Uso de Ferro Reduzido Direto em Forno a Arco Elétrico
Uso de ferro reduzido direto em forno elétrico a arco
A fabricação de aço pelo forno elétrico a arco (EAF) tem uma flexibilidade muito boa com relação à seleção de materiais de carga. O material de carga tradicional para o processo EAF tem sido 100 por cento de sucata fria, mas como os problemas relacionados à sucata, como sua disponibilidade e qualidade, flutuações de preço de mercado e restrições impostas pela sucata na fabricação de alguns tipos de aço devido a elementos residuais e nível de nitrogênio, etc. aumentou, os operadores de EAF intensificaram a busca por materiais alternativos de carga contendo ferro.
O ferro reduzido direto (DRI) como ferro gusa e metal quente é um dos materiais alternativos de carga de ferro que tem sido usado em porcentagem variável no processo de fabricação de aço EAF. O uso de DRI pode ter efeitos distintos no processo de fusão. O consumo de energia, produtividade e rendimento são afetados pela química DRI, porcentagem de DRI usada na mistura de sucata e práticas operacionais. O DRI é utilizado como substituto de sucata no processo de fabricação de aço EAF. A Fig. 1 mostra um perfil de fusão típico com DRI na mistura de carga em um EAF de 150 toneladas.
Fig 1 Perfil de fusão típico com DRI na mistura de carga em um EAF de 150 toneladas
As vantagens normais associadas ao uso de DRI no processo de fabricação de aço EAF são (i) tamanho e dimensão constantes, (ii) composição conhecida, (iii) quase ausência de elementos tramp, (iv) pureza ou ausência de elementos não metálicos substâncias que levam a uma melhor produtividade e consumo de energia, (v) facilidade de uso no EAF, pois o DRI pode ser carregado em um EAF junto com a sucata, usando baldes ou pela alimentação contínua, (vi) melhor disponibilidade em relação ao baixo resíduo sucata, (vii) disponibilidade do teor de carbono associado que produz energia durante o processo de fabricação do aço, (vii) fácil geração de escória espumosa, (vii) carregamento direto no caso de uso de DRI quente com DRI quente reduzindo o consumo de energia em tanto como 16 % a 20 % fazendo uso do valor energético do DRI em temperaturas superiores a 600 graus C, (viii) fácil manuseio e armazenamento com possibilidade de alimentação sem abrir o teto do forno por sistema de alimentação contínua resultando em banho de aço estável superfície que h reduz o risco de quebra de eletrodos, (ix) possibilidade de mistura de DRI com sucata, o que significa que podem ser usados tipos de sucata mais baratos, e (x) mais ecológico, pois evita problemas de contaminantes perigosos, como chumbo (Pb) ou cádmio (Cd) em poeiras de EAF, e reduz a possível formação de dioxinas e furanos.
Historicamente, o uso de DRI em EAF era limitado à produção de aços de baixa qualidade e baixo resíduo com as despesas mais altas previstas devido à energia específica (kWh/ton), tempo de derivação, consumo de fluxo, aumento de FeO na escória, perda de rendimento , e maior desgaste refratário e eletrodo. Este tem sido o caso desde que o DRI foi usado sem identificar e compreender as propriedades inerentes e únicas e modificar as práticas de acordo.
As operações da EAF melhoraram consideravelmente desde o final da década de 1970 – início da década de 1080. A siderurgia em EAFs tem se beneficiado significativamente com a otimização das práticas, aumentando ainda mais o uso de energia química, e com o uso do DRI de forma adequada. As práticas desenvolvidas em relação ao uso de DRI demonstraram que o uso de DRI pode melhorar o consumo de energia, rendimentos, produtividade e principalmente os custos operacionais. Mais DRI com maior teor de carbono permite que a siderurgia EAF obtenha benefícios financeiros e técnicos substanciais. O uso de DRI a quente de alto carbono pode resultar em recursos operacionais aprimorados, juntamente com a produtividade econômica.
Os principais parâmetros que afetam a operação do EAF são a composição das matérias-primas (% ganga / química, metalização, % carbono, % fósforo e teor de energia), práticas operacionais (perfis de energia, escória espumosa e práticas de fusão) e projeto do forno ( calcanhar, uso de oxigênio e ferramentas, AC/DC etc.). Os não metálicos que vêm com DRI (geralmente no caso de DRI produzidos por forno rotativo) também têm efeito adverso na fabricação de aço EAF. Sem atenção a esses fatores, o uso de DRI na siderurgia do EAF pode ter impacto adverso nos parâmetros operacionais do EAF.
