Controle baseado em sensor de ferramentas de corte, máquinas-ferramentas passam da prancheta para o mainstream
Um fator chave de sucesso para as iniciativas da Indústria 4.0 e IIoT (Industrial Internet of Things) é o surgimento de mais e melhores sensores em centros de usinagem e até mesmo nas próprias ferramentas de corte. Esses sensores fornecem os dados e a conectividade que são a base da “fábrica do futuro”.
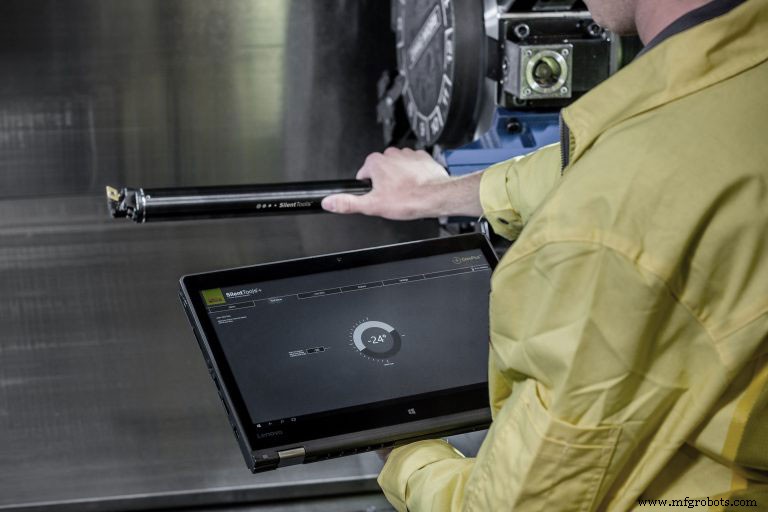
Mas, longe de ser futurista, há uma variedade de “sensores inteligentes” disponíveis hoje – coletando dados e mostrando aos operadores a saúde de suas máquinas e o processo de usinagem. A evolução é alcançada através da medição cada vez mais precisa da posição da peça e da forma geométrica da peça acabada, bem como da configuração e controle das ferramentas utilizadas no processo.
A Engenharia de Manufatura pediu a vários especialistas do setor que avaliassem o estado atual dos sistemas de controle de corte baseados em sensores e também olhassem para a bola de cristal para ajudar a identificar oportunidades futuras.
Agora e no futuro
Na área de controle e otimização baseados em sensores, onde estamos no continuum da prancheta aos produtos maduros? A resposta para essa pergunta é:“Depende”.
“Para medição básica e controle adaptativo, estamos bem ao longo da curva de aprendizado”, disse Frank Powell, gerente de produto para produtos de moagem da Marposs Corp. (Auburn Hills, MI). “As máquinas-ferramentas podem ser equipadas com uma variedade de sensores e transdutores em processo. No primeiro nível, esses sensores são utilizados para proteção da máquina, pois um sistema pode reagir 1.000 vezes mais rápido do que um operador a uma força inesperada ou colisão potencial. A tecnologia avança através da medição cada vez mais precisa da posição da peça e da forma geométrica da peça acabada, bem como da configuração e controle das ferramentas utilizadas no processo.”
Em termos da Indústria 4.0, a tecnologia de fabricação digital de ferramentas de corte está muito mais próxima da prancheta do que de um produto maduro, de acordo com Neil Munson, especialista em vendas técnicas da Silent Tools na Sandvik Coromant (Fair Lawn, NJ). “Estamos no precipício de uma mudança de paradigma em nossa indústria. Na verdade, estamos dando o salto inicial para ferramentas de corte inteligentes baseadas em sensores em nossa empresa”, disse ele.
