Práticas de operação e vida de campanha de um alto-forno
Práticas de operação e vida útil da campanha de um alto-forno
O custo de reconstrução ou reembasamento de um alto-forno (BF) é muito alto. Portanto, as técnicas para prolongar a vida útil da campanha do BF são importantes e precisam ser seguidas de forma muito ativa.
Grandes BFs geralmente têm uma saída de campanha ligeiramente maior por unidade de volume. Essa diferença ocorre porque BFs maiores geralmente são de design mais moderno e bem automatizados. Uma vez que a viabilidade de uma siderúrgica integrada depende de um fornecimento contínuo de metal quente (HM), o que em uma planta com um pequeno número de grandes fornos dá grande importância à longa vida útil da campanha.
As técnicas para prolongamento da vida da campanha BF (Fig. 1) se enquadram nas três categorias a seguir.
- Práticas operacionais – O controle do processo de BF tem um grande efeito na vida da campanha. O BF deve ser operado não apenas para atender às necessidades de produção, mas também para maximizar sua vida útil. Portanto, é necessário modificar as práticas operacionais à medida que a campanha avança e em resposta às áreas problemáticas para maximizar a vida útil da campanha.
- Ações corretivas – Quando o desgaste ou dano que afeta a vida útil do BF se torna evidente, técnicas de reparo de engenharia devem ser usadas ou desenvolvidas para maximizar a vida útil da campanha.
- Projetos aprimorados – À medida que materiais e equipamentos aprimorados são desenvolvidos, eles devem ser incorporados em futuras reconstruções para prolongar a vida útil das áreas críticas do BF, onde for econômico fazê-lo.
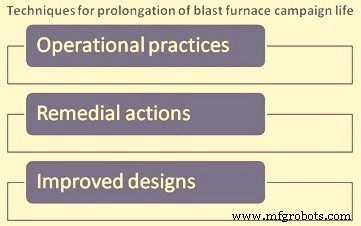
Fig 1 Técnicas para prolongamento da vida útil da campanha do alto-forno
As práticas operacionais para melhorar a vida útil da campanha são discutidas neste artigo. As práticas operacionais que afetam a vida útil da campanha BF estão descritas abaixo.
Produtividade
A produtividade de um BF é normalmente expressa em toneladas (t) de HM por unidade de volume de BF (cum) por dia. A alta produtividade envolve um maior rendimento de materiais em taxas de descida de carga mais altas, com uma maior atividade do forno para remover a maior quantidade de produtos líquidos. A estabilidade da operação é afetada quando o BF está sendo acionado com força, então a descida da carga é menos suave e a zona de fusão é maior. Isso afeta o desgaste da parede do BF. produtos líquidos aceleram o desgaste da fornalha e resultam em condições de furo de macho mais árduas.
A baixa produtividade envolve longos períodos de baixo volume de explosão quente, o que resulta em penetração reduzida da explosão e aumento do fluxo de gás na parede do BF, a menos que sejam feitas modificações adequadas na distribuição de carga. Geralmente, longas pausas de produção ter um efeito prejudicial sobre a condição do coração.
Ao considerar o nível de produtividade dos BFs que alcançaram uma longa vida de campanha, fica claro que esses BFs não foram operados em seu potencial máximo durante a maior parte da campanha. O comum fator é operação estável, consistente, com práticas empregadas para monitorar e proteger as paredes e a lareira. Tal operação é mais facilmente alcançada em níveis de produção abaixo da saída máxima. No entanto, é difícil definir um valor universal de índice de produtividade (t/cum/ dia) para conseguir isso, uma vez que o índice também é afetado por vários fatores além da taxa de condução do BF. Estes são o formato interno do BF, estado de desgaste refratário, condições locais de operação e períodos de manutenção etc.
Para maximizar a vida útil da campanha, é necessária uma estratégia para permitir que o BF seja operado de maneira estável e controlada. Muitas reconstruções de BF envolveram o aumento do volume interno, não para aumentar a produção, mas para permitir que as metas de produção sejam alcançadas em níveis de produtividade mais baixos e, portanto, oferecer o potencial para uma operação mais estável e uma vida útil mais longa da campanha.
É fato que paradas frequentes de um BF reduzem sua produtividade, mas a vida útil da campanha também é reduzida devido ao número excessivo de operações de parada/inicialização. A produção da campanha por unidade de volume é reduzida desproporcionalmente ao percentual de inatividade. Campanhas longas, medidas por este critério, são mais bem alcançadas com operação contínua do BF sem longas paradas.
Reduções de curto prazo na produtividade também são necessárias para atender as áreas problemáticas identificadas no BF, a fim de proteger a integridade do forno, evitando assim o fim prematuro da campanha.
Fardo
Para uma operação estável do BF em níveis razoáveis de produtividade, é necessário coque de boa qualidade. Na verdade, o coque é uma das principais razões para o mau período de operação. Períodos ruins de operação geralmente resultam em operações erráticas e até mesmo refrigeradas que são potencialmente destrutivas para o revestimento do BF e, portanto, para a vida da campanha.
O coque precisa ser forte e estabilizado para suportar o peso da carga com o mínimo de ruptura mecânica. Deve ser suficientemente grande e de tamanho próximo, com um mínimo de finos para criar um leito permeável através do qual líquidos podem escorrer para a fornalha sem restringir os gases ascendentes. Um tamanho consistente é necessário para evitar variações indesejadas na permeabilidade e para apoiar o conceito de variação da espessura da camada de coque ao longo do raio de BF para controlar o fluxo radial de gás. O coque deve ser suficientemente não reage à perda de solução, mantém sua resistência sob tais condições e tem baixo teor de álcalis para minimizar a gaseificação de álcalis na pista, o que tem um efeito deletério na quebra do coque e nos refratários do forno. seu efeito sobre o estado térmico do processo.
Em altos níveis de injeção de hidrocarbonetos na ventaneira, há uma redução correspondente na proporção de coque carregado e, consequentemente, a qualidade do coque torna-se ainda mais importante.
Uma qualidade de coque universal, para uma operação estável compatível com uma longa vida útil do alto-forno, é difícil de especificar, pois não só os diferentes tipos de operação têm diferentes requisitos de coque, mas também as propriedades físicas variam de acordo com o ponto de amostragem entre os fornos de coque e o BF.
No caso de uso de coque de mais de uma fonte, é necessária uma mistura adequada ou carregar discretamente os diferentes coques, pois proporções flutuantes de coques de diferentes propriedades resultam em condições instáveis no BF.
