Como calcular a eficiência da máquina?
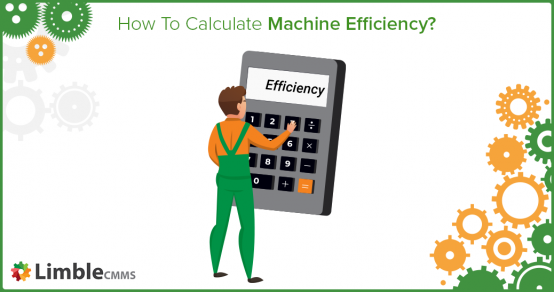
A eficiência da máquina é um aspecto crítico da fabricação moderna. Ele reduz os custos operacionais, melhora o rendimento e reduz os impactos ambientais.
Máquinas ineficientes levam a um baixo ROI - algo que qualquer empresa deve tentar evitar ativamente. Se você é um gerente de manutenção ou de fábrica, não precisamos dizer o quanto os equipamentos de fabricação podem ser caros e por que a eficiência não pode ser apenas uma nota de rodapé em seu trabalho diário.
Abaixo estão várias abordagens que você pode usar para medir e calcular a eficiência da máquina.
O conceito básico de eficiência
Na manufatura, a eficiência é a capacidade de produzir algo sem perder tempo, materiais ou energia.
Na realidade, 100% de eficiência é inatingível - sempre haverá algum tipo de desperdício. No entanto, ainda é o ideal que os fabricantes procuram se aproximar, por meio de princípios como manufatura enxuta, “just-in-time” e melhoria contínua (Kaizen).
A física é um ótimo ponto de partida para entender o conceito de eficiência. Ele define a fórmula básica para eficiência que se parece com isto:
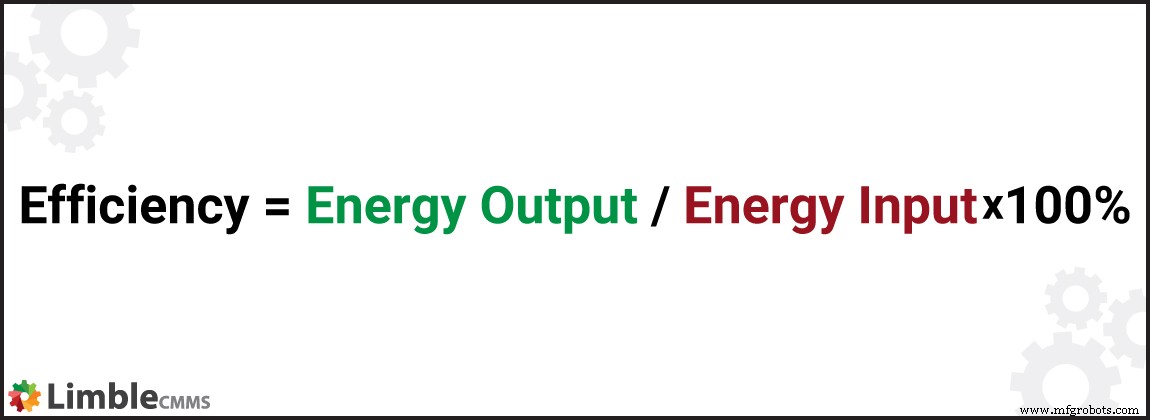
Quando você divide a saída de um processo com as entradas e expressa o resultado como uma porcentagem, obtém a classificação de eficiência desse processo específico.
A eficiência tem um teto máximo de 100% - ela não pode exceder esse limite. Qualquer processo, de fabricação ou não, com índice de eficiência de 100%, pode ser considerado um processo perfeito.
Maneiras de calcular a eficiência da máquina
Existem inúmeras entradas em um processo de fabricação. Usando a fórmula básica, você pode examinar a eficiência de uma máquina de diferentes ângulos, dependendo da entrada em consideração. Isso nos dá várias maneiras diferentes de medir a eficiência da máquina.