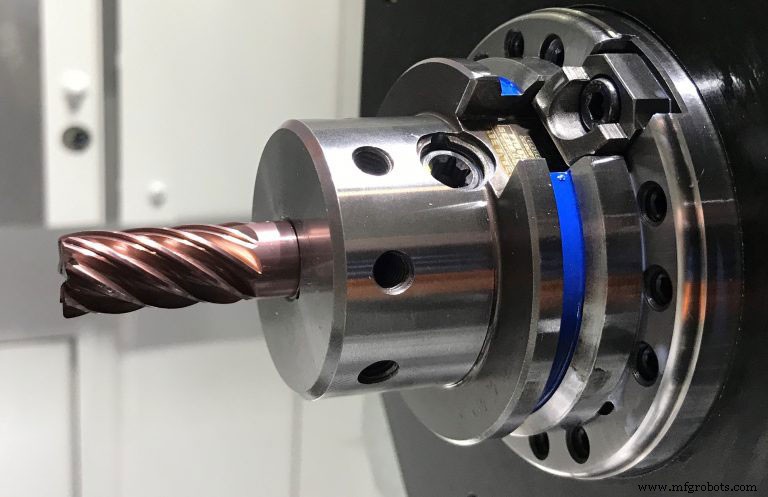
Joe Volansky da BadAxe Tooling Solutions tinha uma visão um pouco diferente. “Os produtos são comprovados e estão bem ao longo da curva de aprendizado e podem ser aplicados de maneiras revolucionárias”, disse Volansky. “No nosso caso, estamos introduzindo um produto para operações de fresamento baseado em ciência comprovada, que apresenta uma solução de uma maneira completamente nova no limite da física das máquinas.” BadAxe Tooling Solutions é uma aliança de três empresas americanas:Briney Tooling Systems (Bad Axe, MI), Fullerton Tool Co. (Saginaw, MI) e BlueSwarf LLC (State College, PA).
“Minha opinião é que estamos no meio da curva em termos de desenvolvimento”, disse Wade Anderson, gerente especialista em produtos e gerente de Centros de Tecnologia da Okuma America Corp. (Charlotte, Carolina do Norte). “Para eficiência de equipamentos básicos e capacidade de comunicação com dispositivos periféricos, existem várias soluções prontas para uso imediato. No entanto, as tecnologias de inteligência artificial (IA) e realidade aumentada (AR) estão cada vez mais em alta.”
Com a grande quantidade de dados agora sendo gerada a partir de equipamentos no chão de fábrica, as tecnologias emergentes às quais Anderson se refere são essenciais, de acordo com Andy Henderson, vice-presidente de engenharia da Praemo (Kitchener, ON). “No mundo da automação, houve uma evolução muito ‘física’ desde a década de 1970”, disse Henderson. “A próxima fronteira é a evolução ‘mental’ – adicionando inteligência aos dados usando IA e aprendizado de máquina (ML). No continuum, essas tecnologias estão maduras e são utilizadas continuamente nos espaços pessoais e de consumo (Google, Amazon, Facebook, etc.). Os aplicativos dentro da indústria de manufatura estão atrasados, mas os softwares que usam essas tecnologias, como o Razor, estão ajudando as oficinas a perceber o valor da IA e do ML.” Razor é um produto Praemo que se conecta a fontes de dados, reúne informações e fornece insights e recomendações sugeridas para ajudar os usuários a tomar medidas preventivas para reduzir o tempo de inatividade do equipamento, otimizar processos de produção e gerenciar riscos.
Regra dos sensores!
