Não é mais a fundição do seu avô
As fundições continuam a evoluir adotando tecnologia inovadora e segurança no local de trabalho
Uma fundição é uma planta industrial onde o metal é derretido e moldado em formas específicas, despejando-o em um molde. O processo em si tem séculos. Hoje, aproximadamente 90% de todos os produtos manufaturados dependem de peças fundidas de metal para componentes, sendo carros e caminhões o maior mercado. Alumínio, ferro e aço são as ligas mais comuns processadas em fundições.

História das fundições
Por gerações, a humanidade encontrou maneiras inovadoras de utilizar matérias-primas encontradas na natureza – trabalhar com metais faz parte da civilização desde os tempos antigos. Uma grande variedade de artefatos foi descoberta por arqueólogos, de objetos de adoração a ferramentas e armas de guerra. De fato, as épocas da história humana foram nomeadas após os avanços na tecnologia do metal:Idade do Cobre, Idade do Bronze e Idade do Ferro. A mais antiga fundição conhecida encontrada pelos historiadores é um machado de cobre, que foi descoberto enterrado com uma múmia de aproximadamente 3300 a.C.
A fundição e o forno são originários da Mesopotâmia e regiões do Iraque e da Síria. Fundições de barro e fogueiras quentes trabalhavam para derreter e moldar cobre, ouro e prata. Essas fundições primitivas derreteram o cobre e foram capazes de criar formas mais complexas, mas não foi até que o estanho foi introduzido que o trabalho com metal fez um avanço significativo. A adição de estanho baixou a temperatura na qual os dois metais derreteram e formaram o bronze – a primeira liga.
Através de sucessivos séculos e gerações, várias técnicas de metalurgia e fundição foram desenvolvidas e perdidas, à medida que diferentes civilizações surgiram para dominar a paisagem cultural e tecnológica. É na Idade Média que os processos de fundição de metal em fundições foram documentados pela primeira vez. Vannoccio Biringuccio (1480-1539) é conhecido como o "pai da indústria de fundição", pois se tornou o autor do primeiro manual sobre fundições, a partir do qual a tecnologia foi desenvolvida.
A primeira fundição oficial era conhecida como “Canon Shop”, que foi construída em Moscou em 1479. A indústria de fundição de metal dos séculos 14 e 15 na Europa ficou conhecida pela produção de sinos de bronze e ferro, canhões e balas de canhão.
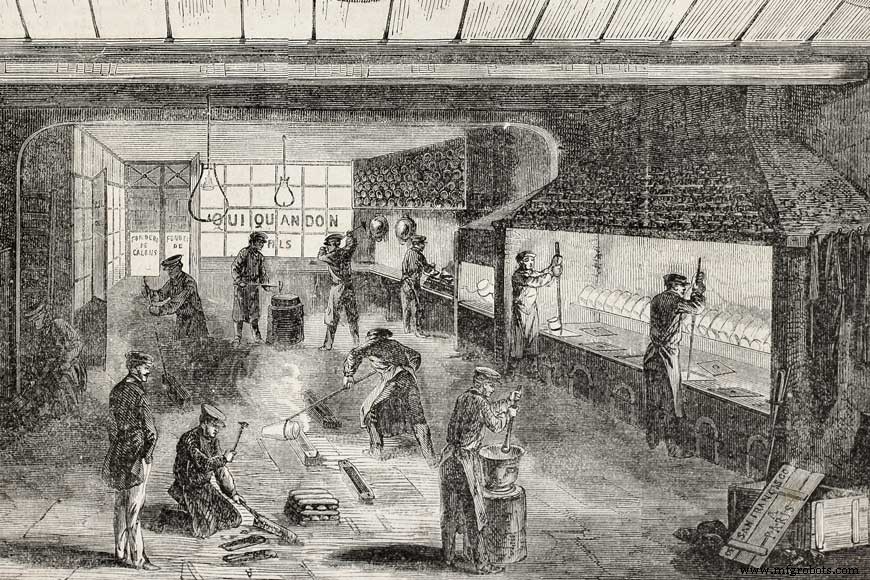
Na América do Norte, a indústria de fundição de metal cresceu em apoio ao progresso dos colonos em todo o Novo Mundo. Ferramentas mais avançadas e mais fortes, ferraduras e trilhos eram necessários para suprir a demanda das cidades e vilas em desenvolvimento.
