Obra-prima com uso intensivo de compósitos:2020 Corvette, Parte 1
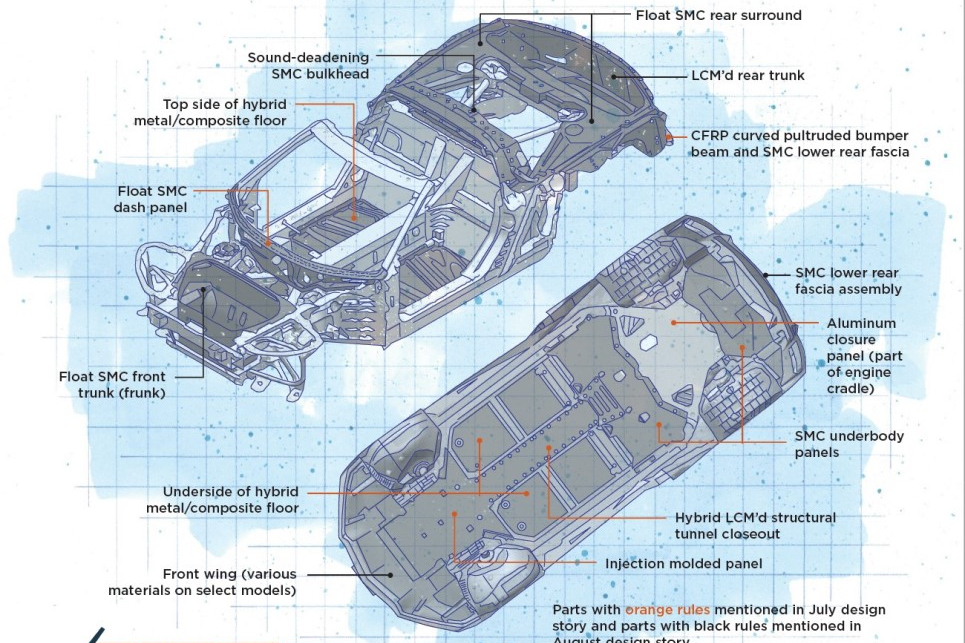
Para a Parte 2, leia “Obra-prima com uso intensivo de compósitos:Corveta 2020, Parte 2”.
O tão aguardado Chevrolet Corvette de oitava geração (C8) da General Motors Co. (GM, Detroit, Michigan, EUA), que tem gerado elogios desde sua revelação oficial em 18 de julho de 2019, iniciou a produção comercial no início deste ano. O novo Corvette Stingray conversíveis e coupés são notáveis não apenas por sua beleza e pelo fato de a GM ter produzido um foguete de motor central de alto desempenho, legal para as ruas, a partir de menos de US $ 60.000 - um terço do preço de um motor central de desempenho comparável carros - mas eles também apresentam uma gama impressionante de novos e genuinamente inovadores conteúdos compostos, que descreveremos aqui e na Parte 2 no próximo mês.
A nova configuração do motor muda tudo
A engenharia da GM entrou no projeto preliminar sabendo que trabalhariam em um veículo com motor central - o primeiro Corveta de produção em oito gerações para ostentar essa configuração. “Nós evoluímos a arquitetura do motor dianteiro o máximo que pudemos para desempenho, então mudar para um projeto de motor central foi o próximo passo lógico para melhorar um carro que já era excelente e ser o líder do segmento”, explica Tadge Juechter, engenheiro-chefe executivo da GM -Global Corveta . Equipado com o pacote de desempenho Z51, o 2020 Corvette Stingray pode acelerar 0-60 mph (0-97 kmh) em 2,9 segundos e atingir velocidades máximas de 194 mph (312 kmh). Empurrar o motor em direção à traseira do veículo afetou muitas coisas, incluindo o centro de gravidade do carro, a posição relativa dos ocupantes, a localização da transmissão e o design dos painéis da parte inferior da carroceria e do armazenamento do porta-malas. O projeto do motor central também introduziu temperaturas de operação e ruído mais elevados em novas áreas do carro.
