17 Capítulo 7:Manufatura Enxuta
OBJETIVO
Após concluir esta unidade, você deverá ser capaz de:
- Aplique 5S em qualquer oficina mecânica.
- Descreva o conceito Kaizen.
- Descreva a implementação do Lean Manufacturing.
Lean 5S:
“5S” é um método de organização do local de trabalho que consiste em cinco palavras:Ordenar, Colocar em ordem, Brilhar, Padronizar e Sustentar. Todas essas palavras começam com a letra S. Esses cinco componentes descrevem como armazenar itens e manter o novo pedido. Na tomada de decisões, os funcionários discutem a padronização, o que deixará claro o processo de trabalho entre os trabalhadores. Ao fazer isso, cada funcionário se sentirá dono do processo.
Fase 0:Segurança
Muitas vezes se supõe que um programa 5S executado corretamente melhorará a segurança no local de trabalho, mas isso é falso. A segurança não é uma opção; é uma prioridade.
Fase 1:classificação
Revise todos os itens do local de trabalho, mantendo apenas o necessário.
Fase 2:endireitar
Tudo deve ter um lugar e estar no lugar. Os itens devem ser divididos e rotulados. Tudo deve ser organizado cuidadosamente. Os funcionários não devem ter que se curvar repetidamente. Coloque o equipamento perto de onde ele é usado. Esta etapa é parte do motivo pelo qual o lean 5s não é considerado “limpeza padronizada”.
Fase 3:brilho
Certifique-se de que o local de trabalho esteja limpo e arrumado. Ao fazer isso, será mais fácil estar ciente de onde as coisas estão e onde deveriam estar. Depois de trabalhar, limpe a área de trabalho e devolva tudo à sua posição anterior. Manter o local de trabalho limpo deve ser integrado à rotina diária.
Fase 4:padronizar
Padronizar os procedimentos de trabalho e torná-los consistentes. Todo trabalhador deve estar ciente de quais são suas responsabilidades ao seguir os três primeiros passos.
Fase 5:Sustentação
Avaliar e manter os padrões. As etapas acima mencionadas devem se tornar a nova norma em operação. Não volte gradualmente aos velhos hábitos. Ao participar do novo procedimento, pense em maneiras de melhorar. Revise as quatro primeiras etapas quando novas ferramentas ou requisitos de saída forem apresentados.
Kaizen
Enquanto o processo lean 5S foca na remoção de desperdícios, o Kaizen foca na prática da melhoria contínua. Assim como o Lean 5S, o Kaizen identifica três aspectos principais do local de trabalho:M uda (resíduos), M ura (inconsistências) e M uri (tensão em pessoas e máquinas). No entanto, o processo Kaizen passo a passo é mais extenso que o processo lean 5S.
A visão geral do processo Kaizen:
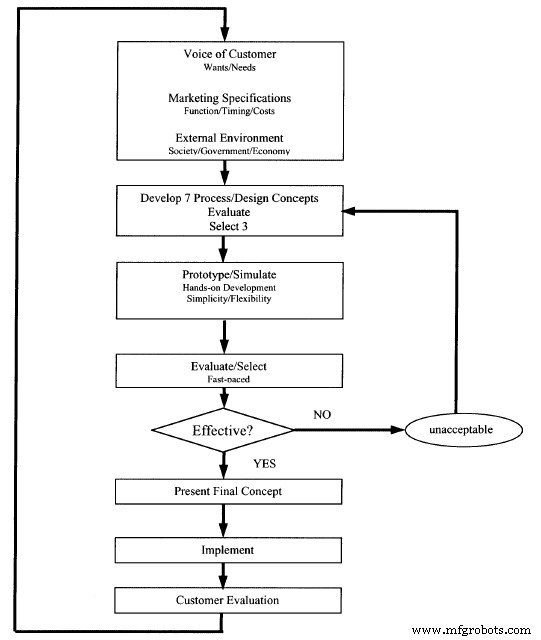
1. Identifique um problema.
2. Forme uma equipe.
3. Reúna informações de clientes internos e externos e determine metas para o projeto.
4. Revise a situação ou processo atual.
5. Faça um brainstorming e considere sete alternativas possíveis.
6. Decida as três melhores alternativas das sete.
7. Simule e avalie essas alternativas antes da implementação.
8. Apresentar a ideia e sugestões aos gestores.
9. Implemente fisicamente os resultados do Kaizen e leve em consideração os efeitos.
A manufatura enxuta melhora com o passar do tempo, por isso é importante continuar a educação sobre como manter os padrões. É crucial mudar os padrões e treinar os trabalhadores quando apresentados a novos equipamentos ou regras.
