Geração de Estufas de Jato de Ar Quente e de Jato Quente
Geração de Fogões de Jato de Ar Quente e Fogões de Jato Quente
Um forno de sopro quente é uma instalação para fornecer continuamente o sopro de ar quente para um alto-forno. Antes de o ar de sopro ser entregue às ventaneiras do alto-forno, ele é pré-aquecido passando-o através de estufas regenerativas a quente que são aquecidas principalmente pela combustão do gás de topo do alto-forno (gás BF). Desta forma, parte da energia do gás de topo é devolvida ao alto-forno na forma de calor sensível. Essa energia térmica adicional devolvida ao alto-forno como calor reduz substancialmente a necessidade de coque de alto-forno e facilita a injeção de combustíveis auxiliares, como carvão pulverizado, em substituição ao caro coque metalúrgico. Isso melhora a eficiência do processo. Um benefício adicional resultante da menor necessidade de combustível é um aumento na taxa de produção de metal quente. Todos estes têm um efeito significativo em termos de redução do custo do metal quente.
História dos fogões a quente
O uso de altos-fornos remonta ao século V a.C. na China. No entanto, não foi até 1828 que a eficiência dos altos-fornos foi revolucionada, pré-aquecendo-os usando fogões quentes em conjunto com o processo, uma inovação criada por James Beaumont Nielson, anteriormente capataz da fábrica de gás de Glasgow. Ele inventou o sistema de pré-aquecimento da explosão para um forno. Ele descobriu que, aumentando a temperatura para 300 graus F (149 graus C), ele poderia reduzir o consumo de combustível de 8,06 toneladas para 5,16 toneladas com reduções adicionais com temperaturas mais altas. Em 1860, o uso cooperativo de fogões quentes com altos-fornos foi transformado ainda mais por Edward Alfred Cowper, reciclando o gás superior do alto-forno, em vez de receber combustível sólido, como os projetos anteriores.
Os primeiros projetos de fogões quentes usados com altos-fornos foram originalmente colocados em cima do forno e não ao lado dele, o layout atual usado hoje. Eles usaram o calor residual do alto-forno entregue através de tubos de ferro fundido para o fogão quente para pré-aquecer o jato de ar frio. Um grande problema com o uso de tubos de ferro fundido era a geração de rachaduras ao longo deles. Isso foi remediado eliminando os tubos e usando refratários em seu lugar. Isso também favoreceu o desenho do layout do fogão quente com o alto-forno para o uso de dois a quatro fogões quentes colocados em série ao lado do alto-forno. Isso permitiu o aquecimento de um alto-forno pelo gás de topo do alto-forno enquanto o outro estava sendo drenado de seu calor para pré-aquecer o jato de ar no alto-forno. Quando o jato de ar entrou no fogão, foi pré-aquecido por tijolos quentes e saiu do fogão como um jato quente. Cambria Iron Works foi a primeira empresa nos EUA a usar fogões regenerativos em 1854. Esses fogões foram construídos com conchas de ferro revestidas com refratário e continham várias passagens de refratário para a explosão. Um fogão típico deste projeto tinha cerca de 186-232 m² de superfície de aquecimento. Em 1870, a Whitwell Stoves projetou e produziu fogões maiores com superfícies de aquecimento de cerca de 8.546 m², que poderiam fornecer uma explosão quente de 454-566 graus C ao alto-forno. Esses também foram os primeiros fogões a usar damas refratárias hexagonais, suportes de verificação de ferro fundido e câmaras de combustão semi-elípticas para melhorar a distribuição de gás pelas damas.
Características de um fogão moderno a jato quente
O poder calorífico do gás de topo do alto-forno não é alto o suficiente em valor para atingir a alta temperatura de chama necessária para as temperaturas mais altas de 1000 graus C a 1200 graus C. Portanto, o gás de alto-forno para os fogões é normalmente enriquecido pela adição de um combustível de poder calorífico muito maior, como o gás de coqueria para obter a alta temperatura de chama. No entanto, muitos dos altos-fornos modernos possuem fogões a quente, que possuem queimadores projetados para o uso apenas do gás de alto-forno.
