Desvendando a evolução morfológica e cinética de corrosão de nanofios de silício poroso durante a corrosão química assistida por metal
Resumo
Muitas aplicações potenciais de nanofios de silício poroso (SiNWs) fabricados com corrosão química assistida por metal são altamente dependentes do controle preciso da morfologia para a otimização do dispositivo. No entanto, os efeitos dos principais parâmetros de corrosão, como a quantidade de catalisador de metal depositado, razão molar HF-oxidante ( χ ), e a concentração de solvente na morfologia e na cinética de corrosão dos SiNWs ainda não foram totalmente exploradas. Aqui, as mudanças na nanoestrutura e na taxa de corrosão do silício do tipo p dopado degenerativamente em um HF – H 2 O 2 –H 2 O sistema de corrosão com catalisador de prata depositado sem eletrodos são sistematicamente investigados. A morfologia da superfície evolui de uma estrutura microporosa e com crateras para um arranjo uniforme de SiNWs em χ suficientemente alto valores. As taxas de corrosão na base e ponta da nanoestrutura são correlacionadas com a corrosão primária induzida por Ag e a corrosão secundária induzida por íons metálicos e orifícios difusos, respectivamente. O H 2 A concentração de O também afeta o χ janela onde os SiNWs se formam e as taxas de corrosão, principalmente pela modulação da diluição do reagente e da taxa de difusão. Ao controlar a corrosão secundária e a difusão do reagente por meio de χ e H 2 Na concentração de O, respectivamente, a fabricação de SiNWs altamente dopados com controle independente da porosidade do comprimento é demonstrada com sucesso, o que pode ser potencialmente utilizado para melhorar o desempenho de dispositivos baseados em SiNW.
Histórico
Apesar dos avanços na pesquisa em vários materiais novos, o silício continua sendo um dos substratos mais atraentes para a fabricação de nanoestruturas devido à sua abundância na natureza e à existência de técnicas bem desenvolvidas para integração de dispositivos. Nos últimos anos, nanoestruturas de silício unidimensionais, como nanofios de silício (SiNWs) e nanopilares, continuaram a atrair a atenção em uma ampla gama de aplicações, como fotovoltaica [1, 2], termoelétrica [3, 4], armazenamento de energia [5,6,7], eletrônica flexível [8], sensoriamento bioquímico [9] e interface biológica [10]. Além das propriedades elétricas, ópticas, térmicas e mecânicas exclusivas de tais nanoestruturas, um impulsionador principal para seu apelo sustentado é o desenvolvimento de novas técnicas de fabricação que permitem a formação fácil das nanoestruturas, mantendo um excelente controle sobre a morfologia e as propriedades físicas. Dentre as várias técnicas de fabricação, o ataque químico assistido por metal (MACE) se destaca do ponto de vista industrial por sua simplicidade, baixo custo e flexibilidade [11, 12]. Usando MACE, escala de wafer, SiNWs sem defeitos com comprimento, porosidade, condutividade, nível de dopagem e orientação de cristal definidos podem ser obtidos simplesmente selecionando o wafer de Si apropriado, composição de corrosão, temperatura de reação e tempo de reação [13,14, 15,16,17,18,19,20,21,22,23]. O controle do diâmetro de SiNW, da seção transversal e do passo da matriz também pode ser obtido por meio de técnicas de padronização de catalisador, como litografia de nanosfera [24], litografia de interferência [25] e litografia de copolímero em bloco [26]. Isso está em contraste com outras técnicas de fabricação, como corrosão iônica reativa e métodos de vapor-líquido-sólido, que requerem equipamentos caros e podem produzir nanofios com defeitos de superfície, orientações cristalográficas não controladas e formas transversais limitadas [11].
Na última década, a fabricação de SiNWs a partir de wafers de Si altamente dopados usando MACE tem sido de particular interesse por causa dos SiNWs porosos resultantes com alta qualidade cristalina [14, 17, 19]. A estrutura porosa permite que os nanofios adquiram propriedades altamente desejáveis, como fotoluminescência sintonizável [15], baixa condutividade térmica [27] e alta área de superfície específica [28], tornando-os materiais promissores para optoeletrônica [14, 16], termoelétrica [ 3, 27], fotocatálise [28, 29] e armazenamento de energia [5]. Em combinação com sua fotoluminescência e alta área de superfície, a biocompatibilidade e biodegradabilidade de SiNWs porosos em ambientes fisiológicos também os tornam candidatos adequados para biolabeling [15] e aplicações de entrega de drogas [30]. Embora SiNWs relativamente porosos possam ser obtidos com wafers de Si de baixo dopagem, utilizando altas concentrações de oxidante no condicionador [15], o uso de Si altamente dopado é vantajoso onde a alta condutividade elétrica é necessária, visto que evita a necessidade de dopagem pós-condicionamento degrau. Isso é especialmente verdadeiro em aplicações termoelétricas de SiNWs porosos, onde o aumento na figura de mérito é devido à diminuição da condutividade térmica sem degradação significativa da condutividade elétrica [27]. Por outro lado, foi relatado que a resistência dos SiNWs porosos é bastante grande em comparação com a dos SiNWs sólidos [14], implicando em uma compensação entre o grau de porosidade e a condutividade elétrica.
