Solução de problemas 101:Princípios gerais para consertar qualquer dispositivo
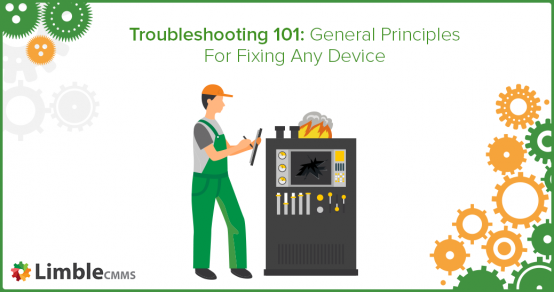
Tudo vai quebrar eventualmente. Quando a reinicialização não resolve o problema, fazemos um brainstorming das causas potenciais e testamos essas hipóteses para encontrar o problema. Resumindo, é a solução de problemas.
Os malfuncionamentos podem ficar caros rapidamente (como você sabe), portanto, um histórico de solução de problemas eficaz oferece credibilidade quando você diz que é hora de substituir em vez de consertar.
Este artigo analisa:
- O que é solução de problemas
- Algumas causas comuns
- Como agilizar o processo usando seu CMMS (sistema de gerenciamento de manutenção computadorizado)
O que é solução de problemas?
A solução de problemas é uma abordagem passo a passo para encontrar a causa raiz de um problema e decidir a melhor maneira de corrigi-lo para colocá-lo novamente em operação. A solução de problemas não é apenas para equipamentos que estão completamente quebrados. Também o usamos quando uma máquina simplesmente não está funcionando como esperado. A solução de problemas eficiente é uma parte essencial do gerenciamento, diagnóstico e reparo de ativos.
As máquinas operadas de maneira adequada e com manutenção regular têm menos probabilidade de sofrer grandes avarias. Ainda assim, nunca haverá uma chance zero de fracasso. Se você estiver usando um equipamento, ele precisará, em algum momento, conserto.
Quando e por que solucionar o problema?
Em termos gerais, a solução de problemas é feita nas seguintes instâncias:
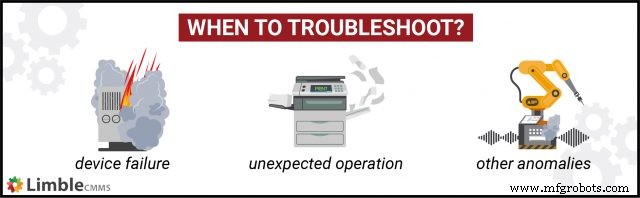
1) Falha do dispositivo
Este é o grande problema:o motivo mais urgente para solucionar o problema. A máquina está quebrada, totalmente fora de serviço e precisa ser consertada imediatamente para continuar funcionando. Isso pode ter um efeito indireto em uma empresa, interrompendo todas as operações e colocando tudo em espera.
O fato é que o tempo de inatividade não planejado é caro para as empresas, frequentemente custando centenas de milhares de dólares por minuto. Suponha que você tenha uma equipe de manutenção competente que sabe como solucionar problemas de forma eficaz. Nesse caso, você pode reduzir interrupções de alta gravidade e economizar dinheiro para a empresa.
Utilizar um CMMS moderno como o Limble para listas de verificação de solução de problemas pode ajudar a reduzir o tempo de inatividade. Como um bônus adicional, cada membro de sua equipe se torna mais valioso para você quando eles têm experiência na solução de problemas de forma eficiente e eficaz.
2) Operação inesperada
Cada máquina tem um conjunto definido de funções que pode executar. A maioria dos dispositivos não faz as coisas exatamente da mesma maneira todas as vezes por causa das limitações de engenharia e erro humano (por mais que possamos tentar evitar). Mesmo com essas pequenas variações no desempenho, a máquina pode operar sem problemas. Este é considerado seu intervalo de operação normal .
Se a máquina começar a funcionar fora dessas faixas, podemos ter um problema e isso precisa estar no radar de sua tripulação. Essas situações não são tão urgentes quanto um fracasso total. Ainda assim, operações inesperadas devem ser relatadas para corrigir o problema antes que um problema real apareça .
Pegue os ventiladores de refrigeração em sua planta, por exemplo. Imagine que eles estão correndo e expulsando ar fresco, mas de vez em quando, eles param de soprar por alguns minutos (ou o ar não está tão frio quanto deveria). Outro equipamento pode superaquecer por causa desse mau funcionamento e, eventualmente, começar a quebrar. Consertar o ventilador assim que você souber sobre ele economizará tempo e muito dinheiro para a empresa.
