Fenômenos de pressão de coque e seus fatores de influência
Fenômenos de pressão de coque e seus fatores de influência
A pressão de coqueamento é um fenômeno que se tornou importante devido ao uso de fornos de coque de parede duplamente aquecidos, verticais e tipo slot. Nos fornos de colmeia redondos, bem como nos fornos de coque de recuperação de calor, que também estão sendo usados para a produção de coque, o carvão pode se expandir livremente para cima e, assim, o inchaço da carga é acomodado por essa expansão livre. Por outro lado, nos fornos de coque tipo slot, a expansão do carvão horizontalmente em relação à parede aquecida é restrita. Existem vários casos de falha prematura das paredes do forno durante o processo de carbonização do carvão.
A montagem dos novos fornos de coque, maiores e mais altos, tem sido acompanhada de ocorrências indesejáveis de paredes distorcidas devido à pressão de coqueamento resultando em diversos estudos sobre o comportamento de expansão do carvão durante a carbonização. Os esforços se concentraram no desenvolvimento de um teste confiável para que as misturas de carvão possam ser testadas quanto à segurança antes de seu uso nos fornos de coque.
Desenvolvimento da pressão de coque
Durante o processo de carbonização, o carvão passa pela fase plástica e a matéria volátil (MV) evolui durante e, em menor grau, após essa fase. É normalmente aceito que a pressão de coqueamento surge no estágio plástico. Em uma câmara de coqueria, duas camadas plásticas verticais paralelas às paredes de aquecimento são formadas desde o início da carbonização. À medida que a carbonização prossegue, essas camadas se movem em direção ao centro do forno. Ao mesmo tempo, camadas horizontais semelhantes são formadas na parte superior e inferior da carga. Estes são unidos com as duas camadas verticais e o todo forma uma região contínua que envolve o carvão não carbonizado e é geralmente referido como o “envelope plástico”.
A permeabilidade das camadas plásticas é baixa no caso de carvões de coque. Assim, com um carvão fortemente plástico, existe a possibilidade de que uma pressão possa se estabelecer dentro da zona fria do carvão não convertido. A soma da pressão interna dentro das camadas de plástico e entre elas é transmitida através das camadas de coque para exercer uma pressão nas paredes.
Quando as camadas de plástico se encontram no centro do forno, a massa central de carvão recebe calor de ambos os lados simultaneamente, enquanto a temperatura do carvão aumenta em toda a faixa de temperatura do plástico. Isso resulta em aceleração na taxa de coqueamento, levando a uma taxa mais rápida de evolução do gás com maior resistência ao seu escape. Isso resulta em valores de pico tanto na pressão interna quanto na pressão da parede.
Uma vez que as camadas de plástico também são formadas paralelamente às portas do forno e, portanto, existe um envelope plástico contínuo completo em torno do carvão não convertido assim que o carvão é carregado. Portanto, a MV desenvolvida a partir do lado frio da camada plástica é aprisionada dentro do envelope. No momento em que as camadas estão prestes a se encontrar, a taxa de aquecimento aumenta e, portanto, a quantidade de gás liberada aumenta, o que resulta em um aumento na pressão. Após a re-solidificação em coque, ocorre uma rápida diminuição da pressão devido ao desaparecimento do envelope.
Conforme outra explicação, não há calor suficiente para a formação de camadas plásticas paralelas às portas do forno. Assim, uma luva plástica (tubo) é formada a partir das duas camadas plásticas principais e das duas secundárias, que é aproximadamente retangular, mas se alarga próximo às portas devido às perdas de calor (Fig. 1). A pressão de coqueamento resulta da pressão dos gases dentro das camadas plásticas e é transmitida para as paredes através do coque e semicoque já formados.
Fig 1 Representação esquemática das zonas plásticas
Os gases que são liberados no lado mais próximo do centro de carga contêm alcatrão que condensa e depois revaporiza à medida que são capturados pela camada plástica. A impregnação do carvão pelo alcatrão condensado modifica a viscosidade da camada plástica. A pressão interna do gás depende muito da natureza do carvão e das condições de carbonização. Parece que está ligado ao equilíbrio estabelecido entre o inchaço da camada plástica, a contração do semicoque e, em certa medida, a compressão do carvão não carbonizado.
O fenômeno principal é o da pressão interna do gás dentro da camada plástica, enquanto a pressão da parede resulta da transmissão da pressão do gás através do semi-coque e do coque para as paredes. É provável que a magnitude da pressão interna do gás dependa da taxa de evolução da matéria gasosa dentro da camada de plástico e da resistência da camada de plástico ao seu fluxo, isto é, da permeabilidade da camada.
No entanto, as taxas de desvolatilização na faixa de temperatura plástica são maiores para os carvões com alto teor de VM e ainda assim esses carvões não dão altas pressões. Assim, a permeabilidade pode ser o fator mais dominante no desenvolvimento da pressão interna do gás. Isso ocorre porque a taxa máxima de evolução de MV para carvões de alto grau está próxima da temperatura de re-solidificação. De fato, existe uma relação entre a pressão máxima da parede e a taxa de evolução do VM remanescente próximo à temperatura de re-solidificação.