As três abordagens que vale a pena observar são:
- Produção de energia
- Consumo de energia
- Produtividade
Produção de energia
O termo produção de energia é um equívoco, pois a energia não pode ser produzida nem destruída - de acordo com a Lei de Conservação de Energia. Aqui, a produção de energia se refere à conversão da energia disponível em uma forma de energia mais “utilizável”.
Um ótimo exemplo seria um painel solar convertendo energia luminosa em energia elétrica, ou um gerador que converte energia mecânica / química em energia elétrica.
A fórmula para calcular a eficiência de produção de energia teria o mesmo formato que a fórmula de eficiência básica:
Eficiência =energia utilizável / energia disponível x 100
Veja o exemplo de um gerador a diesel. Se um galão de diesel tem 40.000 kWh de energia e o gerador o converte em 10.000 kWh de eletricidade, a eficiência pode ser calculada como:
Eficiência =(10.000 / 40.000) x 100 =25%
Consumo de energia
Dado o alto custo dos insumos energéticos e o impacto dos combustíveis fósseis no meio ambiente, a eficiência no consumo de energia adquiriu maior importância nas últimas décadas. De acordo com os estudos do Departamento de Energia dos Estados Unidos, os custos de energia (eletricidade) representam 96% do custo total do ciclo de vida de um motor.
E, na manufatura, as máquinas com motores respondem por quase metade do consumo de energia elétrica. Portanto, quaisquer mudanças na eficiência do consumo de energia industrial terão um impacto enorme nas redes de energia e no meio ambiente em geral.
Podemos usar a mesma fórmula básica de eficiência que usamos até agora.
Considere o exemplo de uma ferramenta elétrica que consome 500 kWh de eletricidade e produz energia cinética da ordem de 320 kWh. Sua eficiência pode ser calculada como:
Eficiência =(320/500) x 100 =64%
Eficiência de produção (produtividade vs eficiência)
Há uma diferença significativa entre “produtividade” e “eficiência” na manufatura. A produtividade se concentra no aumento da quantidade de bens produzidos. Muitas vezes, isso pode custar a eficiência.
Um aumento na porcentagem de unidades defeituosas é um exemplo comum. As empresas que aumentam a produção além do limite ideal muitas vezes enfrentam esse problema, devido a fatores como materiais de baixa qualidade, fadiga do operador, etc. Enquanto o número real de unidades criadas aumentou, a eficiência caiu .
Em contraste, a eficiência da produção se concentra menos na quantidade e mais na qualidade. Quer produzir mais unidades reduzindo o número de defeitos e desperdícios. Quando executado corretamente, melhorar a eficiência de fabricação aumentará a produtividade.
Uma maneira simples de calcular a eficiência da produção seria considerar a taxa de produção real versus a taxa de produção padrão / máxima possível na máquina.
Considere o exemplo de uma máquina de impressão que entrega uma produção real de 650 unidades por hora, em oposição a uma taxa máxima de 900 unidades por hora. Usando a fórmula de eficiência, obtemos os seguintes resultados:
Eficiência =(650/900) x 100 =72,22%
OEE:o padrão ouro em eficiência de fabricação
OEE significa eficácia geral do equipamento. É uma métrica padrão da indústria e um indicador-chave de desempenho (KPI) amplamente aceito, aplicável em uma ampla gama de indústrias.
Essa métrica é popular devido ao seu foco abrangente. Ele analisa três aspectos principais do equipamento na linha de produção:
- Disponibilidade
- Desempenho
- Qualidade
Calculando a disponibilidade
Todos os ativos têm um horário de trabalho programado de X horas por semana / mês. Disponibilidade exibe o tempo de trabalho real de uma máquina como uma porcentagem do tempo de trabalho programado.