Fazer com que os usuários operacionais registrem as falhas quando elas aparecem pode ser uma ótima maneira de resolver os problemas o quanto antes e evitar a falha total. Usar seu CMMS para registrar o problema fornecerá um histórico escrito do que aconteceu e como foi corrigido, tornando o tempo de solução de problemas no futuro muito mais fácil.
3) Outras anomalias
A máquina está funcionando dentro da faixa operacional ideal e fornecendo a produção esperada. No entanto, um operador detectou alguma anomalia. Pode ser um som estranho, um cheiro estranho, fumaça visível, vibração excessiva, etc. Tais anomalias também devem ser investigadas dentro de uma janela de tempo apropriada.
O processo de relatar problemas nunca deve ser transformado em uma tarefa tediosa. É a única maneira de garantir que as pessoas o utilizem. Os usuários do Limble podem enviar e-mail, telefone, escanear um código QR ou registrar uma falha pessoalmente. O sistema ainda possui uma conta central que transformará e-mails em solicitações de trabalho e cria um hub central onde o histórico pode ser registrado e consultado posteriormente.
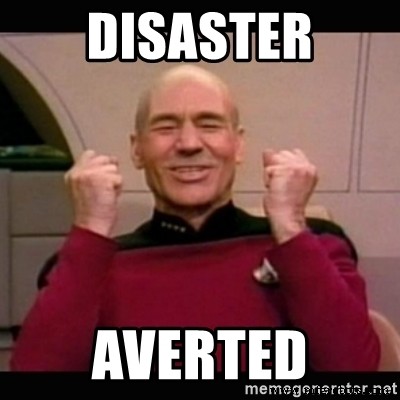
Com registros de histórico de ativos detalhados e experiência em solução de problemas, os usuários podem cuidar de tudo de forma independente. Isso vai liberar mais tempo para sua equipe se concentrar em coisas que são mais importantes.
Quais são os benefícios da solução de problemas?
Existem muitos custos associados à manutenção reativa e à falta de know-how para resolução de problemas. O que nem sempre consideramos é que esses custos vão além de dólares e centavos puros.
Um centavo economizado é um centavo ganho
Os custos imediatos são os custos mais aparentes ligados à manutenção e reparos. Esses são os dólares reais não planejados que custam para consertar equipamentos quebrados e defeituosos. Despesas como essas costumam fazer com que a equipe financeira fique em pé de guerra e se pergunte por que a manutenção é tão cara.
A longo prazo, quebras repetidas, falhas e paradas na produção podem levar à necessidade de trazer fornecedores caros para reparos e substituição do ativo.
Ser capaz de solucionar bem os problemas e ter todas as informações de que precisa ao seu alcance lhe dará a oportunidade de reformular a conversa e o relacionamento. Em vez de o Financeiro vir até você se perguntando por que tudo de que você precisa custa tanto dinheiro, você pode dizer:"Ei, olhe quanto economizamos para você. Isso poderia ter custado centenas, senão milhares mais ”.
Agora, no que diz respeito às finanças, você é o herói em vez do vilão.
O show deve continuar
O tempo de inatividade é caro - mais caro do que apenas o custo de consertar a máquina. Quando você tem um equipamento quebrado, ele interrompe suas atividades de geração de receita. Cada minuto que você não consegue operar, mais dinheiro sai pela janela. Quanto mais rápido sua equipe de manutenção puder voltar a trabalhar, mais dinheiro você economizará.
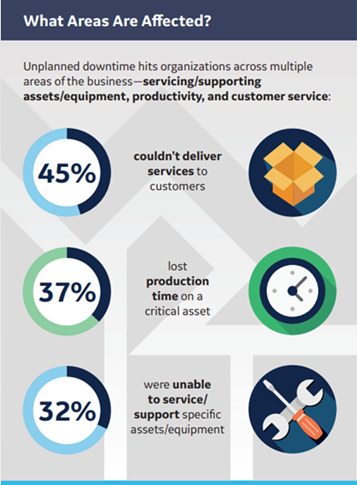
Em um estudo realizado por Vanson Borne da GE Digital for ServiceMax pesquisando 450 tomadores de decisões de TI e serviços em todo o mundo, eles descobriram que:
- Dos 82 por cento das empresas que tiveram paralisações não planejadas nos últimos três anos, essas interrupções duraram em média quatro horas e custaram em média US $ 2 milhões.
- O tempo de inatividade não planejado resulta na perda de confiança e produtividade do cliente - 46 por cento não conseguiram fornecer serviços aos clientes, 37 por cento perderam tempo de produção em um ativo crítico e 29 por cento foram totalmente incapazes de atender ou dar suporte a equipamentos ou ativos específicos.
Sua reputação em jogo
Quebras e interrupções contínuas na produção podem levar a danos à reputação e à falta de confiança de sua equipe e clientes. Se sua empresa não pode garantir a entrega de produtos e serviços, seus clientes irão para quem pode.