DRI é o produto que é produzido pela redução direta de minério de ferro ou outros materiais ferrosos no estado sólido usando carvão não coqueificável ou gás natural. Os processos que produzem DRI por redução do minério de ferro abaixo do ponto de fusão do ferro são normalmente conhecidos como processos de redução direta. Os agentes redutores são monóxido de carbono (CO) e hidrogênio (H2), provenientes de gás natural reformado, gás de síntese ou carvão. O minério de ferro é usado principalmente na forma de pelotas e/ou grumos. O oxigênio (O2) é removido do minério de ferro por reações químicas baseadas em H2 e CO para a produção de DRI altamente metalizado.
No processo de redução direta, o ferro metálico sólido (Fe) é obtido diretamente do minério de ferro sólido sem submeter o minério ou o metal à fusão. A redução direta pode ser definida como a redução no estado sólido em potenciais de O2 que permitem a redução de óxidos de ferro, mas não de outros óxidos (Al2O3, MnO e SiO2 etc.), aos elementos correspondentes. Como a redução está no estado sólido, há muito pouca chance de esses elementos se dissolverem (em baixa atividade termodinâmica) no ferro reduzido, de modo que os óxidos que são mais estáveis que o ferro permanecem essencialmente não reduzidos. DRI tem uma estrutura porosa.
DRI é produzido em muitas formas. Estes são granulados, pellets, ferro briquetado a quente (HBI), finos e ferro briquetado a frio (CBI). HBI e CBI são formas densificadas de DRI. Quando o DRI é descarregado do forno em condição fria (temperatura em torno de 50 graus C), então o produto é conhecido como DRI frio (CDRI) e quando o DRI é descarregado em condição quente (temperatura em torno de 650 graus C) para uso em condição quente na siderurgia então o produto é conhecido como DRI quente (HDRI).
O teor de ferro no DRI está em duas formas. Uma está na forma metálica que é conhecida como ferro metálico, Fe (M), e a segunda forma de ferro que está presente em óxidos de ferro residuais, Fe (O). O ferro total, Fe (T), em DRI é a soma desses dois componentes de ferro. Ferro metálico é a quantidade agregada de ferro, livre ou combinado com carbono (como cementita) presente no DRI. As propriedades químicas e físicas do DRI produzido pelos diferentes processos normalmente variam.
A qualidade do DRI é importante, pois impacta parâmetros da siderurgia, como rendimento, consumo de fluxo, quantidade de escória, consumo de energia e taxas de alimentação de carbono, oxigênio e matéria-prima. A qualidade do DRI depende (i) da qualidade dos insumos principalmente minério de ferro/pelotas e combustível/redutor que determina os materiais/impurezas de ganga no DRI, (ii) processo de produção que determina o teor de carbono no DRI, e ( iii) parâmetros de processo que determinam a metalização do DRI.
Um baixo grau de metalização significa que mais FeO deve ser reduzido no EAF. Por outro lado, um alto grau de metalização resulta em menor geração de CO e menor agitação do banho no EAF, o que, por sua vez, reduz a eficiência da transferência de calor e, consequentemente, aumenta os requisitos de energia dos fornos. Os melhores resultados são obtidos quando a metalização do DRI está entre 94% e 96%.
Há duas razões para usar o DRI como parte do mix de cargas na siderurgia EAF. São eles (i) controle residual e (ii) não disponibilidade de sucata premium. A indisponibilidade da sucata premium cria uma pressão sobre os operadores da EAF para recorrer a fontes de sucata de qualidade inferior, como sucata obsoleta, como fonte de unidades de ferro. O problema da sucata obsoleta é a sua qualidade. Além disso, o crescimento na fabricação de aço FAF levou a um retorno mais rápido inevitável da sucata e, como resultado, ao aumento da contaminação da sucata por outros elementos. Resíduos como cromo (Cr), níquel (Ni), molibdênio (Mo), cobre (Cu) e estanho (Sn), variando de 0,15% a 0,75% dependendo do tipo de sucata, têm efeitos adversos em algumas propriedades mecânicas do aço. Assim, geralmente evita-se o uso de siderurgia baseada apenas em sucata em EAFs para a produção de aços de qualidade, bem como produtos de aço de baixo carbono.
