Passeio pela fábrica:Holland Composites, Lelystad, Holanda
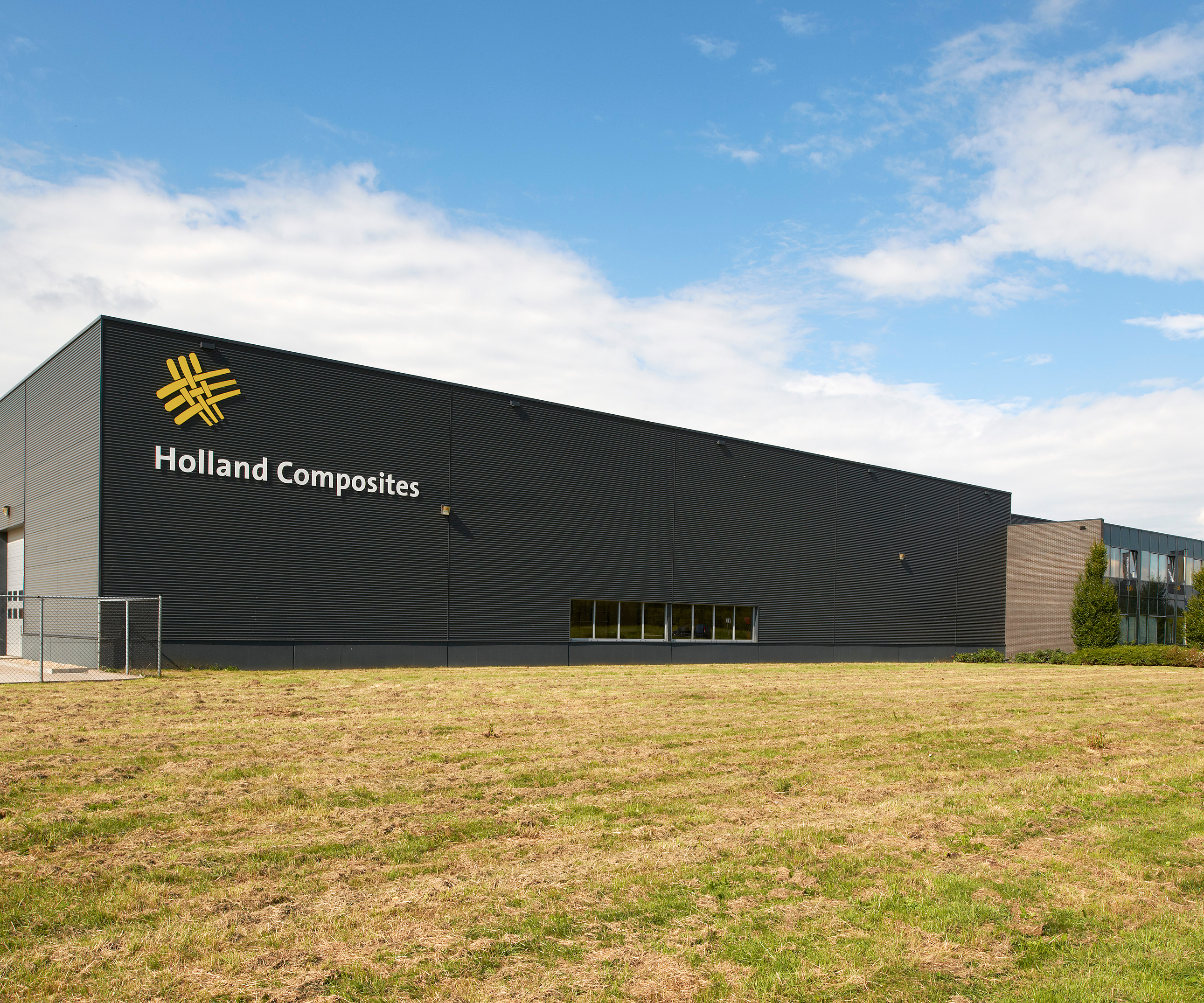
Foiling catamarãs, construção de fachadas e muito mais. Localizada a menos de uma hora de carro de Amsterdã, a Holland Composites desenvolve uma ampla variedade de projetos altamente técnicos em seus 4.500 m 2 instalação. Fonte, todas as imagens | Holland Composites
Localizada em um edifício de 4.500 metros quadrados, a menos de uma hora de carro de Amsterdã, a Holland Composites (Lelystad, Holanda) concentra-se em quatro mercados:marítimo / offshore, arquitetura, energia renovável e projetos especiais. A Holland Composites usa uma mistura de polímero reforçado com fibra de carbono prepreg (CFRP) e favo de mel Nomex para peças altamente carregadas e infusão de resina e fibra de vidro para a indústria de construção e projetos de margem inferior. “Ainda somos capazes de obter alto desempenho, mesmo com essas construções mais econômicas, e mantemos baixa sobrecarga para as peças que usam materiais avançados”, disse Sven Erik Janssen, sócio-gerente da Holland Composites, junto com o fundador Pieterjan Dwarshuis. “Isto é único.”
A empresa também opera a marca DNA Performance Sailing, produzindo veleiros multihull foiling, incluindo o catamarã F1X de 5,5 metros, o trimarã TF10 de 11 metros e o catamarã F4 de 14 metros. O catamarã G4 de 12 metros não está mais em produção, “mas mostra nossas capacidades para construção avançada de iates compostos e alto desempenho”, observa Janssen. “Este barco é um piloto de dupla finalidade e um cruzeiro familiar com beliches, cozinha e cabeceira, mas atinge uma velocidade de mais de 35 nós. A capacidade de frustrar com mais de 4.000 quilos de peso e apenas uma tripulação de seis pessoas - ainda não há competição neste campo, exceto em iates multibilionários da America’s Cup ”.
Transporte marítimo para rodoviário e aéreo
Antes de o tour começar, Janssen conta a história da empresa e as estruturas compostas que ela produz. A Holland Composites foi formada em 1992 por Janssen e Dwarshuis, que eram, na época, alunos da Universidade Técnica de Delft (TU Delft, Holanda). Eles construíram mastros de fibra de carbono para catamarãs Hobie, um iate de 18 metros usando CFRP e favo de mel Nomex em 1993 e um iate de 100 pés usando processamento de infusão de resina em 1994. “Naquela época, tudo o que estávamos construindo era feito de fibra de carbono usando pré-impregnado ou infusão ”, lembra Janssen. No entanto, ele acrescenta, como o negócio estava sujeito aos altos e baixos típicos do mercado marítimo e a projetos pontuais, “Procuramos diversificar, mas queríamos nos manter em compósitos avançados versus FRP [ou seja, fibra de vidro menos avançada, mais commodity e resina de poliéster]. ”
A empresa começou a explorar soluções leves para o transporte rodoviário, produzindo 35 reboques de caminhão com chassis monocoque composto de fibra de vidro / carbono, que reduziu o peso em 3.500 quilos. “Os caminhões transportavam cargas densas, como batatas, e atingiam o peso máximo antes de preencher o volume”, explica Janssen. A Holland Composites também fabricava reboques refrigerados, acrescenta ele:“Mas chegamos um pouco cedo; o mercado ainda não estava pronto - as empresas ainda não eram capazes de calcular os ganhos anuais com o transporte de mais carga e economia de manutenção dos reboques compostos em comparação com seu custo inicial mais alto ”.
