Diferença entre usinagem e retificação
Fabricar produtos de formas complicadas com bom acabamento superficial por fundição nem sempre é viável e econômico. Várias operações secundárias podem ser realizadas nos produtos fundidos para finalmente produzir o objeto desejado. Tais operações incluem união (como soldagem), remoção ou usinagem de material, tratamento térmico ou alteração de propriedade, coloração e revestimento, etc. Os processos de remoção de material basicamente removem o material da superfície da peça para fornecer a dimensão e a tolerância pretendidas. Um grande número desses processos existe para atender a necessidade de processamento de uma variedade de materiais de várias maneiras e para acabamento de suas superfícies em diferentes níveis. Entre eles, os processos de usinagem convencionais são antigos e ao mesmo tempo confiáveis; no entanto, vários processos de corte abrasivo e os chamados processos de usinagem não tradicional (NTM) também podem fornecer facilidade semelhante.
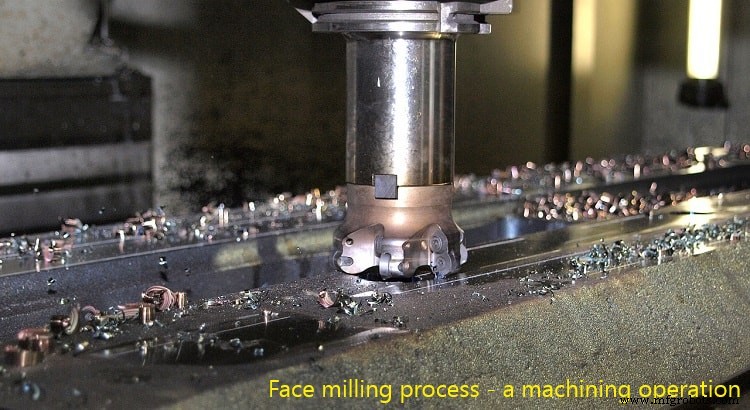
Por definição, usinagem ou corte de metal é um dos processos secundários de fabricação pelo qual o material camada por camada é gradualmente removido na forma de cavacos de uma peça bruta pré-formada para obter a forma, tamanho e acabamento desejados. Para atender a essa demanda, existem vários processos de usinagem como torneamento, rosqueamento, afunilamento, chanfro, fiação, rosqueamento, pescoço, filetagem, faceamento, canal, corte, serrilhado, furação, fresamento, modelagem, planejamento, rasgo, mandrilamento, fresagem, brochamento , etc. Tais processos podem fornecer maior taxa de remoção de material (MRR) e, portanto, são adequados, produtivos e econômicos para a remoção a granel de material de trabalho. Uma ferramenta de corte ou cortador duro e afiado é obrigatoriamente empregada para a remoção de material por cisalhamento. Esta ferramenta de corte também deve possuir especificação definida e material compatível para usinagem ininterrupta e eficiente. A maioria desses processos convencionais pode usinar uma grande variedade de materiais; no entanto, certos materiais de trabalho não fornecem usinabilidade aceitável e, portanto, outros processos de remoção de material (como corte abrasivo ou NTM) são recomendados nesses casos.
Moagem , um tipo de processo de corte abrasivo, pode atender a várias limitações da usinagem convencional. Aqui é utilizado um rebolo em vez da chamada ferramenta de corte. A roda é composta basicamente de partículas abrasivas de tamanho pequeno e mais duras, como alumina, sílica, diamante, etc., que são coladas em um meio adequado. Tais abrasivos têm forma arbitrária e, portanto, carecem de geometria definida; embora a própria roda tenha configuração específica. Embora o material seja removido na forma de chips, aqui os chips são micro-dimensionados. Este processo não é adequado para remoção em massa de materiais; em vez disso, é preferível para o acabamento da superfície em nível de mícron (0,5 – 2,0µm). Ele também pode aterrar com eficiência materiais duros e resistentes. Várias diferenças entre usinagem convencional e retificação são dadas abaixo em forma de tabela.
