Calcinação de calcário
Calcinação de calcário
Calcinação ou calcinação é um processo de tratamento térmico para provocar uma decomposição térmica. O processo ocorre abaixo do ponto de fusão do produto. O nome calcinação é derivado da palavra latina 'Calcinare' que significa queimar cal. A cal (CaO) é um dos produtos químicos mais antigos conhecidos pelo homem e o processo de produção da cal é uma das indústrias químicas mais antigas. A cal virgem foi produzida nos EUA já em 1635 em Rhode Island. O progresso técnico que não existia nos séculos passados avançou rapidamente a indústria da cal durante os últimos cinquenta anos na área de métodos de processo e design.
O calcário é uma das matérias-primas mais básicas empregadas na indústria siderúrgica e é utilizada tanto na siderurgia, siderurgia e processos auxiliares. A maior parte da cal usada na indústria siderúrgica é para fundir impurezas no forno de fabricação de aço e em muitos dos processos secundários de fabricação de aço. A cal também é utilizada em diferentes quantidades no processo de sinterização para a preparação do minério de ferro, na dessulfuração do ferro-gusa, na neutralização ácida e nas estações de tratamento de água.
O calcário é um mineral natural. Os depósitos de calcário têm ampla distribuição. O calcário dos vários depósitos difere em propriedades físicas e químicas. A composição química também pode variar muito de região para região, bem como entre diferentes depósitos na mesma região. O calcário pode ser classificado de acordo com sua composição química, textura e formação geológica. Normalmente, o calcário contém mais de 90% de CaCO3 (carbonato de cálcio) e alguns % de MgCO3 (carbonato de magnésio). A dolomita é um carbonato duplo contendo 54% a 58% de CaCO3 e 40% a 44% de MgCO3.
O calcário é geralmente classificado em dois tipos, a saber (i) alto teor de cálcio em que o teor de carbonato é composto principalmente de CaCO3 com um teor de MgCO3 não superior a 5 % (geralmente menos), (ii) magnésio ou calcários dolomíticos que se referem a um calcário contendo MgCO3 em um nível superior ao do calcário, mas inferior à dolomita e que contém MgCO3 na faixa de cerca de 5% a 20%. O calcário geralmente está associado a impurezas como sílica (SiO2), alumina (Al2O3), ferro (Fe), enxofre (S) e outros oligoelementos.
A reatividade química de vários calcários também mostra uma grande variação devido à diferença na estrutura cristalina e à natureza das impurezas como SiO2, Al2O3, Fe etc. As propriedades variadas do calcário têm grande influência no método de processamento. Por isso, é necessário conhecer informações abrangentes do calcário, como propriedades físicas e químicas, características de queima e parâmetros cinéticos para a calcinação do calcário. Isso ajuda o projeto e a operação ideais em fornos de cal.
As reações de calcinação geralmente ocorrem na temperatura de decomposição térmica ou acima dela. Esta temperatura é geralmente definida como a temperatura na qual a energia livre de Gibbs padrão é igual a zero. A reação de decomposição do calcário é CaCO3=CaO + CO2 (g). A energia de ativação da reação de calcinação é geralmente entre 37 kcal/mol a 60 kcal/mol, com valores predominantemente próximos a 50 kcal/mol. Estes valores são comparados com o valor teórico (em equilíbrio) entre 39 kcal/mol a 41 kcal/mol. A incerteza deriva da complexidade inerente ao processo de calcinação que, assumindo um modelo de núcleo encolhido, envolve um mecanismo de sete etapas. Calor deve ser transferido (i) para a superfície externa da partícula, então (ii) conduzido através da casca externa calcinada para a interface de reação interna, onde (iii) ocorre uma reação química e o CO2 (dióxido de carbono) desenvolvido é para (iv) reagir na interface, ou (v) difundir da interface para a superfície externa e então (vi) se difundir da superfície para a atmosfera circundante, e (vii) CO2 da atmosfera circundante também se difundir para a reação interface. A taxa de calcinação é governada por qualquer uma ou qualquer combinação dessas etapas.
A calcinação é uma reação de equilíbrio. Em princípio, o CaCO3 se decompõe em cal se a pressão parcial ambiente do CO2 estiver abaixo do valor de equilíbrio da pressão parcial a uma dada temperatura. Por outro lado, qualquer cal formada é transformada novamente em carbonato se a pressão parcial de CO2 exceder este valor de equilíbrio. A velocidade da reação de decomposição é, portanto, governada pela pressão parcial de CO2, a temperatura da reação e o tamanho da partícula. A 700°C e à pressão atmosférica, a velocidade da reação torna-se extremamente lenta, mesmo na ausência de CO2. A reatividade química é conhecida por variar entre as fontes de calcário, não apenas por causa das diferenças na estrutura cristalina, mas também dependendo da natureza das impurezas.