O coque no centro do BF substitui gradualmente o morto e o coque na fornalha, que deve permanecer permeável para permitir que os líquidos escoem pelo centro da fornalha. Isso evita o fluxo periférico excessivo de HM na fornalha que pode resultar em desgaste refratário severo na base da parede lateral. Um aumento na temperatura do centro da fornalha geralmente é observado com um aumento no tamanho do coque morto, o que indica aumento da atividade do centro da fornalha. as telas de coque é um parâmetro importante para a manutenção da permeabilidade do forno, geralmente é benéfico aumentar o tamanho da tela e carregar o coque pequeno adicional que surge, misturado com a carga de minério, longe da linha central do BF.
O objetivo do uso de coque de alta qualidade é garantir que o coque grande alcance as regiões mais baixas do BF. Para monitorar isso, é desejável que o coque seja amostrado de tempos em tempos no nível da ventaneira para avaliar a quebra de coque através do forno. Isso normalmente é realizado durante a manutenção planejada. Uma grande amostra de coque é retirada de uma abertura de ventaneira e suas propriedades são comparadas com uma amostra do coque de alimentação correspondente. Dessa forma, outros fatores que afetam o tamanho do coque também pode ser identificado.
Coque de boa qualidade e consistente e o monitoramento da linha de estoque e do coque bosh é claramente uma estratégia importante para uma longa vida útil da campanha.
Mistura de carga de minério
Os BFs estão sendo operados com uma ampla variedade de componentes de carga de minério, como sinter, pelotas e minério de ferro dimensionado (SIO) etc. Uma variedade de fundentes também é usada na carga de minério.
Quantidades menores de outros materiais, como sucata recuperada, finos ferrosos, carepa de laminação, escória de conversão, ilmenita, resíduos reciclados ou mesmo ferro diretamente reduzido ou ferro granulado também são algumas vezes usadas na carga de minério. O uso desses materiais geralmente depende de fatores locais.
As siderúrgicas integradas normalmente têm plantas de sinterização, portanto, os BFs nessas plantas usam uma grande porcentagem de sinter na carga, com o saldo da carga consistindo principalmente de SIO e/ou pellets. sobre SIO em algumas plantas para o equilíbrio da carga devido às suas propriedades superiores.
Em todo o mundo, a porcentagem de pellets na carga de BF varia de 0 % a 100 %. A experiência em diferentes plantas mostrou que BFs que usam uma alta porcentagem de pellets sofrem maiores variações de carga empilhamento e bosh, levando a um desgaste excessivo do stack inferior e bosh e uma vida útil mais curta da campanha. Uma das razões para isso é o controle inadequado da distribuição da carga. linha de estoque inclinada, tendem a rolar facilmente. Isso resulta em uma camada de minério relativamente espessa em direção ao centro do BF, o que incentiva o fluxo excessivo de gás na parede do BF.
Esta situação está sendo contrariada com a adição de resfriamento de alta densidade no eixo inferior e melhor equipamento de distribuição de carga. deve ser controlado pelo controle de distribuição de carga, com carregamento de coque central e adição de coque de castanha aos pellets.
Um aspecto importante do componente de carga individual são as características de amolecimento e fusão. A maior parte da queda de pressão em um BF está na região onde a carga de minério está amolecendo, derretendo e escorrendo o leito de coque através do qual os gases estão subindo. Uma ampla faixa de fusão e amolecimento causa uma queda de pressão aumentada e uma grande raiz de zona coesiva colidindo com a alvenaria do eixo inferior, com os refratários sendo expostos a altas temperaturas em uma área mais ampla do que o desejável. Uma temperatura de parede mais baixa e/ou menos flutuações térmicas ajudam a prolongar a vida útil do trabalho de alvenaria do poço.
As propriedades de fusão e amolecimento de uma carga de múltiplos componentes diferem daquelas dos componentes individuais. Portanto, os dados do teste de amolecimento e derretimento devem ser considerados não apenas para os constituintes da carga individual, mas também para o mix de minério proposto para auxiliar na seleção da carga de minério.
Para minimizar as variações térmicas e químicas, é desejável uma carga homogênea. Os componentes da carga devem ser misturados o mais intimamente possível. Isso depende do número de componentes da carga e do sistema de carga individual, mas geralmente pode ser alcançado em um grau razoável pela seleção de bunkers de armazenamento e a sequência de descarga do material.
É possível obter uma operação estável do BF e uma longa vida útil da campanha usando cargas diferentes, desde que a qualidade do material seja consistente e haja capacidade de resfriamento de parede adequada e controle de distribuição adequado.
Qualidade da carga de minério
Um BF permeável é necessário para uma operação estável. É importante que a carga de minério seja forte, de tamanho aproximado e peneirada com eficiência para remover os finos. Ele não deve se desintegrar excessivamente na pilha e gerar finos adicionais . Deve ser suficientemente porosa, redutível e de tamanho que permita que seja efetivamente reduzida no momento em que atinge a zona de amolecimento. Desta forma, a zona coesiva é menos restritiva, com menos escória rica em FeO, e a carga térmica na parte inferior regiões do BF é menor, favorecendo o bom funcionamento.
As propriedades de amolecimento e fusão dos componentes do minério têm um efeito importante na operação do BF. Restrições na zona coesiva e características de fusão ruins podem resultar em descida errática da carga, operação instável e flutuações. Essas condições provavelmente encurtarão a vida útil da parede BF.
Não há teste padronizado de amolecimento e fusão e há muitos índices citados para representar as temperaturas de amolecimento e fusão, como início da redução direta, queda de pressão durante a fusão e quantidade de material gotejado, etc.
Distribuição de carga
A distribuição de carga é um dos principais fatores que afetam a vida útil da campanha do BF. Não só pode afetar a estabilidade da operação, mas, ao determinar o fluxo radial de gás no BF, é um dos principais fatores que controlam a taxa de desgaste das paredes de BF.
Geralmente o fluxo de gás radial é controlado pela relação minério/coque na carga, uma vez que o tamanho do coque é geralmente maior. Isso normalmente é obtido carregando o material em camadas discretas e variando a espessura da camada ao longo o raio do BF. A proteção das paredes do BF é, portanto, conseguida aumentando a proporção da camada de minério na parede, o que resulta em uma quantidade reduzida de calor removido pelo sistema de resfriamento da parede. No entanto, há um limite para a proporção de minério próximo à parede do BF para evitar a formação de uma camada inativa, o que pode favorecer a formação de acreções de parede e permitir carga despreparada nas regiões inferiores do BF e aumentar as perdas da ventaneira. o BF deve ser suficiente para permitir a operação estável do BF no nível de produção desejado. Uma grande proporção de coque cria uma região relativamente permeável com menos líquidos descendentes, permitindo o uso do volume máximo de sopro com sem grandes flutuações na pressão de explosão e descida errática da carga.