Outro problema associado à fabricação de aço EAF baseada apenas em sucata é o nitrogênio. O teor de nitrogênio dos aços EAF é maior do que o dos aços básicos para forno a oxigênio. Como resultado, os aços produzidos na fabricação de aço EAF baseada apenas em sucata têm características de envelhecimento normalmente pobres que os tornam praticamente inadequados, por exemplo, para aplicações de estampagem profunda.
Para a produção de aços especiais de alta qualidade a partir de sucata com qualidade e composição química variadas, a conformidade com altos níveis de pureza às vezes só é alcançada com a diluição de elementos residuais indesejados, como Pb, Cu, Cr, Ni, Mo e Sn com materiais de substituição altamente puros, como DRI. O nível de elementos tramp diminui linearmente quando a porcentagem de DRI na mistura de carga EAF aumenta. A equação da regra geral para calcular o total de elementos residuais em aço líquido no momento do rosqueamento é 'porcentagem (Cr + Ni + Cu + Sn) =0,3225 - 0,001174 x por cento DRI.
Também com o aumento do percentual de DRI na mistura de carga, os níveis de nitrogênio mostram uma redução semelhante com a formação de espuma de escória adequada. A redução de nitrogênio permite que os EAFs produzam muitos aços especiais. Além disso, o DRI também é usado para a produção econômica de aço de alta qualidade com teor muito baixo de fósforo e hidrogênio.
O DRI possui alta densidade aparente, superior à da maioria dos tipos de sucata de aço. Sua densidade é superior à da escória no forno, o que facilita sua fusão na interface escória/metal. O FeO restante no DRI reage com o carbono no banho de metal líquido para melhorar a escória espumante que protege o refratário do arco elétrico. No entanto, a taxa de alimentação DRI é um parâmetro importante do processo EAF que deve ser controlado. A taxa de alimentação ideal depende da composição química do DRI, da temperatura do banho e da energia de agitação fornecida pelos injetores de oxigênio-carbono e pelos tampões de agitação inferiores. As taxas de alimentação DRI na maioria dos fornos carregados com DRI estão na faixa de 27 kg/min MW a 35 kg/min MW.
O teor de carbono do DRI é importante no que diz respeito ao seu uso na fabricação de aço EAF. O carbono em DRI pode estar presente na forma elementar ou pode estar presente como uma combinação tanto da forma elementar quanto da forma ligada. A forma ligada de carbono em DRI é carboneto de ferro (Fe3C), que é um composto estável de ferro e carbono. Normalmente, cerca de dois terços do carbono contido no DRI está presente como carboneto de ferro, e o restante está na forma de carbono elementar. Quando o carbono está na forma ligada, não há perda do C não ligado devido à sua combustão na atmosfera do EAF. A guia 1 fornece especificações típicas de DRI baseado em gás.
Guia 1 Especificação típica de DRI baseado em gás | |||
Base- Fe em minério de ferro/pelota – 65,5% a 68% | |||
Sl. No. | Parâmetro | Unidade | Intervalo |
1 | Metalização | % | 92,0-96,0 |
2 | Fe (total) | % | 86,1-93,5 |
3 | Fe (Metálico) | % | 81,0-87,9 |
4 | Carbono | % | 1,0-4,0 |
5 | Enxofre | % | 0,001-0,03 |
6 | Fósforo como P2O5 | % | 0,005-0,09 |
7 | Gangue | % | 3,9-8,4 |
8 | Tamanho típico | mm | 4-20 |
9 | Densidade aparente | toneladas/cum | 3,4-3,6 |
10 | Densidade de massa | toneladas/cum | 1,6-19 |
Observação:os resíduos são óxidos não reduzidos, como sílica, óxido de manganês, alumina, cal e magnésia |
É normalmente visto que no DRI à base de gás, o teor de carbono do DRI é geralmente maior do que os requisitos estequiométricos necessários para reduzir o teor de FeO restante no produto DRI. O excesso de carbono tem um impacto significativo no teor de FeO da escória e na formação de espuma da escória, necessária para um processo eficiente de fabricação de aço EAF. Em caso de excesso de carbono negativo, a adição necessária de carvão antracito para redução de FeO é benéfica no final do processo de fabricação de aço EAF. No entanto, nem todo o FeO é reduzido a Fe, uma vez que uma porção do FeO sempre existe na escória do forno. Isso significa que a quantidade prática de excesso de carbono de DRI que está disponível para combustão no banho de aço EAF é maior do que o excesso de carbono calculado para redução de DRI. Este termo é chamado de carbono combustível e definido pela equação ‘Carbono combustível =carbono em DRI – carbono estequiométrico x (FeO em DRI – FeO em escória).
