Estudo de dinâmica molecular em nanomáquina baseada em pontas:uma revisão
Resumo
As abordagens de nanomáquina baseada em ponta (TBN) provaram ser uma técnica poderosa e viável para a fabricação de microestruturas. A simulação de dinâmica molecular (MD) tem sido amplamente aplicada na abordagem TBN para explorar o mecanismo que não pode ser totalmente revelado por experimentos. Este artigo analisa o recente progresso científico na simulação da abordagem de TBN em DM. Os métodos de estabelecimento do modelo de simulação para vários materiais são apresentados pela primeira vez. Em seguida, a análise do mecanismo de usinagem para abordagem TBN é discutida, incluindo a análise da força de corte, a análise da remoção de material e a análise de defeitos em subsuperfície. Finalmente, são fornecidas as deficiências atuais e as perspectivas futuras do método TBN em simulações de DM. Esperamos que esta revisão possa fornecer certa referência para a pesquisa de acompanhamento.
Introdução
A tecnologia de micro / nanofabricação tem sido amplamente utilizada em várias áreas, incluindo meio ambiente, energia, biologia, medicina, defesa nacional e outros campos, que desempenha um papel cada vez mais importante na promoção do desenvolvimento nacional e do progresso social [1,2,3,4] . Para realizar a micro / nanofabricação de alta precisão, a abordagem de usinagem mecânica baseada em sonda de microscopia de força atômica (AFM) conhecida como TBN tem equipamentos e operações simples, precisão de usinagem em nanoescala com baixo requisito ambiental e tem se mostrado um poderoso e viável abordagem para fabricar microestruturas [5, 6]. Até agora, nanopontos, linhas / ranhuras, estruturas bidimensionais (2D) / tridimensionais (3D) e até mesmo nanoestruturas em superfícies curvas conhecidas como os principais componentes dos nanodispositivos já foram fabricados com sucesso pelo método TBN [7].
Para fabricar nanoestruturas com maior precisão, é necessário um conhecimento profundo do processo de usinagem dos métodos TBN. Muitos estudiosos têm investigado o mecanismo de abordagem do TBN com experimentos em vários materiais, como metais [8], semicondutores [9, 10] e polímeros [11]. No entanto, é difícil investigar melhor o mecanismo interno de abordagens de TBN por meio de experimentos. A simulação de dinâmica molecular (MD) tem se mostrado uma ferramenta poderosa para explorar o processo de nanomáquina que não pode ser totalmente revelado por experimentos [12, 13]. Comparado com o método experimental, o método MD pode explicar melhor o mecanismo em microescala de remoção de material e geração de superfície por meio da análise das forças de corte, estado de tensão, dissipação de energia e topografia da superfície [12].
No passado, alguns estudiosos já usaram a tecnologia de simulação MD para investigar os processos TBN. Fang et al. investigaram os efeitos da alimentação do traçador e do ângulo do cone no processo de nanolitografia [14, 15]. Isono e Tanaka analisaram os efeitos da temperatura, usinabilidade e forças interatômicas do metal níquel [16, 17]. Yan et al. estudou os efeitos da geometria da ponta no processo de litografia baseado em AFM [18]. Atualmente, alguns novos processos de TBN foram investigados com simulações de MD. Xiao et al. compararam a diferença entre o método de aração estática e o método de aração dinâmica, e descobriram que nanoestruturas menores poderiam ser fabricadas com o método de aração dinâmica [19]. Geng et al. realizaram simulações de MD de nanoscratching controlado por carga aplicando diretamente uma carga normal constante na sonda [20]. Para fabricar nanogrooves com maior densidade, o feed mínimo (MF) deve ser estudado. Ren et al. apresentou uma nova abordagem que envolve um critério grosso-a-fino para determinar MF com o uso de simulações de MD [21]. Os resultados mostram que MF de alta precisão é obtido. No entanto, no artigo de revisão anterior [12, 13, 22,23,24], esses novos avanços da tecnologia de simulação de MD usada para o processo de TBN não foram incluídos. Assim, nesta revisão, nos concentramos no recente estado da arte da simulação de MD para métodos TBN. As tecnologias de modelagem em vários materiais e novos métodos de usinagem são discutidos primeiro. Em seguida, o mecanismo dos métodos TBN é revisado, incluindo a análise da força de corte, a análise da remoção do material e a análise dos defeitos no subsolo. Finalmente, os desafios restantes e as perspectivas futuras na simulação de MD de TBN também são fornecidos nesta revisão.
Métodos de simulação
Para obter resultados de predição precisos, é necessário otimizar o modelo de simulação e a configuração de processamento relacionada. O modelo de simulação contém principalmente configuração atômica e função potencial. A configuração atômica pode ser categorizada em estrutura cristalina e amorfa. Os átomos em materiais cristalinos como cobre, ferro, silício, etc. são arranjados de maneira regular e ordenada e os materiais amorfos como polímeros são compostos de cadeias moleculares irregulares. O comportamento do material em nanoescala é representado em simulações MD por meio de funções potenciais e várias funções potenciais foram propostas e utilizadas para simular o comportamento do material em simulações atomísticas. Além disso, a configuração de processamento também deve ser considerada, como as várias condições de usinagem e abordagens de usinagem. As seções a seguir apresentarão as metodologias de estabelecimento do modelo e a configuração do processamento.