A Saugus Iron Works foi a primeira fundição nos EUA e foi comissionada em 1642 por siderúrgicas europeias. Estabelecido em Lynn, Massachusetts, tornou-se conhecido como o berço da indústria americana de ferro e aço.
Desenvolvimentos na tecnologia de fundição
Os processos de fundição estão em constante desenvolvimento para melhorar a qualidade dos produtos e a eficiência da produção, além de aproveitar as novas tecnologias. Avanços no desenvolvimento permitiram avanços significativos na fundição de metais em momentos-chave da história da indústria.
Desenvolvimentos de fornos
A migração do carvão para o coque como combustível para fundições foi iniciada por Abraham Darby. Sua inovação em 1709 levou a uma melhoria significativa em eficiência e custo, e permitiu a construção de fornos muito maiores do que anteriormente.
Forno de cúpula
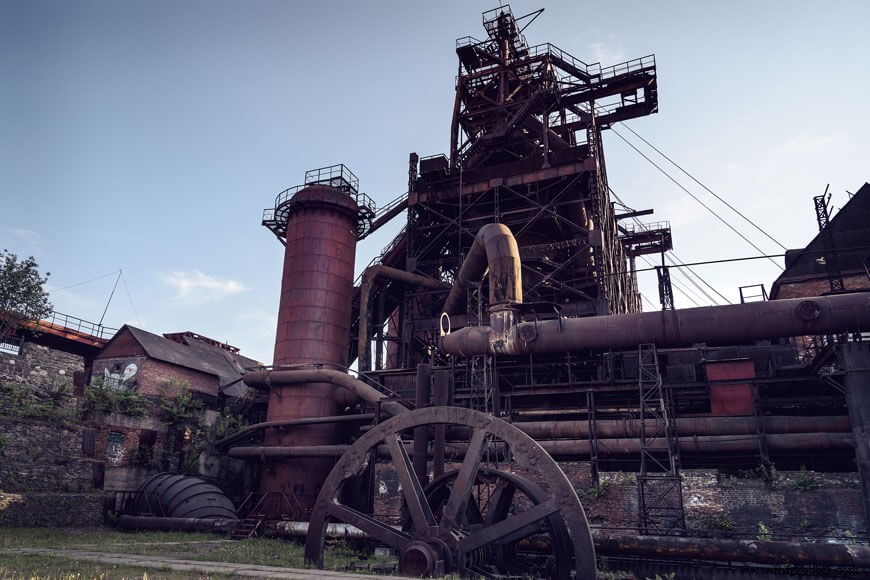
O forno Cupola foi desenvolvido em 1720 pelo francês René-Antoine Ferchault de Réaumur. A estrutura em forma de cúpula possui uma abertura para fornecer a carga e portas articuladas na base para esvaziar o forno após o desligamento. Um leito de coque suporta a carga de fluxo de metal fundido, coque e calcário acima das ventaneiras (aberturas onde o ar é fornecido). Embora o forno Cupola tenha dominado o cenário da fundição, agora foi amplamente substituído por fornos elétricos de indução e arco elétrico mais eficientes.
Processo do cadinho
Na Inglaterra do século 18, Benjamin Huntsman foi o empresário por trás do desenvolvimento do processo de cadinho. Este foi o primeiro processo em que o aço pode ser completamente fundido para produzir um produto uniforme após a fundição.