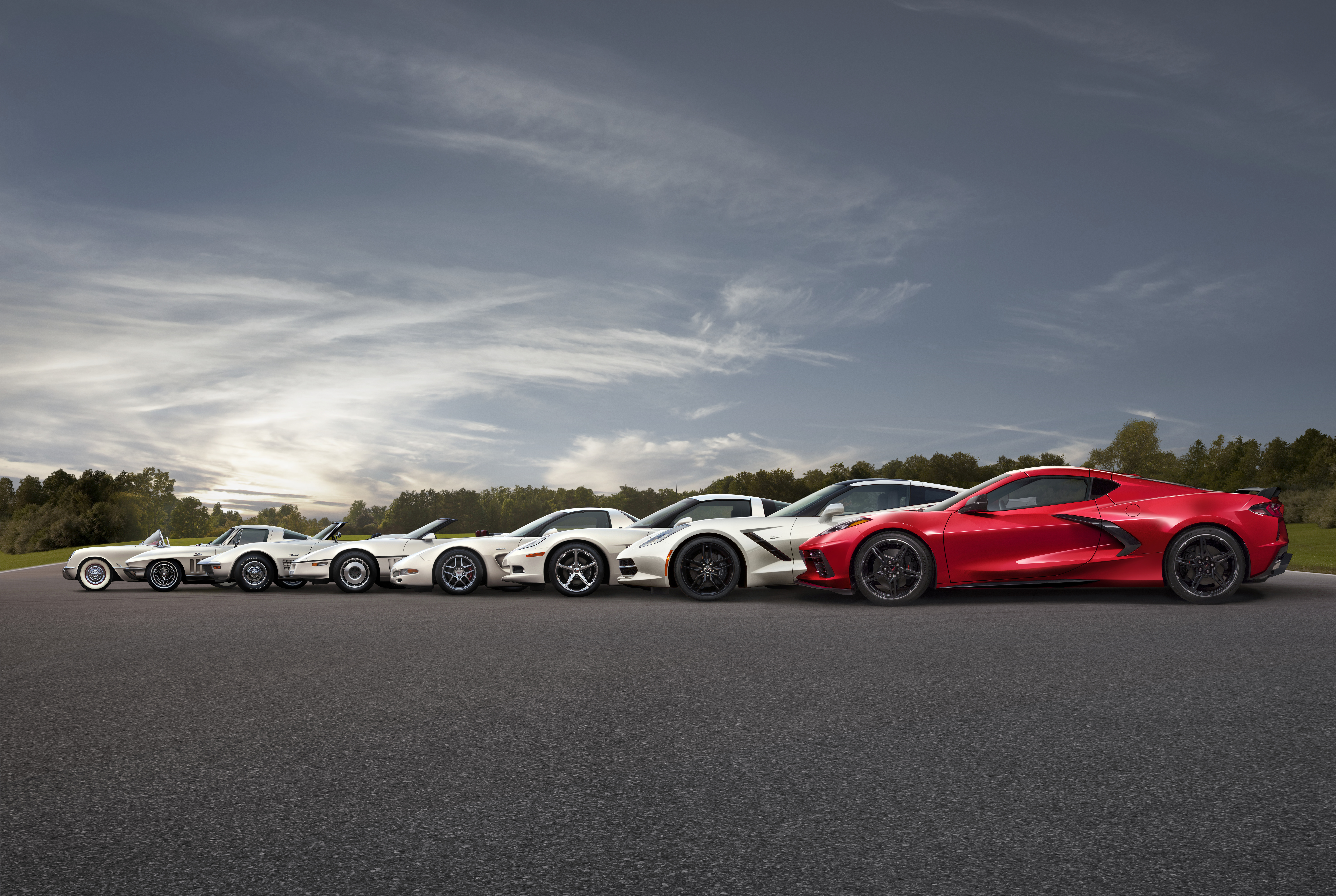
“Por causa do motor central, tínhamos que fazer as coisas de maneira diferente”, explica Ed Moss, Corvette gerente do grupo de engenharia de estrutura corporal. “Desde o início, tivemos muitas discussões sobre como fazer o layout da estrutura corporal. Em um ponto, tudo estava sobre a mesa enquanto discutíamos a melhor maneira de projetar e construir cada sistema. Por exemplo, debatemos metálico versus composto para casas do leme. Se mantivéssemos as casas do leme compostas do C7, teríamos que nos unir ao pilar da dobradiça [Um pilar], que é imediatamente adjacente à roda dianteira em um veículo com motor central, deixando muito pouco espaço na embalagem. Fomos com metal lá. Discutimos até mesmo brevemente painéis de metal versus painéis de corpo composto. No entanto, seria economicamente inviável criar as linhas de estilo do C8 em metais. ”
“Um verdadeiro desafio que enfrentamos foi como lidar com a indução de ar”, lembra Chris Basela, Corvette engenheiro chefe da estrutura da carroceria, explicando a necessidade de um método diferente para canalizar o ar de resfriamento para dentro e através do motor V8 de 6,2 litros de 495 cavalos de potência naturalmente aspirado, que gera 637 Newton-metros (470 libras-pé) de torque. “Nós tentamos todos os tipos de projetos que forçavam o ar a tomar caminhos realmente tortuosos, criando redemoinhos e fluxos que não queríamos. Foi necessário muito trabalho iterativo com a equipe do trem de força para desenvolver o melhor caminho para o fluxo de ar, porque o carro precisa respirar livremente, sem restrições. Também precisávamos acessar a caixa de ar e contornar o espaço traseiro do porta-malas. Outro problema foi o calor e o ruído do motor no habitáculo, porque os ocupantes já não se sentam atrás do motor, mas sim posicionados directamente à sua frente. E estávamos especialmente conscientes da qualidade do ar da cabine, pois as leis haviam mudado na Europa e em outros lugares desde o C7, então trabalhamos muito para reduzir os VOCs [compostos orgânicos voláteis]. ”