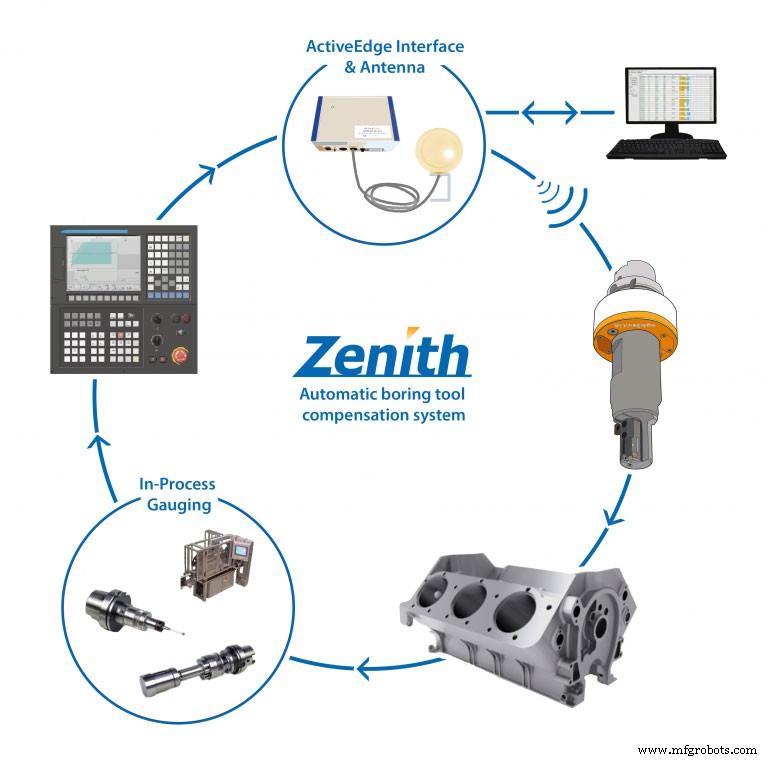
Todos os nossos especialistas do setor concordaram com o papel fundamental que os sensores desempenham. Existe um velho ditado:“O que é medido é gerenciado”. Embora seja incerto quem disse isso (alguns sugerem Lord Kelvin, outros Peter Drucker), isso ressalta o fato de que qualquer tentativa de controlar ou otimizar uma máquina deve ser baseada em dados rápidos, precisos e confiáveis no ponto-chave de contato – onde a ferramenta de corte encontra a peça de trabalho.
Tecnicamente falando, a tecnologia para coletar, distribuir e analisar dados com sucesso para controle adaptativo estava disponível muito antes do interesse atual na Indústria 4.0 e na IIoT. Historicamente, os equipamentos de medição em processo podem traçar suas raízes há mais de 60 anos (por exemplo, o medidor de Mario Possati para verificação de peças durante a retificação). No entanto, os grandes avanços em sensores ocorreram muito mais recentemente.
Tecnologia recente
Um desses avanços é uma ferramenta de mandrilamento que compensa automaticamente o desgaste da aresta de corte. “Independentemente da sofisticação de uma máquina-ferramenta CNC, ela não pode compensar automaticamente o desgaste da aresta de corte em uma ferramenta de mandrilamento”, disse Anthony Bassett, presidente da Rigibore Inc. (Mukwonago, WI). “Nossa ferramenta ActiveEdge alimentada por bateria automatiza o dimensionamento em processo de arestas de corte de ferramentas de mandrilamento. Ele usa tecnologia sem fio para ajustar remotamente vários diâmetros de aresta de corte em uma única ferramenta, otimizando o desempenho do processo e eliminando a necessidade de intervenção do operador.”
Forjar em um novo território na área de fresamento é o sistema de montagem e software BadAxe Smart Tool. BadAxe substitui tentativa e erro com física para atingir imediatamente o “ponto ideal” de uma máquina quando ela é iniciada, de acordo com a empresa. Usando medições dos padrões de frequência de vibração residentes para uma combinação específica de máquina, fuso, porta-ferramentas e ferramenta, os algoritmos e análises patenteados da empresa calculam a zona de estabilidade ideal para a máquina operar. porta-ferramentas e ferramenta pré-balanceados e montados, além de uma interface de software otimizada para máquinas individuais.
“Todo mundo sabe que vibração e trepidação são os principais fatores limitantes na usinagem de alta velocidade”, disse Volansky da BadAxe. “Normalmente, os operadores usam tentativa e erro para encontrar o avanço, velocidade, largura de corte e profundidade de corte corretos. Em muitos casos, eles acham que atingiram a parede em termos de desempenho quando, na realidade, a operação sem vibração seria encontrada em uma configuração contra-intuitiva onde existem taxas de remoção de metal muito mais altas. Essa configuração é definida pelo nosso produto imediatamente desde o início, independentemente de passo por cima, corte de slot completo ou cantos. A tecnologia subjacente provou aumentar significativamente o ROI de um trabalho por organizações como a Boeing Phantom Works, o Departamento de Defesa dos EUA e outras.”
