Entendendo o Processo de Laminação em Laminados de Produtos Longos
Compreendendo o processo de laminação em laminadores de produtos longos
A laminação de aço consiste na passagem do material, geralmente denominado material circulante, entre dois rolos acionados na mesma velocidade periférica em direções opostas (ou seja, um no sentido horário e o segundo no sentido anti-horário) e espaçados de modo que a distância entre eles seja um pouco menor do que a espessura da seção que os insere. Nestas condições, os rolos agarram o material e o entregam com espessura reduzida, comprimento aumentado e provavelmente um pouco aumentado de largura. Este é um dos processos mais utilizados dentre todos os processos metalúrgicos, devido à sua maior produtividade e menor custo operacional. A laminação é capaz de produzir um produto que tem seção transversal constante em todo o seu comprimento. Muitas formas e seções podem ser laminadas pelo processo de laminação de aço.
Os perfis de aço geralmente são laminados em várias passagens, cujo número é determinado pela relação entre o material de entrada inicial e a seção transversal final do produto acabado. A área da seção transversal é reduzida em cada passada e forma e o tamanho do estoque se aproxima gradualmente do perfil desejado.
A laminação é responsável por cerca de 90% de todos os materiais produzidos pelo processo de usinagem de metais. Foi desenvolvido pela primeira vez no final de 1500. A laminação a quente é realizada em temperatura elevada acima da temperatura de recristalização. Durante esta fase, a estrutura de granulação grossa, quebradiça e porosa do aço fundido continuamente é quebrada em uma estrutura forjada com tamanho de grão mais fino e propriedades melhoradas.
Laminador de produtos longos composto por equipamentos para reaquecimento, laminação e resfriamento. Os principais objetivos da etapa de laminação são reduzir a seção transversal do material de entrada e produzir o perfil da seção planejada, propriedades mecânicas e microestrutura do produto.
Os principais parâmetros nas três etapas do processamento do moinho são os seguintes.
- Reaquecimento – O material de entrada geralmente o tarugo é aquecido no forno de reaquecimento até a temperatura de laminação. Os parâmetros importantes são taxa de aquecimento, tempo de aquecimento e temperatura de reaquecimento.
- Laminação – Os parâmetros importantes para a laminação no grupo de desbaste, intermediário e acabamento de bancadas no laminador são temperatura, porcentagem de redução de área, tempo entre passes e taxa de deformação.
- Resfriamento – Os principais parâmetros após o término da laminação durante o resfriamento do produto laminado são a temperatura inicial, a taxa de resfriamento e a temperatura final.
Na fabricação de produtos longos, é comum o uso de uma série de carrinhos de laminação em conjunto para obter altas taxas de produção. Os estandes são agrupados em etapas de desbaste, intermediária e de acabamento. Temperatura típica, velocidade, tempo entre suportes (tempo entre cada suporte), deformação real e faixas de taxa de deformação em cada estágio são mostrados na guia 1. Como a área da seção transversal é reduzida progressivamente em cada conjunto de rolos, o estoque se move em diferentes velocidades em cada estágio do laminador. Um laminador de fio-máquina, por exemplo, reduz gradualmente a área da seção transversal de um tarugo inicial (por exemplo, 150 mm quadrados, 10-12 metros de comprimento) até uma haste acabada (tão pequena quanto 5,0 mm de diâmetro, 1,93 km de comprimento). ) em altas velocidades de acabamento (até 120 m/seg).