Durante uma investigação usando um forno de parede aquecido simples, observou-se que a permeabilidade é mínima no centro da camada plástica e máxima no produto de re-solidificação. A permeabilidade é considerada devido a duas contribuições. A primeira é a da (i) porosidade aberta existente na zona plástica, (ii) ultra-microporosidade permitindo o fluxo molecular, e (iii) macroporosidade permitindo o fluxo viscoso. A segunda contribuição vem do fluxo que segue o estouro das bolhas de desvolatilização. Este fenômeno ocorre porque na região da camada plástica adjacente ao semi-coque o estouro das bolhas prevalece sobre sua formação enquanto no centro da camada ocorre o contrário. Assim, há uma transferência de massa do centro da camada plástica para a zona adjacente ao semicoque estabelecida pelo máximo de porosidade no centro da camada plástica.
No caso de carvões que dão alta pressão, observou-se que este máximo é substituído por um mínimo na zona de carvão adjacente à camada plástica. Isso ocorre porque nesses carvões a segunda contribuição na permeabilidade, ou seja, o estouro de bolhas é baixo e essa suposição é sustentada pela ausência de um máximo de porosidade no centro da camada plástica. Como o escape de gases é limitado, a pressão na área da camada plástica aumenta e provoca uma compactação do carvão que resulta no mínimo observado de porosidade.
Estudos iniciais para pressão de coque
Testes de laboratório foram conduzidos pela primeira vez a fim de verificar a segurança das misturas de carvão. Durante esses testes, uma pequena quantidade de carvão, colocada em um pequeno cadinho, foi aquecida de um lado a pressão constante ou a volume constante. Um teste desenvolvido em 1920 é considerado a primeira tentativa de determinar a pressão de inchamento gerada por carvões. Neste teste, 100 gramas de carvão foram aquecidos em um cadinho de ferro cilíndrico vertical sob condições padrão, em um forno a gás. Um pistão perfurado foi colocado no topo da carga. O movimento do pistão foi registrado adequadamente, e a medida significativa foi a mudança no volume expressa em porcentagem. Este teste foi desenvolvido em duas direções e resultou, por um lado, no teste de pressão constante e, por outro lado, no teste de volume constante.
Na modificação do teste de pressão constante, 80 gramas de carvão seco ao ar foram colocados em um cadinho de aço. Uma carga de 1 kg/cm² é aplicada à carga de carvão e tanto a expansão quanto a contração da carga foram registradas como mudanças no volume. Na modificação do teste de volume constante que foi realizado a volume constante, 120 gramas de carvão seco ao ar foram carbonizados em um cadinho de aço e a pressão necessária para manter o carvão em volume constante foi registrada.
Além disso, foram desenvolvidos vários testes de escala maior que usaram vários quilogramas de carvão. Seus conceitos eram semelhantes aos testes de menor escala. Um exemplo representativo foi o grande teste de pressão constante que diferia do teste menor principalmente em tamanho e tinha uma capacidade de carga de cerca de 5 kg. Apenas as pressões geradas na carga de carvão superiores a 0,08 kg/sq cm foram medidas. Esta pressão foi considerada como o limite máximo permitido na parede de um forno de coque. Outro grande teste de laboratório foi o teste do forno 'aquecido sozinho'. Neste teste, uma carga de cerca de 35 kg foi aquecida unidirecionalmente a partir da sola e foi submetida a uma pressão de cerca de 0,14 kg/cm². O movimento da laje superior foi acompanhado por meio de um catetômetro.
Como o aquecimento nos testes descritos acima foi unilateral, os fenômenos permaneceram bastante diferentes daqueles que ocorrem em um grande forno. Devido à dificuldade de registrar a pressão da parede em um forno de coque, os primeiros pesquisadores sentiram que deveriam tentar simular as condições de carbonização que ocorrem em um forno comercial o mais próximo possível, adotando o aquecimento de parede dupla. Assim, foi projetada uma câmara de forno de grande escala na qual ambas as paredes de aquecimento eram móveis. Fixando uma parede, a pressão exercida na outra parede durante a carbonização pode ser medida com o auxílio de um sistema hidráulico. Este forno foi considerado o protótipo do forno de parede móvel permitindo uma medição direta da pressão de coqueamento.
Existem vários fornos de parede móvel em todo o mundo. Todos os projetos são baseados no aquecimento de dois lados. Uma de suas paredes é montada em um carrinho de modo que fica livre para se mover e a pressão de coqueificação desenvolvida durante a carbonização é expressa como uma força exercida na parede e é medida por meio de um dispositivo adequado e é chamada de pressão da parede. Eles são aquecidos a gás ou eletricamente e recebem cargas de carvão que variam de 250 kg a 500 kg. Como nos fornos de grande escala, duas camadas plásticas verticais são formadas, durante a carbonização, e progridem gradualmente em direção ao centro do forno, onde se fundem.