A calcinação do CaCO3 é uma reação altamente endotérmica, exigindo cerca de 755 Mcal de entrada de calor para produzir uma tonelada de cal (CaO). A reação só começa quando a temperatura está acima da temperatura de dissociação dos carbonatos no calcário. Esta situa-se tipicamente entre 780°C e 1340°C. Uma vez iniciada a reacção, a temperatura deve ser mantida acima da temperatura de dissociação e o CO2 libertado na reacção deve ser removido. A dissociação do CaCO3 prossegue gradualmente da superfície externa da partícula para dentro, e uma camada porosa de CaO, o produto desejado, permanece. Assim, o processo depende de uma temperatura de queima adequada de pelo menos mais de 800 graus C para garantir a decomposição e um bom tempo de residência, ou seja, garantir que a cal/calcário seja mantida por um período suficientemente longo a temperaturas de 1.000 graus C a 1.200 graus C para controlar sua reatividade.
Os fatores que afetam a calcinação são a estrutura cristalina afeta a taxa de calcinação, a resistência interna do calcário e o tamanho do cristal resultante da cal após a calcinação. Os cristais menores se aglomeram durante a calcinação e formam cristais maiores que, por sua vez, causam encolhimento e redução de volume.
Calcinação em temperatura mais alta significa maior aglomeração e mais encolhimento. Também a densidade do calcário está relacionada com a estrutura cristalina. A forma dos cristais determina o espaço vazio entre os cristais e, portanto, a densidade do calcário. Vazios maiores permitem a passagem fácil de gases CO2 durante a calcinação e resulta em uma redução de volume durante a calcinação. Alguns calcários, devido à sua estrutura cristalina, desintegram-se durante o processo de calcinação. Este tipo de calcário não é útil para calcinação. Existe algum outro calcário cujo comportamento é o oposto. Este tipo de calcário torna-se tão denso durante a calcinação que impede a fuga de CO2 e torna-se não poroso. Este tipo de calcário também não é adequado para calcinação
A reatividade da cal é uma medida da taxa na qual a cal reage na presença de água. O método de teste para medir a reatividade da cal moída é realizado por amortecimento da cal em água. A reatividade da cal depende de diferentes parâmetros relacionados à matéria-prima e ao processo. Esses parâmetros são:(i) temperatura e tempo de queima, (ii) estrutura cristalina do calcário, (iii) impurezas do calcário e (iv) tipo de forno e combustível. A classificação da cal é muitas vezes vista em termos de sua reatividade, como (i) calcinada, (ii) dura, (iii) média e (iv) mole.
A cal com uma reatividade mais baixa é muitas vezes referida como média, dura e queimada. A diminuição da reatividade é acompanhada por uma redução da superfície e da porosidade da cal, o que é chamado de sinterização. Cada tipo específico de cal possui uma reatividade particular que, por sua vez, é regida pelos requisitos da aplicação e do processo específico. Como mencionado acima, as características da cal também dependem do material de alimentação do calcário, do tipo de forno e do combustível utilizado. Por exemplo, os fornos de coque geralmente produzem cal com reatividade média a baixa, enquanto os fornos regenerativos de fluxo paralelo a gás geralmente produzem uma cal de alta reatividade. A química e a reatividade da cal são os principais parâmetros que orientam seu uso.
A decomposição de dolomita e calcário dolomítico é muito mais complexa. A decomposição pode ocorrer por meio de um único ou dois estágios discretos ou mesmo por meio de estágios intermediários. As reações envolvidas nessas etapas são CaCO3.MgCO3 + calor =CaCO3.MgO + CO2, CaCO3.MgO + calor =CaO.MgO + CO2 e CaCO3.MgCO3 + calor =CaO.MgO + 2CO2. A temperatura necessária para a decomposição de dolomita e calcário dolomítico é geralmente na faixa de 500 graus C a 750 graus C.
O calcário de menor tamanho é mais adequado para calcinação em fornos rotativos e permite um ótimo tempo de residência. A temperatura de calcinação mais baixa também permite menor consumo de combustível. Em contraste, calcário de tamanho maior e baixa temperatura de calcinação são necessários para fornos verticais. Se o aumento da temperatura for muito rápido, a camada externa das peças de calcário é calcinada muito rapidamente. À medida que a temperatura aumenta, a superfície do calcário encolhe e fecha os poros criados pelo escape de CO2. Isso causa aumento da pressão interna dentro do calcário. Como o gás CO2 não pode escapar, o calcário explode e se desintegra produzindo “finos” indesejados, reduzindo assim a qualidade da cal.
A produção de cal de boa qualidade depende do tipo de forno, das condições de calcinação e da natureza da matéria-prima, ou seja, o calcário. Em temperaturas de calcinação relativamente baixas, os produtos formados no forno contêm carbonato e cal não queimados e são chamados de cal “subqueimada”. À medida que a temperatura aumenta, é produzida uma “cal queimada suave” ou “cal altamente reativa”. Em temperaturas ainda mais altas, é produzida “cal queimada” ou “cal de baixa reatividade”. A cal queimada macia é produzida quando a frente de reação atinge o núcleo do calcário carregado e converte todo o carbonato presente em cal. Um produto de alta produtividade é relativamente macio, contém pequenos cristalitos de cal e possui estrutura porosa aberta com um interior facilmente avaliável. Tal cal tem as propriedades ótimas de alta reatividade, alta área superficial e baixa densidade aparente. Aumentar o grau de calcinação além deste estágio faz com que os cristalitos de cal formados cresçam maiores, se aglomerem e sinterizem. Isso resulta em uma diminuição na área de superfície, porosidade e reatividade e um aumento na densidade aparente. Este produto é conhecido como cal queimada ou cal de baixa reatividade.