Lean
Pense em um departamento de manutenção como atendendo clientes internos:os vários departamentos e funcionários da empresa.
Lean é diferente do modelo ocidental tradicional de produção em massa que depende de economias de escala para gerar lucros. Quanto mais você fizer, mais barato o produto se tornará, maior será a margem de lucro potencial. Baseia-se em previsões das necessidades do cliente ou na criação das necessidades do cliente. Tem dificuldade em lidar com mudanças incomuns na demanda.
A produção enxuta responde à demanda comprovada do cliente. Processamento puxado – o cliente puxa a produção. Em um sistema de massa, o produtor empurra o produto para o mercado, empurra o processamento.
Construir uma cultura de longo prazo que se concentra na melhoria.
Respeito pelos trabalhadores mais bem treinados e educados, mais flexíveis
Lean é uma filosofia que se concentra no seguinte:
- Atender às necessidades do cliente
- Melhoria contínua e gradual
- Fazer produtos continuamente melhores
- Valorizando a contribuição dos trabalhadores
- Visão de longo prazo
- Eliminando erros
- Eliminando o desperdício
Desperdícios:usar muitos recursos (materiais, tempo, energia, espaço, dinheiro, recursos humanos, instruções ruins)
Resíduos:
- Superprodução
- Defeitos
- Processamento desnecessário
- Esperando (perdendo tempo)
- Desperdiçando tempo e talento humanos
- Muitos passos ou deslocamentos Transporte excessivo
- Inventário excessivo
A produção enxuta inclui trabalhar com fornecedores, subcontratados e vendedores para agilizar todo o processo.
O objetivo é que a produção flua sem problemas, evitando partidas e paradas dispendiosas.
A ideia é chamada just in time “produzir apenas o que for necessário, quando for necessário e apenas na quantidade necessária”. O processo de produção deve ser flexível e rápido.
Estoque =exatamente o que você precisa
Na produção em massa =apenas no caso. Suprimentos e produtos extras são armazenados apenas no caso de serem necessários.
Terminologia:
Simplificação do processo - um processo fora do fluxo de produção
Defeitos – o sistema de produção em massa faz inspeção no final da produção para detectar defeitos antes de serem enviados. O problema é que os recursos já foram “gastos” para fazer o resíduo. Tente prevenir os problemas imediatamente, à medida que eles acontecem, e então evite-os. Inspeção durante a produção, em cada etapa da produção.
Segurança – tempo ferido é tempo perdido
Informação – precisa da informação certa na hora certa (muita, pouca, tarde demais)
Princípios:
Poka-yoke – à prova de erros, determinando a causa dos problemas e removendo a causa para evitar mais erros
Erros de julgamento – encontrar problemas após o processo
Inspeções informativas – analisando dados de inspeções durante o processo
Inspeções de origem – inspeção antes do início do processo para evitar erros.
MEAN LEAN
Um dos termos aplicados a uma interpretação simples de corte de custos e corte de empregos do Lean é Mean Lean. Muitas vezes, o gerente moderno pensa que está fazendo o lean sem entender a importância dos trabalhadores e dos relacionamentos de longo prazo.
Manutenção centrada na confiabilidade
A manutenção centrada na confiabilidade é um sistema para projetar um programa de manutenção econômico. Pode ser um complexo detalhado, computadorizado, orientado estatisticamente, mas em seu básico é bastante simples. Suas ideias podem ser aplicadas ao projeto e operação de um sistema PM e também podem orientar seu aprendizado ao fazer manutenção, solução de problemas, reparos e trabalhos de energia.
Estes são os princípios fundamentais do RCM. Esses nove conceitos fundamentais são:
- Falhas acontecem.