Forno a arco elétrico
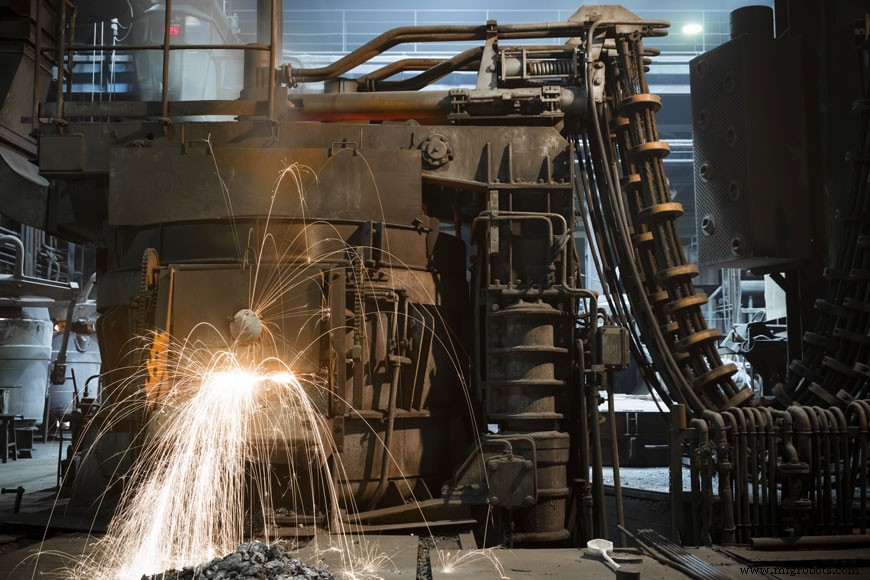
A introdução do fornecimento comercial de eletricidade contribuiu para a invenção dos fornos elétricos a arco. Os eletrodos de grafite criam o arco elétrico e fornecem corrente como fonte de energia para derreter o ferro. O primeiro forno elétrico a arco foi criado em 1900 por Paul Héroult da França. Em 1907, uma fábrica comercial foi estabelecida nos Estados Unidos. Esses fornos são mais econômicos com taxas de produção mais baixas e podem ser operados de forma intermitente, dando mais flexibilidade às fundições de metais.
Forno de indução elétrico
Os fornos elétricos de indução usam uma corrente alternada de alta potência que flui através de uma bobina para induzir correntes parasitas no metal, gerando calor, e são mais comumente encontrados em fundições de produção hoje.
Desenvolvimentos de elenco
Nos tempos antigos, a fundição de metal era feita em moldes de argila. Um dos grandes reis assírios, Senacheribb, afirma ter aperfeiçoado a técnica de fundição de bronze e cobre em moldes de barro. Com o passar do tempo, os desenvolvimentos tecnológicos transformaram o processo de fundição – de fundição em areia à tecnologia eletromagnética.
Fundição na areia
Vannochio Birringucio, o fundador do final do século XV e início do século XVI, escreveu um livro sobre todas as formas de fundição e trabalhos relacionados. O livro descreve o uso de fundição em areia, a próxima grande fase da tecnologia de fundição. Inicialmente areia seria misturada com argila como agente ligante para que o molde mantivesse sua forma durante a fundição, mas com o tempo novos tipos de areia e agentes ligantes foram desenvolvidos.
A areia verde é um dos materiais mais comuns em uso hoje. Historicamente, a areia verde consistia em areia de sílica, argila bentonítica, água e carvão marinho. No entanto, o carvão do mar não é mais comumente usado hoje e foi substituído por outros materiais. Embora a fundição em areia verde permaneça em uso comum, os processos “sem cozimento”, de endurecimento químico ou de endurecimento a frio estão se tornando predominantes nas fundições de hoje.