Tabela:Diferenças entre usinagem e retificação
Usinagem | Moagem |
---|---|
A usinagem é principalmente um processo de remoção em massa (alto MRR). Ela também pode semi-acabar as superfícies. | A esmerilhamento é principalmente um processo de acabamento de superfície. Ele fornece um MRR baixo. |
A precisão dimensional e a tolerância alcançadas por esses processos não são muito boas. Alcançar uma tolerância abaixo de 2µm é muito difícil. | A retificação oferece melhor precisão dimensional e tolerância estreita. Alcançar uma tolerância tão baixa quanto 0,5 µm é facilmente viável. |
Ele emprega uma ferramenta de corte (cortador) para remover o material. Essa ferramenta de corte geralmente é feita de metais; no entanto, também estão disponíveis cortadores de cerâmica, diamante e cBN. | Ele emprega um rebolo para remover o material. O rebolo é feito de pequenos abrasivos afiados (como alumina, sílica, etc.) ligados em outro meio (como resina, metal etc.). |
Cada cortador tem uma geometria específica. Isso significa que vários recursos, como ângulo em diferentes direções, orientação de diferentes planos, raio do nariz e várias arestas, etc. estão bem definidos. | Embora o rebolo tenha certas especificações, as partículas abrasivas têm características aleatórias. Assim, os ângulos, orientação, raio, etc. dos abrasivos não são definidos. |
O ângulo de inclinação de um cortador pode ser negativo ou positivo. Seu valor geralmente varia de +15° a –15°. | Os abrasivos têm ângulos de inclinação abruptos que podem variar de +60° a –60°, mesmo além disso. |
O ângulo de folga do cortador não pode ser zero ou negativo. Seu valor geralmente varia de +3° a +15°. | Os abrasivos também têm ângulos de folga abruptos. Também pode ser zero ou negativo. |
Toda e cada aresta de corte da fresa participa igualmente da ação de corte durante a usinagem. | Apenas poucos (abaixo de 1%) entre todos os abrasivos disponíveis na periferia do rebolo participam da ação de corte. |
O cisalhamento ocorre principalmente durante o processo. | A operação de esmerilhamento está associada a esfregar, arranhar, arar e também cisalhar. |
O consumo específico de energia (energia necessária por unidade MRR) é comparativamente baixo. | Devido à alta perda de energia devido a fricção, aração e arranhões, o consumo específico de energia é muito alto. |
Entre o calor de corte gerado, apenas uma pequena parte vai para dentro do material de trabalho (70 a 80% do calor é levado pelos cavacos em movimento). | Uma quantidade substancial de calor gerado entra no material de trabalho que causa danos térmicos graves na superfície acabada. |
Materiais endurecidos e materiais inerentemente muito frágeis e resistentes não podem ser usinados suavemente por esses processos. | Dureza, ductilidade e tenacidade do material de trabalho geralmente não apresentam problemas na retificação. |
Remoção em massa x processo de acabamento: A taxa de remoção de material (MRR) é definida como a taxa de volume de material de trabalho removido da superfície de trabalho durante qualquer processo de corte. A maioria dos processos de usinagem convencionais (exceto alguns como serrilhados) são usados para remover uma quantidade maior de material para dar uma forma e tamanho básicos. Ele fornece maior MRR e, portanto, mais produtivo. Ele também pode semi-acabar a superfície do produto no nível de 1 – 50µm com base na operação e nos parâmetros de processo correspondentes. A retificação, por outro lado, é empregada principalmente para o acabamento da superfície em um nível muito melhor. Uma rugosidade superficial na ordem de 0,5 – 2µm é facilmente viável com retificação. Assim, pode fornecer alta precisão dimensional e tolerância próxima.
Ferramenta de corte – seu material e geometria: Todo processo de usinagem convencional emprega obrigatoriamente uma ferramenta de corte (também chamada de fresa) com geometria e material específicos. Este cortador contém uma ou mais arestas de corte afiadas para cortar eficientemente o material da superfície de trabalho. O material desta fresa também é um fator importante para decidir o desempenho da usinagem. Mais importante, a dureza do material do cortador deve ser significativamente maior do que a do material de trabalho. A partir de aço rápido (HSS), metal duro e cerâmica, hoje em dia, nitrato cúbico de boro (cBN) e cortadores de diamante estão prontamente disponíveis. A retificação utiliza o rebolo em vez do cortador e os abrasivos no rebolo realmente removem o material. Ao contrário da fresa, tais abrasivos não possuem geometria definida (vários ângulos, raio de aresta, raio de ponta, comprimento de aresta de corte, etc. variam arbitrariamente); entretanto, materiais abrasivos podem ser fixados como alumina, sílica ou diamante.
Ângulo de ataque e ângulo de incidência: O ângulo de saída de uma ferramenta de corte indica a inclinação da superfície de saída do plano de referência. É um fator importante que influencia a deformação por cisalhamento, direção do fluxo do cavaco, espessura do cavaco, força de corte, tensão de cisalhamento, consumo de energia, etc. entre +15° e –15°. Os abrasivos do rebolo têm ângulo de saída abrupto e podem variar de +60° a –60°, às vezes até além deste limite. Esse alto ângulo de saída geralmente é indesejável porque causa desequilíbrio no corte e aumenta o consumo de energia de corte (alto positivo) ou falha da ferramenta (alto negativo). Ao contrário do ângulo de saída, o ângulo de incidência de uma fresa não pode ser negativo ou zero – deve ter um valor positivo. A qualidade e a tolerância da superfície acabada dependem deste ângulo. Para as fresas, o ângulo de incidência geralmente fica entre +3° a +15°; enquanto para abrasivos pode ser arbitrário (pode ser zero ou tão alto quanto +90°).