Quase ao mesmo tempo, a VRR (Rotterdam, Holanda), fornecedora de soluções personalizadas de carga aérea, abordou a empresa. “Eles estavam trabalhando para a Airbus, Boeing e as companhias aéreas”, lembra Janssen. “Desenvolvemos um contêiner leve com um monocoque de composto de fibra de carbono / aramida, que ainda não tem baixo peso hoje”, diz ele. Embora a Holland Composites fizesse alguns milhares desses, o mercado rapidamente ficou saturado com produtos de FRP de baixo custo.
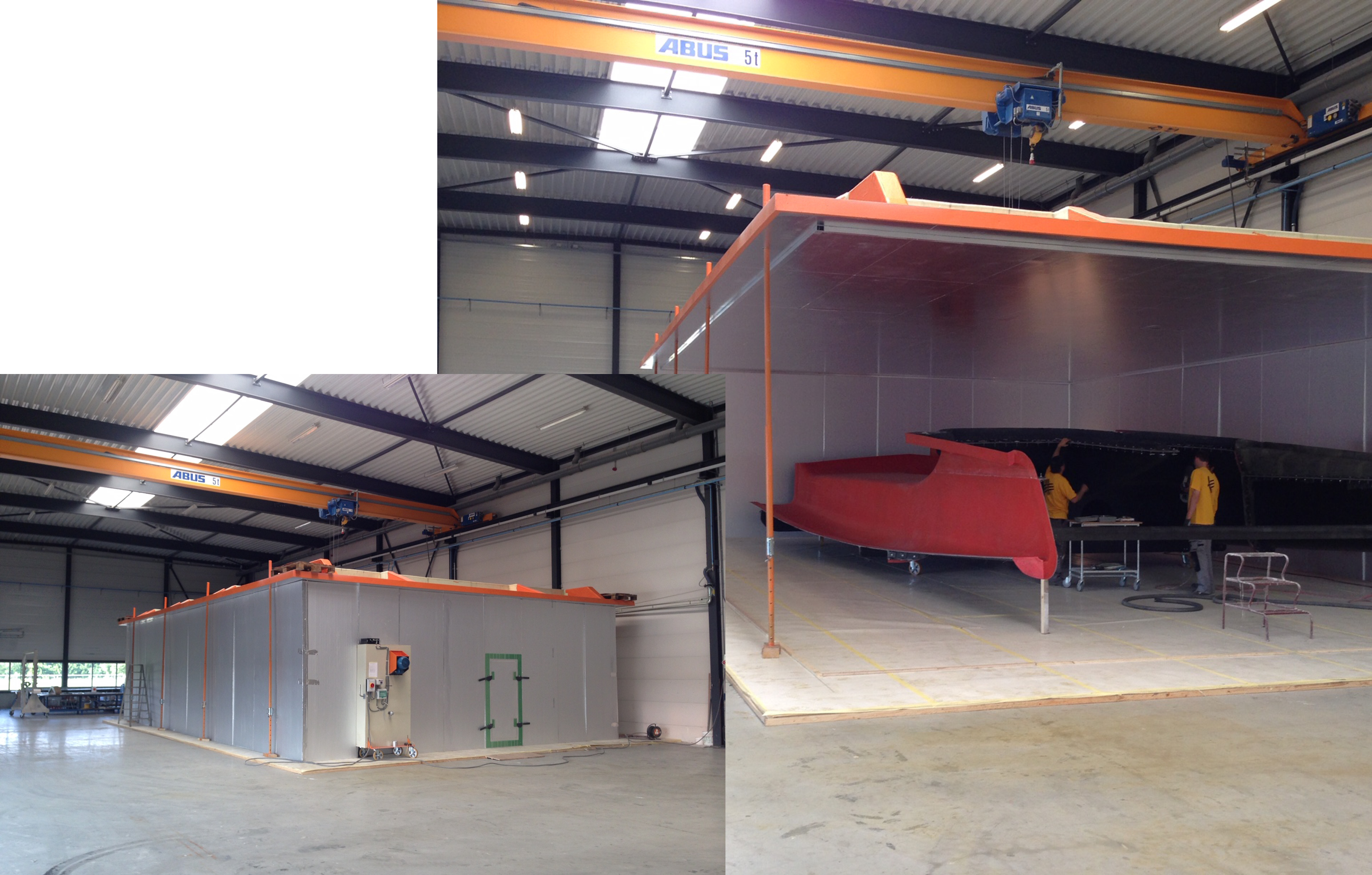
Estruturas curadas com OOA. Grandes estruturas compostas de carbono para sua marca DNA Performance Sailing de veleiros multi-casco de foiling são curadas em fornos flexíveis (direita) compreendendo painéis isolados com aquecimento e circulação de ar controlada por computador a partir de uma unidade externa (inserção).
Marinha continua sendo um ponto forte
Em 1999, a Marinha holandesa abordou a Holland Composites para produzir domos de sonar de fibra de vidro sólida para submarinos. “Eles eram tradicionalmente construídos em duas metades que eram unidas”, diz Janssen, “mas a costura causa uma interrupção no campo de‘ visão ’. Fomos solicitados a construí-los inteiros. Essas cúpulas de sonar são grandes - 11,5 por 3 por 3 metros e 45 a 110 milímetros de espessura - e difíceis de infundir, compreendendo 5.000 quilogramas de resina híbrida de éster de vinil / epóxi fornecida pela Romar-Voss Composites (Roggel, Holanda). A estrutura finalizada pesa 6.500 quilos. Eles devem ser rígidos e resistir a cargas de impacto, pois estão localizados na seção dianteira do casco. “Também temos que igualar a densidade e a transparência do sonar da água”, diz Janssen. “Fazemos isso para navios do tipo destruidor de algumas forças navais em todo o mundo.”
Na outra extremidade do espectro de peso estão os multihulls de controle de desempenho de DNA. “Nossos pequenos barcos foram os primeiros catamarãs a vencer em competição”, afirma Janssen. A Holland Composites também produz hidrofólios compostos para iates de corrida que estabeleceram recordes, como o MOD70’s Team ARGO e Beau Geste . “Temos uma técnica interna que pode criar peças realmente altamente carregadas sem falhas e um método de produção único para essas folhas de alto desempenho”, acrescenta. “Trabalhamos com os melhores velejadores do mundo para alcançar o próximo nível de desempenho de florete e produzir todos os floretes para os barcos da classe Olímpica NACMA17.”
