Conhecimento de precisão de usinagem que deve ser conhecido em usinagem
A precisão de usinagem é o grau de conformidade entre o tamanho real, forma e posição dos três parâmetros geométricos da superfície da peça processada e os parâmetros geométricos ideais exigidos pelo desenho. Os parâmetros geométricos ideais são o tamanho médio para tamanho, para geometria de superfície, são círculos absolutos, cilindros, planos, cones e linhas retas, para as posições mútuas de superfícies, são absolutamente paralelas, verticais, coaxiais, simétricas, etc. O desvio dos parâmetros geométricos reais da peça em relação aos parâmetros geométricos ideais é chamado de erro de usinagem.
1. O conceito de precisão de usinagem
A precisão de usinagem é usada principalmente para o grau de produção do produto. Precisão de usinagem e erro de usinagem são termos usados para avaliar os parâmetros geométricos da superfície usinada. A precisão da usinagem é medida pelo grau de tolerância, quanto menor o valor do grau, maior a precisão. O erro de usinagem é expresso por um valor numérico. Quanto maior o valor numérico, maior o erro. Alta precisão de usinagem significa pequeno erro de usinagem e vice-versa.
Existem 20 níveis de tolerância de IT01, IT0, IT1, IT2, IT3 a IT18. Se IT01 indica que a peça tem a maior precisão de usinagem, IT18 indica que a peça tem a menor precisão de usinagem. Geralmente, IT7 e IT8 possuem nível médio de precisão de usinagem.
Os parâmetros reais obtidos por qualquer método de usinagem não serão absolutamente precisos. Do ponto de vista da função da peça, desde que o erro de usinagem esteja dentro da faixa de tolerância exigida pelo desenho da peça, considera-se que a precisão da usinagem está garantida.
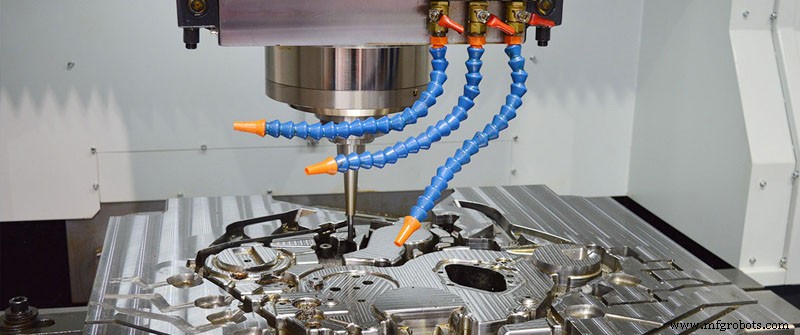
A qualidade da máquina depende da qualidade de processamento das peças e da qualidade de montagem da máquina. A qualidade de usinagem das peças inclui duas partes principais, a precisão da usinagem e a qualidade da superfície.
A precisão da usinagem refere-se ao grau em que os parâmetros geométricos reais (tamanho, forma e posição) da peça após a usinagem estão em conformidade com os parâmetros geométricos ideais. A diferença entre eles é chamada de erro de usinagem. O tamanho do erro de usinagem reflete o nível de precisão da usinagem. Quanto maior o erro, menor a precisão da usinagem e quanto menor o erro, maior a precisão da usinagem.
2. Conteúdo relacionado de precisão de usinagem
(1) Precisão dimensional
Refere-se ao grau de conformidade entre o tamanho real da peça processada e o centro da zona de tolerância do tamanho da peça.
(2) Precisão da forma
Refere-se ao grau de conformidade entre a forma geométrica real da superfície da peça processada e a forma geométrica ideal.
(3) Precisão da posição
Refere-se à diferença de precisão da posição real entre as superfícies relevantes das peças após o processamento.
(4) Relações Mútuas
Geralmente, ao projetar peças de máquinas e estipular a precisão de usinagem das peças, deve-se prestar atenção para controlar o erro de forma dentro da tolerância de posição, e o erro de posição deve ser menor que a tolerância dimensional. Ou seja, peças de precisão ou superfícies importantes de peças, os requisitos de precisão de forma devem ser maiores que os requisitos de precisão de posição e os requisitos de precisão de posição devem ser maiores que os requisitos de precisão dimensional.
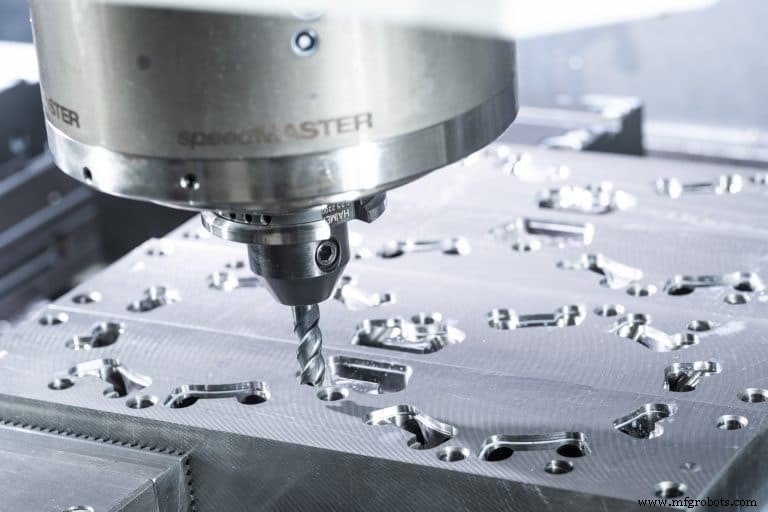
3. Ajuste M método
(1) Ajuste o sistema de processo
(2) Reduza o erro da máquina-ferramenta
(3) Reduzir o erro de transmissão da cadeia de transmissão
(4) Reduzir o desgaste da ferramenta
(5) Reduzir o estresse e a deformação do sistema de processo
(6) Reduzir a distorção térmica do sistema de processo
(7) Reduzir a tensão residual
4. Motivos do impacto
(1) Erro de Princípio de Processamento
O erro do princípio de usinagem refere-se ao erro produzido pelo processamento com perfil aproximado da lâmina ou relação de transmissão aproximada. Os erros do princípio de usinagem aparecem principalmente na usinagem de roscas, engrenagens e superfícies curvas complexas.
