Repensando os sistemas de controle para almofadas de vários poços
Dados, requisitos de controle impulsionam a necessidade de arquitetura de controle modular e escalável.
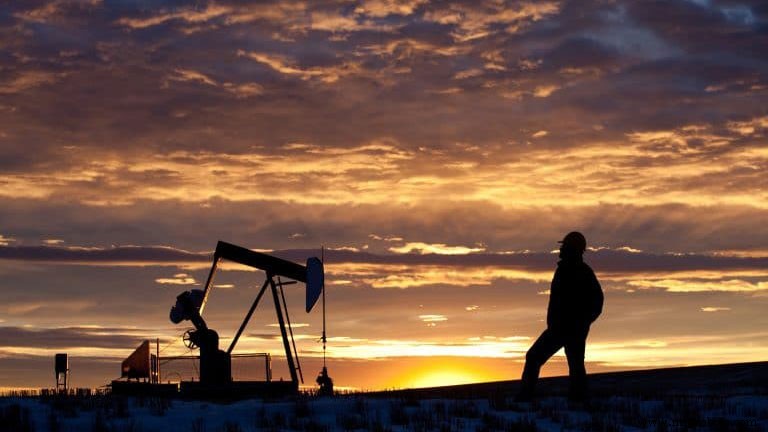
Os avanços na perfuração estimularam a evolução das operações de petróleo e gás de campos simplistas de poço único para blocos mais complexos de vários poços.
Hoje, muitos produtores estão usando técnicas de fraturamento e perfuração lateral para colocar 10 ou mais poços em um bloco. Alguns operadores estão até levando suas operações para até 52 poços em uma única plataforma.
Esses avanços não apenas aumentaram as recuperações de produção de poços, mas também criaram oportunidades de produção inteiramente novas em áreas não convencionais. Eles também permitiram que os produtores de petróleo e gás reduzissem sua pegada operacional.
Apesar de todos os benefícios das almofadas multi-poços, no entanto, seu grande aumento em tamanho e escopo criou um novo desafio. A densidade mais alta de vários poços em um único bloco aumenta o equipamento necessário no local e resulta em dados e requisitos de controle muito maiores.
As arquiteturas de controle tradicionais que têm sido usadas por décadas estão sendo levadas ao limite e simplesmente podem não ser mais sustentáveis. Em vez disso, são necessários sistemas de controle mais avançados para lidar com as arquiteturas escaláveis exigidas pelos blocos de poços modernos.
Como resultado, tanto os operadores quanto os fabricantes de equipamentos que os apoiam devem agora modificar - se não mudar radicalmente - sua abordagem de sistemas de controle para esses blocos de vários poços.
Evolução da tecnologia RTU
Os produtores de petróleo e gás a montante contam com a tecnologia de unidade terminal remota (RTU) para controle do local do poço há décadas. Inicialmente, o custo de implementação das UTRs e os desafios em programá-las limitavam os dispositivos à simples aquisição e controle de dados.
Com o tempo, no entanto, as UTRs incorporaram mais recursos, incluindo E/S, comunicações e programação IEC-61131. Esses recursos permitiram que os operadores de petróleo e gás monitorassem mais pontos de dados, registrassem histórico e alarmes e adicionassem cálculos mais complexos às UTRs. Construtores de equipamentos e empresas de engenharia também começaram a desenvolver aplicações especiais para controles de elevação artificial de cabeça de poço com controladores microprocessados proprietários.
Eventualmente, praticamente todos os fabricantes de elevadores artificiais desenvolveram sua própria UTR para controlar e otimizar suas respectivas soluções. As empresas de engenharia também desenvolveram seus próprios métodos com aplicações RTU ligeiramente diferentes, enquanto os fabricantes de instrumentação introduziram novos instrumentos para medir praticamente qualquer ponto de processo necessário.
Recentemente, no entanto, os requisitos crescentes associados às operações de almofadas de vários poços começaram a exceder as capacidades da tecnologia RTU.
