Novo pré-impregnado para moldagem por compressão em RAPM
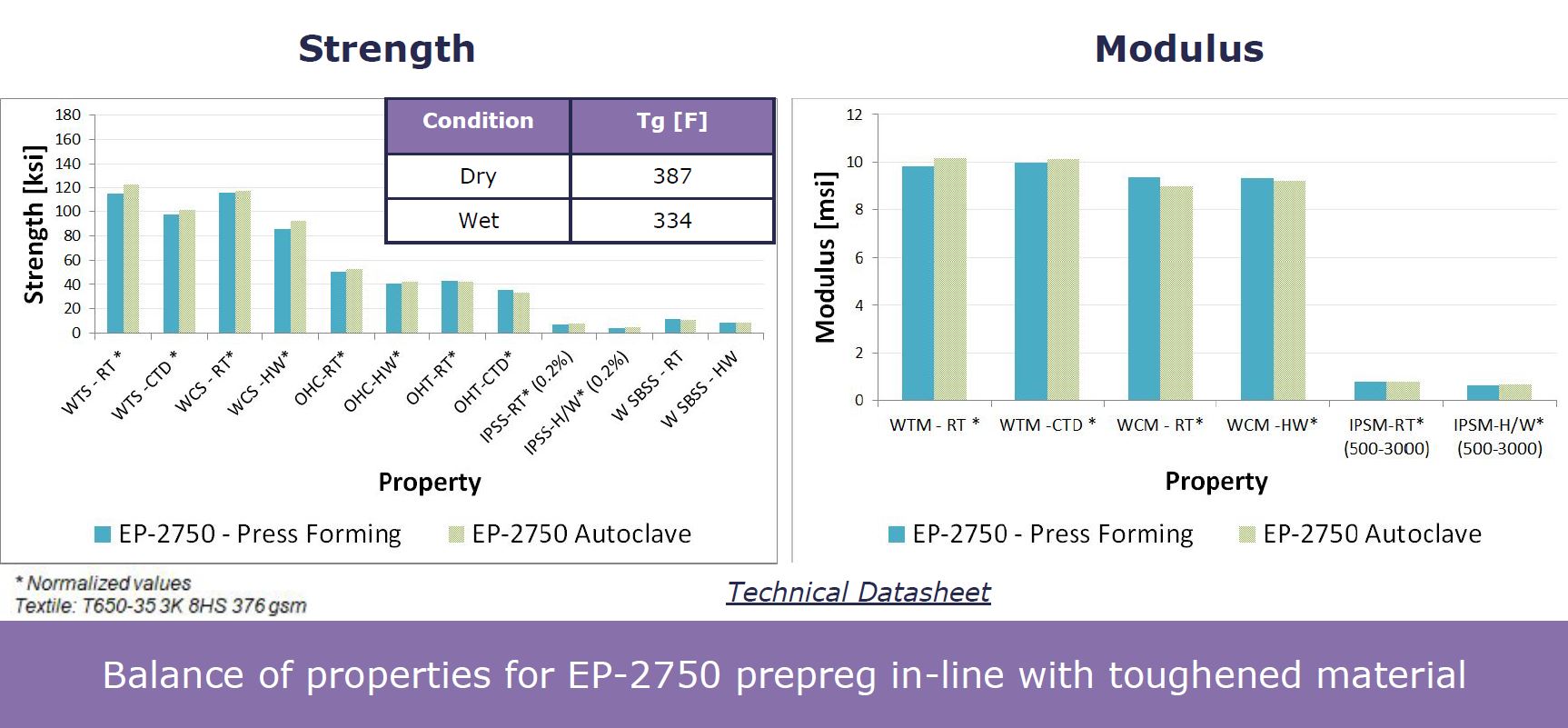
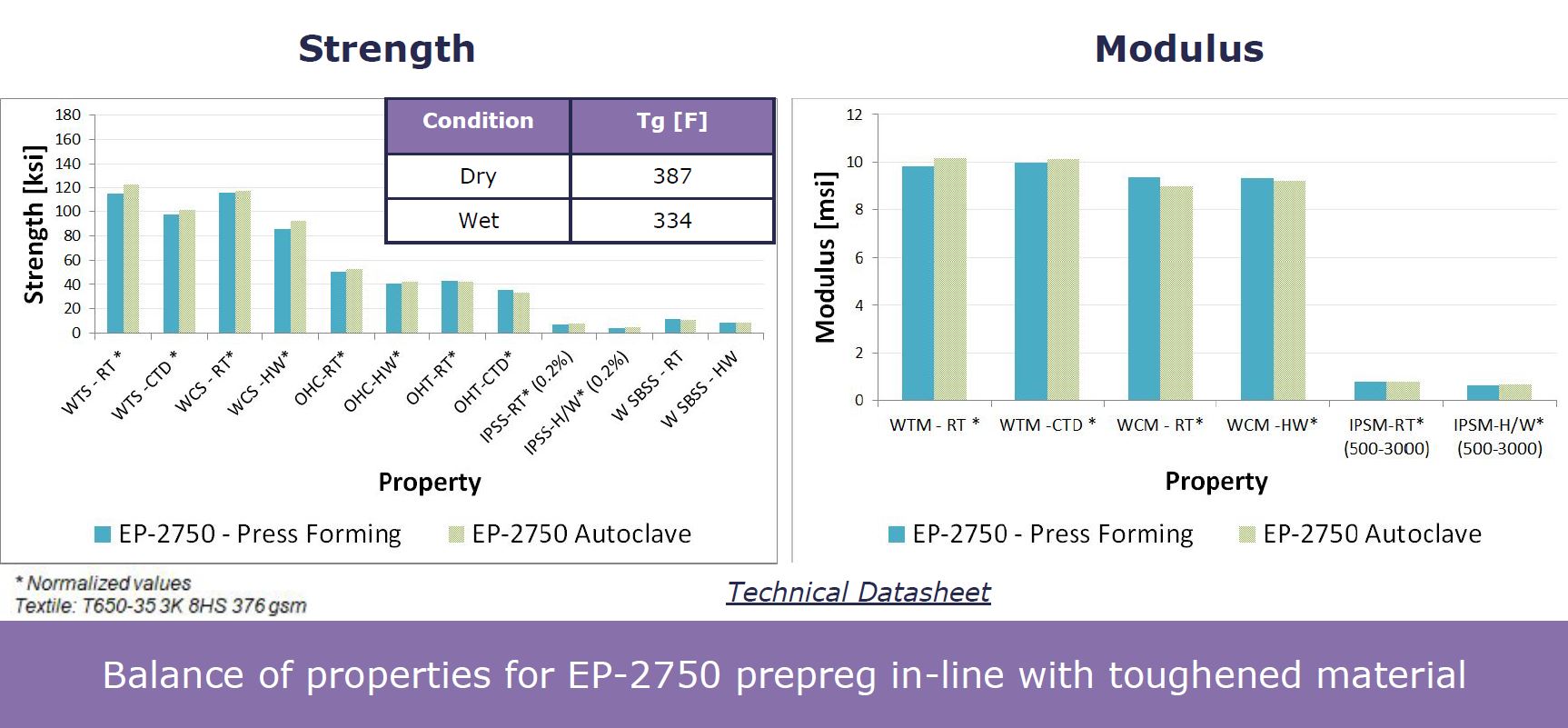
Fibra de carbono / epóxi prepreg tem sido o material de base para compostos aeroespaciais por décadas porque fornece altas propriedades mecânicas e conteúdo preciso de resina / fibra, bem como facilidade de manuseio para cura em layup e autoclave. No entanto, como os fabricantes de aeronaves e de mobilidade aérea urbana (UAM) exploram taxas de produção mais altas e custos mais baixos, a moldagem por compressão é atraente, reduzindo os tempos de ciclo e aumentando a eficiência em relação à autoclave. Na sua forma mais simples, a moldagem por compressão compreende o pré-aquecimento do material de moldagem, colocando-o em uma cavidade de ferramenta aberta e consolidando com pressão hidráulica na temperatura, durante a qual o material termofixo líquido é convertido em um sólido. A peça curada é então ejetada para todas as etapas de corte e acabamento necessárias.

A combinação de moldagem por prensagem e prepreg não só oferece um processo eficiente e de alta taxa com o desempenho e fácil manuseio de prepreg, como também evita algumas das complexas dinâmicas do processo de enchimento de reforços secos com resina líquida durante processos como infusão de resina e moldagem por transferência de resina (RTM). Especialmente para aeroestruturas menores, a moldagem por prensagem pré-impregnada oferece o potencial para tempos takt de <30 minutos, ao mesmo tempo que atinge peças de geometria complexa de alta qualidade.
Solvay Composite Materials (Alpharetta, Ga., U.S.) foi um parceiro-chave no programa RApid High-Performance Manufacturing (RAPM) liderado por The Boeing Co. (Chicago, Illinois, U.S.). O RAPM é a parte “integrante” do programa Tailorable Feedstock and Forming (TFF) lançado pela Defense Advanced Research Projects Agency (DARPA, Arlington, Va., EUA) em 2015. Seu objetivo é permitir rapidez, baixo custo e agilidade fabricação de peças compostas pequenas e de formato complexo e aumenta a capacidade dos compostos para competir com o alumínio usinado em aplicações de defesa.
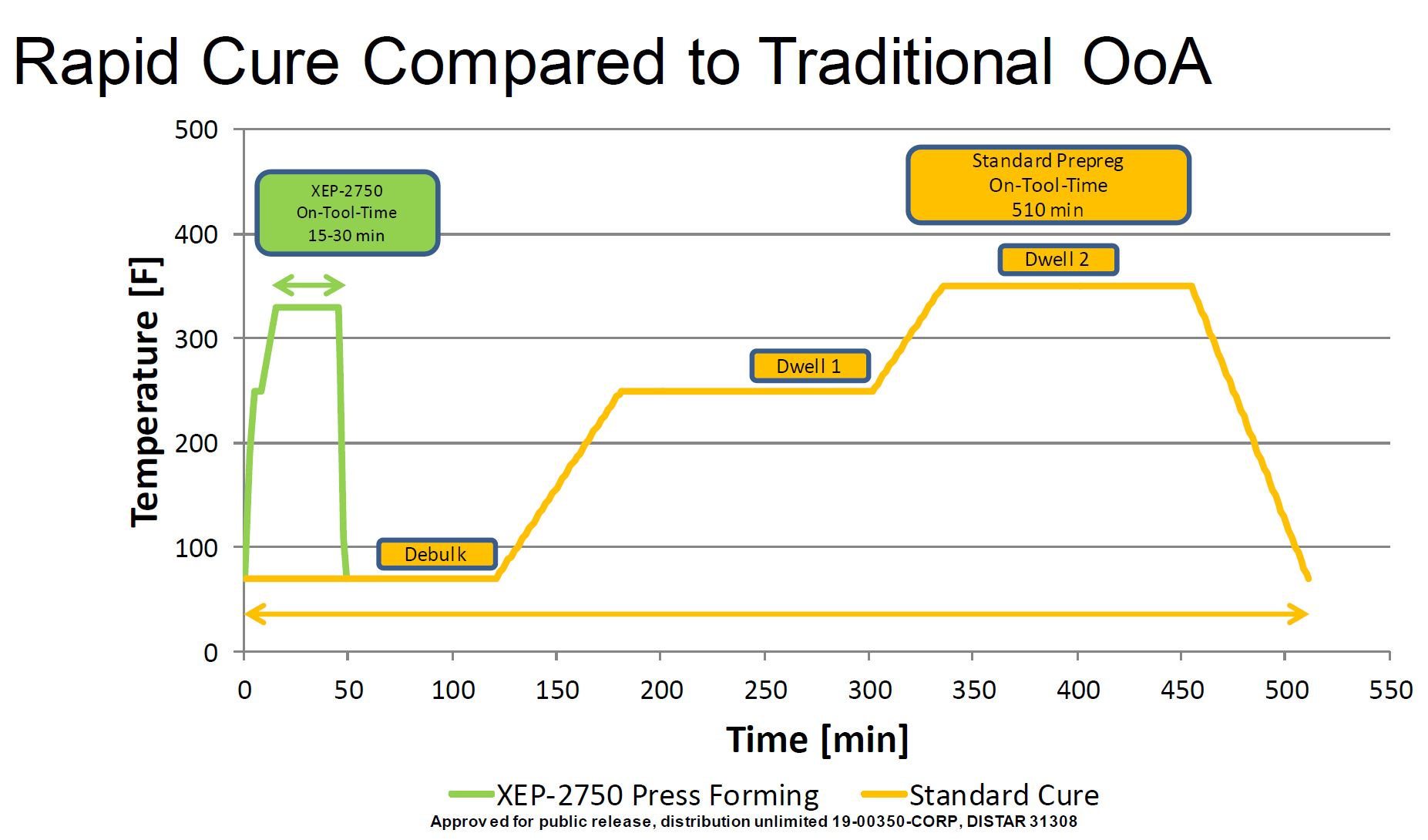
Fornecedora de longa data da Boeing para aplicações de defesa, a Solvay também é líder em novas soluções para aeroespacial comercial, como o epóxi prepreg CYCOM 5320-1 out-of-autoclave (OOA) e também para o setor automotivo, como o tempo takt de 1 minuto, híbrido de vinil SolvaLite 730 prepreg.