“Até mesmo tentando descobrir como montar o carro foi um desafio ”, acrescenta Moss. “Com um projeto de motor dianteiro, você tem um capô comprido e um grande compartimento do motor, proporcionando aos operadores bastante espaço para construir o carro de dentro do compartimento, mesmo com a barra do para-choque dianteiro já soldada. No Corveta com motor central , com seu clipe frontal muito curto, mantemos a frente do carro aberta conforme o veículo é construído e, em seguida, aparafusamos o para-choque dianteiro. ”
“Foi um ato de equilíbrio para obter as formas adequadas, garantindo que nossos fornecedores pudessem produzir as peças e nossa equipe em Bowling Green [GM Corvette com sede em Kentucky montadora] poderia montá-los ”, continua Basela. “No final, havia apenas um composto de transporte do corpo do C7 para o C8.” Este era um composto de moldagem de folha (SMC) resistente de Classe A, gravidade específica 1,2 (SG) desenvolvido para o Corveta 2016 e usado em uma variedade de fechamentos externos no novo veículo.
Arquitetura do veículo
Por quatro gerações (C5-C8), Corvetas apresentam uma estrutura de corpo multimaterial de três camadas:a moldura , geralmente uma mistura de alumínio ou aço - desta vez com uma peça de composto reforçado com fibra de carbono (CFRP); a estrutura corporal , que é composto em grande parte ligado para capitalizar na flexibilidade de design e fabricação; mais fechamentos bolt-on (painéis da carroçaria), que têm sido compostos desde Covette’s Estreia em junho de 1953. Esta estrutura híbrida em camadas não só fornece leveza acessível em grandes volumes de produção - particularmente para carros desta classe de desempenho - mas também permite que várias variantes de veículos sejam produzidas com baixo investimento em ferramentas. Na verdade, para o C8 atual, a GM conseguiu produzir todos os painéis de corpo composto de Classe A (internos e externos ligados) tanto no modelo básico coupé quanto no conversível usando apenas 20 ferramentas.