Em um dos projetos mais antigos de forno de parede móvel, cerca de 250 kg de carvão foram carbonizados em uma câmara de coqueamento de 300 mm x 700 mm x 1100 mm. Uma parede foi montada sobre rolos e foi equipada com um sistema de peso de alavanca para medir a pressão desenvolvida contra a parede. Este forno foi usado para estudar as pressões de coqueamento desenvolvidas pelos carvões americanos. Foram realizados 300 testes nos quais o carvão foi triturado 80% abaixo de 3 mm e carregado com baixo teor de umidade com densidade aparente (BD) variando de 785 kg/cum a 850 kg/cum.
As curvas obtidas por plotagem de pressão em função do tempo de coqueamento foram categorizadas em seis tipos de acordo com diversas características dos carvões testados. A Fig 2 mostra exemplos de cada um dos tipos de curvas de pressão. As curvas de pressão dos tipos 1 a 3 são todas para aqueles carvões ou misturas que normalmente são seguras para uso em fornos comerciais. Carvões que dão curvas 2 ou 3 podem dar pressões mais altas quando carregados em BD mais alto. Os tipos 4 a 6 são curvas de pressão de carvões que são perigosos para uso em fornos de coque.
Fig 2 Curvas de pressão de testes de diferentes carvões em forno de teste de parede móvel
Um forno de parede móvel maior de 400 kg foi usado para uma extensa investigação dos fenômenos de pressão de coque no Centro de Pirólise de Marienau (CPM). Neste forno, as duas paredes eram de construção em corindo que permitia o funcionamento a temperaturas mais elevadas e oferecia mais resistência e resistência ao choque térmico. A força exercida na parede móvel foi medida por uma balança de extensômetro que foi montada na parte externa da parede no centro geométrico da superfície útil da parede de aquecimento. Durante os vários testes neste forno, foram feitos quatro tipos principais de pressão de coqueamento – curvas de tempo que foram as mais frequentemente encontradas e são mostradas na Fig 3.
Fig 3 Principais tipos de curvas de pressão de coque
Analisando a forma destas curvas concluiu-se que estas resultaram da sobreposição de duas curvas básicas, cada uma delas correspondendo a uma das duas etapas. O primeiro estágio reflete a formação das camadas plásticas paralelas às paredes do forno e seu movimento em direção umas às outras, e o segundo estágio reflete a coalescência das camadas plásticas no centro do forno. As curvas dos tipos 1 e 2 foram dadas por carvões desenvolvendo altas pressões. O tipo 3 era característico dos carvões carregados estampados qualquer que fosse a magnitude da pressão, enquanto o tipo 4 foi registrado para carvões com baixas pressões. Carvões que deram altas pressões mostraram tipos semelhantes de curvas.
No caso de carvões com baixa VM, a pressão subiu regularmente desde o início até o máximo. O outro tipo de curva típica de alta pressão de coqueamento mostrou um rápido aumento na pressão durante a primeira hora. Então a pressão permaneceu relativamente constante durante o curso da carbonização. Quando as camadas plásticas se encontraram, ocorreu um aumento adicional até que o carvão plástico desapareceu.
Outra abordagem para a questão da pressão de coqueamento foi a medição da pressão do gás no centro da camada plástica. Essas medições foram feitas tanto nos fornos de parede móvel quanto nos fornos industriais, permitindo assim comparações entre os dois conjuntos de resultados. A pressão do gás foi medida por meio de tubos introduzidos através dos orifícios nas portas do forno ou nas tampas do orifício de carga.
Houve vários estudos de medição simultânea de pressão de gás e pressão de parede em fornos de teste. Nestes estudos verificou-se que a pressão máxima do gás no centro da carga está relacionada com o pico de pressão na parede. A pressão do gás aumentou com a distância da parede do forno e atingiu seu valor máximo no centro da carga no momento do encontro das camadas plásticas. Essa pressão máxima do gás geralmente coincidia com o pico da pressão da parede e era sempre maior. Diferentes valores foram dados para a razão entre a pressão do gás e a pressão da parede em diferentes estudos.
Em um dos estudos notou-se que à medida que a carbonização prosseguia e à medida que a camada plástica se movia, havia um aumento súbito na pressão do gás. Quando a camada de plástico se moveu além do ponto, a pressão do gás caiu rapidamente e aquela sonda não registrou novamente nenhuma pressão do gás. Quando as camadas de plástico se encontraram no centro do forno, a pressão do gás registrada foi maior do que as pressões em outros pontos do forno. A razão entre a pressão do gás e a pressão da parede neste experimento variou de menos de 1 para baixas pressões até 3 para altas pressões.