Os fogões a quente de um alto-forno moderno têm as seguintes características.
- Atingimento de combustão de alta eficiência – Obtenção de combustão de alta eficiência mesmo na operação apenas com gás de alto-forno.
- Menor radiação de calor do corpo do fogão.
- Baixos custos de construção.
- Alta vida útil do fogão -A vida útil esperada de um fogão moderno é de cerca de 40 anos
- Eliminação completa de rachaduras por corrosão sob tensão.
- Baixa concentração de CO não queimado acima da superfície superior dos tijolos xadrez.
A maioria dos altos-fornos está equipada com três estufas a quente, embora em alguns casos existam quatro. Os fogões são altos, estruturas cilíndricas de aço revestidas com isolamento e quase totalmente preenchidas com tijolos de xadrez onde o calor é armazenado e depois transferido para o jato de ar. Cada fogão é tão grande em diâmetro quanto o alto-forno, e a altura da coluna de damas é cerca de 1,5 vezes maior que a altura de trabalho do alto-forno. Nos altos-fornos modernos, a relação do tamanho do fogão com o tamanho do forno é ainda maior. A título de exemplo, um alto-forno novo típico tem diâmetro interno de 9,75 m e altura de trabalho de 25,9 m, e está equipado com três estufas, cada uma com diâmetro interno de 10,36 m e altura de 40 m.
A Fig. 1 mostra as vistas típicas em corte transversal de um fogão convencional de duas passagens. Como se vê na figura, a câmara de combustão de formato oval ocupa cerca de 10% da área total da seção transversal do recuperador. Estende-se da parte inferior do fogão até cerca de 4 m do topo da cúpula do fogão. Uma robusta parede peitoral de tijolos separa a câmara de combustão da balança da salamandra, que é preenchida com tijolos de xadrez apoiados em uma grade de aço sustentada por colunas de aço.
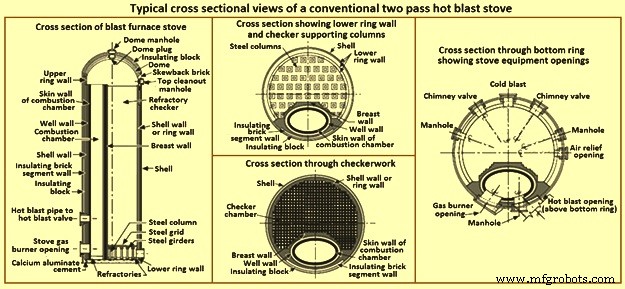
Fig 1 Vista transversal típica de um fogão convencional a quente
Há um revestimento isolante apenas dentro do invólucro de aço. Isso normalmente é muito espesso no lado próximo à câmara de combustão. A câmara de combustão é completamente cercada por uma parede de tijolos, que é revestida com tijolos refratários super resistentes contendo 50% a 60% de alumina. Para temperaturas de jateamento muito altas, superiores a 1200 graus C, toda a câmara de combustão e a cúpula são revestidas com este tipo de tijolo. Além disso, os 8 m a 10 m superiores de damas são normalmente de tijolos super resistentes.
No entanto, para fornos mais novos para os fogões. os refratários de sílica são o material de escolha para melhorar a estabilidade devido à eliminação dos movimentos de expansão na estrutura superior durante a operação. Os refratários de sílica têm uma vantagem adicional sobre os refratários de alumina, pois são resistentes ao acúmulo de poeira. Por esse motivo, normalmente são instaladas sete camadas de sílica no topo do poço do verificador, em fogões à base de alumina.
Na montagem do revestimento da cúpula, são usados tijolos em arco e é fornecido um espaço entre o tijolo e a cúpula para permitir a expansão da parede do anel a partir da qual é suportado. Em alguns fogões, há um deslocamento na estrutura de aço na parte superior da parede do anel para que o tijolo da cúpula possa ser suportado independentemente.
As cúpulas hemisféricas tradicionais, embora de forma simples, têm uma instabilidade natural com tendência para a parte superior da cúpula desmoronar primeiro. Assim, alguns altos-fornos têm uma cúpula em forma de catenária invertida. Esta cúpula tem uma forma estaticamente equilibrada e pode ser construída com um mínimo de tijolos de formas especiais. Como os refratários de cúpula em cogumelo também se expandem e se contraem, uma construção de suporte articulado permite esses movimentos, sem exercer qualquer força sobre a estrutura.