Calcinação de calcário no forno
A passagem de calcário (com ou sem um teor significativo de MgCO3) através do forno pode ser dividida em três estágios ou zonas de transferência de calor (Fig 1) consistindo em (i) zona de pré-aquecimento, (ii) zona de calcinação e (iii) zona de resfriamento .
Zona de pré-aquecimento -O calcário é aquecido desde a temperatura ambiente até cerca de 800°C por contacto directo com os gases que saem da zona de calcinação composta principalmente por produtos de combustão juntamente com excesso de ar e CO2 das calcinações.
Zona de calcinação – O combustível é queimado em ar pré-aquecido da zona de resfriamento e (dependendo do projeto) em ar de “combustão” adicional adicionado ao combustível. Nesta zona, são produzidas temperaturas superiores a 900 graus C. De 800 graus C a 900 graus C, a superfície do calcário começa a se decompor. Em temperaturas acima da temperatura de decomposição do calcário, ou seja, 900 graus C, a decomposição ocorre abaixo da superfície dos pedaços de calcário. A uma temperatura de 900 graus C, estas peças saem da zona de calcinação e encontram-se por vezes como calcário residual que ainda está retido no seu interior. Se as peças que estão totalmente decompostas e ainda residem na zona de calcinação, ocorre a sinterização.
Zona de resfriamento – A cal que sai da zona de calcinação a temperaturas de 900°C, é arrefecida por contacto direto com o ar de 'arrefecimento', parte ou todo o ar de combustão, que por sua vez é pré-aquecido. A cal sai desta zona a temperaturas inferiores a 100 graus C.
O tempo de residência do calcário-cal em um forno varia dependendo do tipo de forno e do tipo de produto final necessário. Este período é encontrado entre seis horas e dois dias. A cal é muitas vezes referida como leve ou macia, média ou duramente queimada, dependendo da extensão em que foi calcinada. O grau de reatividade, isto é, reatividade à água, diminui à medida que o nível de porosidade aumenta.
Fig 1 Estágios de zonas de transferência de calor e forno rotativo longo
A taxa de decomposição do calcário no forno é, portanto, encontrada como dependente de vários fatores inerentes às próprias partículas de calcário, ou seja, morfologia e composição, e das condições do processo. As principais variáveis encontradas são (i) as características químicas do calcário, (ii) o tamanho e forma das partículas, (iii) o perfil de temperatura da zona de calcinação e (iv) a taxa de troca de calor entre gases e partículas.
A maioria dos fornos usados são baseados no projeto de eixo ou rotativo. Existem alguns outros fornos baseados em princípios diferentes. Todos esses projetos incorporam o conceito das três zonas. Enquanto os fornos de cuba geralmente incorporam uma zona de pré-aquecimento, alguns outros fornos de cal, nomeadamente fornos rotativos, funcionam por vezes em ligação com pré-aquecedores separados. A maioria dos sistemas de fornos são caracterizados pelo fluxo em contracorrente de sólidos e gases, o que tem implicações nas emissões de poluentes resultantes.
A cal run-of-kiln (ROK) é processada peneirando a fração negativa da cal. A fração positiva da cal é usada para fabricação de aço, enquanto a fração negativa é usada na sinterização de minério de ferro, estações de tratamento de água e muitos outros pequenos usos na usina siderúrgica.
Tipos de fornos de cal – técnicas e design
Fornos de calcinação são basicamente vem em duas categorias. São eles i) fornos rotativos e ii) fornos verticais. Ambos os tipos de fornos podem ser projetados com qualquer um dos combustíveis sólidos, líquidos ou gasosos. Os fornos rotativos podem ser fornos longos com resfriadores rotativos retos, enquanto os fornos verticais podem ser de vários tipos. Os fornos de calcinação precisam de calcário com índice de decrepitação adequado. O índice de decrepitação do calcário é uma medida de sua suscetibilidade à desintegração durante a calcinação. Baixo valor de decrepitação diminui a porosidade do leito impedindo assim o escoamento dos gases a eficiência do forno. Os fornos rotativos também precisam de calcário com bom índice de tombamento.