O coque no centro da BF substitui o coque na fornalha e um centro permeável rico em coque estimula uma fornalha permeável, que relaciona o fluxo de líquido através da fornalha. A chaminé central de coque não é ser desnecessariamente largo. Nesse caso, resultados de ineficiência e danos podem ocorrer em certas partes do topo do forno devido à capacidade de calor excessivamente alta do gás ascendente.
Carregamento de tamanho dividido
Sistemas de distribuição mais sofisticados permitem um controle adicional da distribuição de carga utilizando mais de uma faixa de tamanho de um determinado material. Uma das práticas mais utilizadas é a cobrança de materiais de minério fino, muitas vezes a partir de peneiramentos da carga de minério principal. Os finos são carregados separadamente em pequenas quantidades perto da parede do BF, para dar uma redução localizada na permeabilidade e, assim, proteger as paredes. Carregar um pequeno lote separado de material mais fino geralmente reduz a capacidade de carga do BF.
Coque de nozes
Um sistema de carregamento flexível permite o uso de porca de coque (tamanho típico está na faixa de 10 mm a 30 mm). O carregamento de coque de castanha, misturado na carga de minério e posicionado ao longo do raio médio, melhora a operação, melhorando a eficiência de redução e a permeabilidade da camada de minério na zona coesiva. Há permeabilidade aprimorada e temperaturas da barriga reduzidas com carregamento de coque de nozes. O coque de noz carregado na parede, imprensado entre as duas cargas de minério, evita uma região de parede inativa quando o minério fino foi carregado na parede. O coque de noz é adicionado às pelotas para aumentar seu ângulo de repouso, reduzindo assim a proporção de carga de minério no centro de BF.
Segregação de tamanho
Muitos sistemas de carregamento criam algum grau de segregação de tamanho nos materiais de entrada. Se o material inicial a ser descarregado for mais fino e o material final for mais grosso, essa característica pode ser utilizada para beneficiar a distribuição de tamanho radial e, portanto, a distribuição radial do fluxo de gás. Este tipo de segregação geralmente ocorre em fornos carregados com correia, em vez de fornos carregados com salto, e é mais controlável com um topo sem sino. Modificações adequadas também podem ser adicionadas ao sistema de carregamento para melhorar as características de segregação desejadas.
A segregação de tamanho radial adicional também pode ocorrer rolando para baixo uma linha de estoque inclinada. A segregação de tamanho também pode modificar as características de fusão e amolecimento da carga ao longo do raio BF, quando um componente tem uma faixa de tamanho e química diferentes.
Alguns sistemas de cobrança resultam em uma variação circunferencial na distribuição da carga. Essas variações devem ser minimizadas pelo projeto ou operação.
Carregamento de coque central
Uma grande proporção de coque é geralmente necessária no centro de BF, para incentivar o trabalho suficiente do centro para uma operação estável. Isto é particularmente verdade em produtividades mais altas e ao operar com altos níveis de injeção de hidrocarbonetos na ventaneira. No entanto, operar com coque inteiramente no centro do forno é menos eficiente em termos de combustível e técnicas foram desenvolvidas para minimizar a largura desta região do carregamento de coque central. Em um topo sem sino, isso é conseguido carregando um pequeno lote de coque com a calha giratória totalmente abaixada.
É necessário um leito de coque permeável na fornalha, para favorecer o fluxo de líquidos pelo centro da fornalha e reduzir o fluxo periférico, que pode causar desgaste excessivo das paredes laterais. O coque do morto e da lareira é gradualmente substituído pelo coque do centro da fornalha. O carregamento de coque central reduz a porcentagem de material de minério no centro de BF e melhora a permeabilidade do forno. A permeabilidade da lareira pode ser melhorada com maior carregamento de coque estabilizado no centro.
Vida da armadura da garganta
Para uma longa vida de campanha, é importante minimizar o desgaste da armadura da garganta fixa causada pelo impacto direto dos materiais de carga. Embora seja possível reparar a armadura da garganta ou incorporar placas de proteção, isso pode envolver longas paradas para manutenção, que podem ser prejudiciais à vida útil do forno. Portanto, a distribuição da carga e a altura da linha de estoque usada devem ser escolhidas para evitar esse impacto da carga.
Qualidade do metal quente
Ao operar sem um crânio protetor na lareira, o carbono da lareira geralmente é removido por ataque de solução de ferro e escória. A cementação precoce do ferro, antes de entrar em contato com o refratário da fornalha, minimiza esse desgaste da fornalha.
Para cementação precoce, é necessário um período prolongado de contato entre os líquidos e o coque. A uma dada produtividade, isso pode ser incentivado por uma zona de gotejamento mais alta e homem morto, com uma zona de maior coesão. Isso normalmente resulta em um aumento no silício HM (Si). Geralmente o nível de saturação de carbono diminui com o aumento do teor de Si. Como resultado, o HM está mais próximo da saturação em níveis mais altos de Si, para um determinado tamanho de BF e a temperatura do HM.
Além disso, um aumento no HM Si aumenta a temperatura do HM liquidus e, assim, reduz sua fluidez. Isso tende a reduzir a velocidade do fluxo na fornalha e favorecer a formação de uma camada solidificada no refratário da fornalha.
Em temperaturas de HM mais baixas, o nível de saturação de carbono do ferro é menor e é alcançado mais cedo. A baixa temperatura de HM tem o benefício adicional de aumentar a viscosidade do ferro, o que reduz o fluxo periférico, reduzindo a tendência de dissolver os crânios protetores e penetrar em rachaduras e poros finos.
Maior HM Si e menor temperatura de HM são difíceis de alcançar juntos, pois uma zona coesiva mais alta geralmente resulta em um forno mais quente, mas o efeito geral é que o HM que entra na fornalha se torna mais próximo da saturação de carbono. Uma redução na alta pressão de topo provavelmente resultará em um leve aumento de Si sem afetar o estado térmico do BF. A probabilidade de dissolução do carbono do forno é menor em níveis mais altos de Si.