A fim de realizar o potencial de SiNWs porosos nas aplicações mencionadas acima, é imperativo compreender completamente os efeitos de vários parâmetros de corrosão durante MACE de Si altamente dopado. Uma série de estudos [13,14,15,16,17, 19,20,21, 23] fabricaram com sucesso SiNWs altamente dopados com diferentes comprimentos e porosidades usando MACE em HF – H 2 O 2 etchant. Suas investigações lançaram luz sobre o efeito do H 2 O 2 concentração [14,15,16,17, 20, 21, 23], concentração de HF [21], HF-H 2 O 2 proporção de volume [19], duração de corrosão [14, 16, 17, 19,20,21, 23] e temperatura de corrosão [19,20,21, 23] na porosidade [14, 16, 17, 19, 20] , comprimento [16, 17, 19,20,21, 23], taxa de corrosão [15] e morfologia geral [15, 16, 21] das matrizes SiNW. No entanto, estudos sistemáticos sobre o efeito do condicionador HF – H 2 O 2 razão molar, definida como χ =[HF] / ([HF] + [H 2 O 2 ]), e H 2 A concentração de O na formação de nanoestruturas de Si altamente dopadas é limitada. Isso apesar do fato de χ é um parâmetro chave na determinação da morfologia e taxa de corrosão de nanoestruturas de Si [18, 31], enquanto [H 2 O] é fundamental na formação de SiNWs em áreas micro-padronizadas [18]. Até o momento, apenas Chiappini et al. [15] e Balasundaram et al. [19] utilizaram uma ampla gama de χ valores (0,4–0,98 e 0,7–0,99, respectivamente) na fabricação de SiNWs altamente dopados, embora nenhum tenha explorado totalmente o efeito do condicionador [H 2 O]. Além disso, apesar de uma série de estudos elucidando o mecanismo para a evolução morfológica, porosificação e afilamento de SiNWs leve e altamente dopado fabricados com MACE [15, 17, 32], o mecanismo de evolução do comprimento devido aos efeitos concorrentes do metal depositado corrosão, corrosão de metal nucleada, difusão em orifícios e difusão de reagentes não foram totalmente investigados. Neste estudo, MACE de duas etapas [33] em bolachas de Si tipo p dopadas degenerativamente usando catalisador Ag depositado sem eletrodos e H 2 O 2 oxidante foi executado. Comparado com MACE usando catalisador de Au padronizado, a deposição sem eletrodos pode formar apenas SiNWs distribuídos aleatoriamente com diâmetros variados [13], enquanto Ag pode limitar as relações de aspecto de SiNW alcançáveis devido à sua dissolução mais rápida do que Au [11]. No entanto, o uso de deposição química e catalisador Ag em MACE é considerado a forma mais simples e barata de formar nanoestruturas de Si, incluindo SiNWs. A fim de explorar os efeitos da composição do agente de corrosão nas nanoestruturas e taxas de corrosão resultantes, os agentes de corrosão com uma faixa relativamente ampla de χ e [H 2 Valores O] foram utilizados. Ao determinar a cinética de corrosão na ponta e na base das nanoestruturas de Si, uma visão sobre os efeitos da injeção de orifício e taxas de dissolução de Si, corrosão secundária induzida por íons metálicos dissolvidos e orifícios difusos e taxa de difusão de reagentes na morfologia resultante e comprimento de as nanoestruturas são fornecidas. SiNWs altamente dopados com os mesmos comprimentos também foram fabricados usando condicionadores compostos de diferentes χ e [H 2 Valores O], mostrando assim que a porosidade pode ser efetivamente ajustada pela composição de corrosão, apesar das durações de corrosão variadas.
Métodos
Bolachas de Si (100) tipo p dopadas com boro polidas de lado único com uma resistividade de 0,001–0,005 Ω cm e uma camada de óxido térmico de 50 nm no lado polido foram usadas como o material de partida. As bolachas foram completamente limpas com água desionizada (DI), acetona e etanol, e o óxido térmico foi removido com HF diluído, resultando em superfícies de Si terminadas em H. Para confinar a corrosão na superfície de Si polida, a parte de trás das bolachas de Si foi revestida com fotorresiste (AZ5214). Amostras de Si para os experimentos MACE foram obtidas clivando as bolachas em 1 × 1 cm 2 peças. Amostras de Si do mesmo wafer foram usadas para cada conjunto de experimentos.
O MACE foi realizado usando um processo de corrosão de duas etapas que consiste na deposição sem eletrodos do catalisador Ag e, em seguida, a corrosão em HF – H 2 O 2 soluções, como mostrado esquematicamente na Fig. 1. As peças de Si foram primeiro imersas em HF 5% por 3 min. A deposição química de nanopartículas de Ag (AgNPs) no substrato de Si foi então realizada em uma solução aquosa contendo 4,8 M HF e 0,005 M AgNO 3 para durações de tempo diferentes (Fig. 1a). Após lavagem suave com água DI, as amostras de Si revestidas com AgNP foram gravadas em HF – H aquoso 2 O 2 soluções com diferentes χ e [H 2 O] valores (ver arquivo adicional 1:Tabela S1) para diferentes durações de tempo (Fig. 1b). As amostras de Si gravadas foram completamente enxaguadas com água DI e, em seguida, imersas em 1:1 ( v / v ) HNO 3 por 10 min para dissolver os AgNPs. Após outro enxágue completo com água DI, as amostras de Si foram embebidas em HF 5% por 3 min para remover qualquer camada de óxido formada e, em seguida, enxaguadas novamente com água DI várias vezes. Deposição de Ag e HF – H 2 O 2 gravura foram realizadas no escuro. Todas as amostras foram processadas à temperatura ambiente (22–23 ° C) em copos de plástico separados contendo 15 ml da solução necessária.
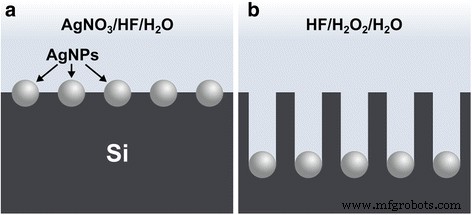
Vista esquemática em corte transversal da fabricação de nanoestruturas de Si usando MACE de duas etapas. a Na primeira etapa, os AgNPs são depositados sem eletrodos na superfície do Si em uma solução aquosa contendo AgNO 3 e HF. b Na segunda etapa, os AgNPs catalisam a corrosão do substrato de Si em uma solução composta de HF, H 2 O 2 , e H 2 O, levando à formação de nanoestruturas de Si
As superfícies de Si gravadas foram caracterizadas por microscopia eletrônica de varredura (SEM, Phenom Pro ou FEI / Philips XL-30) e microscopia eletrônica de transmissão (TEM, Philips CM20). Para preparar as amostras para observação em MEV, o fotorresiste na parte traseira foi removido com acetona. As amostras de Si foram então enxaguadas com etanol e secas em uma placa de aquecimento para minimizar a aglomeração de SiNW devido à evaporação da água [19].