Estabelecimento do modelo de DM
A configuração atômica interna de materiais cristalinos são várias, como cobre (cúbico centrado na face), ferro (cúbico centrado no corpo), titânio (hexagonal compactado) e silício (estrutura em diamante) [27, 28]. A maioria dos materiais cristalinos está na forma de estrutura cristalina única e policristalina. O sólido de cristal único possui uma estrutura atômica que se repete periodicamente em todo o seu volume, na ausência de defeitos. A duplicação da célula unitária em todas as três direções espaciais pode facilmente estabelecer o modelo de cristal único [13]. Ao estabelecer o modelo atômico MD, as várias orientações da superfície devem ser consideradas, o que pode influenciar as propriedades de usinagem da peça de trabalho [29,30,31]. A estrutura policristalina possui a estrutura com diferentes tamanhos de grãos, a qual foi construída seguindo o método de mosaico de Voronoi [32]. O material nanotwined (NT) é um tipo de estruturas especiais de policristalino que se tornou objetos de pesquisa mais importantes devido às suas excelentes propriedades mecânicas, como ultra-alta resistência, boa ductilidade e alta tenacidade à fratura [33,34,35,36] . Nesta revisão, o método para construir o Cu policristalino NT é dado como um exemplo [25]:primeiro, uma multicamada que consiste em múltiplas camadas de Cu cristalino de igual espessura é construída e forma-se TB entre as camadas adjacentes. Em segundo lugar, o ângulo de cada grão é calculado. Finalmente, NT policristalino com condições de contorno periódicas é gerado usando a construção de Voronoi, que acomoda a multicamada e o ângulo de grão obtido. A Figura 1a apresenta as configurações atômicas do cobre, incluindo Cu cristalino sing, Cu policristalino e Cu policristalino NT, em que os átomos são coloridos pelo vizinho comum.
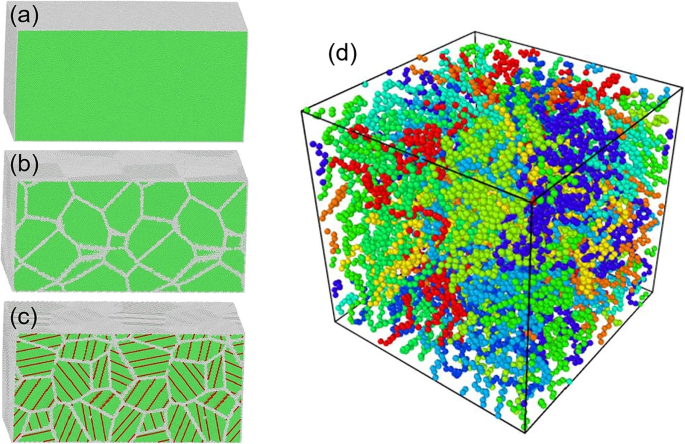
a Microestrutura de Cu cristalino único. b Microestrutura de nanopolycrystalline. c Microestrutura de NT policristalino. Os átomos são coloridos de acordo com os valores CNA, como verde e branco representam FCC e átomos defeituosos [25]. d O modelo de átomo unido equilibrado de PE amorfo, o modelo foi colorido por diferentes cadeias moleculares [26]
Em estudos anteriores, o polímero foi modelado com um modelo genérico de granulação grossa [37, 38]. Por exemplo, os detalhes para estabelecer o modelo de polietileno (PE) são dados como segue [39]:(i) o sistema PE inicial com 10 cadeias moleculares foi obtido com o uso do algoritmo de passeio aleatório autoevitível de Monte Carlo [39]; (ii) o primeiro átomo de cada cadeia foi inserido em um local disponível da rede em primeiro lugar e, em seguida, a cadeia molecular começou a crescer ao longo de uma certa direção com base em uma forma probabilística gradual de acordo com o comprimento da ligação e os locais desocupados na célula .; (iii) uma vez que a densidade inicial é dada, o tamanho da caixa de simulação é determinado. Em nossa simulação, a dimensão da caixa de simulação inicial era de cerca de 80,06 × 80,06 × 80,06 Å 3 para o sistema que consiste em 10 cadeias de PE. O modelo MD de PE é mostrado na Fig. 1d.
A geometria da ponta é geralmente complexa e variável, incluindo forma de cone [40], pirâmide triangular [18] e hemisfério (forma romba) [21], que desempenha um papel importante no processo de TBN. Em particular, a forma da ferramenta piramidal no modelo MD é consistente com aquela do processo de usinagem AFM e a ferramenta esférica é consistente com o grão abrasivo no processo de retificação; assim, o mecanismo de usinagem pode ser melhor explicado comparando os resultados da simulação com os resultados experimentais. Na maioria dos casos, a ponta é considerada infinitamente rígida, o que é conseguido mantendo as posições relativas dos átomos constantes e viajando em velocidade constante [41].
