Produção e características de barras de reforço de alta resistência
Produção e características de barras de reforço de alta resistência
Durante as últimas décadas, a construção de concreto armado geralmente utilizou barras de armadura com limite de escoamento de 415 MPa (415 N/sq mm) para a maioria das vigas, vigas e pilares e, menos frequentemente, barras de armadura com limite de escoamento de 500 MPa para pilares que não fazem parte de um quadro especial de resistência a momentos. No entanto, atualmente, as barras de reforço de alta resistência estão substituindo as barras de reforço usadas anteriormente com limite de escoamento de 415 MPa para a construção de edifícios e estruturas de concreto alto, especialmente nas áreas com alto risco sísmico. Isso está sendo feito para resistir às forças do terremoto. Barra de reforço de alta resistência é normalmente definida como aquela barra de reforço que tem um YS de 500 MPa ou mais. No Japão, barras de reforço com resistência ao escoamento de até 690 MPa estão sendo usadas atualmente em elementos de construção projetados para resistir a forças de terremoto.
Vários estudos têm sido realizados para avaliar o uso de barras de reforço com maiores resistências para vigas, longarinas e pilares que suportam cargas vivas e permanentes. Esses estudos indicaram que há uma necessidade crescente de barras de reforço de maior resistência em aplicações sísmicas e não sísmicas. Existem muitos benefícios potenciais para o uso de barras de reforço de alta resistência na construção de concreto. Isso inclui economia de custos, tempo de construção reduzido e redução no congestionamento de reforço.
Nos EUA, atualmente, os produtores de aço estão desenvolvendo barras de reforço com resistências YS chegando a 830 MPa e com propriedades mecânicas e químicas variadas. As novas barras de reforço de alta resistência estão sendo produzidas usando diferentes métodos de produção. No entanto, nenhuma das barras de reforço de alta resistência é capaz de corresponder às propriedades mecânicas de referência das barras de reforço de grau 415 MPa. Cada uma das variantes de alta resistência difere do comportamento de referência de maneiras diferentes. Existe a preocupação de que as barras de reforço de alta resistência menos dúcteis possam fraturar nas dobras e possam precisar de diâmetros de dobra maiores.
No Japão, um projeto de 5 anos sob o nome de código 'New RC' foi iniciado e terminou em 1993. Uma das tarefas deste projeto foi estabelecer um padrão para barras de reforço de alta resistência para uso em edifícios em regiões sísmicas. A comparação deste padrão com alguns dos outros padrões para barras de reforço de alta resistência é dada na Tab 1.
Guia 1 Comparação de alguns dos padrões para barras de reforço de alta resistência | ||||
Sl. No. | País | Padrão | Força de rendimento em Mpa | Observações |
1 | Japão | Novo projeto RC 1993 | 980 | Também inclui grau de 1275 MPa, mas apenas para aplicações de reforço transversal |
2 | EUA | ASTM 1035-14 | 830 | Alta resistência ao escoamento controlando a microestrutura |
3 | Índia | IS 1786 – 2008 | 650 | Aço microligado com CE máximo de 0,53 |
4 | Rússia | GOST 10884-94 | 1200 | Alta resistência ao escoamento com adição de silício até 2,3% |
5 | Coreia | KS D3504-11 | 700 | Aumento de CE permitido até 0,63 |
6 | Ucrânia | DSTU 3760-06 | 1000 | |
7 | Reino Unido | BS 6744-01 + A2:09 | 650 | Vergalhão de aço inoxidável |
8 | China | GB 1.499,2 -07 | 500 | CE 0,55 máximo |
Observação:Carbono equivalente CE =C + Mn/6 + (Cu + Ni)/15 + (Cr + Mo + V)/15 |
Produção de barras de reforço de alta resistência
Existem três métodos normalmente utilizados para a produção de barras de reforço de alta resistência. São eles (i) trabalho a frio, (ii) adição de elementos de liga na composição do aço e (iii) têmpera e revenimento do aço durante sua laminação. Barras de reforço de alta resistência produzidas através de têmpera e revenimento normalmente apresentam relações de resistência à tração relativamente baixa para resistência ao escoamento e deformações relativamente altas na fratura. As barras de reforço de alta resistência produzidas por microligas têm uma relação resistência à tração relativamente alta para resistência ao escoamento e deformações relativamente altas na fratura. Esses métodos são mostrados na Fig1 e descritos abaixo.