Guia 1 Parâmetros típicos em estágios de laminação | ||||
Unidade | Desbaste | Intermediário | Finalizando | |
Intervalo de temperatura | Grau C | 1000-1100 | 950-1050 | 850-950 |
Intervalo de velocidade | m/seg | 0,1-1 | 1-10 | 10-120 |
Intervalo de tempo entre intervalos | Milisegundo | 1600-10300 | 1000-1300 | 5-60 |
Intervalo de tensão real | 0,20-0,40 | 0,30-0,40 | 0,15-0,50 | |
Intervalo da taxa de deformação | por segundo | 0,90-10 | 10-130 | 190-2000 |
A qualidade dimensional final do produto laminado é determinada pelas bancadas de laminação dentro do laminador de acabamento. A precisão dimensional no produto final depende de muitos fatores, incluindo as dimensões iniciais do estoque, sequência de passagem do rolo, temperatura, microestrutura, qualidade da superfície do rolo, rigidez do rolo e do suporte e a condição de atrito do rolo/estoque.
Com relação ao material aço aço, o desenvolvimento da microestrutura durante a laminação é complexo e envolve a recristalização estática e dinâmica da austenita. Do ponto de vista prático, a distribuição granulométrica da austenita no produto laminado é de suma importância no controle das propriedades mecânicas. Nos estágios de desbaste e intermediário da laminação, o estoque está se movendo lentamente entre as bancadas, de modo que o material tem a chance de se “normalizar” como resultado da recuperação e recristalização. Durante a fase de laminação de acabamento, o estoque está trafegando em alta velocidade entre estandes pouco espaçados e, consequentemente, não tem tempo adequado para se normalizar. Essa falta de normalização pode ter um efeito significativo na microestrutura final e nas propriedades mecânicas do produto laminado.
Uma vez que a composição química é fixada para graus específicos de aço, os requisitos para um determinado produto que pode ser controlado no laminador consistem em geometria, propriedades mecânicas e microestrutura. As características do produto que são controladas são a forma geométrica e a tolerância. Estes são determinados a partir do perfil da seção do produto acabado. As propriedades mecânicas incluem rendimento e resistência à tração final, % de redução na área (ductilidade) e dureza. As características da microestrutura incluem tamanho de grão, distribuição de grão, composição de fase e distribuição de fase.
O rolamento envolve fenômenos macroscópicos e microscópicos (Fig. 1). Os fenômenos macroscópicos podem ser amplamente classificados como (i) fluxo de calor durante a laminação e (ii) deformação sob aplicação da carga de laminação. Os fenômenos macroscópicos incluem os fatores indicados abaixo.
- Condução no material circulante e nos rolos e convecção/radiação para o meio ambiente
- Aquecimento adiabático devido à deformação
- Expansão e contração térmica durante os ciclos de aquecimento e resfriamento.
- Grandes deformações e deslocamentos devido ao fluxo plástico
- Os efeitos da tensão, taxa de deformação e temperatura
- Contato e atrito
O processo no nível microscópico envolve muitos fenômenos físicos complexos associados à nucleação e evolução da microestrutura. Os principais fenômenos microscópicos que são importantes durante o processo de laminação são (i) recristalização da austenita e crescimento de grãos, e (ii) transformação da austenita em ferrita, perlita, bainita e martensita (e/ou outras fases).
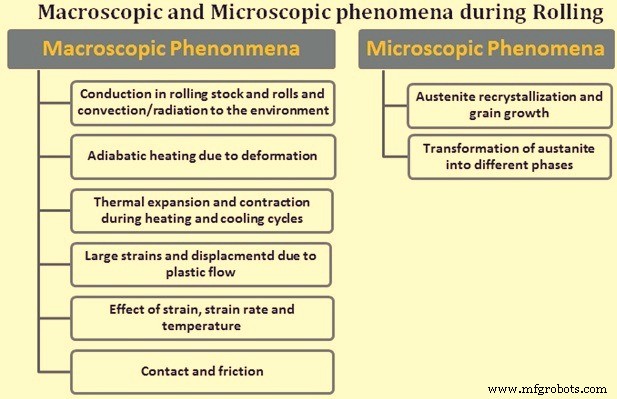
Fig 1 Fenômenos macroscópicos e microscópicos durante o rolamento
O espalhamento e superfícies livres laterais são muito importantes na laminação. O spread é definido como a dimensão do material deformado após a laminação na direção perpendicular à direção de laminação. Mede o aumento da largura do estoque devido à deformação de laminação. A superfície livre lateral é definida como a região da superfície do material que não entra em contato com os cilindros durante o processo de laminação. O perfil de superfície de um estoque deformado depende do espalhamento, do perfil de superfície livre e do alongamento do estoque. Isso significa que a forma final do estoque depende principalmente desses parâmetros. Como a forma final do estoque é muito importante para o produto laminado, esses parâmetros são muito importantes para um projetista de passe de laminação ao projetar um passe de laminação específico para requisitos específicos de formato e tamanho. A precisão no cálculo desses parâmetros é fundamental para satisfazer requisitos geométricos como circularidade (no caso de barras e varões) e tolerância. A circularidade é definida como a diferença entre o diâmetro máximo e o diâmetro mínimo. Tolerância é a diferença permitida nas dimensões máximas/mínimas em relação às dimensões nominais.
