Limbo Artificial
Antecedentes
Braços e pernas artificiais, ou próteses, destinam-se a restaurar um certo grau de função normal aos amputados. Dispositivos mecânicos que permitem que os amputados voltem a andar ou continuem a usar as duas mãos provavelmente têm sido usados desde os tempos antigos, sendo o mais notável a simples perna de pau. O procedimento cirúrgico para amputação, entretanto, não teve muito sucesso até cerca de 600 a.C. Os armeiros da Idade Média criaram as primeiras próteses sofisticadas, usando ferro forte, pesado e inflexível para fazer membros que o amputado mal conseguia controlar. Mesmo com as articulações inventadas por Ambroise Paré nos anos 1500, o amputado não conseguia se flexionar à vontade. As mãos artificiais da época eram imitações muito bonitas e intrincadas de mãos reais, mas não eram excepcionalmente funcionais. Os membros superiores, desenvolvidos por Peter Baliff de Berlim em 1812 para amputados abaixo do cotovelo e Van Peetersen em 1844 para amputados acima do cotovelo, eram funcionais, mas ainda muito aquém do ideal.
O século XIX viu muitas mudanças, a maioria iniciadas pelos próprios amputados. J. E. Hanger, um estudante de engenharia, perdeu a perna na Guerra Civil. Posteriormente, ele projetou uma perna artificial para si mesmo e, em 1861, fundou uma empresa para fabricar pernas protéticas. A J. E. Hanger Company ainda existe hoje. Outro amputado chamado A. A. Winkley desenvolveu um dispositivo de encaixe abaixo do joelho para si mesmo e, com a ajuda de Lowell Jepson, fundou a Winkley Company em 1888. Eles comercializaram as pernas durante a Reunião dos Veteranos da Guerra Civil Nacional, estabelecendo assim sua empresa.
Outro amputado chamado D. W. Dorrance inventou um dispositivo terminal para ser usado no lugar da mão em 1909. Dorrance, que perdera o braço direito em um acidente, estava descontente com os braços protéticos disponíveis. Até sua invenção, eles consistiam em um soquete de couro e uma estrutura de aço pesada, e tinham uma mão pesada de cosmético em uma luva, uma mão mecânica rudimentar ou um gancho passivo incapaz de preensão. Dorrance inventou um gancho dividido que era ancorado no ombro oposto e podia ser aberto com uma tira nas costas e fechado por elásticos. Seu dispositivo terminal (o gancho) ainda é considerado um grande avanço para amputados porque restaurou suas habilidades de preensão até certo ponto. Ganchos modificados ainda são usados hoje, embora possam estar escondidos por uma pele de aparência realista.
O século XX testemunhou os maiores avanços nas próteses de membros. Materiais como os plásticos modernos produziram dispositivos protéticos que são fortes e mais leves do que os membros anteriores feitos de ferro e madeira. Novos plásticos, pigmentos melhores e procedimentos mais sofisticados são responsáveis por criar uma pele de aparência bastante realista.
O desenvolvimento mais emocionante do século XX foi o desenvolvimento de próteses mioelétricas de membros. A mioeletricidade envolve o uso de sinais elétricos dos músculos do braço do paciente para mover o membro. A pesquisa começou no final dos anos 1940 na Alemanha Ocidental e, no final dos anos 1960, dispositivos mioelétricos estavam disponíveis para adultos. Na última década, as crianças também receberam membros mioelétricos.
Nos últimos anos, computadores têm sido usados para ajudar a adaptar amputados a membros protéticos. Oitenta e cinco por cento das instalações protéticas privadas usam um CAD / CAM para projetar um modelo
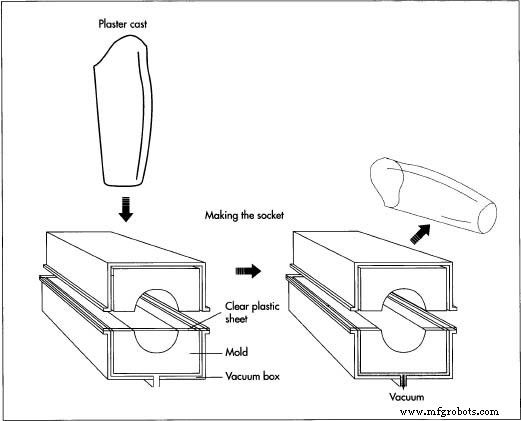
Matérias-primas
O dispositivo protético típico consiste em um encaixe personalizado, uma estrutura interna (também chamada de pilão), joelheiras e cintos que o prendem ao corpo, meias protéticas que amortecem a área de contato e, em alguns casos, aparência realista pele. A fabricação de próteses de membros está atualmente passando por mudanças em muitos níveis, alguns dos quais relacionados à escolha de materiais.
Um dispositivo protético deve, acima de tudo, ser leve; portanto, grande parte dele é feito de plástico. O soquete geralmente é feito de polipropileno. Metais leves como titânio e alumínio substituíram grande parte do aço no poste. Ligas desses materiais são usadas com mais freqüência. O mais novo desenvolvimento na fabricação de próteses tem sido o uso de fibra de carbono para formar um pilão leve.