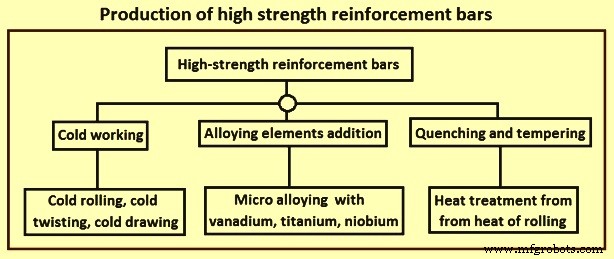
Fig 1 Produção de barras de reforço de alta resistência
Trabalho a frio – O trabalho a frio é um método antigo de produção de barras de reforço de alta resistência. No trabalho a frio do aço, a deformação do aço é realizada por qualquer um dos processos de trabalho a frio, como laminação a frio, torção a frio ou trefilação a frio etc. Este método permite a produção de barras de reforço de alta resistência a partir de aços de baixo carbono e manganês que são soldáveis. Neste método, as barras de reforço são submetidas a um encruamento após a laminação a quente. Para essas barras de reforço, a resistência ao escoamento pode ser aumentada aumentando a extensão da deformação. O trabalho a frio é realizado abaixo da temperatura de recristalização do aço. O processo causa a geração de discordâncias e movimentos dentro da estrutura cristalina do material de aço. Um deslocamento é um defeito cristalográfico ou irregularidade dentro de uma estrutura cristalina. A presença dessas discordâncias afeta fortemente o limite de escoamento e a ductilidade do material de aço. O trabalho a frio elimina um platô de escoamento e endurece o aço. Embora o trabalho a frio melhore a resistência ao escoamento, ele reduz a ductilidade e a relação entre a resistência à tração e a tensão de escoamento. Portanto, normalmente não é um método apropriado para produzir barras de reforço de alta resistência para membros resistentes aos efeitos de terremotos.
Adição de elementos de liga – Neste método, a tensão de escoamento do material de aço é aumentada pela modificação da composição química pela adição de elementos de liga, mas os teores de carbono e manganês são mantidos baixos para evitar uma diminuição significativa na soldabilidade do aço. As barras de reforço de alta resistência produzidas pela adição dos elementos de liga são usadas na condição laminada após resfriamento lento ao ar. Normalmente, a alta resistência do material de aço é alcançada pela adição de pequenas quantidades de titânio, nióbio ou vanádio, que é conhecido como microligação. A microligação é um processo que envolve a introdução de pequenas quantidades de elementos de liga para atingir as propriedades desejadas nas barras de reforço. A microligação pode produzir um ponto de escoamento marcado e uma relação resistência à tração/tensão de escoamento maior do que a de barras de reforço de aço temperado e revenido (da ordem de 1,25 para barras de reforço de grau 690 MPa).
A microliga forma carbonetos intermetálicos que produzem reforço de grão fino e endurecimento por precipitação. O reforço de grão fino ocorre pela fixação de defeitos planares (contornos de grão) durante o processamento termomecânico (laminação), que produz um tamanho de grão muito fino nas barras de reforço de aço. Em geral, quanto mais fino o tamanho de grão, maior é a tensão de escoamento. Essa relação é conhecida como efeito Hall-Petch (a relação Hall-Petch informa a resistência em materiais que é tão alta quanto sua própria resistência teórica pode ser alcançada reduzindo o tamanho do grão. De fato, a resistência do material continua a aumentar com a diminuição do tamanho do grão para cerca de 20 nanômetros a 30 nanômetros onde a força atinge o pico.). Quando esses carbonetos intermetálicos são dispersos através dos grãos de ferrita, ocorrem defeitos na linha de fixação (deslocamentos), que aumentam ainda mais a tensão de escoamento do material. Este mecanismo é conhecido como endurecimento por precipitação.
A microligação de titânio contribui para o endurecimento por precipitação, mas a forte tendência do titânio de combinar com oxigênio, enxofre e nitrogênio dificulta o controle dos efeitos de fortalecimento. A microliga de nióbio é amplamente utilizada na produção de chapas e tiras de aço, na qual a temperatura no final da produção é relativamente baixa e a deformação é alta. A produção de barras de reforço requer altas temperaturas de laminação e menos deformação, tornando a microligação de nióbio ineficaz para a produção de barras de reforço de alta resistência.