Dispositivos levados ao limite
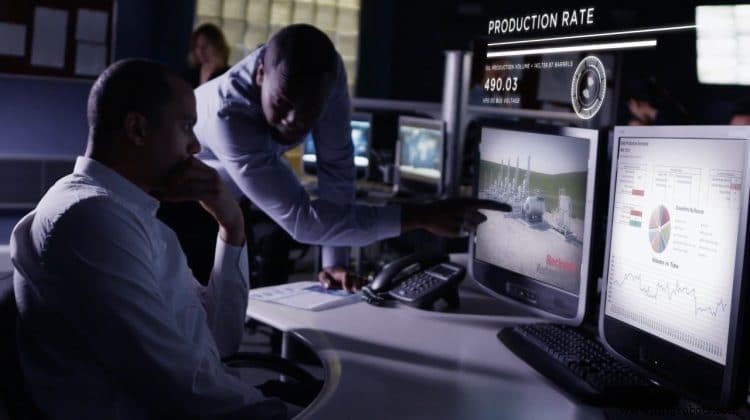
Cada poço em uma almofada de vários poços requer uma elevação artificial, medição de fluxo, controle de equipamento e medição de nível. Isso cria mais E/S e demanda de controle do que uma única RTU pode manipular. Como resultado, os produtores de petróleo e gás são forçados a comprar UTRs adicionais e distribuir o controle de aplicações e locais em várias unidades.
Os produtores de petróleo e gás implementaram com sucesso vários controladores de RTU em um poço, mas enfrentam alguns problemas comuns com essas arquiteturas. Alguns desses problemas incluem:
- Altere o gerenciamento de várias configurações ou programas em cada bloco de poço.
- Gerenciamento de comunicação das muitas UTRs no local (por exemplo, comunicações ponto a ponto).
- Comunicação SCADA para hardware de vários fornecedores.
- Execução não confiável de programas personalizados nas UTRs.
A demanda final em dispositivos RTU ocorre quando é necessário um controle de almofada de vários poços muito maior. Isso pode incluir uma operação com 10 ou mesmo várias dezenas de poços em um único bloco de poços. A maior densidade de poços em um bloco também aumenta o equipamento necessário no local. Por exemplo, muitas dessas almofadas de poços têm seu próprio separador.
Também se torna mais econômico instalar compressão de dutos, unidades de recuperação de vapor (VRUs) e torres VRU devido à alta taxa de gás natural produzida a partir do bloco. Unidades de transferência automática de custódia (LACT), transferência de água e máquinas de injeção de produtos químicos também são comumente vistas nesses poços.
Além disso, muitos produtores de petróleo e gás estão investindo em edifícios elétricos conhecidos como E-houses. Esses edifícios abrigam a distribuição de energia principal da concessionária, centros de controle de motores (MCC), interruptores de rede e fontes de alimentação ininterruptas (UPS) e geralmente são controlados ambientalmente.
Todos esses aumentos – em equipamentos, instrumentação de campo e aplicativos – apenas agravam os problemas comuns com arquiteturas RTU.
Eles também criam novos desafios de serviço e suporte. O uso de várias UTRs levou a várias configurações de aplicativos e programas para mantê-las. Também forçou os operadores de petróleo e gás a trabalhar com vários fornecedores.
Além disso, ter vários dispositivos de vários fornecedores também exige que os funcionários tenham mais treinamento e experiência para dar suporte a eles. Enquanto alguns produtores estão totalmente equipados com pessoal treinado o suficiente para lidar com a manutenção dos sistemas de controle de poços, muitos não estão. Esses produtores devem contar com o suporte do fabricante ou suporte de engenharia contratada para manter seus sistemas de controle.
Mudando para sistemas de controle modulares e escaláveis
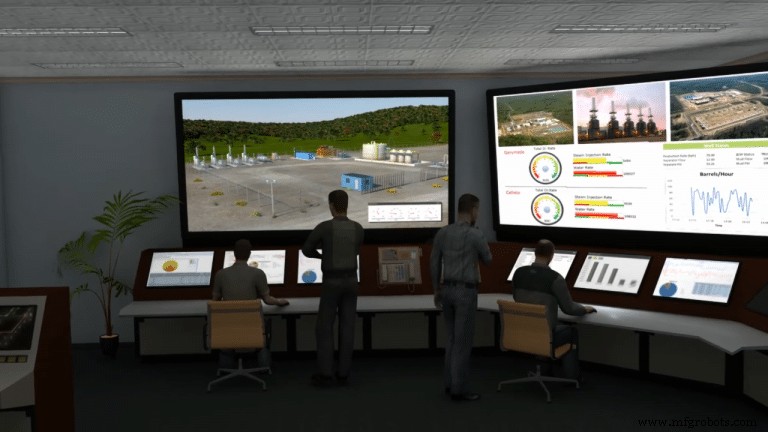
As RTUs cumprem seu papel há décadas no tratamento de requisitos de controle simples, interação simples entre dispositivos de campo e comunicações simples. Mas eles não são mais suficientes nos ambientes operacionais mais complexos de hoje.
