Eficiência Energética e Produção de Ferro e Aço
Eficiência Energética e Produção de Ferro e Aço
Nos últimos anos, a necessidade de um uso mais racional e eficiente da energia emergiu como uma questão estratégica e urgente. Tal necessidade é particularmente percebida na produção de ferro e aço, não apenas pelo aumento dos custos de energia, mas também como consequência da concorrência, que enfatiza algumas características do processo e de seus produtos finais (por exemplo, custo e qualidade). Além disso, o uso racional do recurso energético pode ser considerado como uma questão dupla, sendo um primeiro aspecto relacionado à consciência alcançada da limitada disponibilidade de energia, considerada como fonte, e o segundo sendo representado por uma apreciação madura dos custos nascido para obter energia.
Globalmente, o consumo cada vez maior de energia anda de mãos dadas com as crescentes preocupações sobre sua conservação. Além de ser caro e propenso a flutuações repentinas de preços, a esmagadora maioria das fontes de energia não são renováveis. Portanto, a conservação de energia é considerada vital não apenas para evitar o desperdício de um recurso precioso, mas também para retardar o rápido esgotamento dos recursos de carvão, petróleo e gás natural. No entanto, com o movimento ambientalista ganhando terreno nos últimos 30 anos, as ramificações do uso insustentável de energia não estão mais confinadas apenas à economia. Como a maior parte das emissões de gases de efeito estufa (GEE) é resultado da queima de combustíveis fósseis, a conservação de energia está hoje intrinsecamente ligada à questão climática. Como interromper o uso de combustíveis fósseis não é uma opção sem a viabilidade de fontes alternativas, a única maneira de reduzir o uso de energia e gerenciar as emissões é, portanto, maximizar sua eficiência.
Como a indústria siderúrgica apresenta um dos setores mais intensivos em energia dentro da economia de qualquer país, é, portanto, de particular interesse no contexto das discussões ambientais locais e globais.
O perfil da eficiência energética aumentou recentemente, devido ao aumento das preocupações com os impactos ambientais locais e globais do uso de energia. Os desafios à segurança energética também trouxeram à tona a eficiência energética, pois contribuem diretamente para a redução do uso de energia.
A eficiência energética na produção de ferro e aço é fundamental para garantir a redução do custo de produção, a competitividade dos produtos siderúrgicos e minimizar os impactos ambientais, como as emissões de GEE. A maior parte da entrada de energia em uma usina siderúrgica integrada vem de combustível e eletricidade. A energia do combustível vem principalmente de combustível sólido (principalmente carvão) e apenas uma pequena entrada vem de combustíveis líquidos e gasosos. O combustível na produção de ferro e aço é usado para fornecer energia térmica. Também é usado como redutor para reduzir o minério de ferro para produzir ferro. A energia elétrica é utilizada para atender às necessidades do processo, acionando os motores e a iluminação das instalações.
A pessoa que primeiro deu forma à ideia de eficiência energética foi o físico americano e ativista ambiental Amory Lovins. Abalado pela crise do petróleo de 1973, Lovins postulou e popularizou o conceito de ‘negawatts’, um sistema de atendimento às necessidades energéticas não explorando maiores quantidades de energia, mas aumentando a eficiência das quantidades existentes. Em outras palavras, para usar uma expressão americana, “tirar o máximo de retorno do investimento”. Desde então, todos em todo o mundo estão trabalhando para ajustar a tecnologia existente ou criar soluções completamente novas que maximizem o valor derivado de cada unidade de energia. Esses esforços foram auxiliados pelo apoio de pessoas com autoridade, que criaram um ambiente propício para a motivação para o uso eficiente da energia.
A produção de ferro e aço é intensiva em energia. É o maior consumidor de energia entre todos os setores industriais. É também o maior emissor de emissões de CO2. Constitui uma parcela significativa do custo de produção do aço. O custo da energia como percentual do custo total está na faixa de 20% a 40% dependendo da rota de produção, tipo de minério de ferro e carvão utilizado, mix de produtos siderúrgicos, tecnologia de controle de operação e eficiência do material.
As fontes primárias de energia utilizadas na produção de ferro e aço incluem carvão coqueificável, carvão não coqueificável, óleos combustíveis líquidos e eletricidade. Onde quer que o gás natural esteja disponível, ele é usado na produção de ferro. Dos vários tipos de fontes primárias de energia, o carvão de coque detém a maior parte da energia utilizada (65% a 80%). Enquanto carvão coqueificável, carvão não coqueificável e óleos combustíveis líquidos são usados principalmente em usinas siderúrgicas integradas, a eletricidade é, de longe, o principal insumo para a fabricação de aço em mini usinas usando fornos elétricos a arco ou fornos de indução.