Resultados e discussão
Deposição de catalisador de prata e formação de SiNWs porosos
O efeito da duração da deposição de Ag (10 sa 15 min) em uma solução de 0,005 M AgNO 3 e 4,8 M HF na formação de SiNWs altamente dopados foi investigado. Quando as amostras carregadas de Ag foram gravadas em uma solução contendo 4,8 M H 2 O e χ =0,95 por 30 min, tempos de deposição curtos (≤2 min) resultaram em uma matriz densa de poros verticais com alguns poços laterais, como mostrado na Fig. 2a. No entanto, os poros não eram densos o suficiente para formar estruturas de nanofios bem separadas se o tempo de deposição fosse ≤1 min. Por outro lado, SiNWs que quase não tinham defeitos foram obtidos com um tempo de deposição de Ag de 4 min (Fig. 2b), com tempos de deposição mais elevados resultando em SiNWs sem corrosão. Além das mudanças na morfologia do SiNW, uma variação não monotônica na taxa de corrosão do SiNW em relação ao tempo de deposição de Ag também foi observada, conforme mostrado na Fig. 2c (símbolos de diamante). A taxa de corrosão SiNW aumentou de um tempo de deposição de 10 s para 4 min, mas diminuiu inesperadamente entre 4 min e 6 min. Posteriormente, a taxa de corrosão aumentou novamente até 15 min, embora com valores de taxa de corrosão relativamente mais baixos.
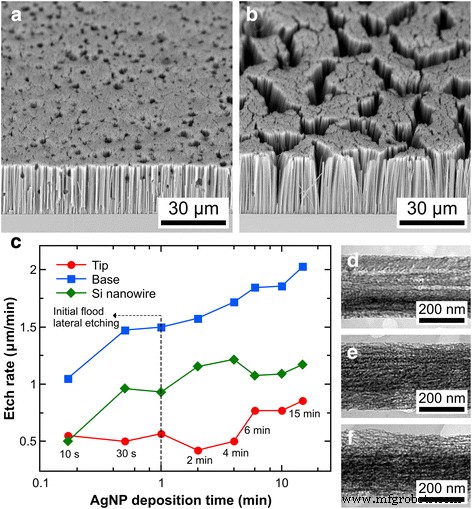
SiNWs fabricados usando uma solução de deposição de Ag contendo 0,005 M de AgNO 3 e 4,8 M HF e uma solução de corrosão composta por 48 M H 2 O e 0,95 HF – H 2 O 2 razão molar. Imagens SEM dos SiNWs para tempos de deposição de Ag de a 30 se b 4 min. c Taxa de corrosão dos SiNWs para diferentes tempos de deposição de Ag. Imagens TEM da seção intermediária dos SiNWs para tempos de deposição de Ag de d 4, e 10, e f 15 mostrando o grau de porosidade. A duração do ataque para todas as amostras foi de 30 min
A fim de levar em conta a tendência peculiar na taxa de corrosão do SiNW, as taxas de corrosão na ponta e na base dos SiNWs também foram determinadas a partir das imagens de seção transversal de SEM, alinhando a micrografia de uma amostra de Si gravada com a de um Si não esticado amostra do mesmo wafer na parte traseira (consulte o arquivo adicional 1:Figura S1). Na Fig. 2c, pode-se ver que a taxa de corrosão na base SiNW (símbolos quadrados) aumenta monotonicamente com o tempo de deposição de AgNP. Por outro lado, três domínios podem ser vistos a partir da linha de tendência da taxa de corrosão da ponta SiNW (símbolos de círculo):(a) ≤1 min, onde a taxa de corrosão é relativamente alta; (b) entre 1 e 6 min, onde a taxa de corrosão é relativamente baixa; e (c) ≥6 min, onde a taxa de corrosão é a mais alta. Assim, o aumento inicial na taxa de corrosão SiNW do tempo de deposição de 10 s para 1 min foi devido ao aumento constante na taxa de corrosão na base, enquanto o aumento subsequente na taxa de corrosão nos tempos de deposição de 2 e 4 min foi devido a as taxas de corrosão relativamente baixas nas pontas. Enquanto isso, a queda na taxa de corrosão SiNW no tempo de deposição de 6 min e as taxas de corrosão relativamente baixas nos tempos de deposição sucessivos foram causadas pelo aumento na taxa de corrosão nas pontas.
Uma vez que a cobertura da superfície de AgNPs está diretamente relacionada ao tempo de deposição de Ag [22, 34, 35], a corrosão lateral para tempos de deposição baixos pode ser atribuída a uma rede de Ag esparsa [18, 34, 36] com alguns AgNPs isolados movendo-se para dentro direções <100> aleatórias devido à sua forma irregular [37]. Espera-se que a taxa de corrosão de SiNW na base aumente com o tempo de deposição de Ag devido ao aumento na quantidade de catalisador de Ag, que fornece mais área de superfície para injeção de furo por H 2 O 2 . Além disso, uma quantidade maior de Ag também significa mais Ag oxidado por H 2 O 2 [15, 17], resultando em uma concentração mais alta de Ag + íons que podem contribuir para a dissolução de Si por meio de uma reação de deslocamento galvânico [31]. Por outro lado, as taxas de corrosão relativamente altas nas pontas para tempos de deposição de Ag ≤1 min podem ser explicadas por uma corrosão lateral de inundação inicial causada por AgNPs de formato irregular da rede Ag esparsa. Os aumentos subsequentes na taxa de corrosão da ponta com o aumento do tempo de deposição de Ag podem ser atribuídos a taxas crescentes de renucleação de metal [17, 38] nas pontas e, em menor extensão, difusão em furo [31, 39].