Um grande número de técnicas e projetos de fornos têm sido usados, embora atualmente os fornos de cal sejam dominados por um número relativamente pequeno de projetos, muitas alternativas estão disponíveis, que são particularmente adequadas para aplicações específicas. As propriedades do calcário, como resistência antes e depois da queima, tipo de combustível disponível e qualidade do produto, devem ser consideradas ao escolher uma técnica de forno. Existem em geral seis tipos gerais de fornos usados para a calcinação de calcário. Os principais fatores importantes para a seleção de um forno incluem (i) natureza do depósito de calcário, (ii) características, disponibilidade e qualidade do calcário, (iii) granulometria de entrada que consiste em propriedades mecânicas da alimentação do forno e finos na alimentação, (iv) exigência das propriedades da cal para seu uso principal, (v) capacidade do forno, (vi) tipo de combustível disponível, (vii) impacto ambiental e (viii) capital e custo operacional. As propriedades físico-químicas da cal estão inerentemente ligadas ao tipo de fornos utilizados para a calcinação. A guia 1 fornece diferentes tipos de fornos.
Tab 1 Tipos de fornos de cal | |||
Sl. No. | Tipo de forno | Intervalo de capacidade em toneladas/dia | Intervalo de tamanho de alimentação do forno em mm |
1 | Forno rotativo longo | 160-1.500 | 2-60 |
2 | Forno rotativo com pré-aquecedor | 150 -1.500 | 10-60 |
3 | Forno regenerativo de fluxo paralelo | 100-600 | 10-200 |
4 | Forno de eixo anular | 80-300 | 10-150 |
5 | Forno de eixo de alimentação mista | 60-200 | 20-200 |
6 | Outros fornos | 10-200 | 20-250 |
Fornos rotativos
Existem dois tipos de fornos rotativos que são normalmente utilizados para a produção de cal:(i) forno rotativo longo (LRK) e (ii) forno rotativo com pré-aquecedor (PRK).
Fornos rotativos longos (LRK) – O LRK (Fig. 1) consiste em um cilindro giratório de até 150 metros (m) de comprimento e inclinado em um ângulo de 1 grau a 4 graus com a horizontal com diâmetro em torno de 2 ma 4,5 m. O calcário é alimentado na extremidade superior e o combustível e o ar de combustão são disparados da extremidade inferior. A cal é descarregada do forno para um resfriador de cal, onde é usada para pré-aquecer o ar de combustão. Diferentes designs de resfriadores de cal são usados, incluindo unidades planetárias montadas ao redor da carcaça do forno, grelhas móveis e vários tipos de resfriadores de eixo de contrafluxo.
No LRK, não há pré-aquecedor e os queimadores de combustível estão na extremidade de descarga de cal. O tipo de combustível pode ser gás, líquido, combustíveis fósseis sólidos pulverizados, combustíveis residuais ou biomassa. A necessidade de calor é de 1.430 Mcal/t de cal a 2.200 Mcal/t de cal. A necessidade de eletricidade é de 18 kWh/t de cal a 25 kWh/t de cal. A estrutura do forno é cilindro giratório inclinado com revestimento refratário e ‘misturadores’ para melhorar a troca de calor. Os tipos de resfriador podem ser (i) planetário ao redor da carcaça do forno, (ii) grelha móvel, (iii) cilindro giratório ou (iv) resfriador de eixo estático. A injeção do ar de combustão é feita através de ar de resfriamento na extremidade do resfriador e ar primário com o combustível. A extração do gás de combustão é feita por um ventilador de tiragem induzida (ID) na extremidade do cilindro rotativo no lado de alimentação do calcário através de um duto. O gás é resfriado e despoeirado antes da descarga. O desenho de cal está na extremidade do refrigerador. Pontos importantes são a qualidade do refratário e a moagem fina do carvão para garantir uma boa combustão e redução do acúmulo (formação de anéis) no forno.
A medição contínua de CO e O2 é necessária para uma boa combustão e segurança. A LRK tem flexibilidade de produção. Há uma reação muito rápida para modificação de parâmetros. Ampla gama de tamanhos de calcário de alimentação pode ser usada. O CO2 residual muito baixo é alcançável. Há flexibilidade de reatividade de suave a duramente queimado. Existe a possibilidade de produzir dolomita queimada morta. Existe flexibilidade no que diz respeito ao uso de combustível. O calcário macio pode ser usado, mas gera muitos finos durante a calcinação. As desvantagens do LRK incluem altos requisitos de energia e formação de anéis (cinzas de carvão, sulfatos de cálcio e argila etc.)
O projeto de um queimador é importante para a operação eficiente e confiável do forno LRK. A chama deve ser ajustável para diferentes tipos de combustíveis. Devido ao fato de que as condições do processo podem ser alteradas de maneira fácil e rápida, os LRKs podem produzir uma faixa mais ampla de reatividade da cal e níveis residuais de CO2 mais baixos do que os fornos de eixo. Os calcários de alimentação relativamente fracos que se quebram e são inadequados como alimentação para fornos de eixo são adequados para fornos rotativos.
Os fornos rotativos podem ser acionados com uma ampla variedade de combustíveis. Como a transferência de calor na zona de calcinação é amplamente influenciada pela radiação e, à medida que as emissividades do infravermelho aumentam na sequência gás, óleo e combustíveis sólidos, a escolha do combustível pode ter um efeito significativo no uso de calor. As perdas por radiação e convecção são altamente em relação a outros projetos de fornos de cal que resultam em um consumo de energia geralmente maior em comparação com outros tipos de fornos.