Quando os funcionários não podem fazer seus trabalhos porque o equipamento de que precisam não funciona e não podem obter ajuda, eles ficam frustrados. A perda de clientes pode eventualmente significar cortes de empregos. Ninguém quer trabalhar em um local onde há incerteza de trabalho.
Mas quando você tem uma equipe de manutenção que é eficaz na solução de problemas com um ótimo sistema para apoiá-los, eles ajudam a manter a reputação da sua empresa, o que ajuda a impulsionar a fidelidade à marca.
Em 2019, a Pacific Gas and Electric da Califórnia foi forçada a cortar a energia de mais de 2 milhões de pessoas para finalmente recuperar o atraso na manutenção que não faziam há anos. Foi comprovado que a falta de manutenção levou à queda das linhas de energia, que causou duas dezenas de incêndios florestais mortais. Mais do que provável, houve pequenos problemas ao longo do caminho que, se detectados, poderiam ter ajudado a evitar esses desastres. Posteriormente, a PG&E pediu concordata após ser considerada responsável por dezenas de bilhões de dólares em danos.
Quando não resolvemos os problemas de forma eficaz, os problemas pioram. As coisas se acumulam e a manutenção se torna reativa, não proativa. As coisas escapam pelas fendas ou são escovadas para debaixo do tapete, o que pode ter consequências devastadoras.
Substitua ou repare o dilema
Às vezes, faz mais sentido substituir o equipamento em vez de consertá-lo. Mas nem sempre é fácil pedir ao departamento financeiro para desembolsar dinheiro para novos equipamentos, especialmente se não fizer parte do orçamento original.
Ao rastrear a manutenção e os reparos em um CMMS com relatórios funcionais, você pode produzir informações factuais sobre a manutenção planejada e não planejada, custos, frequência de paralisações e perda de produtividade de qualquer ativo.
Os relatórios personalizados do Limble irão ajudá-lo a contar a história com mais facilidade para seus amigos em Finanças. Você pode medir quanto tempo de inatividade um ativo está causando e quanto isso está custando à empresa. Mostre isso para o Financeiro e, de repente, a discussão será vencida facilmente. O custo de substituição é justificado.
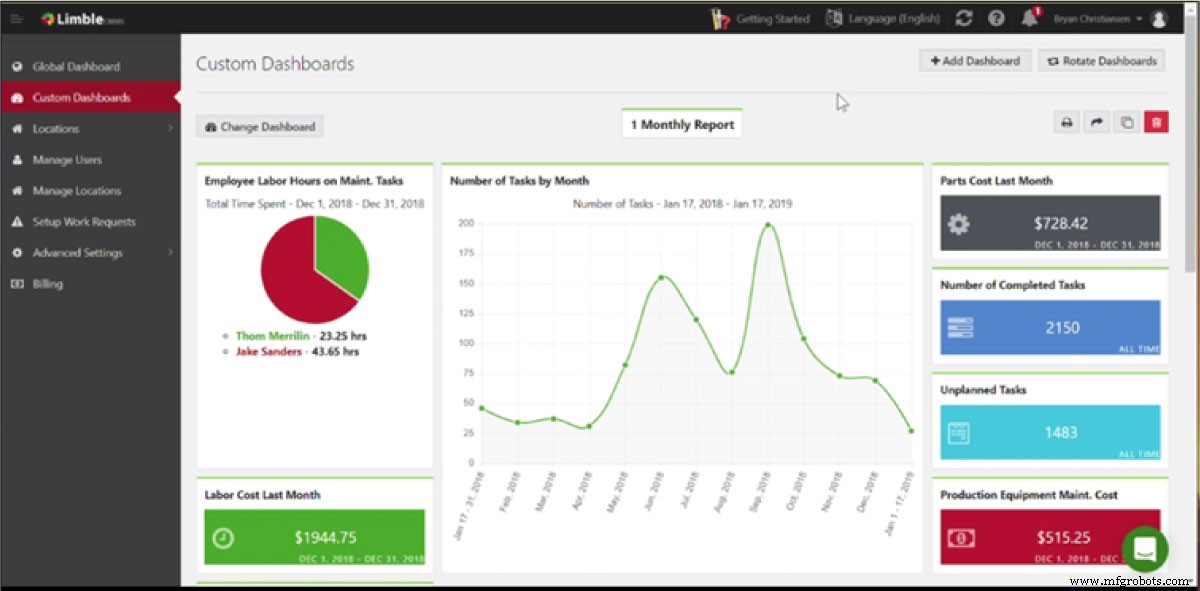
Exemplo de um painel personalizado no Limble CMMS
Solucionar problemas no mesmo dispositivo repetidamente pode ser extremamente irritante. Ter dados para fazer backup de sua recomendação de substituição pode economizar muito tempo, dinheiro e dores de cabeça para todos.
