Novas abordagens para a fabricação de peças para a mancha de óleo
O fracking levou a grandes mudanças na camada de óleo e grandes mudanças na usinagem de peças.
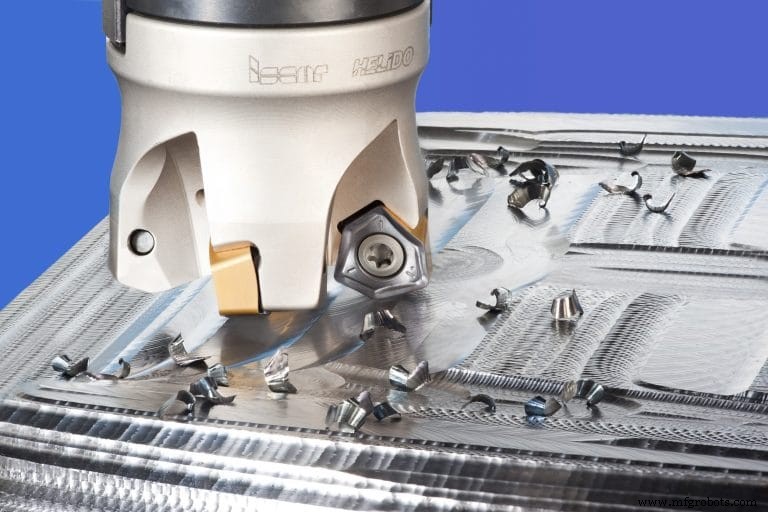
Rod Zimmerman, do fabricante de ferramentas de corte Iscar Metals, mora em uma agradável zona verde em um subúrbio de Fort Worth. No entanto, a menos de 800 metros de sua casa, uma empresa petrolífera afundou um buraco vertical de 2.286 m de profundidade, do qual se estendeu nove linhas laterais, cada uma com cerca de 800 metros. Está bombeando fluido de fraturamento para essas linhas a 9.000 psi para extrair o gás natural. É um exemplo tão bom quanto qualquer um da onipresença da revolução do fracking e da incrível tecnologia envolvida.
E embora a revolução possa não estar literalmente “em todos os lugares”, Salvatore Deluca, gerente de produto de outro fabricante de ferramentas de corte, Allied Machine &Engineering, disse que as gigantescas instalações de fraturamento em seu município são chamadas de “cidades”. Exceto que, ao contrário de Dallas-Fort Worth, essas “cidades” estão no distante Ohio, um estado que não era conhecido anteriormente pelo petróleo. Não é surpresa, então, que grandes mudanças no remendo de óleo tenham levado a grandes mudanças na usinagem de peças para o remendo de óleo.
Enfrentando o bloqueio de fraturamento
Como mencionado acima, o fraturamento hidráulico (mais comumente chamado de fracking) recupera gás e petróleo das formações de xisto perfurando a terra e injetando uma mistura de água, areia e produtos químicos na rocha a uma pressão extremamente alta. Gerar essa pressão requer bombas gigantes, cujo componente chave é o “fluid end” ou “fracking block” e suas válvulas, pistões e revestimentos.
A alta pressão e abrasividade da polpa bombeada através desses blocos causam rápido desgaste e rachaduras. E como os operadores de campos petrolíferos precisam manter alta pressão, eles são forçados a substituir as extremidades do fluido a cada poucos dias, de acordo com Paul Best, especialista em produtos da Allied Machine, Dover, Ohio. As melhores extremidades fluidas são usinadas a partir de blocos sólidos de aço e geralmente têm cerca de 3' de altura, 4' de largura e 2-3' (0,61-0,91 m) de espessura. Com contornos complexos, vários canais, três a cinco furos passantes (cada um com até 8″ [203,2 mm] de diâmetro) e três a cinco furos cruzados de interseção, as extremidades fluidas exigem grandes quantidades de fresamento, furação e rosqueamento.
Zimmerman, vice-presidente de vendas da Zona Oeste da Iscar, disse que as extremidades do fluido são tradicionalmente feitas de liga de aço da série 4000, mas para combater o desgaste, os usuários estão tentando “ligas mais exóticas, como material de aço inoxidável 17-4 PH, aço inoxidável super duplex e aço inoxidável 15-5.” Deluca estimou que cerca de metade das extremidades fluidas que ele vê agora são uma variante de um aço inoxidável pré-endurecido e a proporção continua a crescer.