A casa de convés CFRP leve que a Holland Composites produz para embarcações de serviço / apoio de parques eólicos Windcat Workboats (consulte “Compósitos de convés de corte de peso”) usa construção em sanduíche de espuma CFRP com infusão de resina para obter rigidez e alcançar um vão grande e aberto sem pilares dentro da cabine. “O convés monocoque é leve o suficiente para que possamos colocá-lo em bons amortecedores para isolá-lo do motor e da vibração das ondas no casco”, diz Janssen. “O Windcat é conhecido por seu passeio realmente silencioso e os barcos são muito apreciados pelos grandes fabricantes de turbinas eólicas. Todos esses parques eólicos devem ser mantidos, para que haja um novo mercado para catamarãs de alta velocidade de 50 a 60 pés de comprimento. ”

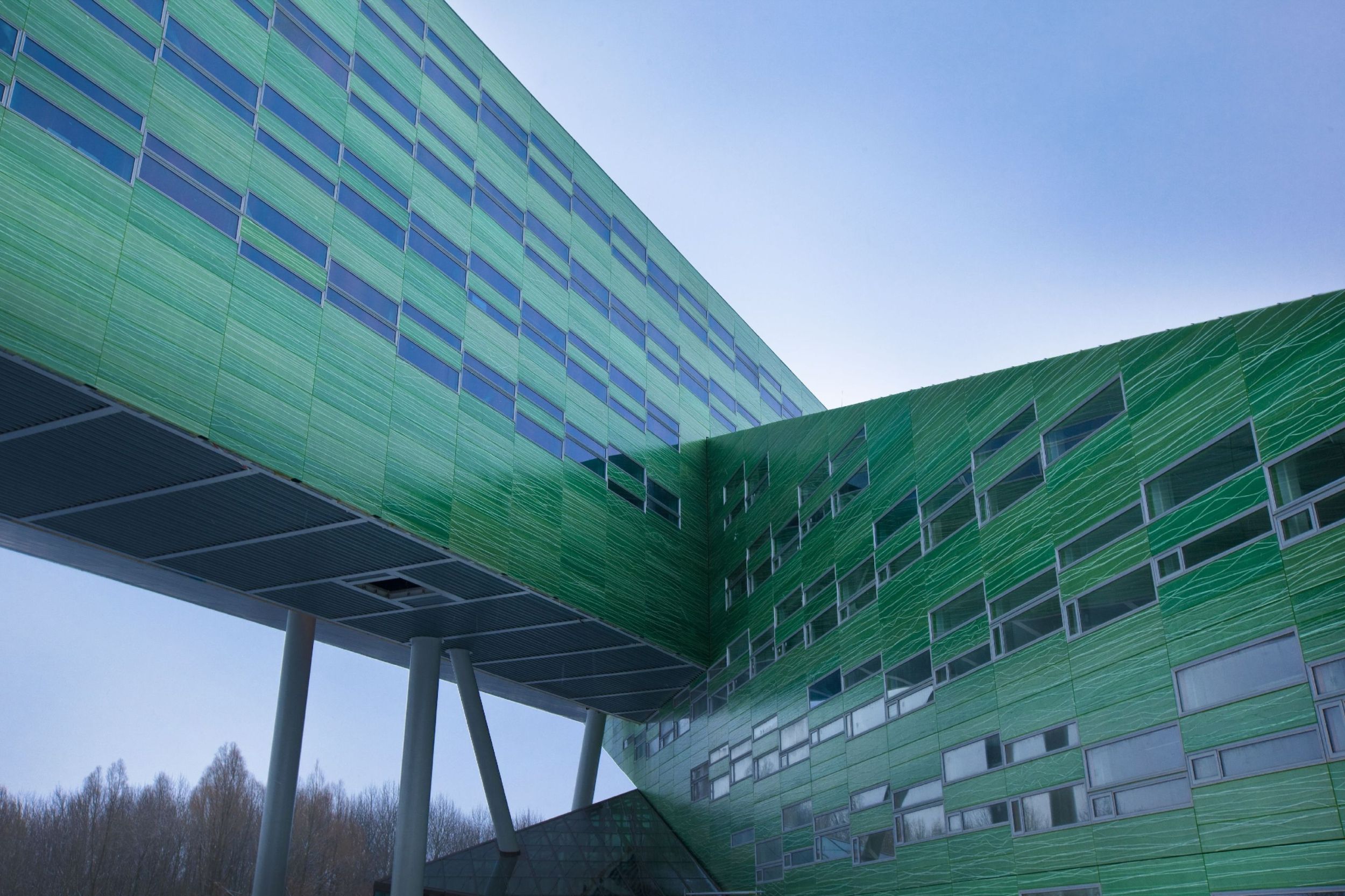
Holland Composites forneceu a fachada composta estrutural para a University of Groningen Life Prédio de ciências, usando seu sistema de painel translúcido RAFICLAD e tamanhos de painel grandes (3,6 por 3,3 metros), conseguindo economia de peso e máximo isolamento térmico.
Setenta e cinco seções compostas de 40 por 60 metros foram enviadas para Israel, laminadas juntas e içadas no lugar para criar as seções do telhado em forma de asa para o Centro Yitzak Rabin em Tel Aviv.
“Tudo o que fazemos é estrutural”
Para o Yitzak Rabin Center (Tel Aviv, Israel), a empresa foi solicitada a construir estruturas de telhado em forma de asa que seriam muito pesadas se feitas de concreto. “Mais uma vez, criamos as maiores seções possíveis”, diz Janssen. Setenta e cinco seções de 40 por 60 metros foram infundidas com resina usando fibra de vidro e resina de éster de vinil à base de epóxi e, em seguida, enviadas para Israel. No local, eles foram colocados de cabeça para baixo em gabaritos para laminá-los juntos em “telhados de asa” com vão máximo de 31 metros. Janssen observa que o projeto foi muito desafiador estruturalmente. “Esses painéis têm 200 a 300 milímetros de espessura e mantêm a fachada de vidro unida, incluindo uma seção cantilever de 11 metros. O material composto pode suportar todas as forças, dando a você a possibilidade de projetar vãos de telhado suspensos. ”
A torre do Fletcher Hotel é outro projeto, concluído em 2012-2013. Começou como um shopping center próximo a uma rodovia, mas exigiu uma atenuação acústica substancial na estrutura após a decisão de converter o prédio em um hotel de alto padrão. “O esqueleto de concreto não suportava muita carga adicional, por isso fomos chamados para fornecer uma solução leve”, diz Janssen. A Holland Composites desenvolveu painéis compostos de 8,5 por 3 metros nos quais a fachada de vidro plano poderia ser fixada. “O vidro fica pendurado em nossos painéis, o que ajuda a lidar com a carga”, ressalta. “Em seguida, prendemos nossos painéis ao esqueleto de concreto. Esta combinação do vidro na frente dos painéis sanduíche compostos com o entreferro cria uma enorme barreira acústica. ” Cada painel composto estava pronto para pintura para as paredes internas de um lado e acabado com revestimentos resistentes aos raios ultravioleta no lado externo voltado para o vidro.