Quem realiza a solução de problemas?
Freqüentemente, os técnicos mais experientes são os responsáveis pela solução de problemas. Infelizmente, 60% desses profissionais de manutenção estão se aposentando nos próximos anos.
O que torna esses técnicos tão bons no que fazem? Muitos deles aprenderam por tentativa e erro quais são as melhores técnicas de solução de problemas para cada peça do equipamento. Há um valor enorme em ter esses técnicos sênior executando as equipes de solução de problemas e criando listas de verificação que abordam os problemas mais comuns.
O problema é que quando todos esses técnicos experientes se aposentam, eles levam seus conhecimentos consigo. Já existe uma grande escassez de mão de obra no setor. Suponha que não tenhamos codificado as informações em um hub central (como Limble). Nesse caso, corremos o risco de perder informações históricas valiosas quando eles partem.
A capacidade do Limble de rastrear o conhecimento histórico dos ativos torna mais fácil para um técnico ver todo o histórico de trabalho do ativo. Os usuários também podem adicionar notas e “peculiaridades” sobre a máquina que normalmente exigiriam muitas tentativas e erros para serem descobertas, economizando muito tempo.
Dependendo da complexidade da máquina, sua equipe de manutenção pode treinar usuários experientes para tarefas diretas de solução de problemas. Eles precisarão realizar verificações visuais, solução de problemas gerais e outras tarefas de manutenção para fazer isso. É uma abordagem conhecida como manutenção autônoma.
Se os usuários ou operadores estiverem solucionando problemas, você precisará de um método fácil de entender e amigável para coletar e salvar o máximo de informações possível. Isso pode tornar os reparos atuais e futuros muito menos complicados.
Todas essas informações (ordem de serviço, histórico de manutenção, listas de verificação, manuais, etc.) residem no Limble CMMS. Ter as informações certas facilmente acessíveis pode acelerar significativamente o processo de solução de problemas.
Etapas de solução de problemas
A solução de problemas é um processo passo a passo. Abaixo, nós o dividimos em seis etapas simples de seguir. Não importa se você é um profissional avançado ou inexperiente; você sempre seguirá a mesma abordagem sistemática.
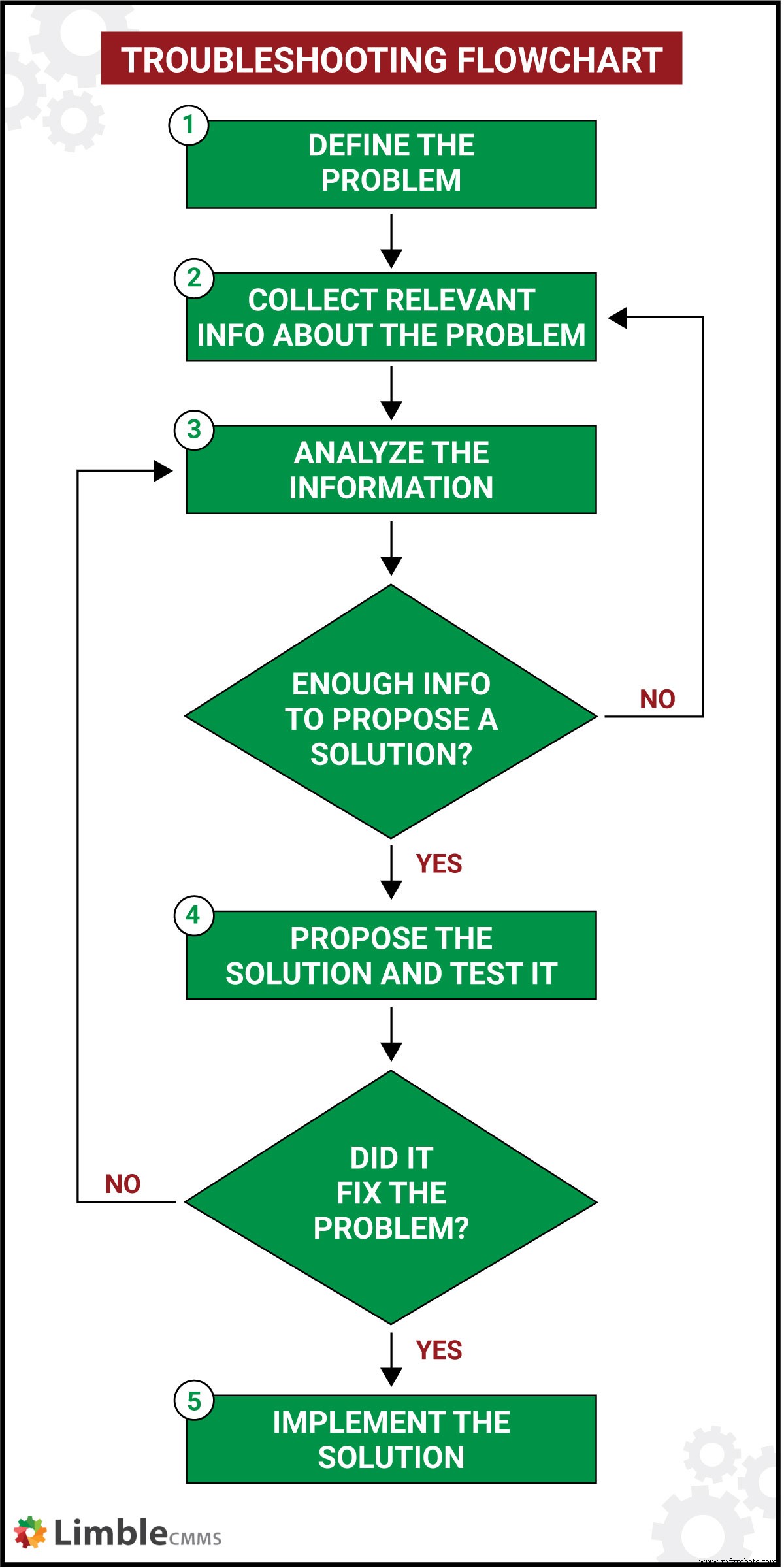
Etapa 1:Defina o problema
O primeiro passo para resolver qualquer problema é saber que tipo de problema é e defini-lo bem. Uma definição clara é fundamental para a solução de problemas.
Ao examinar um problema, você precisa saber o que está enfrentando e as possíveis causas. É uma falha da máquina, uma operação inesperada, erro do usuário ou uma anomalia aleatória? O que aconteceu que o alertou sobre o problema?