Houve um aumento geral na porosidade dos SiNWs fabricados conforme o tempo de deposição de Ag aumentou, conforme mostrado na Fig. 2d-f. (Consulte o arquivo adicional 1:Figura S2a-c para imagens TEM complementares.) Esses aumentos na porosificação são esperados devido a concentrações mais altas de Ag + íons, que resultam em metal nucleado e corrosão induzida por íons [15, 17, 38]. Além disso, taxas mais altas de injeção de orifícios também podem ter resultado em orifícios mais difusos, o que pode contribuir para a formação de poros [19, 39]. A estrutura porosa dos SiNWs parece ocorrer como uma casca porosa na maioria dos nanofios, semelhante ao que foi observado em estudos anteriores [14, 17]. Para alguns SiNWs com um tempo de deposição de Ag de 15 min, as paredes laterais parecem consideravelmente mais ásperas com manchas escuras relativamente grandes (diâmetro de ≈20 nm), provavelmente devido a partículas maiores de Ag renucleadas. No entanto, a distribuição da porosidade não é nítida:alguns SiNWs com um tempo de deposição de Ag de 4 min têm quase a mesma porosidade que os SiNWs com um tempo de deposição de Ag de 10 min; o mesmo pode ser dito de SiNWs com tempos de deposição de Ag de 10 e 15 min. Isso provavelmente se deveu aos SiNWs obtidos de diferentes áreas da amostra, que experimentaram taxas de porosificação ligeiramente diferentes dependendo da quantidade real de AgNPs depositados (ou re-nucleados) e da concentração de decapante não reagido, que deverá ser maior nas laterais da amostra. No entanto, a tendência geral observada aqui indica que a quantidade total de Ag depositado fornece outro grau de liberdade no controle da porosidade dos SiNWs.
O grau de porosidade aumenta da base até a ponta dos SiNWs (ver Arquivo adicional 1:Figura S2d – l), semelhante ao de estudos anteriores [16, 19]. Isso é esperado devido à exposição mais longa das regiões superiores dos nanofios ao condicionador [19]. Por outro lado, a maioria dos SiNWs tem um perfil longitudinal cônico, o que é característico de SiNWs altamente dopados fabricados usando Ag-MACE devido à dissolução contínua dos AgNPs na base do SiNW e à nucleação em outros locais [15, 17 ] No entanto, havia alguns SiNWs com um perfil ligeiramente bicônico ou de ampulheta, ou seja, a seção transversal do meio é maior ou menor, respectivamente, do que as seções superior e inferior. Isso sugere que o celular Ag + íons poderiam ser redepositados não apenas nas seções superiores dos nanofios, mas também em AgNPs vizinhos na base.
Composição Etchant e evolução morfológica de nanoestruturas de Si
A morfologia das nanoestruturas resultantes em Si dopado degenerativamente foi determinada usando χ valores de 0,7 a 0,99 e H 2 Concentrações de O de 46, 48 e 50 M. A deposição sem eletrodos de AgNPs foi realizada em uma solução de 0,005 AgNO 3 e 4,8 M HF por 4 min, durante a corrosão em HF – H 2 O 2 –H 2 As soluções de O foram realizadas por 30 min. A Figura 3 mostra a morfologia da superfície de Si vista a partir do SEM. Para [H 2 O] =46 M e 48 M, as características no Si gravado evoluem de Si microporoso com crateras ( χ =0,7 e 0,75, Fig. 3d, e), para macroporos com poros profundos ( χ =0,75 e 0,80, Fig. 3f), e então para SiNWs ( χ ≥ 0,85). Para [H 2 O] =50 M, a evolução da superfície de Si é ligeiramente diferente:do Si polido ( χ =0,7), para macroporos com poros profundos ( χ =0,75), para Si microporoso com crateras ( χ =0,8–0,85), e então para SiNWs ( χ ≥ 0,9). Em contraste com o trabalho de Chiappini et al. [15], SiNWs sobre um filme de Si poroso por 0,7 < χ <0,95 não foram observados, e estruturas apenas de SiNW foram obtidas em um χ maior intervalo ( χ ≥ 0,85 em vez de χ > 0,95). Essas diferenças foram provavelmente devido às variações na quantidade de AgNPs depositados, tempo de decapagem, H 2 Concentrações de O e HNO 3 e tratamentos pós-corrosão HF.
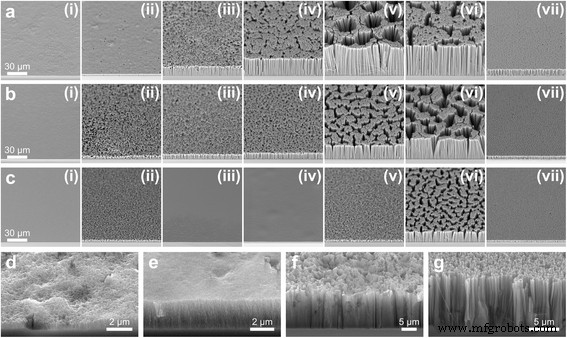
Imagens SEM da superfície de Si gravada em soluções com H 2 Concentrações de O de a 46 milhões, b 48 M e c 50 M e HF – H 2 O 2 razões molares de (i) 0,7, (ii) 0,75, (iii) 0,8, (iv) 0,85, (v) 0,9, (vi) 0,95, e (vii) 0,99. d - g Imagens SEM de alta ampliação das amostras em a (i) , (ii ), ( iii ), e (vii ), respectivamente. As amostras foram gravadas em HF – H 2 O 2 por 30 min
As morfologias de Si obtidas podem ser explicadas em termos de densidade de corrente na interface Ag – Si e Ag + corrosão induzida por íons [15, 17, 31, 38]. A formação de SiNWs em alto χ valores (≥0,85 ou 0,9) podem ser atribuídos à formação de Si microporoso em baixas densidades de corrente com subsequente dissolução do Si microporoso por polimento [31, 38]. Um mecanismo semelhante foi provavelmente responsável pela formação de Si macroporoso com poros profundos em χ inferiores valores, exceto que as densidades de corrente mais altas na extremidade do poro resultaram na formação de óxido e subsequente difusão do orifício [31], resultando em macroporos rasos na superfície superior. Espera-se que a difusão desse furo seja particularmente significativa para o tipo p de Si altamente dopado por causa da altura da barreira Schottky positiva que puxa os furos injetados para longe da interface metal-Si [40]. Também é possível que o valor relativamente alto [H 2 O 2 A razão] para [HF] levou a significativa dissolução de Ag, que por sua vez resultou na baixa densidade de poros profundos no substrato de Si. Por outro lado, o aparecimento de Si microporoso com crateras em χ =0,7–0,85 indica a ocorrência de baixas densidades de corrente neste χ intervalo, o que é consistente com a observação de Chartier et al. [31] Além disso, a porosificação concomitante de Si por Ag + também é esperado que ocorram íons neste regime. A formação de SiNWs em um χ superior valor para o condicionador mais diluído (50 M H 2 O) é consistente com a observação de Chiappini et al. [15] que concentrações mais altas de etanol favorecem a formação de Si poroso e polido ao invés de SiNWs. Esses resultados podem ser devido à difusão lenta de reagentes para a base da nanoestrutura devido ao baixo HF e H 2 O 2 gradientes de concentração ao longo da profundidade da nanoestrutura de Si. Neste caso, o impacto da gravação nas pontas torna-se relativamente significativo e poros profundos não podem ser formados pelas partículas de metal.