“Essa também foi uma maneira muito rápida de montar o revestimento em um edifício de formato redondo”, diz Janssen. “Montamos a fachada completa em uma etapa e alcançamos um valor de R de isolamento de 8, que é o dobro da classificação dos materiais exteriores normais de construção. ” Expandindo essa ideia, Janssen diz que acredita que a neutralidade energética é crítica para a construção de edifícios futuros. “Não é necessária muita energia para aquecer os edifícios que usam nosso revestimento de composto estrutural, portanto, nossa abordagem é muito eficiente para atingir uma pegada líquida zero. BREEAM é a certificação holandesa para eficiência energética, e os dois primeiros edifícios que alcançaram isso usam nossos compósitos. ”
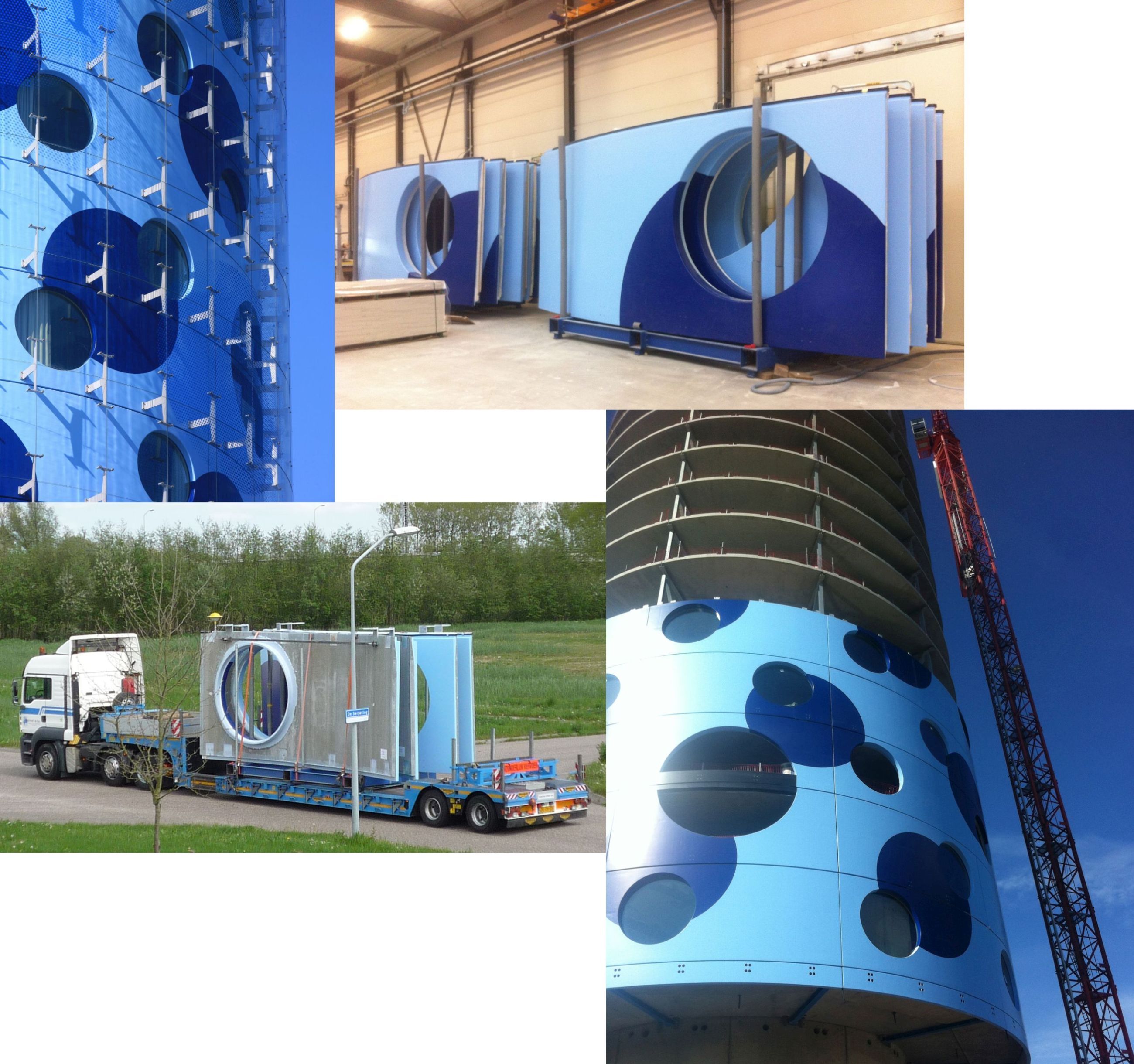
Para o Fletcher Hotel, a Holland Composites percebeu um exterior estético com redução de ruído ao anexar painéis compostos curvos ao esqueleto de concreto do edifício, ao qual a fachada de vidro poderia ser fixada sem adicionar carga morta excessiva.
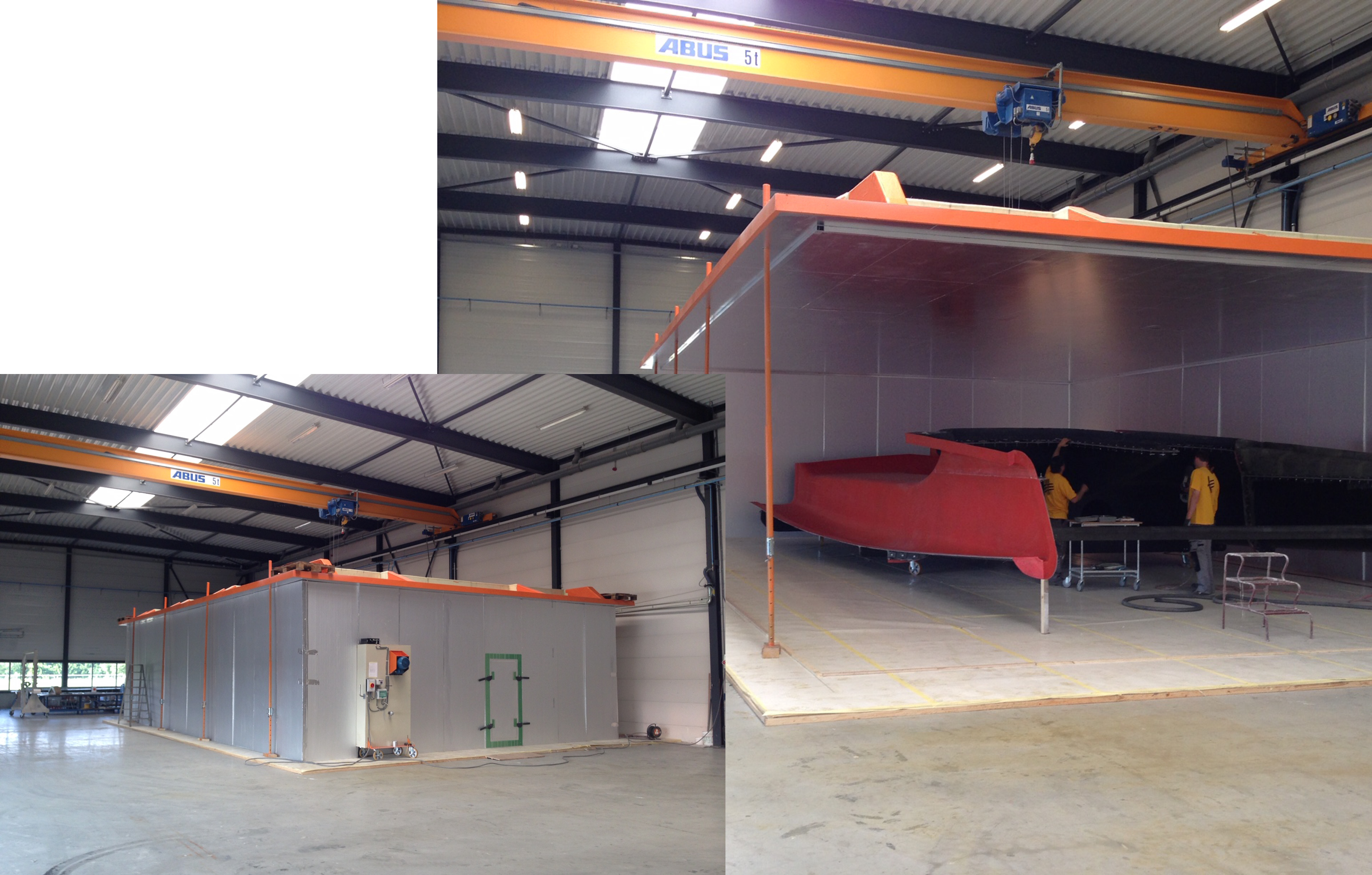
Janssen destaca o Museu Stedelijk de arte contemporânea no centro de Amsterdã como o pináculo dos projetos de construção técnica da Holland Composites (consulte “Grande museu, grandes estruturas”). “Foi um exercício extremo de gestão da expansão térmica e ilustra o que fazemos.” A Holland Composites também foi pioneira em fachadas estruturais à prova de terremotos, que agora são exigidas em certas partes da Holanda, explica Janssen, porque o solo foi desestabilizado devido ao fraturamento hidráulico (fracking). O edifício Wiebenga em Groningen apresenta uma fachada à prova de terremotos que pode se mover 30 centímetros sem falhar. “O aço e o concreto típicos não suportam esse tipo de movimento”, acrescenta.