O carbono combustível reage com o oxigênio injetado no banho de aço EAF para liberar calor no banho de aço e também contribuir com gás CO para a formação de espuma de escória. Com o aumento do carbono combustível no EAF, o teor de nitrogênio do aço rosqueado também diminui. O excesso de carbono do DRI diminui a entrada de carvão antracito que é uma fonte importante para o nitrogênio dissolvido no banho EAF (0,1% N2) além do ar infiltrado. Um segundo benefício obtido do carbono em DRI é através dos benefícios energéticos do carbeto de ferro. O Fe3C produz energia através das reações exotérmicas obtidas durante sua dissociação no banho de aço (- 0,4 kWh/kg C), em contraste com a dissolução endotérmica das partículas de carbono no banho de aço (0,62 kWh/kg C).
Rendimento metálico e quantidade de escória
O rendimento metálico do aço líquido é influenciado durante a fabricação do aço EAF com a adição de DRI na carga EAF. Vê-se que o rendimento metálico diminui quando a percentagem DRI na mistura de carga EAF é aumentada. Isso se deve principalmente ao aumento do volume de escória.
O volume de escória aumenta à medida que a porcentagem de DRI na mistura de carga EAF aumenta. A equação da regra geral para a quantidade de escória é 'Quantidade de escória (kg/ton de aço líquido) =127 + 2,43 x por cento DRI'. De acordo com esta equação da regra geral, um aumento de 10% de DRI na mistura de carga EAF leva a um aumento no peso da escória em 24,3 kg. O peso da escória depende principalmente do teor e composição da ganga no DRI e da basicidade da escória.
A química e o volume da escória afetam o rendimento no EAF. Com DRI na carga do EAF, o operador deve ter cuidado com a escória para que ocorra uma boa formação de espuma com o volume mínimo da escória na basicidade necessária. Devido à reação de redução endotérmica do FeO pelo carbono, (FeO + C =Fe + CO), e o maior volume de escória encontrado devido ao uso de DRI, o consumo de energia elétrica do EAF normalmente aumenta com o aumento do percentual de DRI no metal carregar. Normalmente, o consumo de energia elétrica aumenta mais ou menos linearmente com o aumento do percentual de DRI no EAF.
Consumo de energia elétrica
O consumo de energia elétrica (kWh por tonelada de aço líquido) durante a fabricação de aço EAF aumenta quando há um aumento no percentual de DRI no mix de carga EAF. De acordo com a regra geral, a cada aumento de 10% na porcentagem DRI leva a um aumento no consumo de energia elétrica de 14,5 kWh/ton de aço líquido sob certas condições.
Muitos fatores tendem a aumentar o consumo de energia elétrica quando se utiliza DRI na siderurgia EAF. Com boa formação de espuma de escória, um EAF que derrete 100% de sucata fria e sem outros insumos energéticos normalmente consome energia na faixa de cerca de 400 kWh/ton a 435 kWh/ton de aço líquido. Para fins de comparação, um EAF com uma mistura de carga composta por 98,2 % DRI com espuma de escória muito boa atingiu um nível médio de consumo de energia de 635 kWh/ton de aço líquido.
A metalização DRI afeta o consumo de energia. O menor nível de metalização do DRI significa maior nível de FeO. A redução química do FeO é uma reação endotérmica. A redução de uma tonelada de FeO para Fe precisa de cerca de 800 kWh nas temperaturas de fabricação do aço. O aumento dos níveis de SiO2 no DRI aumenta os requisitos de energia elétrica. O SiO2 precisa da adição de cal para manter a razão de basicidade. A fusão de uma tonelada de escória requer cerca de 530 kWh de energia. Quantidades crescentes de SiO2 precisam de quantidades crescentes de CaO para manter a razão de basicidade. Tanto o SiO2 no DRI quanto a cal calcinada consomem energia durante o processo de fusão. A Fig. 2 mostra a relação entre o teor de ganga de DRI e o consumo de energia por tonelada de aço líquido. Além disso, há uma série de fatores adicionais que afetam o processo de fabricação de aço. Isso inclui rendimento, requisitos de cal e as necessidades de injeção de oxigênio e carbono.