Certas partes do membro (por exemplo, os pés) são tradicionalmente feitas de madeira (como bordo, tília, salgueiro, choupo e tília) e borracha. Ainda hoje os pés são feitos de espuma de uretano com uma construção de quilha interna de madeira. Outros materiais comumente usados são plásticos, como polietileno, polipropileno, acrílico e poliuretano. As meias protéticas são feitas de vários tecidos macios, porém fortes. As meias anteriores eram feitas de lã assim como alguns modernos, que também podem ser feitos de algodão ou vários materiais sintéticos.
A aparência física do membro protético é importante para o amputado. A maioria das próteses endoesqueléticas (pilões) é coberta por uma capa de espuma de poliuretano macia que foi projetada para se adequar ao formato do membro sadio do paciente. Essa capa de espuma é então coberta com uma meia ou pele artificial pintada para combinar com a cor da pele do paciente.
O processo de fabricação
Membros protéticos não são produzidos em massa para serem vendidos em lojas. Semelhante à forma como dentaduras ou óculos são adquiridos, membros protéticos são prescritos primeiro por um médico, geralmente após consulta com o amputado, um protesista e um fisioterapeuta. O paciente então visita o protesista para receber um membro. Embora algumas peças - o encaixe, por exemplo - sejam feitas sob encomenda, muitas peças (pés, pilões) são fabricadas em fábrica, enviadas ao protesista e montadas nas instalações do protesista de acordo com a necessidade do paciente. Em algumas instalações, os membros são feitos sob medida do início ao fim.
Medição e fundição
- 1 Precisão e atenção aos detalhes são importantes na confecção de membros protéticos, pois o objetivo é ter um membro que chegue o mais próximo possível de ser tão confortável e útil quanto um membro natural. Antes de iniciar o trabalho de fabricação do membro, o protesista avalia o amputado e faz uma impressão ou leitura digital do membro residual.
- 2 O protesista mede então o comprimento dos segmentos corporais relevantes e determina a localização dos ossos e tendões na parte restante do membro. Usando a impressão e as medidas, o protesista faz então um molde de gesso do coto. Geralmente é feito de gesso, porque seca rápido e produz uma impressão detalhada. A partir do molde de gesso, é criado um modelo positivo - uma duplicata exata - do coto.
Fazendo o soquete
- 3 Em seguida, uma folha de termoplástico transparente é aquecida em um grande forno e, em seguida, formada a vácuo em torno do molde positivo. Neste processo, a folha aquecida é simplesmente colocada sobre o topo do molde em uma câmara de vácuo. Se necessário, a folha é aquecida novamente. Então, o ar entre a folha e o molde é sugado para fora da câmara, dobrando a folha ao redor do molde e forçando-a na forma exata do molde. Esta folha termoplástica é agora o soquete de teste; é transparente para que o protesista possa verificar o ajuste.
- 4 Antes de fazer o encaixe permanente, o protesista trabalha com o paciente para garantir que o encaixe de teste se encaixa corretamente. No caso de falta de uma perna, o paciente caminha com o soquete de teste e o protesista estuda a marcha. O paciente também é solicitado a explicar como é o ajuste; o conforto está em primeiro lugar. O soquete de teste é então ajustado de acordo com a entrada do paciente e tentado novamente. Como o material do qual o soquete de teste é feito é termoplástico, ele pode ser reaquecido para fazer pequenos ajustes na forma. O paciente também pode ser equipado com meias mais grossas para um ajuste mais confortável.
- 5 O encaixe permanente é então formado. Como geralmente é feito de polipropileno, pode ser moldado a vácuo sobre um molde da mesma forma que o bocal de teste. É comum que o coto encolha após a cirurgia, estabilizando aproximadamente um ano depois. Assim, o encaixe é geralmente substituído nesse momento e, posteriormente, quando as alterações anatômicas exigirem uma alteração.
Confecção da prótese
- 6 Existem muitas maneiras de fabricar as partes de um membro protético. As peças de plástico - incluindo peças de espuma macia usadas como forros ou enchimento - são feitas nos métodos usuais de conformação de plástico. Isso inclui a formação a vácuo (veja o nº 3 acima), a moldagem por injeção - forçando o plástico derretido em um molde e deixando-o esfriar - e a extrusão, na qual o plástico é puxado através de uma matriz moldada. Pilares feitos de titânio ou alumínio podem ser fundidos sob pressão; neste processo, o metal líquido é forçado a formar uma matriz de aço com o formato adequado. As peças de madeira podem ser aplainadas, serradas e furadas. Os vários componentes são montados de várias maneiras, usando parafusos, adesivos e laminação, para citar alguns.
- 7 Todo o membro é montado pelo técnico do protesista usando ferramentas como uma chave de torque e uma chave de fenda para aparafusar o
Um membro artificial típico, neste caso uma prótese acima do joelho. A capa de espuma é coberta com pele artificial pontiaguda para combinar com a cor natural da pele do paciente. dispositivo protético juntos. Depois disso, o protesista encaixa novamente o encaixe permanente no paciente, desta vez com o membro feito sob medida anexado. Os ajustes finais são então feitos.