Também é crucial selecionar as funções de energia potencial adequadas que determinam a credibilidade dos resultados da simulação [21]. EAM é um potencial multicorpo adequado para sistemas metálicos [24]. Ele fornece uma descrição mais realista da coesão metálica e evita a ambigüidade herdada pela dependência de volume, que é empregada para descrever a interação entre átomos metálicos, como cobre [42] e ferro [43]. Os potenciais de Tersoff [44] e Stillinger-Weber (SW) [45] provaram ser os particularmente viáveis para modelar materiais com uma estrutura cúbica de diamante. Para investigar o mecanismo de Si no processo TBN, o deslizamento de deslocamento e a transformação de fase devem ser observados nas simulações de MD. Comparado ao potencial Tersoff, o potencial SW não só tem flexibilidade suficiente para descrever uma série de configurações de silício diferentes, mas também fornece a correspondência mais próxima aos resultados de nucleação de deslocamento ab initio em silício livre de defeitos [46, 47]. Assim, a função potencial SW pode ter mais potencial para descrever a interação entre os átomos de silício. Potencial de ordem de ligação analítica (ABOP), ordem de ligação empírica reativa (REBO) e potenciais de ordem de ligação empírica reativa intermolecular adaptativa (AIREBO) são uma classe de potenciais que estendem a função potencial de Tersoff de acordo com a aproximação de ligação estreita e dependem de quantidades fundamentais [ 48]. O potencial ABOP é ideal para as interações entre os átomos de silício e carbono, o qual é empregado para investigar a deformação do material e o comportamento de remoção no processo de SiC. O potencial REBO é particularmente popular em simulações de nanotubos de carbono e carbono. O modelo AIREBO foi desenvolvido para superar as deficiências da função potencial REBO, fornecendo uma aproximação mais precisa do que os termos REBO e também recursos adicionais de modelagem de interações mais complexas [41]. As interações intermoleculares e intramoleculares na amostra de poliestireno são descritas pelo potencial AIREBO bem estabelecido [49].
A maioria das simulações de MD foi realizada com o uso do Simulador Atômico / Molecular Massivamente Paralelo de Grande Escala (LAMMPS) [50]. Alguns modelos de peças complexas, como materiais policristalinos policristalinos e nanotwined, podem ser realizados com Atomsk [51]. A construção de polímeros, incluindo átomos, ângulo de ligação, impróprios, e seus diversos tipos são obtidos a partir do arquivo de dados gerado no Material Studio (MS) [52]. Tanto a Open Visualization Tool (OVITO) [53] e a dinâmica molecular visual (VMD) [54] são ferramentas úteis para visualizar o modelo ou o processo de usinagem.
Com o uso de simulações de MD, vários modelos de materiais podem ser estabelecidos de forma eficaz. No entanto, a maioria dos modelos de peças são menores que 50 nm × 50 nm × 50 nm em tamanho, o que pode resultar no desvio dos resultados reais [40, 55, 56]. Além disso, ainda faltam funções potenciais que possam descrever efetivamente alguns materiais como GaAs e Lu 2 O 3 . Assim, os modelos MD e funções potenciais relacionadas ainda precisam ser otimizados para descrever o processo de simulação com mais precisão.
Configuração de processamento
Em experimentos TBN, o modo de carga controlada é geralmente realizado aplicando uma carga normal constante na ponta. Este modo demonstrou ser de maior precisão, especialmente conduzindo nanomáquinas em superfícies inclinadas ou curvas. No entanto, muitas simulações MD de processos TBN são realizadas sob o modo de controlador de deslocamento, o que pode levar a diferenças entre a simulação e o experimento [18, 57]. Assim, alguns estudiosos realizaram simulação MD do processo de nano-arranhões controlados por carga aplicando diretamente uma carga normal constante na sonda [20, 58]. Nos processos de usinagem, ele pode ser dividido em três partes:estágio de relaxamento, estágio de penetração e estágio de raspagem. Além disso, a ponta não é completamente perpendicular à peça de trabalho devido à curvatura do feixe do microscópio de força atômica (AFM), substrato com um ângulo de inclinação, bem como aspereza da superfície da amostra. Assim, o efeito da inclinação da ponta não deve ser negligenciado. Liu et al. escolheu pontas com diferentes ângulos de inclinação para investigar o efeito da inclinação da ponta nos resultados da usinagem [59]. Além disso, o desgaste da ponta é um fator chave para o processo de usinagem, que tem grande influência na qualidade da usinagem. Nanoscratching com lubrificação por camada de água pode reduzir o desgaste da ponta para aumentar a vida útil da ferramenta e garantir a qualidade da usinagem. No entanto, o mecanismo de usinagem afetado pela lubrificação por camada de água ainda não é bem conhecido. Para resolver esse ponto, Ren et al. usou o método de simulação MD para investigar os efeitos da lubrificação por camada de água nos resultados da usinagem com cobre monocristalino [60].
O processo de single scratch provou ser um método fácil de fabricar nanogroove, mas tem a limitação da dimensão do groove. O método multi-pass scratching foi apresentado para aumentar o tamanho da nanogroove [62]. Geng et al. estudaram a diferença entre a abordagem de passagem única e a abordagem de passagem múltipla com simulação MD e resultados experimentais [20]. Tanto as abordagens de passagem única quanto de passagem múltipla podem ser consideradas como litografia de aração estática, que são conduzidas com o modo de contato do sistema AFM. No entanto, a litografia do arado estático pode induzir um desgaste da ponta não desprezível ao realizar o processo de raspagem de longa distância. A técnica de usinagem baseada no modo de rosqueamento é denominada litografia de aragem dinâmica, que tem o potencial de reduzir o desgaste da ponta. A Figura 2 mostra os esquemas da litografia de aração estática e dinâmica em cobre monocristalino, respectivamente. Para a aração estática, a ponta de diamante primeiro alimentou para baixo e, em seguida, começou a arar ao longo da direção negativa do x eixo. Após o término da aração, a ponta foi retirada para cima, para a posição vertical original. Para o processo de aragem dinâmica, a ponta do diamante moveu-se ao longo de uma curva senoidal com amplitude e período pico-vale pontiagudo [19]. Com base no princípio da técnica de usinagem baseada no modo de rosqueamento, Sundaram et al. desenvolveram um novo método de nanomaquinagem usando AFM, que é conhecido como Nano Impacto de Usinagem Assistida por Vibração por Abrasivos Soltos (VANILA). Nesse método, o AFM é utilizado como plataforma e os nanoabrasivos são injetados na lama entre a peça de silicone e a vibração da ponta do AFM. A energia cinética para os abrasivos é gerada pela vibração da ponta do AFM e consequentemente resulta na remoção do material em nanoescala da amostra [61]. A representação esquemática do processo VANILA é mostrada na Fig. 2b, c.