A intensidade energética é medida em termos físicos como consumo específico de energia por unidade de produção (SEC).
O consumo específico de energia (SEC) é definido como segue. A SEC é medida em GJ/ton de produto.
SEC =Energia usada / produto produzido =(Energia importada – Energia exportada) / produto produzido
Os processos industriais costumam usar energia de diferentes formas, como combustíveis, vapor e eletricidade, e a SEC desse tipo de processo é calculada da seguinte forma.
SEC =E (combustíveis) + E (vapor) + E (eletricidade) / produto produzido
Onde E (combustíveis) é o consumo de combustível, E (vapor) é o consumo de vapor e E (eletricidade) é o consumo de eletricidade do processo.
Na maioria dos casos, a SEC é comparada com a melhor prática para determinar a porcentagem de redução de energia por unidade de produção que pode ser alcançada pela adoção das melhores práticas. A SEC para a produção de ferro e aço reduziu consideravelmente nos últimos anos. Hoje a SEC nas usinas energeticamente eficientes do mundo usando a rota alto-forno – forno a oxigênio básico, varia de 17 GJ/ton de aço bruto a 23 GJ/ton de aço bruto. Em plantas não tão eficientes, está na faixa de 25 GJ/ton de aço bruto a 34 GJ/ton de aço bruto.
Essa variação da SEC é influenciada/depende da qualidade do minério de ferro e do carvão, do grau do aço e da eficiência do material. A rota do forno de lareira aberta é mais intensiva em energia e menos produtiva.
Atualmente, apenas uma capacidade muito pequena ainda está em uso devido à substituição dessa tecnologia pela tecnologia BOF. A rota de produção de aço utilizando forno elétrico a arco não requer uma planta de coque ou sinterização, mas a sucata de aço reciclada. A intensidade energética desta rota varia de 9,1 a 12,5 GJ por tonelada de aço bruto onde a entrada é apenas a sucata de aço.
Outra maneira de produzir aço bruto é reduzindo diretamente o minério de ferro para produzir ferro reduzido direto (DRI). A intensidade energética média é tipicamente entre 28,3 e 30,9 GJ por tonelada de aço bruto. Esta tecnologia utiliza principalmente gás natural ou carvão não coqueificável. Hoje em dia há um interesse considerável no mundo para produzir DRI usando gás de xisto nas áreas onde está disponível em abundância.
As emissões típicas de SEC e CO2 específicas de diferentes oficinas em siderúrgicas na Europa são fornecidas na Tabela 1.
Guia 1 SEC típica e emissões específicas de CO2 para a produção de ferro e aço na Europa | ||||
Unidades de usina siderúrgica | Energia primária | Energia direta | Emissões totais de CO2 | Emissões diretas de CO2 |
GJ/ton | GJ/ton | toneladas de CO2/ton | toneladas de CO2/ton | |
Fábrica de coque e subprodutos | 6.827 | 6.539 | 0,824 | 0,794 |
Planta de sinterização | 1.730 | 1.549 | 0,211 | 0,200 |
Fábrica de pellets | 1.204 | 0,901 | 0,075 | 0,057 |
Alto-forno | 12.989 | 12.309 | 1.279 | 1.219 |
Forno de oxigênio básico | -0,253 | -0,853 | 0,202 | 0,181 |
Forno a arco elétrico | 6.181 | 2.505 | 0,240 | 0,240 |
Flor, laje e moinho de tarugos | 2.501 | 1.783 | 0,125 | 0,088 |
Laminação de tiras a quente | 2.411 | 1.700 | 0,120 | 0,082 |
Moinho de chapas | 2.642 | 1.905 | 0,133 | 0,098 |
Fábrica de seção | 2.544 | 1,828 | 0,127 | 0,084 |
Linha de decapagem | 0,338 | 0,222 | 0,016 | 0,004 |
Laminação a frio | 1.727 | 0,743 | 0,075 | 0,008 |
Recozimento | 1.356 | 1,086 | 0,070 | 0,049 |
Linha de revestimento por imersão a quente | 2.108 | 1.491 | 0,104 | 0,059 |
Linha de revestimento eletrolítico | 4.469 | 2.619 | 0,208 | 0,046 |
Linha de revestimento orgânico | 1.594 | 0,758 | 0,074 | 0,003 |
Central de energia | 12.173 | 12.173 | 1.989 | 1,989 |
Fluxo de energia e utilização de gás de processo em usinas siderúrgicas integradas
A interdependência energética em uma siderúrgica integrada é bastante complexa. A Figura 1 ilustra um exemplo típico dos fluxos de entrada e saída de diferentes tipos de energia e agentes redutores, juntamente com o fluxo interno de energia de uma siderúrgica japonesa integrada.