Embora equilibrar a miríade de requisitos com custo e cronograma seja um desafio ao construir estruturas, Janssen observa que o maior problema atualmente é a resistência ao fogo. “Implementações erradas de compósitos trouxeram uma má reputação à indústria de compósitos a este respeito ”, explica ele. “Agora usamos apenas materiais resistentes ao fogo nesses projetos de construção e testes completos de incêndio de acordo com os regulamentos aprovados.”
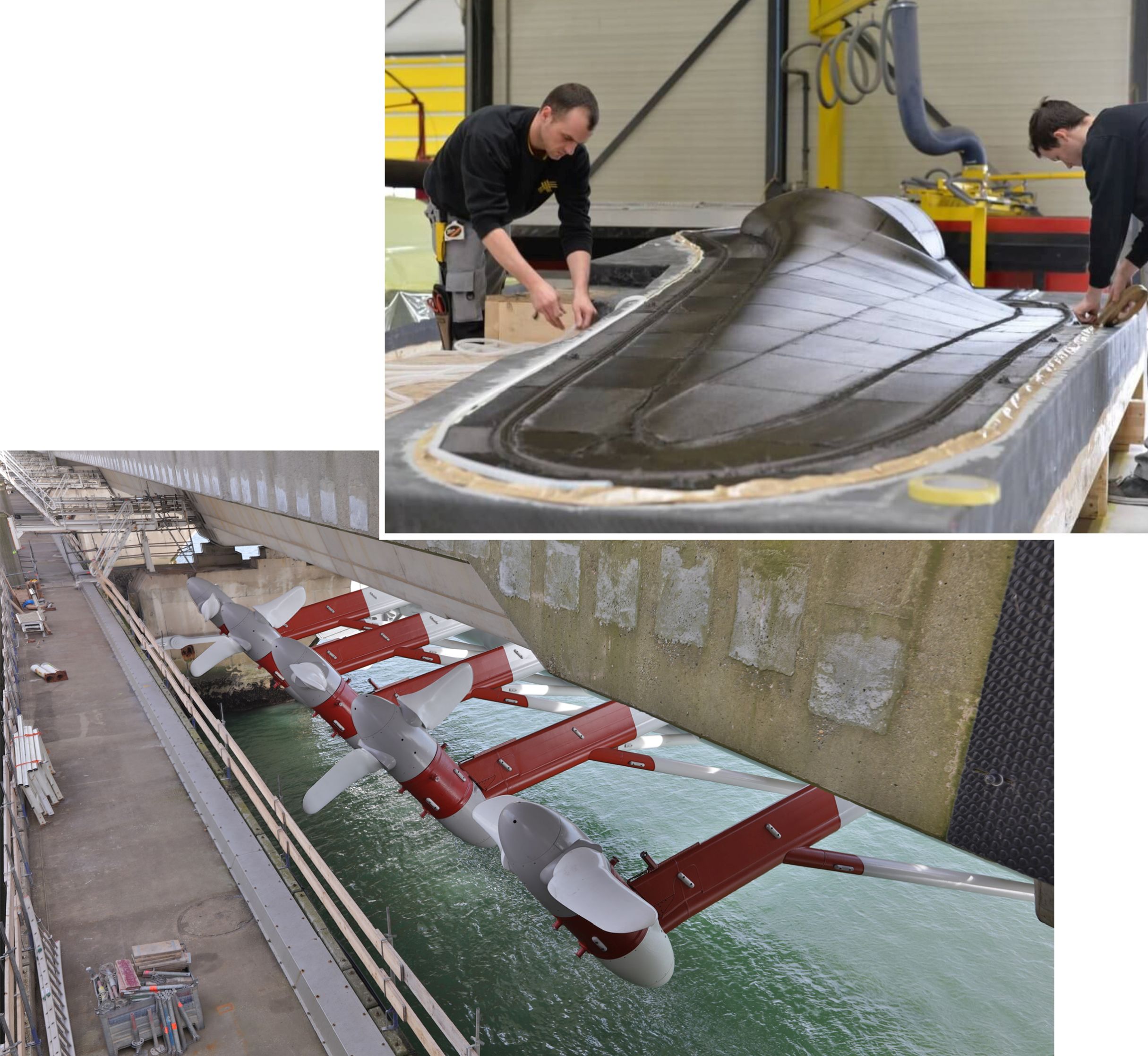
A Holland Composites constrói lâminas para geradores de turbinas de marés usando pré-impregnado de fibra de carbono, curado em autoclave, para lidar com as grandes cargas colocadas nessas estruturas de baixa velocidade e alto torque.
Offshore e energia renovável
A Holland Composites também tem contratos de longo prazo na indústria de petróleo e gás offshore. “Os compósitos aqui oferecem não apenas leveza e resistência à corrosão, mas também fácil reparo”, diz Janssen. “Plataformas e embarcações offshore não têm tempo de inatividade permitido. No entanto, o reparo de estruturas metálicas requer soldagem e faíscas, portanto, a produção deve ser interrompida devido ao risco de incêndio. Podemos corrigir as composições sem essa interrupção. ” A empresa tem novos clientes solicitando esses produtos para uma variedade de construções offshore.