BadAxe está construindo um grande banco de dados para diferentes combinações de máquinas e montagens. Se a máquina de um cliente não estiver no banco de dados, um teste único pode ser feito para determinar sua dinâmica de configuração.
A Sandvik Coromant faz a transição de sensores em processo para sensores em ferramenta com a introdução de seu sistema inteligente SilentTools+ ferramentas de corte. “SilentTools+ são soluções de ferramentas amortecidas para fornecer uma visão tremenda dos processos de usinagem de longo balanço, onde os operadores normalmente estão voando às cegas”, disse Munson.
“A usinagem de longo balanço em uma instalação de alta tecnologia é um desafio porque [os operadores] querem ter controle do processo até a ponta de corte”, disse ele. “Incorporamos sensores em nosso SilentTools que se comunicam via Bluetooth com uma interface gráfica para que o operador tenha olhos e ouvidos dentro da máquina fechada e dentro de um furo. Além disso, possui um recurso que permite uma configuração rápida e fácil, determinando quando a ponta de corte está no centro.”
Usando o sistema SilentTools+, a deflexão da ferramenta, vibração, forças de corte, carga da ferramenta e temperatura são monitorados em tempo real. “Devido à percepção de todas essas áreas, acreditamos que as taxas de sucata serão reduzidas e ganhos de produtividade serão realizados, gerando economias reais”, acrescentou Munson.
Informações por favor!
Enquanto algumas saídas do sensor são apenas para informação, o valor agregado é quando os sinais do sensor são processados e usados para controlar a qualidade da peça e a condição da ferramenta. Os fabricantes podem minimizar os caminhos da ferramenta e o tempo de usinagem, melhorar o acabamento da superfície, maximizar a vida útil da máquina e usinar com eficiência peças mais desafiadoras, como aquelas com geometrias complexas, paredes finas, cilindros ocos e eixos finos.
Disse Anderson, “O Sistema de Monitoramento Okuma é um bom primeiro passo. Ele permite até 64 entradas diferentes que podem ser personalizadas para necessidades específicas do processo. Temos clientes que foram capazes de medir o tempo de inatividade da máquina e analisar os dados OEE [eficácia geral do equipamento] para determinar que uma coisa simples era desligar a máquina quando um operador estava preso em outro lugar. Ao usar o sistema de monitoramento, o operador [pode ser alertado] de que há um problema em potencial que a ação preventiva pode evitar.”
Henderson, da Praemo, acredita que o caminho para o sucesso da fabricação passa pela montanha de dados que as ferramentas estão gerando em aplicações de usinagem. “Esses dados são 'matéria-prima' valiosa para otimização”, disse ele. “Os algoritmos para analisar dados em nosso software Razor podem filtrar grandes quantidades de dados para encontrar inter-relações e padrões que um humano com uma planilha nunca descobriria. As tecnologias de IA e ML são usadas para desenvolver modelos que ajudam operadores e gerentes a chegar a conclusões claras muito rapidamente e agir com base em conclusões baseadas em dados. Embora a inteligência seja artificial, ela imita muito de perto como os humanos no mundo da manufatura abordam as coisas. A única diferença é que ele não fica sobrecarregado por grandes quantidades de dados. Quanto mais os dados são coletados e quanto mais dados são coletados, mais o Razor aprende.”
Habilidade comprovada
Os sistemas de hoje provaram sua capacidade de manter o processo de corte, antecipando quando algo não está certo e notificando um operador ou a máquina para tomar medidas corretivas, de acordo com Powell da Marposs. “A decisão de notificar apenas, ou tomar ações automáticas, é ditada pelo cliente”, disse ele. “Tecnicamente, temos muitos recursos para controle automático que, em alguns casos, não estão sendo utilizados.”