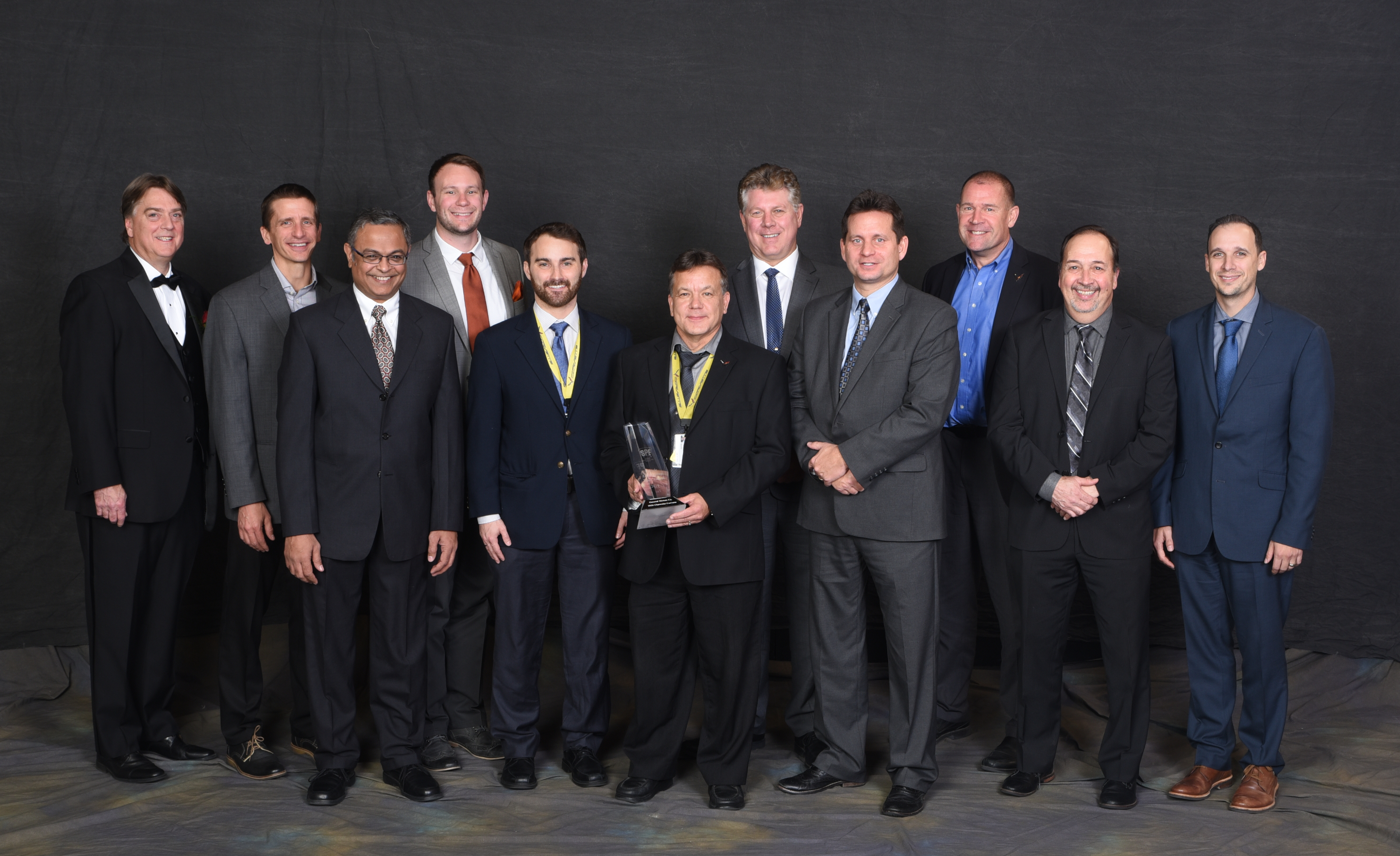
Além disso, Corvetas sempre foram projetados com uma arquitetura de teto aberto, independentemente de serem realmente conversíveis ou coupés com painéis de teto fixos ou removíveis. Como os veículos com teto aberto são geralmente menos rígidos do que aqueles com teto fixo, um foco importante para cada Corveta ’ s engenharia visa sempre criar a base mais rígida possível para melhorar a suspensão e a direção. Historicamente, túneis (transmissões de habitação e eixos de transmissão em veículos com motor dianteiro) dominaram o Corvette estruturas corporais e têm sido os principais capacitadores para alcançar alta rigidez de torção. No caso do novo Corvette , A GM alcançou uma rigidez ainda maior. Com o teto removido, o corpo do C8 é 53,78% mais rígido do que um concorrente de motor central de alto desempenho de referência, 29,27% mais rígido do que um segundo concorrente de motor central de alto desempenho e 13,79% mais rígido do que o C7. Duas peças compostas deram contribuições importantes para a rigidez do veículo - uma diretamente fixada à estrutura do chassi (viga do pára-choque traseiro) e outra fixada à parte inferior da carroceria (fechamento do túnel inferior).
