seria necessária uma máquina CNC especializada.
Como resultado, imprimimos em 3D alguns protótipos de colares e, por ser uma impressão em 3D, podemos atingir a tensão necessária porque ele precisa se torcer e se mover com um veículo. Isso foi muito bem sucedido.
No entanto, quando você está olhando para potencialmente 50.000 veículos por ano, são 100.000 desses produtos, ainda não está em nosso reino de possibilidades, porque temos apenas uma impressora. Não somos uma empresa de manufatura 3D atualmente.
Portanto, agora a equipe de design ainda está procurando moldar essas peças e obter um molde de plástico. A impressão 3D tem estado bem para o desenvolvimento, mas ainda é um processo lento.
Qual é a visão da Dunlop para a tecnologia no futuro? Você vê o uso da impressão 3D se expandindo para outros aplicativos?
Atualmente, estamos nos concentrando em ferramentas porque precisamos recriar completamente uma nova linha de ferramentas nos próximos 12 a 18 meses. Estamos no processo de projetar isso com impressão 3D.
Temos todos os designs atuais, que funcionaram bem para a nossa linha atual. Com a impressão 3D, você precisa fazer uma ligeira conversão para tornar a peça mais forte em certas áreas e agora podemos adicionar fibra de carbono. Portanto, esse é o nosso foco agora.
No entanto, como projetamos peças de suspensão da década de 1960, ainda temos clientes que as compram. Portanto, a indústria ferroviária compra nossas válvulas de nivelamento de projeto antigo. Trata-se de um elemento no corpo que usa um sistema básico de alavanca para mover o ar de uma parte do trem para a outra, de modo que ele se incline nas curvas. É usado por clientes como Virgin Trains e Bombardier.
Esta parte foi projetada na década de 1960 e no início dos anos 1970. A fundição original, que é em alumínio, está se desgastando, então estamos tentando reformar essa fundição, que é bastante cara. Mas também há a opção de imprimir o corpo em 3D para depois utilizar o sistema. Essa é uma possibilidade. Certamente precisaremos de mais impressoras para isso.
Outra coisa que estamos analisando é se podemos reciclar alguns de nossos produtos porque os moldes estão ficando muito velhos.
O que o próximo ano reserva para a Dunlop?
Vai ser um ano muito agitado para nós, pois temos o lançamento de uma nova plataforma de veículo elétrico chegando. Devemos também apoiar nossos negócios crescentes em sistemas ECAS para outros OEMs que obtiveram a acreditação IATF 16949. Além disso, vamos nos concentrar no importante mercado de reposição, que tem sido um modelo de negócios de longa data para nós.
O foco da nossa empresa será na produção OEM de alto volume, menor produção pós-venda e no desenvolvimento de nossa linha industrial de componentes antivibração.
Em relação à impressão 3D, estamos sobrecarregando nossa impressora 3D - ela não parou de funcionar. Portanto, também pretendemos comprar uma impressora nova e maior. Isso significa que teremos duas impressoras funcionando, o que nos dará mais rendimento.
Para saber mais sobre os sistemas Dunlop, visite: https://www.dunlopsystems.com/
impressao 3D
- Entrevista com um especialista:Professor Neil Hopkinson, Diretor de Impressão 3D da Xaar
- Entrevista com um especialista:Philip Cotton, fundador do 3Dfilemarket.com
- Entrevista com um especialista:Spencer Wright de pencerw.com e nTopology
- Entrevista com um especialista:Dr. Alvaro Goyanes da FabRx
- Entrevista:Terry Wohlers sobre o Relatório Wohlers 2018, a ascensão da impressão 3D e para onde a indústria está indo
- Entrevista com especialista:Duncan McCallum, CEO da Digital Alloys, sobre a impressão Joule e o futuro da impressão 3D em metal
- Entrevista com especialista:Nano Dimension Co-Fundador Simon Fried sobre a ascensão da impressão 3D para eletrônicos
- Soluções de impressão 3D para empresas de petróleo e gás
- BigRep e Bosch Rexroth confirmam parceria de desenvolvimento para sistemas de impressão 3D
- A fabricação e ferramentaria de peças metálicas para sistemas de injeção de combustível