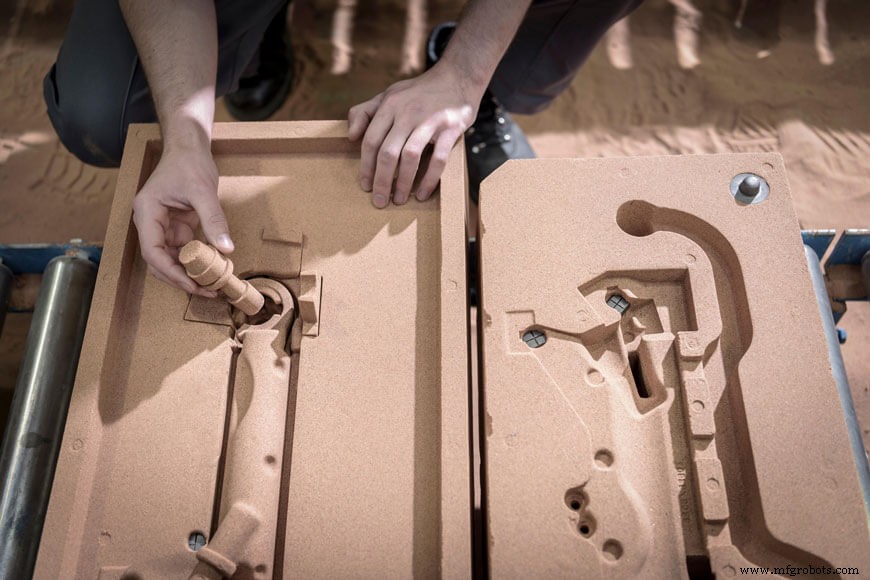
Fundição em molde
A fundição sob pressão e a moldagem por investimento são técnicas modernas que utilizam materiais recém-disponíveis para melhorar a qualidade do acabamento da fundição e o custo de produção. A fundição sob pressão é caracterizada por forçar o metal fundido sob alta pressão em uma cavidade do molde. Uma máquina de câmara quente ou fria é usada dependendo do tipo de metal que está sendo fundido. Os fundidos sob pressão são conhecidos por fornecer um bom acabamento superficial e consistência dimensional.
Lançamento contínuo
Talvez o avanço mais significativo no processo de lingotamento tenha sido a introdução da máquina de lingotamento contínuo. O metal fundido é derramado em um molde e retirado lentamente para criar comprimentos contínuos de metal solidificado. A principal vantagem deste método de fundição de aço carbono é a eliminação de algumas das etapas de processamento a jusante. Esses produtos semi-acabados podem ser mais facilmente transformados em produtos acabados por meio da laminação.
Moldes permanentes
No século 21, os processos de fundição deram outro salto com a introdução da tecnologia eletromagnética. Uma bobina de indução é enrolada em torno de um molde refrigerado a água com corrente alternada gerando campos eletromagnéticos.
Esses campos eletromagnéticos passam pelo metal de resfriamento causando a formação de correntes parasitas no metal fundido, resultando em dois resultados positivos:
- O contato entre o metal de resfriamento e a superfície do molde é “suave” proporcionando uma melhor qualidade de acabamento. Na fundição refrigerada a água padrão, uma pele grossa de microestrutura grosseira se forma devido ao contato “duro” com o molde. Essa película é fresada antes da laminação, resultando em desperdício significativo de produto e aumento de custos.
- A homogeneidade do metal é muito melhorada com uma redução nas segregações do contorno de grão.
Desenvolvimentos de qualidade
Sir Henry Bessemer foi o inovador por trás de novas técnicas para remover carbono e oxigênio em excesso do aço fundido que culminou na invenção do conversor. Bessemer descobriu que soprar oxigênio através do metal fundido causava uma reação com carbono e silício no material – removendo impurezas, mas também aquecendo o material para facilitar o vazamento.