Estrutura do quadro
A estrutura do C8 é em grande parte de liga de alumínio com uma peça CFRP desenvolvida para atender às rígidas metas de dólar por quilograma da GM. Em contraste, o quadro do C7 era todo em alumínio e o C6 era principalmente aço.
A única parte composta diretamente montada no quadro que viaja com o corpo em branco (BIW) através do processo de revestimento eletroforese de ferrugem (que a GM chama de ELPO), é uma viga de pára-choque traseiro de CFRP exclusiva. Esta parte ajuda a enrijecer o quadro e contribui para o desempenho de impacto traseiro. Sua forma curva - possível graças a um novo processo chamado pultrusão de raio desenvolvido por Thomas GmbH + Co. Technik + Innovation KG (TTI, Bremervörde, Alemanha) - permite que ele corresponda às sugestões de estilo traseiro e caiba no espaço limitado da embalagem, mantendo a integridade dimensional próxima ao calor do compartimento do motor. Como a primeira peça pultrudada curva da indústria automotiva (veja nosso artigo completo sobre esta parte na edição CW de maio de 2020), a viga oca de duas câmaras foi produzida pela Shape Corp. (Grand Haven, Michigan, EUA) em equipamentos desenvolvidos e construído por TTI. A viga pesa apenas 1,3 kg e apresenta um olhal de gancho de reboque colado / aparafusado capaz de 25 quilonewtons de força de tração.