Com as melhores instalações de limpeza de gás disponíveis atualmente, é possível usar verificadores com aberturas de chaminé menores sem qualquer perigo de entupimento das chaminés com sujeira. Com chaminés menores, as taxas de transferência de calor são melhores porque a proporção da superfície de aquecimento para o peso do verificador é grande e mais peso do verificador é instalado no espaço disponível. No entanto, com as aberturas de chaminé menores, tornou-se muito importante colocar os damas corretamente para que as chaminés se encaixem perfeitamente. As chaminés desalinhadas aumentam significativamente a queda de pressão através das estufas e impedem o uso eficaz de toda a capacidade de armazenamento de calor.
O queimador do fogão do alto-forno está localizado próximo ao fundo da câmara de combustão. Na maioria dos fogões de jacto quente, os queimadores são externos à câmara de combustão. Existe uma válvula de corte do queimador entre o queimador e a estufa que é fechada para isolar o queimador quando a estufa está em chamas, mas aberta quando a estufa está a acender. O gás e o ar de combustão são parcialmente misturados no queimador metálico, mas, devido à sua alta velocidade através do queimador, a ignição real provavelmente não ocorre até dentro do fogão. A mistura de gás e ar colide com a parede alvo diretamente oposta à porta do queimador e, em seguida, faz uma curva de 90 graus.
A combustão continua enquanto o gás sobe pela câmara de combustão. Quando um recuperador de calor deve ser aquecido a partir da condição fria, normalmente é usado um ignitor para iniciar a combustão, mas, durante a operação normal, o calor residual na parede alvo é suficiente para causar ignição.
Em vários fogões modernos de sopro quente, são usados queimadores de cerâmica. Esses queimadores, com sua câmara de mistura, são instalados dentro da câmara de combustão e a queima é ascendente no sentido vertical em vez de no sentido horizontal como no queimador metálico convencional. Com este tipo de queimador são necessárias válvulas de corte tanto na conduta de gás como na conduta de ar de combustão. Estas válvulas são capazes de suportar a força da pressão de explosão. Os queimadores cerâmicos têm alguns benefícios devido às suas características especiais de design.
A porta através da qual o ar quente sai do fogão está localizada na lateral da câmara de combustão, geralmente 4 m a 7 m acima do queimador. Entre a salamandra e o jacto principal está localizada uma válvula de jacto quente refrigerada a água que evita que o ar de alta pressão do canal principal entre no recuperador durante o processo de aquecimento. A válvula de jacto de calor está normalmente localizada a uma curta distância da salamandra para reduzir a quantidade de radiação que recebe dos gases de combustão. Em várias oficinas de alto-forno, o ar frio de mistura que é usado para controlar a temperatura do sopro quente é misturado com o ar quente do fogão no lado do fogão da válvula. Isto é para evitar que a válvula fique exposta ao ar na temperatura máxima obtida na cúpula da estufa. Alguns altos-fornos têm uma única abertura central do misturador de jateamento frio que está localizada no alto-forno principal entre o fogão mais próximo e o próprio forno.
O sistema central tem a vantagem de menos ciclos térmicos do jacto principal de calor com os sistemas de temperatura mais elevada. A maioria das válvulas de jateamento quente são do tipo gate ou cogumelo e têm 1,2 m a 2,0 m de diâmetro.
O reaquecimento do fogão requer instrumentação na área da cúpula, no refratário do verificador e na área de saída de gases residuais no mínimo. Existe uma abertura na cúpula da salamandra a quente através da qual normalmente é inserido um termopar ou um detector de temperatura do tipo radiação. Este instrumento serve para controlar a quantidade de gás e ar durante o processo de queima. Os instrumentos de monitoramento de temperatura na cúpula, verificadores e área de gás residual também são usados para proteger os refratários de uma condição de superaquecimento.