Diâmetro da tubeira
O diâmetro da tuyère é escolhido para garantir a penetração adequada do jateamento para determinadas condições de operação e para evitar que o gás excessivo suba pelas paredes do BF. A seleção do tamanho da ventaneira influencia o grau de trabalho central do BF e o grau de proteção das paredes do poço e do poço inferior. Geralmente é necessário variar o diâmetro da ventaneira em torno do BF para garantir o equilíbrio circunferencial do fluxo de gás.
Embora os tamanhos das ventaneiras sejam cuidadosamente escolhidos, um aumento significativo no diâmetro é frequentemente observado quando uma ventaneira é alterada, particularmente quando são alcançadas vidas longas. Isso afeta ambos os fatores acima e é vantajoso em termos de vida útil da campanha trocar as ventaneiras após um determinado período, não apenas para minimizar o efeito do desgaste da ventaneira, mas para reduzir a probabilidade de vazamento de água no BF e o número de desligamentos não programados períodos de explosão para alterar as ventaneiras com falha.
O diâmetro das ventaneiras diretamente acima do furo da torneira é frequentemente reduzido, ou as ventaneiras até mesmo fechadas, para promover uma fundição suave e reduzir o ferro feito acima do furo da torneira.
O diâmetro do tuyère é frequentemente reduzido localmente, em resposta às altas temperaturas da parede lateral da lareira, para reduzir o gotejamento de líquidos e a atividade da lareira na área problemática. Isso é feito pela adição de inserções de ventaneiras ou por substituição de ventaneiras. Em casos graves, ou como medida de emergência de curto prazo, as ventaneiras em questão podem ser fechadas por tamponamento com argila. Isso muitas vezes tem um efeito rápido na redução das temperaturas correspondentes da parede lateral da lareira.
Práticas de elenco
As práticas da casa de fundição desempenham um papel importante no controle do fluxo de líquido na fornalha e na prevenção de altos níveis de líquido que podem colidir com a pista, afetando a distribuição da explosão ou até mesmo causando danos à ventaneira ou maçarico. Esses fatores podem afetar a estabilidade da operação, resultar em períodos sem detonação e potencialmente afetar a vida útil da campanha.
Comprimento do furo da torneira
Com um furo de torneira mais longo, os produtos fundidos não são retirados apenas da parte inferior da fornalha, mas também de um ponto mais próximo do centro da fornalha. Isso reduz o fluxo periférico próximo ao orifício da torneira e, portanto, o desgaste da parede lateral da lareira. Para estender o comprimento do furo da torneira, é necessário aumentar a quantidade de massa do furo da torneira injetada ao longo de um período de tempo, para aumentar progressivamente o tamanho do cogumelo no interior do BF, que também protege o refratário abaixo do furo da torneira. Com um comprimento de furo de macho curto e fundição alternada de furos de macho amplamente espaçados, as flutuações de temperatura da parede lateral aumentam, potencialmente aumentando a erosão refratária.
Altas temperaturas da almofada da fornalha podem ser experimentadas devido à perda de uma camada congelada e/ou dissolução do carbono da fornalha, enquanto as temperaturas da parede lateral da fornalha são satisfatórias. Nesses casos, pode ser necessário encurtar o furo do macho, diminuindo a quantidade de massa do furo do macho injetada e possivelmente pela redução da inclinação do furo do macho. Isso ajuda na redução do fluxo de HM próximo ao centro do BF e aumenta os líquidos retidos na almofada da lareira.
Diâmetro do furo da torneira
O diâmetro do furo do macho necessário para sustentar uma determinada produtividade depende dos parâmetros do BF, como a proporção do tempo de fundição, pressão de topo, volume da escória, tamanho do coque da lareira, viscosidades do líquido e as propriedades da massa do furo do macho. Caso o furo do macho seja muito pequeno para uma determinada taxa de produção, não será possível fundir o forno a seco. Se o furo da torneira for muito grande, menos produtos fundidos podem ser removidos do forno durante a fundição, pois o furo da torneira explodirá prematuramente, uma vez que os líquidos acima do furo da torneira são removidos antes que os líquidos do lado oposto da fornalha possam descer. a cama de coque. Em ambos os casos, o nível de líquido na lareira permanece alto e acaba afetando a operação estável. Portanto, é necessário o tamanho ideal do furo de macho, obtido com base na experiência.
Quando um único furo de macho é usado, o tamanho deve ser escolhido para permitir que o BF seja vazado a seco e fornecer tempo suficiente para a massa do furo de macho curar entre os moldes. Em um BF onde são usados furos de torneira alternativos, furos de torneira de tamanhos diferentes podem ser necessários sob certas condições de operação, para garantir a drenagem através do forno.
Em um furo de macho múltiplo BF que está sofrendo desgaste na almofada da lareira, pode ser desejável aumentar o diâmetro do furo de macho. Isso, juntamente com uma diminuição no comprimento do furo da torneira, reduz o fluxo de ferro através da almofada da fornalha e aumenta o ferro residual na fornalha no final da fundição, incentivando assim a formação de uma camada congelada na almofada da fornalha.
Massa do furo da torneira
As propriedades de massa do furo de macho são importantes para as operações de BF. A massa deve endurecer rapidamente e curar completamente entre os moldes para criar um furo de macho forte e durável. A massa do furo da torneira deve ter boas propriedades de adesão, para construir uma estrutura forte e permanente que resista ao fluxo de líquidos e também proteja os refratários da lareira abaixo do furo da torneira.
Número, posição e desempenho
Alta produtividade pode ser alcançada em um alto-forno de tamanho médio com furo único. No entanto, existem vantagens quando mais de um furo de macho está disponível, sendo esta uma necessidade em níveis de produção mais elevados. A fundição alternada de furos de macho em lados opostos do forno resulta em uma drenagem mais eficaz da fornalha e também dá um período mais longo para a massa do furo de macho curar completamente, resultando em um furo de macho mais durável. A existência de dois furos de torneira permite uma grande reforma de um canal de ferro principal sem a necessidade de um período sem jateamento. Se ocorrerem pontos quentes na parede da fornalha de um orifício de derivação múltipla BF, pode ser possível usar um orifício de derivação alternativo que não estimule o fluxo periférico na área erodida. O desgaste da parede lateral resultante do fluxo periférico será espalhado mais uniformemente ao redor da circunferência em um forno de furos múltiplos.
Para um BF grande e de alta produtividade, é preferível ter quatro furos de macho, permitindo que um par oposto seja operado enquanto um corredor é reparado e o outro está em espera. Para uniformizar o desgaste das paredes laterais e favorecer a drenagem completa da fornalha, estas devem ser localizadas idealmente em intervalos de 90 graus.
