Economizando tempo e dinheiro com o monitoramento de condição
Um estudo recente de emissão acústica (EA) identificou uma possível falha crítica de rolamento que se tornou uma ação preventiva planejada para um fabricante líder de alimentos. Isso também evitou custos consideráveis e tempo de inatividade não planejado.
O equipamento de emissão acústica e a principal ferramenta utilizada durante as rotas de inspeção planejadas foram fabricados pela Holroyd Instruments. Este exemplo mostrará o valor desse tipo de equipamento para evitar um grande evento não planejado que poderia ter consequências de custo massivas para o negócio. Danos colaterais ao equipamento associado teriam se mostrado muito caros, e o tempo necessário para reconstruir poderia ter causado um grande tempo de inatividade, o que significaria que os clientes insatisfeitos não poderiam confiar na disponibilidade de estoque.
A história começou em abril de 2010, quando algumas leituras iniciais elevadas foram observadas em dois pontos de nó em uma grande caixa de transferência abaixadora que foram amostradas em uma rotina de sete dias. As leituras de socorro foram elevadas e acionaram o nível de alarme. Eles foram preocupantes e evidentes nas inspeções subsequentes. A terceira leitura elevada, que fazia parte de uma tendência ascendente, instigou uma ordem de serviço planejada no sistema computadorizado de gerenciamento de manutenção (CMMS) para investigar e tomar medidas adicionais. Este equipamento não poderia ser colocado fora de serviço levianamente, pois estava na época limitado por altas demandas de produção. A experiência com a mudança de rolamento planejada anterior de uma linha irmã também desempenhou um papel importante na escalada do risco.
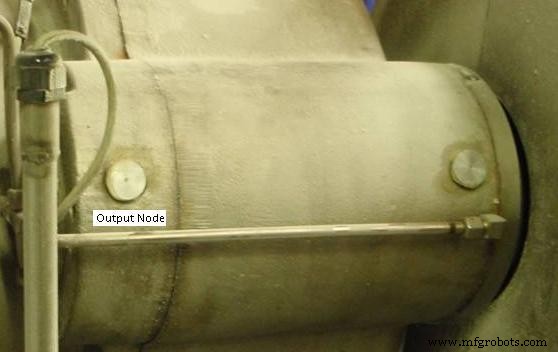
O lado de entrada de uma caixa de transferência é mostrado com o ponto do nó do rolamento de saída no lado esquerdo.
Em inspeções mais detalhadas, determinou-se que o rolamento com maior angústia era de fato o rolamento de saída suspeito. Cliques audíveis foram altos e claros no rolamento da extremidade de saída. Os dois rolamentos nas localizações dos nós estavam na linha de transmissão do motor nas extremidades de entrada e saída da caixa de transferência. Os rolamentos adjacentes na grande engrenagem redutora helicoidal ainda estavam com uma leitura baixa e não tinham cliques audíveis. O gerente de engenharia foi informado de que havia uma anomalia em um dos rolamentos de entrada, que os outros estavam em boas condições e que a produção poderia continuar com o monitoramento de condição direcionado. A amostragem de óleo de rotina foi aumentada de mensal para a cada duas semanas. As inspeções de AE foram aumentadas, com leituras de espectro agora em um ciclo de quatro dias. Isso daria alguma evidência comparativa quando os novos rolamentos foram eventualmente instalados.
A mudança planejada do conjunto de rolamentos foi combinada com o planejador de produção, gerente de manutenção e especialista de produto. Ficou claro que o equipamento teria que operar por pelo menos mais seis meses até estar disponível. Planos de contingência foram formulados para uma mudança de emergência se qualquer uma das leituras de AE ou amostras de óleo mostrasse avanços em direção ao fracasso. Foram emitidos avisos de que isso poderia ocorrer rapidamente se o rolamento falhasse. Um novo conjunto de rolamentos foi adquirido e uma reunião foi agendada com o fabricante do rolamento para examinar os rolamentos usados quando eles fossem trocados no início de 2011.
As leituras de AE permaneceram em um nível elevado durante esta longa fase de espera e os resultados das amostras de óleo não mostraram leituras elevadas nos principais elementos associados a falhas em rolamentos de rolos. Durante as semanas anteriores à renovação, muitos espectros foram obtidos de todos os pontos da caixa de engrenagens para avaliação futura. Isso excluiria as frequências da bomba de óleo e outros componentes ao redor da montagem. Um gráfico de espectro de envelope AE antes da mudança de direção é mostrado abaixo.
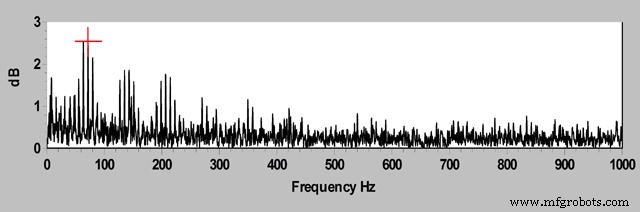
Como pode ser visto, havia algo criando um pico em 73 Hz, que coincidia com a frequência da pista do rolamento. Isso forneceu uma pista de que havia algum tipo de defeito na superfície da pista e não um elemento quebrando ou a gaiola se desintegrando.