O vanádio é um dos elementos de liga mais usados para aumentar a resistência das barras de reforço. A microligação de vanádio ou vanádio-nitrogênio é normalmente usada para produzir barras de reforço de alta resistência que são soldáveis. A adição de vanádio aumenta a tensão de escoamento e a tenacidade à fratura principalmente devido à inibição do crescimento de grãos durante o tratamento térmico e a precipitação de carbonetos e nitretos. A microligação somente de vanádio resulta em 35,5% do vanádio formando carboneto e nitreto precipitado, enquanto 56,3% do vanádio acaba como solução sólida dissolvida na matriz, o que não melhora a tensão de escoamento da barra de reforço. A quantidade de precipitados formadores de vanádio pode ser aumentada até 70% com a adição de nitrogênio. Outra vantagem das barras de reforço micro-ligadas de vanádio-nitrogênio é que ele elimina os efeitos adversos do envelhecimento por deformação nas propriedades do aço porque fixa o nitrogênio solúvel. O uso de vanádio pode reduzir a quantidade de carbono necessária para obter resistências mais altas e, portanto, é útil para obter barras de reforço de alta resistência soldáveis.
Revenimento e têmpera – A têmpera é o resfriamento rápido do aço que foi aquecido até a fase austenítica (na qual o material de aço sólido recristaliza). O processo de têmpera e revenimento consiste em têmperar o aço imediatamente após a laminação e, em seguida, permitir que a barra de reforço seja revenida pelo calor que permanece no núcleo enquanto ela resfria gradativamente no leito de resfriamento. Como resultado, este processo produz aço com propriedades mecânicas que variam significativamente entre sua camada interna de núcleo e sua camada externa de revestimento, com o núcleo interno apresentando menor resistência ao escoamento e mais ductilidade do que a camada externa. Barras de reforço tratadas com têmpera e revenimento mantêm seu platô de rendimento, uma vez que não foram endurecidas por deformação e uma vez que a composição química geral não foi alterada. Essas barras de reforço podem ser soldáveis se sua química satisfizer os requisitos. Essas barras de reforço normalmente apresentam uma baixa relação resistência à tração para tensão de escoamento (da ordem de 1,15 para barras de reforço de grau 690 MPa).
O aço é temperado normalmente em água, o que resulta em uma estrutura de material duro e quebradiço. A têmpera é o aquecimento do aço temperado, que modifica a microestrutura para diminuir a dureza e aumentar a ductilidade do material.
O processo de produção de barras de reforço de alta resistência é baseado no processamento termomecânico. O processo termomecânico é um processo metalúrgico que combina o processo de deformação plástica com os processos térmicos, como tratamento térmico, têmpera em água, aquecimento e resfriamento em várias taxas em um único processo. O processo confere alta resistência às barras de reforço pela técnica de tratamento termomecânico em oposição ao trabalho mecânico por trabalho a frio. A resistência das barras de reforço é devido à camada externa de martensita temperada, enquanto a ductilidade das barras de reforço é devido à estrutura de ferrita-perlita no núcleo das barras de reforço.
O tratamento termomecânico converte a superfície das barras de reforço em uma estrutura endurecida (martensita) e posteriormente a fase evolui por resfriamento à temperatura ambiente para permitir que o núcleo quente tempere a superfície por meio de troca térmica. Isso resulta em uma microestrutura composta única composta por martensita temperada na zona periférica/caso, zona de transição de perlita e bainita logo após a periferia da martensita e um grão fino de ferrita-perlita na zona central/núcleo (Fig. 2). Devido ao processo de produção de têmpera e auto-revenimento, as barras de reforço de alta resistência produzidas também são chamadas de "vergalhões temperados e auto-revenidos (QST)".
Fig 2 Microestrutura de barras de reforço temperadas e temperadas
Existe mais um método de produção para a produção de barras de reforço de alta resistência. Este método é coberto na especificação ASTM número ASTM A1035; 2011. Essas barras de reforço normalmente têm grandes relações de resistência à tração para resistência ao escoamento, mas deformações relativamente baixas na fratura. Este processo de produção de barras de reforço de alta resistência é um processo patenteado e é conhecido como processo de 'Manipulação de Microestrutura (MMFX)'. O processo patenteado MMFX envolve a manipulação da microestrutura do aço para obter as propriedades mecânicas e a resistência desejadas. O processo gera barras de reforço com relações tensão-mancha que não possuem um limite de escoamento bem definido, apresentam uma resistência à tração relativamente alta para a relação tensão de escoamento, mas têm alongamentos de fratura relativamente baixos. O MMFX de barras de reforço de alta resistência atende às especificações ASTM A1035.