Frequência e taxa de transmissão
A taxa de fundição é determinada pelo tamanho da broca do furo do macho usado, as características de desgaste da massa do furo do macho, a pressão máxima, a viscosidade dos líquidos e o número de furos do macho em uso. Com a massa do furo de macho moderno de alto desempenho, há uma tendência de redução do número de fundidos, o que reduz os custos operacionais do furo de macho. Ao diminuir a taxa de fundição, as velocidades do líquido dentro da lareira diminuem, mas continuam por um período mais longo. Em um BF multifuncional, existe a possibilidade de fundir simultaneamente a partir de furos opostos (lap casting), proporcionando a cura total do furo em um tempo menor do que a duração da moldagem e a mão de obra e logística permitem isso. Esta técnica reduz as velocidades de fluxo na fornalha, embora muitas vezes seja usada apenas em momentos de alto nível de líquido ou antes da detonação do BF.
Atrasos de fundição longos devem ser evitados a todo custo, para minimizar a interrupção das operações de BF. Isso requer um bom projeto e operação confiável de equipamentos de fundição, boas práticas de fundição e transporte bem coordenado de panelas de HM.
Álcalis e zinco
Metais alcalinos e zinco têm efeito deletério sobre o processo BF e refratários. O ônus é ter um teor de álcalis e zinco em um nível econômico mínimo. Normalmente, álcali e zinco são controlados em níveis inferiores a 5 kg/tHM (a melhor prática é 2 kg/tHM), mas pela condensação do vapor alcalino na carga descendente, uma grande carga de recirculação pode se acumular no BF. Isso resulta em maior degradação do sinter e quebra de coque, e estimula a formação de acreções de parede, todas as quais podem resultar em descida irregular da carga e operação instável do BF.
Os álcalis e o zinco, na forma gasosa, penetram nas fissuras e poros dos refratários de parede BF. O ataque químico resultante e a ciclagem térmica enfraquecem a camada superficial do refratário, que é eventualmente removida pela carga descendente, permitindo que o processo seja repetido.
As dissecações da lareira após o final da campanha mostraram que ocorre um desgaste excessivo na base da parede lateral e que geralmente se forma uma zona frágil entre a casca e a face quente do carvão. Os álcalis e o zinco são frequentemente encontrados em níveis elevados nesta zona frágil. Vários mecanismos de degradação têm sido propostos envolvendo esses compostos. Estresse e rachaduras térmicas na parede lateral permitem que álcalis gasosos e zinco penetrem e se depositem nos poros. Isso leva à expansão do tijolo, fragilização, inchaço adicional e, finalmente, destruição da massa refratária. Um grau significativo de proteção do refratário contra álcalis e zinco é alcançado se uma acreção ou crânio for congelado na face quente do refratário, protegendo assim o refratário do ataque químico.
A maioria dos álcalis é removida na escória e o restante no gás de topo. No entanto, a prática de escória, estado térmico e distribuição de carga desempenham um papel importante na remoção de álcalis. Uma redução na basicidade da escória aumenta a quantidade de álcali removido na escória como um aumento no nível térmico do BF ou na temperatura de topo, ampliando ou intensificando o grau de trabalho central. Além disso, para uma dada carga alcalina, a degradação do coque provavelmente será maior para operações com alta taxa de injeção de hidrocarbonetos na ventaneira, devido ao aumento do tempo de residência da carga. É importante que o balanço de entrada e saída de álcali e zinco seja monitorado e que o BF seja operado com regime térmico e químico compatível com o nível de entrada desses elementos, para favorecer sua remoção na escória e gás de topo.
Adição de TiO2
Amostras do revestimento da lareira no final de uma campanha em BFs normalmente contêm depósitos de rolamentos de titânio. Estes formam uma camada protetora em regiões erodidas da parede lateral da lareira, na salamandra e em poros e juntas de tijolos. O titânio está geralmente na forma de carbonitretos Ti(C,N), uma solução sólida de carboneto de titânio (TiC) e nitreto de titânio (TiN). Portanto, atualmente a prática envolve a introdução de titânia (TiO2) no BF para promover essas camadas protetoras. Três métodos são normalmente usados para a introdução de TiO2. Estes são (i) adição à carga, (ii) injeção nas ventaneiras, (iii) adição através da massa do furo de derivação.
A técnica mais comum tem sido pela adição de minérios titaníferos (geralmente ilmenita) à carga. Alternativamente, TiO2 pode ser adicionado através de sinterização, embora em níveis baixos.
Two strategies are generally adopted for TiO2 addition. The first one is remedial, commencing TiO2 additions only when high hearth temperatures are observed, indicating hearth wear. The other takes a preventive approach and adds a small quantity of TiO2 continuously, increasing the addition level if high temperatures are observed. The TiO2 intake for the preventive approach is generally 3 to5 kg/tHM, which usually results in up to 0.1 % Ti in the HM and 1 % to 1.5 % TiO2 in the slag. For remedial action, the TiO2 dosage can be up to 20 kg/tHM, at which level the HM may contain up to 0.3 % Ti and the slag up to 3.5 % TiO2. This creates operating problems due to high slag viscosity and scaffolding in the runner, and hence such high TiO2 levels are only used for short periods.
For promoting the precipitation of Ti(C,N), sometimes the TiO2 addition is increased before a shutdown so that the HM remaining in the hearth get saturated in Ti. As the hearth cools during the shutdown, this promotes precipitation. However the resumption of production is more difficult at high Ti levels as it creates operational problems.
TiO2 can also be added by injecting TiO2 fines through the tuyeres. The advantages of the technique are (i) application at localized positions, (ii) reduced cost due to lower TiO2 rate, and (iii) good results from short time injection, and (iv) unchanged burden properties.
The third method of TiO2 addition is by the use of tap hole mass containing TiO2. One such mass which had been tried was tar bonded with approximately 10 % TiO2. Clearly, the titania is bound in the tap hole mass in an unreduced form, and is injected in relatively small quantities. However there are doubts whether it gets reduced and dissolves in HM in sufficient quantities to be precipitated or whether it is reduced and bonded adequately to the hearth sidewall to be of benefit.
TiO2 is normally partially reduced in BF and is dissolved in the HM. The solubility is greater at higher temperatures. If the Ti in the HM is nearing saturation and the refractory hot face temperature in eroded regions, cracks and pores temperature is lower than the HM temperature, then Ti is precipitated, as Ti(C,N). The technique is more likely to succeed at higher addition rates, but there are other factors which can interfere with this basic mechanism, including thermal state of the hearth, metal/slag chemistry and liquid flow characteristics.