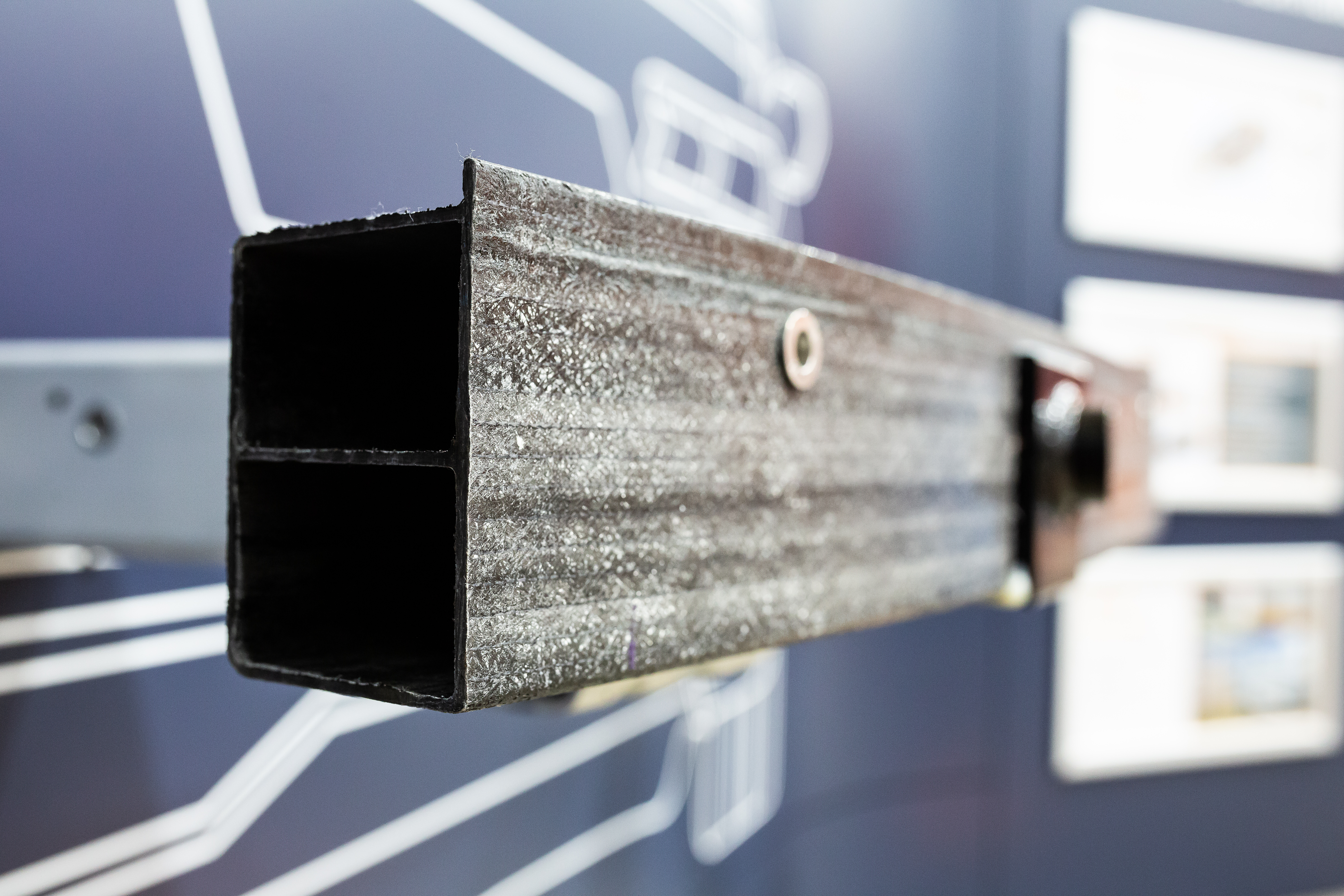
Estrutura do corpo:parte A
Praticamente todos os componentes da estrutura do corpo do C8 são compostos e são unidos e / ou aparafusados ao quadro após o último passar por ELPO. As peças compostas notáveis neste nível incluem fechamentos estruturais da parte inferior da carroceria e o piso - que abordaremos nesta edição - e troncos dianteiros e traseiros, dutos de indução e o entorno traseiro e anteparo - que cobriremos, junto com os painéis da carroceria e acabamento , próximo mês.
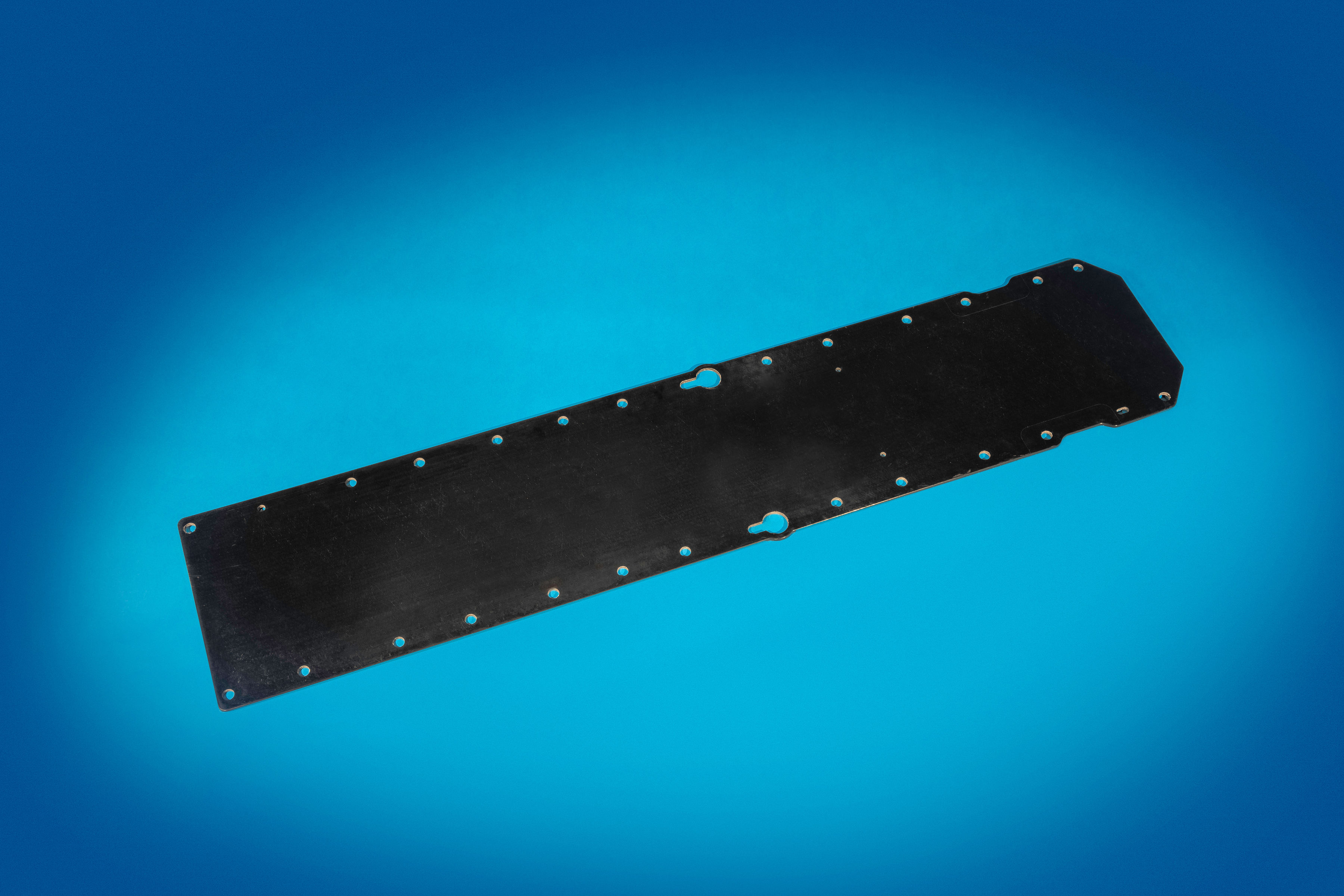
O fechamento estrutural removível do túnel inferior no C8, que atua como uma porta de acesso, contribui com mais de 10% da rigidez torcional do veículo e atua como um caminho de carga primário durante uma colisão. Este painel de composto híbrido consiste em três camadas de pré-forma de fibra de vidro. Eles consistem em fibras contínuas / tecidas e cortadas / aleatórias em uma fração de volume de fibra de 38% (FVF), com véus adicionados às camadas da face superior e inferior em cada pilha para um acabamento superficial aprimorado. As pré-formas de vidro são intercaladas com duas camadas de pré-formas feitas usando fibra de carbono de módulo padrão T700 12K da