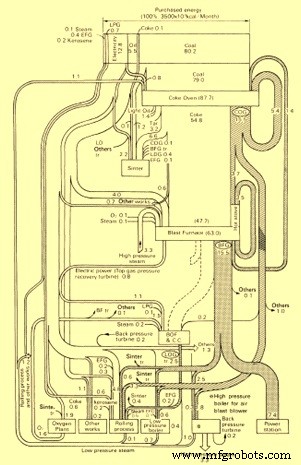
Fig 1 Exemplo de fluxo de energia típico em uma usina siderúrgica japonesa integrada
Os insumos dominantes usuais são carvão, óleo combustível e, se comprado de uma fonte externa, coque. Esses insumos são utilizados principalmente para a produção de coque na coqueria e como agentes redutores no alto-forno. É comum o uso de agentes redutores alternativos no alto-forno, como carvão, alcatrão ou óleo que são injetados no alto-forno no nível da ventaneira. Óleos usados, gorduras, vários gases (por exemplo, gás de coqueria) e outros hidrocarbonetos, como resíduos de plástico, também podem ser injetados.
A qualidade (valor calórico e limpeza) e o volume dos diferentes gases variam significativamente e esses fatores têm impacto sobre onde os combustíveis podem ser usados de forma útil. Para otimizar a eficiência energética, é necessário que cada gás combustível seja consumido na planta mais adequada. A gestão de energia desempenha um papel importante neste sentido. A principal tarefa do gerenciamento de energia é a distribuição e uso eficientes dos gases de processo e dos combustíveis adquiridos. Um bom layout da planta pode facilitar ainda mais essa tarefa.
O gás de coqueria (COG), o gás de alto-forno (gás BF) e o gás de forno de oxigênio básico (gás BOF) constituem a base do sistema de energia em uma siderúrgica integrada. A maior parte da demanda de energia é satisfeita por esses gases; a parte restante deve ser equilibrada com energia comprada, normalmente energia elétrica e outros combustíveis como óleo combustível.
Potenciais para melhorias de eficiência energética baseiam-se em grande parte nas mudanças em curso no setor de ferro e aço. Eles surgem da melhoria nos fatores de entrada, da conversão e modernização de tecnologia, bem como da reciclagem e recuperação de calor residual. O potencial na recuperação de calor residual, por exemplo, é imenso. Atualmente, mais de 50% da energia é perdida em muitas das siderúrgicas. Perdas ocorrem como gases de exaustão e subprodutos que não poderiam ser usados para geração de eletricidade ou produção de vapor de baixo calor.
Embora a maioria das medidas para melhoria da eficiência energética seja rentável e forneça benefícios líquidos dentro de um determinado período de tempo, apenas algumas medidas foram ou estão sendo implementadas atualmente em muitas das siderúrgicas. As barreiras à melhoria da eficiência energética são principalmente a disponibilidade de capital nessas siderúrgicas.
Melhoria na SEC
A melhoria na SEC é obtida através do seguinte.
- Ao melhorar a eficiência energética do processo
- Selecionando os materiais de entrada adequados do processo
- Reduzindo ou reduzindo as perdas de energia do processo
- Recuperando o calor residual do processo.
- Aprimorando o monitoramento do consumo de energia por meio do sistema de gerenciamento de energia.
As áreas de melhorias são identificadas através de auditorias energéticas adequadas. As auditorias podem ser feitas internamente ou por meio de agências externas qualificadas. As áreas de melhorias devem ser categorizadas em três categorias.
- Curto prazo – São aqueles itens de melhoria que podem ser implementados praticamente sem investimento ou com muito pouco investimento. Geralmente são melhorias de processo, monitoramento aprimorado, reciclagem de resíduos e melhorias nos insumos do processo, etc.
- Médio prazo – Essas melhorias precisam de adição/substituição de determinados equipamentos/instrumentos que possuem prazo de pagamento muito rápido.
- Longo prazo – Essas melhorias precisam de investimentos substanciais e podem envolver o descarte do equipamento/processo antigo.
Para implementar qualquer uma das melhorias acima, o suporte de gerenciamento é um ingrediente essencial. Sem o apoio da gestão, o programa de melhoria da eficiência energética pode ter sucesso.
Processo de manufatura
- O monitoramento das condições aumenta e mantém a eficiência na produção de papel
- Tendências de Fabricação:Robótica, Qualidade e Eficiência
- Inclusões em siderurgia e siderurgia secundária
- Avaliação do ciclo de vida e sustentabilidade do aço
- Ferro Reduzido Direto e seus Processos de Produção
- Produção de chapas de estanho e aço sem estanho
- Comportamento de materiais de ferro e aço durante o teste de tração
- Tendências do mercado de ferro e aço para conhecer
- Máquinas VMC para produção e eficiência
- Matérias-primas usadas na fabricação de ferro e aço