Noções básicas de laminação de aço
Noções básicas de laminação de aço
O aço líquido é geralmente fundido em máquinas de lingotamento contínuo na forma de tarugos, blocos ou placas. Em algumas fábricas, também está sendo moldado em máquinas de lingotamento contínuo na forma de placas finas ou seções de osso de cachorro. Essas formas são processadas por laminação a quente, passando-as por rolos cilíndricos rotativos lisos ou ranhurados para produzir chapas, chapas, varetas, seções estruturais, tubos etc.
O processo de laminação é uma das operações industriais de conformação de metais mais importantes e amplamente utilizadas. Proporciona alta produção e controle rigoroso do produto final. Foi desenvolvido no final de 1500. É responsável por 90% de todos os metais produzidos por processos de usinagem de metais.
A laminação de aço é um processo de conformação de metal no qual o aço é passado através de um par de rolos rotativos para deformação plástica do aço. A deformação plástica é causada pelas forças de compressão aplicadas através dos rolos rotativos. Altas tensões de compressão são resultado do atrito entre os rolos e a superfície do estoque de aço. O material de aço fica espremido entre o par de rolos, como resultado, a espessura é reduzida e o comprimento aumentado. A laminação é classificada de acordo com a temperatura do aço laminado. Se a temperatura do aço estiver acima de sua temperatura de recristalização, então o processo é denominado como laminação a quente. Se a temperatura do aço estiver abaixo de sua temperatura de recristalização, o processo é denominado como laminação a frio.
Os rolos rodam em rolamentos de pescoço maciço montados em carcaças de enorme resistência e acionados por potentes motores elétricos. Estes são conhecidos como estandes de moinho. Um suporte de laminação contém dois ou mais rolos para deformação plástica de aço entre rolos rotativos. Consiste basicamente em (i) rolos, (ii) mancais, (iii) uma carcaça para conter essas peças, (iv) uma caixa de engrenagens, (v) um acionamento (motor) para aplicação de potência aos rolos, (vi) velocidade dispositivos de controle de velocidade e (vii) sistemas hidráulicos. O suporte do laminador requer uma construção muito rígida e motores grandes para fornecer energia suficiente. Existem vários tipos de suportes para laminadores, conforme indicado abaixo.
- Two-high stand – É o tipo básico de stand de laminação em que são usados dois rolos opostos. O suporte possui rolos não reversíveis girando na mesma direção. Portanto, a peça de trabalho não pode ser alimentada do outro lado. O suporte de duas alturas pode ser um suporte horizontal ou vertical. O suporte horizontal tem os dois rolos na horizontal, enquanto o suporte vertical tem os dois rolos na vertical.
- Suporte de pulôver com duas alturas – O material de aço rolante é devolvido à entrada para redução adicional.
- Suporte de duas alturas, reversível – O trabalho pode ser passado para frente e para trás através dos rolos invertendo o sentido de rotação. Essas usinas aumentam a produtividade.
- Base de três alturas – Consiste em três rolos. Os rolos superior e inferior são acionados enquanto o rolo do meio gira por fricção. A primeira laminação ocorre em uma direção entre o par de rolos inferior e o do meio. Em seguida, o trabalho é invertido na direção e alimentado através do par de rolos do meio e do topo. Isso melhora a produtividade.
- Estante de quatro alturas – Possui rolos de pequeno diâmetro (menos resistência e rigidez) são suportados por rolos de apoio de maior diâmetro. O poder de rolamento é diretamente proporcional ao diâmetro do rolo. Rolos de diâmetro menor podem, portanto, reduzir a entrada de energia. A resistência dos rolos de pequeno diâmetro é baixa. Portanto, os rolos podem dobrar. Como resultado, rolos de apoio de diâmetro maior são usados para suportar os rolos menores. Seções finas podem ser enroladas usando rolos de diâmetro menor.
- Estande universal – Este estande possui dois rolos horizontais e dois rolos verticais. Os rolos verticais são usados para controlar a largura do trabalho simultaneamente.