O RAPM foi uma oportunidade perfeita para a Solvay testar e refinar seu sistema experimental XEP-2750, agora comercializado como CYCOM EP2750, que foi desenvolvido para unir a produção de compósitos aeroespacial e automotivo. Este blog - uma barra lateral online para o artigo de maio de 2020 “Revolucionando o paradigma de custos de compósitos, Parte 2:Formação” - analisa esse desenvolvimento, bem como os processos de moldagem por compressão usados e o que o CYCOM EP2750 oferece aos fabricantes de compósitos aeroespaciais e automotivos.
As referências para este blog incluem:
- “Spring Frame Press Fabricação de componentes de produção aeroespacial” por Timothy J. Luchini
1
, Alejandro J. Rodriguez
2
, Scott A. Rogers
2
, Aurele Bras
3
, Adam Whysall
3
, Richard Russell
3
, Scott Lucas
2
, Gail L. Hahn
1
. Procedimentos da Conferência SAMPE. Charlotte, NC, 20 a 23 de maio de 2019.
- “Challenges of Aerospace Structural Part Geometries for High-Rate Compression Molding” por Aurele Bras
1
, Alejandro J. Rodriguez
2
, Richard Russell
1
, Timothy J. Luchini
3
, Travis Adams
3
, Adam Whysall
1
, Scott A. Rogers
2
, Scott Lucas
2
, Gail L. Hahn
3
. Society for the Advancement of Material and Process Engineering - North America.SAMPE Conference Proceedings. Seattle, WA, 4 a 7 de maio de 2020. Society for the Advancement of Material and Process Engineering - North America.
- “Moldagem rápida de alto desempenho de xEP-2750 Prepreg estrutural para moldagem por compressão” por Timothy J. Luchini 1 , Alejandro J. Rodriguez 2 , Scott A. Rogers 2 , Aurele Bras 2 , Adam Whysall 2 , Richard Russell 2 , Scott Lucas 2 , Gail L. Hahn 1 . SAMPE 2019.
1 The Boeing Company, Saint Louis, MO 63134, 2 Solvay Composite Materials, Anaheim, Califórnia, EUA e 3 Solvay Composite Materials, Heanor, Reino Unido
- webinar CompositesWorld:“Automotive Processes for High-rate Aerospace Composites Manufacturing” por Alejandro Rodriguez, Solvay Composite Materials, Anaheim, Califórnia, EUA.
Metas de material e processo
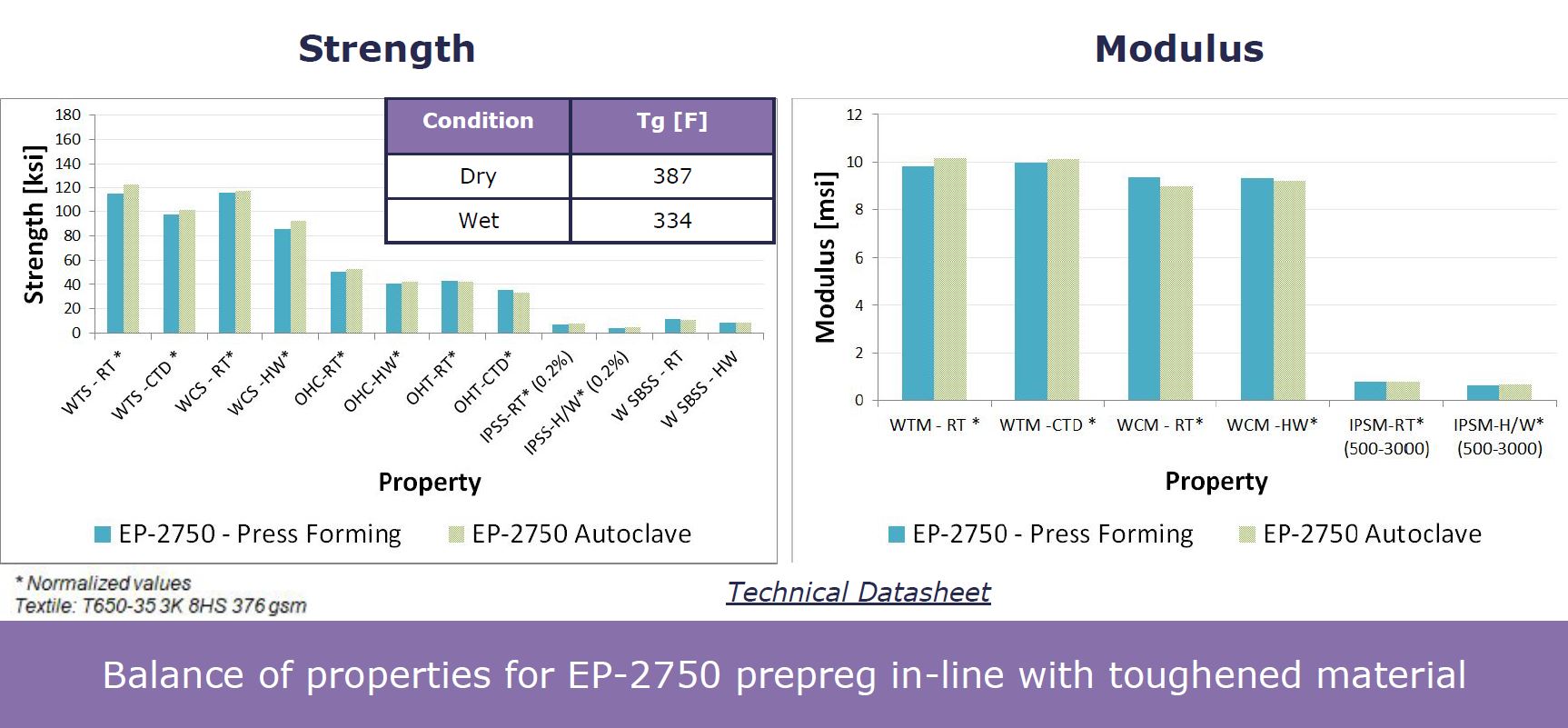
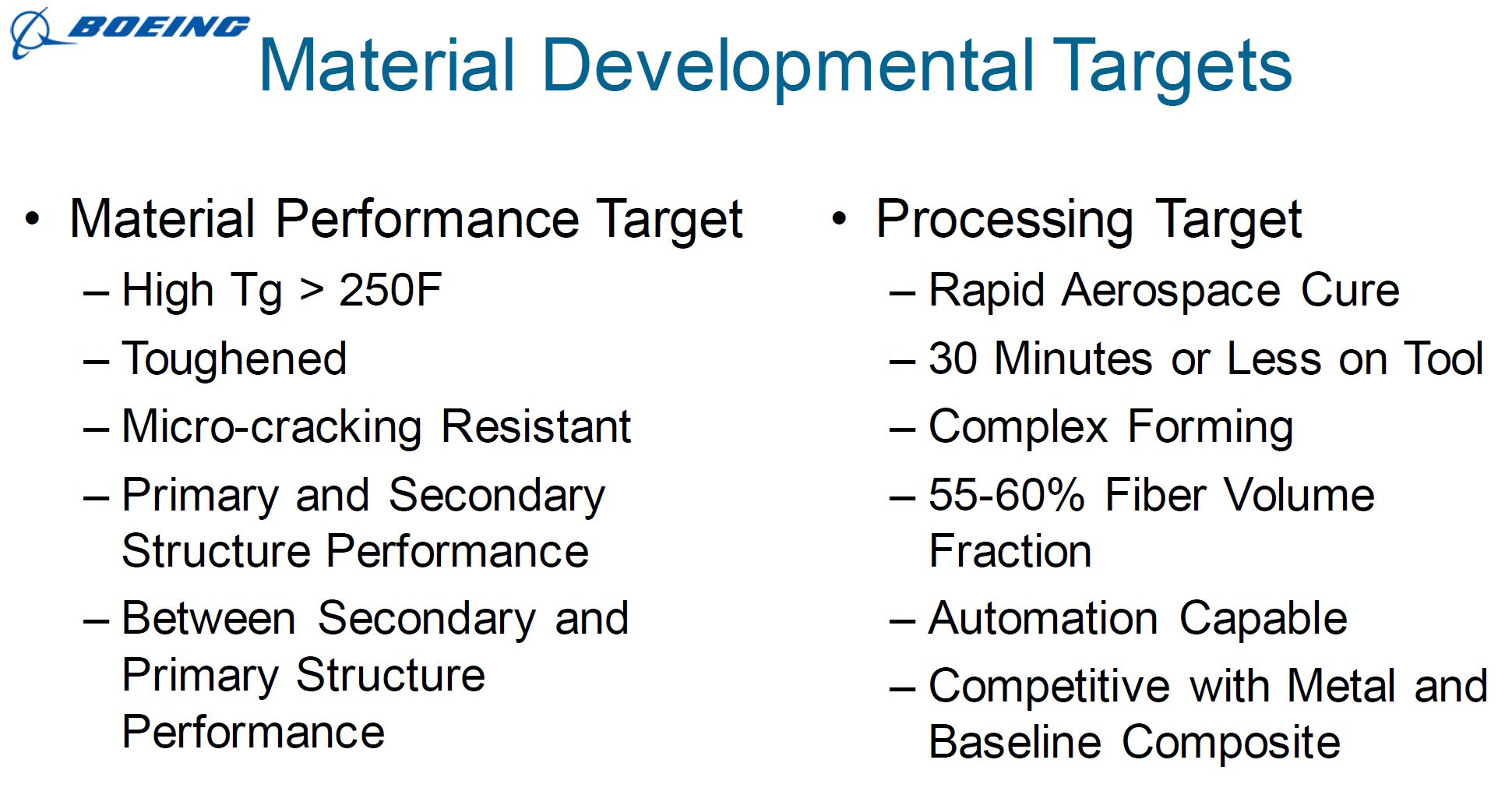
CYCOM EP2750 foi desenvolvido para atender às metas de desempenho estabelecidas pela Boeing para um epóxi endurecido aeroespacial, exibindo um equilíbrio de temperatura de transição vítrea (Tg) de até 350 ° F, boas propriedades entalhadas - por exemplo, compressão de orifício aberto (OHC) e tensão de orifício aberto (OHT) - e resistência a solventes. Esta nova classe de pré-impregnado é aplicável às aeroestruturas primárias e secundárias e é compatível com vários reforços (por exemplo, carbono e fibra de vidro).