Gayle Vollmer, serviços de engenharia da Hartwig em Houston (revendedor da Okuma na área) disse que também há um movimento para usar materiais mais duros para as partes de um bloco de fraturamento que são mais suscetíveis ao desgaste e uma tentativa de redesenhar blocos de fraturamento para que mais componentes são facilmente substituíveis. Mas ele supôs que a demanda atual por alta produção colocou essa pesquisa “em segundo plano”.
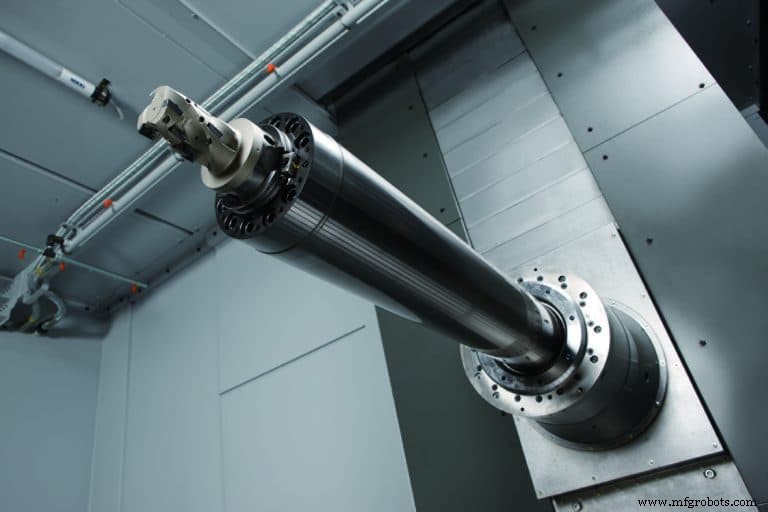
Seja feito de 4340 ou de um aço inoxidável mais duro, lidar com uma extremidade fluida praticamente exige uma grande mandriladora ou centro de usinagem horizontal. Jason Schooley, gerente regional de vendas da JTEKT Toyoda Americas, Arlington Heights, Illinois, disse que o objetivo é realizar o maior número possível de operações em uma única máquina, o que é duplamente importante em uma peça tão grande e difícil de mover.
Schooley disse que enquanto as mandriladoras normalmente têm mesas maiores para peças ainda maiores, as horizontais como a FH1250SX da Toyoda são quase quatro vezes mais rápidas. Isso se deve em parte a um fuso de 6.000 rpm acionado por engrenagem (opcionalmente 8.000 rpm ou um fuso de alto torque de 15.000 rpm) e uma taxa de alimentação rápida de 1.654 ipm (42 m/min). A máquina é construída em uma base de ferro fundido Meehanite para máxima rigidez com guias de rolos cilíndricos para maior velocidade, enquanto o acionamento de fuso de esferas duplo nos eixos Y e Z aumenta a estabilidade da usinagem durante o corte pesado.
O FH1250SW também possui um eixo W para operações de perfuração profunda e mandrilamento. Ele acrescentou que nos últimos anos “vários fabricantes de máquinas-ferramenta optaram por um cabeçote de eixo U integrado” ou um eixo W, que são paralelos ao eixo X ou ao eixo Z, respectivamente. Isso torna possível alterar o centro de rotação para uma ferramenta de torneamento fixa, um recurso útil ao cortar furos grandes ou outros contornos grandes. Isso ocorre porque não apenas as extremidades do fluido têm furos grandes, como os furos geralmente são “em forma de garrafa” por dentro, para que não possam ser simplesmente perfurados. Para máquinas que não possuem eixo U integrado, os usuários podem adicionar um cabeçote “feed-out” que executa a mesma função, sendo a D’Andrea um desses fornecedores.
Existem desvantagens na montagem de um cabeçote grande em um fuso rotativo, incluindo possível interferência de peças e incompatibilidade com o fornecimento de refrigerante através do fuso. A opção de pós-venda também precisa de sua própria unidade externa e pode não ser possível trocar automaticamente o equipamento como faria com outras mudanças de ferramenta.