Na câmara plenum abaixo da grade que suporta as damas, existem aberturas para a chaminé e para o jato frio principal. Geralmente, existem duas válvulas de chaminé, com dimensões que variam de 1,5 m a 2,0 m de diâmetro, que são abertas durante o aquecimento da estufa para que os produtos da combustão sejam levados para a chaminé da estufa. Quando a estufa está em alta (aquecendo o ar de explosão), as válvulas da chaminé estão fechadas. As sedes da válvula são dispostas de modo que, quando a estufa estiver em alta, a pressão na estufa mantenha as sedes juntas para evitar vazamentos. Quando o recuperador de calor deve ser retirado e colocado em aquecimento, existe uma válvula de descarga que é aberta para aliviar a pressão. Devido à necessidade de despressurizar a estufa rapidamente, o ar deve sair a uma velocidade muito alta. Consequentemente, as válvulas de descarga são equipadas com silenciadores para manter o nível de ruído dentro dos limites toleráveis.
A válvula de sopro frio é do tipo que é mantida fechada pela pressão na tubulação principal de sopro frio. Antes que esta válvula possa ser aberta, as pequenas portas no disco da válvula são abertas para pressurizar a estufa e equalizar a pressão em cada lado da válvula.
Em vários altos-fornos modernos, as estufas são equipadas com câmaras de combustão completamente externas à carcaça da estufa. Estes fogões têm queimadores metálicos externos situados perto do topo do fogão.
A vantagem deste design é que todo o revestimento do fogão pode ser preenchido com damas. Além disso, o padrão térmico na salamandra é muito mais simétrico e há muito menos tensões que tendem a distorcer e romper a alvenaria. No entanto, tem havido muitos problemas induzidos por estresse que causaram rupturas na estrutura de aço da seção de junção entre a câmara de combustão e o fogão. Como resultado, são necessários reparos freqüentes na estrutura de aço neste local.
Rede aérea
Entre as estufas de alta temperatura e o soprador do alto-forno está a tubulação de ar frio. É sem revestimento porque a temperatura do jato frio é geralmente de 150°C a 250°C, que é a temperatura resultante do calor de compressão no soprador. Na extremidade do fogão principal estão as válvulas de sopro de frio para os fogões e a linha de misturadores equipada com uma válvula borboleta. Para manter uma temperatura constante de sopro quente para o alto-forno, um termopar na tubulação principal de sopro quente controla esta válvula borboleta na linha do misturador e proporciona a quantidade de ar entregue ao fogão e a quantidade que o desvia.
Quando um fogão aquecido começa a explodir, a temperatura do ar aquecido é muito mais alta do que a temperatura de explosão quente desejada, de modo que uma parte significativa do ar deve contornar o fogão. À medida que o calor é removido do fogão e a temperatura diminui, a válvula borboleta da linha do misturador é gradualmente fechada e força mais ar através do fogão. Em alguns sistemas de troca automática de estufas, a posição da válvula reguladora é utilizada como sinal que inicia uma troca de estufas.
A tubulação de ar frio também é equipada com uma válvula de snort, geralmente localizada próxima ao alto-forno, que é aberta quando é necessário diminuir rapidamente a pressão de sopro. Isso descarrega o ar frio de sopro para a atmosfera e mantém uma pressão positiva na linha de sopro frio para que o gás do forno não possa voltar para o soprador. Devido à rápida descarga de ar quando a válvula snort é aberta, geralmente também é equipada com um silenciador.
Para gerar o ar de sopro, muitos altos-fornos são equipados com turbo-ventiladores centrífugos providos de três ou quatro estágios. Para altos-fornos muito grandes, geralmente são fornecidos dois sopradores que operam em paralelo. No entanto, com altos-fornos muito grandes, um soprador axial pode ser usado de forma mais eficiente.
Nas usinas, onde o jateamento é enriquecido com oxigênio, o oxigênio é normalmente adicionado à pressão atmosférica na entrada do turbo-ventilador ou pode ser adicionado sob pressão na tubulação principal do jateamento frio. A umidade é adicionada no jateamento frio principal quando é necessária para o controle de umidade do jateamento.