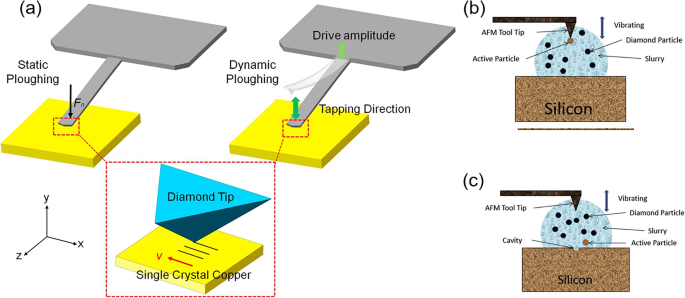
a Os esquemas da litografia de aração estática e dinâmica em cobre monocristalino [19]. b Ponta da ferramenta AFM atingindo uma partícula de diamante. c partícula de diamante atingindo a peça de trabalho [61]
Análise do resultado da simulação
Análise da força de corte
A força de corte pode refletir claramente o processo de remoção de material e defeito de evolução, que é um parâmetro físico importante para a compreensão do fenômeno de corte [19, 63, 64]. Além disso, a força de corte está intimamente relacionada com o poder de corte e a vida útil da ferramenta, o que pode fornecer orientação no processo de usinagem TBN [65]. No processo TBN, a força de corte é avaliada principalmente pelo método de calibração de força, mas a força lateral não pôde ser obtida por este método [66, 67]. Usando a tecnologia de dinâmica molecular, a variação das forças de corte incluindo forças laterais e tangenciais podem ser observadas em tempo real para todo o processo [68]. Além disso, a força média e a força resultante também podem ser obtidas através do método de simulação MD.
Por meio da análise da variação da força de corte, a diferença de várias estruturas de materiais e a influência dos parâmetros de usinagem no processo TBN podem ser refletidas. Li et al. encontraram forças mais altas para arranhar no Cu policristalino em comparação com o Cu cristalino único é atribuído ao fato de que a anisotropia do grão da superfície tem pouco efeito entre a peça e a ponta quando a ponta vai de um grão para outro grão de diferentes orientações de cristal, enquanto o fluxo de plástico estável é mostrado na remoção de material de cristal único Cu devido ao seu sistema de orientação única [25]. Verificou-se também que a força de corte para diferentes estruturas cristalinas aumenta com o incremento da velocidade de corte, pois uma velocidade de nanoscratching mais alta produz mais cavacos [69]. Ao contrário, a mudança da força de corte apresenta comportamento adverso no processo de raspagem do SiC, pois maior velocidade pode gerar átomos da estrutura cristalina mais amorfa, o que torna o material do SiC mais dúctil e mais fácil de ser removido [70]. Yan et al. investigaram a processabilidade das bicamadas Cu / Ni usando o método de simulação MD e descobriram que a força das bicamadas Ni-Cu é maior em comparação com Cu, Ni e as bicamadas Cu-Ni, uma vez que o movimento dos deslocamentos foi impedido pela interface das bicamadas que serviam como uma barreira de propagação [71]. Em relação aos polímeros amorfos, a propriedade de usinagem foi influenciada pela velocidade de raspagem em três aspectos diferentes como segue [72]:em primeiro lugar, a maior altura de empilhamento na frente da ponta gerada em maior velocidade leva a uma maior força tangencial devido a mais resistência à ponta. Então, uma velocidade mais alta leva a uma taxa de deformação mais alta, o que pode ocasionar o endurecimento por deformação do material. Isso também levaria ao incremento das forças de corte. Por fim, com o incremento da velocidade, o efeito de maciez térmica permite que a peça seja usinada com mais facilidade, reduzindo a força tangencial e a força normal. Nos processos de usinagem de polímeros, as forças de corte aumentam com o incremento da velocidade, indicando que o efeito de empilhamento e endurecimento da taxa de deformação desempenham papéis mais importantes na determinação das forças de arranhão. Além da influência dos materiais da peça, a geometria da ponta também desempenha um papel importante no processo de usinagem [18, 73, 74]. Ren et al. investigou o efeito dos ângulos de ponta nas forças de corte com ponta em forma de cone. Verifica-se que as forças aumentam com o aumento dos ângulos de semiapex devido ao aumento da área de contato entre a ponta e os materiais da peça [21]. Além disso, o coeficiente de atrito diminui fortemente com o semi-ápice, enquanto a dureza aumenta [75].
Alguns estudiosos também investigaram a variação da força de corte em condições específicas de usinagem. Ren et al. analisou a correlação entre a espessura da camada de água e as forças de arranhão. A variação das forças de arranhão com a mudança na espessura da camada de água é mostrada na Fig. 3. Ao contrário do processo de macroscratching onde a camada de água desempenha principalmente o papel de lubrificação e redução da força de corte, a resistência da camada de água é dominante em comparação com o efeito de lubrificação e a camada de água mais espessa leva a maiores forças de corte totais [60]. Além disso, o efeito da inclinação da ponta também é discutido pela análise da dureza (força normal por átomo) e coeficiente de atrito [59]. Os resultados mostram que a dureza normal é mais sensível na direção para frente ou para trás em comparação e o efeito da inclinação da ponta lateralmente pode ser desprezado. Além disso, o efeito de inclinação na força normal é a principal razão para a mudança do coeficiente de atrito e o efeito de inclinação na força de arranhão é muito menor do que o efeito na força normal.