Outros aspectos da produção – Barras de reforço de alta resistência são normalmente produzidas em comprimentos retos no laminador. No entanto, enrolar barras de reforço de tamanho menor está se tornando uma prática. As barras são enroladas logo após a laminação, o que retém o calor na bobina. Assim, a taxa de resfriamento de barras de reforço enroladas é um pouco mais lenta do que para barras retas. Uma vez que as amostras de teste precisam ser endireitadas antes do teste, as barras enroladas tendem a ter uma tensão de escoamento mais baixa e a forma da curva tensão-deformação pode ser um pouco arredondada. Para contrariar este efeito, as barras de reforço em espiral de alta resistência precisam de maiores quantidades de elementos de microliga em comparação com os tamanhos correspondentes de barras de reforço retas.
No processo de produção das barras de reforço, as marcas de identificação das barras são adicionadas durante a laminação e as propriedades mecânicas são testadas após as barras serem laminadas (e marcadas). Se as propriedades mecânicas do reforço de alta resistência não forem alcançadas, o resultado é que as barras de reforço não atendem às especificações associadas à marca.
Problemas de fabricação – Os problemas com a fabricação de barras de reforço de alta resistência podem ser agrupados em duas categorias, a saber (i) a introdução de vários graus de barras de reforço que precisam ser programadas, recebidas e armazenadas em uma instalação de fabricação antes do uso e (ii) ) mudanças no processo de fabricação necessárias como resultado das propriedades das barras de reforço de alta resistência.
Os processos de fabricação de cisalhamento e flexão são afetados pelas propriedades das barras de reforço de alta resistência. Barras de reforço de alta resistência resultam em maiores forças de cisalhamento e flexão para a mesma barra de tamanho e experimentam mais recuperação elástica após a flexão, levando a preocupações de fabricação em relação a (i) desgaste em equipamentos existentes e a possível necessidade de novos equipamentos de maior capacidade , (ii) segurança dos trabalhadores em caso de falha da barra ou equipamento durante as operações de dobra, e (iii) cumprimento das tolerâncias de fabricação da barra. Há falhas de equipamentos mais frequentes associadas à fabricação de barras de reforço de alta resistência. As preocupações com a segurança aumentam nos casos em que os defeitos da barra causaram fratura durante as operações de dobra em níveis de força mais altos. Precauções extras são necessárias para manter um ambiente de trabalho seguro, o que pode afetar a eficiência das operações de fabricação.
Propriedades do material
A resistência e a ductilidade das barras de reforço de alta resistência são definidas de diferentes maneiras. As propriedades de tração e outros requisitos que definem a resistência e a ductilidade que são especificados incluem (i) tensão de escoamento mínima ou limite inferior, conforme especificado na especificação relevante, (ii) tensão de escoamento máxima ou limite superior, conforme especificado na especificação relevante, (iii) ) comprimento do platô de escoamento ou deformação no final do platô de escoamento, (iv) resistência à tração, (v) alongamento uniforme e alongamento total, (vi) razão entre resistência à tração e tensão de escoamento ou seu inverso (referido como o limite de escoamento razão), e (viii) resultados de um teste de dobra ou um teste de dobra-rebenção. Algumas, mas não todas, essas propriedades e testes são especificados para cada armadura de alta resistência. Várias das propriedades de tração são indicadas na curva tensão-deformação idealizada mostrada na Fig 3.
Fig 3 Curva de tensão-deformação idealizada mostrando as propriedades de resistência e ductilidade
Reduz o estresse – Para todas as barras de armadura, normalmente são especificados o limite de escoamento ou a tensão de escoamento. No entanto, em alguns padrões (por exemplo, ASTM), a deformação no final do platô de escoamento é especificada para algumas das barras de reforço de alta resistência. Esses padrões especificam a tensão no final do platô de escoamento. As normas ASTM não permitem que o valor medido da tensão de escoamento caia abaixo do grau do aço, enquanto outras normas (como as normas da Austrália/Nova Zelândia) usam o conceito de 5 % de fractile, no qual uma pequena porcentagem de testes é permitida estar abaixo da força mínima. ASTM A370, ‘Standard Test Methods and Definitions for Mechanical Testing of Steel Products’ define o limite de escoamento como ‘a primeira tensão em um material menor que a tensão máxima obtida, na qual ocorre um aumento na tensão sem um aumento na tensão’. O ponto de escoamento é aplicável a armaduras que apresentam aumento de deformação sem aumento de tensão, o que geralmente ocorre apenas em barras de armadura com menores resistências.