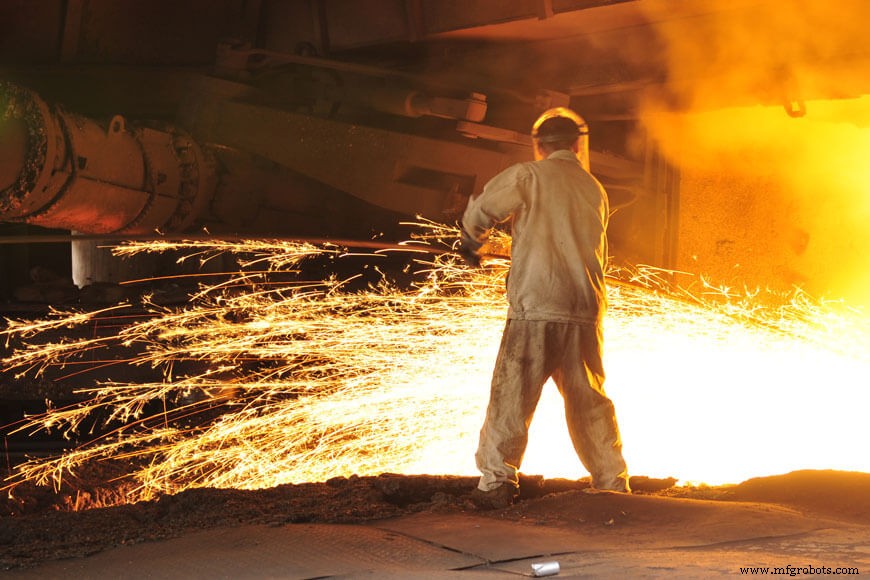
Os conversores agora são usados para graus finos de controle de qualidade, definindo proporções precisas de teor de carbono e adicionando ligas e outros aditivos para as propriedades específicas do produto exigidas. Em um forno elétrico a arco, o oxigênio pode ser injetado no banho para “queimar” o carbono e muitos outros elementos e impurezas. Isso torna o banho inicial o mais limpo possível e permite que a fundição ligue o fundido até o conteúdo perfeito. Na fusão por indução, a fundição só pode começar com um banho que é criado a partir da alimentação ou sucata fundida - o conteúdo químico da sucata deve corresponder à química do banho que a fundição usa inicialmente.
Desenvolvimentos de medição e controle
Juntamente com os avanços nos métodos de produção, houve progresso nos métodos de teste de laboratório de metal fundido enquanto a fabricação ainda está em processo. As amostras podem ser retiradas de conversores e analisadas usando espectrômetros ou análise de fluorescência de raios-x. Esse feedback em tempo real da composição química cria uma oportunidade para os fabricantes fazerem ajustes antes do vazamento, economizando tempo e recursos valiosos devido ao retrabalho.
Embora um operador experiente possa detectar defeitos de superfície e possíveis falhas no produto fundido a olho nu, a melhoria nos métodos de teste não destrutivos deu aos clientes mais segurança na integridade do produto:
- Pó penetrante e fluorescente de corante pode ser suspenso em óleo penetrante e aplicado na superfície do fundido acabado. Rachaduras e falhas na superfície são imediatamente visíveis na aplicação do revelador ou na presença de luz ultravioleta.
- A inspeção radiográfica é o método mais eficaz para identificar furos internos, rachaduras ou inclusões. O molde é exposto à radiação de um tubo de raios X e a imagem criada no filme radiográfico indica mudanças na densidade do molde. A vantagem deste método é que o raio-x serve como um registro permanente, que pode acompanhar o produto ao longo de seu ciclo de vida para controle de qualidade e segurança.
- A Inspeção de Corante Líquido (LPI) pode encontrar pequenas rachaduras, poros ou outras imperfeições superficiais em fundidos ferrosos e não ferrosos que são difíceis de ver a olho nu. O LPI usa uma solução de óleo corante colorido na superfície da peça fundida que chega aos defeitos da superfície. Depois que um revelador especial é aplicado, os defeitos se tornam claramente visíveis.
- A inspeção de partículas magnéticas (MPI) ajuda a identificar a localização das descontinuidades da superfície em metais ferrosos. Também pode indicar defeitos subsuperficiais se a força de magnetização for suficiente para produzir um campo de vazamento na superfície. Neste teste, um fluxo magnético é induzido em material ferromagnético. Qualquer descontinuidade abrupta em seu caminho resulta em um campo de vazamento de fluxo local. Se partículas finamente divididas de material ferromagnético são trazidas para a vizinhança, elas oferecem um caminho de baixa relutância para o campo de vazamento e assumem uma posição que delineia aproximadamente seus limites efetivos. O fundido a ser inspecionado é magnetizado e sua superfície polvilhada com o pó magnético. Um fluxo de ar de baixa velocidade sopra o excesso de pó, deixando o defeito a ser delineado pelas partículas de pó restantes. O pó pode ser aplicado enquanto a corrente de magnetização está fluindo (método contínuo) ou após a corrente estar desligada (método residual). Pode ser aplicado seco ou suspenso, em um destilado leve de petróleo semelhante ao querosene.