A deformação plástica efetiva média é extremamente importante para prever e controlar as propriedades mecânicas do produto laminado após a laminação. suporte durante o processo de laminação. A evolução da microestrutura requer variáveis termomecânicas como deformação plástica efetiva média, taxa de deformação plástica efetiva média e temperatura em cada bancada de laminação. A evolução da temperatura devido à energia mecânica convertida em calor durante o processo de deformação também depende da deformação plástica efetiva média e da taxa de deformação plástica efetiva média. Além disso, a taxa de deformação plástica efetiva média é, por sua vez, uma função da deformação efetiva média e do tempo de processo. Tudo isso sugere que a capacidade de prever a deformação plástica média é essencial para controlar as propriedades mecânicas e a microestrutura do produto laminado.
O cálculo da força do cilindro é importante porque o cálculo do torque e da potência em um laminador é baseado no cálculo da força do cilindro. A previsão precisa da força de rolagem para laminação ranhurada é consideravelmente mais difícil do que prever a geometria do material circulante. Existem essencialmente três problemas, presentes também durante a laminação, mas um tanto fáceis de lidar. Eles são (i) resistência do material à deformação, em função da deformação, taxa de deformação e temperatura, (ii) a capacidade de calcular as distribuições das deformações, taxas de deformação, tensão e temperatura na zona de deformação, e (iii) as condições na interface do metal laminado, ou seja, os coeficientes de atrito e transferências de calor.
Um parâmetro mais importante da laminação de alta velocidade e alta temperatura é o comportamento da tensão de fluxo do tipo de aço em particular. A tensão de escoamento é definida como a tensão de escoamento instantânea ou tensão verdadeira de um aço definida quando o aço começa a sofrer deformação plástica contínua. Os dois principais métodos para obter com precisão a tensão de escoamento de um tipo particular de aço são resultados experimentais diretos e equações constitutivas empíricas. As equações constitutivas empíricas são muitas vezes derivadas da análise de regressão de dados experimentais. Normalmente, essas equações definem a resistência ao fluxo de um material em função da variável considerada importante.
Rolos e design de passe de rolo
Os rolos são as ferramentas do laminador e são os consumíveis mais caros em um laminador. A maneira como os rolos são usados para executar sua função de deformar o aço é, em muitos casos, amplamente determinada pelo projeto do passe do rolo. O objetivo do projeto do passe do rolo é (i) produzir o perfil correto dentro dos limites de tolerância com bom acabamento superficial (livre de defeitos superficiais), (ii) produtividade máxima com o menor custo, (iii) desgaste mínimo do rolo, (iv) fácil trabalhando, e (v) utilização ótima de energia.
A precisão e a velocidade de trabalho e a vida útil do rolo estão relacionadas ao design da passagem do rolo e à escolha do material do rolo. A sequência de laminação de um projeto de passe de rolagem está sujeita às limitações aplicadas pela carga de laminação, a força de rolagem e o torque disponível para laminação. O projeto do passe de rolo também garante que as dimensões físicas e o material do rolo sejam capazes de suportar as cargas mais pesadas que surgem durante a sequência de laminação.