Em outra investigação, a influência das condições de carga e carbonização na pressão interna do gás foi estudada e descobriu-se que as pressões internas do gás eram influenciadas pelas mesmas variáveis que as pressões da parede.
Em outra investigação no CPM, duas observações foram feitas:(i) duas camadas plásticas foram formadas no início da carbonização paralelas à sola e ao teto e progredindo em direção ao centro do forno, e (ii) nenhuma camada plástica paralelas às portas foram formadas. Para a razão pressão do gás/pressão da parede foi encontrado um valor em torno de 0,5.
As diferenças na razão entre a pressão máxima do gás e a pressão de pico relatadas em vários estudos foram atribuídas a diferenças no equipamento de teste e no procedimento. No forno de parede móvel, embora o coqueamento proceda principalmente das paredes de aquecimento, ao mesmo tempo, um considerável coqueamento procedeu para dentro da sola, teto e questionavelmente das portas e isso reduziu a área das camadas plásticas que se encontravam no centro do forno.
O CPM propôs uma fórmula para o tempo de encontro das camadas plásticas no centro do forno. A fórmula era Pw/Pi =Si/S, onde Pw era a pressão da parede, Pi era a pressão interna, S era a superfície lateral da carga, Si era a área de projeção da camada plástica no plano central na tempo do pico de pressão da parede. Pi era maior que Ps e essas pressões eram a pressão interna e de parede ao mesmo tempo. O Si foi avaliado descarregando-se os fornos de teste no momento em que as duas principais camadas plásticas se uniram. A razão k =Si/S por definição era 1 no momento do carregamento, durante o curso da carbonização diminuiu devido aos efeitos finais e tornou-se zero após a re-solidificação do carvão. Em um forno de grande escala, os efeitos finais foram pequenos em comparação com a altura da parede, de modo que a razão Si/S ficou em torno de 1 e a pressão da parede de coqueamento foi igual à pressão máxima do gás central. Sugeriu-se que se uma mistura carbonizada sob certas condições no forno de teste produz uma pressão de parede P, então a pressão esperada em um grande forno trabalhando nas mesmas condições é da ordem de 2P.
Definição de limites de segurança.
Vários estudos realizados em fornos de parede móvel e fornos de grande escala visaram essencialmente controlar o fenómeno da pressão de coque e proteger os fornos de danos causados por pressões excessivas. Para uma avaliação de uma mistura de carvão, geralmente é empregado o teste de forno de parede móvel e a pressão máxima de parede resultante é usada para classificar a mistura de carvão como segura ou perigosa em comparação com os limites previamente estabelecidos. O BD da mistura no forno de teste é considerado extremamente importante. Deve ser pelo menos igual à média do forno em escala real e, de preferência, um pouco maior.
Se uma pressão é excessiva ou não, depende não apenas da pressão exercida, mas também da pressão que a parede do forno pode suportar. Assim, muitos esforços têm sido feitos para avaliar a resistência das paredes do forno de coque.
O requisito de resistência da parede é governado em grande parte pelo pico de pressão de coqueamento desequilibrado que é exercido nas paredes durante o processo de carbonização. Essas pressões desequilibradas causam a flexão da parede na direção horizontal, que deve ser estabilizada pela carga vertical da gravidade, incluindo o peso do telhado e da parede, porque as juntas na parede não têm resistência à tração consistente.
Um estudo foi realizado em uma parede de forno de coque especialmente construída que foi submetida à pressão lateral de uma prensa hidráulica. Foi demonstrado quão baixa é a resistência da parede do forno de coque à pressão lateral. As rachaduras iniciais apareceram na parede quando a pressão estava em torno de 0,09 kg/cm2 e a taxa de abaulamento aumenta rapidamente à medida que a pressão é aumentada para 0,13 kg/cm2. Com base nestes resultados de uma parede fria, foi sugerido um limite de segurança muito baixo de 0,07 kg/cm2. Um limite muito baixo restringe a flexibilidade na escolha de fontes de carvão, misturas de carvão e condições de carbonização. Assim, após comparar os resultados de várias centenas de carvões carbonizados em forno de parede móvel e tendo em conta o comportamento destes carvões em fornos comerciais, foram estabelecidos os seguintes limites de segurança para carvões carbonizados em fornos de coque.
- Os carvões que desenvolvem uma pressão superior a 0,14 kg/sq cm são perigosos.
- Os carvões que desenvolvem uma pressão superior a 0,11 kg/sq cm podem ser perigosos quando carbonizados regularmente em fornos com altura superior a 3 metros (m).
- Os carvões que fornecem pressões inferiores a 0,11 kg/cm² são seguros.