- Nem todas as falhas têm a mesma probabilidade
- Nem todas as falhas têm as mesmas consequências
- Componentes simples se desgastam, sistemas complexos quebram
- Uma boa manutenção fornece a funcionalidade necessária pelo menor custo possível
- A manutenção só pode alcançar a confiabilidade inerente do projeto do equipamento
- Manutenção desnecessária retira recursos da manutenção necessária
- Bons programas de manutenção passam por melhorias contínuas.
A manutenção consiste em todas as ações tomadas para garantir que os componentes, equipamentos e sistemas forneçam suas funções pretendidas quando necessário.
Um sistema RCM é baseado em responder às seguintes perguntas:
1. Quais são as funções e padrões de desempenho desejados do equipamento?
2. De que forma pode deixar de cumprir suas funções? (Quais são as falhas mais prováveis? Qual a probabilidade de cada tipo de falha? As falhas serão óbvias? Pode ser uma falha parcial?)
3. O que causa cada falha?
4. O que acontece quando ocorre cada falha? (Qual é o risco, perigo, etc.?)
5. De que forma cada falha importa? Quais são as consequências de uma falha total ou parcial?
6. O que pode ser feito para prever ou prevenir cada falha? Quanto custará prever ou evitar cada falha?
7. O que deve ser feito se uma tarefa proativa adequada não puder ser encontrada (ações padrão) (nenhuma tarefa pode estar disponível ou pode ser muito cara para o risco)?
O equipamento é estudado no contexto de onde, quando e como está sendo usado
Todas as ações de manutenção podem ser classificadas em uma das seguintes categorias:
- Manutenção corretiva – Restaurar função perdida ou degradada
- Manutenção Preventiva – Minimiza a oportunidade de falha de função
- Manutenção Alternativa – Elimine condições insatisfatórias alterando o design ou o uso do sistema
Dentro da categoria de manutenção preventiva, todas as tarefas realizadas podem ser descritas como pertencentes a um dos cinco (5) tipos principais de tarefas:
- Direcionado à condição – Renova a vida útil com base na condição medida em comparação com um padrão
- Tempo Direcionado – Renove a vida independentemente da condição
- Localização de falhas – determine se ocorreu uma falha
- Manutenção – Adicionar/reabastecer consumíveis
- Lubrificação – Óleo, graxa ou outro tipo de lubrificação
Fazemos manutenção porque acreditamos que a confiabilidade do hardware diminui com a idade, mas podemos fazer algo para restaurar ou manter a confiabilidade original que se paga.
O RCM é centrado na confiabilidade. Seu objetivo é manter a confiabilidade inerente do projeto do sistema ou equipamento, reconhecendo que as mudanças na confiabilidade inerente podem ser alcançadas apenas por meio de mudanças no projeto. Devemos entender que o equipamento ou sistema deve ser estudado na situação em que está trabalhando.
Implementação do Lean Manufacturing
Analise cada etapa do processo original antes de fazer a mudança
O foco principal da manufatura enxuta está na redução de custos e no aumento do faturamento e na eliminação de atividades que não agregam valor ao processo de fabricação. Basicamente, o que a manufatura enxuta faz é ajudar as empresas a atingir a produção direcionada, além de outras coisas, introduzindo ferramentas e técnicas fáceis de aplicar e manter. O que essas ferramentas e técnicas estão fazendo é reduzir e eliminar o desperdício, coisas que não são necessárias no processo de fabricação.
Os engenheiros de manufatura decidiram usar a metodologia seis sigma DMAIC (Projetar, Medir, Analisar, Melhorar, Controlar) — em conjunto com a manufatura enxuta — para atender aos requisitos do cliente relacionados à produção de tubos.
Os engenheiros de fabricação foram encarregados de projetar um novo layout de processo da linha de produção de tubos. Os objetivos para o projeto incluíam:
- Qualidade melhorada
- Redução de sucata
- Entrega no ponto de uso
- Tamanhos de lote menores
- Implementação de um sistema puxado
- Melhor feedback
- Aumento da produção
- Responsabilidade individual
- Diminuição do WIP
- Flexibilidade de jantar
Antes de fazer alterações, a equipe analisa cada etapa do layout original do processo da linha de produção de tubos.