Cisalhamento e participação de arestas de corte: Um cortador pode consistir em uma ou mais arestas de corte e, portanto, pode ser cortador de ponto único ou cortador de vários pontos. Independentemente do número, cada uma das arestas de corte participa igualmente na ação de remoção de material. Além disso, na usinagem, o material é removido por cisalhamento de uma fina camada de material quando uma força de compressão suficiente é aplicada pelo cortador. No rebolo, apenas alguns abrasivos expostos (às vezes até abaixo de 1%) participam da ação de remoção de material. O resto dos abrasivos não tocam a superfície de trabalho (observe que a alimentação é muito baixa, mesmo abaixo de 10µm) ou causam arranhões, arados ou atrito em vez de cisalhamento. No entanto, o material é removido apenas por cisalhamento; outros apenas aumentam a força normal de forma indesejável.
Consumo de energia específico: A energia de corte necessária para remover o volume unitário do material é denominada energia específica, medida em J/mm 3 . Matematicamente a potência dividida pela MRR dá energia específica. A usinagem convencional fornece alta taxa de remoção de material (MRR) e, portanto, a energia específica é comparativamente baixa. Por outro lado, na moagem, o MRR é baixo e a maior parte da energia é desperdiçada devido a arranhar, arar ou esfregar em vez de cisalhar. Assim, a energia específica aumenta acentuadamente; mesmo pode ser 5 – 20 vezes maior.
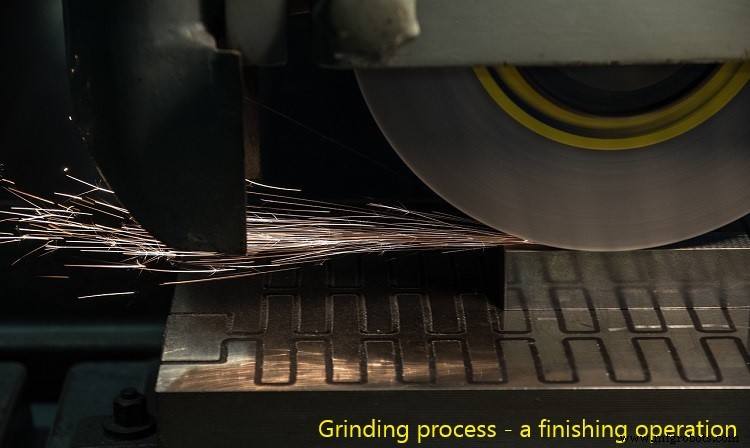
Dano de superfície por geração de calor: Na usinagem convencional, a maior parte do calor de corte é gerado na zona de deformação secundária, onde ocorre o atrito intenso entre o cavaco e a superfície de saída. A zona de cisalhamento primário também contribui até certo ponto. No entanto, a maior parte do calor gerado (70 – 80%) é levado pelos cavacos que fluem continuamente e apenas uma pequena porção vai para dentro da fresa ou da peça de trabalho. Assim, o dano térmico da peça de trabalho e da fresa é geralmente insignificante, especialmente quando o fluido de corte apropriado é aplicado. Na retificação, a geração de calor ocorre principalmente devido a arranhar, arar e esfregar. Tal calor se acumula dentro da peça de trabalho porque os abrasivos são isolantes térmicos e um volume muito pequeno de formas de microchips. A acumulação extrema de calor pode levar a vários danos térmicos na superfície acabada, incluindo queima da superfície, alterações nas propriedades mecânicas, imprecisão dimensional devido à expansão térmica, etc.
Usinagem de materiais duros e resistentes: Esses materiais apresentam muitos desafios quando processados por processos de usinagem convencionais, como alto desgaste da ferramenta, cavacos fragmentados, etc., que acabam levando a uma usinabilidade ruim. A retificação pode ser aplicada com vantagem independentemente da tenacidade e dureza do material de trabalho.
A comparação científica entre usinagem convencional e retificação é apresentada neste artigo. O autor também sugere que você consulte as seguintes referências para melhor compreensão do tema.
- Usinagem e máquinas-ferramentas por A. B. Chattopadhyay (1 st edição, Wiley).
- Engenharia e Tecnologia de Manufatura:Edição SI por S. Kalpakjian e S. R. Schmid (7 th edição, Pearson Ed Asia).
- Diferença entre Usinagem e Retificação por Difference.minaprem.com.
Tecnologia industrial
- Diferença entre Estrutura e União
- Diferença entre C e C++
- Diferença entre C e Java
- Python vs JavaScript:Diferença entre JavaScript e Python
- Diferença entre acionamento por corrente e acionamento por engrenagem
- Diferença entre acionamento por correia e acionamento por corrente
- Qual é a diferença entre a Indústria 4.0 e a Indústria 5.0?
- A diferença entre o processo de usinagem convencional e não convencional
- Diferença entre o processo de usinagem tradicional e não tradicional
- Diferença entre o compensado de madeira macia e o compensado de madeira dura