Com base em seu trabalho em 1948 e 1952, a British Coke Research Association (BCRA) concluiu que uma mistura de carvões era segura se a pressão desenvolvida em seu forno de teste fosse inferior a 0,14 kg/cm². Este limite foi confirmado por outros trabalhos realizados no BCRA em 1956. Neste trabalho eles carregaram várias misturas para os fornos comerciais que estavam no fim de sua vida útil e para um forno de parede móvel. Eles mediram o movimento das paredes nos fornos em escala real por aparelhos especiais e as paredes foram examinadas durante o teste e depois que a bateria foi resfriada para determinar o movimento e verificar os danos. Eles sugeriram que uma deflexão elástica de paredes de fornos comerciais de até 0,13 mm poderia ocorrer sem o aparecimento de rachaduras. Além desse ponto, mais deflexão não ocorreu prontamente e rachaduras ocorreram.
Nas décadas de 1960 e 1970, a construção de fornos de coque altos (6 m ou mais) tornou-se predominante. Esses fornos de coque foram operados sob a suposição de que pressões de coque abaixo de 0,14 kg/cm² eram seguras. O resultado foi que, em alguns casos, esses fornos sofreram danos refratários graves e precoces. Foi relatado que uma bateria de 6 m de altura sofreu danos progressivos e teve que ser desligada após menos de 5 anos de operação. As investigações para determinar as causas da falha prematura incluíram uma análise estrutural de uma parede de 6 m.
Foi realizado um estudo matemático de uma parede de forno de 6 m submetida à pressão de um lado. A partir desta análise, a pressão lateral desequilibrada que poderia causar colapso foi calculada como sendo um pouco acima de 0,12 kg/sq cm. Ao levar em conta o fator de carga ao vivo recomendado de 1,7, bem como a capacidade de manutenção em relação à fissuração, foi recomendado que a pressão lateral desequilibrada permitida não excedesse 0,07 kg/cm².
Fatores que influenciam a pressão de coque
Desde o início da década de 1950, o forno de parede móvel e outros fornos piloto de tamanho similar estavam sendo usados para avaliar carvões para coqueificação. O teste em escala piloto é mais barato do que o teste em forno em escala real e geralmente fornece uma boa orientação sobre o comportamento dos carvões em escala maior. Alguma garantia vem da comparação das pressões internas de gás geradas nos fornos de parede móvel e em escala real. A maioria dos estudos feitos sobre os fatores que influenciam a pressão de coqueamento foram feitos em fornos de escala piloto.
Muitos fatores foram encontrados para afetar a magnitude da pressão de coqueamento. Eles podem ser categorizados em três grandes categorias especificamente (i) características inerentes do carvão, (ii) preparação do carvão e propriedades físicas, e (iii) condições de operação do forno.
Carvão – Os primeiros estudos mostraram que foram encontradas pressões perigosas ao carregar carvões com teor de VM na base isenta de cinzas secas entre 16 % e 30 % e nunca com carvões com teor de VM inferior ou superior. Verificou-se que os carvões com forte expansão consistem principalmente em carvão brilhante, enquanto aqueles com maior proporção de carvão sem brilho apresentam menor força expansiva. Assim, das investigações petrográficas podem-se tirar algumas conclusões quanto ao grau de expansão dos carvões.
Uma série de experimentos foi conduzida pela Bethlehem Steel Corporation sobre a influência da composição do carvão na pressão de coqueamento usando um forno de teste de 18 polegadas (457 mm) e uma grande variedade de carvões únicos e misturas de carvão. Verificou-se que existe uma relação geral entre a classificação do carvão (como mostrado pela refletância da vitrinita) e a pressão de coque (Fig. 4). A partir da Figura 4, pode-se observar que a alta pressão de coqueificação tende a ser gerada por alguns, mas não todos, carvões de baixa VM com refletância maior que 1,35%. Além disso, verificou-se que a pressão de coqueamento não só aumenta com o aumento do teor de carvão, mas também aumenta com a diminuição do teor de inertes.
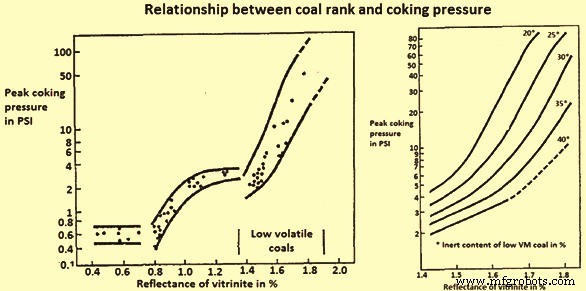
Fig 4 Relação entre classificação de carvão e pressão de coque
O teor de carvão e o conteúdo inerte têm uma interação sinérgica. Em qualquer nível de classificação, a pressão de coqueificação tende a ser menor se o carvão tiver um alto teor de inertes. Quando apenas o efeito do carvão de baixo VM é levado em consideração, a pressão gerada pela mistura de carvão aumenta com o aumento da refletância do carvão de baixo VM e esse aumento acelera quando a refletância do carvão de baixo VM ultrapassa 1,65%. No entanto, o conhecimento da classificação não permite avaliar o perigo da pressão de coque de um carvão com qualquer grau de certeza. Pode-se afirmar que entre 18% e 25% VM o perigo é grande e entre 25% e 28% VM ainda existe, embora em menor grau. Carvões de baixa VM com refletância superior a 1,65% e baixo teor de inertes produzem altas pressões, sejam coqueadas isoladamente ou em misturas.