O CYCOM EP2750 também foi desenvolvido com a capacidade de aumentar a produção usando manuseio automatizado e moldagem por compressão. Isso inclui um tempo de cura na ferramenta de 15-30 minutos a 330-370 ° F, com uma pós-cura de 1 hora a 350 ° F. Esse tempo takt de 30 minutos ou menos permite um volume de produção anual de 10.000 peças por ferramenta.
A Solvay usou duas variações de moldagem por compressão durante o programa RAPM:moldagem com estrutura de mola e formação de diafragma duplo (DDF). Ambos usam o princípio de segurar um bloco plano e carregá-lo através de um estágio de pré-aquecimento infravermelho (IV) antes de colocá-lo em uma cavidade de ferramenta de metal correspondente. A prensa então fecha o molde de aço seguindo um programa automatizado e aplica pressão total ao pré-impregnado pelo tempo restante na ferramenta.
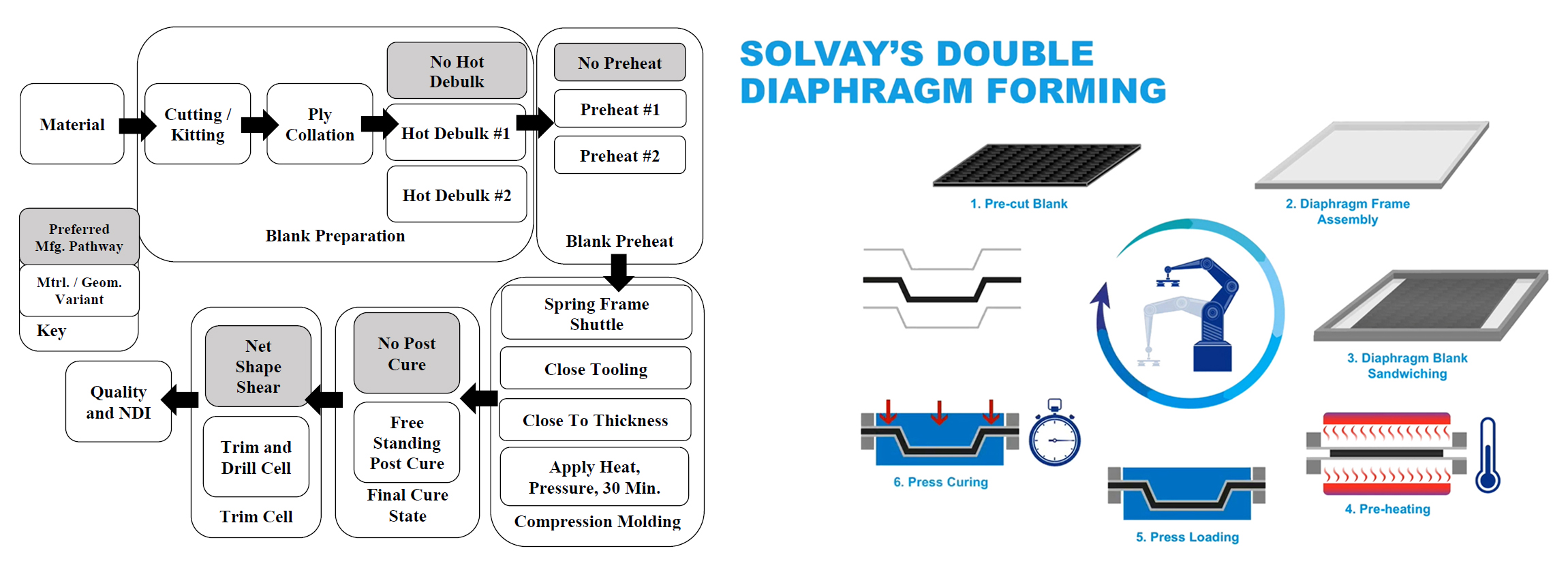
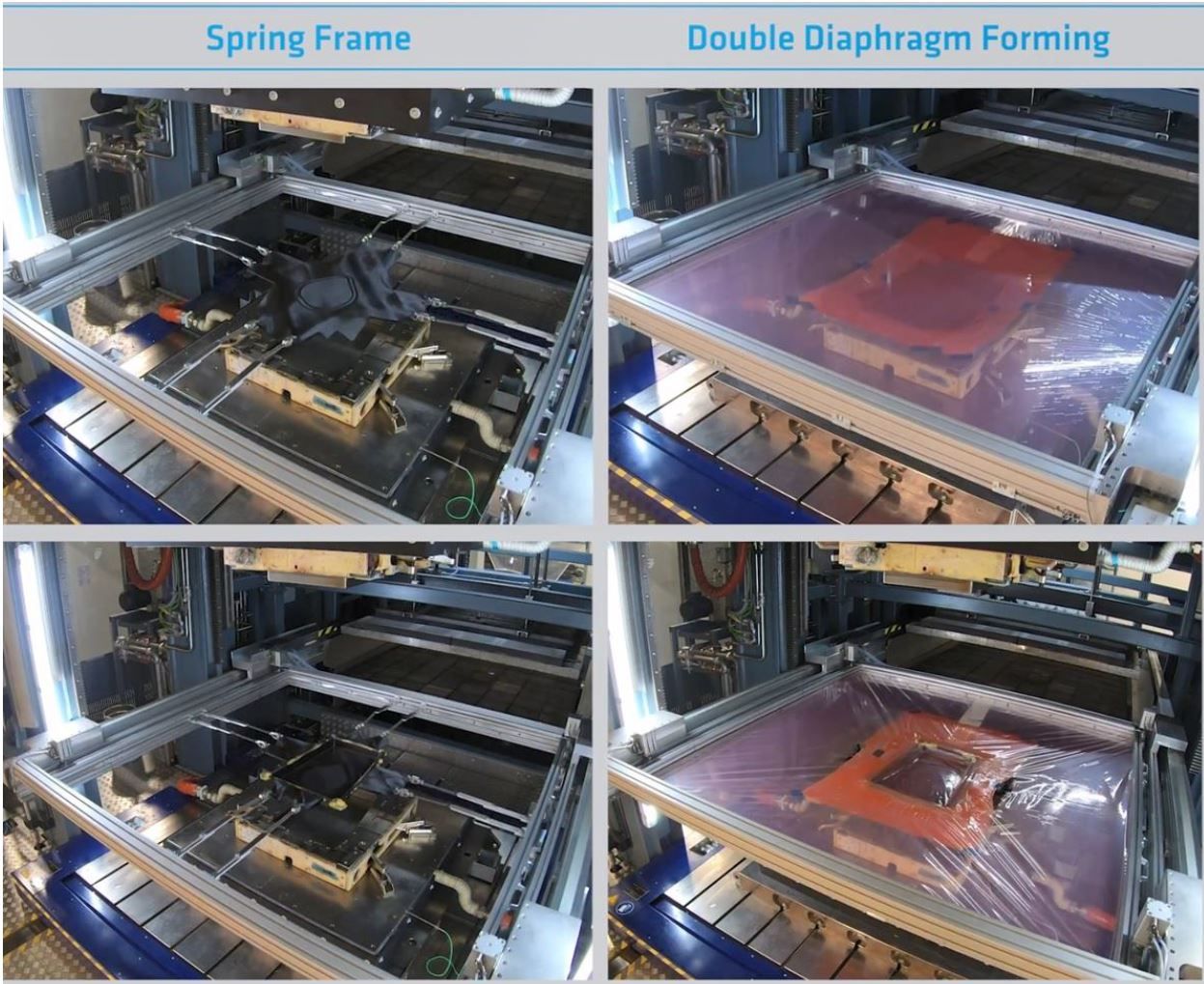
A moldagem com estrutura de mola e DDF usam ferramentas de metal combinadas e oferecem uma abordagem hot-in, hot-out, eliminando o aquecimento e resfriamento da ferramenta, para produção de alta taxa. Ambos foram usados para moldar com sucesso vários tipos de peças de geometria complexa com almofadas, flanges verticais e variações de espessura de 3,8 a 8,9 milímetros. Essas peças foram feitas no Centro de Aplicação da Solvay em Heanor, Reino Unido. Embora não disponível durante o RAPM, Heanor agora apresenta uma linha de moldagem por compressão totalmente automatizada de rolo pré-impregnado a peça moldada, atingindo tempos takt de 15 a 60 minutos para peças aeroespaciais feitas com EP2750 e takt tempos de 3 minutos ou menos para peças pequenas a médias usando pré-impregnados automotivos. A Solvay vê vários benefícios no processo de DDF, incluindo:
- Eliminação da etapa de pré-formação - peça bruta 2D para peça 3D
- Sem desmoldagem ou limpeza necessária
- Redução de materiais auxiliares (por exemplo, respirador, sangrador, ensacamento, fita) vs. autoclave
- Melhor compra para voar vs. moldagem de moldura de mola porque menos material em excesso é necessário para prender as pinças de mola.
A impregnação total vs. parcial mantém a pressão
As características do EP2750 que facilitam a moldagem por compressão incluem seu baixo tack para manuseio automatizado de pick and place e sua natureza totalmente impregnada versus CYCOM 5320-1, que é parcialmente impregnado para facilitar a respiração das bordas, necessária para laminados livres de vazios usando processamento OOA. A moldagem por compressão, no entanto, explora o fluxo de resina forçado muito rápido devido às pressões mais altas aplicadas - por exemplo, até 350 psi (máximo típico para EP2750) em comparação com 35 psi comum no processamento de autoclave e 14,7 psi no processamento OOA apenas a vácuo.