Uma vantagem do forno rotativo é que o enxofre (S) do combustível e, em menor grau, do calcário, pode ser expelido do forno nos gases do forno por uma combinação de controle da temperatura e da porcentagem de CO na calcinação. zona. Assim, a cal com baixo teor de S pode ser produzida usando combustíveis com alto teor de S, sujeitos aos limites de emissão de SO2 nos gases de escape. Os LRKs são fornos flexíveis quanto ao uso de combustíveis e diferentes tamanhos de alimentação de calcário, principalmente as frações mais finas.
Fornos rotativos com pré-aquecedores (PRK) – Os fornos rotativos podem ser equipados com pré-aquecedores. PRKs (Fig. 2) são geralmente consideravelmente mais curtos do que os LRKs convencionais (por exemplo, 40 m a 90 m). O uso de calor diminui devido à redução das perdas por radiação e convecção, bem como ao aumento da recuperação de calor dos gases de escape.
Vários projetos de pré-aquecedores foram desenvolvidos, incluindo eixos verticais e grelhas móveis. O pré-aquecedor deve ser selecionado com base no tamanho e nas propriedades do calcário de alimentação. A maioria pode aceitar um tamanho inferior de 10 mm, enquanto alguns usaram calcários até 6 mm, e alguns não podem tolerar calcários fracos ou calcários propensos a quebrar.
Embora a eliminação de S seja mais difícil com PRKs, existem várias maneiras pelas quais ela pode ser alcançada, como (i) operar o forno em condições redutoras e introduzir ar adicional na extremidade traseira (só funciona com certos projetos de o pré-aquecedor), e no queimador, ar de combustão, pré-aquecedor, forno e resfriador, e (ii) adicionar calcário finamente dividido suficiente à alimentação para que ele absorva preferencialmente SO2 e para que possa ser coletado em o coletor de pó traseiro, ou é peneirado para fora da cal descarregada do resfriador.
No PRK, os queimadores de combustível estão na extremidade de descarga de cal. O tipo de combustível pode ser gás, líquido, combustíveis fósseis sólidos pulverizados, combustíveis residuais ou biomassa. A necessidade de calor é de 1.220 Mcal/t cal a 1.860 Mcal/t cal. A necessidade de eletricidade é de 17 kWh/t de cal a 45 kWh/t de cal. A estrutura do forno é cilindro giratório inclinado com revestimento refratário e ‘misturadores’ para melhorar a troca de calor. Os PRKs têm diâmetro de 2 m a 4,5 m e comprimento máximo de 90 m. Os tipos de resfriador podem ser (i) planetários ao redor da carcaça do forno, (ii) grelha móvel ou (iii) cilindro giratório. A injeção do ar de combustão é feita através do ar de resfriamento na extremidade do resfriador. O gás de combustão é passado através do pré-aquecedor e a extração é feita por um ventilador ID. O gás é resfriado quando troca calor com a alimentação de calcário. O desenho de cal está na extremidade do refrigerador. Pontos importantes são a qualidade do refratário, moagem fina do carvão para garantir uma boa combustão e redução do acúmulo no forno, e estanqueidade ao ar da junção entre pré-aquecedor e forno. Um alto teor de finos na alimentação de calcário pode bloquear o pré-aquecedor. A medição contínua de CO e O2 é necessária para uma boa combustão e segurança.
PRKs têm flexibilidade de produção. Há uma reação muito rápida para modificação de parâmetros. Eles podem usar uma ampla gama de tamanhos de calcário de alimentação. O CO2 residual muito baixo é alcançável. Há flexibilidade de reatividade de macio a duro queimado, com possibilidade de produzir dolomita queimado morto. Há flexibilidade de combustível, uma vez que os PRKs podem usar combustíveis fósseis gasosos, líquidos ou sólidos pulverizados, bem como combustíveis residuais e biomassa. Alimentos de calcário macio podem ser usados, mas produzem muitos finos durante a calcinação. A menor necessidade de combustível nos PRKs se deve à melhor troca de calor no pré-aquecedor (início da descarbonização). As desvantagens incluem a formação de anéis (cinzas de carvão, sulfatos de cálcio, argila), e o pré-aquecedor é um equipamento adicional de manutenção.
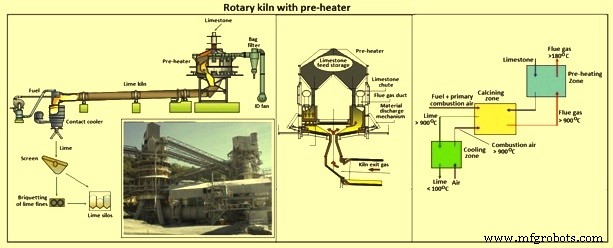
Fig 2 Forno rotativo com pré-aquecedor
Fornos de eixo
Os fornos de eixo constituem a maioria de todos os fornos atualmente usados para a produção de cal. Os tipos de fornos de eixo são (i) forno de eixo de alimentação mista (MFSK), (ii) forno regenerativo de fluxo paralelo (PFRK), (iii) forno de eixo anular (ASK) e (iv) outros fornos. Os fornos de eixo são verticais em design, até 30 m (metros) de altura e com um diâmetro de até 6 m. Para este tipo de forno, o calcário é alimentado na parte superior do forno que progressivamente desce pelas diferentes etapas do forno até ser descarregado na parte inferior como cal. O desempenho dos fornos de eixo tradicionais tem sido limitado pela dificuldade em obter uma distribuição uniforme de calor sobre a seção transversal do forno e movimento uniforme do material através do forno.