Deve-se notar que para valores relativamente baixos de χ (≤0,8), a morfologia em toda a superfície de Si não era uniforme (consulte o arquivo adicional 1:Figura S3). Para [H 2 O] =50 M, corrosão não uniforme também ocorreu para χ =0,85. Em todos os casos, uma superfície uniformemente gravada foi obtida apenas quando SiNWs foram formados. Para superfícies gravadas não uniformemente, seções com morfologias homólogas tendem a ocorrer aproximadamente no mesmo local geral do centro da amostra. A dinâmica de corrosão não uniforme em diferentes áreas da amostra pode ser explicada pelo aumento na concentração de íons catalisadores dissolvidos na solução e sua subsequente difusão e re-nucleação em outras áreas da amostra. Isso foi facilitado até certo ponto pela difusão simultânea de H 2 para fora bolhas como o Si foi gravado.
Muito alto χ valor (0,99), uma matriz muito densa de SiNWs finos foi obtida, levando a uma superfície de amostra preta (consulte o arquivo adicional 1:Figura S3a – c (vii)). No entanto, muitos desses SiNWs tinham paredes laterais inclinadas e alguns poços laterais, os quais ocorrem perto da base (Fig. 3g) e em longos tempos de corrosão (Arquivo adicional 1:Figura S4d). Uma série de saliências onde a formação de nanofios terminou prematuramente também pode ser vista. Esses recursos foram provavelmente causados pelo esgotamento de H 2 O 2 na solução de gravação que levou a diferentes taxas de afundamento de várias partes do filme AgNP. Com a desintegração da rede Ag, algumas seções de AgNP ou pequenas seções de filme de Ag começaram a gravar em direções horizontais <100>.
Cinética de corrosão de nanoestruturas de Si durante MACE
A variação da taxa de corrosão com χ para diferentes [H 2 O] valores são mostrados na Fig. 4. A taxa de corrosão aparente das nanoestruturas geralmente aumenta com χ e picos em χ =0,95, após o qual as taxas de corrosão caem significativamente. Esta tendência é verdadeira independentemente do [H 2 O] e a morfologia da nanoestrutura de Si. No entanto, [H 2 O] pode ter afetado consideravelmente a magnitude das taxas de corrosão, com a magnitude aumentando para diminuir [H 2 O] valores (ou seja, condicionadores mais concentrados). A Figura 4b mostra que a taxa de corrosão na ponta diminuiu muito após χ =0,85 para [H 2 O] =46 e 48 M e após χ =0,9 para [H 2 O] =50 M. Por outro lado, a Fig. 4c mostra que a taxa de corrosão na base aumentou consideravelmente em χ =0,85 e 0,9 para 46 M H 2 O etchant, mas apenas ligeiramente para 48 e 50 M H 2 O etchants. A taxa de corrosão na base permaneceu alta em χ =0,95 mas diminuiu significativamente em χ =0,99.
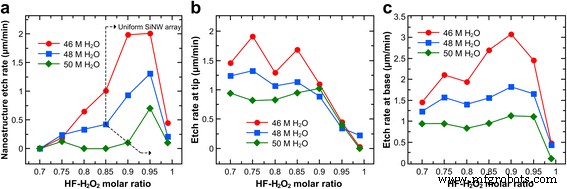
Taxas de corrosão aparentes observadas após 30 min de corrosão em soluções compostas por diferentes HF – H 2 O 2 razões molares e H 2 Concentrações de O. a Taxa de corrosão das nanoestruturas de Si com base no comprimento resultante. b , c Taxa de corrosão da massa de Si em relação à ponta e à base das nanoestruturas de Si, respectivamente
A partir das tendências nas taxas de corrosão na ponta e na base das nanoestruturas de Si, pode ser determinado que o aumento no comprimento de SiNW para [H 2 O] =46 M foi principalmente devido à aceleração da gravação na base, enquanto o alongamento dos SiNWs para [H 2 O] =48 e 50 M foram ditados principalmente pela supressão do ataque nas pontas. Além disso, a tendência da taxa de corrosão geral da nanoestrutura não é exatamente a mesma que a tendência da taxa de corrosão na base. Em particular, o χ valor onde ocorre a taxa de gravação de pico na base e o χ valor onde a maior altura da nanoestrutura é alcançada não são os mesmos (0,9 contra 0,95, respectivamente) devido ao efeito competitivo da taxa de corrosão da ponta.