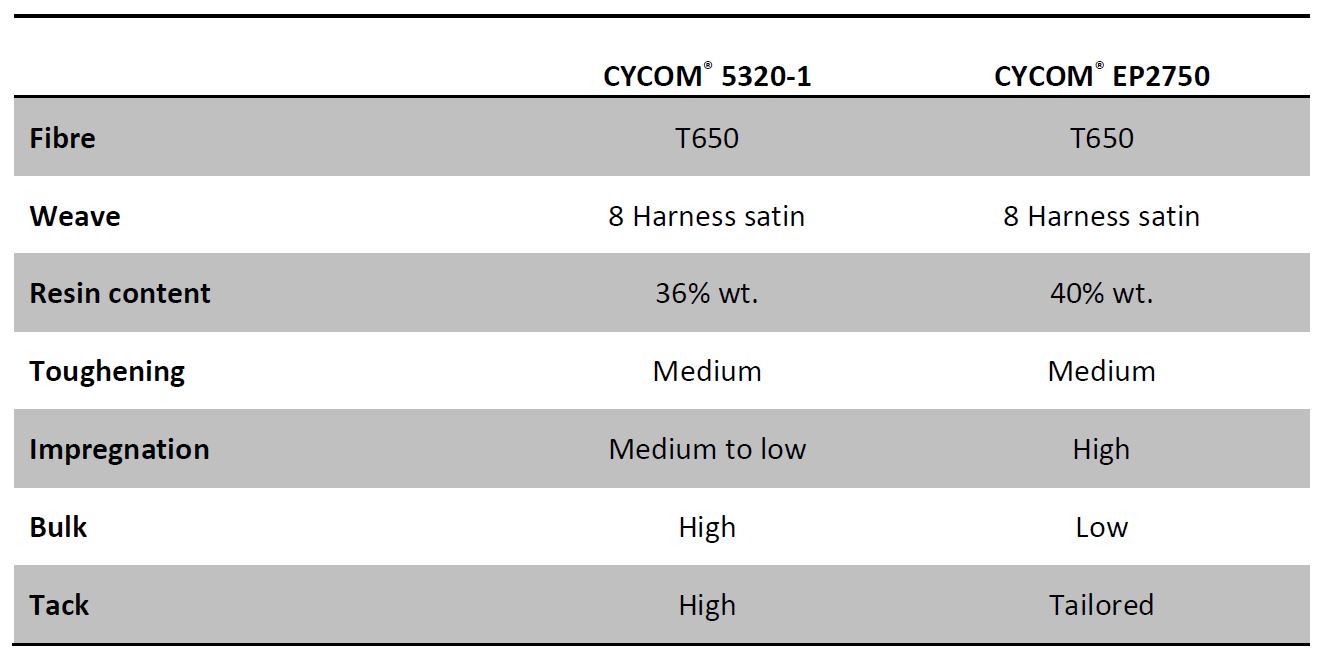
Ter um pré-impregnado mais totalmente impregnado, embora o conteúdo de resina seja apenas ligeiramente superior - 40% no CYCOM EP2750 em comparação com 36% no CYCOM 5320-1 - mantém a pressão hidrostática durante a compactação e cura na cavidade da ferramenta de metal correspondente, resultando em menos risco para áreas secas, espessura de peça curada inconsistente (CPT), enrugamento e outros defeitos, garantindo uma boa qualidade de superfície.
Notavelmente, a Solvay desenvolveu um Transformer Film patenteado para aumentar a pressão hidrostática ao usar o pré-impregnado CYCOM 5320-1 com menor teor de resina. Aplicado ao layup da peça antes da moldagem por compressão, o Transformer Film aumenta o conteúdo de resina e ajudou a adequar o CPT aos requisitos dos ensaios de moldagem de peças RAPM.
Ensaios de moldagem de peças RAPM
Conforme explicado no artigo de fundo de maio de 2020 da CW, CYCOM EP2750 foi um dos principais materiais testados na faixa prepreg termofixo do RAPM. Peças do Pathfinder testadas na fase inicial de Fabricação e Desenvolvimento incluídas
TS-RAPM-001 e -009 painéis de acesso frisados, nervura TS-RAPM-002 e canal C curvo TS-RAPM-003. As peças foram projetadas na Boeing (vários locais globalmente), as ferramentas foram feitas na C-Con GmbH (Munique, Alemanha), as peças foram fabricadas no Centro de Aplicações da Solvay em Heanor, Reino Unido e depois testadas na Solvay Anaheim, Califórnia, EUA e Boeing St. Louis, Missouri, EUA
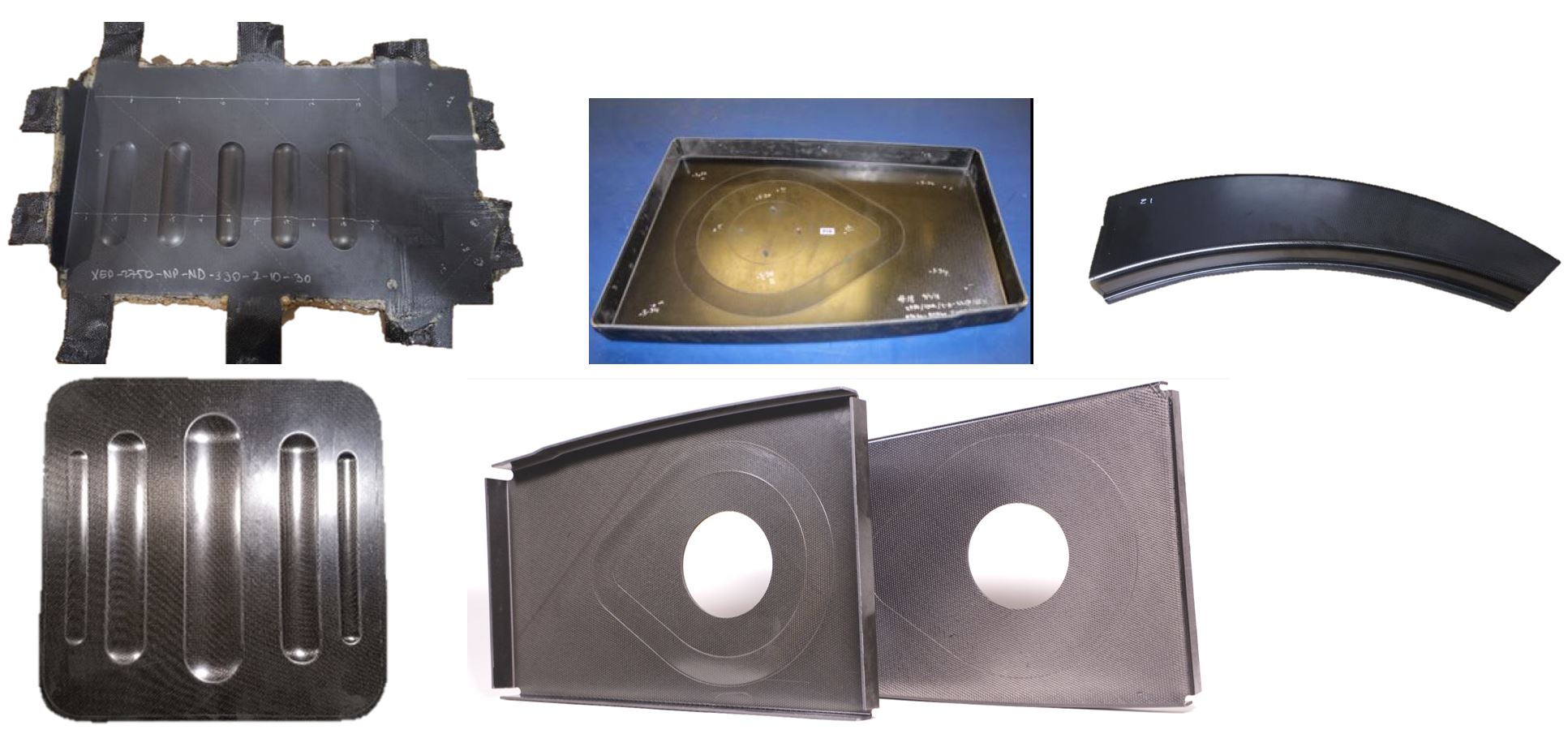
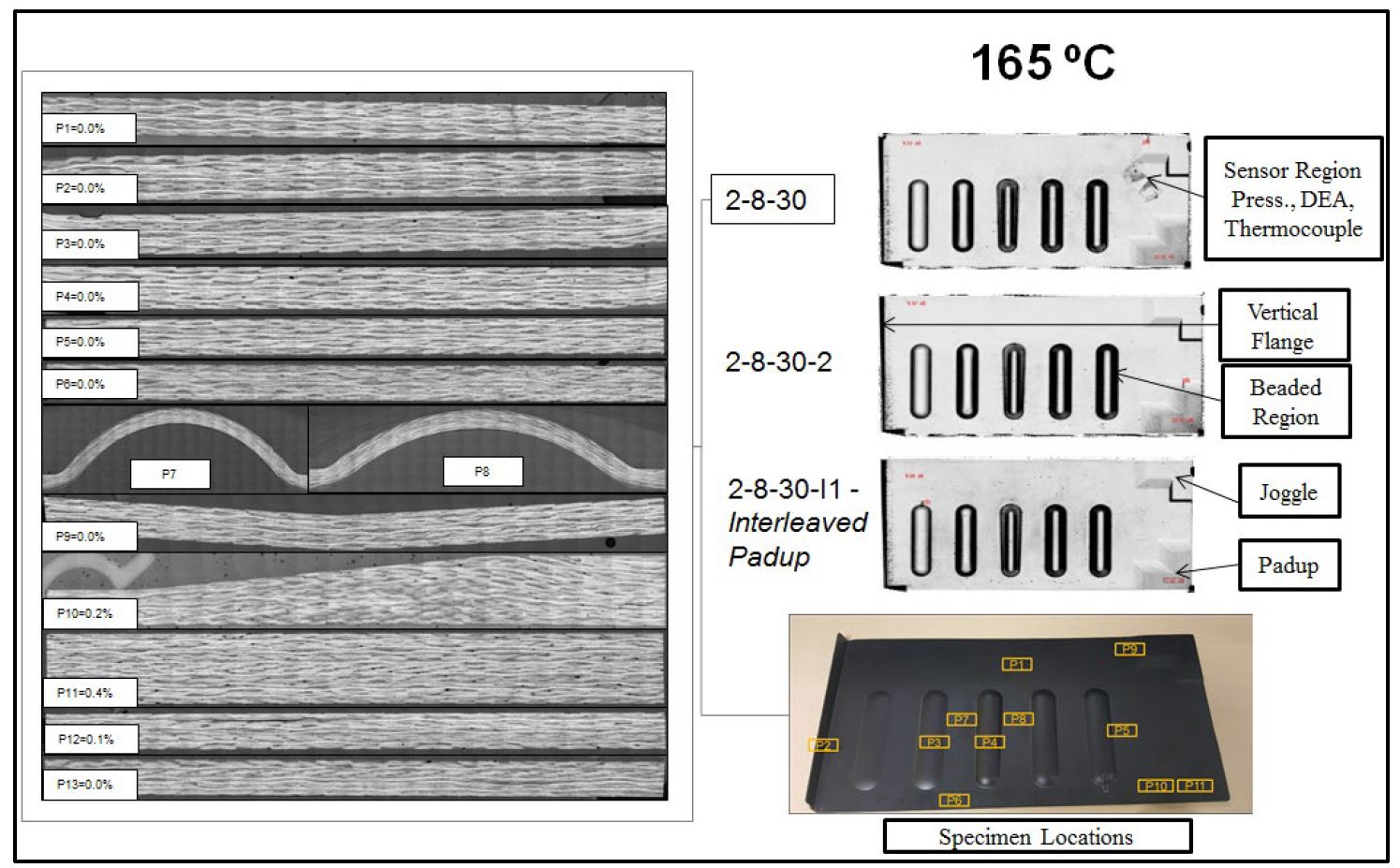

A qualidade da superfície foi avaliada por meio de inspeção não destrutiva (NDI) e os painéis selecionados foram seccionados quanto à porosidade, cisalhamento de feixe curto, fração de volume de fibra, teor de resina, grau de cura e temperatura de transição vítrea.
Níveis de porosidade abaixo de 0,5% foram prontamente alcançados, atribuídos às altas pressões de consolidação da moldagem por compressão. Embora os parâmetros do processo tivessem que ser otimizados para cada parte diferente, uma vez bloqueado, o processo se mostrou repetível.