Também fabricou lâminas para turbinas de maré. A captação de energia das marés ainda é nova, diz Janssen, mas os primeiros projetos foram concluídos e os resultados são impressionantes. “As turbinas de maré oferecem uma fonte de energia confiável”, explica ele. “As marés estão sempre lá, em comparação com a eólica e a solar, então você pode prever a produção de energia com segurança, o que é fundamental para as empresas de energia.” A Holland Composites usa pré-impregnado de fibra de carbono curada em autoclave para essas lâminas porque as cargas são enormes. “As lâminas se movem em baixa velocidade, mas com alto torque”, diz Janssen. “Você quer a tradução máxima da velocidade do rotor no motor para produzir energia, então os fabricantes de turbinas precisam de estruturas fortes, mas eficientes, que são moldadas para obter o máximo de energia possível dos movimentos das marés.”
Cada turbina tem duas lâminas de 3 metros de comprimento e 18 milímetros de espessura. Existem cinco turbinas por gerador de marés. “A carga nessas lâminas da turbina é descrita como igual a um rebocador de 13.600 cavalos de força indo para a frente com força total”, diz Janssen, “mas o cliente também precisa de lâminas que sejam rígidas, leves e de baixa manutenção com boa resistência à fadiga para durabilidade. O aço seria muito pesado, tornando os geradores menos eficientes. ” A Holland Composites fabrica apenas as lâminas; carenagens, cone do nariz e revestimento não estrutural são feitos por fabricantes de FRP.
Instalação orientada para o futuro
O passeio começa na área de layup, que apresenta uma grande mesa de layup, peças para os veleiros de desempenho de DNA e uma variedade de lâminas de CFRP sendo preparadas para instalação. O teto é baixo aqui por causa de um mezanino para armazenamento de materiais. Isso se abre para um piso de produção de teto alto, com uma máquina de corte automatizada Zünd (Altstätten, Suíça) logo além da área de layup. O cortador tem uma faixa de corte de 5,7 por 2,8 por 0,3 metros para processar materiais prepreg, fibra seca e espuma de até 25 milímetros de espessura.
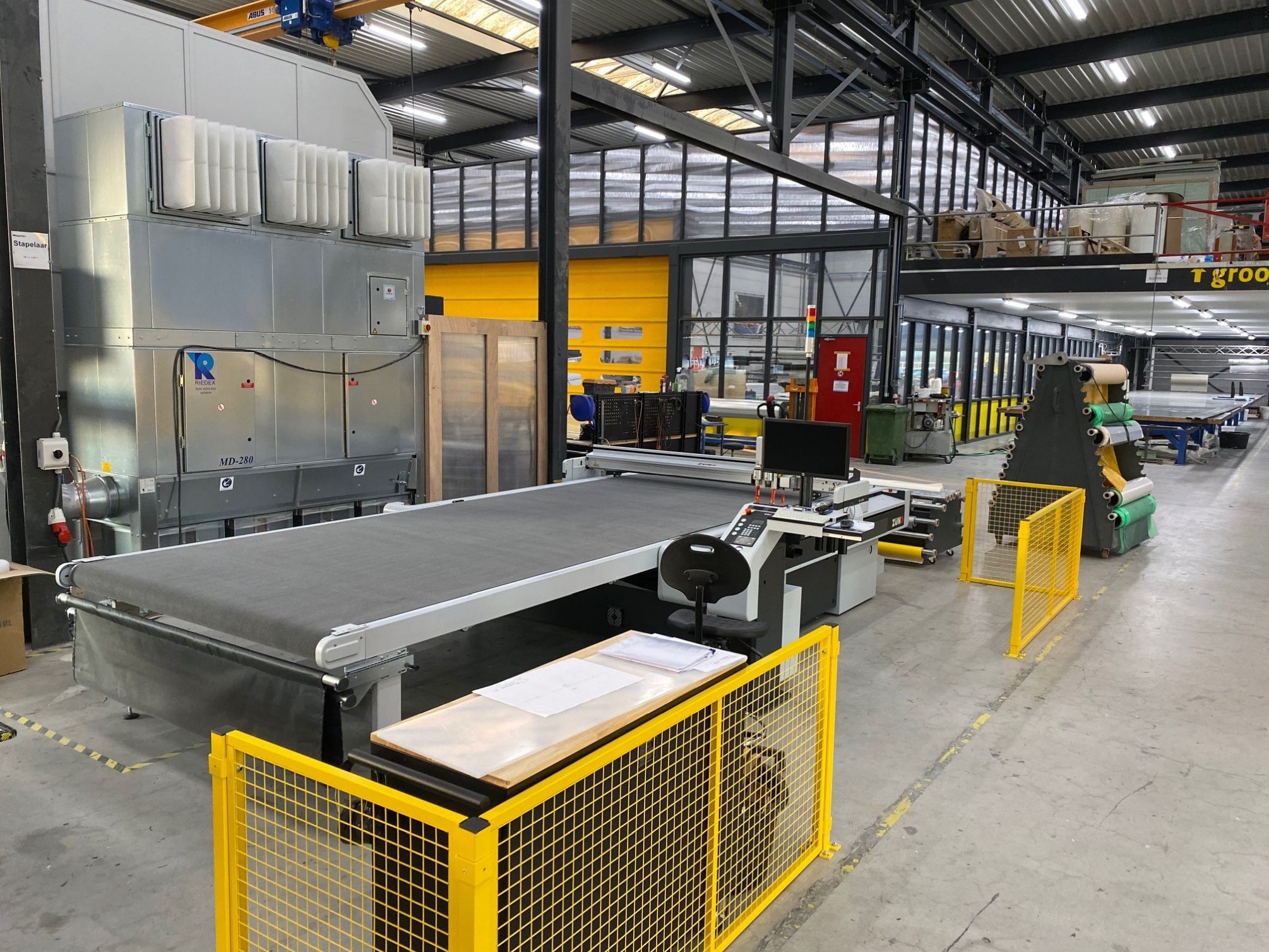
A cortadora automatizada Zünd em primeiro plano fornece reforços de corte e espuma para a área de layup, que pode ser vista na parte traseira, à direita, com o mezanino de estocagem de materiais acima. A área de usinagem fechada fica atrás da porta de enrolar amarela, vista aqui atrás da lateral do centro de usinagem CMS, que fica ao lado da mesa de corte Zünd.
Afastando-nos do cortador Zünd, caminhamos para uma sala de ferramentas envolta em vidro que confina com a área de armazenamento. Entrando por uma porta amarela de enrolar, várias ferramentas estão sendo processadas e as peças estão sendo curadas em sacos a vácuo. “Nós fazemos nossos próprios moldes”, diz Janssen. “Para peças de CFRP, usamos CFRP ou alumínio para as ferramentas, bem como orifícios de ventilação para a circulação de ar dentro das ferramentas, o que ajuda a garantir uma cura uniforme em toda a peça.”