Oxidação do carvão – A oxidação do carvão reduz a plasticidade máxima e a zona plástica se estreita. Verificou-se que a oxidação de alguns carvões inicialmente aumenta a pressão de coqueificação, mas depois há uma queda na dilatação e uma redução abrupta na pressão de coqueificação. Ao mesmo tempo, o índice M10 aumenta.
Estudos no infravermelho com transformada de Fourier (FIR) indicam que nos estágios iniciais da oxidação, os principais grupos funcionais formados são carbonila e carboxila. Em graus mais elevados de oxidação, a evidência indica um aumento significativo nos grupos éter, éster e fenólicos. A perda de propriedades plásticas na oxidação é atribuída à formação de ligações cruzadas de éter e éster.
O efeito da oxidação do ar de três carvões espanhóis foi investigado. A partir dos resultados, concluiu-se que, para carvões que foram caracterizados como “perigosos” pelo teste, a oxidação aumentou seu caráter perigoso até um máximo em um determinado nível de oxidação, após o qual diminuiu acentuadamente. Para um carvão caracterizado como seguro, não houve efeito apreciável da oxidação do ar.
Em um estudo no CPM da influência da oxidação na baixa permeabilidade entre 500°C e 600°C exibida por carvões de alto grau mostrou que a permeabilidade aumentou com a oxidação. Isso foi atribuído ao aumento do volume de poros abertos nos carvões oxidados. Existe um consenso geral de que é difícil reduzir a pressão de coque por oxidação sem simultaneamente prejudicar a qualidade do coque, enquanto a oxidação moderada pode aumentar a pressão.
Estudos de misturas de carvão – Uma série de estudos experimentais foi feita sobre o comportamento de blendas de carvão e sua pressão de coqueamento. As misturas foram carregadas por gravidade a um teor de umidade de 3,5% e trituração simples a 80% inferior a 2 mm. A partir dos resultados foi concluído o seguinte.
- O carvão que fornece uma pressão de coqueamento média quando carregado sozinho afeta a pressão de coqueificação de um carvão perigoso quase linearmente em função da composição da mistura.
- Carvões de alta VM que não dão pressão de coqueamento diminuem a pressão mais rapidamente do que em proporção à quantidade adicionada. Portanto, eles são mais eficazes na redução da pressão. A eficácia de tais carvões é maior quanto menor for sua classificação.
- Semi-antracite (baixo VM) se comporta de maneira diferente. Se for triturado com a mistura, o efeito de redução da pressão é acentuado, mas também há uma acentuada deterioração da qualidade do coque. Por outro lado, se for triturado separadamente (95 % a menos de 1 mm), uma adição de 15 % é suficiente para diminuir a pressão e a qualidade do coque é apenas ligeiramente reduzida. A semi-antracita que é um inerte aumentou a viscosidade do carvão durante a fusão e isso prejudica a coesão do carvão. Também reduz a contração do semicoque, enquanto com a adição de carvões de alto VM a contração é aumentada.
Também foi observado que as misturas de carvão dão pressão maior do que a gerada por carvões individuais quando carregados sozinhos. Isso ocorre quando um carvão pouco fusível e de baixa VM está associado a um carvão muito fusível. Então as condições do fluido permitem que o caráter perigoso do carvão de baixa VM seja expresso.
No BCRA, verificou-se que, no que diz respeito ao desenvolvimento de pressões de expansão, o comportamento de uma mistura binária depende em grande parte do caráter do carvão que está em excesso na mistura. De seus estudos sobre os efeitos da mistura, foi concluído o seguinte.
- A pressão de coque ocorre apenas com misturas de carvão com VM inferior a 24%.
- A adição de 30% de carvão de coque fraca diminui consideravelmente as propriedades perigosas de um carvão de baixa VM.
- Em misturas de carvões com alto/baixo VM, ocorre uma diminuição na pressão ao aumentar a porção de carvão com alto VM.
- Em misturas ternárias com conteúdo de VM semelhante, a adição de 15% de um carvão quase não coqueificável evita o desenvolvimento de qualquer pressão de coqueificação.
Efeito da adição de pitch – A diminuição da disponibilidade de carvões de alto teor levou a um aumento do interesse no uso de aditivos de breu em misturas de carvão para a produção de coque metalúrgico. O piche pode se comportar como agente de ponte e melhorar a resistência do coque resultante. O piche (i) modifica o estado plástico e esta modificação está associada a reações de transferência de hidrogênio (H2) envolvendo o movimento de H2 do piche para os radicais livres, estabilizando assim o estado plástico, (ii) alarga a camada plástica e (iii) aumenta a evolução da VM. A adição de piche a um carvão tende a aumentar a pressão de coqueificação, mas a magnitude do efeito depende da natureza do carvão.