Toray (Tóquio, Japão) na forma de tecido biaxial NCF a 21% FVF e uma matriz de éster vinílico (VE). O fechamento é produzido pela Molded Fiber Glass Co. (MFG, Ashtabula, Ohio, EUA) usando seu processo proprietário PRiME (Reforço Pré-Posicionado garantindo Excelência na Fabricação), um tipo de moldagem por compressão líquida (LCM).
Além de um único fechamento de alumínio próximo às rodas traseiras que faz parte do berço do motor, os painéis da parte inferior da carroceria restantes consistem em SMC moldado por compressão ou termoplásticos moldados por injeção. Entre outros benefícios, esses painéis reduzem a turbulência e o arrasto da parte inferior da carroceria, melhoram a eficiência do combustível e mantêm a umidade, a poeira e as pedras longe do motor e da linha de transmissão do veículo. Além disso, eles fornecem a base dimensional para várias interfaces externas e internas.
A baixa densidade, mas estrutural Os painéis SMC apresentam novas formulações (neste caso, fibra de vidro cortada 40% FVF / resina de poliéster insaturado (UP)) desenvolvidas pela MFG. O material é chamado de SMC "flutuante" porque a densidade de cada painel é inferior a 1,0 (SG médio =0,97) e, portanto, pode flutuar na água. A MFG produziu todas as peças estruturais SMC e LCM do carro.