TiO2 additions is usually carried out in conjunction with other remedial actions such as reducing productivity, closing tuyeres and improving hearth cooling intensity. The direct effect of TiO2 addition is therefore often difficult to determine. It is essential to carry out regular, accurate Ti balances to assess the technique and modify operation to encourage Ti retention. The effect of high rate additions can even have a detrimental effect on furnace operation, negating any benefits.
The addition of TiO2 for hearth protection is normally to be considered as part of a hearth protection plan rather than in isolation.
Monitoring
Burden distribution is to be monitored regularly for ensuring the wall protection and a stable and driving BF. Changes in the operating parameters, e.g. changes in tuyere hydrocarbon injectant rate or blast volume, may need adjustments to burden distribution. The effect of burden distribution is usually monitored with various probes and instruments.
For maximizing the campaign life, it is necessary that the charging equipment is capable of controlling accurately the burden distribution. Also necessary instrumentations are to be fitted to comprehensively monitor the BF operation so that the burden distribution is changed and assessed in a controlled and technical manner.
Instrumentation and control
Early warning of hearth problem areas is vital to maximize campaign life, and thermocouples located in the hearth sidewall and in the hearth pad are absolutely necessary to monitor hearth wear. Revised operating practices and actions to protect the hearth are to be taken as a result of increasing hearth temperatures. Hearth pad and sidewall temperatures can also give an indication of liquid flow in the hearth, an important factor in hearth wear.
Temperatures recorded by thermocouples are influenced by only a small area round the thermocouple. It is therefore vitally important to locate the thermocouples in the critical wear areas. Important areas are below the tap holes and around the base of the sidewalls where the so called ‘elephant’s foot’ wear pattern is normally found. An adequate number of thermocouples are to be installed, in the best layout to give as complete coverage as far as practical. At several locations, thermocouples can be positioned at two or three different depths to allow calculation of the thermal profile in the refractory and hence the thickness of residual refractory.
Movement of carbon blocks can nip hearth pad thermocouples, causing false hot junctions or total failure. These problems can be overcome by fitting the thermocouples in sheaths. Thermocouples are also to be positioned around the tap holes, to monitor tap hole conditions and operation.
Additional thermocouples are often added part way through a campaign in areas of known refractory wear, to give a more localized picture of developing problems. Similarly, thermocouples are often added to repaired areas to monitor the repair.
Monitor hearth cooling
Heat flux in the hearth pad or stave cooling water can be determined from the water flow rates and the difference between inlet and outlet water temperature, using resistance thermometers. It can be used only to give an indication of the average hearth wear. It is particularly applicable in the later stages of a campaign, following thermocouple deterioration. Monitoring long term trends in hearth cooling water temperature may give an indication of the efficiency of the cooling system.
Furnace wall conditions
The process conditions at the furnace wall are vital to campaign life. The walls is not to be subjected to high heat loads from an excessive quantity of gas ascending at the wall or impingement of the melting zone on the wall, which results in rapid deterioration of the refractory and wear of the cooling members. On the other hand the walls must not be so inactive that large accretions are permitted to form on them, which prevents smooth burden descent, control of burden distribution and stable blast furnace operation. To monitor wall conditions a variety of methods are used.
The common method of monitoring the walls is using in-wall thermocouples, positioned in the brick work, with the tips a short distance back from the hot face to give a good thermal response. Wall activity is monitored from the temperature level and fluctuations.
There must be a good coverage of thermocouples both vertically and circumferentially to monitor the walls adequately. Typically seven levels of thermocouples, each with eight circumferential positions are used. With a large number of thermocouples, it is difficult for the operator to monitor the variation of them all. By using the temperatures at many points, an isothermal map is normally generated, identifying regions of high or low temperatures which relates to refractory wear, asymmetrical operation or accretion formation. The dynamic temperature behaviour is also be utilized to predict the formation or loss and extent of an accretion.
Throat or skin thermocouples are often installed around the periphery, just below the fixed throat armour. The thermocouple tips are installed level with the hot face of the refractory, to record gas temperature. These give a direct measure of the gas flow at the wall and are usually unaffected by deposition of material, unlike in-wall thermocouples lower in the stack.
Radial measuring probes
The use of retractable probes is one of the important techniques to monitor and optimize burden distribution, and hence campaign life. Such probes are the only method of measuring the variation in operating characteristics along the furnace radius, as opposed to relying solely on wall measurements. They are essentially of two types namely (i) overburden, and (ii) underburden.
Overburden probes have several functions. The simplest type is usually fixed, water cooled and measures the radial or diametrical top gas temperature profile and, in some instances, the gas analysis. Most retractable probes measure the stock line layer profile and can be of a mechanical type, where a weight is lowered to the stock line or a non-contact type, using radar, microwaves, lasers, etc.
Top gas velocity can also be physically determined to measure the quantity of gas flow, and top gas analysis and temperature measurement is frequently carried out in conjunction with the other functions. Probes are also used to determine the trajectory of material off the rotating chute or movable throat armour, for calibration of burden distribution predictive models and to determine the effect of charging chute wear.
Underburden, or in-burden, probes sample gas and measure temperature at a number of radial positions. They are generally positioned in the upper stack, typically 3 m to 6 m below the stock line. These probes are generally of two types. The consumable type, is typically 50 mm in diameter, bends with the descending burden and is straightened on withdrawal for subsequent re-use.
Since the top gas has to pass from the stock line up one of the four off takes, the gas flow pattern begins to distort near the stock line. A large degree of gas mixing then occurs above the burden, and overburden probes must be positioned close to the stock line, and preferably inclined, to give acceptable temperature and gas profiles. The upper stack underburden probes are more sensitive and give superior results to overburden probes. In addition, fixed overburden probes can be quite big in size and, depending on the stock line height, can create a ‘shadow’ and distort the burden distribution below them, which can give unrepresentative results.
Probes, especially underburden probes, are essential tools for prolonging BF campaign life.
Hearth models
In recent years, with increasing computing power available, many mathematical and numerical techniques have been developed to predict blast furnace hearth erosion and liquid flow in the hearth.
Hearth lining wear may be calculated by mathematical model, using temperature measurements from embedded thermocouples in the hearth bottom and sidewall. For this technique to be accurate, a good coverage of thermocouples is required and their depth of insertion needs to be known precisely, together with the thermal properties and geometry of the lining. The accuracy may also be affected by parameters that may change with time, such as the conductivity of ramming, thermal contact between courses of brickwork and the development of a brittle zone in the refractory, which can significantly change its conductivity.