Muitos produtores de petróleo e gás que enfrentaram problemas comuns de RTU encontraram uma solução alternativa viável na forma de um controlador lógico programável (PLC) modular e escalável. A tecnologia PLC vem sendo ajustada há anos em ambientes de controle de processos industriais que são tão robustos quanto a produção de petróleo e gás upstream.
Os PLCs oferecem vários benefícios em comparação com as RTUs:
- Modularidade: Algumas RTUs suportam hardware modular. Mas equilibrar os requisitos do módulo com os requisitos de aplicação e controle em uma RTU é muito mais difícil do que em um PLC. Além disso, módulos de terceiros para RTUs normalmente não estão disponíveis porque as RTUs não são arquiteturas abertas, enquanto os PLCs são.
Uma grande variedade de módulos está disponível para PLCs que permitem o monitoramento e controle de uma ampla variedade de instrumentos de campo. O suporte de comunicação para muitos tipos de rede diferentes também é suportado por meio de configuração modular. - Escalabilidade: Isso é importante ao considerar como uma almofada de vários poços é montada. Um único poço geralmente será instalado em um local com vários poços, e só meses ou mesmo anos depois que poços e equipamentos adicionais entrarão em operação.
Nestes casos, os fabricantes de equipamentos desejam ser capaz de construir skids de equipamentos fora do local e, em seguida, simplesmente conectá-los e configurá-los no poço. Eles querem reduzir a necessidade de abertura de valas, tração de fios, terminação de fios, instalação de painéis e instrumentos no campo para ajudar a reduzir custos. A escalabilidade na programação e no hardware é necessária neste caso, e é exatamente isso que a tecnologia PLC oferece. - Facilidade de programação: Historicamente, os PLCs eram vistos como uma tela em branco para automação e controle. Somente empresas de engenharia ou programadores experientes sabiam como começar do zero e desenvolver o controle necessário em um CLP.
No entanto, os CLPs modernos possuem bibliotecas de códigos pré-desenvolvidos e documentados que podem ser adicionados rapidamente em um moda de arrastar e soltar. Alguns fornecedores de PLC também possuem bibliotecas de petróleo e gás upstream pré-desenvolvidas que podem ser configuradas no local. Os produtores de petróleo e gás só precisam habilitar e configurar os dados necessários da HMI para iniciar um PLC ou adicionar hardware de skid em um sistema existente.
Isso pode eliminar a necessidade de alguém como um poço técnico com experiência especializada para conhecer o ambiente de programação e escrever novo código ao adicionar hardware.
Além disso, as alterações de programa e configuração podem ser feitas on-line em um CLP sem interromper o processo. As RTUs tradicionalmente não podem aceitar tais alterações sem serem colocadas offline e baixadas. Esse é um diferencial crítico em um ambiente moderno de vários poços porque desligar o sistema de controle resulta em perda de produção. - Funcionalidade de E/S remota: As RTUs tradicionalmente não têm funcionalidade de E/S remota nativa, mas os CLPs têm. Isso pode reduzir os custos de instalação. Além disso, quando os skids de equipamentos são adicionados a um local, eles podem vir com E/S e instrumentos pré-montados e com fio. A inicialização desses skids é tão simples quanto conectar um cabo Ethernet em um switch e configurar a E/S no controlador.
Melhorando o gerenciamento do ciclo de vida
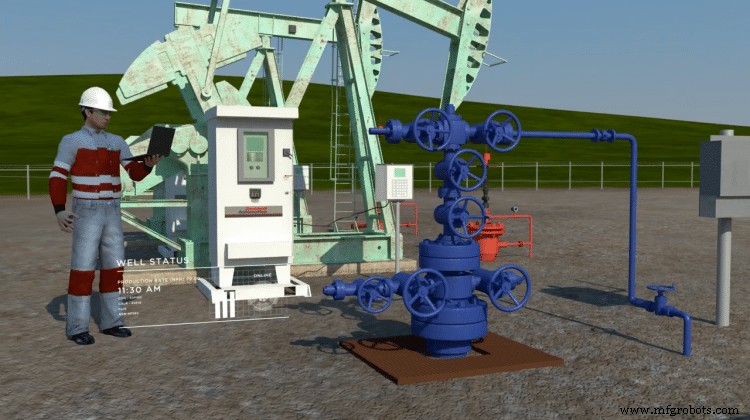
O gerenciamento do ciclo de vida do poço pode ser uma grande dor de cabeça para as equipes de operações. Os poços podem passar por muitos estados de fluxo diferentes, incluindo fluxo natural, bomba submersível eletrônica (ESP) ou bomba de cavidade progressiva (PCP) e bomba de haste de sucção. E o tipo de fluxo e o ciclo de vida podem variar também.