Forno de eixo de alimentação mista (MFSK) – MFSK (Fig 3) usa calcário com um tamanho de topo na faixa de 20 mm a 200 mm e uma proporção de tamanho de cerca de 2:1. O combustível mais utilizado é um coque denso com baixo teor de cinzas. O tamanho do coque é apenas ligeiramente menor que o do calcário. Assim, ele desce com o calcário em vez de escorrer pelos interstícios. O calcário e o coque são misturados e carregados no forno de forma a minimizar a segregação. O antracito é cada vez mais utilizado nos dias de hoje devido ao preço e menor disponibilidade de coque metalúrgico.
No MFSK, a alimentação de combustível é misturada com calcário. A necessidade de calor é de 810 Mcal/t de cal a 1.120 Mcal/t de cal. A necessidade de eletricidade é de 5 kWh/t de cal para 15 kWh/t de cal. A estrutura do forno é cilíndrica vertical ou eixo retangular com revestimento refratário. O ar de combustão consiste em ar de refrigeração injetado pela parte inferior. O desenho de cal é por placa excêntrica rotativa. O ponto importante é que requer uma mistura uniforme de pedra e combustível e requer uma distribuição uniforme de calcário sobre a seção transversal. Há alta retenção de S do combustível na cal.
A cal produzida no forno tem baixa reatividade. O ar de resfriamento é usado como ar de combustão. O forno funciona com baixo excesso de ar. A mistura uniforme ar/combustível é difícil de conseguir no forno, produzindo variações na relação ar/combustível. As condições do processo levam a emissões de CO. O forno precisa de grande tamanho de alimentação do calcário. Há baixa reação para modificar os parâmetros (24 horas), portanto, grande inércia.
Fig 3 Forno de eixo de alimentação mista
Forno regenerativo de fluxo paralelo (PFRK) – A principal característica do PFRK padrão (Fig 4) é que ele possui dois eixos circulares conectados por um canal cruzado, embora alguns projetos iniciais tivessem três eixos enquanto outros tinham eixos retangulares. O método de operação do PFRK incorpora os dois princípios-chave a seguir.
- A zona de pré-aquecimento em cada eixo atua como um trocador de calor regenerativo, além de pré-aquecer o calcário até a temperatura de calcinação. O calor excedente dos gases é transferido para o calcário do outro poço durante a primeira etapa do processo. Em seguida, é recuperado do calcário pelo ar de combustão, que é pré-aquecido a cerca de 800 graus C. Como resultado, o forno tem um consumo de calor específico muito baixo.
- A calcinação do calcário ocorre a uma temperatura relativamente moderada, normalmente em torno de 900 graus C a 1100 graus C. Isso torna os fornos ideais para produzir cal de reatividade moderada e alta com baixo nível residual de CO2.
Na prática, os lotes de calcário são carregados alternadamente em cada poço e passados para baixo através da zona de pré-aquecimento, ao redor das lanças de combustível e depois para a zona de calcinação. Da zona de calcinação, passam finalmente para a zona de resfriamento. A operação do forno consiste em dois períodos iguais, que duram de 8 minutos a 15 minutos em plena potência. Durante o primeiro período, o combustível é injetado através das lanças no primeiro poço e queima com o ar de combustão soprado neste poço. O calor emitido é parcialmente absorvido pela calcinação do calcário neste primeiro poço. O ar de resfriamento é soprado na base de cada eixo para resfriar a cal. O ar de resfriamento no poço número um, juntamente com os gases de combustão e o CO2 da calcinação, passam pelo duto cruzado de interligação no poço número dois a uma temperatura de cerca de 1050 graus C. No poço número dois, os gases provenientes do poço eixo número um são misturados com o ar de resfriamento soprado na base do eixo número dois e fluem para cima. Assim, eles aquecem o calcário na zona de pré-aquecimento do eixo número dois.
Se o modo de operação acima continuar, a temperatura dos gases de escape aumenta para bem acima de 500 graus C. No entanto, após um período de 8 minutos a 15 minutos, os fluxos de combustível e ar no primeiro eixo são interrompidos e uma 'reversão' ocorre. Depois de carregar o calcário no eixo número um, combustível e ar são injetados no eixo número dois e os gases de escape são expelidos do topo do eixo número um.