Although hearth temperatures alone give a direct indication of hearth wear, this type of modelcombines information from the thermocouples, at differing distances from the hot face, to predict the extent of wear and solidified layers more accurately.
Direct measurement of hearth lining wear is difficult and undesirable since this requires test borings and embedded sensors through the full refractory thickness.
Artificial Intelligence
The blast furnace process is a complex one, with a large number of process variables. Modern, well instrumented furnaces have hundreds of sensors which require to be monitored by a decreasing number of operators. Consequently, computerized systems are being developed to process the primary information available and give secondary advice to the operators. This is based on a set of operating rules, statistical analysis of data, identifying trends that compare with historical data and use of intelligent techniques such as fuzzy logic and neural networks. The aim of these systems is to predict deviation from steady operation and to quantify the change in control parameters required to minimize the deviations in production and quality. This results in more stable BF operation, avoiding major operating problems such as erratic burden descent and chilled conditions, which is a primary requirement for long campaign life.
Furnace top sensors
Since the late 1970s, many BFs have been equipped with infra-red cameras viewing through windows in the top cone, to measure stock line temperature profile. This technique overcomes some of the disadvantages of fixed overburden temperature probes. The falling burden is not scattered as with probes, leading to a more symmetrical burden distribution, and by measuring material temperature the effects of stock line to probe distance, which can result in gas mixing and desensitizes the temperature profile, are avoided. A further benefit is that the rotation of the distribution chute in the furnace can be observed. However, these systems are expensive, difficult to maintain and experience problems in keeping the viewing window clean, due to the moist, dusty top gas. Problems have been experienced with the dust in the top gas also affecting the temperature distribution. Hence these cameras are not a standard fitment and many operators have abandoned them in favour of radial probes.
Some furnaces are equipped with non-contact stock line profile measurement systems installed in the furnace top cone. These systems effectively replace a retractable overburden probe and, although expensive, have the advantage that they measure over a larger proportion of the stock line than the single radius of a probe.
Thermography
The use of thermal imaging cameras to detect hot spots, on the furnace shell, top gas system, tuyere stocks, stoves, hot blast and bustle mains and other ancillary plant, is important. Not only does it enable early detection of problem areas and permit their systematic rectification, but it also helps prevent catastrophic failures, in which the BF has to be taken off-blast in a sudden uncontrolled manner followed by an often difficult recovery, which would have a detrimental effect on campaign life.
Leak detection
An efficient system of detecting water leaks into the BF from tuyeres and other cooling members is essential. Undetected water leaks may chill the furnace, resulting in erratic operation and difficult recovery from chilled conditions. Water leakage directly affects BF campaign life if it damages the refractories. Water leaks in lower, hotter regions of the BF, which are lined with carbonaceous materials, inevitably results in oxidation of the refractories. Rat holes in the hearth refractories can result, which can lead to breakouts. Water leakage can also result in tap hole problems which may disrupt operations.
Tuyere leak detection systems are often used. One leak detection system incorporates a system of magnetic flow meters with computer analysis of the differential flows. Another system of leak detection uses a pressurized closed circuit water system incorporating make up tanks with the makeup frequency indicating the severity of a leak. Other systems involve observation of gas bubbles or dissolved CO content in the water, differential pressure measurements etc.
A good leak detection system often warns the operator of a water leak in its early stages, before an immediate off blast is required. This gives the opportunity for the leaking member to be isolated prior to the furnace being taken off in a controlled manner, with reduction in tuyere hydrocarbon injection and ore/coke ratio adjustments, thereby minimizing detrimental effects resulting from the subsequent stoppage.
Plant maintenance
All maintenance work possible are to be carried out during production, thereby reducing the off blast time necessary. To minimize the duration of a planned stoppage, good planning and advance preparation are necessary. Although these factors are obvious for economics and to maximize plant output, their long term effect on furnace life is not always considered.
Preparations should always be in hand for maintenance to be carried out if the furnace comes off blast unplanned for other reasons. For instance, if the furnace is off for a tuyere change, it may be possible for work to be carried out on the charging system. If the furnace is off blast for problems at the steel melting shop, then it may be possible for more extensive maintenance to be performed. In this way, the total number of stoppages during a BF campaign can be reduced and their duration minimized.
Effective maintenance reduces the number of breakdowns which result in unplanned stoppages. This involve routine maintenance, regular inspections, periodic checking of important instrumentation, and condition monitoring, e.g. vibration and thermal monitoring. This is most important at later stages of a campaign, as ancillary equipment gets older and less reliable.
Similarly, improved cast house maintenance techniques can reduce off blast time, e.g. extension of the life of the main iron runner on a single tap hole furnace reduces downtime.
Off blast periods
The number of off blast periods, mainly unplanned ones, has a major effect on campaign life in terms of output per unit volume, which is reduced disproportionally to the percentage downtime. Wall damage can result from an increased degree of wall working at the lower blast volumes encountered whilst coming off and on blast, cooling and reheating of the refractories or erratic operation during recovery from the stoppage.
Some BF operators indicate that off blast periods ‘rest’ the hearth and allow a protective skull to form or thicken. In fact, taking the BF off blast is often an emergency procedure, at later stages of the campaign, when high temperatures are detected within the hearth refractory.
Short stoppages
For planned stoppages, additional coke can be charged several hours in advance, to compensate for the reduced blast conditions and the heat losses during the stoppage period. This extra coke in the lower regions of the BF assists smooth recovery from the stoppage. It is usual to decrease or remove tuyere hydrocarbon injection for a stoppage.
At high injection rates, there is a much lower proportion of coke in the BF, which is consequently less permeable and this may hinder recovery from the stoppage. In addition, at high injection rates, the BF is markedly fuel deficient during the recovery until the injection is resumed. This may not happen until the blast volume has reached about half of its full rate, when an adequate raceway is formed and the injectant can be consumed safely. In case there are operating problems in establishing raceway conditions and returning to the level of blast at which injection is possible, it can result into cold conditions or tuyere blockages with slag and the BF is fuel deficient at a time when additional fuel is needed.
In addition to ore/coke ratio compensation, a burden change is generally desirable for a stoppage period. Smaller material components of the burden is to be removed from the burden to promote permeability following the stoppage. High levels of titaniferrous ores is also to be reduced to avoid problems at lower HM temperatures after the stoppage. The proportion of burden components that deteriorate when at high temperatures over a long period, such as ores prone to decrepitation, are to be reduced in a stoppage burden. In addition, a more acid burden may be charged to compensate for higher Si content in the HM during recovery from the shut down.