Efeito de inertes – Verificou-se que proporções relativamente pequenas de inertes são suficientes para reduzir consideravelmente a pressão de um carvão, enquanto o tamanho das partículas dos inertes tem um efeito muito grande. Os inertes podem ter vários efeitos, nomeadamente (i) um efeito diluente no carvão, uma vez que os inertes não mudam de volume, o espaço disponível para o carvão inchar aumenta, (ii) efeito do tamanho das partículas significando que se o tamanho do inerte é mais fino que o carvão aumenta a finura média, diminuindo assim a pressão, (iii) ação específica já que os inertes absorvem certa quantidade de alcatrão e betume, reduzindo a fluidez e inchamento do carvão, quanto mais finos e porosos são os inertes maior o efeito, (iv) modificar a contração da carga após a re-solidificação, (v) os inertes podem aumentar a permeabilidade da camada plástica.
No BCRA, foi feito um estudo sobre a adição de brisa de coque na pressão de coqueamento. Normalmente, a pressão média da parede diminui com o aumento da proporção de brisa de coque. Em outra série de testes, com até 30 % de brisa grossa, verificou-se que a pressão interna máxima do gás diminui com a adição de mais de 5 % de brisa de coque, enquanto a pressão máxima da parede não é consideravelmente reduzida até que mais de 10 % seja adicionado .
Uma patente para redução da pressão de coqueamento sugere a adição de 2% a 8% de flocos formados a partir de serragem ou outros materiais inertes. A ação dos flocos é considerada o rompimento das camadas plásticas na carga do forno, proporcionando assim a passagem necessária para os gases.
Efeito da adição de óleo – A adição de óleo em misturas de carvão, altera o BD em teor de umidade constante e diminui a pressão. The added oil acts as a diluent and a reduction in pressure can be achieved without damaging the mechanical properties of the resultant coke. It has been observed that the addition of anthracene oil decreases the wall pressure of coals considerably while the maximum in the pressure is observed at a very low temperature, less than 300 deg C. This has been attributed to the ‘balloon effect’, i.e., the volatiles from the oil formed at low temperatures become trapped between the advancing plastic layers and their accumulation leads to the development of pressure.
Effect of moisture – An increase in the moisture in the charge decreases the pressure by decreasing the BD. The use of wet charges makes the carbonizing process very uneven and highly disturbed. The steam acts on the coal particles affecting their ability to absorb the liquid pyrolysis products. The moisture breaks through the plastic zone at different points and so by travelling along the chamber wall reaches the gas free space. The result is a highly deformed plastic layer.
The joining of the plastic layers is spread chronologically and locally over individual sections. So the pressure on the wall manifests itself only in a reduced form. On the other hand during carbonization of preheated charges the plastic layers formed converge with parallel faces to the heating walls and at the same time practically join together over the entire length and height of the chamber thus the pressure on the wall attains its maximum value.
During carbonization in slot type ovens, the moisture content across the charge rises steadily, in comparison with the moisture of the original charge, as moisture is distilled towards the oven centre. .
Several investigators measuring internal pressure in the full scale ovens recorded a peak pressure coinciding with the temperature reaching 100 deg C at the oven centre. This peak is called the water or steam peak and is attributed to the fact that the steam can no longer condense in this region of the oven and must be expelled. Eventually it becomes trapped within the plastic envelope.
In a study, it has been found that the average water peak pressure depends only on the coal moisture and it decreases as moisture is increased suggesting that the BD is the important factor.
Effect of bulk density – BD is regarded as the most important of the variables affecting coking pressure. By increasing the BD, a safe blend can develop very high pressures. In several studies, it has been proved that the danger of damage to the oven increases with greater charge densities. With the erection of large ovens, the influence of BD of coal on the degree of expansion become more important because the coal charge become denser on account of the increased height of the fall during charging.
In several studies on the influence of BD on coking pressure, it is seen that a lack of agreement exists regarding the nature of the functional relationship between test oven wall pressure and BD. In some of the studies it is claimed that the logarithm of wall pressure with BD gives a straight line with slope, while in the other studies it is claimed that this relationship is better represented by a curve. In another it has been shown that at densities above 800 kg/cum (dry), the rate of increase in pressure with increasing BD is enhanced.
In a study at BCRA, it has been shown that gas pressure also displays the same variation with BD as wall pressure. It has been concluded that a given change of BD produces a given change in pressure irrespective of the method employed for BD control.
In a more recent work on the influence of BD on coking pressure, where a single blend has been used with different bulk densities, it has been seen that the variations in BD have been achieved in different ways such as oil addition, preheating treatment, variations in moisture content. In this study it has been found that BD has a large influence on the coking pressure and it is probably the most important factor affecting the pressure developed by any coal or blend charge.