- Cluster mill ou suporte Sendzimir – Neste suporte de laminador, cada um dos cilindros de trabalho é suportado por dois cilindros de apoio. O moinho cluster e o moinho Sendzimir são usados para laminar tiras finas de materiais e folhas de alta resistência [0,0025 mm de espessura]. O rolo de trabalho nesses moinhos pode ter até 6 mm de diâmetro – feito de carboneto de tungstênio.
- Moinho planetário – Consiste em um par de rolos de apoio pesados cercados por um grande número de rolos planetários. Cada rolo planetário dá uma redução quase constante à laje à medida que varre um caminho circular entre os rolos de apoio e a laje. À medida que cada par de rolos planetários deixa de ter contato com a peça de trabalho, outro par de rolos faz contato e repete essa redução. A redução total é a soma de uma série de pequenas reduções por cada par de rolos. Portanto, o moinho planetário pode reduzir a quente uma placa diretamente para tira em uma passagem pelo moinho. A operação requer rolos de alimentação para introduzir a placa na usina e um par de rolos de aplainamento na saída para melhorar o acabamento da superfície.
Um laminador contínuo possui uma série de carrinhos de laminação dispostos em sucessão para aumentar a produtividade. O estoque de aço se move em diferentes velocidades em cada estande da usina.
Em um sentido mais amplo, um laminador é um sistema automático ou linha de carrinhos de laminação juntamente com uma série de equipamentos que executam operações de laminação e auxiliares:transporte do tarugo/bloom/laje original do estoque para os fornos de aquecimento e o laminador rolos, transferência do material laminado de um suporte de rolos para outro, torneamento ou torção no caso de alguns laminadores, transporte do metal após a laminação, corte, resfriamento do material laminado em leito de resfriamento em alguns laminadores, marcação ou estampagem, rebarbação, embalagem , e transporte para o estoque de produto acabado. Em alguns laminadores (por exemplo, laminador de tiras a quente, laminador de fio-máquina, laminador comercial e laminador a frio), o produto laminado é enrolado em uma bobina ou bobina de enrolamento.
Principalmente, a laminação é feita em alta temperatura, chamada de laminação a quente, devido à exigência de grandes deformações. A laminação a quente resulta em um produto residual livre de tensões. No entanto, o dimensionamento é um problema importante durante a laminação a quente, devido ao qual a precisão dimensional é difícil de manter.
A laminação a frio de aço laminado a quente é importante, devido à alta precisão e falta de escamação de óxido. É realizado abaixo da temperatura de recristalização e introduz encruamento. O material de partida para a chapa de aço laminada a frio é a bobina laminada a quente decapada do laminador de tiras a quente contínuo. A redução total alcançada pela laminação a frio geralmente varia de cerca de 50% a 90%. A redução em cada arquibancada deve ser distribuída uniformemente sem cair muito abaixo da redução máxima para cada passagem. Geralmente, a redução percentual mais baixa ocorre no último passe para permitir um melhor controle da planicidade, calibre e acabamento da superfície.
A laminação é classificada de acordo com a temperatura da peça laminada. Se a temperatura do aço estiver acima de sua temperatura de recristalização, então o processo é denominado como laminação a quente. Para processos de trabalho a quente, grandes deformações podem ser repetidas sucessivamente, pois o aço permanece macio e dúctil. O estoque de aço é submetido a altas tensões de compressão como resultado do atrito entre os rolos e a superfície do aço. A laminação envolve a passagem do material entre dois rolos girando mais ou menos na mesma velocidade periférica, mas em direções opostas, ou seja, no sentido horário e anti-horário. A distância entre eles é espaçada, que é um pouco menor que a altura do estoque de aço que entra neles. Esses rolos podem ser planos ou ranhurados (contornados) para a laminação a quente de varetas ou formas. Nessas condições, os rolos agarram a peça de aço e a entregam, com área de seção transversal reduzida e, portanto, aumentada em comprimento.
