Carbonização de Carvão para Produção de Coque Metalúrgico
Carbonização de Carvão para Produção de Coque Metalúrgico
A carbonização do carvão também é conhecida como coqueificação do carvão. O processo consiste na decomposição térmica dos carvões na ausência de ar ou em atmosfera controlada para produzir um resíduo carbonáceo conhecido como coque.
A carbonização do carvão pode ser realizada nas três faixas de temperatura a seguir.
- A carbonização em baixa temperatura é normalmente realizada na faixa de temperatura de 500°C a 700°C. Nesse tipo de carbonização, os rendimentos de produtos líquidos são maiores e há menor rendimento de produtos gasosos. O coque produzido possui maior matéria volátil e queima livre.
- A carbonização de temperatura média é feita na faixa de temperatura de cerca de 800 graus C. Esta carbonização produz coque macio sem fumaça. Os subprodutos produzidos são semelhantes em características à carbonização de alta temperatura. A carbonização de temperatura média raramente é praticada hoje em dia.
- A carbonização de alta temperatura é realizada a uma temperatura acima de 900 graus C. Esta carbonização proporciona maior rendimento de produtos gasosos e menor rendimento de produtos líquidos. Essa carbonização produz coque duro e normalmente é empregado para a produção de coque metalúrgico a partir de carvões de coque.
Processo de carbonização do carvão
A transformação de carvão em coque ocorre à medida que o carvão é aquecido. Quando o estado de fusão é alcançado, a camada de carvão aquecido amolece e se funde. De cerca de 375°C a 475°C, o carvão se decompõe para formar uma camada plástica. As reações de destilação destrutivas prosseguem rapidamente na camada plástica com evolução de produtos voláteis. A cerca de 475°C a 600°C, há uma evolução marcada de alcatrão e compostos de hidrocarbonetos aromáticos. O gás e o vapor condensável ficam aprisionados na massa plástica e, à medida que se expandem, tendem a inchar. À medida que as reações prosseguem e à medida que a temperatura da zona fundida aumenta, a plasticidade do carvão diminui. Com o aquecimento contínuo e a evolução do gás, a camada fundida gradualmente se solidifica em semi-coque com estrutura de coque celular típica. O coque nesta fase ainda contém matéria volátil substancial. À medida que a temperatura aumenta além de 600 graus C, a reação de destilação destrutiva continua com a evolução de gás e um pouco de alcatrão. A estabilização do coque ocorre à medida que a temperatura aumenta de 600 graus C para 1100 graus C. Isso é caracterizado pela contração da massa do coque, desenvolvimento estrutural do coque e evolução final do hidrogênio. Nesta fase ocorrem as reações finais. Essas reações separam o hidrogênio de hidrocarbonetos extremamente complexos e de alto peso molecular. Com o aumento da temperatura, a massa de coque encolhe com o desenvolvimento de trincas de retração.
O mecanismo de aglomeração
Quando os carvões de coque são carbonizados, primeiro forma-se a massa plástica de isotrópico óptico e, posteriormente, formam-se gradualmente cristais líquidos nemáticos lamelares. Essa fase polimérica é chamada de mesofase. Esta é a fase intermediária entre o carvão fluido isotrópico e o semicoque sólido anisotrópico formado em última instância a partir da mesofase, e possui propriedades intermediárias entre sólidos e líquidos. Se a fluidez da fase intermediária for bastante alta, a mesofase coalescerá imediatamente em uma única unidade maior. Ao longo de uma faixa de temperatura crescente, a mesofase é formada continuamente, cresce em tamanho e finalmente se toca. Assim, a mesofase pode solidificar e converter de carvão de coque em textura anisotrópica óptica de coque.
História dos carvões de coque
A Coca-Cola foi produzida na China antiga de acordo com fontes históricas que datam do século IV. O povo chinês usou pela primeira vez o coque para aquecer e cozinhar o mais tardar no século IX. Em 1709, um alto-forno a coque para produzir ferro fundido foi estabelecido na Grã-Bretanha. , No início do século XVIII o coque era fabricado queimando carvão em montes no solo de tal forma que apenas a camada externa queimava, deixando o interior da pilha em estado carbonizado.
O processo de fabricação de coque 'Hearth', usando carvão granulado, continuou a ser usado em muitas áreas durante a primeira metade do século XIX. Esse processo era semelhante ao da queima de carvão, mas usando um monte de carvão coberto com pó de coque em vez de um monte de madeira preparada, coberto com galhos, folhas e terra.
Estes levaram posteriormente ao desenvolvimento de fornos de colmeia de diferentes formas e tamanhos para atender às crescentes demandas de coque duro para fundição de ferro.
Fornos de colmeia
Um forno de colmeia é uma câmara simples de tijolos refratários construída com um telhado arqueado para que a forma interna seja a de uma colméia antiquada. Suas dimensões são tipicamente 4 m de largura e 2,5 m de altura. Os fornos de colmeia são geralmente construídos em filas, um forno ao lado do outro com paredes comuns entre os fornos vizinhos. Essa fileira de fornos é chamada de bateria. Uma bateria geralmente consiste em muitos fornos, às vezes centenas, seguidos. A seção transversal típica de um forno de colmeia é mostrada na Fig 1.