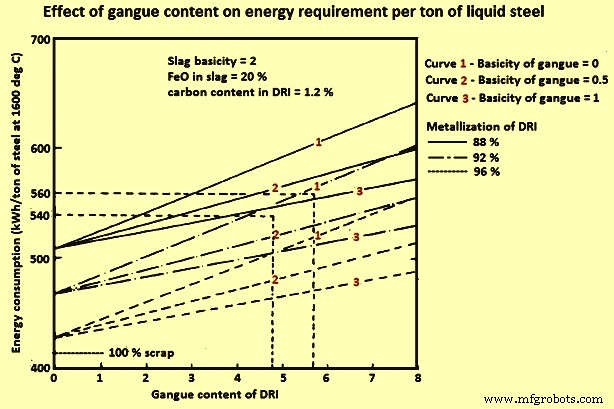
Fig 2 Efeito do conteúdo de ganga na necessidade de energia por tonelada de aço líquido
Os teores de fósforo e enxofre podem ter um efeito negativo no consumo de energia devido aos requisitos de cal. O CaO na cal absorve o fósforo do banho. Se o EAF estiver sendo operado em uma porcentagem constante de FeO, a única maneira de remover mais fósforo é adicionando mais cal. O aumento da quantidade de cal resulta em maior consumo de energia e perda de rendimento de Fe. A remoção eficiente de enxofre requer o uso de uma escória redutora. Os EAFs normalmente operam com uma escória oxidante básica. Embora seja possível remover um pouco de enxofre do EAF aumentando a quantidade de adição de cal, isso resulta em maior consumo de energia e não é muito eficaz.
O DRI carburado tem um efeito positivo no consumo de energia se houver oxigênio de alto volume disponível para injetar no banho. O consumo de energia pode ser reduzido em 2 kWh/N cum para 4 kWh/N cum de oxigênio, se for injetado com a quantidade correta de carbono e for produzida uma boa escória espumante.
Carregar o DRI quente economiza energia, mas a oxidação é um problema. O transporte de DRI quente diretamente do módulo DRI deve ser feito sob uma atmosfera selada de nitrogênio ou gás de processo antes de carregar no EAF.
Efeito da adição de DRI na carga do EAF na hora de ligar
O tempo de ativação é aumentado quando a porcentagem de DRI na mistura de carga EAF é aumentada. A equação da regra geral para calcular o tempo de ativação é 'Tempo de ativação EAF =46,36 +0,1320 x DRI por cento. A substituição da sucata de aço por DRI aumenta o tempo necessário para a fusão da carga EAF (power-on time). Isso é atribuído à menor taxa de fusão do DRI causada pelo FeO que precisa ser reduzido. Além disso, tendo uma escória ácida causada pelos materiais de ganga contendo SiO2 e Al2O3 no DRI. Também é óbvio que o consumo específico de cal e dolomita aumenta para gerenciar a basicidade apropriada da escória próxima (CaO / SiO2) igual a 2. Devido ao aumento da quantidade de escória devido ao aumento do DRI na carga metálica, novamente é necessário para trazer a escória à solução e, consequentemente, há um maior consumo de energia elétrica, e isso também é o motivo do aumento da cal, do consumo total de fluxo e, portanto, da quantidade de escória.
Efeito da metalização no rendimento e outros parâmetros
O rendimento de aço líquido da DRI é uma função da taxa de metalização, conteúdo total de ganga e práticas de injeção e adição de carbono. Uma carga típica de DRI pode conter 93% de ferro total com 86% de ferro metálico para uma metalização de 92%. Se for possível uma redução de 100% do FeO, a carga DRI fornece um rendimento de aço líquido de 93%. Na prática, esse resultado não é alcançável na EAF. Se forem desejados rendimentos mais altos, então o DRI precisa ter uma metalização mais alta. Além disso, à medida que a metalização diminui, ela tem influência negativa em todos os parâmetros. A Fig. 3 mostra a relação típica de metalização com rendimento e consumo de energia experimentado em um EAF.
Fig 3 Relação típica de metalização com rendimento e consumo de energia
Efeito da porcentagem de DRI na mistura de carga na cal e no fluxo total
DRI normalmente contém sílica como o principal constituinte da ganga, juntamente com baixos níveis de outras impurezas, como enxofre e fósforo. De acordo com as concentrações desses componentes no DRI e a proporção de DRI na carga metálica, quantidades variáveis de cal devem ser adicionadas ao EAF para escória da sílica e remover o enxofre e o fósforo para os níveis permitidos desses elementos para o grau do aço a ser produzido.