A fórmula para calcular a disponibilidade é:
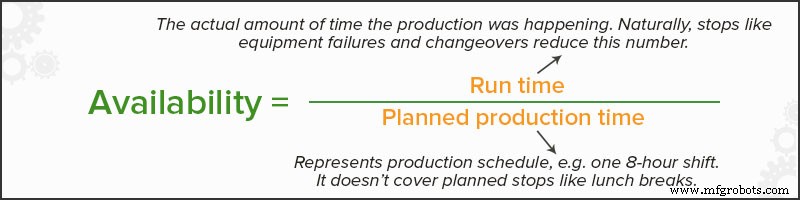
A disponibilidade raramente chega a 100%, pois o tempo de inatividade pode ocorrer devido a uma ampla gama de fatores. Falha de equipamento, ajustes, reparos, manutenção não planejada e outros fatores contribuem para a disponibilidade reduzida.
Calculando o desempenho
O desempenho representa o número real de unidades produzidas por uma máquina, como uma porcentagem do número máximo de unidades que ela poderia ter produzido na velocidade máxima, durante o tempo real de trabalho no chão.
A fórmula básica para desempenho é:

O desempenho pode ser afetado por pequenas paradas durante o processo de produção. Os defeitos da máquina e os operadores não treinados podem diminuir a velocidade de produção, levando a um desempenho inferior.
Calculando a qualidade
A qualidade mostra a porcentagem de produtos “bons” versus produtos defeituosos em qualquer lote. Produtos defeituosos levam ao desperdício, pois devem ser descartados ou retrabalhados.
A fórmula para calcular a qualidade é bastante simples:
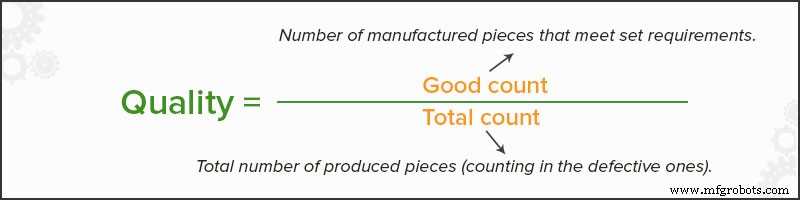
A qualidade pode ser afetada por muitos fatores, diretos e indiretos. Defeitos no processo de produção podem resultar em qualidade inferior ou produtos defeituosos. Erros do operador, matérias-primas de baixa qualidade e falhas da máquina também podem diminuir o percentual de qualidade na produção.
Como calcular OEE
Uma vez que você tenha as métricas de Disponibilidade (A), Desempenho (P) e Qualidade (Q) para uma instalação de máquina / planta, calcular OEE é um processo relativamente simples.
A fórmula básica para OEE é:
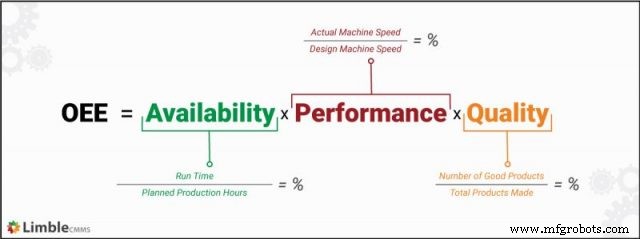
Uma pontuação OEE de 100% é considerada como "produção perfeita". Possui três características principais:
- A máquina não está produzindo peças com defeito
- A máquina está produzindo peças sem parar (durante o tempo de execução programado)
- A máquina está funcionando em velocidade máxima
Apenas para contextualizar, as instalações de produção médias têm a pontuação OEE em torno de 60%.
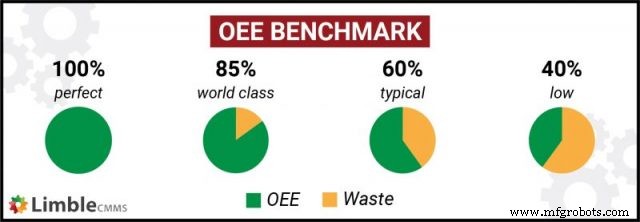
Para obter uma versão mais detalhada e exemplos desses cálculos OEE, leia nosso guia completo sobre eficácia geral do equipamento.