Na usinagem, o processamento aproximado é geralmente usado para melhorar a produtividade e economia na premissa de que o erro teórico pode atender aos requisitos de precisão da usinagem.
(2) Erro de ajuste
O erro de ajuste da máquina-ferramenta refere-se ao erro causado por ajuste impreciso.
(3) Erro de máquina-ferramenta
Erro de máquina-ferramenta refere-se ao erro de fabricação, erro de instalação e desgaste da máquina-ferramenta. Inclui principalmente o erro de guia da máquina-ferramenta, o erro de rotação do fuso da máquina-ferramenta e o erro de transmissão da cadeia de transmissão da máquina-ferramenta.
5. Método de medição
A precisão de processamento adota diferentes métodos de medição de acordo com diferentes requisitos de conteúdo e precisão de processamento. De um modo geral, existem os seguintes tipos de métodos:
(1) Conforme o parâmetro medido é medido diretamente, ele pode ser dividido em medição direta e medição indireta.
Medição direta:meça diretamente o parâmetro medido para obter o tamanho medido. Por exemplo, use calibradores e comparadores para medir.
Medição indireta:Meça os parâmetros geométricos relacionados ao tamanho medido e obtenha o tamanho medido através do cálculo.
Obviamente, a medição direta é mais intuitiva e a medição indireta é mais complicada. Geralmente, quando o tamanho medido ou a medição direta não atende aos requisitos de precisão, a medição indireta deve ser usada.
(2) De acordo com se o valor de leitura da ferramenta de medição representa diretamente o valor do tamanho medido, ele pode ser dividido em medição absoluta e medição relativa.
Medição absoluta:O valor de leitura indica diretamente o tamanho do tamanho medido, como medir com um paquímetro.
Medição relativa:O valor de leitura indica apenas o desvio do tamanho medido da quantidade padrão. Se você usar um comparador para medir o diâmetro do eixo, você precisa primeiro ajustar a posição zero do instrumento com um bloco de medição e, em seguida, realizar a medição. O valor medido é a diferença entre o diâmetro do eixo lateral e o tamanho do bloco padrão. Esta é uma medida relativa. De um modo geral, a precisão relativa da medição é maior, mas a medição é mais problemática.
(3) De acordo com se a superfície medida está em contato com a cabeça de medição do instrumento de medição, ela é dividida em medição de contato e medição sem contato.
Medição de contato:O cabeçote de medição está em contato com a superfície que está sendo tocada e há uma força de medição mecânica. Como medir peças com um micrômetro.
Medição sem contato:A cabeça de medição não está em contato com a superfície da peça medida. A medição sem contato pode evitar a influência da força de medição no resultado da medição. Como o uso do método de projeção, interferometria de ondas de luz e assim por diante.
(4) De acordo com o número de parâmetros de medição, é dividido em medição única e medição abrangente.
Medição única:meça cada parâmetro da peça testada separadamente.
Medição abrangente:meça o índice abrangente refletindo os parâmetros relevantes da peça. Por exemplo, ao usar um microscópio de ferramenta para medir a rosca, o diâmetro real do passo da rosca, o erro de meio ângulo do perfil do dente e o erro cumulativo do passo da rosca podem ser medidos separadamente.
A medição abrangente geralmente é mais eficiente e confiável para garantir a intercambialidade das peças e é frequentemente usada para inspeção de peças acabadas. A medição única pode determinar o erro de cada parâmetro separadamente e geralmente é usada para análise de processo, inspeção de processo e medição de parâmetros especificados.
(5) De acordo com o papel da medição no processo de processamento, ela é dividida em medição ativa e medição passiva.
Medição ativa:a peça é medida durante o processamento, e o resultado é utilizado diretamente para controlar o processamento da peça, de modo a evitar a geração de resíduos no tempo.
Medição passiva:a medição realizada após o processamento da peça. Esse tipo de medição só pode julgar se a peça processada é qualificada e se limita a descobrir e rejeitar produtos residuais.
(6) De acordo com o estado da peça medida no processo de medição, ela é dividida em medição estática e medição dinâmica.
Medição estática:A medição é relativamente estática. Como um micrômetro para medir o diâmetro.
Medição dinâmica:A superfície medida e o cabeçote de medição se movem um em relação ao outro no estado de trabalho simulado durante a medição.
O método de medição dinâmica pode refletir a situação da peça próxima ao estado de uso, que é a direção do desenvolvimento da tecnologia de medição.
Processo de manufatura
- Usinagem CNC para indústria de semicondutores:O que você deve saber
- Usinagem CNC 101:Conheça os Fundamentos da Usinagem CNC
- Cálculo de custo de usinagem CNC:todos os fatores e dicas que você deve saber
- 6 tendências da indústria de manufatura em 2022 que você deve conhecer para se manter competitivo
- Métodos comuns para obter a precisão da peça de trabalho na usinagem (2)
- 11 Conhecimento geral sobre usinagem de gravação CNC que você deve saber
- As 3 principais formas de marcação de peças que você deve conhecer
- Coisas que você deve saber sobre biela
- Coisas que você deve saber sobre o radiador de óleo do motor
- Coisas que você deve saber sobre termostato automotivo