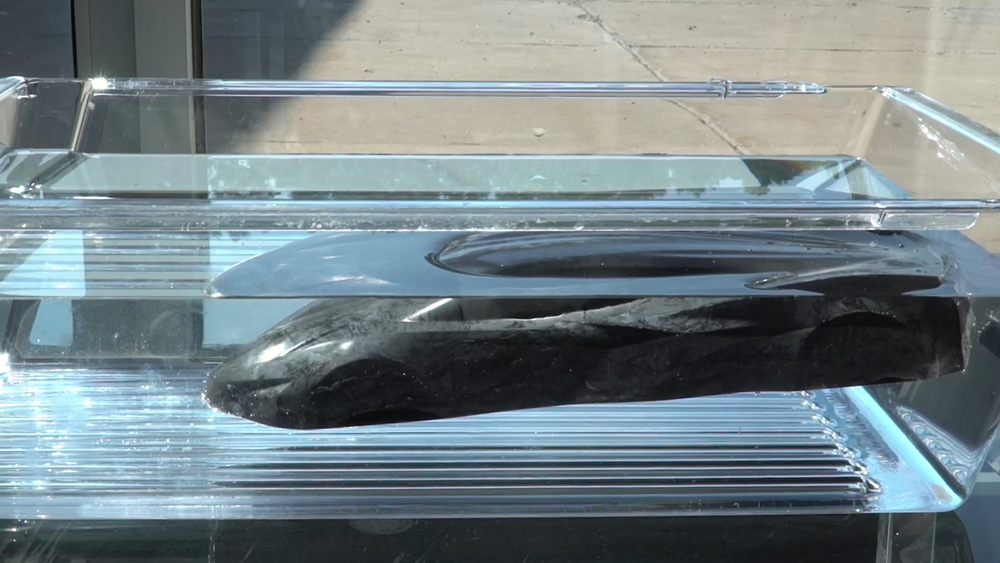
O veículo também apresenta um piso híbrido otimizado para proteção contra impacto de torção e contra impacto nos postes laterais (envolvendo os painéis do balancim e o túnel, ao qual está unido). Os painéis de piso apresentam alumínio estampado voltado para a cabine ligado a folhas de composto 1,5-SG voltado para a estrada (60% em peso de fibra de vidro contínua e tecida / VE) produzida por meio do processo PRiME. Antes de ligar por calor ambas as camadas com o adesivo estrutural de poliuretano Pliogrip 9100 da Ashland Global Holdings Inc. (Wilmington, Del., EUA), o MFG limpa e prepara os materiais.
Todas as peças compostas diretamente ligadas ao quadro C8 são primeiro submetidas a ablação a laser, um processo desenvolvido pela GM, MFG e Adapt Laser Systems LLC (Kansas City, Mo., EUA) para o Corvette 2016, e adaptado de um método da indústria de compósitos para limpeza de moldes. A ablação a laser substitui o lixamento manual e reduz o trabalho, o tempo e os custos, elimina a poeira e melhora a repetibilidade. O caminho do laser, o ângulo de ataque e o nível de energia são personalizáveis para o material e a geometria de cada peça. Para maximizar a flexibilidade de fabricação, toda a parte inferior da carroceria, incluindo o piso, é conectada à estrutura e a si mesma por meio de colagem e parafusos.
Na edição de agosto da CW, continuaremos cobrindo a inovação de compósitos no novo Corvette , retomando com componentes adicionais ao nível das estruturas da carroceria e terminando com fechamentos externos (painéis da carroceria), além de acabamentos adicionais e atualizações. Veja a Parte 2.
Resina
- 10 vantagens da computação em nuvem em 2020
- O futuro da impressão 3D:12 principais conclusões da AM Landscape Digital Conference 2020 da AMFG (Parte 1)
- Liderança de manutenção, Parte 3
- Introdução aos harmônicos:parte 1
- Sustentabilidade na fabricação - Parte 3
- Tendências e desafios de 2020 impactados pelo Covid-19:Parte I
- O giro é opcional
- O que é um número de peça?
- Usinagem de peças pequenas
- Cilindricidade em GD&T