O forno pode ser aceso com gás, combustíveis líquidos ou sólidos pulverizados, bem como combustíveis residuais ou biomassa. O forno também tem uma alta taxa de redução, embora em taxas de produção mais baixas possa haver alguma perda de eficiência energética. Uma vez que um forno tenha sido aceso, é indesejável desligá-lo, pois isso pode resultar em uma vida útil mais curta do refratário. A vida útil de campanha do refratário no canal de queima e cruzamento é em torno de 4 anos a 8 anos. O PFRK padrão precisa de calcário limpo, idealmente com uma proporção de calcário não superior a 2:1. O tamanho mínimo do calcário é de 30 mm, embora um projeto modificado chamado forno de cal fina PFRK possa operar em tamanhos tão pequenos quanto 10 mm a 30 mm em calcário limpo.
No PFRK a alimentação do combustível é feita através de lanças no leito de calcário. A necessidade de calor é de 765 Mcal/t de cal a 1.000 Mcal/t de cal. A necessidade de eletricidade é de 20 kWh/t de cal a 41 kWh/t de cal. A estrutura do forno é de dois ou três cilindros verticais ou eixos retangulares com revestimento refratário ligados por um canal para circulação de gases quentes. A injeção de ar de combustão está no topo (principal) e lanças (10%). O desenho de cal é por placa excêntrica rotativa. O ponto importante é a qualidade dos trabalhos refratários. A PFRK tem a flexibilidade de produção. A reatividade da cal produzida é alta com razoável flexibilidade de reatividade de alta a média, quando o calcário permite. O consumo de combustível e energia é baixo. O PFRK tem flexibilidade limitada de parada/partida. Não é adequado para calcário com alta decrepitação. O revestimento refratário é mais caro do que para outros tipos de fornos.
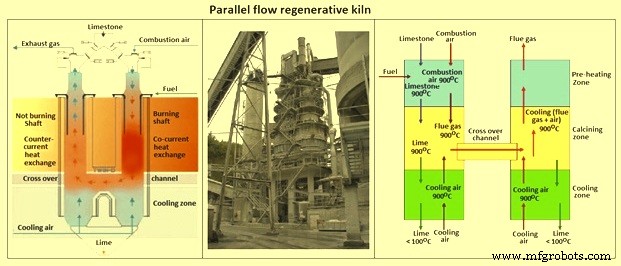
Fig 4 Forno regenerativo de fluxo paralelo
Fornos de eixo anular (ASK) – A principal característica dos ASKs (Fig. 5) é um cilindro central que restringe a largura do anel e, juntamente com arcos para distribuição de gás de combustão, garante uma boa distribuição de calor. A coluna central também permite que parte dos gases de combustão dos queimadores inferiores seja puxada para baixo no poço e injetada de volta na câmara inferior.
This recycling moderates the temperature at the lower burners and ensures that the final stages of calcination occur at a low temperature. Both effects help to ensure a product with a low residual CO2 level and a high reactivity. The ASK can be fired with gas, oil or solid fuel. The exhaust gases have a high CO2 concentration.
In ASK, the fuel feed is both at the upper and lower part of the burning chamber sometimes mixed with limestone. Central cylinder restricts the width of the annulus. Heat requirement is from 790 Mcal/t of lime to 1,170 Mcal/t of lime. Electricity requirement is 18 kWh/t of lime to 35 kWh/t of lime (upto 50 kWh/t for feed sizes of below 40 mm). The structure of the kiln is vertical cylinder shaft with refractory lining. ASK has external chambers and burners. Type of fuel which is used can be gas, liquid, pulverized solid fuels, waste fuels, or biomass. The combustion air injection is at the top of the calcining chamber. Drawing of lime is by rotating eccentric plate. The important point is that it requires very accurate process control.
The lime produced from the kiln has low residual CO2 and high to medium reactivity. Fuel saving is through heat recovery. The kiln has good heat distribution. ASK has maintenance of heat recuperator and outer chambers. It has relatively high construction cost due to its conception.
Fig 5 Annular shaft kiln
Other types shaft kilns
This group of kilns includes a number of designs. In these designs, fuel is introduced through the walls of the kiln, and is burned in the calcining zone, with the combustion products moving upwards counter-current to the lime and limestone. In some designs, the fuel is partially combusted in external gasifiers. In others, it is introduced through devices such as a central burner, beam burner or injected below internal arches. Some of these kilns are described below.
Double inclined shaft kilns – This type of kiln (Fig 6) can produce a reactive low carbonate product. It is essentially rectangular in cross-section but incorporates two inclined sections in the calcining zone. Opposite each inclined section, offset arches create spaces into which fuel and preheated combustion air are fired through the combustion chambers. Cooling air is drawn into the base of the kiln where it is preheated, withdrawn and re-injected through the combustion chambers. The circuitous paths for both the gases and the burden, coupled with firing from both sides, ensure an efficient distribution of heat. A range of solid, liquid and gaseous fuels can be used, although they are to be selected with care to avoid excessive build-ups caused by fuel ash and calcium sulphate deposits.