Mas Schooley disse que a interferência não é um problema nas aplicações do bloco de fraturamento se o deslocamento do eixo Z da máquina for longo o suficiente para impedir que o cabeçote adicional se estenda além da linha do medidor. Com 1.850 mm de deslocamento no eixo Z e 200 mm do nariz do fuso até a zona morta do centro da mesa, a máquina 1250 lida com blocos de fraturamento sem interferência. Ele acrescentou que a Toyoda desenvolveu ainda mais a capacidade de troca automática para seus cabeçotes de contorno para “ajudar nossos clientes a ficarem à frente da curva em um setor tão volátil quanto o petróleo”.
Na experiência da Schooley, as ferramentas modulares de mandrilamento disponíveis da Innovative Tooling Solutions e outras vêm com refrigeração no fuso como recurso padrão e muitas oficinas que fazem blocos de fraturamento usam uma mandrilar horizontal dedicada com um cabeçote de contorno para terminar os furos. A Toyoda também oferece centros de usinagem horizontal de eixo-árvore com 1.560 ft-lb de torque para operações pesadas. Schooley disse que o fuso de 4.000 rpm combina o alcance e a força necessários para mandrilamento e perfuração profunda, permitindo que peças de trabalho que antes exigiam duas operações sejam concluídas em uma única máquina. O palete rotativo de 360.000 posições da máquina oferece flexibilidade máxima para usinagem pesada em uma variedade de peças.
Okuma America Inc., Charlotte, N.C., desenvolveu uma opção de programação chamada Turn-Cut que permite que um centro de usinagem horizontal imite um torno no corte de recursos circulares e angulares em peças grandes e desbalanceadas sem usar um cabeçote em U. Como explicou Ted Winkle, coordenador do centro de tecnologia da Okuma em Houston, “em vez de girar a peça, o que seria difícil ou impossível para algumas peças grandes, você gira a ferramenta ao redor da peça. E, em vez de um cabeçote em U movendo a ferramenta para fora do centro do eixo rotacional, o Turn-Cut interpola esses eixos em X e Y enquanto também alimenta uma ferramenta de torneamento de ponto único em Z.”
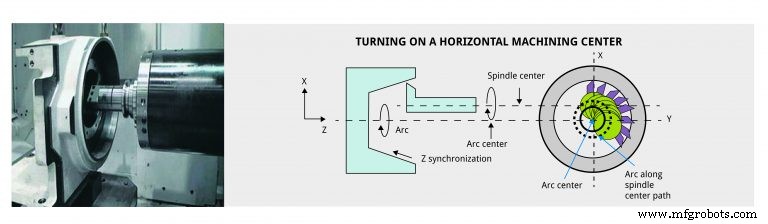
Winkle acha que a Turn-Cut desempenhará um papel maior na indústria de petróleo e gás para peças como blocos de fraturamento porque “à medida que os furos aumentam de diâmetro, é preciso muito torque para executar uma ferramenta sólida para fazer um furo desse tamanho. Ter capacidade de corte por rotação, em oposição a um cabeçote em U e todas as ferramentas caras associadas a isso, é um benefício.”
Por outro lado, o Turn-Cut não é barato porque requer software adicional para aceleração, desaceleração e sincronização especializada, além de escalas de vidro e resfriamento de fuso de esferas. Mas você obterá melhor precisão para uma variedade de peças com esses recursos e aumentará a probabilidade de poder terminar as peças em uma configuração.
Schooley respondeu que a técnica requer muito movimento repetitivo na mesma área dos fusos de esferas e guias (quanto menor o diâmetro, mais isso ocorreria) e isso poderia diminuir a vida útil da máquina.
Então, novamente, disse Winkle, a menos que você use esse recurso com frequência em peças do mesmo tamanho, você não terá movimento excessivo na mesma área. E se você não precisar do recurso com frequência, não poderá justificar a grande despesa de um eixo U, portanto, o Turn-Cut seria uma opção mais lógica. Como qualquer recurso de máquina-ferramenta, existem compensações.