Barras de armadura de alta resistência normalmente não têm um limite de escoamento definitivo, então outros meios de definir a tensão de escoamento são necessários. A ASTM A370 define a tensão de escoamento como "a tensão na qual um material exibe um desvio limite especificado da proporcionalidade da tensão à deformação". A tensão de escoamento pode ser determinada pelo método de compensação de 0,2% ou pelo método de 'extensão sob carga' (EUL) da ASTM A370. O método de compensação de 0,2 % é usado para o cálculo da tensão de escoamento para as barras de armadura, mas uma verificação adicional usando o método EUL para uma deformação de 0,0035 também é necessária para definir a tensão de escoamento mínima das barras de armadura. O método EUL com uma deformação de 0,0035 produz tensões mínimas de 550 MPa e 620 MPa para 690 e 830 graus de armadura de alta resistência, respectivamente. O método de compensação de 0,2% também é usado para definir a tensão de escoamento em especificações em muitos países.
Resistência à tração – Nas especificações, a resistência à tração é definida consistentemente como o pico de tensão na curva tensão-deformação. A resistência à tração é calculada dividindo a carga máxima que o corpo de prova suporta pela área nominal da barra.
Alongamento – O alongamento é normalmente relatado como o alongamento total ao longo de um comprimento de referência prescrito que se estende ao longo da fratura de uma barra. ASTM A370 fornece dois métodos para a determinação do 'alongamento total'. Em um método, uma barra é marcada com um comprimento inicial de 200 mm e puxada até a fratura. Este método não leva em conta o alongamento elástico. Para o primeiro método, as extremidades da barra fraturada são encaixadas e o comprimento de referência é medido novamente. O alongamento é então relatado como o aumento percentual no comprimento em relação ao comprimento de referência original. No segundo método, o alongamento na fratura pode ser medido usando um extensômetro, caso em que o alongamento elástico está incluído. Ambos os métodos incluem o alongamento localizado adicional na região com gargalo mais o alongamento ao longo das porções sem gargalo da barra dentro do comprimento de referência.
O alongamento uniforme é a deformação que ocorre quando a barra atinge seu pico de tensão (resistência à tração), expressa em porcentagem. Seu nome se origina do fato de que esta é a maior deformação na barra de teste enquanto as deformações de tração são uniformes em todo o comprimento entre as garras de teste. Ocorre logo antes do início do necking em uma barra. O alongamento uniforme é normalmente medido com um extensômetro enquanto uma amostra de barra está sendo testada. Inclui tanto a deformação plástica quanto a deformação recuperada ao descarregar a barra. Também pode ser determinado medindo o alongamento plástico após a remoção da amostra de barra da máquina de teste e, em seguida, adicionando a deformação recuperada. Neste caso, a deformação plástica é medida longe da região do pescoço e a deformação recuperada é adicionada a ela para obter o alongamento uniforme.
O alongamento uniforme calculado usando o 'Canadian Associations Standard CSA G30.18 (CSA, 2009)' assume descarga linear com um módulo igual ao módulo inicial do aço, Es, de 200.000 MPa. No entanto, os dados de teste em barras de reforço de 415 MPa indicam (i) o módulo de descarga diminui com o aumento da deformação de tração, (ii) a curva de descarga é linear apenas durante a fase inicial de descarga e (iii) a resposta torna-se progressivamente não linear, pois as barras estão totalmente descarregadas. Uma linearização da resposta de descarga pode resultar em um módulo de descarga em torno de dois terços do módulo de carregamento inicial. Para barras de reforço de alta resistência, a deformação recuperada pode chegar a 1%. Algumas normas (por exemplo, Norma Australiana/Nova Zelândia 4671, 2001) exigem o relato do alongamento uniforme.