A operação inicial de trabalho a quente para a maioria dos produtos de aço é feita no desbaste primário. O objetivo é desmembrar para reduzir a seção transversal do material rodante para posterior acabamento em barras, tiras, chapas ou várias seções laminadas. Os blocos, placas ou tarugos fundidos são aquecidos inicialmente de 1100 graus C a 1300 graus C. Na laminagem a quente de aço, a temperatura na bancada final de acabamento varia de 850 graus C a 900 graus C, e está sempre acima do limite crítico superior temperatura do aço. O aço é espremido entre os rolos até que a espessura e as formas finais sejam alcançadas. Para conseguir isso, os rolos exercem forças de milhares de toneladas.
O layout de um laminador varia, desde um simples laminador de bancada única até várias bancadas posicionadas lado a lado ou em linha. Um mecanismo, comumente chamado de mesa de roletes, direciona a peça de trabalho para os rolos, e outra mesa de roletes para manuseio das peças que emergem do rolo. A mesa na frente dos rolos força o aço contra os rolos que prendem e puxam o aço entre eles. O aço é, assim, reduzido a uma espessura igual à distância entre os rolos, e se os rolos são ranhurados, é moldado de acordo com o desenho da ranhura. A laminação a quente permite que grandes deformações do aço sejam alcançadas com um pequeno número de ciclos de laminação.
A laminação a quente ocorre em várias etapas e tiragem / redução é dada em todas as etapas. O calado final está a uma temperatura acima da temperatura de recristalização ou mudança de fase. Consequentemente, o estoque frio é aquecido a uma temperatura muito mais alta do que a temperatura de recristalização. Portanto, a temperatura final à qual a peça de trabalho depende da quantidade de calado total, do número de etapas em que o calado é fornecido e da composição do estoque de aço.
O objetivo de um laminador é diminuir a espessura do aço com um aumento no comprimento e com pouco aumento na largura. O material no centro do material circulante é restringido na direção ao longo da largura da folha e as restrições de ressaltos de material subformados em cada lado dos rolos impedem a extensão do material circulante na direção da largura. Esta condição é conhecida como deformação plana. O material, portanto, fica mais longo e não mais largo.
Fatores que influenciam a mecânica de rolamento
Os principais fatores que influenciam a mecânica de rolamento são apresentados a seguir.
- O diâmetro dos rolos
- Quantidade de redução em uma passagem
- A espessura inicial do material a ser laminado
- A velocidade de rolamento que decide a taxa de deformação
- As tensões frontais e traseiras
- A natureza do atrito entre os rolos e o aço sendo laminado
- A faixa de temperatura do material de aço e dos rolos
- As propriedades físicas do material de aço que está sendo laminado
- A forma do contorno do rolo da passagem do rolo no qual o material de aço está sendo deformado
- O comportamento do moinho sob carga
- O efeito do tratamento prévio do material resultando em endurecimento por trabalho ou outros efeitos
- A deformação elástica dos rolos sob carga
- A resistência à deformação do metal influenciada pela metalurgia, temperatura e taxa de deformação.
- O estado de anisotropia do material
- A relação de aspecto ou a relação entre a largura do material circulante e a espessura inicial
Os parâmetros acima podem, isoladamente ou em conjunto, em combinações de dois ou mais, gerar parâmetros e fenômenos secundários mais diretamente relacionados e comumente associados ao processo de laminação. A pressão do rolo, torque, trabalho e potência são influenciados por esses fatores. A maioria destes parâmetros são dados abaixo.
- Coeficiente de calado, calado absoluto e calado relativo, que são estabelecidos pelo calado inicial, que são estabelecidos pelas espessuras médias inicial e final do material rodante.
- Deslizamento que se caracteriza pela diferença da velocidade linear do material circulante e a velocidade periférica dos rolos. O ângulo neutro é determinado pelo ponto sem escorregamento.
- O spread é a diferença na largura do material de saída em comparação com o material circulante de entrada.