1. Tente entender o processo do estado original, identificar a área problemática, etapa desnecessária e sem valor agregado.
2. Após o mapeamento do processo, a equipe lean coletou dados da bancada do Material Review Board (MRB) para medir e analisar os principais tipos de defeitos. Para entender melhor o processo, a equipe também fez um estudo de tempo para um período de produção de 20 dias.
No estado original, a linha de tubos consistia em um operador e quatro operações, separados em duas estações por uma grande mesa usando um sistema de empurrar. A tabela atuou como um separador entre a segunda e a terceira operação.
O primeiro problema descoberto foi o desbalanceamento da linha. A primeira estação foi usada cerca de 70% do tempo. Os operadores da segunda estação passavam muito tempo esperando entre os tempos de ciclo. Ao combinar as estações um e dois, ficou evidente a possibilidade de melhorias em relação à responsabilidade individual, controle de estoque pelo operador e feedback imediato quando ocorreu um problema. O estudo de tempo e o layout do departamento refletem essas descobertas.
Um segundo problema foi reconhecido. Devido ao fluxo do processo, a taxa de produção não permitia que o cronograma de produção fosse atendido com duas estações. Como os operadores perdiam o controle dos ciclos da máquina, as máquinas esperavam pela atenção do operador. Os operadores também tentaram empurrar as peças pela primeira estação – a operação de gargalo no processo – e depois continuaram a fabricar as peças nas duas últimas operações. Normalmente, longas execuções de WIP se acumulavam e os problemas de qualidade não eram detectados até que um grande número de peças defeituosas fosse produzido.
Os dados do estado original foram obtidos nos últimos 20 dias antes da mudança. As equipes analisam cada etapa no original e fazem as alterações. As conclusões do estudo de tempo sobre o processo original forneceram a base para reduzir o tempo de ciclo, equilibrar a linha, projetar o uso de kanbans e agendamento Just In Time, melhorar a qualidade, diminuir o tamanho do lote e WIP e melhorar o fluxo. Os novos dados do processo foram obtidos a partir de um mês após a implementação. Esse atraso deu aos operadores de máquinas a oportunidade de treinar e se familiarizar com o novo sistema de layout de processo.
Com o design de célula em forma de U; As peças atendem a todos os requisitos do cliente. A tabela no processo original foi removida, quase eliminando o WIP. Com a redução do WIP e o aumento da produção.
Alguns dos conceitos usados para melhorar o processo incluíam envolvimento total do funcionário (TEI), tamanhos de lote menores, programação, estoque de ponto de uso e layout aprimorado. Todos os funcionários e supervisores do departamento estiveram envolvidos em todas as fases do projeto. Suas idéias e sugestões foram incorporadas no processo de planejamento e implementação para obter uma aceitação mais ampla das mudanças no processo. Tamanhos de lote menores foram introduzidos para minimizar o número de peças produzidas antes que os defeitos fossem detectados. Kanbans foram introduzidos (na forma de racks de manuseio de materiais) para controlar o WIP e implementar um sistema puxado. E o layout da célula diminuiu o deslocamento entre as operações.
Os operadores foram autorizados a parar a linha quando surgiram problemas. No estado original, os operadores ainda continuavam executando peças quando uma operação estava inativa. Com Kanban
controle, o layout eliminou a capacidade de armazenar WIP, exigindo que o operador desligue toda a linha. O layout da célula oferece excelentes oportunidades para melhorar a comunicação entre os operadores sobre problemas e ajustes, para obter melhor qualidade.
Na inspeção diária do processo no estado original, os operadores passavam muito tempo esperando pela pessoa de manuseio de materiais ou realizando o manuseio de materiais. Com a célula em forma de U, a entrega ao ponto de uso é melhor para o operador. O operador coloca as caixas de matéria-prima em seis carrinhos de rolos móveis, de fácil acesso. As seis caixas são suficientes para durar um período de 24 horas.