O χ valor em que ocorreu o pico de comprimento do SiNW (0,95) é próximo ao obtido por Qi et al. [21] ( χ =0,91) para um substrato de Si tipo n altamente dopado. A diminuição inicial na taxa de gravação da ponta ocorrendo perto de χ =0,85 é consistente com a evolução morfológica observada da superfície de Si, em que a difusão de baixo furo e a re-nucleação de Ag permitiram a formação de SiNWs em χ ≥ 0,85. A queda quase simultânea na taxa de gravação da ponta e salto na taxa de gravação base em torno de χ =0,85 significa que buracos e Ag + íons que anteriormente se difundiram para longe da frente de corrosão na parte inferior χ os valores agora estavam sendo restringidos na base devido à inibição da formação de óxido na interface Ag-Si. Ao mesmo tempo, o [HF] aumentou em χ mais alto os valores aceleraram a dissolução do Si, levando a um aumento na taxa de penetração do Ag. Uma vez que [HF] e [H 2 O 2 ] diminuir quando [H 2 O] aumenta para um determinado χ valor (consulte o arquivo adicional 1:Tabela S1), a diminuição na taxa de corrosão nas pontas e na base para [H 2 O] valores são esperados. Os menores aumentos na taxa de gravação de base entre χ =0,85 e 0,95 para [H 2 O] =48 e 50 M são devido à difusão mais lenta de reagentes através do comprimento SiNW para gravações mais diluídas.
Em χ =0,9, a taxa de corrosão na base é máxima devido às taxas ótimas de injeção de orifício por H 2 O 2 e dissolução de Si por HF. Abaixo desse valor, [HF] é o fator determinante da taxa, pois a dissolução do Si oxidado não é rápida o suficiente; acima deste valor, [H 2 O 2 ] determina a taxa de reação porque o número de orifícios injetados é muito baixo. Este esgotamento de H 2 O 2 na solução explica porque a taxa de corrosão na base começa a diminuir em χ =0,95 e cai abruptamente em χ =0,99. Tal dependência da taxa de corrosão em [HF] e [H 2 O 2 ] foi observada anteriormente [21] e implica que ambas as concentrações de reagentes devem ser consideradas em qualquer expressão para a taxa de reação de MACE de Si. Por outro lado, um valor máximo para χ não é aparente a partir da taxa de corrosão da ponta. Em vez disso, a taxa de gravação da ponta é determinada principalmente por [H 2 O 2 ] Uma vez que a corrosão na ponta das nanoestruturas de Si pode ser atribuída principalmente à re-nucleação de íons metálicos e difusão de buraco, esta correlação é razoável quanto maior [H 2 O 2 ] valores em relação a [HF] levam a maiores concentrações de Ag + móvel íons [15, 17] e orifícios injetados [31, 32].
Evolução do comprimento de SiNW com o tempo para diferentes composições de Etchant
O comprimento dos SiNWs é um parâmetro importante em aplicações fotovoltaicas [2], armazenamento de energia [6], sensoriamento [41] e termelétricas [4]. A fim de fabricar SiNWs de um comprimento especificado, a variação temporal do comprimento SiNW foi determinada para condicionadores com χ =0,9, 0,92, 0,95 e 0,98 e [H 2 O] =46, 48 e 50 M. Para esses experimentos, o tempo de deposição de AgNP foi aumentado para 10 min para minimizar a corrosão lateral nos SiNWs fabricados com longos tempos de corrosão (consulte o arquivo adicional 1:Figura S4a-c). Da mesma forma, o maior χ valor utilizado foi de 0,98 porque SiNWs com paredes laterais inclinadas e poços laterais foram obtidos para χ =0,99 mesmo com um tempo de deposição AgNP de 10 min (consulte o arquivo adicional 1:Figura S4d).
A Figura 5a mostra que o comprimento dos SiNWs formados aumenta com o tempo de reação MACE, consistente com observações em estudos anteriores [14, 16,17,18,19, 21, 23]. No entanto, pode ser visto que o aumento no comprimento de SiNW diminui com o tempo, ou seja, a taxa de corrosão está diminuindo (consulte o arquivo adicional 1:Figura S5a), o que pode ser devido ao aumento das taxas de corrosão nas pontas de SiNW ou na diminuição das taxas de corrosão em a base ou ambos. A Figura 5d mostra taxas crescentes de gravação de ponta ao longo do tempo para χ =0,92 e 0,95, com o aumento sendo mais pronunciado no primeiro (ver Arquivo adicional 1:Figura S5b). Isso indica uma quantidade crescente de Ag renucleado nas pontas do SiNW, que se espera que seja mais significativo para χ valores. Por outro lado, a Fig. 5e mostra que em tempos de corrosão maiores que 5 min, a taxa de corrosão na base SiNW foi quase constante para χ =0,9 e 0,92, mas diminuindo para χ =0,95 e 0,98 (consulte o arquivo adicional 1:Figura S5c). The latter was probably due to impeded diffusion of reactants to the SiNW base caused by the longer diffusion lengths (SiNW lengths were longer for χ = 0.95 and 0.98) and depletion of H2 O 2 in the etching solution.
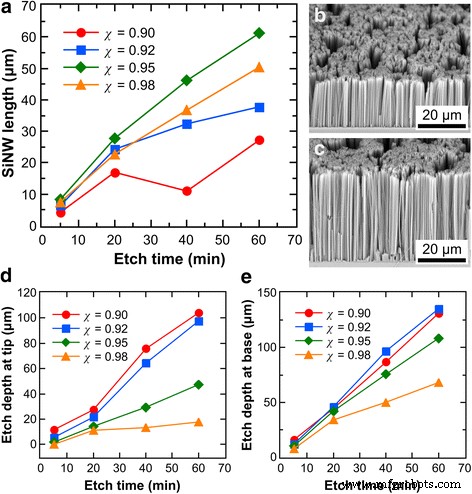
Evolution of SiNW length with time for different HF–H2 O 2 molar ratios at 48 M H2 O. a Effect of etch time on SiNW length. b , c SEM images of SiNWs after etching for 1 h in a solution composed of 48 M H2 O and HF–H2 O 2 molar ratios of 0.9 and 0.98, respectively. d , e Etched bulk Si thickness with respect to the tip and base of the SiNWs over time
It should be noted from Fig. 5 that at χ = 0.9, the evolution of length with time is erratic because of the non-monotonic trend of the etch rate at the tip (see Additional file 1:Figure S5b). This may be due to differing amounts of re-nucleated Ag as more mobile Ag + ions were generated. Nevertheless, lower χ values have the advantage of forming defect-free SiNWs (Fig. 5b) as higher χ may result in some lateral pits, as shown in Fig. 5c for χ = 0.98. The trend of the overall etch rates and etch rates at the tip and base of the SiNWs with respect to χ mirrors those observed in Fig. 4. However, it can be seen in Fig. 5e that χ = 0.92, which is not included in Fig. 4, actually results in a higher base etch rate than χ = 0.9.