TS-RAPM-009 painel frisado
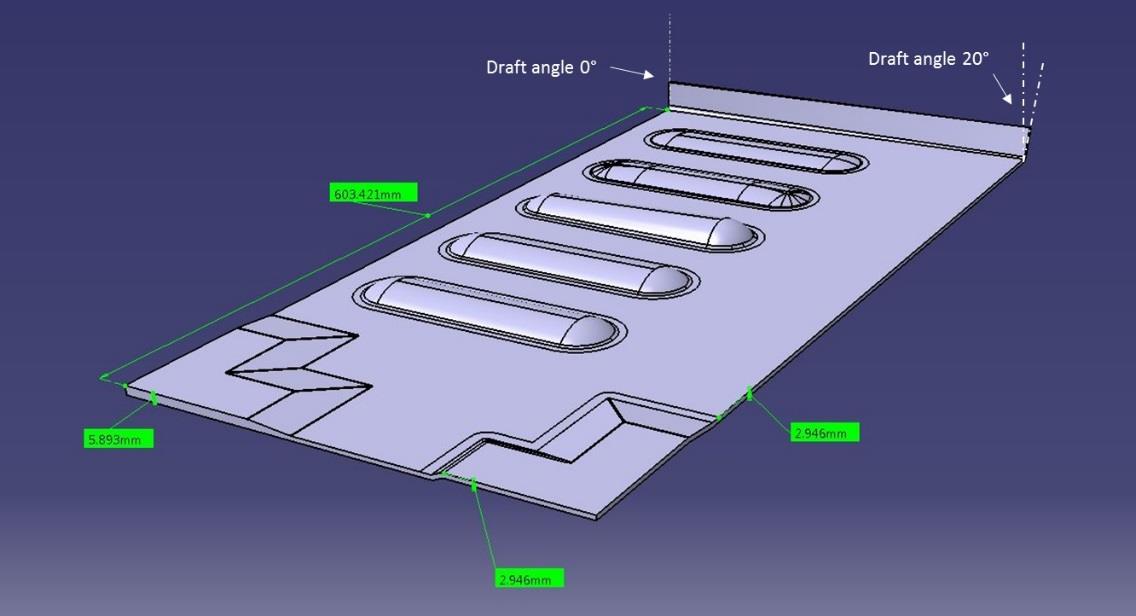
Esta parte plana de 600 milímetros de comprimento apresentava contas paralelas de várias geometrias. A espessura aumentou de 3 para 6 milímetros em um canto (almofada), enquanto o canto oposto apresentava um recuo de espessura constante. A aresta oposta compreendia um flange vertical com ângulo de inclinação que variava linearmente de 0 ° a 20 °.
Deslizamento de almofadas
Os testes iniciais foram executados com almofadas empilhadas na superfície da bandeja. Porém, como as lonas de enchimento ficavam localizadas próximas à borda da peça, era possível que fossem espremidas para fora da peça, resultando em uma região de baixa pressão durante a cura e porosidade. A solução foi intercalar as lonas acolchoadas dentro da pilha de laminados. O risco de escorregamento e porosidade não foi visto em partes posteriores, onde as almofadas foram localizadas longe das bordas e efetivamente travadas pelo material circundante.
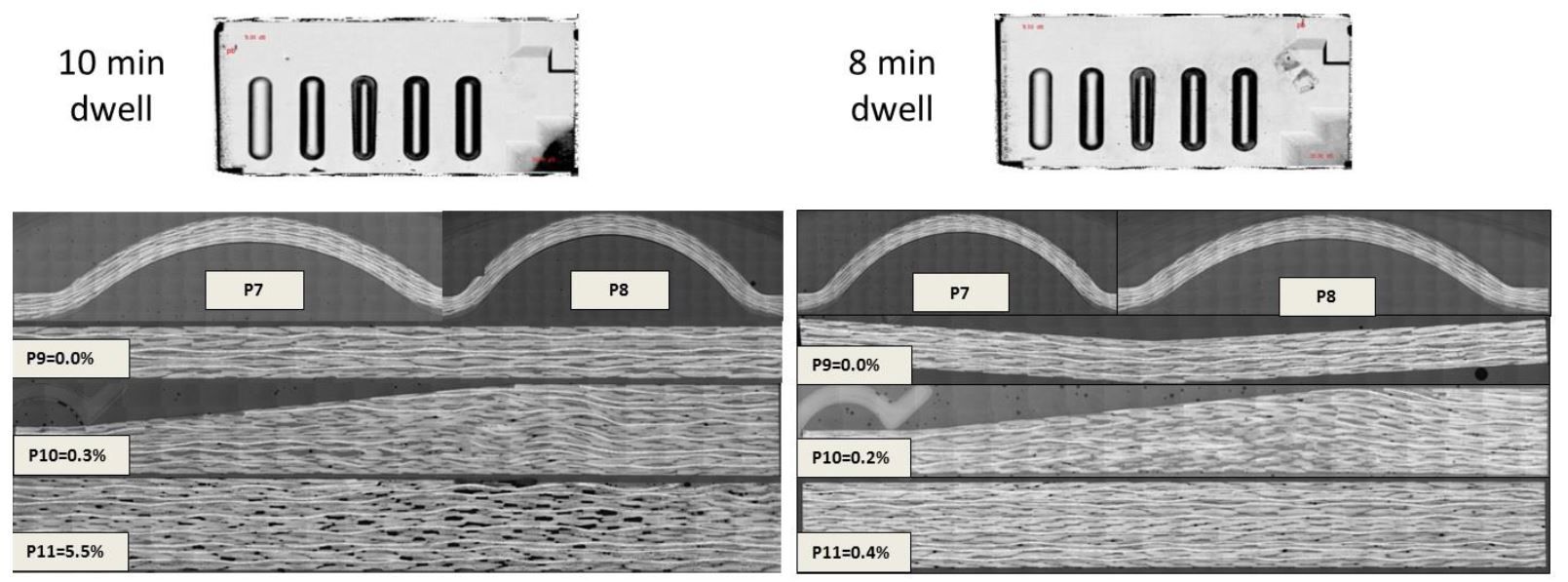
Porosidade com tempo de permanência
O aumento da porosidade também foi observado se o tempo de permanência foi muito longo. Painéis frisados feitos com resfriamento de 8 minutos tiveram menor conteúdo de vazios do que aqueles feitos com resgate de 10 minutos. Isso foi particularmente verdadeiro na área de preenchimento, onde o conteúdo de vazios foi de 5,5% para a pausa de 10 minutos e 0,4% para a parada de 8 minutos. O tempo de espera mais curto mantém um alto fluxo de resina, umedecendo as fibras de maneira eficaz e sustentando a pressão na cavidade da ferramenta durante a cura.
A maior permanência permitiu que o fluxo e a pressão da resina diminuíssem, principalmente na área de acolchoamento, devido à sua proximidade com a borda da cavidade da ferramenta, que não apresentava borda de cisalhamento ou redução na seção. Assim, a pressão na cavidade da ferramenta diminuiu na borda da peça, principalmente em regiões mais grossas onde a seção transversal era maior. A ausência de pressão aqui também exacerbou o risco de escorregamento das lonas acolchoadas. “Ao projetar ferramentas, uma redução na seção ao redor da cavidade da ferramenta ajudará a aumentar e manter a pressão, particularmente para peças com espessuras variadas”, explica Gail Hahn, pesquisador da Boeing e investigador principal do projeto RAPM. “É necessário apresentar alguma forma de pinçamento ou vedação para estimular um estado de pressão hidrostática na cavidade”.
Costela TS-RAPM-002
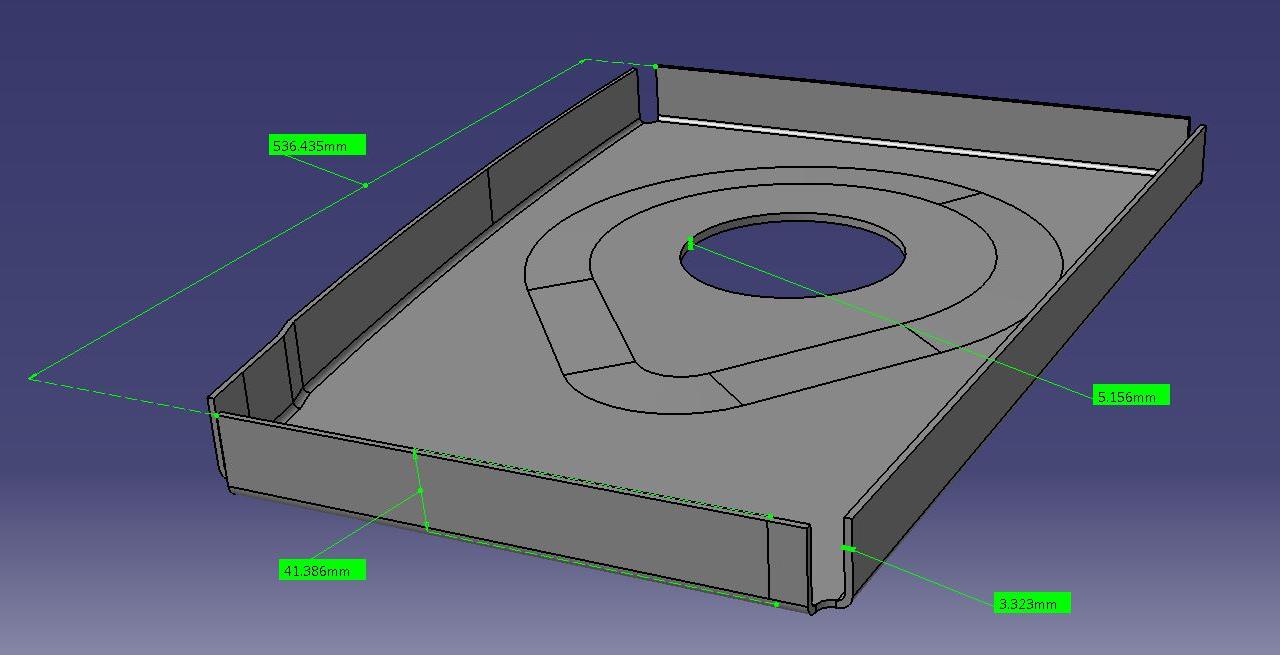
Uma vez que os parâmetros de processamento foram estabelecidos para os painéis frisados TS-RAPM-009, o processo foi repetido para a nervura TS-RAPM-002, que media 540 milímetros em sua borda mais longa. A nervura acumulou espessura no centro de 3,3 a 5,2 milímetros e a profundidade de estiramento foi de 42 milímetros na parte final aparada. Todas as quatro bordas apresentam flanges verticais. Observe que um ângulo de compensação de mola foi determinado durante os testes do painel frisado e foi então aplicado à geometria da ferramenta da nervura. Os testes de painel frisado também levaram a uma maior capacidade de tensão e modularidade da localização da mola na estrutura da mola.