Alguns equipamentos terão maneiras integradas de informá-lo; alarmes podem soar, luzes vermelhas piscam ou um aviso pode disparar quando certas peças sobreaquecem. Esses sinais podem ajudar na resolução de problemas. Outros equipamentos simplesmente param de funcionar.
Seja qual for o caso, você deve identificar e definir o problema antes de seguir em frente.
Etapa 2:Colete informações relevantes
Você precisa reunir todas as informações disponíveis sobre a máquina e suas operações. Você vai precisar do manual da máquina, todos os dados relativos às operações. Por exemplo, quantas vezes a máquina é usada, por quem, por quê e por quanto tempo. Você também precisará do histórico de manutenção, relatórios de problemas, etc.
Um CMMS moderno como o Limble deve ter a opção de manter uma cópia digital de todos os documentos, histórico e informações. Se a comunicação com o Fabricante de Equipamento Original (OEM) for possível, a equipe de manutenção pode discutir o problema primeiro. Às vezes, ligar para o OEM é a maneira mais rápida e fácil de obter a ajuda certa.
Etapa 3:Analise os dados coletados
Usando todas as informações que você reuniu, listas de verificação disponíveis e todo o conhecimento técnico que puder reunir, agora você pode tentar determinar a causa raiz do problema. Procure a experiência de outros solucionadores de problemas de manutenção ou da pessoa que relatou a falha. É muito mais fácil resolver um problema que você viu antes.
Pense nas mudanças recentes no ativo. Pergunte a si mesmo:
- Usamos peças de reposição novas?
- Houve uma atualização recentemente?
- Mudamos o tipo de material de entrada que usamos?
- O dispositivo foi usado de maneira diferente do normal?
- Houve um pico de eletricidade?
Mudanças recentes no sistema ou ambiente geralmente podem explicar por que o problema surgiu.
Se você ainda não tem ideia do que causou o problema depois de analisar os dados, você precisa voltar para a Etapa 2 e coletar mais informações. É possível ignorar coisas ou desconsiderar algo tão sem importância durante a primeira rodada do processo de coleta de informações.
Após esse exercício, a pessoa que está realizando a solução de problemas deve formular uma estimativa fundamentada e apresentar algumas soluções.
Etapa 4:propor uma solução e testá-la
Usando o que você sabe de cima, você pode criar seu plano de ataque. Você chegará à solução por meio de um processo de eliminação e tentativa e erro. Em alguns casos, você pode testar sua teoria em um ativo de escala menor. Você pode ter várias opções para tentar. Comece com o mais simples primeiro e trabalhe a partir daí.