Um novo sistema da Marposs chamado BLÚ é o resultado de mais de 50 anos de experiência em retificadoras e outras máquinas-ferramentas. Ele combina todos os aplicativos de monitoramento de máquina-ferramenta e controle de processo em um único sistema para monitoramento de ferramenta e processo em tempo real, controle adaptativo e mitigação de falhas com um rápido tempo de processamento e amostragem. Segundo Powell, “o BLÚ foi projetado para se integrar quase perfeitamente com a máquina-ferramenta para auxiliar o operador em qualquer modo:configuração, manual ou automático”.
O coração do sistema é um nó mestre alojado dentro do gabinete da máquina. Possui estrutura de barramento para conectar outros nós para medições na máquina, monitoramento de emissões acústicas, balanceamento de rodas (esmerilhamento), retração de ferramentas e outras funções.
O sistema Zenith é um sistema automático de circuito fechado para operações de perfuração, de acordo com Bassett da Rigibore. “Os sistemas tradicionais são puramente mecânicos sem feedback contínuo para a máquina de perfuração”, disse ele. “A Zenith fornece feedback ao controle da máquina para confirmar que a ferramenta foi ajustada na quantidade desejada. Esse feedback do sensor de posição evita que uma peça defeituosa seja usinada.”
Até onde essa tecnologia pode nos levar?
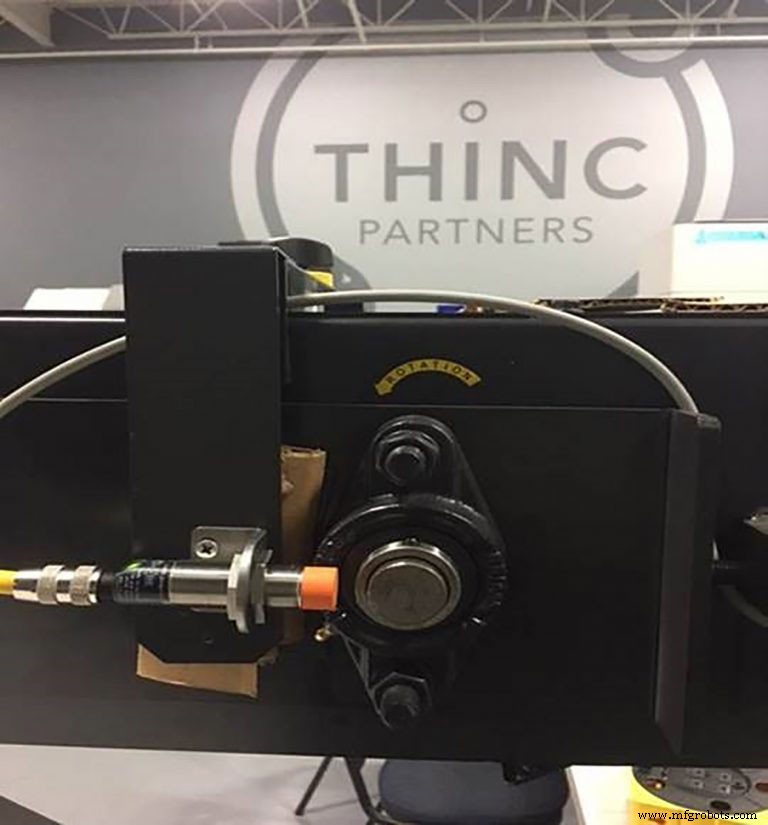
“Não vejo necessariamente um jogo final para soluções de ferramentas de corte digitais ou baseadas em sensores”, disse Munson, da Sandvik Coromant. “Em oficinas de máquinas modernas e instalações de fabricação, os sensores e o uso de IIoT em ferramentas de corte se tornarão mais onipresentes nos próximos cinco a 10 anos, seguindo o caminho das aplicações do consumidor [produto]. Para nós, a progressão natural é a integração de nosso SilentTools+ nos controles de máquinas CNC. Hoje, é um sistema autônomo com uma visualização de processo ao vivo. Estamos trabalhando com fabricantes de máquinas-ferramenta e parceiros de software CAM para passar de um sistema autônomo para controle de máquina e integração de processos.”