O maçarico, que conecta o sistema de jato quente à ventaneira, se encaixa em um assento esférico usinado na base da ventaneira. O resfriador de ventaneira e a ventaneira são resfriados a água. Em altos-fornos modernos com temperaturas de sopro a quente de 1000 graus C a 1200 graus C, as passagens de água do corpo da ventaneira são projetadas para manter a velocidade da água acima de 20 m/s e as passagens de água do nariz da ventaneira são projetadas para manter a velocidade da água acima de 27,5 m /seg para melhorar a taxa de transferência de calor. Normalmente, o nariz do maçarico também é resfriado a água, embora nos altos-fornos mais antigos isso não fosse feito. A lança auxiliar de injeção de combustível entra pela parede do maçarico e geralmente descarrega o combustível ligeiramente fora da linha central e cerca de 50 mm atrás do nariz do maçarico. Com o uso do carvão pulverizado como combustível da ventaneira, a colocação da lança de injeção é mais crítica para evitar o impacto no interior da ventaneira e para uma melhor combustão do carvão pulverizado.
A zarabatana é mantida firmemente contra a ventaneira por tensão na haste do freio, que conecta a coronha da ventaneira à jaqueta da lareira. A mola do freio na extremidade da haste do freio permite movimento limitado à medida que o maçarico se expande e se contrai com as mudanças na temperatura do jato quente. O maçarico em si é um tubo de liga de aço revestido com material refratário para evitar que o metal fique muito quente.
Na parte de trás da ventaneira, na linha central do maçarico e da ventaneira, há uma pequena abertura através da qual uma haste pode ser inserida para limpar o material do maçarico. A abertura é fechada por uma tampa que pode ser aberta quando necessário, mas é à prova de gás quando fechada. Nesta tampa, chamada de tampa de ventaneira, há uma mira de vidro coberta que permite ao operador inspecionar o interior do forno diretamente na frente da ventaneira. A parte superior da coronha é conectada por uma junta giratória ao bocal revestido de refratário do pescoço de ganso ao qual é fixada por olhais e chaves que se encaixam nos assentos das barras suspensas. Cada pescoço de ganso, por sua vez, é conectado por flanges e parafusos a um gargalo que se estende radialmente a partir do diâmetro interno do tubo de agitação. O tubo de agitação é um tubo grande, circular, revestido de refratário e isolado que circunda a fornalha acima do nível da manta e distribui o jato quente da tubulação principal de jato quente para cada conexão da ventaneira.
Operação do fogão
Atualmente, com o uso de cargas bem preparadas e bom controle de distribuição de cargas, a operação dos altos-fornos é muito mais uniforme. Portanto, os altos-fornos são normalmente operados muito perto da temperatura máxima de sopro quente que os fogões podem manter ou que os materiais de carga específicos podem aceitar sem causar fusão prematura e movimento inadequado da carga. Com temperaturas de sopro a quente mais altas, a operação do alto-forno é mais eficiente porque uma porcentagem maior do calor consumido é fornecida pelo calor sensível do sopro a quente e menos combustível é necessário no alto-forno. Na operação do sistema de sopro a quente, o trabalho cerâmico dos fogões é aquecido pela combustão do gás de alto-forno às vezes complementado por gás de coqueria, e então o ar dos sopradores passa pelos fogões e é aquecido pelo gás quente trabalho do verificador. No ciclo de aquecimento, os fogões são acesos até que a temperatura dos gases de saída nas válvulas de chaminé atinja uma temperatura máxima estabelecida de cerca de 400 graus C a 450 graus C, ao mesmo tempo em que se toma cuidado para não superaquecer as cúpulas do fogão. Durante o ciclo de aquecimento, a temperatura na cúpula da estufa é controlada para que não ultrapasse um máximo, determinado principalmente pelo tipo de material refratário utilizado para o revestimento da cúpula. Se a temperatura da cúpula atingir esse máximo antes que a temperatura da chaminé atinja seu máximo, o excesso de ar é adicionado através do queimador para manter a temperatura da chama baixa e evitar que a cúpula seja superaquecida enquanto a queima continua até que a temperatura do gás da chaminé atinja seu limite. No entanto, se a temperatura da cúpula não aumentar rapidamente o suficiente para atingir sua temperatura máxima permitida no momento em que a temperatura do gás de chaminé atingir seu máximo, o gás do alto-forno geralmente é enriquecido com um combustível de maior poder calorífico para obter uma taxa de aquecimento mais rápida.