Inspeção de partículas magnéticas
A inspeção de partículas magnéticas (MPI) é um tipo de teste não destrutivo que usa fluxo magnético para determinar quaisquer defeitos de superfície. Observe como um trabalhador realiza testes não destrutivos em uma soldagem de petróleo e gás.
- Testes ultrassônicos (UT) identificam defeitos internos através do som, empregando energia acústica de alta frequência que é transmitida em uma peça fundida. O UT permite a investigação da área da seção transversal de uma peça fundida e, portanto, é considerado um método de inspeção volumétrica. A energia acústica de alta frequência viaja através do fundido até atingir a superfície, interface ou defeito oposta. A interface ou defeito reflete partes da energia que são coletadas em uma unidade receptora e exibidas para o analista visualizar. O padrão de deflexão de energia pode indicar a localização e o tamanho de um defeito interno, bem como a espessura da parede e a contagem de nódulos de ferro dúctil. A UT requer conhecimento e experiência para uma interpretação precisa dos resultados, aumentando o custo da inspeção.
Desenvolvimentos de segurança
Trabalhar em uma fundição é uma ocupação perigosa. Existem inúmeros riscos químicos, mecânicos e de temperatura que devem ser controlados para eliminar possíveis danos aos trabalhadores.
Uma das áreas-chave que melhorou a segurança dos trabalhadores é a mecanização da indústria.
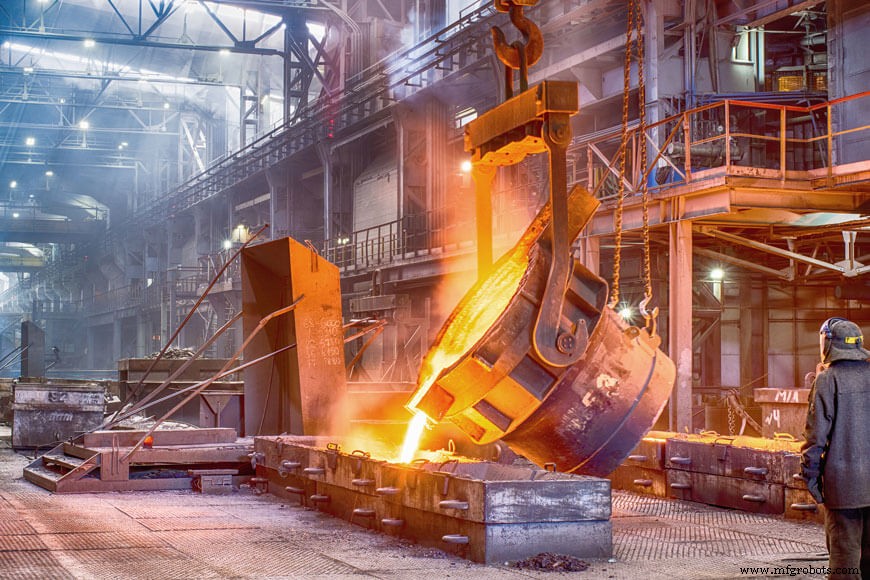
Anteriormente, as conchas eram manuseadas, recolhidas e movidas pelo local da fundição. Em seguida, foram introduzidas panelas com engrenagens, o que permitiu que um operador operasse e controlasse a panela à distância, em vez de ficar ao lado do recipiente de metal fundido. Guindastes foram introduzidos para levantar panelas em posição para vazamento, mas o ruído do ambiente de produção e as restrições de linha de visão ainda significavam que os operadores de guindastes eram vulneráveis a causar incidentes. Os guindastes de processo são o desenvolvimento mais recente em que as panelas funcionam em trilhos predefinidos com elevadores, eliminando a chance de um operador estar no caminho da panela móvel em condições normais de operação.