During a stoppage, other deleterious factors can occur which affects the return to full blast operations. For example, this may include (i) extended periods at reduced blast volume to cast the furnace dry before the off blast, (ii) an extended stoppage period for a variety of reasons, (iii) water leakage into the BF during the shutdown, and (iv) problems during the recovery that may require several off blasts (may be to rectify blast leaks or charging faults etc.). Under such circumstances, the undesirable operating conditions are extended and the additional coke charged may not be adequate, leading to a less smooth recovery from the stoppage.
To ensure smooth operation and minimize the effect of a stoppage on the life of BF, some operators believe a slow start after a planned stoppage. A typical of this is to control output to 90 % on the day before a stoppage and resume at 80 %, then 90 % output on the two days following the stoppage. However, this may not be acceptable to other operators, under conditions where high output is needed.
Unplanned stoppages are undesirable and, if possible, many BF operators try to delay taking the BF off blast for long enough to allow a compensated burden to descend to bosh level. Attempt is usually made to cast the BF as dry as possible, to avoid getting slag back into the tuyeres and blowpipes, which may freeze and further prolong the stoppage. This also gives time to prepare for the repair work due to be carried out and to minimize the time of off blast. To compensate for the heat lost due to an unplanned stoppage, the tuyere hydrocarbon injection is generally increased after coming back on blast, providing it is not already at its maximum level.
Production stoppages can also occur due to the problems in the steel melting shop or during periods of low demand. These occurrences are to be coordinated so as to get advanced warning wherever possible, and to give the option of a compensated burden. The pig casting machine (PCM), torpedo ladle fleet or steel melting shop mixers are to be used as a buffer for short stoppages. In certain circumstances, when there is minimal advance warning of a shutdown, the BF is not dry and there is little empty ladle capacity, and there is no PCM available, it is preferable to dump the HM.
Stack spray techniques for the repair of wall refractories have advanced, enabling the walls to be gunned in a relatively short stoppage, by blowing the burden down to a low level. Although this allows a large quantity of coke to be charged at the lower levels of the furnace to aid start up, there is often difficulty due to the quantity of rebounded refractory falling into the furnace. Start up is easier if a low rebound material is used and the BF is blown down to tuyere level, enabling the rebound material to be raked from the furnace. This can be achieved more effectively by the use of T shaped sheets of corrugated sheeting, inserted rolled up through the tuyere cooler apertures. The blow-in burden chemistry is also to be adjusted to give a slag chemistry that enables the residual rebound material to be melted.
There is a difference of opinion as to whether or not cooling water flows should be decreased for stoppages of greater than a given duration. Some operators prefer reduced flows to maintain refractory temperatures. The majority prefer the hearth cooling water on full flow to promote a thicker protective skull, whilst others who reduce the water flow suggest that by removing less heat it assists a smooth start up.
Another factor which affects the recovery from a stoppage is the removal of an accretion from the BF walls, resulting from the additional wall working and erratic burden descent. This can results into chilled conditions at a time when they are least desirable. If an accretion is known to have formed, it is desirable to try and remove it before a long stoppage. A good system of accretion monitoring provide immediate warning in case of its occurrence, to enable thermal compensation as soon as possible.
Long stoppages
Depending on the duration of the stoppage, the BF may be filled with a coke blank and a low ore/coke burden, or the burden may be blown down to tuyere level. For stoppages of several weeks or longer, the salamander is to be tapped. If this is not done, not only will a considerable amount of process heat be needed, during the recovery, to melt it, but it will expand whilst still solid and create undue stresses on the hearth refractories and shell, shortening their life. This is even more important with those BFs, where the sump depth has been increased to reduce peripheral iron flow in the hearth. It is desirable to monitor these stresses with strain gauges attached to the hearth jacket, and to develop procedures to minimize such stresses.
To recover from longer stoppages, when the BF is in a cold condition, it is necessary to’ warm the hearth and establish an early link between the tap hole and the tuyeres to allow liquids to be removed. This may be done by the use of a blast pipe at the tap hole or the use of an oxy-fuel lance. It is important to prevent the oxygen, entering at the tap hole, damaging the hearth carbon, which can directly shorten the campaign life. Recovery from chilled hearth conditions, following major water ingress during a routine maintenance stop, has been reported to have resulted in severe hearth erosion. Recovery from long shutdowns, with a large quantity of solid metal in the hearth and an impermeable dead man, may result in excessive peripheral flow in the hearth with accelerated hearth sidewall erosion.
Production rules
Being a continuous process, the BF is operated by a number of different operators who, without a set of rules to operate to, would react differently to a given situation. The individual actions taken may not be the correct one and, as a result, the process can be more variable than if the ideal action was taken. The majority of BFs are therefore operated according to set procedures that have been developed and improved from experience. These rules cover a wide area, including practical procedures and process control.
To maximize BF stability, it is necessary to control accurately both the thermal state and the aero-dynamics of the furnace. Steel plants usually devise their own rules to control thermal state, which generally involve the HM Si and temperature as indicators, with the use of top gas analysis and calculation of the quantity of heat available in the BF for silica reduction and to superheat the liquid products. Control of thermal state is usually by adjustment of conditions at the tuyere or by small changes in the quantity of coke charged. Furnace aero-dynamics are monitored by rules relating to furnace pressure drops and burden descent rates, with adjustment to blast volume, burden distribution or burden properties to achieve stability.
Operating rules are also necessary for non-routine operations, where damage to the BF may result from incorrect procedures, for instance in the recovery from chilled hearth conditions, where damage to refractories can happen.
Specific rules for prolongation of BF life
Many operators have a specific set of operating practices for the prolongation of campaign life, which are in place to minimize damage to or prevent further deterioration of the BF. As the hearth is the critical region of the BF which cannot be repaired without a long shutdown, these rules or action plans often relate to hearth conditions. Typically, the actions are defined according to hearth temperatures or refractory thickness.
Processo de manufatura
- Escória de alto forno e seu papel na operação do forno
- Aspectos importantes do projeto de alto-forno e equipamentos auxiliares associados
- Sistema de automação, medição e controle de processos de alto forno
- Forno de indução e siderurgia
- Geração e uso de gás de alto-forno
- Uso de Nut Coke em um Alto Forno
- Produtividade do Alto Forno e os Parâmetros Influenciadores
- Operação de alto-forno e escória de alta alumina
- Irregularidades do alto-forno durante a operação
- Fabricação de ferro por alto-forno e emissões de óxido de carbono