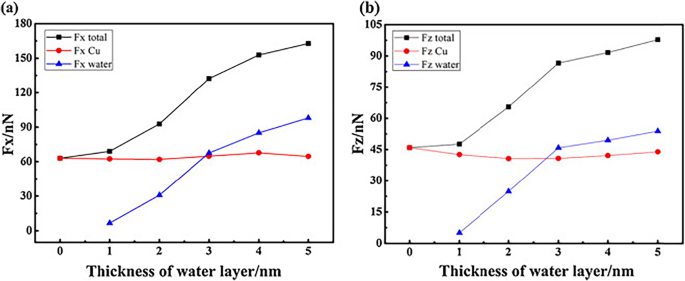
a Variação das forças médias de arranhão com mudança na espessura da camada de água: a forças tangenciais e b forças normais [60]
Comparando a força de corte entre a aração estática e a aração dinâmica, a diferença de mecanismo pode ser revelada. A força de corte na litografia de aração dinâmica oscila drasticamente com o bater periódico da ponta do diamante, enquanto pequenas flutuações são observadas na aração estática. Além disso, a força média de usinagem na aração dinâmica é menor que a metade daquela na aração estática, indicando menor desgaste da ponta na litografia de aração dinâmica [19]. No processo de aração dinâmica, a orientação da ponta tem grande influência na força de corte. Yan et al. combinou a profundidade da ranhura e a força de aragem para comparar a eficiência da usinagem. Os resultados mostram que a face frontal da ponta tem a melhor eficiência, pois tem a força de aração semelhante à da orientação frontal da ponta, mas ao mesmo tempo mais do que o dobro da profundidade do sulco [63]. Através da análise das forças de corte, o mecanismo do processo de usinagem TBN com vários materiais e condições de usinagem pode ser explicado mais detalhadamente. Além disso, a comparação das forças de corte em vários modos de processamento pode fornecer orientação para a otimização do processo da abordagem TBN.
Análise do estado de remoção de material
A análise do estado de remoção de material também é um método essencial para revelar o mecanismo da abordagem TBN. A retirada do material e a topografia no processo de usinagem são geralmente observadas por meio de microscópio eletrônico de varredura (MEV) e AFM. No entanto, a morfologia do sulco e o estado de remoção só podem ser detectados após o processamento e o processo de remoção de material não pode ser compreendido dinamicamente. Recentemente, Zhang et al. usaram ferramentas de corte linear conectadas diretamente no SEM para ver o processo de formação de cavacos no corte de material, enquanto este método é complicado e o SEM deve ser modificado [76]. Portanto, esse método é difícil de ser generalizado. Comparado com o método experimental, o método de simulação MD pode ser facilmente usado para explorar o mecanismo de remoção de material e geração de superfície em nanoescala, e o processo de usinagem pode ser observado em tempo real através do método MD.
É conhecido dos resultados da simulação MD do processo TBN que os estados de deformação são classificados em estado de aragem e estado de corte. Com o movimento da ponta, os átomos do material da peça à frente da ponta são comprimidos e então se acumulam para formar o cavaco contínuo durante o estado de corte. Simultaneamente, há também alguns átomos do material da peça se acumulam nos lados esquerdo e direito da ranhura fabricada após a passagem da ponta [57]. Ao comparar a relação entre o estado de corte e o estado de não corte, podemos obter se o estado de corte ou o estado de lavra ocupam a parte dominante quando os vários raios da ponta são usados para arranhar em diferentes profundidades de arranhão [77]. Nos últimos anos, muitos estudiosos investigaram ainda mais as propriedades do material nos estados de remoção de material. Por exemplo, material monocristalino apresenta anisotropia no processo TBN, que tem grande efeito na remoção de material [20]. Em comparação com materiais monocristalinos, os limites de grão têm um efeito importante nas propriedades mecânicas dos materiais policristalinos. Gao et al. descobriram que a orientação do grão ao invés do tamanho do grão também é dominante na determinação do perfil do empilhamento [78]. Além disso, a geometria da ponta também tem forte efeito na remoção de material. Três tipos de ponta (cônica, pirâmide triangular e ponta hemisférica) foram selecionados para revelar o efeito da geometria da ponta no estado de remoção do material. Para a ponta cônica, existe uma clara dependência do ângulo do meio ápice. Com uma metade do ápice maior, o ângulo da ponta leva a mais volume de cavacos e melhora a suavidade da superfície de arranhão, mas requer maior força de arranhão, gera maior coeficiente de atrito e temperatura mais alta na peça de trabalho, e aumenta o dano subsuperficial [40]. Alhafez também investigou o efeito do ângulo do meio ápice na formação de empilhamento [75]. Verificou-se que ao riscar com pequeno ângulo do meio ápice da ponta, o empilhamento principalmente se acumula na direção para frente, enquanto o empilhamento lateral domina para a condição de usinagem do grande ângulo do meio ápice da ponta. Alguns estudos focaram na ponta triangular piramidal que é consistente com a geometria real da ponta no processo de usinagem baseado em AFM [19, 20, 63, 79]. Três direções de usinagem foram comparadas principalmente, que são borda frontal, frontal e lateral frontal. No processo de usinagem de SiC, o estado de remoção de material pode ser controlado simplesmente ajustando a direção de arranhão da ferramenta. A direção de arranhamento de ponta pode fornecer um processo mais estável, o que pode resultar em melhor precisão de tamanho e consistência das ranhuras obtidas [79]. No entanto, o estado de remoção de material dos polímeros é mais sensível à temperatura em comparação com metais ou materiais semicondutores. Durante o processo de riscar, a temperatura local na zona de arranhar é superior à temperatura de transição vítrea, o que indica que a peça de trabalho na zona de arranhar pode ser removida de forma dúctil [72]. Zhan et al. investigou os mecanismos microscópicos de fricção do poliestireno amorfo. Eles descobriram que a flexibilidade das cadeias moleculares aumenta com o aumento da temperatura, o que pode permitir que as cadeias moleculares se enrolem mais facilmente e retornem ao seu estado original [56]. Du et al. descobriram que a velocidade de usinagem tem grande influência nos resultados da usinagem de poliestireno. A mudança intracadeia domina a deformação permanente da amostra de poliestireno quando a velocidade de usinagem é pequena, enquanto o deslizamento entre cadeias é mais pronunciado quando a velocidade de usinagem é grande [80].