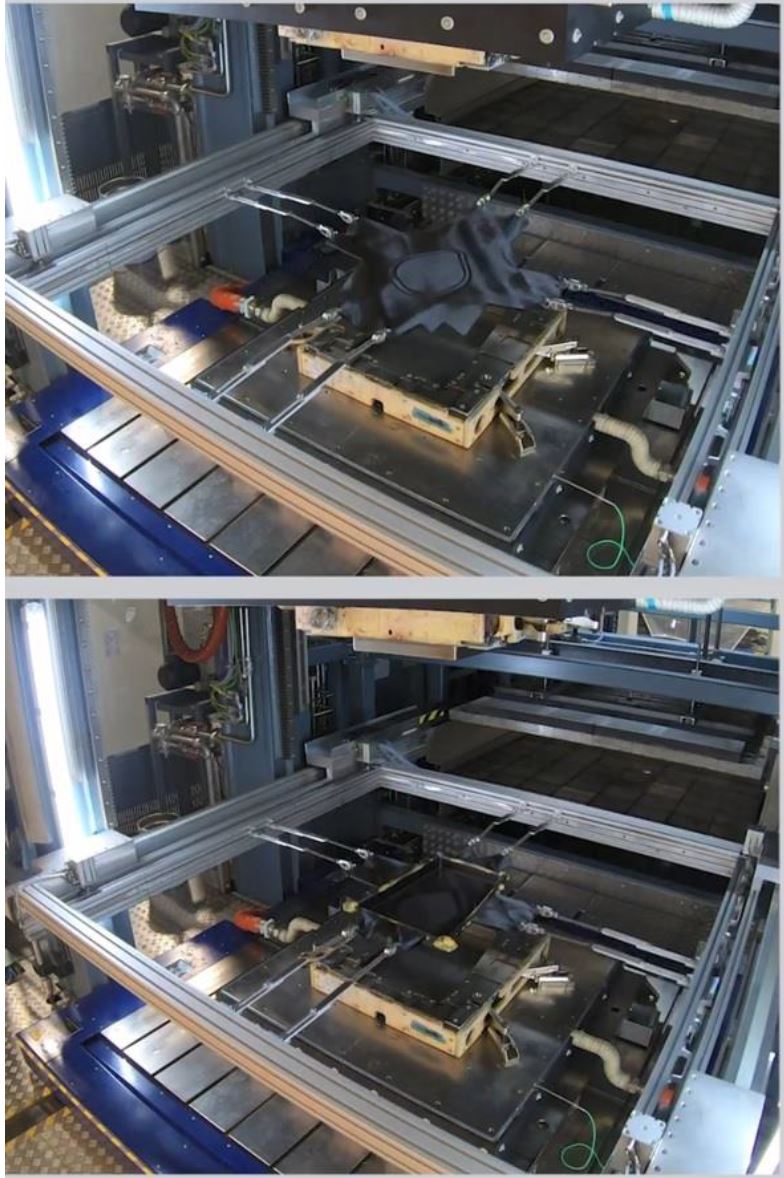
Excesso de material para grampos
As costelas foram feitas usando moldagem de mola e DDF. Devido ao estiramento profundo da nervura, o excesso de material foi necessário para prender as braçadeiras de estrutura de mola, mas isso poderia ser reduzido ao usar DDF. Outro problema era que o projeto da ferramenta limitava o espaço para os grampos de mola ficarem próximos à cavidade da ferramenta.
Variações no CPT
A espessura da camada curada (CPT) foi maior nas partes planas da nervura do que em suas bordas verticais. Argumentou-se que a geometria da peça mantinha a resina dentro da área plana central, observando que os flanges verticais agiam como uma vedação de resina. Isso ajudou na compactação e no acabamento da parte na área plana central. No entanto, os flanges verticais sofreram forte cisalhamento durante o fechamento da ferramenta, o que causou rugosidade da superfície, mas não porosidade (consulte os dados de porosidade abaixo). O CYCOM EP2750, um material a granel inferior, ajudou a mitigar esse efeito - sua espessura inferior diminuiu o cisalhamento.
Variações na espessura da teia com conteúdo de resina pré-impregnada
Investigações de qualidade mostraram nervuras repetíveis com porosidade <0,1% e enrugamento / ondulação mínima da fibra. No entanto, embora fosse assumido que a variação da espessura da peça seria minimizada com o processamento do molde compatível, a revisão dos parâmetros de processamento do material e da peça acabada CPT mostrou que, embora a lacuna da ferramenta nos flanges verticais da nervura fosse fixa e consistente, a espessura da teia poderia variar em função do teor de resina pré-impregnada (menos de +/- 2%) e do processo - CPT pode variar entre os flanges e a teia, pois a resina pode migrar para dentro da cavidade.
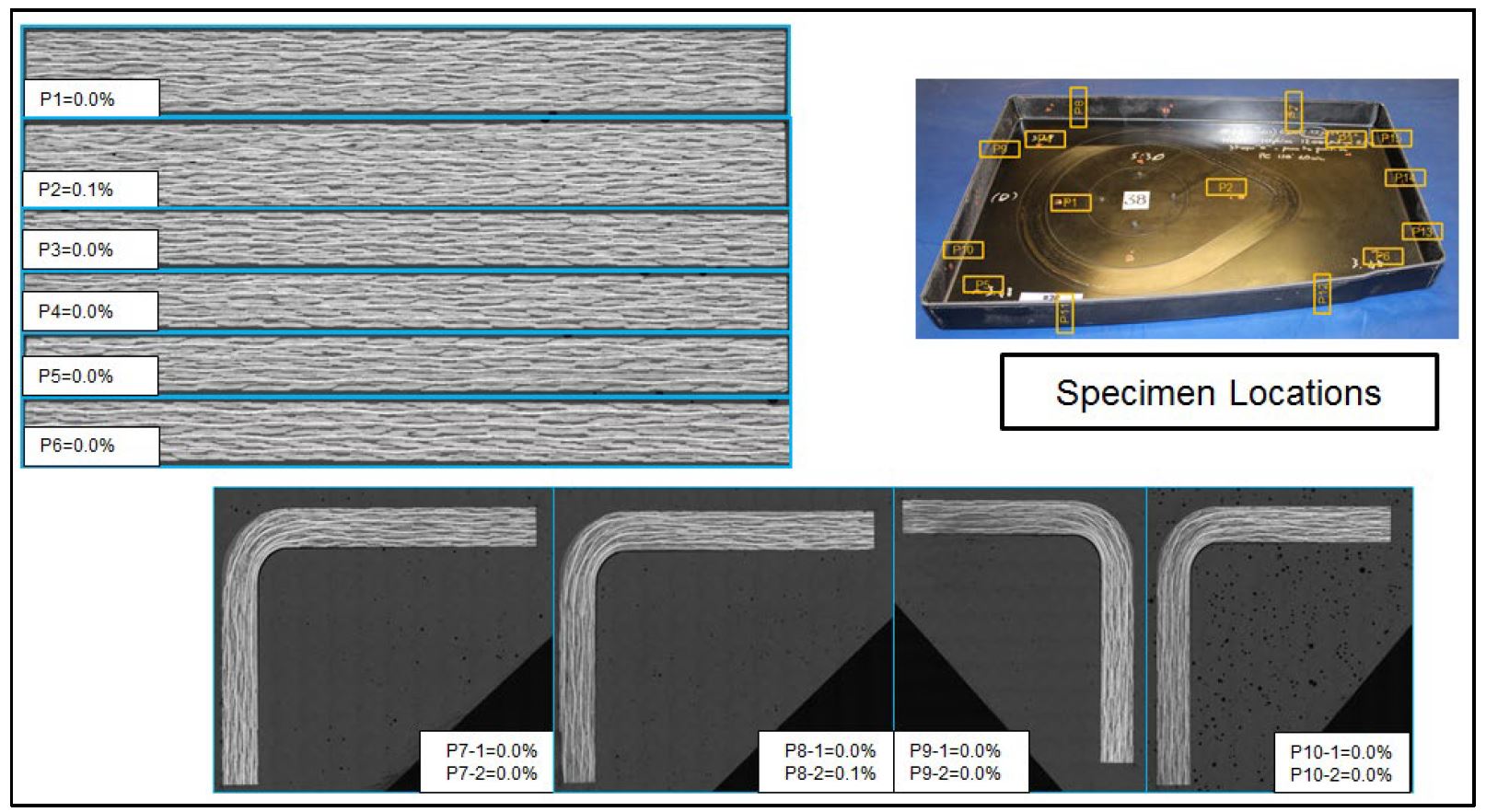
TS-RAPM-003 canal C curvo
Essa peça tinha 640 milímetros de comprimento com um corte em U de 40 milímetros de profundidade na peça final aparada. O raio interno da seção era maior do que o raio externo, e a espessura aumentou de 6,6 milímetros na seção estreita para 8,8 milímetros na extremidade larga. Devido à sua espessura, a parte do canal C era substancialmente mais pesada do que as partes anteriores discutidas. Portanto, a estrutura de mola exigia mais pontos de fixação do que as peças anteriores.
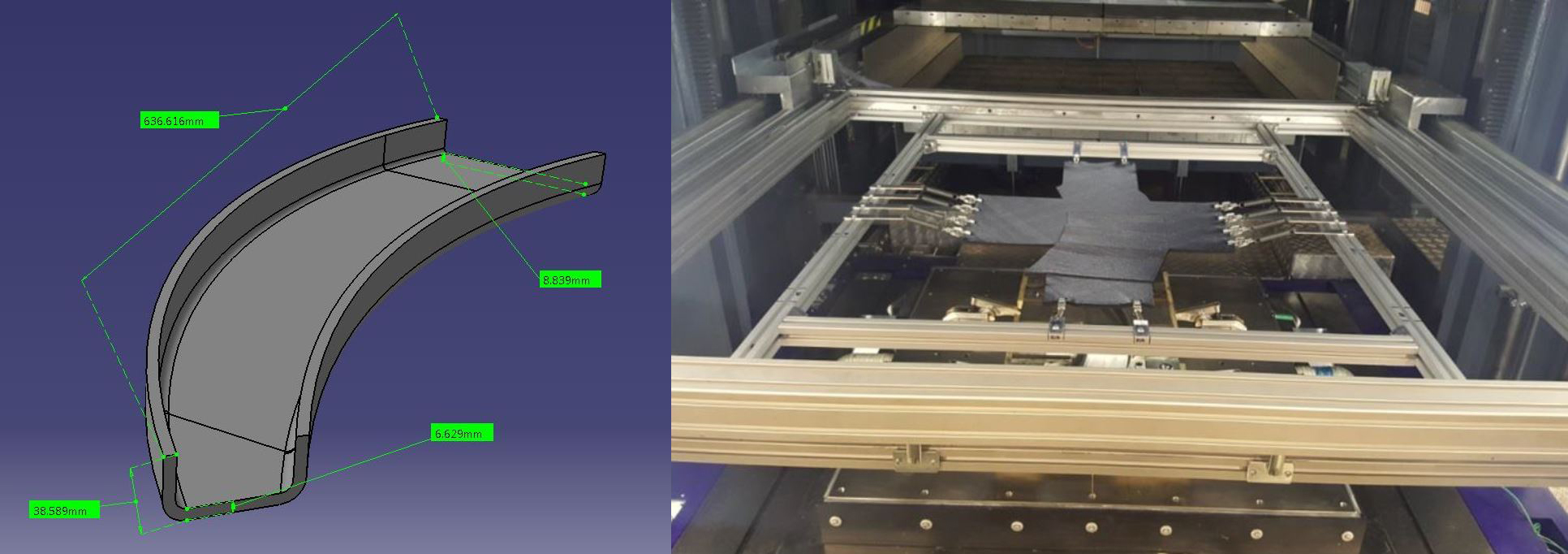
Parada dupla para manter a pressão em partes grossas
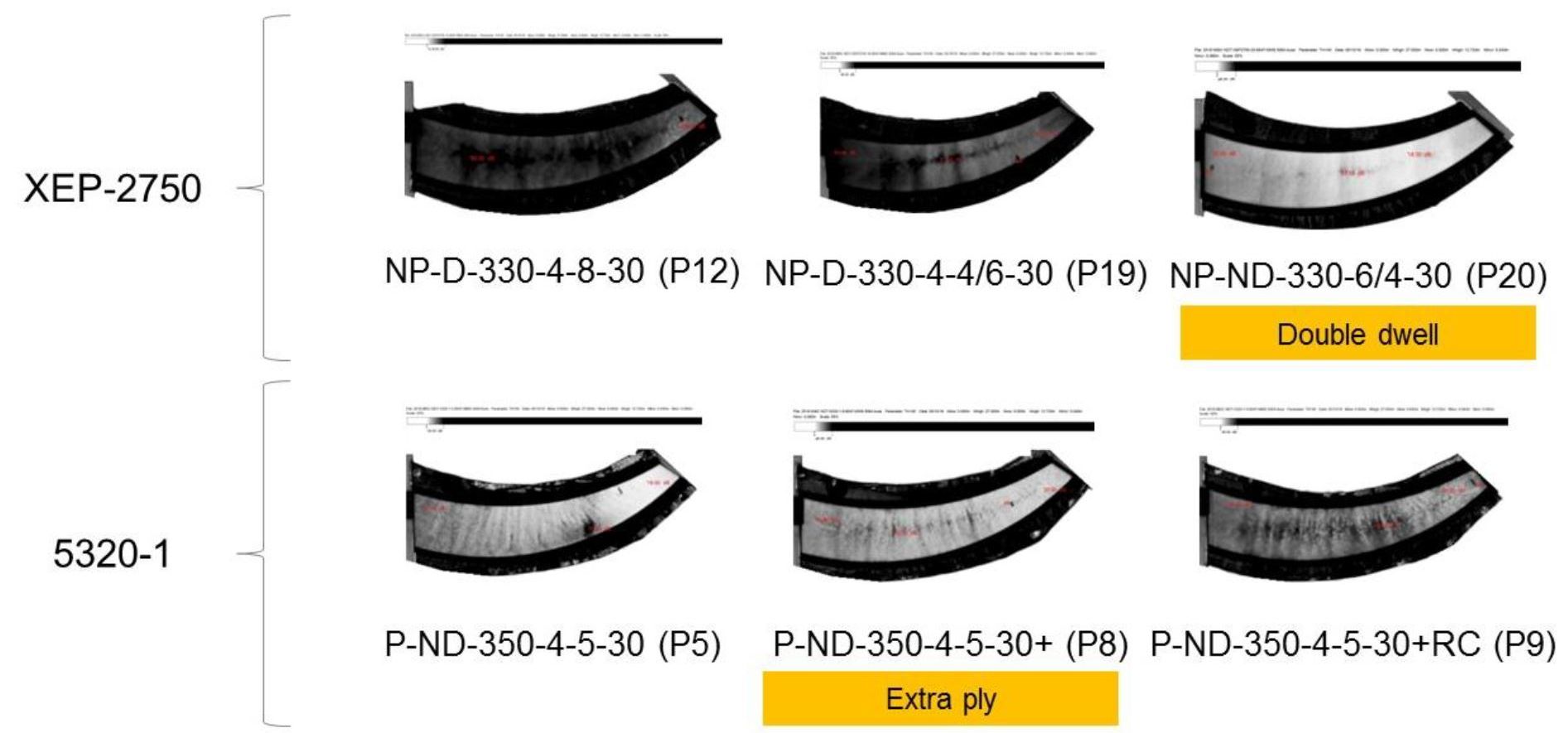
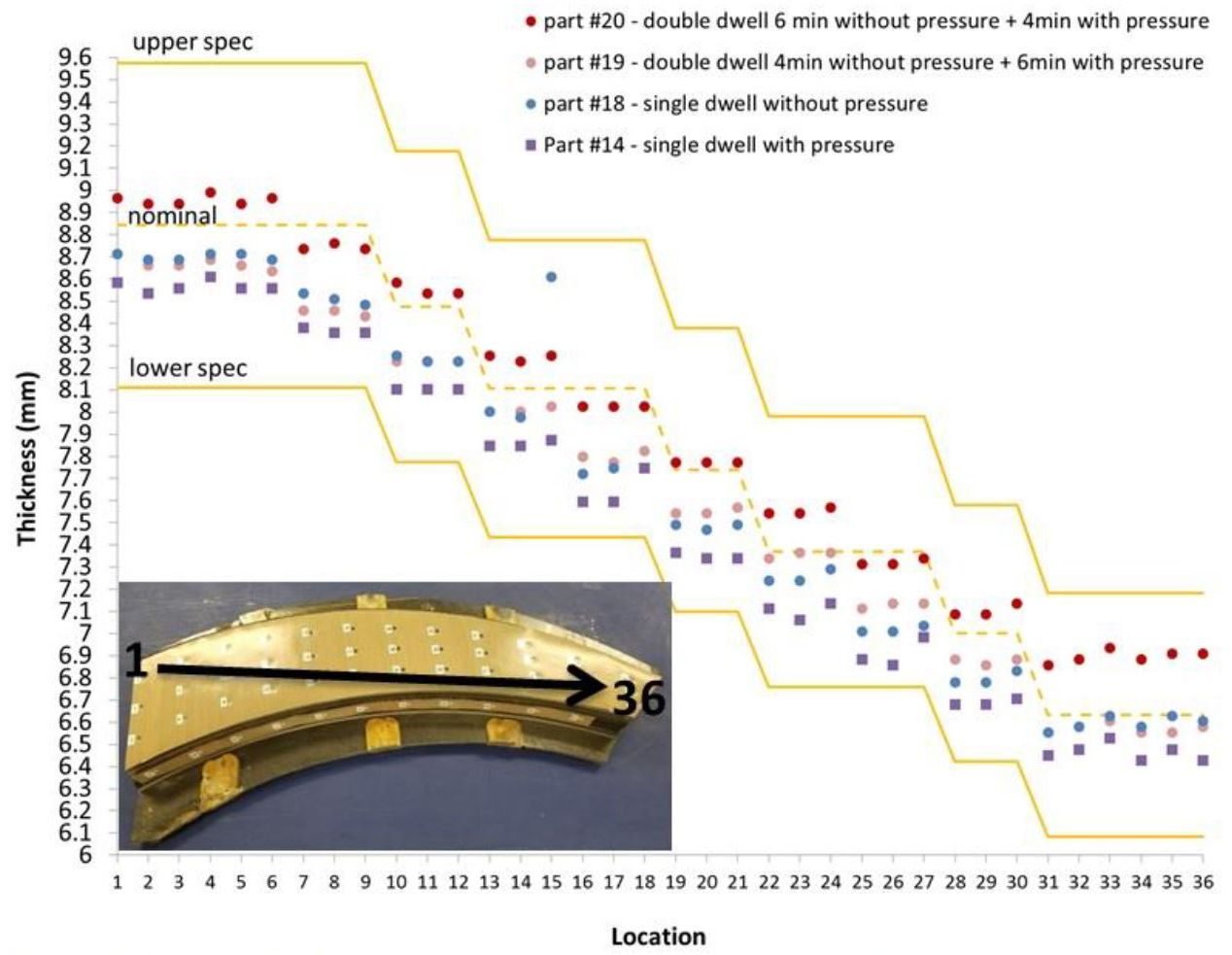
C-scans de peças moldadas destacam uma ruga que se propaga do raio interno para o raio externo para peças que usam espaços em branco pré-consolidados. A escala de cinza indica que as rugas também carregam porosidade.