O alongamento uniforme é uma propriedade útil para o projeto sísmico, uma vez que está mais intimamente relacionado ao alongamento máximo (o alongamento utilizável) que é confiado em um local de escoamento, ou seja, uma região de dobradiça plástica. O alongamento utilizável deve ser considerado como 75% ou menos do alongamento uniforme, porque sob condições de carregamento cíclico, as barras de reforço podem atingir o estado de dano equivalente associado ao alongamento uniforme em um alongamento menor. As barras de reforço normalmente têm uma razão característica de alongamento uniforme para alongamento de fratura, que varia de acordo com o tipo de reforço.
Ductilidade – Os ensaios de dobra e dobra-reflexão são duas formas de avaliar a ductilidade das armaduras. Normalmente, as especificações das barras de reforço incluem um teste de flexão em que as barras são dobradas em torno de um pino ou mandril de um diâmetro especificado e com um grau de flexão especificado. O diâmetro da dobra varia com o diâmetro da barra. A amostra de teste passa se não aparecerem rachaduras na parte externa da parte dobrada da barra.
Três categorias principais de testes experimentais são úteis para investigar o comportamento de dobras em barras de reforço, com cada categoria de testes voltada para responder a um determinado conjunto de questões. Essas categorias são (i) inspeções visuais de curvas (testes de flexão ASTM), (ii) testes de flexão/recurvatura e (iii) testes de flexão em concreto.
As especificações da ASTM para barras de reforço especificam o requisito de flexão como "O corpo de prova de teste de dobra deve resistir a ser dobrado em torno de um pino sem rachar na parte externa da porção de dobra". O teste de dobra necessário envolve, portanto, dobrar barras a 180 graus (ou 90 graus para barras de 43 mm de diâmetro e maiores) em um diâmetro de dobra de pino especificado. Uma inspeção visual é então realizada para identificar rachaduras na curva. Se nenhuma rachadura for visualmente observada, uma amostra é considerada aprovada no teste de dobra. O teste, embora simples de realizar, não fornece uma medida da resistência de reserva e ductilidade das curvas da barra, como um teste de carga pode. É possível que microfissuras não visíveis a olho nu possam comprometer o desempenho das barras de reforço in situ.
Nos testes de dobra e re-dobra, as amostras de barra são dobradas para o ângulo e diâmetro de dobra necessários e, em seguida, endireitadas em taxas de carregamento quase estáticas ou dinâmicas. Para barras com grau de 415 MPa, o encruamento aumenta a resistência do aço nas dobras e normalmente faz com que as amostras se rompam nas dobras de maneira dúctil. No entanto, se as barras de reforço têm ductilidade limitada, como barras de reforço de alta resistência, as demandas de deformação nas dobras podem causar trincas, o que pode tornar as dobras mais fracas do que as partes não dobradas das barras de reforço e mais suscetíveis à fratura frágil. Se uma barra de reforço falhar de maneira frágil em uma curva, considera-se que ela falhou no teste de dobra/reflexão. Se, no entanto, uma barra de reforço falhar de maneira dúctil, considera-se que ela passou no teste. Este tipo de teste tem a vantagem de colocar curvas de barras sob carga e, portanto, fornece uma medida direta do desempenho de resistência e ductilidade das curvas de barras.
Alguns padrões precisam de um teste de dobra-recurva para diâmetros de barra menores e um teste de dobra para diâmetros de barra maiores. Para o teste de dobra-reflexão, a amostra da barra deve ser dobrada em torno de um mandril de diâmetro especificado em um ângulo de 90 graus no meio do comprimento da amostra. Duas curvas adicionais de 45 graus são feitas para que a amostra fique reta em uma parte, em forma de V perto de seu comprimento médio e reta na outra extremidade, conforme mostrado na Fig 4. A amostra é então envelhecida em óleo por uma hora a 100 grau C, resfriado e dobrado na direção inversa, aplicando uma força de tensão nas extremidades da amostra. As etapas de envelhecimento e resfriamento são necessárias para simular os efeitos prejudiciais do envelhecimento por deformação. Quando as barras de reforço são dobradas, o nitrogênio pode ser liberado do aço, o que pode levar à fragilização. Ao dobrar novamente, o aço fragilizado é mais propenso a rachar. Nenhuma rachadura deve ser evidente na barra rebentada para passar no teste.