Como pode ser visto na discussão acima, a maioria dos estudos focou principalmente na condição seca em vez de fluidos. No entanto, os átomos acumulados à frente da ferramenta são reduzidos e as rebarbas ao longo das ranhuras não são óbvias com a alta espessura da camada de água e a rugosidade da superfície diminui visivelmente e resulta em uma superfície relativamente lisa. Pode ser explicado que a camada de água atua como o lubrificante para reduzir a região de aderência entre a ferramenta e a superfície do cavaco recém-formada e reduz a força de arrasto exibida no limite da face cavaco-ferramenta. A consequência direta é que a qualidade da superfície é muito melhorada. Com o aumento da espessura da camada de água, a qualidade da superfície pode ser melhorada gradativamente [60]. Em algumas novas abordagens de usinagem, Shockly et al. investigou os efeitos dos parâmetros (velocidade de impacto, ângulo de impacto e temperatura de operação) na usinagem de nanoimpacto assistida por vibração na formação de nanocavidade e descobriu que os parâmetros operacionais têm influência substancial na profundidade e largura das nanocavidades geradas, conforme mostrado na Fig 4 [61]. Xiao et al. descobriram que a profundidade e a largura do sulco no processo de aração dinâmica são menores do que no processo de aração estática, o que significa que nanoestruturas com pequenas características podem ser fabricadas por litografia de aração dinâmica. Além disso, as dimensões das ranhuras podem ser controladas pela relação da amplitude do acionamento no processo de aração dinâmica, e isso demonstra que a fabricação das ranhuras também pode ser controlável [19].
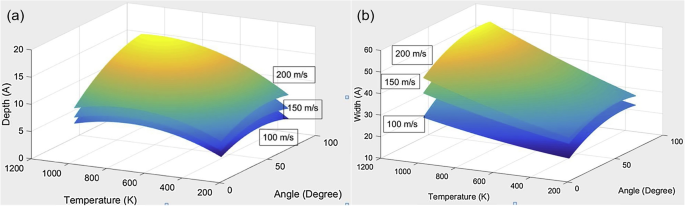
Gráfico de regressão linear múltipla para a profundidade da nanocavidade (velocidade de impacto, ângulo de impacto e temperatura operacional) e b largura da nanocavidade (velocidade de impacto, ângulo de impacto e temperatura operacional) [61]
Durante o processo de remoção de material, existe um comportamento de desgaste na ponta. Na maioria dos estudos anteriores, a ponta é definida como um corpo rígido, o que significa que o fenômeno do desgaste da ferramenta não pode ser observado diretamente [13]. Muitos estudiosos investigaram o desgaste da ferramenta estudando o estado de remoção do material, tensão e distribuição de temperatura [70, 77]. A fim de refletir o real fenômeno do desgaste da ponta durante o processo de usinagem, Meng et al. definir a ponta como corpo deformável e encontrar o comportamento de desgaste da ponta durante o processo de usinagem [81]. Os resultados mostram que a forma de desgaste abrasivo do diamante é principalmente desgaste adesivo no estágio inicial e desgaste átomo por átomo no estágio de estabilidade de processamento e a quantidade de desgaste de atribuição átomo por átomo do abrasivo é menos afetada pela velocidade de corte [ 81]. É notável que existem relativamente poucos relatórios sobre o comportamento de desgaste da ponta. Espera-se que o uso do corpo deformável da ponta promova ainda mais a investigação do comportamento ao desgaste da ponta durante o processo de nanomáquina.
A análise do estado de remoção de material fornece um suporte eficaz para o monitoramento em tempo real do processo de usinagem. No entanto, devido à limitação da escala de comprimento mencionada acima, a morfologia da superfície usinada e o processo de remoção de materiais só puderam ser analisados por comparação qualitativa. É difícil prever os resultados precisos do processamento.
Defect Evolution Process Analysis
To obtain the information about the defects generated during the scratching process, TEM is usually employed after the FIB sample preparation techniques, which has several disadvantages, such as relatively complicated operation, high cost, and strong material dependence.