Leve o seguinte em consideração:
- potenciais preocupações de segurança
- todos os recursos necessários e custos associados
- quão complexa será a implementação
- as perspectivas de longo prazo para a máquina
- qualquer preconceito pessoal que a pessoa que realiza a solução de problemas pode ter
Continue testando até ter certeza de que encontrou a solução certa. Se nada funcionar, você precisará repensar qual é a causa real.
Etapa 5:Implementar a solução
Depois de diagnosticar com precisão o problema, encontrar a solução e testá-la, é hora de sujar as mãos e consertá-lo. Mesmo que sua solução tenha funcionado durante o teste, é importante testá-la novamente. Certifique-se de que o ativo está funcionando da maneira que deveria antes de embalar e assinar. Você também vai querer anotar todas as etapas que executa à medida que as executa, para que não se esqueça do que fez.
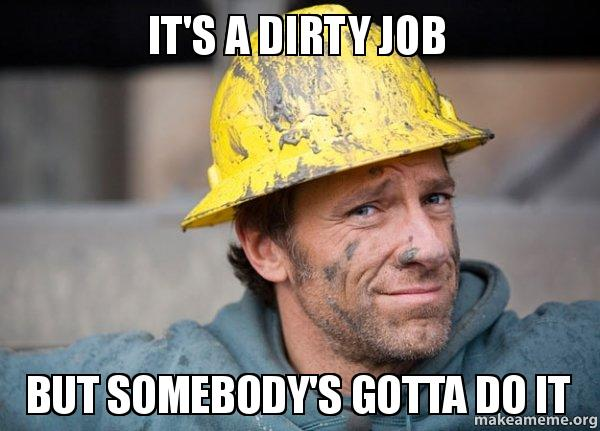
Etapa bônus:corrigida! Você é um herói! O que agora?
Parece óbvio, mas é crucial documentar a solução e adicione-o ao registro de ativos em seu CMMS. É fácil se deixar levar pelo trabalho e se esquecer de documentar suas descobertas. “Ah, farei da próxima vez”, você pode pensar. Mas e se você não se lembrar da próxima vez?!? Então estamos com problemas.
Conforme você avança no processo, reserve um tempo para fazê-lo certo e evite problemas da próxima vez.
Um kit de ferramentas de manutenção prático contém o máximo de informações possível sobre um ativo. Em Limble, rastrear o histórico de um ativo é ridiculamente fácil. Você pode ver todas as ordens de serviço relacionadas, peças que trabalharam mais recentemente - você pode até adicionar manualmente notas e imagens tiradas com seu telefone.
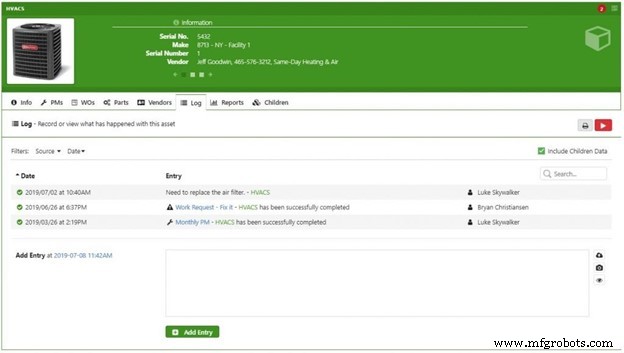
Exemplo de uma entrada de registro de ativos no Limble CMMS
Ao manter um registro de cada etapa, desde relatar a falha ou falha até as cinco etapas acima, você pode criar um caminho claro através da jornada de solução de problemas para reparar ou, em alguns casos, mostrar a necessidade de substituir o ativo.
Imagine como será fácil consertar se o problema se repetir!
Maneiras de facilitar a solução de problemas
Estamos aqui para facilitar o seu trabalho. Quando se trata de solucionar problemas, pode parecer opressor e desorganizado.
Existem muitas ferramentas disponíveis para ajudar você e sua equipe a resolver qualquer problema. Abaixo estão algumas das ferramentas e recursos comumente usados para uma solução de problemas eficaz.
Listas de verificação de solução de problemas
As listas de verificação são uma ótima maneira de abordar os problemas comuns de maneira metódica e ajudar a padronizar o processo. Eles fazem o trabalho pesado para você. Quando você tem muita coisa acontecendo, pode ser arriscado confiar em seu próprio cérebro para se lembrar de todas as etapas. Ter uma lista de verificação significa que você não precisa.
Plataformas de manutenção como Limble também permitem criar e armazenar listas de verificação de solução de problemas que podem ser acessadas em dispositivos móveis e usadas em campo.
Os engenheiros de manutenção podem trabalhar com técnicos experientes para identificar ativos problemáticos e criar instruções de solução de problemas passo a passo que incluem avisos e imagens para ativos / problemas específicos. Ao terminar, você pode anexar cada lista de verificação ao equipamento correspondente.