O material do rolo é importante, pois deve ser capaz de suportar cargas que deformam plasticamente o material circulante sem que ele próprio se deforme plasticamente. Na laminagem de aço a quente, este não é um problema difícil e os rolos de ferro ou aço são adequados se forem operados a uma temperatura consideravelmente inferior à do material circulante. A escolha do material do rolo, seja ferro fundido ou aço (fundido ou forjado), depende da função específica que os rolos devem desempenhar e das propriedades importantes, como tenacidade da superfície, resistência a trincas térmicas ou carga de choque ou propriedades de desgaste. A seleção de qualquer rolo específico depende das demandas de produção, do custo inicial e das qualidades específicas exigidas. Os rolos de carboneto de tungstênio são geralmente usados em blocos de acabamento de fio-máquina e em algumas aplicações de laminação de forma. Esses rolos de metal duro requerem água de resfriamento de alta qualidade em uma faixa estreita de pH e dureza limitada.
O material do rolo é importante para estimar as cargas que os rolos devem suportar. Além disso, sugere o tamanho do moinho mais adequado para determinadas gamas de produtos, de modo a garantir uma eficiência razoável no funcionamento do moinho. Talvez um dos fatores mais importantes no que diz respeito à vida útil do rolo sejam as propriedades de desgaste do material do rolo.
Durante a laminação a quente do aço, o calor é transferido para os rolos. Se não for resfriado, o acúmulo de calor causa o aumento da temperatura do rolo para uma temperatura igual à do estoque que está sendo laminado. Nesta fase, o rolo também sofreria deformação plástica. Para remover o calor do rolo, é aplicada água de resfriamento. A dificuldade na remoção do calor do rolo é resultado de dois fatores. O primeiro é chamado de coeficiente de condutividade térmica e o segundo é a interface entre o rolo e o material circulante em relação à água de resfriamento e o rolo. O calor é transferido por condução, convecção e radiação.
Durante o tempo de contato do material rodante no passe, o material rodante a quente aquece o rolo devido à condução durante o tempo de contato com o rolo. Como resultado, o perfil de temperatura na superfície do rolo aumenta quando em contato com o rolo e depois cai à medida que o calor é absorvido pelo corpo do rolo. Isso também significa que o melhor lugar para remover o calor do rolo é imediatamente após a barra deixar o contato com o rolo. A melhor taxa de remoção de calor ocorre quando a diferença de temperatura é maior. Um sistema típico de distribuição de água de resfriamento de rolos consiste em orifícios na guia de distribuição para a aplicação de água o mais próximo possível do ponto em que o material circulante entra em contato com o rolo. Dois tubos de água de meio círculo para cada rolo também fornecem água de resfriamento secundária para garantir que o calor da laminação não penetre no corpo do rolo. A aplicação de água de resfriamento deve ser controlada para que a água não caia no material circulante no ponto de entrada dos rolos. Caso isso aconteça, apenas resfria o material rodante, cria bolsões de vapor entre o rolo e o material rodante, e desperdiça água que poderia ser melhor aproveitada do outro lado do rolo. Para minimizar o desgaste do rolo, a água de resfriamento do rolo deve ser aplicada o mais próximo do ponto em que o material circulante deixa o rolo. As pressões típicas da água de resfriamento são de 2 kg/cm2 a 5 kg/cm2 a uma vazão de cerca de 1,5 litros/mm por minuto. Os melhores sistemas de entrega usam tubos, bicos e cabeçotes de pulverização para obter 'resfriamento suave' em baixa pressão e alto fluxo, não um jato forte que 'salta' a água do rolo.