Múltiplas UTRs são frequentemente usadas apenas para controlar os vários ciclos de vida do poço. Alterar a UTR significa alterar os drivers de comunicação para o sistema SCADA porque a UTR física no poço é um hardware de um novo fornecedor. E configurar a RTU para controlar o aplicativo e configurar esse hardware no sistema geralmente é um processo meticuloso.
Um bloco de poço baseado em PLC pode proporcionar alívio significativo nesta área, proporcionando benefícios de eficiência e otimização que os operadores podem nunca imaginar serem possíveis.
Usando as arquiteturas de hardware de E/S modulares e escaláveis que um CLP oferece, os operadores podem instalar módulos de E/S exatamente onde a instrumentação está localizada e enviar esses dados para o CLP. E, independentemente da abordagem de projeto de E/S que um produtor de petróleo ou gás usa, o hardware no sistema de controle permanecerá constante, as comunicações com o sistema SCADA usarão os mesmos drivers e o sistema permanecerá on-line e no controle de todos os aplicativos, conforme atualizações são feitas. Durante todo o tempo, resta apenas um programa PLC para manter.
Há também a questão do suporte ao aplicativo do fornecedor. Como já mencionado, muitos fornecedores fazem seus próprios aplicativos para uma variedade de necessidades de produção upstream, e cada fornecedor normalmente usa um tipo diferente de RTU. Como resultado, os fornecedores geralmente podem oferecer suporte apenas a alguns aplicativos específicos, não a todos eles.
O suporte do fornecedor de PLC em projetos de almofadas de vários poços está crescendo diariamente. Isso inclui suporte para aplicações de controle de equipamentos, elevação artificial e medição de vazão. A automação de equipamentos é facilmente gerenciada por meio de ambientes de programação ricos e uma ampla variedade de módulos de E/S e comunicação. A medição de vazão também é compatível com a medição de vazão compatível com AGA e API, suporte para calibração e relatórios de transferência de custódia para sistemas SCADA. As aplicações de elevação artificial, embora não tão prevalentes em PLCs, também estão sendo desenvolvidas rapidamente para suportar todos os tipos de elevadores artificiais.
Por fim, muitos produtores de petróleo e gás expressaram frustração com os aplicativos de RTU sendo “caixa preta”. Isso significa que o sistema foi projetado com entradas específicas destinadas a controlar apenas saídas específicas.
Uma abordagem de caixa preta impede a flexibilidade, pois não permite que os produtores de petróleo e gás mudem a maneira como o sistema funciona. Como resultado, eles precisam mudar de fornecedor para atender às suas necessidades ou simplesmente viver com a tecnologia que possuem, sabendo que ela não está funcionando com a eficiência necessária.
Um sistema baseado em CLP, por outro lado, pode ser modificado em campo com ferramentas industriais comuns (IEC-61131), proporcionando uma flexibilidade muito maior.
Abraçando o novo normal
O PLC tem sido visto há muito tempo como uma solução mais adequada para instalações de fabricação do que para controle de poços. Mas os poços modernos de hoje são, em essência, pequenas fábricas. Eles têm edifícios com controle ambiental, energia elétrica ou geradora e requisitos de dados e controle muito maiores.
Isso os torna um ajuste ideal para um PLC. Um sistema de controle de almofadas de vários poços que utiliza os recursos modulares e escaláveis de um PLC pode reduzir custos e tempos de instalação, melhorar o tempo de atividade da produção e facilitar o gerenciamento do ciclo de vida.
Zack Munk é gerente de desenvolvimento de negócios de petróleo e gás upstream onshore da Rockwell Automation.
Sistema de controle de automação
- Construindo Sistemas de Manufatura Flexíveis para Indústria 4.0
- ASM Assembly Systems usa o robô Sawyer da Rethink Robotics para verificações de controle de qualidade
- Considerações para painéis de controle AFD
- Vantagens Tecnologias incorporadas para projeto modular
- Soluções simples para sistemas de automação antigos
- Empresas estabelecem prazos para sistemas inteligentes
- 10 principais fluxos de trabalho para fabricantes
- Sistemas locais x globais para controle de produção
- Vantagens de usar VIA em eletrodos
- Marposs anuncia sistema de controle modular BLÚ LT para máquinas-ferramenta