Após o aquecimento do fogão, ele está pronto para ser colocado em chamas. Isso é feito primeiro fechando o gás e o suprimento de ar para o queimador e, em seguida, fechando a válvula de fechamento do queimador e as válvulas da chaminé. A válvula de sopro frio é então aberta de tal forma que o ar que entra na estufa a leve a uma pressão igual à pressão de sopro sem reduzir excessivamente a pressão de sopro. Em algumas das modernas instalações de alto-forno, os controles do soprador são trocados de controle de volume constante para controle de pressão constante durante uma troca de fogão. Em tal sistema, o soprador acelera para que o fogão possa ser enchido e pressurizado rapidamente sem causar uma diminuição detectável na pressão de jateamento.
Após o enchimento da estufa, a válvula misturadora (que controla a quantidade de ar frio que é desviada ao redor da estufa para ser misturada com o ar muito quente da estufa para produzir a temperatura desejada de sopro quente) é ajustada aproximadamente na abertura correta. A válvula de jacto de calor é então aberta para colocar a estufa em funcionamento e, uma vez que a salamandra está em funcionamento, o controlador de temperatura de jacto de calor ajusta automaticamente a abertura da válvula misturadora para manter a temperatura de jacto de calor desejada.
A estufa de jacto quente após a sua utilização é então retirada do jacto fechando primeiro a válvula de jacto frio e depois a válvula de jacto quente. A válvula de descarga é então aberta para despressurizar a estufa e, após a despressurização, as válvulas da chaminé são abertas e a válvula de descarga é fechada. Em seguida, a válvula de fechamento do queimador é aberta e o suprimento de ar para o queimador é ligado. Finalmente, a válvula de corte de gás é aberta para obter a vazão de gás desejada.
Nas modernas instalações de alto-forno, as válvulas do fogão são motorizadas e a troca de válvulas é automatizada, de modo que apenas cerca de três minutos são necessários para a troca do fogão. Com o tempo de troca mais curto, o tempo de aquecimento pode ser aumentado para que temperaturas mais altas de jateamento quente possam ser usadas e maior eficiência possa ser obtida. O ciclo de troca automática da estufa pode ser iniciado por meio do toque de um botão quando a troca for necessária ou por um sinal eletrônico totalmente automático. Este sinal pode ser baseado na extensão da abertura da válvula misturadora (como, por exemplo, quando a válvula misturadora está 85% fechada), na temperatura da cúpula ou estritamente em um ciclo de tempo.
Normalmente, os altos-fornos são equipados com três estufas a quente, e cada fogão é mantido aceso por cerca de uma hora. Assim, a quantidade de calor que é extraída da estufa enquanto ela está em chamas deve ser colocada de volta na estufa no período de aquecimento que é simplesmente o dobro do tempo de queima menos o dobro do tempo de troca da estufa. Em alguns fornos, há quatro fogões. Com o fogão extra, a taxa de queima não precisa ser tão grande porque o ciclo de aquecimento é três vezes o ciclo de queima menos o dobro do tempo de troca do fogão. Outra vantagem do fogão extra é que se houver algum problema com o equipamento do fogão, os fogões podem ser consertados um de cada vez sem afetar significativamente o funcionamento do forno. A Fig. 2 mostra um layout típico com três fogões de sopro quente.
Fig 2 Layout típico com três fogões a quente
Processo de manufatura
- Balão de ar quente
- Geração e uso de gás de alto-forno
- Geração e uso de gás de forno de coque
- Produtividade do Alto Forno e os Parâmetros Influenciadores
- Operação de alto-forno e escória de alta alumina
- Turbina a Vapor e Geração de Energia
- Casa de Fundição do Alto Forno e seu Funcionamento
- Prós e contras de uma bomba de calor
- Processo de Laminação a Quente e Frio
- Geração de ar comprimido e nitrogênio na indústria metalúrgica