A degradação da superfície do rolo ocorre principalmente devido ao ciclo térmico do aquecimento e resfriamento da superfície versus o estado relativamente estável da subsuperfície e do material adjacente. Isso cria tensão e compressão locais à medida que o rolo se move por 360 graus de rotação. O objetivo do resfriamento do rolo é minimizar esse ciclo. O objetivo da seleção do material do rolo é usar materiais que possam tolerar esse ciclo sem rachaduras, fissuras ou desgaste prematuro. As rachaduras desenvolvidas na superfície do rolo devem ser removidas, girando para baixo um material considerável do rolo e, no processo, reduzindo o diâmetro do rolo. Isso afeta a vida útil do rolo e aumenta o custo do rolo por tonelada.
É fato que todos os cilindros do moinho eventualmente se deterioram e os passes dos cilindros precisam ser trocados para obter o controle de tamanho e a qualidade da superfície do produto acabado. Quando o diâmetro do rolo reduz para menos do que o diâmetro mínimo exigido pela bancada do moinho após a rotação para baixo, o rolo deve ser descartado.
Configuração da guia de suporte e rolagem
O objetivo do moinho e da configuração da guia do rolo é obter a primeira barra laminada ao trocar de produto, no leito de resfriamento dentro da tolerância, para que seja um produto vendável. Os dados necessários para executar esta função geralmente são fornecidos em duas formas. Um é fornecido pelos construtores do moinho e fornece informações sobre rolos, peças de guia e outros equipamentos que precisam ser alterados em relação à configuração anterior. Ele também inclui configurações de folga, ajustes de guia e quaisquer instruções especiais.
As folhas de configuração do piso do moinho e do púlpito também contêm configurações de altura do loop, rpm do motor (rotações por minuto), velocidade de saída, taxa de produção, fatores R, informações de configuração de cisalhamento e outras informações pertinentes. Para permitir a inicialização mais rápida possível, as informações retidas devem refletir as condições na inicialização. Ou seja, se as rolagens são sempre vestidas em troca, os R-Factors devem ser o que foram os últimos sucessos nas novas rolagens. Os dados coletados no final de uma laminação com rolos usados não serão precisos ao rolar em rolos novos.
Controle de tensão
Em um moinho contínuo, a velocidade correspondente ao suporte para atingir um fluxo de massa constante através do moinho garante uma baixa taxa de pedregulho e menos defeitos. Alta tensão pode esticar reduzir a seção transversal da barra tornando o controle de forma muito difícil. No extremo, a tensão pode separar a barra, criando um paralelepípedo. A compressão da barra entre os suportes pode criar defeitos de criação de vibração ou, no extremo, causar o crescimento do laço, levando a um paralelepípedo.
Usando o diâmetro de trabalho dos rolos, o rpm do rolo (rotações por minuto) é combinado com a velocidade da barra através do moinho. À medida que os rolos se desgastam e a extensão da barra no passe muda, a rotação dos suportes precisa ser ajustada à medida que a área da barra muda. A maioria dos sistemas de controle modernos modifica o R-Factor conforme isso ocorre.
A velocidade da barra em cada estande é calculada usando a taxa de tonelagem de produção para o produto como uma constante de moinho.
Os valores de entrada para definir as velocidades do motor do moinho são taxa de produção, diâmetros do colar do cilindro e folgas do cilindro, áreas e larguras da barra e relações de transmissão. As classificações de velocidade do motor são normalmente verificadas em relação às velocidades calculadas.
Utilização do moinho
A utilização do moinho é uma medida da porcentagem de tempo que o moinho está laminando aço. A medida mais verdadeira de desempenho é uma porcentagem do tempo do calendário. Os fatores que influenciam a utilização são interrupções de manutenção, interrupções de feriados programadas e não programadas, tempo de inatividade para limpeza de pedregulhos, trocas de rolos e passagens, folga excessiva do tarugo e outros fatores que criam tempo quando um tarugo não está na usina. Bons números para moinhos de barras e barras são de 90% a 93%, para moinhos estruturais, os bons números de utilização do moinho são de 75% a 78%.