Um CMMS moderno
Ter o CMMS certo pode agilizar, organizar e automatizar suas operações de manutenção. Um CMMS moderno economizará muito tempo para você e sua equipe e muito dinheiro para sua empresa.
Como um repositório centralizado de dados de manutenção, um CMMS mantém muitas informações úteis usadas durante o processo de solução de problemas, como:
- Manuais OEM
- informações de contato para fornecedores de máquinas e peças
- registros e relatórios de manutenção
- detalhes da solicitação de trabalho enviada para relatar o problema
- solução de problemas e outras listas de verificação de manutenção
- dados anteriores e atuais de condição e desempenho da máquina coletados por meio de sensores CBM
Limble CMMS usa códigos QR para fornecer aos usuários acesso fácil a todas as informações sobre o equipamento com uma simples leitura do telefone. Eles podem escanear o código na lateral do equipamento e relatar rapidamente falhas para sua equipe com o ativo correto já anexado à ordem de serviço.
Ter acesso rápido e fácil a essas informações pode acelerar significativamente o processo de solução de problemas e reduzir a perda de conhecimento institucional quando os técnicos se aposentam ou seguem em frente. Esses são apenas alguns dos muitos motivos pelos quais mais e mais organizações estão implementando soluções de manutenção baseadas em nuvem.
O futuro da solução de problemas
As fábricas estão se tornando mais automatizadas e as máquinas precisam de menos operadores. Por causa dessas mudanças, o número de técnicos necessários para solução de problemas e manutenção de equipamentos está crescendo.
Felizmente, a tecnologia está tornando a solução de problemas mais fácil, rápida e menos perigosa. Aqui estão algumas soluções que estão chegando a muitos andares de fábricas.
Um robô com uma bola de cristal
Você pode imaginar um mundo onde os computadores se consertam? O aprendizado de máquina é um passo nesse sentido. Dá aos sistemas a capacidade de aprender e melhorar as coisas sem serem programados. Pode ajudar a prever possíveis problemas e é uma grande parte da manutenção preditiva.
Quando se trata de solução de problemas, o aprendizado de máquina está nos ajudando a analisar grandes quantidades de dados e identificar / prever possíveis causas de falhas e falhas.
Algumas organizações já estão avançando um pouco mais e testando algo chamado análise prescritiva. No contexto da solução de problemas, a análise prescritiva visa ajudar as máquinas a se diagnosticar e, em seguida, apresentar possíveis soluções com base nesse autodiagnóstico.
Aprimorando o mundo real com AR
A realidade aumentada (AR) combina imagens geradas por computador com o equipamento real para fornecer uma camada adicional de informações. Você pode sobrepor partes e olhar para coisas que normalmente não seria capaz de fazer.
Tudo que você precisa é um telefone ou tablet carregado com o software. Segure-o sobre a máquina e o programa irá puxar todas as diferentes camadas para você olhar.
Se você estiver no meio de um diagnóstico, essa pode ser uma ótima maneira de verificar se tudo está onde deveria estar ou de se tudo está funcionando corretamente.
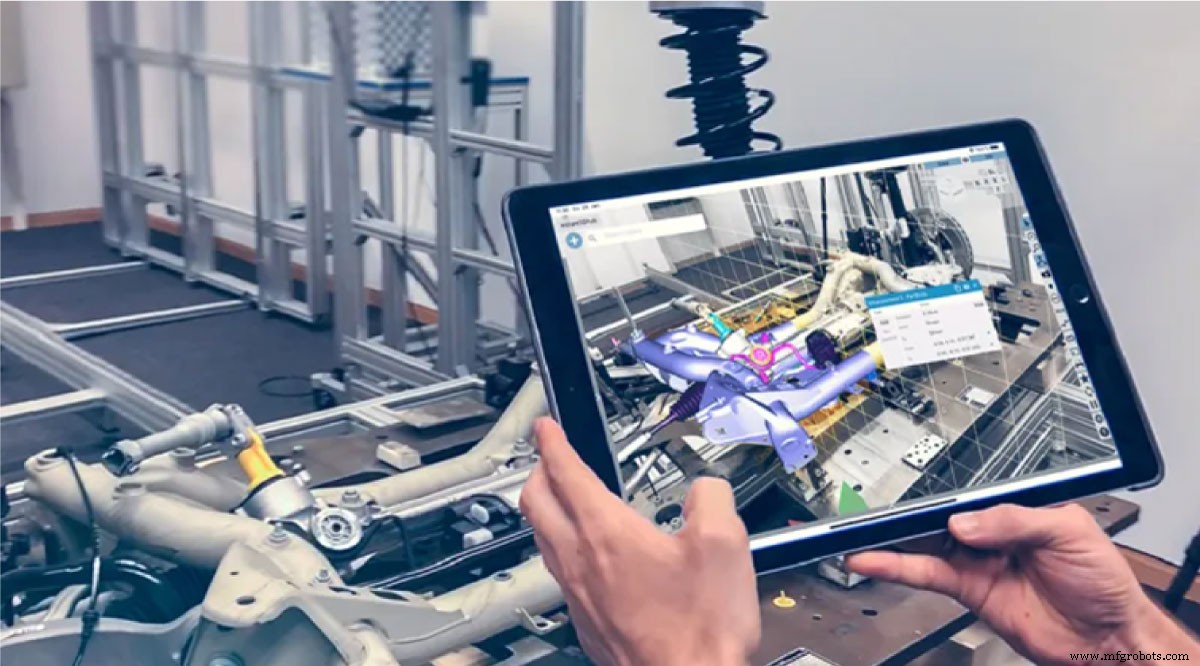
Realidade aumentada no controle de qualidade. Fonte: Metrology.news
AR permite que sua equipe de manutenção veja todas as informações sobre um componente na tela. Ele também pode mostrar dicas, avisos e próximas etapas, melhorando a qualidade e a segurança durante o processo de solução de problemas.