Essas rugas e porosidade foram removidas para as peças pré-impregnadas do CYCOM EP2750 usando uma “dupla permanência” processo. Consiste em aplicar uma certa pressão durante a pausa imediatamente após o aumento da viscosidade do material. “Isso foi determinado usando os dados fornecidos pela impressora e as ferramentas durante o desenvolvimento do processo”, explica Hahn. “Basicamente, existem duas etapas de aumento progressivo da pressão antes da aplicação de pressão total. Como resultado, o perfil de pressão versus tempo tem uma forma semelhante ao perfil de viscosidade da resina. Uma pausa inicial na espessura total é usada para aumentar a viscosidade da resina para evitar um afinamento da carga do material [em branco ou pré-molde]. Se a carga for de espessura significativa, duas paradas são usadas para evitar a perda de pressão devido ao encolhimento da resina. A primeira parada está em uma lacuna de X e a segunda em uma lacuna de Y, com Y
A Fig. 18 acima mostra o efeito da pausa dupla na espessura da peça do canal C. A combinação da pressão com a viscosidade da resina permitiu que mais resina fosse retida dentro da peça, o que umedeceu as fibras para obter baixa porosidade e aumentar a espessura para atingir o valor nominal necessário, embora mantendo baixa distorção da fibra. No entanto, a equipe RAPM enfatizou que esse processo de dupla permanência é favorecido apenas para peças mais espessas, observando que pode induzir irregularidades de CPT em peças de espessuras variadas.
Lições aprendidas de RAPM e outros testes de peças
Os testes de peças RAPM discutidos aqui contribuíram com conhecimento para a fabricação de alta taxa de peças estruturais aeroespaciais usando moldagem por compressão pré-impregnada. As lições aprendidas incluem:
- Baixo volume é benéfico para a qualidade da peça, especificamente para conter os níveis de porosidade e aumentar o acabamento superficial em bordas verticais. Prepreg com maior teor de resina, como CYCOM EP2750, permite uma janela de fabricação mais ampla, bem como maior repetibilidade do processo
- Idealmente, o equipamento de prensagem deve incluir uma estação de pré-aquecimento infravermelho (IR), estrutura de transporte automatizada para transportar o molde pré-aquecido / pré-formado para o molde, tolerâncias de paralelismo estreitas entre as prensas superior e inferior, capacidade de controlar e monitorar a posição das prensas a uma tolerância restrita e a capacidade de pressionar usando forças baixas e altas.
- A pré-consolidação de blanks / pré-formas permite reduzir a perturbação da fibra em paredes verticais e contribui para reduzir os níveis gerais de porosidade nas peças moldadas. OBSERVAÇÃO, isto é redução de volume, NÃO pré-formação em uma ferramenta moldada
O RAPM demonstrou que a moldagem por compressão pré-impregnada pode produzir estruturas de grau aeroespacial de alta qualidade, ao mesmo tempo que reduz o tempo de ciclo e a mão de obra. Isso permite que os compostos concorram melhor em estudos comerciais para aplicações aeroespaciais, proporcionando maior economia de peso e desempenho do componente (por exemplo, resistência à corrosão, rachaduras e fadiga, etc.).
A Solvay e a Boeing trabalharam juntas para refinar o novo sistema pré-impregnado EP2750, demonstrando tempos takt de até 20 minutos, graças a uma combinação de química de materiais, pré-impregnação e conhecimento e automação de processo.