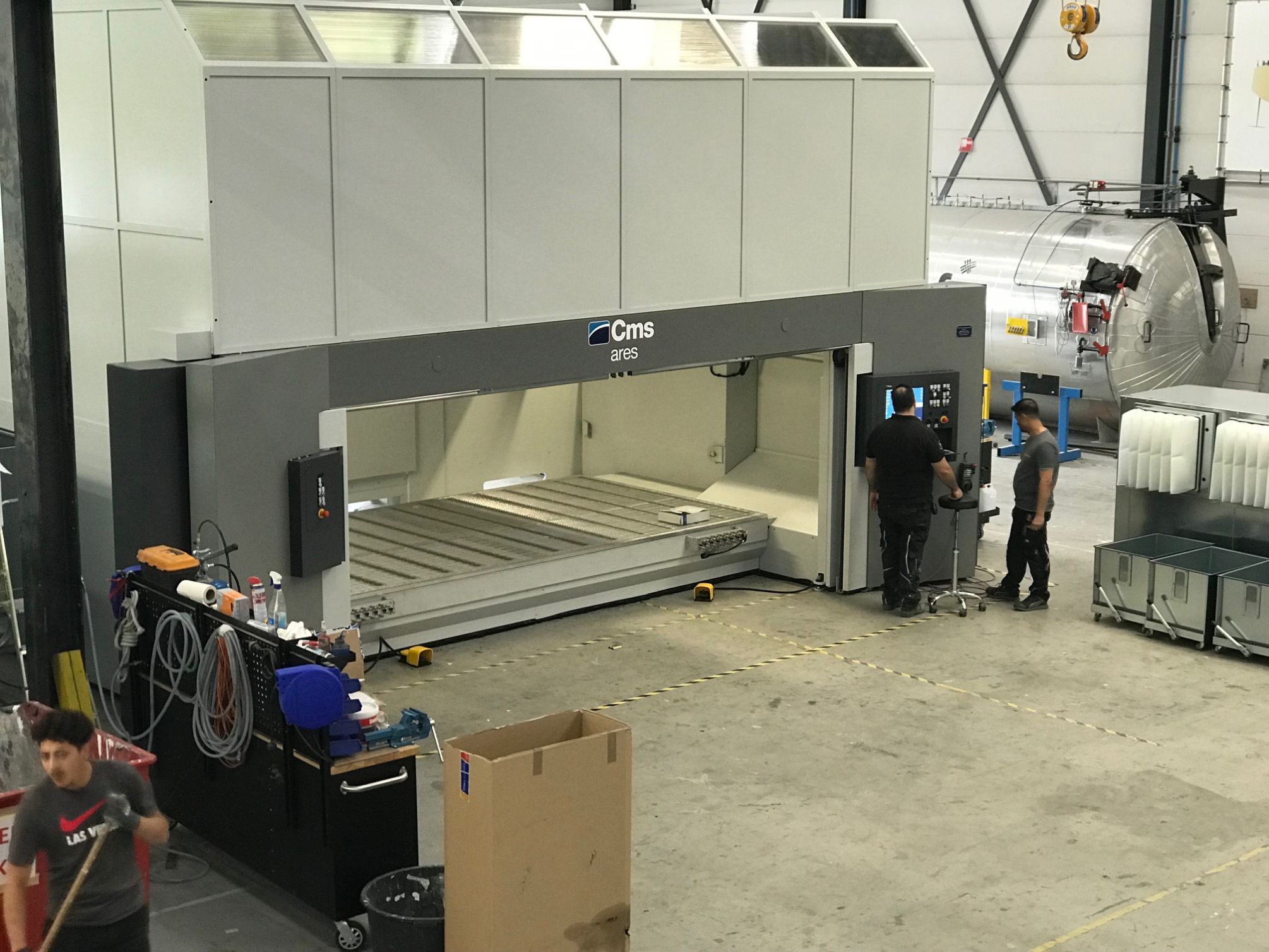
O centro de usinagem CMS está situado entre a mesa de corte à sua esquerda (fora de vista) e a autoclave (extrema direita, contra a parede).
Ao sair da sala de ferramentas, passamos pelo centro de fresamento CNC de 5 eixos 5 por 2 por 1,8 metros (CMS SpA, Zogno, Itália) e podemos ver a autoclave de 6,5 por 2,2 metros (Tankbouw Rootselaar, Nijkerk, Holanda). “Normalmente curamos a 125 ° C com pressão de 6 bar ”, observa Janssen.
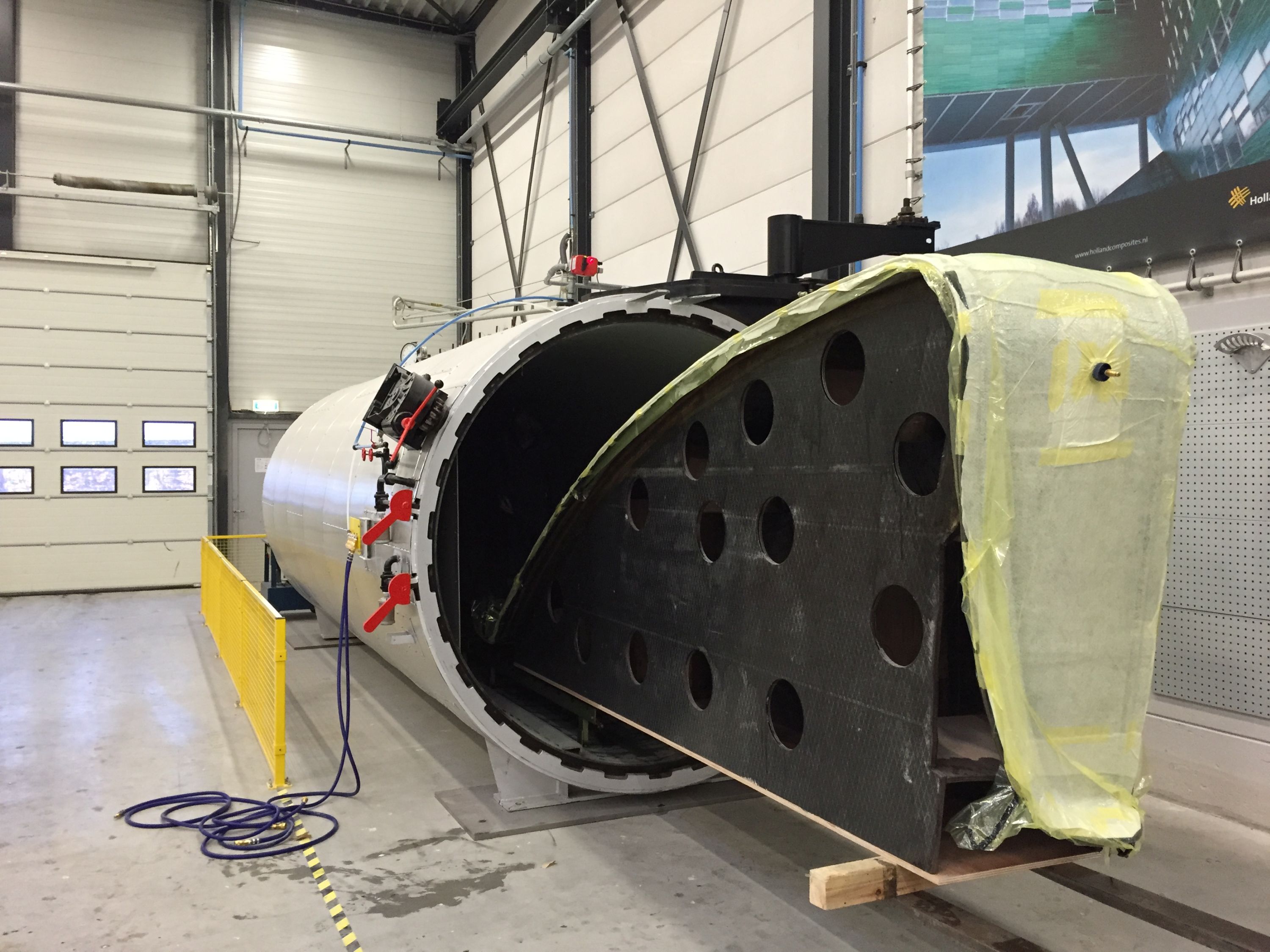
A autoclave também é vista abaixo com uma ferramenta de CFRP (observe os orifícios para ventilação de ar) e uma grande folha de CFRP sendo curada sob um saco a vácuo para um veleiro multihull de alto desempenho.