Simulações e realidade virtual
Achou que AR era legal? Veja isso.
A realidade virtual (VR) leva você a um mundo de possibilidades infinitas enquanto você é levado para um ambiente simulado da máquina em que está trabalhando. Neste ambiente virtual, equipamentos caros não podem ser danificados e você não pode se machucar.
É uma ótima maneira de aprender, brincar, experimentar e praticar antes de ter que retornar ao mundo real para consertar a máquina real. Você pode ter uma experiência 100% envolvente consertando coisas. É como transformar seu trabalho em um videogame.
Gêmeo digital (não maligno)
Um gêmeo digital é uma cópia virtual de sua máquina. Os sensores instalados em sua máquina enviam dados sobre sua condição e desempenho. Esta cópia baseada na nuvem analisa esses dados (que vêm de dezenas ou centenas de andares de produção diferentes que usam o mesmo tipo de máquina) e os usa para avançar a tecnologia, prever falhas e encontrar maneiras de reparar problemas à distância.
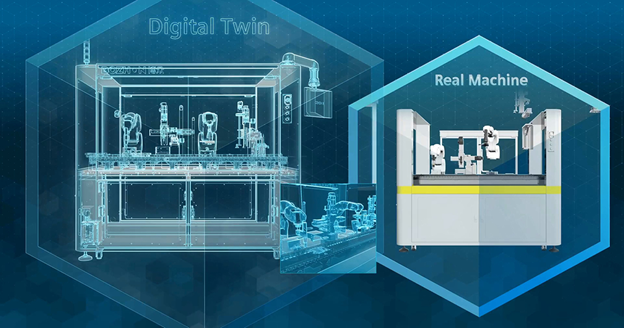
Gêmea digital na manufatura. Fonte: Siemens
Se ocorrer uma falha em sua localização, o OEM pode compará-la com os dados de todas as outras máquinas do mesmo tipo. Com base na meta-análise, o OEM pode identificar se um incidente semelhante aconteceu com uma máquina em alguma outra planta - e propor uma solução potencial.
É isso
Na melhor das hipóteses, um dispositivo com defeito resultará em um incômodo leve. No pior cenário, pode causar um incidente de segurança e ter um efeito debilitante nos resultados financeiros de uma empresa.
Saber lidar rapidamente com problemas de equipamentos é um reflexo do departamento de manutenção e da capacidade de organizar o trabalho e treinar seus funcionários. Visto que habilidade e experiência são tão importantes, as empresas devem fazer um esforço extra para reduzir a rotatividade de técnicos e operadores experientes.
Se você tiver alguma dúvida sobre solução de problemas, pule para a seção de comentários abaixo. Se você quiser saber mais sobre o Limble CMMS, pode entrar em contato conosco diretamente ou iniciar um teste gratuito.
Manutenção e reparo de equipamentos
- Dicas gerais para solução de problemas
- DHT Tiny Breakout para Raspberry Pi
- Ao solucionar problemas de equipamento, as primeiras impressões são importantes
- Como remover um rolamento para reparo
- Automação:Novas garras para Cobots
- Saber quando usar sensores para soldagem robótica
- Principais dicas de manutenção e solução de problemas para drives de frequência variável
- Dicas para solucionar problemas de PLCs problemáticos
- Quando considerar o reparo DIY para sua eletrônica industrial
- Dicas para reparos e solução de problemas do servo motor