Anderson de Okuma concordou. “A tecnologia e, mais importante, a implementação da tecnologia, irão gerar novas tecnologias”, disse ele. “Há muitos anos, eu achava que um espelho retrovisor com escurecimento automático em um veículo era ridículo. Agora, eu não compraria um veículo sem um. De maneira semelhante, em nossa indústria, as novas tecnologias ajudarão a desenvolver novos mercados para avanços alternativos”.
Powell de Marposs concordou que nunca deveria haver um jogo final. “Acho que a tecnologia está pronta para monitorar todos os principais parâmetros e variáveis”, disse ele. “Certamente, existem áreas que podem ser melhoradas e estamos trabalhando diariamente para desenvolver sensores mais rápidos e sensíveis, e softwares que possam processar os dados dos sensores de forma mais rápida e inteligente. Dentro de 10 anos, tenho certeza de que haverá pelo menos um divisor de águas, um avanço técnico que tornará uma oficina mecânica mais eficiente e produtiva. Quando o jogo mudar, nós mudaremos com ele.”
Volansky da BadAxe acha que sua empresa tem um divisor de águas agora. “O ritmo de desenvolvimento está aumentando”, disse ele. “Os clientes não querem esperar cinco ou 10 anos. Temos um produto que redefine a eficiência e ajuda as máquinas-ferramentas a operar nos limites da física. O próximo passo para nós, no entanto, será remover nosso conjunto de ferramentas da equação, incorporando nosso sensor de vibração proprietário e análise de dados diretamente na máquina e em sua lógica.” Dessa forma, a máquina funcionará apenas em seu estado mais otimizado, sem tentativa e erro do operador, acrescentou.
Como disse Bassett da Rigibore, “Algumas metas de desenvolvimento para nós são o pedido automático de ferramentas de metal duro usando o controle CNC, uma mudança para menos intervenção dos operadores, ajustes feitos a partir de um local central e a entrada de um modelo sólido na máquina CNC enquanto outro processo está em operação. Os principais limites que enfrentamos hoje são a incompatibilidade e a falta de padrões entre os diferentes fabricantes de máquinas CNC e fabricantes de controladores de máquinas.” No final, uma abordagem proprietária limitará o crescimento e será mais cara para um cliente que deseja adicionar facilmente novos recursos, concluiu Bassett.
De acordo com Henderson, da Praemo, algumas pessoas definem a fabricação sem luz, sem intervenção humana, como o jogo final. “Pessoalmente, acho que o apagamento das luzes é semelhante à busca pela paz mundial”, disse ele. “Para a indústria manufatureira, é um conceito que é atraente para se lutar, mas não será alcançável em muitas situações. Sensores embutidos em ferramentas e redes de ferramentas; software que coleta, organiza e analisa dados de forma transparente; e máquinas-ferramentas que são conectadas em rede a uma fonte de inteligência de fábrica nos aproximam muito daquela fábrica apagada. Isso não significa que as máquinas substituem as pessoas. Isso os libera para fazer um trabalho menos servil, mais satisfatório e definitivamente mais produtivo. É semelhante ao advento do CNC, que automatizou o controle manual dos centros de usinagem. Permitiu que as pessoas trabalhassem de forma mais segura e produtiva.”
Sistema de controle de automação
- Solução de Corte para Indústria de Tapetes - Máquina de Corte Digital
- Solução de corte para a indústria cinematográfica - Máquina de corte digital
- Máquina de corte digital e a laser - a melhor solução de corte para a indústria têxtil / têxtil
- A cadeia de suprimentos está atraindo novos talentos de mais gerações e setores
- Nova máquina construída e um cliente da Inglaterra aprendeu a operar esta máquina CNC
- A Universal Robots faz parceria com a Phillips Machine Tools India
- Operações de Torno e Ferramentas de Corte de Torno
- O que é torneamento de máquina?
- Ferramentas multifuncionais que todas as oficinas devem ter
- Uma rápida comparação de máquinas-ferramentas CNC