Fig 4 Amostras de teste de barras de reforço mostrando dobra-rebentação
Deve-se notar que os ensaios de flexão/recurvatura aplicam demandas maiores nas curvas da barra do que normalmente são observadas em uma estrutura de concreto. Por esta razão, é melhor comparar o desempenho de flexão/recurvatura das barras de armadura de alta resistência com as barras de 415 MPa, que são usadas há décadas e têm demonstrado desempenho adequado em membros de concreto. Curvas em barras de reforço também podem ser testadas em concreto. Nesses ensaios, a interação entre o concreto e as barras-curvas pode ser investigada. Versões simplificadas do teste incluem incorporar uma barra em gancho em um bloco de concreto e puxá-la até a falha. Possíveis modos de falha que podem ser esperados em testes de blocos incluem (i) fratura da barra fora do bloco onde as demandas na barra são mais altas, (ii) falha da barra dentro do bloco próximo ou na curva, ou (iii) rachadura do concreto quadra. Tais testes, no entanto, podem não expor as curvas ao pior carregamento que pode ser experimentado em uma estrutura, pois o concreto circundante pode aliviar as curvas de alguma carga. Em contraste, alguns dos piores carregamentos em curvas de barra podem surgir em aplicações de confinamento, onde um núcleo de concreto em expansão endireita parcialmente curvas de aro enquanto aplica altas cargas de tração a elas. Outra aplicação crítica para curvas de barras é em regiões danificadas, onde a aderência ao concreto e seus efeitos benéficos nas curvas são reduzidos (por exemplo, juntas sob carga sísmica severa ou regiões severamente rachadas). No entanto, testes de flexão de barras em membros de concreto são essenciais para validar o desempenho adequado de flexões de barras em barras de armadura de alta resistência. No entanto, esses testes são caros de realizar e não se prestam facilmente à tarefa de determinar os diâmetros mínimos de dobra enquanto exploram as inúmeras variáveis que afetam o desempenho de dobras de barras.
Envelhecimento por tensão – Envelhecimento por deformação é definido como o processo pelo qual o aço tensionado além de seu limite elástico sofre mudanças dependentes do tempo em suas propriedades mecânicas. Normalmente, barras de reforço tensionadas além de seu limite elástico irão, ao longo do tempo, ver um aumento em sua resistência à tração e uma diminuição em sua ductilidade (Fig. 5). Também foi comprovado que o envelhecimento por deformação afeta a temperatura de transição frágil no aço. Os fatores que afetam o envelhecimento por deformação incluem a composição do aço, a temperatura e o tempo decorrido desde que grandes deformações ocorreram. O envelhecimento por deformação é atribuído principalmente à realocação de nitrogênio dentro da matriz de aço. Temperaturas mais altas aceleram esse processo. Assim, o envelhecimento por tensão ocorre muito mais rápido em regiões mais quentes.
Normalmente, a maioria dos efeitos do envelhecimento por coloração em barras de reforço de aço ocorre dentro de alguns meses após a ocorrência de deformações inelásticas. À medida que as barras de reforço são dobradas, elas sofrem grandes deformações inelásticas. As curvas de barras são, portanto, propensas a fragilização por envelhecimento por deformação, o que pode causar fraturas prematuras e limitar sua capacidade de sustentar deformações inelásticas durante o carregamento estrutural.
Fig 5 Curvas de tensão e deformação típicas mostrando os efeitos do envelhecimento por deformação
Um estudo realizado sobre o envelhecimento por deformação de barras de reforço sugere que aços microligados, incluindo titânio e vanádio, podem diminuir os efeitos do envelhecimento por deformação nas barras de reforço. Tais elementos de liga têm propriedades que lhes permitem ligar-se ao nitrogênio na composição para formar nitretos. Essas reações limitam a quantidade de nitrogênio livre em todo o aço que é atribuída aos efeitos do envelhecimento por deformação.
Processo de manufatura
- Considerações para usinagem suíça de alta produção
- Características e aplicações do titânio
- Mar-Bal e EnterpriseIQ
- Avaliação do ciclo de vida e sustentabilidade do aço
- Ferro Reduzido Direto e seus Processos de Produção
- Barras de reforço temperadas e temperadas
- Corrosão de armaduras de aço em concreto
- Barras e Sistemas Condutores de Guindaste
- Máquinas VMC para produção e eficiência
- Entendendo a dureza, resistência e tenacidade dos materiais