O consumo total de cal aumenta com o aumento do percentual DRI na mistura de carga EAF. Como regra geral, há um aumento no consumo de cal em 2,6 kg/ton de aço líquido a cada 10% de aumento de DRI na mistura de carga. A equação da regra geral para calcular o consumo total de fluxo (em kg por tonelada de aço líquido) é ‘Consumo de fluxo (kg/t) =45,31 + 0,2416 x DRI por cento.
Metodologia de cobrança
Com o aumento do uso de DRI na fabricação de aço EAF, os métodos de cobrança mudaram. Com uma planta DRI cativa, a porcentagem de DRI na carga EAF é normalmente alta para essas plantas. Nessas usinas, o abastecimento direto ao EAF é feito por meio de um sistema de carregamento contínuo até um quinto orifício no teto do EAF. Invariavelmente, há caixas de armazenamento ou grandes armazéns para aceitar o fornecimento de DRI quando a loja EAF está inativa para manutenção ou atrasos ou quando é necessário estocagem para desligamentos da planta DRI. A Fig 4 mostra diferentes práticas de carregamento sendo seguidas com o uso de DRI na fabricação de aço EAF.
Fig 4 Diferentes práticas de cobrança sendo seguidas com o uso de DRI na fabricação de aço EAF
A alimentação contínua é geralmente empregada acima de 25% para facilitar a adequação da taxa de alimentação à potência e à entrada de energia química e para evitar a formação de “iceberg” ou “ferroberg”. A prevenção de ferrobergs é determinada em parte pela taxa de alimentação e pela entrada de energia disponível.
O carregamento do balde é usado nos EAFs que normalmente usam menos de 25% a 30% de DRI na mistura de carga, embora seja preferível carregar continuamente o DRI. O DRI na caçamba auxilia na densificação da carga, bem como na redução de resíduos em aço líquido. O carregamento do balde evita o custo de um sistema de carregamento contínuo. O DRI é normalmente carregado em cima de sucata pesada ou pacotes (Fig 4) para maximizar a densificação da carga, e o restante da caçamba é carregado de acordo com a prática específica do local. O DRI é normalmente dividido entre baldes em cargas de baldes múltiplos, com mais no último balde para melhorar o refino de fusão, onde o % C mais baixo e o aumento do teor de O2 podem compensar a falta de capacidade de entrada de O2 e minimizar a descarga no final do calor . Se uma prática de carga de balde único for usada, o DRI será inserido em várias camadas. O DRI é carregado mais acima (terceira e penúltima camadas) no balde para evitar que o DRI caia no fundo do balde.
O telhado através de um quinto furo é o preferido para DRI e é definitivamente mais eficiente quando se usa mais de 30% DRI. O carregamento contínuo facilita a coordenação da taxa de alimentação com a entrada de energia e alimentação de fluxo para garantir o controle da escória (altura da espuma e viscosidade etc.) e evitar ferrobergs, que ocorrem quando o DRI frio é carregado muito rapidamente.
O carregamento contínuo a quente (600 dg C) DRI pode reduzir a energia necessária em até 16% a 20%. A alimentação contínua reduz consideravelmente a necessidade de energia do EAF, pois permite a operação de portas fechadas. Isso anula as perdas de calor e tempo de balanço(s) do teto e carregamento, também o potencial de captação de nitrogênio decorrente da entrada de ar que ocorre quando o teto está aberto. O carregamento a quente DRI reduz a necessidade de energia em 20 kWh/100 graus C para 30 kWh/100 graus C. Existem muitos métodos diferentes de carregamento a quente. Um método é o carregamento a quente, transportando o DRI da planta DRI para o EAF em caminhões isolados. Outro método utiliza um sistema de transporte pneumático com alimentação por gravidade através do quinto furo. Várias plantas fazem uso de transportadores ou alimentação direta por gravidade. Um estudo de benchmarking baseado em dados publicados de 150 EAFs mostra que alguns dos EAFs que cobram HDRI estão correspondendo ao consumo de energia de EAFs baseados em sucata.
Processo de manufatura
- Automação de Controle e Modelagem de Forno Elétrico a Arco
- Ferro Reduzido Direto e seus Processos de Produção
- Uso de Nut Coke em um Alto Forno
- Utilização de Metal Quente para Siderurgia em Forno a Arco Elétrico
- Forno de arco elétrico DC
- Opções de descarga para ferro reduzido direto e seu transporte a quente
- Fornos de Arco Submerso
- Uso de Pelotas de Minério de Ferro na Carga do Alto Forno
- Diferentes tipos de processo de soldagem a arco elétrico
- Entendendo a soldagem a arco elétrico