O futuro das fundições
Tendências tecnológicas futuras
A eficiência é a motivação predominante que impulsiona os avanços tecnológicos nas fundições. Há um forte foco na redução do consumo de energia devido à ênfase na fabricação sustentável, bem como na redução de custos associada. Uma força de trabalho menor nas fundições também reduzirá o potencial de lesões e otimizará a produção.
Melhorias na automação e um movimento em direção a simulações de computador - como software de simulação de solidificação - reduzirão a dependência da indústria de fundição em mão de obra e melhorarão a precisão e a eficiência. A simulação de processo auxiliada por computador oferece modelos de processo que agora estão suficientemente maduros. Isso permite que os engenheiros de fundição usem o mundo virtual em preparação para o mundo real, minimizando assim o número de iterações de teste.
A máquina de medição por coordenadas (CMM) está trazendo um novo nível de medição de precisão para o chão de fábrica na indústria de usinagem. A inspeção de furos, ranhuras, peças soldadas e deformações pode ser feita rapidamente, reduzindo significativamente o tempo de ciclo. Os dados digitalizados são então combinados com resultados táteis em relatórios gráficos para facilitar a interpretação. O CMM é uma força motriz para aumentar a produtividade e fornecer uma visão prática.
Tendências futuras do mercado
O mercado de fundição foi dominado na última década pela consolidação em grandes conglomerados. As economias de escala são um fator-chave para essa tendência e provavelmente continuarão no futuro próximo. Operações menores e menos eficientes continuarão paralisadas devido à competitividade do mercado.
Tendências ambientais e de segurança futuras
A reciclagem de metais é uma das histórias de sucesso do desenvolvimento sustentável, mas permanece a necessidade de desenvolver o uso sustentável de outros produtos envolvidos no processo de fundição de metais. Novas maneiras de usar escórias e areias de moldes usadas continuarão a ser identificadas e exploradas para acompanhar os constantes avanços regulatórios contra o descarte de resíduos.
Os rápidos avanços na tecnologia robótica abriram portas de oportunidade para reduzir a exposição dos seres humanos a situações perigosas. Inovadores em tecnologia robótica para ambientes industriais estão desenvolvendo células de trabalho robóticas que são completamente automatizadas e não requerem intervenção humana no local de trabalho.
Fundições e sua evolução contínua
A fundição de metal faz parte da sociedade humana desde os tempos antigos e está crescendo em uso e avanços a cada dia.
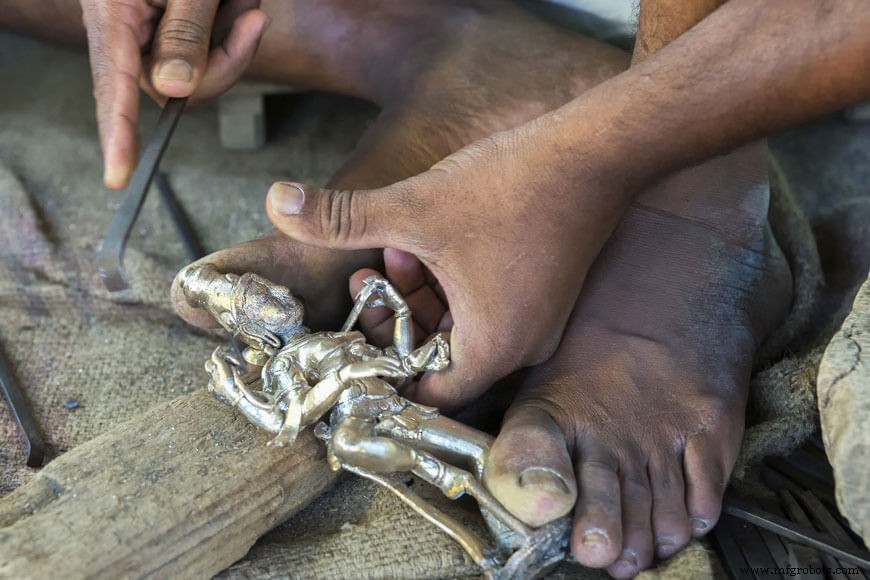
Hoje, os produtos de metal fundido afetam nossas vidas de várias maneiras. Peças de automóveis, utensílios de cozinha, ferramentas e muitos outros produtos de uso diário são todos resultados dos processos de fabricação das fundições.