- O coeficiente de alongamento depende dos valores relativos do calado e do espalhamento.
- Roll bite que é uma função do calado, diâmetro do rolo, coeficiente de atrito e espessura de entrada.
Conceito fundamental de rolamento
O conceito fundamental de laminação de aço é dado abaixo.
- O arco de contato entre os rolos e o aço é parte de um círculo.
- O coeficiente de atrito é constante em teoria, mas na realidade varia ao longo do arco de contato.
- Considera-se que o material de aço se deforma plasticamente durante a laminação.
- O volume de estoque sendo rolado é constante antes e depois da laminação. No entanto, praticamente o volume pode diminuir um pouco devido ao fechamento dos poros.
- Supõe-se que a velocidade dos rolos seja constante.
- O estoque de aço só se estende na direção de laminação e não se estende na largura do material.
- A área da seção transversal normal à direção de rolagem não é distorcida.
Com exceção da laminação a frio com tensão de tira, é o atrito externo, ou seja, o atrito entre a superfície dos cilindros e o material laminado, que é o fator fundamental na redução do material de aço por laminação. É a força que puxa o material entre os rolos e é o que marca a diferença básica entre laminação e trefilação. O atrito afeta muito a magnitude e a distribuição da pressão que atua entre os rolos e o material e, consequentemente, afeta a potência necessária para a redução do material. Ele também controla a quantidade de redução que é possível tomar. Normalmente, quanto maior o coeficiente de atrito, maior é a tiragem possível. Dependendo das condições sob as quais o material de aço se move para a folga do rolo, podem ocorrer as duas situações a seguir.
- O aço é agarrado pelos rolos e puxado para dentro da folga do rolo.
- O aço desliza sobre a superfície do rolo, não é agarrado e o rolamento não ocorre.
A magnitude da força de atrito depende da condição das superfícies em contato e aumenta com o aumento da rugosidade, da velocidade relativa entre os rolos e da pressão exercida pelo rolo.
A seguir estão as estratégias para reduzir a força de rolagem.
- Reduzindo o atrito na interface rolo-peça
- Usando rolos de diâmetro menor para reduzir a área de contato
- Fazer reduções menores por passagem para reduzir a área de contato
- Rolamento em temperaturas elevadas para diminuir a resistência do material
- Aplicando tensões frontais e/ou traseiras ao material laminado
Quando o produto de aço forjado ou fundido é laminado a quente, a estrutura do grão, que é de granulação grossa, torna-se mais fina em tamanho, mas alongada ao longo da direção da laminação. Este tipo de estrutura de grão texturizado causa propriedade direcional [anisotropia] para o produto laminado. Para refinar os grãos, o tratamento térmico é realizado imediatamente após a laminação, o que resulta na recristalização após a laminação.
Tipos de laminadores
Existem diferentes tipos de laminadores. Estes são dados abaixo.
- Laminação contínua
- Laminação reversível
- Laminação transversal – Usa rolos de cunha circulares. A barra aquecida é cortada no comprimento e alimentada transversalmente entre os rolos. Os rolos giram em uma direção no moinho.
- Laminação moldada ou laminadora de seção – Os laminadores moldados são laminadores de barras, laminadores comerciais, laminadores de fio-máquina, laminadores estruturais, laminadores de vigas e laminadores ferroviários.
- Laminação de anéis – Neste laminador, a pré-forma em forma de rosca é colocada entre um rolo interno de giro livre e um rolo externo acionado. O moinho de anel torna a seção mais fina enquanto aumenta o diâmetro do anel.
- Laminação de pó - O pó metálico é introduzido entre os rolos e compactado em uma "faixa verde", que é posteriormente sinterizada e submetida a outros ciclos de trabalho a quente e/ou trabalho a frio e recozimento.
- Laminação e fundição de placas finas – É usado para a produção de tiras a quente. O aço líquido é fundido em placas finas (espessura de 50 mm a 80 mm) que são laminadas no laminador de acabamento do laminador de tiras a quente após equalização de temperatura em um forno.