Se uma usina rola 80% do ano civil, isso é 365 x 24 x 0,80 =7008 horas. Se a usina lamina 800.000 toneladas por ano, ela opera a uma taxa média de produção de 114,16 toneladas/hora. Se a utilização puder ser melhorada em 1%, as horas rolantes disponíveis são 365 x 24 x 0,81 =7096,6, criando 87,6 horas rolantes extras. A 114,16 toneladas/hora, 10.000 toneladas adicionais podem ser laminadas.
O excesso de folga do tarugo pode ser uma perda não contabilizada de tempo de laminação. Se uma usina lamina 800.000 toneladas por ano usando tarugos de 1,25 tonelada de peso, ela lamina 640.000 tarugos por ano. São 639.999 lacunas de tarugos. Se o intervalo médio do tarugo for de 5 segundos, ou seja (5 segundos x 639.999)/3.600 segundos/hora =888,89 horas de intervalo do tarugo. Se a folga média do tarugo for reduzida em 0,5 segundo, isso seria (4,5 s x 639.999)/3.600 s/hora =800 horas de folga do tarugo, criando 88,89 horas adicionais de tempo de rolagem. Em 114,16 toneladas/hora, são 10.147 toneladas adicionais de aço laminado.
Rendimento
O rendimento é a medida da perda de produção desde a carga do forno até o produto acabado empacotado, empilhado ou enrolado. Os fatores que influenciam o rendimento são a perda de escala, perda de colheita, perda de paralelepípedos e qualquer outro fator que reduza o peso do produto acabado. Quando o tarugo é carregado no forno de reaquecimento, ele é pesado ou considerado como tendo um peso nominal baseado em sua seção transversal e teor. À medida que avança pelo forno, forma-se uma incrustação que é removida no desincrustante ou cai durante a laminação. Isso pode atingir cerca de 1% a 1,2% do peso carregado. As tesouras que cortam a extremidade frontal malformada da barra à medida que ela avança pelo moinho podem remover até 0,3 ma 0,4 m de material em cada corte. Depois de dividir a barra no leito de resfriamento, uma tesoura ou serra a frio corta a barra em comprimentos vendáveis, limpando as variações de comprimento. Fresas estruturais geralmente fazem um corte de serra adicional em material empilhado e agrupado. Todo o material removido contribui para a perda de rendimento. Bons números de rendimento estão em torno de 97% a 98% para laminadores de barras e vergalhões, e 92% a 94% para laminadores estruturais. Se o produto for laminado com tolerância negativa e vendido com base no peso nominal, o rendimento se torna muito maior. Por esse motivo, alguns dos laminadores de vergalhões que laminam com tolerância negativa e vendem vergalhões com base no peso nominal estão relatando um rendimento do produto acabado de 100% ou mais, embora o rendimento nominal do laminador seja normal de 97%.
Taxa de paralelepípedos
A taxa de paralelepípedos é a medida da porcentagem de tarugos carregados perdidos para os paralelepípedos. Se a taxa de paralelepípedos for 0,75%, então 0,75% de todos os tarugos cobrados serão perdidos para os paralelepípedos. Se uma usina lamina 640.000 tarugos por ano, isso significa que 4.800 tarugos são perdidos. A 1,25 toneladas por tarugo, a perda em toneladas é de 6.000 toneladas. Portanto, é necessário que todas as tentativas sejam feitas no moinho para reduzir a taxa de pavimentação.
Processo de manufatura
- Compreendendo o Processo de Fabricação do Eixo
- Entendendo o processo de fundição de minério de ferro
- Entendendo o processo de fundição em areia
- Entendendo o processo de soldagem por fricção
- Entendendo o processo de soldagem a gás
- Entendendo o processo de soldagem
- Processo de Laminação a Quente e Frio
- Entendendo o processo de extrusão
- Entendendo o processo de usinagem não tradicional
- Entendendo o processo de usinagem e a máquina-ferramenta