A parede ao lado da autoclave corta a área de produção em duas metades, percorrendo o comprimento do edifício ao longo da sala de ferramentas. Damos meia-volta e passamos por uma porta para a segunda metade das instalações da Holland Composites, que contém uma máquina de corte por jato de água (faixa de corte de 8 por 2 por 0,5 metros), vários fornos de até 15 por 10 por 3,5 metros e a cabine de pintura da empresa de 19 por 12 por 3,5 metros. “Atualmente, estamos produzindo grandes painéis para um projeto no Catar e uma série de decks de CFRP para os barcos Windcat”, diz Janssen.
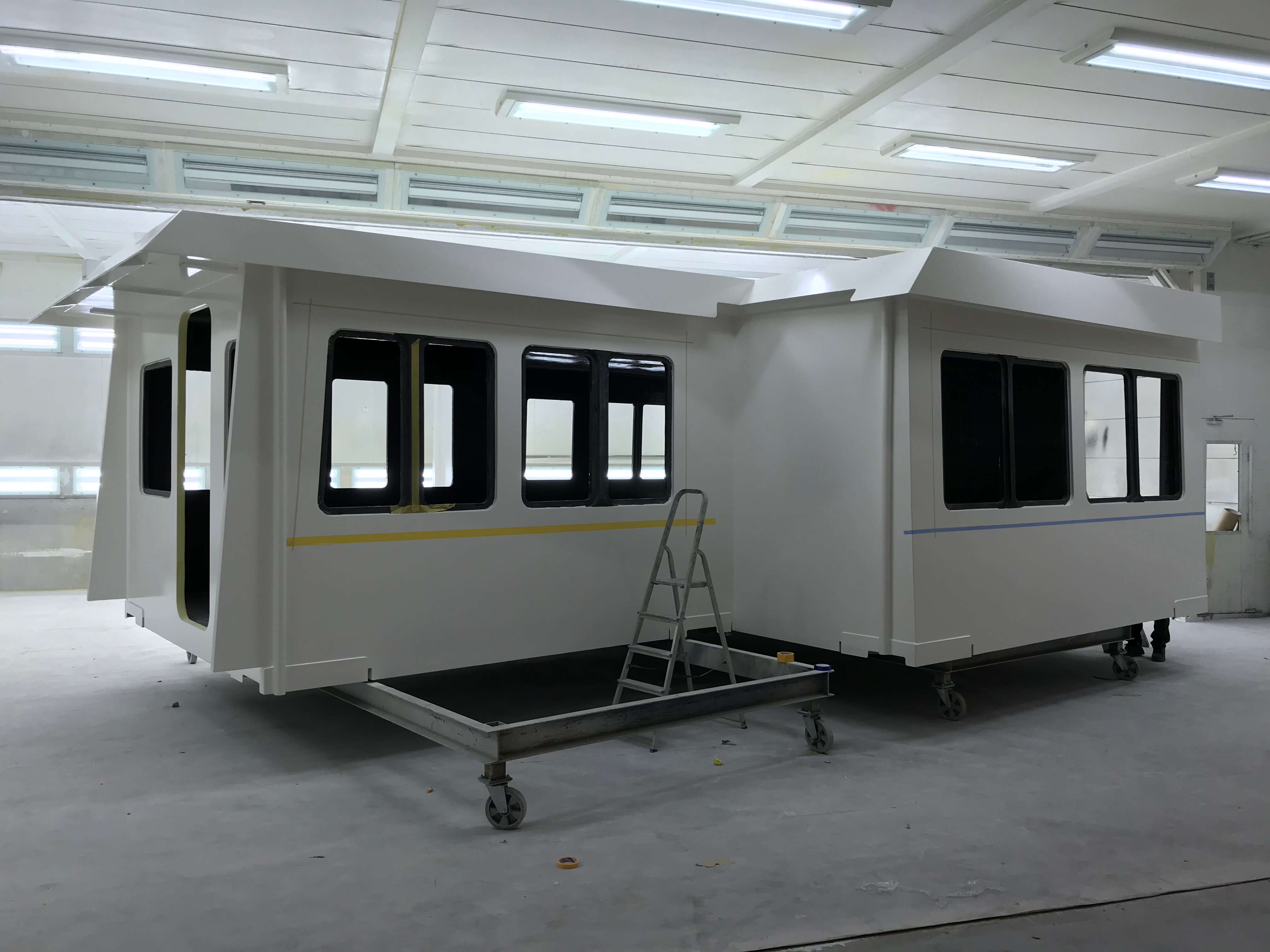
Os decks de CFRP que a Holland Composites produz para os catamarãs Windcat Workboats são pintados na cabine de pintura da empresa de 19 por 12 por 3,5 metros.
A última instalação da Holland Composites é uma impressora Massivit 3D (Lod, Israel) 1800 Pro com um volume de construção de 145 por 111 por 180 centímetros. “Somos parceiros inovando a impressão 3D de moldes usando três cabeças de impressão, onde duas estão imprimindo as películas de um sanduíche e o bico central imprime o enchimento ou estrutura de treliça entre eles”, explica Janssen. “Usaremos material reforçado com fibra em desenvolvimentos futuros, mas por enquanto, podemos imprimir ferramentas precisas com o mínimo de fresamento necessário. Usamos muito menos material e temos tempos de produção de moldes muito rápidos. Agora temos uma cadeia de processo completa, com a capacidade de ir do design aos moldes e às peças pintadas em um curto período de tempo. ”
Ele observa que a empresa ainda está explorando como aumentar o uso da automação para avançar ainda mais em seus produtos, mas sem aumentar os custos. “Tudo se resume à engenhosidade. Somos atraídos por problemas altamente complexos que poucos ousam resolver, mas, como construtores de barcos, sempre tivemos que ser muito criativos com recursos limitados. Para o que fazemos em compósitos, vemos muitas oportunidades no futuro. ”
Resina
- Os fabricantes visitam a United Safety for Plant Tour, discussão de melhores práticas
- CompositesWorld SourceBook 2022
- Resolução de problemas de termoformação de compósitos termoplásticos
- A evolução dos compostos aditivos
- Compostos termoplásticos:Suporte de pára-choque estrutural
- Compostos como reforços da carroceria
- Holanda para mostrar a experiência de compósitos do país no JEC World 2019
- TPAC e TPRC desenvolvem processo de reciclagem de compósitos termoplásticos
- Compósitos termoplásticos de soldagem
- Compostos de alto desempenho em Israel