Para reduzir os tempos de configuração, as ferramentas necessárias para reparo e ajustes da máquina estão localizadas na célula. Os parafusos não são padronizados; as ferramentas são configuradas em ordem crescente de tamanho para identificar rapidamente a ferramenta adequada.
Durante três meses o processo foi monitorado para verificar se estava sob controle. A comparação dos estudos de tempo do estado original e do layout implementado demonstrou um aumento na produção de 300 para 514 produtos acabados por turno. O novo layout eliminou a dupla movimentação entre a segunda e a terceira operação, bem como na etapa de embalagem. Também reduziu ao longo do tempo, facilitando o ciclo de todas as quatro operações em uma ordem de sistema pull. A demanda dos clientes foi atendida em dois turnos, o que reduziu o custo de mão de obra.
Os resultados do redesenho são os seguintes:
- WIP diminuiu 97%
- A produção aumentou 72%
- A sucata foi reduzida em 43%
- A utilização da máquina aumentou 50%
- A utilização de mão de obra aumentou 25%
- Os custos trabalhistas foram reduzidos em 33%
- O nível Sigma aumentou de 2,6 para 2,8
Esse projeto resultou em custos reduzidos de mão de obra e refugos e permitiu que a organização fizesse um trabalho melhor de fazer entregas no prazo, ao mesmo tempo em que permitia um estoque menor de produtos acabados. Os números diários de produção e o tempo de ciclo de peça única serviram como referência para monitorar o progresso em direção à meta. Apesar do aumento do nível sigma, a redução de 43% nos defeitos, redução de 97% no WIP e aumento de produção de 72% contribuíram para o objetivo do projeto.
A implementação do lean é um processo sem fim; isso é o que a melhoria contínua é tudo
cerca de. Quando você implementa um aspecto do lean, ele sempre pode ser melhorado. Don’t get hung up on it, but don’t let things slip back to the starting point. There will always be time to go back and refine some of the processes.
Before Lean Manufacturing was implemented at Nypro Oregon Inc., we would operate using traditional manufacturing. Traditional manufacturing consists of producing all of a given product for the marketplace so as to never let the equipment idle. These goods them need to be warehoused or shipped out to a customer who may not be ready for them. If more is produced than can be sold, the products will be sold at a deep discount (often a loss) or simply scrapped. This can add up to an enormous amount waste. After implementing Lean Manufacturing concepts, our company uses just in time. Just in time refers to producing and delivering good in the amount required when the customer requires it and not before. In lean Manufacturing, the manufacture only produces what the customer wants, when they want it. This often a much more cost effective way of manufacturing when compared to high priced, high volume equipment.
Unit Test:
1. What is 5S?
2. Please Explain each “S” of the 5S.
3. Please Explain Kaizen concept.
4. What is the Pull processing?
5. What is the Poka-yoke?
6. What is the six-sigma DMAIC?
7. What is the objectives for a new process layout of the tube production line?
8. Before making changes, The Manufacturing engineers team do what first?
9. Please lists the results of the redesign.
10. The key to implementing lean new idea or concept is to do what?
CHAPTER ATTRIBUTION INFORMATION
Este capítulo foi derivado das seguintes fontes.
- Lean 5S derived from Lean Manufacturing by various authors, CC:BY-SA 3.0.
- Kaizen derived from A Kaizen Based Approach for Cellular Manufacturing System Design:A Case Study by VirginiaTech, CC:BY-SA 4.0.
- Kaizen (image) derived from A Kaizen Based Approach for Cellular Manufacturing System Design:A Case Study by VirginiaTech, CC:BY-SA 4.0.
Tecnologia industrial
- Comparando Six Sigma e manufatura enxuta
- Benefícios da automação na manufatura enxuta
- 5 Blogs de manufatura e manutenção que você deveria estar lendo
- 6 áreas de melhoria que cada consultor analisa
- 5 Ferramentas de Manufatura Enxuta necessárias [Infográfico]
- O que é Manufatura Enxuta? Como otimizar com automação flexível
- As principais ferramentas de manufatura enxuta que os fabricantes de D2C precisam
- Os 8 desperdícios do Lean Manufacturing
- Reduza o desperdício em 3 etapas simples com Lean Manufacturing
- Como retomar a manufatura enxuta