Effect of particle size – When coal particles differing in size are heated the conditions for the transport of the gaseous pyrolysis products from the middle of the particle to the surface differs. The larger is the particle size, the greater has the pressure developing inside it as a result of the pyrolysis of the organic mass. This promotes condensation which exerts a major influence on the subsequent thermal changes of the coal substance. It has been found that the initial softening temperature increases and the plastic temperature range becomes smaller as the particle size decreases but the viscosity of the plastic mass increases.
It is difficult in practice to analyze separately the influence of BD and particle size on coking pressure. It is known in fact that an increase in the fineness of the blend involves a reduction in charge density and a reduction in coking pressure. The independent influence of crushing on coking pressure has been studied. In the study examination has been carried out regarding the influence of the degree of overall fineness of the blend, the degree of fineness of each blend constituent (differential crushing) and finally the effect of the mode of crushing, i.e., the shape of the size distribution curve. It was found that at practically constant density, the particle size has a very marked effect on coking pressure, fine crushing reducing the pressure.
Crushing the constituents of a blend separately does not seem to present any particular advantage. A study has shown that systematic crushing can in certain cases have a specific effect, i.e., at the same degree of fineness the pressure is lower than with simple crushing. The conclusion of this study is that the pressure depends much on the proportion of coarse particles (higher than above 2 mm to 3 mm).
By examining the simultaneous action of bulk density and crushing it has been found that the effect of one of the factors depends on the level of the other. Thus the effect of density is greater, the coarser the crushing and similarly, the effect of crushing is more pronounced, the higher the density.
Effect of oven width – The effects of changes in width of the oven chamber, studied using pilot ovens on the wall pressure is not consistent. In the area of 150 mm to 330 mm, the oven width seems to have a substantial effect with decrease of wall pressure with increasing width. However, for greater widths the effect is small or negligible.
At BCRA by using two different ovens with widths 300 mm and 426 mm, it has been found no significant difference between the pressures developed by a given coal when carbonized under similar conditions of BD and flue temperature.
In one of the studies a good correlation has been reported between wall pressure measured in both 150 mm and 300 mm in wide ovens. The plastic area/wall area ratio has been about the same for both these widths.
The coking pressure value measured in a movable wall oven is associated with the ratio K given by surface area of plastic zone/surface area of heating wall. When the width of the chamber is increased so is the increase in the carbonization time. So more time is available for carbonization to progress simultaneously from the sole upwards and the roof downwards, the final plastic layer therefore has a smaller area in a wide oven than in a narrow one. This has been confirmed by direct measurement of the plastic zone area through premature pushing. Thus widening of the chamber involves a reduction in coking pressure but the magnitude of the variation depends on the blend considered while generally remaining small.
Effect of flue temperature – An increase in flue temperature increases the heating rate which in turn (i) shifts the softening and re-solidification temperatures to higher values widens the plastic temperature range, (ii) increases the flow of gas liberated in the plastic layers, (iii) increases the thickness of the plastic layer, and (iv) reduces the viscosity. The increase in flue temperature also reduces the thickness of the plastic layer due to the increase of the temperature gradient. These effects act on opposite directions so the final effect can be very small or insignificant. By studying this effect the BCRA found that with two blends and one coal, higher heating rates resulted in some increase in wall pressure. However with one coal the opposite was observed and with two other coals they found no obvious effect.
In a study where testing of two blends has been carried out at three levels of temperature 1020 deg C, 1120 deg C, and 1200 deg C, it has been seen that, one blend has shown an increase in both wall and gas pressure with increasing flue temperature while the effect produced using the other blend was not significant.
In another investigation, where the influence of coking rate on gas pressure in commercial ovens has been studied, it has been concluded that increased coking rates has not significantly increased the pressure of the charged blends for the range of coking rates used (the centre of the oven has reached 900 deg C in 12.3 hours to 18.3 hours).
Other investigators have found that coking at faster rates increase the pressure in a consistent way (coking rate is based on time required to reach a coke mass centre temperature of 980 deg C) (Fig 5).
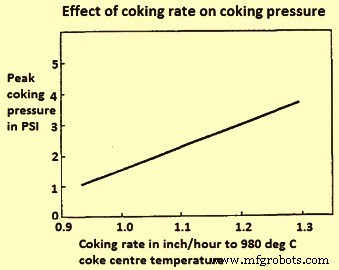
Fig 5 Effect of coking rate on coking pressure
Processo de manufatura
- BME280 Temperatura, Umidade e Pressão na Tela Nextion
- BMP280:Medir temperatura, pressão e altitude
- Medição e registro de pressão do Arduino
- Escória de alto forno e seu papel na operação do forno
- Ferro Reduzido Direto e seus Processos de Produção
- Máquinas CNC e suas vantagens na engenharia industrial
- A máquina do moinho e suas diferentes subcategorias
- Entendendo a soldagem de pinos a arco e suas técnicas
- Entendendo o processamento e fabricação de plásticos
- Entendendo o chassi do carro e sua importância