The SiNW length also increases with etch duration for more concentrated (46 M H2 O) and dilute (50 M H2 O) etchants, as shown in Fig. 6a. Likewise, the etch rate decreases with etch time for all H2 O concentrations used (see Additional file 1:Figure S6a). Figure 5d, e show that, while the etch depth at the tip and base of the SiNWs both increase with time, the amount of increase at the tip is almost constant but that at the base is decreasing (see Additional file 1:Figure S6b, c). These trends are consistent with those observed for χ = 0.95 in Fig. 5 and Additional file 1:Figure S5. Hence, for χ = 0.95, the increase in the amount of re-nucleated Ag at the SiNW tips with time is negligible, while the increasing SiNW lengths progressively hampers reactant diffusion to the SiNW base. Figure 6 also shows that regardless of the etching time point, lower [H2 O] generally results in more etched Si, similar to what was observed in Fig. 4. However, Fig. 6b, c show that low [H2 O] solutions may result in some lateral pitting in the SiNWs whereas high [H2 O] solutions do not. This could be due to fast etching at sites with re-nucleated Ag particles for low [H2 O] etchants.
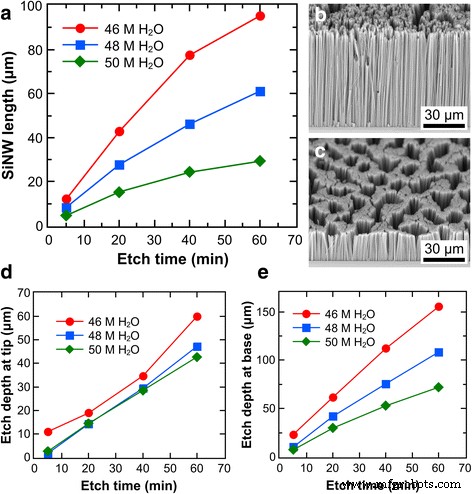
Evolution of SiNW length with time for different H2 O concentrations at a fixed HF–H2 O 2 molar ratio of 0.95. a Effect of etch time on SiNW length. b , c SEM images of SiNWs after etching for 1 h in a solution composed of HF–H2 O 2 molar ratios of 0.95 and H2 O concentrations of 46 and 50 M, respectively. d , e Etched bulk Si thickness with respect to the tip and base of the SiNWs over time
Fabrication of Highly Doped SiNWs with Controlled Porosity
SiNW porosity is another key parameter in SiNW-based devices [5, 16, 27, 29], making its controlled formation during SiNW fabrication highly important. The degree of porosity of SiNWs fabricated using two-step MACE is directly related to the H2 O 2 concentration [14,15,16,17, 20], etching time [14, 16, 17, 20], and temperature [20] and inversely related to the HF–H2 O 2 volume ratio [19] and wafer resistivity [17]. In our Ag deposition experiment, SiNW porosity was also found to be directly related to the amount of deposited Ag. However, the extent of SiNW porosification cannot be easily tuned without affecting other parameters. For example, length and porosity are expected to vary together if one of them is adjusted using either [H2 O 2 ], etch time, or temperature. If a SiNW of a specific length needs to have higher porosity, the [H2 O 2 ] can be increased, but the etch duration needs to be decreased as higher [H2 O 2 ] may have a higher etch rate. This raises the question of whether the desired porosity can still be achieved given the shorter etch time.
Here, the extent of SiNW porosification caused independently by χ and [H2 O] was compared for χ = 0.92, 0.95, and 0.98 ([H2 O] fixed at 48 M) and [H2 O] = 46, 48, and 50 M (χ fixed at 0.95). The SiNW length was fixed at 20 μm by using different etch durations based on the etch rate of the respective etchant composition (see Additional file 1:Table S2). The porosity, in general, was found to be inversely related to χ and directly related to [H2 O], as shown in Fig. 7a–c and Fig. 7d, b, e, respectively. (The trends are more apparent in Additional file 1:Figure S7 where more samples are shown.) Comparing the SiNWs for χ = 0.95 and χ = 0.98 (Fig. 7b, c), the samples for χ = 0.95 appear to have a higher pore density and most are surrounded by a thin porous shell [14, 17]. Meanwhile, for χ = 0.98, some SiNWs appear to be rough and solid rather than porous, which indicates a much lesser degree of porosification. On the other hand, the overall porosity obtained for χ = 0.92 (Fig. 7a and Additional file 1:Figure S7a) appears to depart from the expected trend. While some SiNWs have a porous shell, others seem to be only roughened although to a higher extent compared with those for χ = 0.98. In contrast, the increase of porosity with [H2 O] is more consistent. Although no rough solid SiNWs were obtained for [H2 O] = 46 M, highly porous SiNWs were formed for [H2 O] = 50 M unlike in the case of χ = 0.92.

TEM images of fabricated SiNWs with a length of ≈20 μm showing the variation of porosity at the middle section with a –c HF–H2 O 2 molar ratio and d , b , c H 2 O concentration. a –c HF–H2 O 2 molar ratio of the etchant was 0.92, 0.95, and 0.98, respectively, with [H2 O] = 48 M. d , b , c H 2 O concentration of the etchant was 46, 48, and 50 M, respectively, with HF–H2 O 2 molar ratio = 0.95. TEM images of SiNWs with f –h low and i –k high porosity corresponding to those shown in c e e , respectively, but including the f , i top and h , k bottom sections. The scale bar in e and k also applies to the images in a –d e f –j , respectivamente
The higher SiNW porosity obtained for χ = 0.95 than χ = 0.98 is consistent with the fact that metal re-nucleation, metal ion-induced etching, and hole diffusion are higher for lower χ valores. It also shows that the longer etch time utilized for χ = 0.98 to obtain 20-μm long SiNWs did not overcome the porosification caused by the etchant χ value. The seemingly lesser degree of porosification for χ = 0.92 could not have been due to the difference in etch time as a longer etching period was utilized for it than for χ = 0.95. It is possible that more porous SiNWs were actually obtained for χ = 0.92; however, due to the very high porosity, HF–H2 O 2 etching of porous Si both at the surface and inside the pore walls resulted, leading to the rapid collapse of the porous shells [42] and subsequent exposure of the less porous Si surface underneath. That more porous SiNWs were obtained for higher [H2 O] values confirms that etch duration has a significant effect on porosity [14, 16, 17, 20]. (Note the large differences in etch times in Additional file 1:Table S2 for different [H2 O] values.) The high degree of porosity obtained for 50 M H2 O without the collapse of the porous shell could be due to minimized HF–H2 O 2 etching inside the pore walls because of the lower diffusion rate of reactants in dilute etchants.