Ao longo dos séculos, a tecnologia fez avanços dramáticos para melhorar a consistência e o controle de qualidade dos produtos de metal fundido, melhorando a segurança ocupacional dos trabalhadores e reduzindo os custos por meio de maior eficiência. Um estudo da história das fundições revela excelentes empreendedores, engenheiros, inovadores e solucionadores de problemas que desempenharam um papel no desenvolvimento dessa indústria.
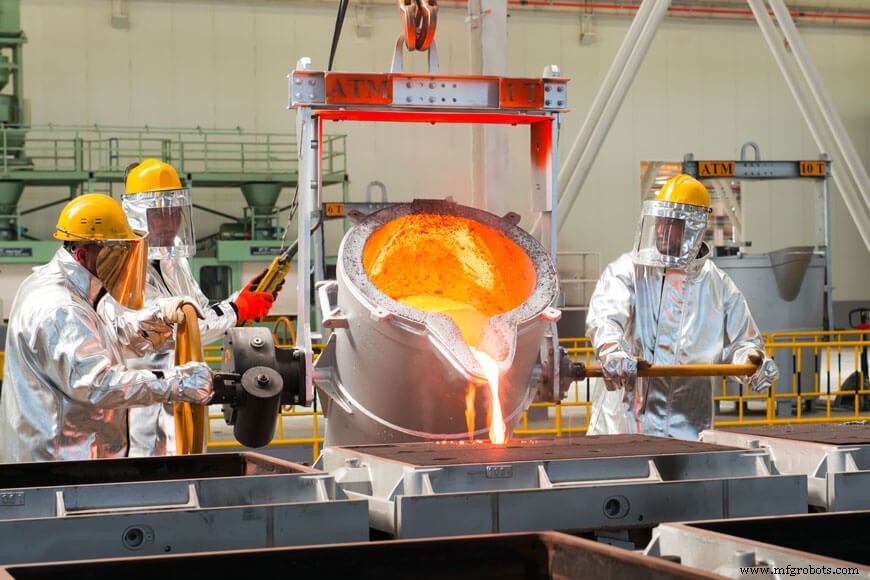
As pressões econômicas do mercado global continuam a criar um ambiente que recompensa inovação, consistência e eficiência. As próximas décadas deverão produzir novas tecnologias empolgantes, como o uso de big data e robótica, e novos modelos de negócios por meio de fusões e atualizações. As tendências globais em direção à fabricação sustentável continuarão a impulsionar melhorias ambientais e de segurança no setor, o que beneficiará trabalhadores e comunidades.
Referências
- Fundição de metal industrial. “História da Fundição de Metal”
- O Dicionário Livre. “Indústria de Fundição”
- Fundição Waupaca. “Histórico de Fundição de Metal”
- Serviço Nacional de Parques dos EUA. “Sítio Histórico Nacional Saugus Iron Works”
- Enciclopédia Britânica. “Forno de Cúpula”
- Fundação Americana para Estudos Siríacos. “O contexto da invenção no mundo antigo”
- O Instituto de Ferro e Aço do Japão. “Tecnologia siderúrgica nos últimos 100 anos”
- Sociedade Americana de Fundição. “Fundição em nosso mundo”
- Tecnologias de Metal. “História das fundições de metal”
- AMAG. “A tecnologia EMC aumenta a qualidade e a eficiência de custos”
- T.P. Fundições. "Indústria de Fundição:Breve História e Definição"
Processo de manufatura
- Guilhotina
- Silício
- Dobradiças para seus gabinetes de chapa metálica
- 5 maneiras de melhorar suas peças de chapa metálica
- 5 maneiras de tornar suas peças de metal resistentes à corrosão
- Seu guia para cisalhamento do processo de fabricação de metal
- 5 perguntas importantes para fazer ao seu fornecedor de metal
- Como evitar a corrosão em seu equipamento de metal
- Como usar sua máquina de perfuração para perfurar metal
- O que é uma Fundição?