A troca de rolamento finalmente ocorreu e a planta de produção foi revertida em 12 horas para que o equipamento não sofresse qualquer tempo de inatividade não planejado. O conjunto de rolamentos usado foi devolvido com a caixa de transferência e as duas unidades foram desengraxadas. Na primeira inspeção, ambos pareciam semelhantes e em boas condições. Os elementos e gaiolas foram então desmontados das raças externa e interna, com o cuidado de mantê-los em ordem e no aspecto correto para remontagem posterior.
Ficou claro que no rolamento de saída suspeito, uma grande fragmentação na pista interna havia se desenvolvido e cada elemento estava cheio dos detritos emitidos. Nesse ponto, um representante do fabricante do rolamento foi convidado para visitar e examinar os rolamentos. Ele concordou que os rolamentos duraram muito bem considerando a atmosfera e o calor em que operaram por quase 10 anos. Isso seria considerado um modo de falha de fim de vida. Pode ter durado muitos mais meses ou pode ter falhado em dias ou semanas. A fotografia abaixo é da lasca que media aproximadamente 10 mm de comprimento e 2,5 mm de largura.
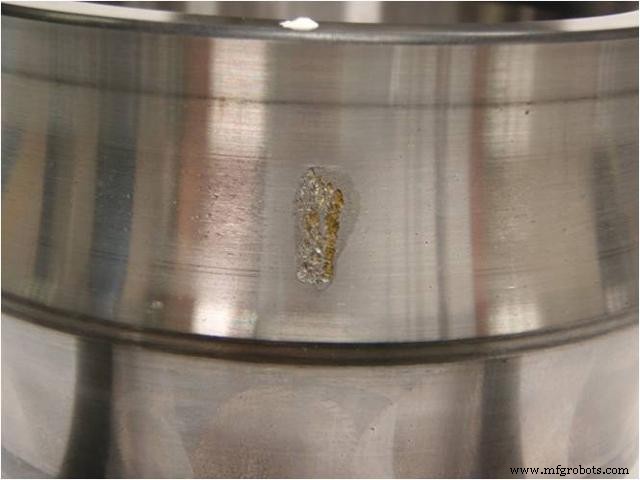
O dano por estilhaçamento na pista é mostrado acima com bordas emplumadas e corrosão superficial na área carregada da estilhaçamento. Observe a próxima camada de material no lado direito que cedeu.
Quando o trabalho corretivo foi concluído, amostras de espectro adicionais foram registradas e monitoradas para aprender mais. Os níveis de ruído do tapete foram mais baixos e a escala de decibéis foi um terço do exemplo do gráfico anterior. O pico máximo agora era inferior a 0,4 decibéis, enquanto o nível do carpete era inferior a 0,2 decibéis.
Em conclusão, os sistemas e ferramentas usados todos os dias provaram ser eficazes na captura dessa anomalia antes que ela se transformasse em um grande evento. A chave para isso foi o envolvimento total da engenharia com as operações para planejar o trabalho corretivo com o mínimo de interrupção possível.
Entre as lições aprendidas estavam que as frequências de inspeção em intervalos de sete dias estavam corretas para esta planta crítica, a ação preventiva foi iniciada na primeira oportunidade, o equipamento permitiu a localização da falha de rolamento, a instalação de áudio permitiu uma segunda referência que vinculou rpm com os cliques audíveis e que tudo isso deu evidência suficiente para o trabalho planejado começar na primeira oportunidade.
A análise da causa raiz foi realizada diretamente após a troca do rolamento ser concluída para investigar quaisquer recomendações futuras para a manutenção deste equipamento. Foi decidido que, como os rolamentos atingiram o fim de sua vida útil, não havia necessidade de alterar nenhuma manutenção planejada futura. O monitoramento de condição com AE forneceu a confiança para detectar quaisquer anomalias em um estágio muito inicial da curva.
Para obter mais informações sobre os sistemas de monitoramento de condição, visite Kittiwake Holroyd em www.kittiwakeholroyd.com.
Manutenção e reparo de equipamentos
- 5 dicas de computação em nuvem para colocar tempo (e dinheiro) do seu lado
- Monitoramento da temperatura ambiente com Raspberry Pi e Nagios
- Monitoramento da temperatura ambiente com Moteino e Raspberry Pi
- Monitorando a temperatura com Raspberry Pi
- Melhorando a manutenção proativa com monitoramento de lubrificação em tempo real
- Liderando com Persistência e Perseverança
- O monitoramento das condições aumenta e mantém a eficiência na produção de papel
- Tempo é dinheiro:dicas para usar software de manutenção para economizar tempo e gastar com mais eficiência
- Por que o monitoramento de carga é crítico em tempos de crise e além
- Data e hora do C++