Examination of the surface roughness along the length of the SiNWs reveals the characteristic increase in porosity from the base to the tip of highly doped SiNWs fabricated with MACE [16, 19], as shown in Fig. 7f–k (also in Additional file 1:Figure S8). The increase in porosity towards the tip of the SiNWs is due to the longer exposure time of these portions in the etchant solution [19]. Figure 6f–k and Additional file 1:Figure S8 also show that the SiNWs are tapered, with the tapering being more severe in SiNWs which are more porous (Fig. 7i–k and Additional file 1:Figure S8a–c). This is expected considering that porosification is directly related to the amount of dissolution of the metal catalyst at the SiNW base [15, 17]. However, a closer look at the SiNWs reveals that some nanowires exhibit a slightly biconic or hourglass longitudinal profile, which seems to occur more often among those with higher porosity. Likewise, more porous SiNWs generally have larger diameters than the less porous ones (see Additional file 1:Figure S7). In order to achieve highly porous SiNWs with smaller diameters, it might be necessary to use a more inert catalyst like Au [32].
Based on the results obtained here, porosity control in highly doped SiNWs of a given length is possible through the use of the appropriate etchant composition. To achieve low porosity, it is best to use high χ values as rough solid nanowires could be obtained. To achieve highly porous SiNWs, on the other hand, the use of dilute etchants with moderate χ values (≈0.95) is advisable as this avoids the disintegration of the porous shell which occurs in etchants with low χ valores. It is conceivable that lower porosities could be achieved using an etchant of both high χ and low [H2 O] values and higher porosities using an etchant of both (slightly) lower χ and high [H2 O] values. In the case of low-porosity SiNWs, the maximum χ and minimum [H2 O] values would probably be dictated by the values where considerable lateral pitting occurs. On the other hand, for high-porosity SiNWs, the minimum χ and maximum [H2 O] values would be determined by the values where the porous shell dissolves and the SiNW structures are lost, respectively. These methods can be combined with our earlier finding of porosity control via the amount deposited Ag in order to obtain a wide range of SiNW porosities.
Conclusions
Porous SiNWs were fabricated from degenerately doped p-type Si substrates using metal-assisted chemical etching in HF–H2 O 2 with electrolessly deposited Ag catalyst. The effect of Ag deposition time, etchant HF–H2 O 2 molar ratio, and etchant H2 O concentration on the morphology and etch rate of the Si nanostructures was systematically studied. It was shown that there is an optimal amount of deposited Ag particles necessary to form damage-free SiNWs. Furthermore, the amount of deposited Ag particles affects the SiNW etch rate in a non-monotonic manner and provides an additional mechanism to control the porosity of the resulting nanowires. Likewise, the etchant composition has a significant effect on the resulting nanostructures. There is an appropriate χ window within which uniform SiNW arrays can be formed. For H2 O concentrations between 46 and 48 M, this χ range is 0.85–0.98; more dilute etchants increase the minimum χ due to sluggish etching at the SiNW base. The formation of Si nanostructures during Ag-catalyzed chemical etching is a result of the competing effects of different factors, namely, deposited Ag-catalyzed Si dissolution, re-nucleated Ag-catalyzed Si dissolution, hole diffusion, and reactant diffusion through etched pores, as reflected by the etching kinetics at the tip and base of the Si nanostructures. These factors result in a gradually decreasing etch rate over time, with re-nucleated Ag-catalyzed etching being dominant for low χ values and impeded diffusion being more pronounced for high χ valores. These mechanisms can be exploited to control the porosity of SiNWs of the same length fabricated with different etch times. In particular, suppressing Ag re-nucleation and hole diffusion using higher χ values can effectively decrease pore density, while more controlled porosification can be achieved using dilute etchants owing to slower reactant diffusion and longer etch times. Since the general mechanism of Ag- and Au-catalyzed MACE of Si is similar [11, 33, 35], the findings of this study may also apply to porous SiNWs fabricated with Au metal catalyst, except that metal ion-induced etching is expected to be greatly suppressed and hole diffusion acts as the main mechanism of porosification and tip etching.
Abreviações
- AgNP:
-
Ag nanoparticle
- DI:
-
Deionized
- MACE:
-
Metal-assisted chemical etching
- SEM:
-
Microscopia eletrônica de varredura
- SiNW:
-
Silicon nanowire
- TEM:
-
Microscopia eletrônica de transmissão
- χ :
-
HF–oxidant molar ratio
Nanomateriais
- Heróis no Vale do Silício (e na Reunião do Grupo de Usuários RTI)
- A evolução do mercado de materiais de impressão 3D:tendências e oportunidades em 2019
- A evolução do SLS:novas tecnologias, materiais e aplicações
- Instrumentação de monitoramento de benzeno para as indústrias química, farmacêutica e petroquímica
- Matrizes nanopilar de GaAs com cobertura au fabricada por corrosão química assistida por metal
- Desvendando as Complexidades das Leis Antissuborno e Corrupção
- A evolução e o futuro da entrega no meio-fio para o varejo
- A incrível evolução da impressão 3D no setor aeroespacial e de defesa
- Sistemas de manutenção preventiva e software CMMS :a evolução
- Aço inoxidável e a evolução da montanha russa