Como implementar e usar OEE em suas instalações
Como já explicado, a fórmula para OEE é bastante direta. Os gerentes que buscam calcular o OEE devem compilar dados sobre disponibilidade, desempenho e qualidade.
As etapas a seguir podem melhorar as chances de implementação bem-sucedida do OEE:
- Escolha um piloto: Comece de forma simples, com uma máquina que seja relativamente fácil de revisar. Escolha operadores ansiosos que tenham uma atitude positiva e sejam receptivos a feedback. Designe um técnico de manutenção competente para o projeto como pessoa de contato. Confie a liderança a um gerente de linha / gerente de departamento com supervisão clara do processo de produção.
- Defina os parâmetros OEE: Defina limites para os dados que precisam ser coletados. Selecione a categoria de tempo para medições, produtos a serem rastreados, a velocidade máxima da máquina e assim por diante.
- Organize a coleta de dados: Escolha a melhor maneira para um operador coletar facilmente os dados relevantes definidos na etapa 2. Mantenha os formulários e procedimentos tão curtos e simples quanto possível para máxima eficácia e precisão.
- Treine o pessoal: Explique os fundamentos e benefícios do OEE para todos os participantes da equipe piloto. Se necessário, forneça treinamento adicional para coleta de dados e relatórios.
- Colete dados: Evite o erro de não confiar nos operadores nesta tarefa. Eles estão melhor posicionados para rastrear as métricas necessárias para calcular o OEE. Se essa for uma opção, você pode fornecer um supervisor com experiência em OEE para melhorar a precisão e evitar erros.
- Dados do processo: Faça com que o líder da equipe analise e processe os dados assim que estiverem prontamente disponíveis, de preferência antes da próxima rodada de coleta de dados. Crie gráficos e relatórios legíveis para facilitar a comunicação das medições OEE.
- Dê feedback aos operadores: Compartilhe os resultados do OEE com os operadores para ajudá-los a obter informações sobre as áreas que precisam ser melhoradas. A comunicação imediata é essencial, pois o feedback pode ser incorporado à produção antes da próxima rodada de coleta de dados OEE.
- Envolva a gestão: Os resultados do OEE podem revelar pontos fracos que requerem intervenção de alto nível no processo de produção. Somente a administração é capaz de resolver alguns desses problemas. Relate todos os resultados do OEE para a gerência de nível superior para uma implementação bem-sucedida.
Para obter o máximo de chance de sucesso, o OEE deve ser um esforço concentrado envolvendo todos - operadores, gerenciamento de nível médio e supervisão de alto nível.
Lutando contra as ineficiências da máquina
A ineficiência da máquina é uma grande dor de cabeça para os fabricantes. O que torna as coisas piores é que muitas organizações nem mesmo estão totalmente cientes das perdas que estão sofrendo devido à baixa eficiência.
O tempo de inatividade dos equipamentos é um dos principais responsáveis por atrapalhar o processo produtivo. A manutenção oportuna e pró-ativa pode ser empregada para minimizar o risco de tempo de inatividade não planejado.
Se você precisar de ajuda para rastrear e organizar atividades de manutenção no chão de fábrica, Limble CMMS está aqui para ajudar. Não hesite em agendar uma demonstração ou entre em contato conosco diretamente se tiver alguma dúvida sobre o software.
Manutenção e reparo de equipamentos
- Como a máquina de corte a laser de fibra melhora a eficiência do corte?
- Como Encontrar uma Máquina CNC Usada
- Como limpar uma máquina CNC usada
- Quão verde é o seu consumo de energia?
- Como escolher sua máquina CNC
- Oportunidades de eficiência energética em sistemas de bombeamento
- Como reduzir o uso de energia na fabricação
- Como aumentar a eficiência do compressor de ar
- 5G Telcos se concentra na eficiência energética
- Como se tornar um maquinista em Quebec