Paraíso da potência
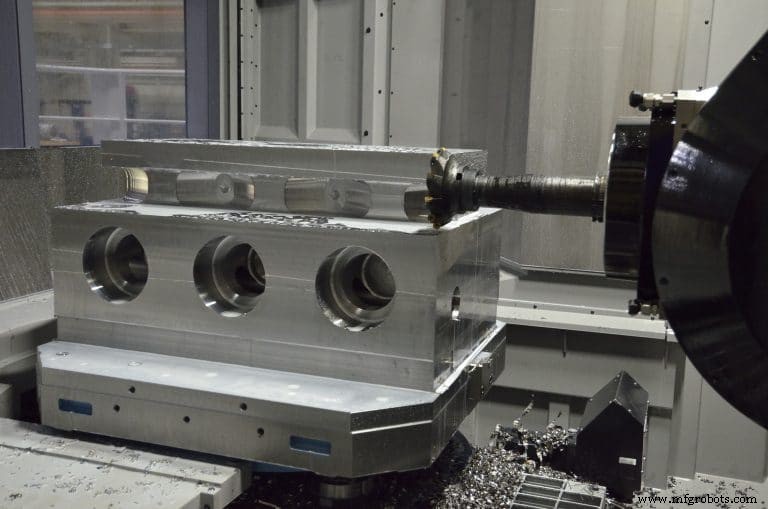
Para Makino Inc., Mason, Ohio, as plataformas de referência para peças como blocos de fraturamento são seus centros de usinagem horizontal de cinco eixos T1 e T2. David Ward, gerente de marketing de produto, disse que ambas as máquinas possuem fusos de acionamento direto que são “ideais para os desafiadores aços inoxidáveis e de alta liga usados nesta indústria”.
O T1 tem um fuso HSK100 de 12.000 rpm com 143 hp e torque nominal de serviço de 740 pés-lb. O fuso T2 maior utiliza uma interface HSK125 para rigidez radial. O fuso T2 de 4.000 rpm oferece 200 HP e 1.107 pés-lb de potência e torque nominal de serviço.
Ward acrescentou que ambos os fusos mantêm seus valores máximos de torque até 1.000 rpm. “Ao levar os valores máximos de torque até este ponto, garante que o fuso será capaz de aproveitar os novos avanços na tecnologia de ferramentas de corte, como revestimentos de pastilhas de alta temperatura.”
Winkle observou que a mancha de óleo é dominada por máquinas CAT 50, mas concordou que o contato facial fornecido pelas interfaces HSK e BIG Plus seria uma vantagem “se você tiver uma longa saliência. Mas como a maioria das forças de usinagem são axiais, não faz muita diferença qual tipo de fuso você escolhe. Desde que seja grosso. “Aproximar-se de um bloco de fraturamento com uma máquina de fuso ISO 40 seria um exercício de futilidade”, disse ele.
As fontes concordaram que a refrigeração de alta pressão é essencial para a remoção de calor e cavacos em muitas aplicações de petróleo e gás, ou como Zimmerman da Iscar disse, “quase independentemente da aplicação. Ao trabalhar profundamente em um furo em uma extremidade fluida, é fundamental remover os cavacos e é difícil fazê-lo. Uma ferramenta de fresamento alimentada por refrigeração é de longe o caminho a percorrer em tais aplicações.”
Portanto, se a máquina não veio com esse recurso, os usuários estão adicionando unidades de fornecedores como ChipBLASTER. “Eu nem consideraria comprar uma fresadora hoje sem refrigeração de alta pressão no fuso”, disse Zimmerman. “É um divisor de águas tanto para fresamento quanto para perfuração.” A única exceção é uma situação em que você não pode direcionar a refrigeração para a aresta de corte. Nesse caso, o refrigerante “às vezes funciona contra você e é melhor usinar a seco para evitar rachaduras térmicas das pastilhas”, disse ele.
Deluca disse que os fabricantes de máquinas-ferramenta responderam a essa demanda de tal forma que agora ele normalmente encontra máquinas com uma bomba fornecida pelo OEM fornecendo 1.000 psi a 20 gpm. Ward disse que o T1 da Makino fornece 26 gpm a 1.000 psi, enquanto o T2 fornece essa mesma pressão a 53 gpm.
Avanços da ferramenta de corte
Embora você possa adorar ter um monstro de alta potência para seus blocos de fraturamento, Deluca, da Allied Machine, disse que enfrenta cada vez mais o desafio oposto:a necessidade de fazer furos grandes com máquinas focadas em fresamento onde as velocidades do fuso são maiores, mas a potência atinge o máximo de 40 a 50.