Fig 6 Double inclined shaft kiln and gas suspension calcination kiln
Gas suspension calcination (GSC) kilns – Gas suspension calcination (GSC) kilns are a technique for minerals processing, such as the calcination of limestone, dolomite and magnesite from pulverized raw materials to produce highly reactive and uniform products. Most of the processes in the GSC kiln plant, such as drying, preheating, calcination and cooling, are performed in gas suspension. Hence, the plant consists of stationary equipment and a few moving components (Fig 6). The amount of material present in the system is negligible, which means that after a few minutes of operation, the product conforms to specifications. There is no loss of material or quality during start-up and shut-down so there is no sub-grade product. The GSC process produces a product with high reactivity, even when calcined to a high degree. The material to be processed in the gas suspension is required to have a suitable fineness. The practical experience has shown that 2 mm particle size is not to be exceeded. Some performance figures for the balanced operation of GSC kiln plant are fuel consumption of around 1,150 Mcal/ton of product and power consumption of 33 kWh/ton of product.
Multi-chamber shaft kilns – This is another type of double inclined kiln. It consists of four or six alternately inclined sections in the calcining zone, and opposite of each is an offset arch. The arches serve the same purpose as in the double-inclined kiln. Cooling air is preheated by lime in the cooling zone and is withdrawn, de-dusted and re-injected through the combustion chambers. A feature of the kiln is that the temperature of the lower combustion chambers can be varied to control the reactivity of the lime over a wide range. The kiln can be fired with solid, liquid and gaseous fuels or a mixture of different types of fuels.
Travelling grate kilns – For limestone feed with a size range of 15 mm to 45 mm, an option is the ‘travelling grate’ or CID kiln. It consists of a rectangular shaft preheating zone, which feeds the limestone into a calcining zone. In the calcining zone, the limestone slowly cascades over five oscillating plates, opposite of which are a series of burners. The lime passes to a rectangular cooling zone. The kiln can burn gaseous, liquid or pulverized fuels and is reported to produce a soft burned lime with a residual CaCO3 content of less than 2.3 %.
Top-shaped kilns – The ‘top-shaped’ lime kiln is a relatively new development, which accepts feed limestone in the range of 10 mm to 25 mm. This consists of an annular preheating zone from which the limestone is displaced by pushing rods into a cylindrical calcining zone. Combustion gases from a central, downward facing burner, fired with oil and positioned in the centre of the preheating zone are drawn down into the calcining zone by an ejector. The lime then passes down into a conical cooling zone. The kiln is reported to produce high quality lime, suitable for steelmaking. The kiln capacities are upto 100 tons/day of lime. It is reported that, because of its relatively low height, the kiln can accept limestone with low strengths.
Rotating hearth kilns – This type of kiln, now almost obsolete, was designed to produce small sized lime. It consists of an annular travelling hearth carrying the limestone charge. The limestone is calcined by multiple burners as it rotates on the annular hearth. The combustion air is preheated by surplus heat in the exhaust gases and/or by using it to cool the lime. Due to the reduced abrasion compared to rotary and shaft kilns, rotating hearth kilns produce a high proportion of small sized lime.
Storage and handling
Storage of lime – Lime is preferably stored in dry conditions and free from drafts to limit air slaking. High care is to be exercised to ensure that water is excluded from the lime, as hydration liberates heat and causes expansion, both of which can be dangerous.
Air pressure discharge vehicles are able to blow directly into the storage bunker, which is fitted with a filter to remove dust from the conveying air. The filter is to be weather-proof and water-tight. The collected dust can be discharged back into the bunker. A pressure/vacuum relief device fitted to the bunker is a precautionary measure to enable maintenance work to be done on the discharge mechanism. Where the amount of lime is insufficient to justify storage bunkers the product can be stored on a concrete base, preferably in a separate bay within a building to prevent excessive air slaking.
Many types of equipment are suitable for transferring the lime and new ones are continually being developed. The following techniques have been used successfully, but may not be suitable for all applications.
Skip hoists can be used for all granular and lump grades but are more suitable for particles greater than 100 mm. Elevators (both belt-and-bucket and chain-and-bucket elevators) have been used for all grades of lime. Drag-link conveyors are suitable for granular and fine lime. They are generally used for horizontal or inclined transfer. Conveyor belts are widely used for transferring lump and granular grades horizontally and on an upward slope. Screw conveyors are widely used for fine lime. Vibrating trough conveyors have been used for particle sizes upto 40 mm. They operate more successfully when there is a slight downward slope from the feed to the discharge point. Pneumatic conveying can be used for products with a maximum size of upto 20 mm and often has a lower capital cost than alternatives, but the operating costs are higher. The product is fed into a rotary blowing seal connected to a blower. The pipeline bore, and volume/pressure of the blowing air, is designed taking into account the size of lime being conveyed, the transfer rate and the length/route of the pipeline. The receiving silo is equipped with an air filter and a pressure relief valve.
Processo de manufatura
- O que é VMC Machining?
- Guia para marcação a laser em alumínio
- Soldagem MIG vs. Soldagem TIG
- Guia para marcação a laser
- Considerações para usinagem suíça de alta produção
- Guia de Prototipagem CNC
- Compreendendo o Processo de Fabricação do Eixo
- Eletropolimento vs. Passivação
- O que é passivação de aço inoxidável?
- O cuidado com o equipamento na mineração de calcário é um verdadeiro desafio