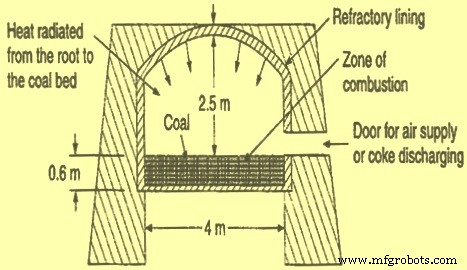
Fig 1 Seção transversal típica de um forno de colmeia
Os trilhos ferroviários para transportar o carvão para os fornos corriam ao longo dos topos; e outros trilhos para movimentação dos vagões de coque corriam ao lado dos fornos. O telhado tem um orifício para carregar o carvão ou outros gravetos a partir do topo. O orifício de descarga é fornecido na circunferência da parte inferior da parede.
O carvão é carregado em um forno vazio através do orifício no ápice da cúpula. Forma uma pilha em forma de cone que é nivelada a uma camada uniforme por meio de um ancinho passado pela porta para produzir uma camada uniforme de cerca de 600 mm a 900 mm de profundidade.
O processo de carbonização é iniciado por meio do calor retido nas paredes do forno pela carga anterior de carvão. Quase imediatamente após o carregamento, o gás constituído por matéria volátil é produzido a partir do carvão. O ar de combustão é admitido por uma abertura na parte superior da porta do forno ou pela porta lateral. O início da carbonização produz matéria volátil que é queimada dentro da porta lateral parcialmente fechada. A carbonização prossegue de cima para baixo. O calor é fornecido pela queima de matéria volátil, de modo que nenhum subproduto é recuperado. Os gases de escape são liberados para a atmosfera.
O tempo de coqueificação, que depende muito da profundidade da camada de carvão, varia de 48 a 72 horas. À medida que a coqueificação prossegue, o volume de gás liberado diminui e o tamanho da abertura na porta diminui correspondentemente ou pela introdução de tijolos na abertura superior. Isso regula a quantidade de ar e evita a entrada de um volume excessivo de ar, que de outra forma queimaria parte do coque e poderia ser suficiente também para resfriar o forno.
O coque quente é temperado com água e descarregado manualmente pela porta lateral. Quando a coqueificação está completa, a porta é aberta e o coque branco quente é extinto por jato de água direcionado através da abertura. O coque temperado é então retirado do forno manualmente e carregado em vagões de trem para transporte. As paredes e o teto retêm calor suficiente para iniciar a carbonização da próxima carga.
Quando o carvão é queimado em um forno de coque, as impurezas do carvão ainda não são expelidas como gases se acumulam para formar escória, que é efetivamente um conglomerado das impurezas removidas. Por não ser o coque desejado, a escória é descartada ou utilizada como ingrediente na fabricação de tijolos, cimento misto e até mesmo como fertilizante.
Os novos fornos são aquecidos por aquecimento com carvão ou lenha antes de serem carregados.
A coqueificação da colmeia é agora um processo obsoleto devido à pequena quantidade que produzia e à grande quantidade de poluição que produzia. No entanto, ainda está sendo usado.
Baterias de forno de coque subproduto
A quantidade máxima de produção global de coque vem dessas baterias. O carvão nessas baterias é carbonizado na ausência de ar e essas baterias são operadas com pressão positiva nos fornos. O processo de fabricação de coque nessas baterias de fornos de coque é chamado de fabricação de coque de subproduto, uma vez que o gás residual é coletado e enviado para a planta de subprodutos, onde vários subprodutos são recuperados. A maioria dos subprodutos das baterias de fornos de coque é integrada em uma planta de ferro e aço para fins de gás de coqueria.
Os detalhes da fabricação de coque em subprodutos de baterias de fornos de coque e planta de subprodutos de fornos de coque são fornecidos em artigos separados nos links http://www.ispatguru.com/coke-making-in-byproduct-coke-oven-batteries/ e http:// www.ispatguru.com/coke-oven-by-product-plant/.
Baterias de forno de coque sem recuperação
Nas baterias de forno de coque sem recuperação, o carvão é carbonizado em grandes câmaras de forno. O processo de carbonização ocorre de cima por transferência de calor radiante e de baixo por condução de calor através do piso da sola. O ar primário para combustão é introduzido na câmara do forno através de várias portas localizadas acima do nível de carga nas portas laterais do empurrador e do coque do forno. Os gases parcialmente queimados saem da câmara superior através de passagens “descendentes” na parede do forno e entram na chaminé única, aquecendo assim a sola do forno. Os gases queimados são coletados em um túnel comum e saem por uma chaminé que cria uma corrente de ar natural no forno. Como os subprodutos não são recuperados, o processo é chamado de fabricação de coque sem recuperação. Nestas baterias geralmente o gás residual sai em uma caldeira de recuperação de calor residual que converte o excesso de calor em vapor para geração de energia, portanto, este processo também é chamado de coque de recuperação de calor. Os detalhes da produção de coque em baterias de forno de coque sem recuperação são fornecidos em artigo separado no link http://www.ispatguru.com/non-recovery-coke-ovens-battery/.
Processo de manufatura
- Considerações para usinagem suíça de alta produção
- A impressão 3D está pronta para a produção da peça final?
- Processo Finex para Produção de Ferro Líquido
- Recuperação de amônia durante a produção de coque de carvão de coque
- Série projetada para linha de produção automotiva
- 3 dicas práticas para acelerar a fabricação
- Práticas de rastreabilidade para produção de fundição
- Máquinas VMC para produção e eficiência
- Taiwan CNC CMM para produção de alta qualidade
- Medição de CMM de Taiwan para Produção Mundial