The MD simulation method can obtain the defects generated beneath the sample surface easily. Moreover, the defect evolution process during the scratching could also be observed by using the MD simulation approach, which could not be obtained by experimental method. Many available algorithms to extract defect types were presented, including common neither analysis (CNA) [82], centro-symmetry parameter (CSP) [83], slip vector analysis [84], Ackland-Jones analysis [85], etc. However, these methods are not suitable for tracing the propagation of dislocations, especially when a large number of dislocations are generated by tip scratching along certain direction, and we can no longer investigate what is going on inside the specimen using these methods [86]. Chen et al. presented slipping analysis for visualizing the atomic slipping process for material deformation, which could filter out those atoms that have slipped relative to its neighbor atoms during a specified period of time in the condition with large numbers of atoms [86]. By using this method, Xiao et al. investigated the slipping process during dynamic and static ploughing lithography [19]. The relationship between the cutting force and slipping process is shown in Fig. 5. It could be seen that for dynamic ploughing, the sample material mainly flows downwards and sidewards, whereas no obvious downwards material flow is observed in static ploughing process. In addition, the propagation of the dislocation is dependent on the orientation of the tip, leading to the various morphologies of the grooves. Dislocation extraction algorithm (DXA) is also a useful dislocation analysis tool to identify the lattice dislocation and to determine their Burger vector [87]. By using this method, Gao et al. investigated the behavior of the nanoscratching of iron. They found that a distinct reorganization of the dislocation network. At the beginning, the plastic zone grows linearly with the scratching length along the path. Then, the dislocation density decreases rapidly after some length dislocation reactions. Plastic activity then is concentrated only on the scratch front. Only few dislocations remain in the middle of the scratch. Vacancies in this zone are created by dislocation reactions. It is also found that point defects vacancies generated by dislocation reactions and deformation twining [88].
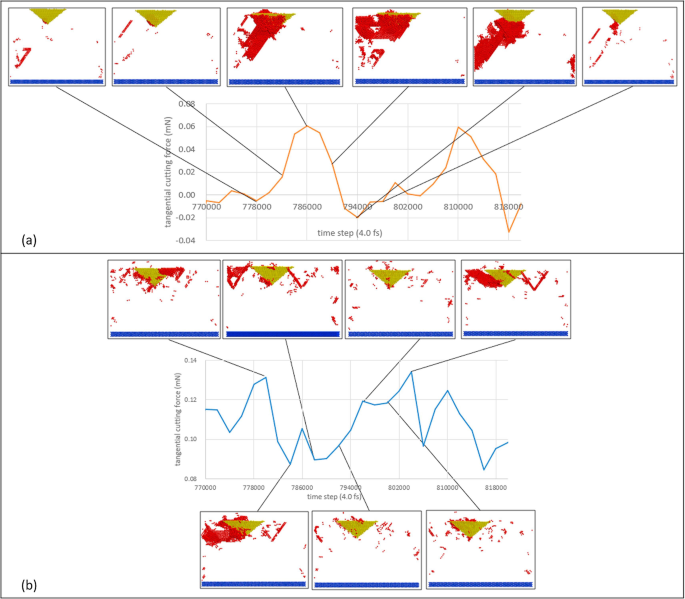
Slipping processes in a dynamic ploughing and b static ploughing [19]
For the polycrystalline materials, the deformation mechanism was mediated by dislocation nucleation within grain interior as well as grain boundary dislocations in polycrystalline material [43]. While the dislocation propagation is associated with the formation of nanovoids and interstitial clusters in the case of larger grain size, and the formation of twins at the grain boundary was dominating for smaller clusters. This behavior was attributed to the transition of dislocation movement from smooth (larger grain) to rough (smaller grain) during scratching process. Li further concluded the difference of material deformation mechanism about single crystal Cu, polycrystalline Cu, and NT polycrystalline Cu. The results show that the plastic deformation is mainly affected by the interaction between dislocations during scratching process in single crystal Cu; while for polycrystalline Cu both dislocations and GB dominate the plastic deformation; and the plastic deformation is controlled by the interactions of the dislocation, grain boundary (GB), and twin boundary (TB) accompanied with twinning/detwinning [25].
Furthermore, many studies focused on the MD simulation of the TBN process on the semiconductor materials, such as silicon, silicon carbide, gallium arsenide, and aluminum nitride. To investigate these brittle materials, phase transformation is also an important deformation mode in addition to dislocation slip [89]. The interaction between dislocation and phase transformation varies with the crystal orientation. The results indicate that prior to the “Pop-In” event, Si (010) undergoes inelastic deformation accompanied by the phase transformation from the Si-I to the Si-III/ Si-XII, which is not occurred in Si (110) and Si (111). While, the phase transformation from the Si-I to the bct-5 is the dominant mechanism of incipient plasticity for each crystallographic orientation, and dislocation nucleation is also an operating deformation mode in the elastic-plastic transition of Si (010). Dai et al. investigated the subsurface damage mechanism on single crystal silicon during TBN process. It is found that the evolution of crystalline phases is consistent with the distribution of hydrostatic stress and temperature [40]. SiC is also a kind of important semiconductor material, which has the similar property as silicon. The SiC material removal process is achieved through the phase transfer from zinc blended to amorphous structure with few hexagonal diamond structures. Higher scratching speed generates more amorphous structure atoms, fewer hexagonal diamond atoms, and fewer dislocation atoms due to larger impaction and less rearrangement time [90]. While Meng et al. found when the phase transition is not the dominant deformation mechanism, the Schmidt coefficient method can effectively predict the sliding motion of 3C-SiC during the TBN process (elastic sliding motion and dislocation slip motion) [79]. Moreover, Meng et al. further studied on the strain rate and heat effect on the removal mechanism of SiC. They found that the strain rate effect and the thermal softening effect directly affect the material removal amount and form of the subsurface damage (SSD). The influence of the thermal softening effect on the stress in the processing region under the condition of high strain rate exceeds that of the decrease in the growth rate of the dislocation generation speed. The polycrystalline SiC removal process is dominated by the amorphous phase transition. Furthermore, several hexagonal diamond structure atoms and dislocations are found in the GBs during the scratching. Higher scratching speed and larger depth of cut promotes more atoms to transfer into the amorphous structure due to larger impaction [81]. Compared with monocrystalline SiC, the microstructure in polycrystalline makes the SiC more soften by generating less normal scratching force and amorphous structure phase transition and thinner plastic deformation induced SSD [91]. Dislocation propagation and phase transition analysis could explain the mechanism in machining process. However, most researches focused on single crystalline materials and the materials with complex structure are rarely reported, which should be further studied.