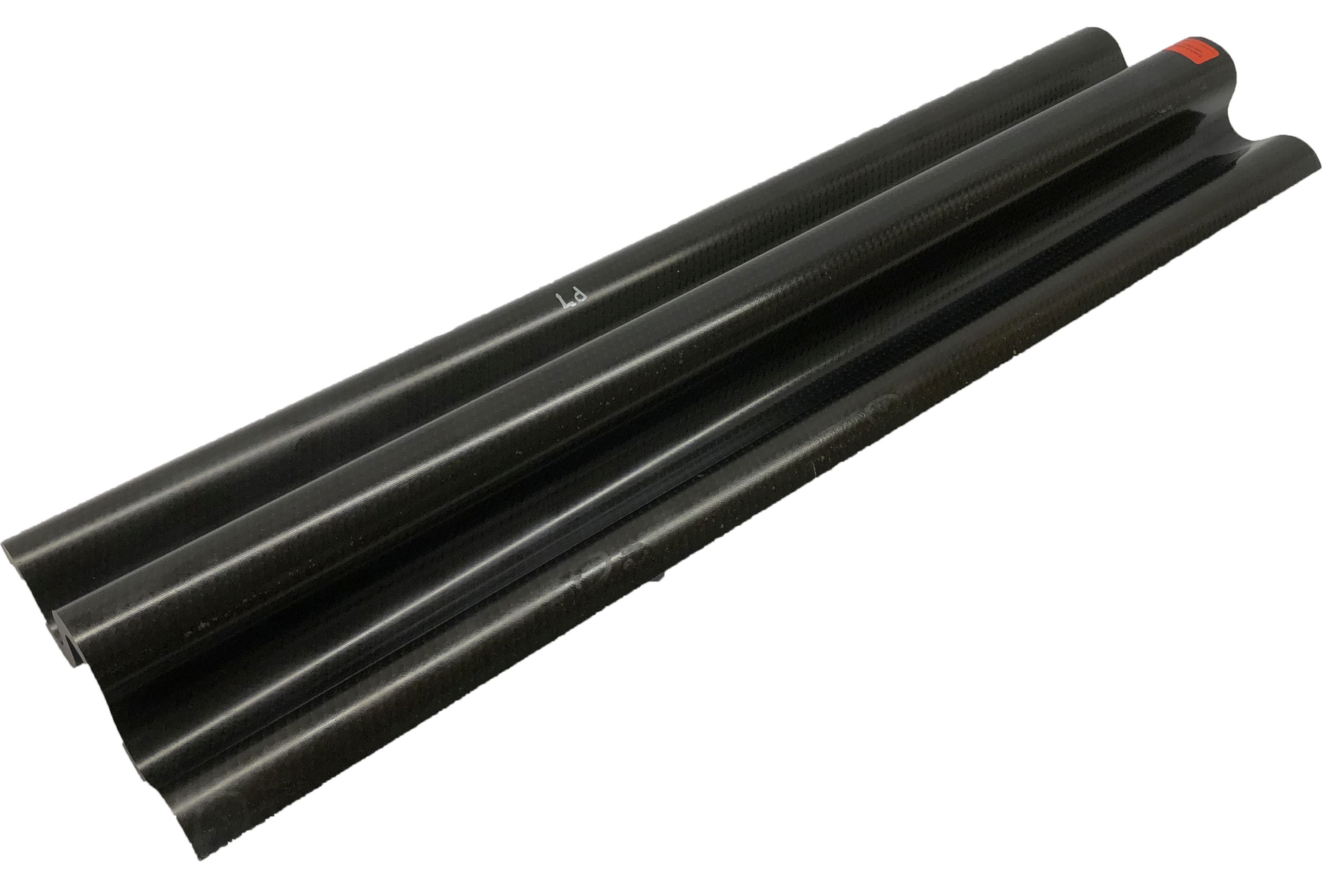
Além das peças de Desenvolvimento de Fabricação discutidas acima, RAPM também produziu várias peças de Desafio e Transição, destinadas a desafiar desenvolvimentos iniciais e transição candidatos com potencial para vencer o alumínio usinado em aplicações de defesa. Esses incluem:
- Parte do desafio TS-RAPM-007 Solvay
- TS-RAPM-008 painel de acesso à capa
- TS-RAPM-012 Boeing “wave”
- braço motor TS-RAPM-014
- TS-RAPM-015 fin
Os resultados e as lições aprendidas com esses testes de peças e outros estudos de recursos de fabricação RAPM serão publicados em 2020/2021.
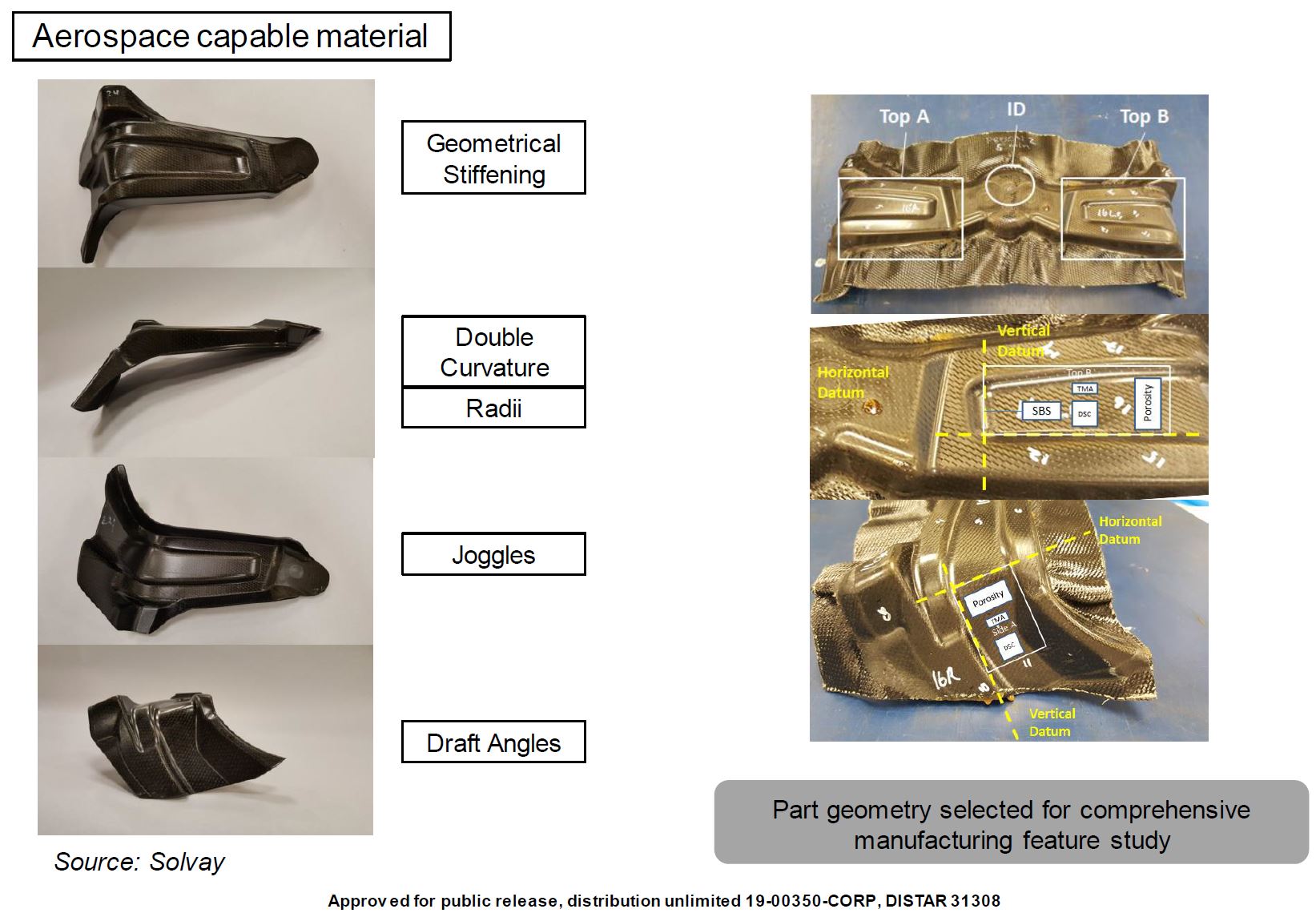
Testes de peças automotivas Solvay
A Solvay também ilustrou como EP2750 funciona em peças automotivas, como um pilar B de 36 por 16 por 2 polegadas com uma espessura de 0,0725 polegadas, compreendendo 5 camadas de Solvay THORNEL T650-35 módulo padrão 3K de fibra de carbono em um 376 tecido de cetim com 8 arnês em gramas / metro quadrado. Esta peça foi feita na Solvay Heanor, Reino Unido, usando DDF. Quando comparado ao pré-impregnado padrão autoclavado, a combinação de CYCOM EP2750 e DDF oferece uma redução de 60% no tempo de ciclo e 85% no tempo takt (tempo entre o início de uma peça e a próxima peça em uma linha de produção - ou seja, o tempo de pulso da linha) .
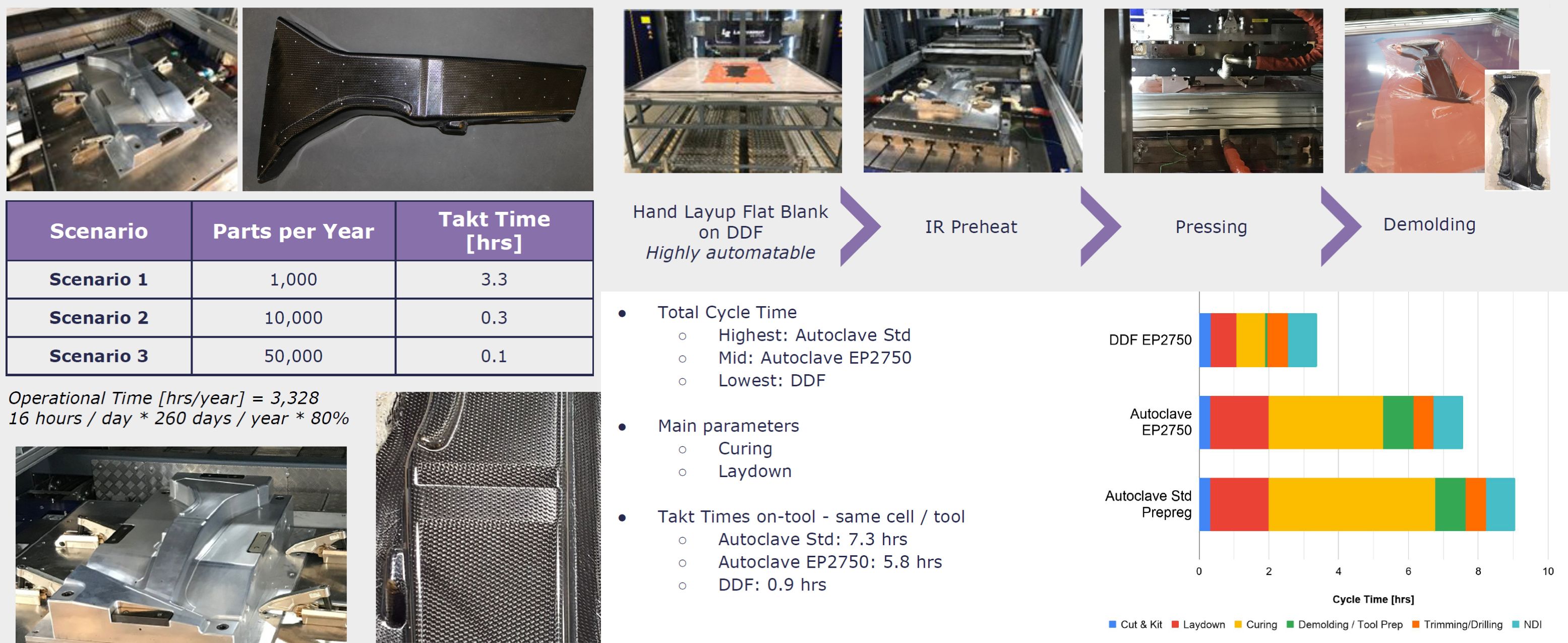
Resina
- Moldagem por compressão vs moldagem por injeção:Qual é a diferença?
- Moldagem por compressão:Como funciona
- Moldagem por compressão e moldagem fundida:prós e contras
- Agente de purga altamente eficiente para poliolefinas de moldagem por sopro
- PEEK de alta viscosidade para moldagem por injeção e extrusão
- Esteira personalizada para moldagem de pré-forma
- Terceira patente emitida para termoplástico flexível prepreg
- Solvay lança pré-impregnado epóxi para moldagem por compressão de aeroestruturas
- Toray pré-impregnado aeroespacial otimizado para moldagem por pressão assistida por vácuo
- Fitas contínuas, D-LFT se encontram em novo processo de moldagem por compressão