“As empresas que fabricam essas peças geralmente são de pequeno a médio porte e normalmente não se dedicam à fabricação de blocos de fraturamento”, disse ele. “E muitas pessoas desconfiam de se concentrar neste mercado e gastar meio milhão de dólares em uma máquina para uma indústria que funciona como uma montanha-russa. Portanto, tivemos
que desenvolver uma ferramenta que pode cortar um furo de 4″ de diâmetro em velocidades de fuso muito mais altas e taxas de avanço muito mais baixas do que nossos produtos de furação tradicionais.”
O desafio na perfuração de blocos de fraturamento vai além do tamanho dos furos necessários. “Cortes interrompidos são inerentes à fabricação de blocos de extremidade fluida, pois os furos cruzados são perfurados perpendicularmente aos furos existentes”, disse Allied Machine's Best. “Devido à forma resultante dos furos de interseção, as bordas externas da broca continuarão engatadas no corte, enquanto a borda interna não. Isso pode desestabilizar a broca, o que pode destruir a ferramenta e danificar a integridade do bloco de fraturamento.”
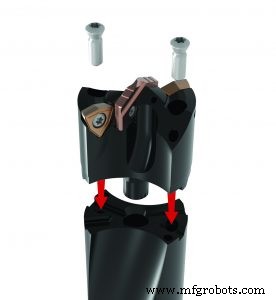
Além disso, se o cliente estiver economizando usando material que não foi tratado termicamente, a broca pode encontrar variações significativas. Deluca, da Allied, disse que normalmente isso significa que um operador deve monitorar constantemente o processo ou arriscar uma falha catastrófica da broca em segundos após atingir um bolso na fundição, o que pode destruir uma peça em que você colocou horas. As oficinas também experimentam variações de material de bloco para bloco, dificultando a escolha da broca e dos parâmetros operacionais perfeitos.
A Allied enfrentou esses desafios com uma ferramenta de “próxima geração” chamada APX. Possui um substrato de metal duro mais resistente e um revestimento exclusivo para resistir ao choque de atingir um bolso. “Você pode lascar a ferramenta e ouvir um guincho”, disse Deluca, “mas ainda poderá terminar o buraco”.
Ele acrescentou que a Allied abordou as dificuldades da perfuração de furos cruzados adicionando um alisador à pastilha para melhorar a estabilidade, além de pastilhas de desgaste para fornecer estabilidade adicional quando o piloto sai em um espaço vazio ou em um furo cruzado. “Também recomendamos diminuir o avanço e manter a mesma velocidade ao perfurar orifícios de saída em ângulo para que a ferramenta não queira empurrar ou andar. Geralmente não é necessário ao perfurar a linha principal ou os furos transversais, mas há muita engenharia que você pode colocar em uma ferramenta para compensar o corte extremamente interrompido dos furos angulares.”
Para fresamento, Zimmerman disse que a pastilha HeliDo H600 de dois lados e seis cantos da Iscar funciona extremamente bem para esse tipo de material. “Também oferecemos o Mill 4 Feed, uma pastilha quadrada de face única com uma geometria mais positiva para um corte mais suave que requer menos potência.”
Sua principal mensagem é que, como a Iscar está comprometida há muito tempo com a indústria de petróleo e gás e contrata apenas maquinistas experientes, ela pode desenvolver o processo ideal para um cliente e escolher entre uma ampla variedade de ferramentas. “Temos muitos estilos de fábricas de ração e podemos otimizar uma fábrica de ração com base na aplicação, material e máquina, considerando sua rigidez, potência e torque.”
Multitarefa e automação
É provável que blocos de fraturamento de 9.500 libras não levem a pensar em “automação”, mas Makino e outros construtores oferecem soluções que permitem que um operador execute várias máquinas. Para blocos de fraturamento, isso geralmente significa um trocador de paletes rotativo que alterna entre uma peça bruta e uma peça acabada em menos de um minuto. Depois disso, o operador tem bastante tempo para retirar a peça acabada.
Com tempos de ciclo de alguns minutos, os tubos das pistolas de fraturamento estão na outra extremidade do espectro. E como eles são um “item de uso único”, disse Vollmer, “as taxas de produção são astronômicas. Milhares são feitos todos os dias.”
Como resultado, a peça é ideal para automação, e Hartwig e Okuma trabalharam juntos para oferecer várias opções. Isso inclui robôs para sistemas de carga/descarga e alimentação por barra, como aqueles usados para peças pequenas em tornos estilo suíço, exceto que aqui eles lidam com diâmetros de 2-4″. A abordagem mais rápida alimenta o material em uma máquina de fuso duplo, usinando uma extremidade e, em seguida, alimentando a peça diretamente no subfuso para trabalhar na outra extremidade.