Fisioterapia
Uma vez que o membro protético foi colocado, é necessário que o paciente se sinta confortável com o dispositivo e aprenda a usá-lo para enfrentar os desafios do dia a dia. Ao mesmo tempo, eles devem aprender exercícios especiais que fortalecem os músculos usados para mover a prótese. Quando o paciente recebe um dispositivo mioelétrico, às vezes é verdade que os músculos estão muito fracos para sinalizar o dispositivo com eficácia, então, novamente, os músculos são exercitados para fortalecê-los. Alguns novos amputados são treinados para lavar os dispositivos - incluindo as meias - diariamente e praticar como colocá-los e tirá-los.
Um paciente equipado com um braço artificial deve aprender a usar o braço e seu dispositivo de travamento, bem como a mão. Se o amputado perder um braço devido a um acidente e posteriormente receber um dispositivo mioelétrico, isso é relativamente fácil. Se a perda do membro for congênita, isso é difícil. Um sistema de instrução foi desenvolvido para ensinar amputados como realizar muitas tarefas pequenas usando apenas uma mão.
Alguns pacientes com perna artificial também são submetidos a fisioterapia. Normalmente, um novo amputado leva de 18 a 20 semanas para aprender a andar novamente. Os pacientes também aprendem como entrar e sair da cama e como entrar e sair do carro. Eles aprendem como subir e descer ladeiras e como cair e se levantar com segurança.
Controle de qualidade
Não existem padrões para membros protéticos nos Estados Unidos. Alguns fabricantes defendem instituir aqueles da Organização de Padrões Internacionais da Europa, especialmente porque os exportadores dos EUA de membros protéticos para a Europa devem obedecer a eles de qualquer maneira. Outros acreditam que esses regulamentos são confusos e irrealistas; eles preferem que os Estados Unidos produzam seus próprios padrões mais razoáveis.
A falta de padrões não significa que os fabricantes de membros protéticos não encontraram maneiras de testar seus produtos. Alguns testes avaliam a resistência e a vida útil do dispositivo. Por exemplo, cargas estáticas testam a força. Uma carga é aplicada por um período de 30 segundos, mantida por 20 segundos e removida por um período de 30 segundos. O membro não deve sofrer deformação com o teste. Para testar a falha, uma carga é aplicada ao membro até que ele se quebre, determinando os limites de força. Cargas cíclicas determinam a vida útil do dispositivo. Uma carga é aplicada dois milhões de vezes com uma carga por segundo, simulando cinco anos de uso. Membros protéticos experimentais são geralmente considerados viáveis se sobreviverem a 250.000 ciclos.
O Futuro
Muitos especialistas estão otimistas sobre o futuro das próteses; pelo menos, a maioria concorda que há um vasto espaço para melhorias. Um membro protético é um dispositivo sofisticado, embora tenha um design preferencialmente simples. O dispositivo protético ideal deve ser fácil para o paciente aprender a usar, exigir pouco reparo ou substituição, ser confortável e fácil de colocar e tirar, ser forte, porém leve, ser facilmente ajustável, ter aparência natural e ser fácil de limpar . A pesquisa visa este dispositivo protético reconhecidamente utópico, e avanços foram feitos nos últimos anos.
A fibra de carbono é um material forte e leve que agora está sendo usado como base das partes endoesqueléticas (os postes). No passado, era usado principalmente para reforço de próteses exoesqueléticas, mas alguns especialistas afirmam que a fibra de carbono é um material superior que acabará por substituir os metais nos postes.
Um pesquisador desenvolveu um software que sobrepõe uma grade em uma tomografia computadorizada do coto para indicar a quantidade de pressão que o tecido mole pode suportar com o mínimo de dor. Ao visualizar o modelo do computador, o protesista pode projetar um encaixe que minimiza a quantidade de tecido mole que é deslocado.
Um pé sensível à pressão experimental também está em obras. Transdutores de pressão localizados nos pés enviam sinais aos eletrodos colocados no coto. Os nervos podem então receber e interpretar os sinais de acordo. Amputados podem andar mais normalmente com o novo dispositivo porque podem sentir o solo e ajustar sua marcha de forma adequada.
Outro desenvolvimento revolucionário na área de próteses de pernas é a introdução de uma prótese acima do joelho que possui um computador embutido que pode ser programado para se adequar à marcha do paciente, tornando assim o andar mais automático e natural.
Processo de manufatura
- Grama Artificial
- Coração Artificial
- Válvula cardíaca artificial
- Sangue Artificial
- Três aplicativos de impressão 3D para sorrir
- Bosch adiciona inteligência artificial à indústria 4.0
- Inteligência artificial é ficção ou moda passageira?
- Robôs de Inteligência Artificial
- Vantagens e desvantagens da inteligência artificial
- Big Data x Inteligência Artificial