Future Research Directions and Challenges
At present, the research on the TBN process through MD simulation is widely reported. However, there are still some limitations to be considered. Thus, future directions are discussed in this review.
- (1)
With the development of TBN methods, some novel technologies have been proposed in this field. For example, AFM tip-based nanomilling process has a broad prospect due to its great machining performance and size control properties [92, 93]. However, the mechanism of nanomilling has not been fully understood due to limitation of the detection equipment. With the use of MD simulation, it is hopeful that the variation of the cutting force, the dynamics change of defects, and the removal state of workpiece materials during rotating process of the tip. In addition, sample vibration-assisted nanoscratching method has not been reported yet. MD simulation approach could provide meaningful guidance in the early stage.
- (2)
Due to the limitation of the length and time scales, MD methods still could not fully describe the experimental process quantitatively. In some studies combining experiments and MD simulations, MD simulation approach could only qualitatively explain the experimental phenomena [19, 20, 94]. In particular, for some time-dependent materials such as amorphous polymers, the velocity of the probe has a significant impact on the removal state of polymers. Thus, in order to accurately predict the experimental process and quantitative analyze the experimental results, the improvement of algorithm and computing capability is indispensable.
- (3)
Many nanostructures have been achieved on polymer materials using the TBN method [95,96,97]. In particular, the mechanical machining process of polymer materials based on TBN method keeps the normal load constant so as to guarantee the accuracy of the machined nanostructures [98]. However, the reports of MD simulation of polymer in TBN process are limited until now. Moreover, thermal scanning probe lithography is developing in polymer, which has the potential to improve the machining accuracy of the TBN process. It is necessary to reveal the material removal mechanism of the polymer materials when conducting nanoscale scratching process with the mechanical-thermal effect.
Conclusão
It is undeniable that MD simulations technology plays an increasingly crucial role in nanomachining process to reveal hitherto unknown phenomena [99]. This review concluded the recent progress in MD simulation of TBN method, and the above contents are summarized as follows:
- (1)
The establishment of MD models of various materials and related potential function were summarized. In particular, the modeling process of NT polycrystalline materials and amorphous polymers were discussed in this section. The accuracy of MD models is of great significant to the subsequent simulation results.
- (2)
The new technologies of TBN methods, including multi-scratching, dynamic ploughing, and VANILA were presented. With the help of MD simulation, the mechanism of these methods could be better understood. In particular, the essential difference between static ploughing and dynamic ploughing was revealed by MD method from the aspects of internal defects, morphology and cutting forces.
- (3)
The analysis of MD simulations in TBN process, including the cutting force, the state of material removal, and defect analysis are also summarized. Besides, some novel analysis methods like slipping analysis are also given. With these methods, the processing mechanism based on TBN approach is reviewed, which shows the materials dependence on the TBN machining process.
Abreviações
- TBN:
-
Tip-based nanomachining
- AFM:
-
Força atômica microscópica
- MD:
-
Dinâmica Molecular
- NT:
-
Nanotwined
- PE:
-
Polietileno
- EAM:
-
Embedded atom method
- SW:
-
Stillinger-Weber
- ABOP:
-
Analytical bond order potential
- REBO:
-
Reactive Empirical Bond Order
- AIREBO:
-
Adaptive Intermolecular Reactive Empirical Bond Order
- LAMMPS:
-
Large-scale Atomic/Molecular Massively Parallel Simulator
- MS:
-
Material studio
- OVITO:
-
Open Visualization Tool
- VMD:
-
Visual molecular dynamics
- VANILA:
-
Vibration-Assisted Nano Impact machining by Loose Abrasives
- SEM:
-
Microscópio eletrônico de varredura
- CNA:
-
Common neighbor analysis
- CSP:
-
Centro-symmetry parameter
- DXA:
-
Dislocation extraction algorithm
- GB:
-
Grain boundary
- TB:
-
Twin boundary
- SSD:
-
Subsurface damage
Nanomateriais
- Nano e ânodo de bateria:uma revisão
- Uma revisão sobre a aplicação de biossensores e nanossensores em agroecossistemas
- Efeito de superfície no transporte de petróleo em nanocanais:um estudo de dinâmica molecular
- Modelagem de Dinâmica Molecular e Simulação de Corte de Cério com Diamante
- O estudo de um novo sistema micelar em forma de verme aprimorado por nanopartículas
- Estudo antitumoral de nanogéis de sulfato-metotrexato de condroitina
- Estudo do Efeito da Direção de Impacto no Processo de Corte Nanométrico Abrasivo com Dinâmica Molecular
- Estudo de comportamentos de atrito em nanoescala de grafeno em substratos de ouro usando dinâmica molecular
- Baixa deterioração do túnel de junções de molécula única de alcano terminado por iodo
- Novo estudo examina a dinâmica e os fatores de produtividade na fabricação dos EUA