Vollmer disse que as peças requerem torneamento, rosqueamento e algum fresamento, idealmente usando ferramentas vivas para o último, um recurso que Winkle se referiu como “uma das maiores mudanças na indústria nos últimos anos”. Fracking e perfuração direcional são novamente um grande motivo para essa transição.
No entanto, para muitas das peças amplamente cilíndricas necessárias nas operações de “fundo” de hoje, o torno ideal tem mais do que ferramentas vivas e uma ou duas torres. Possui cabeçote giratório e capacidade de fresamento multi-eixos, como a série MULTUS de torneamento da Okuma.
“As peças necessárias tanto para a perfuração quanto para a fase de completação são muito mais complexas do que nos poços verticais tradicionais”, explicou Winkle. “Você precisa ser capaz de abrir e fechar válvulas para mudar as zonas de produção. As peças têm encanamento hidráulico através delas, bem como equipamentos de monitoramento eletrônico.”
Isso requer furos cruzados e intrincados recursos fresados no diâmetro externo e interno, de modo que as máquinas precisam de posicionamento de cinco eixos e nove ou mais eixos de movimento da máquina para cortar uma peça em uma extremidade e trocar os fusos para trabalhar na outra.
Os fios são outro desafio. Winkle disse que existem literalmente centenas de tipos e as tolerâncias são apertadas:“Mais 1,5 mil, menos nada”. Isso porque, em petróleo e gás, as roscas não apenas mantêm as peças juntas, “elas têm que selar perfeitamente e suportar um enorme estresse de tração da gigantesca sequência de peças que percorre quilômetros de profundidade no buraco”, disse Winkle. “E eles têm que lidar com expansão térmica e carga de choque. Este componente de vedação e suporte de carga não existe em nenhuma outra indústria.”
Cortar esses fios requer uma máquina rígida e uma configuração que resista à vibração. Kyle Downs, diretor de gerenciamento de projetos e marketing da SMW Autoblok, Wheeling, Illinois, disse que tudo isso é complicado pelo fato de que “o material recebido é muito inconsistente. A automatização da centralização de tubos em gancho, dobrados e/ou oblongos pode ser alcançada com dois cenários, um mandril de compensação e autocentragem 3+3 ou um mandril de compensação e uma solução de centragem montada no cabeçote móvel, que normalmente também é um mandril .”
Finalmente, a adição da capacidade de deposição de metal a laser para máquinas de remoção de metal adiciona novas possibilidades, como exemplificado pela nova série LASER EX da Okuma. Se, por exemplo, você tivesse uma peça com apenas alguns recursos salientes, você poderia adicionar esses recursos ao corpo principal, em vez de cortar os recursos do estoque maior. Isso é potencialmente uma enorme economia no tempo de usinagem.
Winkle acrescentou que você também pode fundir materiais diferentes, combinando, digamos, Inconel e aço inoxidável, o que “nunca é possível com tecnologia puramente subtrativa. A junta é tão forte ou mais forte do que se fosse usinada a partir de um sólido”, disse ele.
Isso tem potencial imediato em petróleo e gás para adicionar as almofadas de desgaste necessárias em conjuntos de perfuração ou adicionar as aletas laterais usadas para evitar que o tubo raspe o diâmetro interno de um revestimento de poço à medida que se move por uma curva em um poço direcional. Okuma também oferece a capacidade de endurecer uma zona de material até cerca de 50 Rockwell usando o mesmo laser com uma abertura diferente.
Sistema de controle de automação
- Nova Certificação para a Elite de Lubrificação
- Argumentando sobre chips neuromórficos para computação IA
- Repensando a Manufatura Inteligente para o Novo Normal
- Se data for o novo óleo, quem é o seu refinador?
- Para cadeias de suprimentos, a experiência do cliente é o novo diferencial
- Preparando sua cadeia de suprimentos para o futuro para o novo normal
- A pandemia está gerando um novo modelo para tomada de decisão na cadeia de suprimentos
- A nova onda de desafios para fabricantes de equipamentos industriais
- As 5 principais peças de Stromag para sua plataforma de petróleo
- Encontrando as peças certas da máquina:conselhos para engenheiros