- Laminação de roscas – Neste laminador, as matrizes são pressionadas contra a superfície do blank cilíndrico. À medida que a peça em bruto rola contra as faces da matriz de alimentação, o material é deslocado para formar as raízes da rosca e o material deslocado flui radialmente para fora para formar a crista da rosca.
Forças e relações geométricas no rolamento
Uma chapa de aço com espessura ho entra nas jogadas no plano de entrada xx com uma velocidade vo . Ele passa pelo espaço de rolagem e sai do plano de saída yy com espessura reduzida hf e a uma velocidade vf . Dado que não há aumento da largura, a compressão vertical do aço se traduz em um alongamento na direção de laminação. Como não há mudança no volume de aço em um determinado ponto por unidade de tempo ao longo do processo, portanto,
bxho xvo =bxhf xvf =bxh xv
Onde b é a largura da folha v é a velocidade em qualquer espessura h intermediário entre ho e hf .
A Fig. 1 mostra a relação geométrica e as forças durante a laminação.
Em apenas um ponto ao longo da superfície de contato entre o rolo e a chapa, duas forças atuam sobre o aço, a saber (i) uma força radial Pr, e (ii) uma força de atrito tangencial F . Entre o plano de entrada (xx ) e o ponto neutro a folha está se movendo mais lentamente do que a superfície do rolo, e a força de atrito tangencial, F , aja na direção (veja a Fig 1) para puxar o aço para dentro do rolo. No lado da saída (aa ) do ponto neutro, a folha se move mais rápido que a superfície do rolo. A direção da força de atrito é então invertida e se opõe à entrega da folha dos rolos.
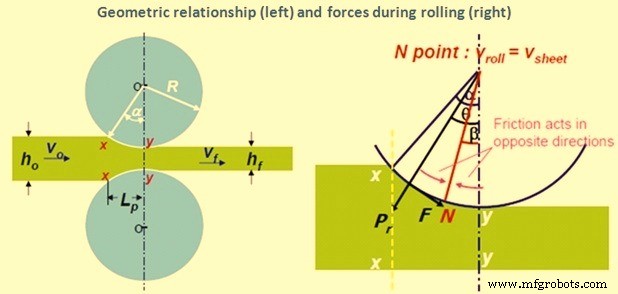
Fig 1 Relação geométrica e forças durante o rolamento
Pontos importantes sobre a rolagem
A seguir estão os pontos salientes na laminação do aço.
- A laminação é o processo de conformação de metal de aço mais amplamente utilizado e sua participação é de aproximadamente 90%
- O material a ser rolado é puxado por meio de fricção na abertura dos dois rolos giratórios
- As forças de compressão aplicadas pelos rolos reduzem a espessura do material ou alteram sua área de seção transversal
- A geometria do produto depende do contorno da folga do rolo
- Os materiais do rolo são ferro fundido, aço fundido e aço forjado devido aos requisitos de alta resistência e resistência ao desgaste
- Os rolos de laminação a quente geralmente são ásperos para que possam morder o trabalho, e os rolos de laminação a frio são retificados e polidos para um bom acabamento
- Na laminação, os grãos se alongam na direção de laminação. Na laminação a frio, o cristal mantém mais ou menos a forma alongada, mas na laminação a quente eles começam a se reformar depois de sair da zona de deformação
- A velocidade periférica dos rolos na entrada excede a da tira, que é arrastada se o atrito da interface for alto o suficiente.
- Na zona de deformação, a espessura do estoque de aço é reduzida e alongada. Isso aumenta a velocidade linear do aço laminado na saída.
- Assim, existe um ponto neutro onde a velocidade do rolo e a velocidade da tira são iguais. Nesse ponto, a direção do atrito se inverte.
- Quando o ângulo de contato excede o ângulo de atrito, os rolos não podem desenhar tiras frescas
- Torque de rolo, potência etc. aumentam com o aumento do comprimento de contato do rolo de trabalho ou raio de rolo
Processo de manufatura