Remoção de barreiras para diminuir o peso de navios com compósitos
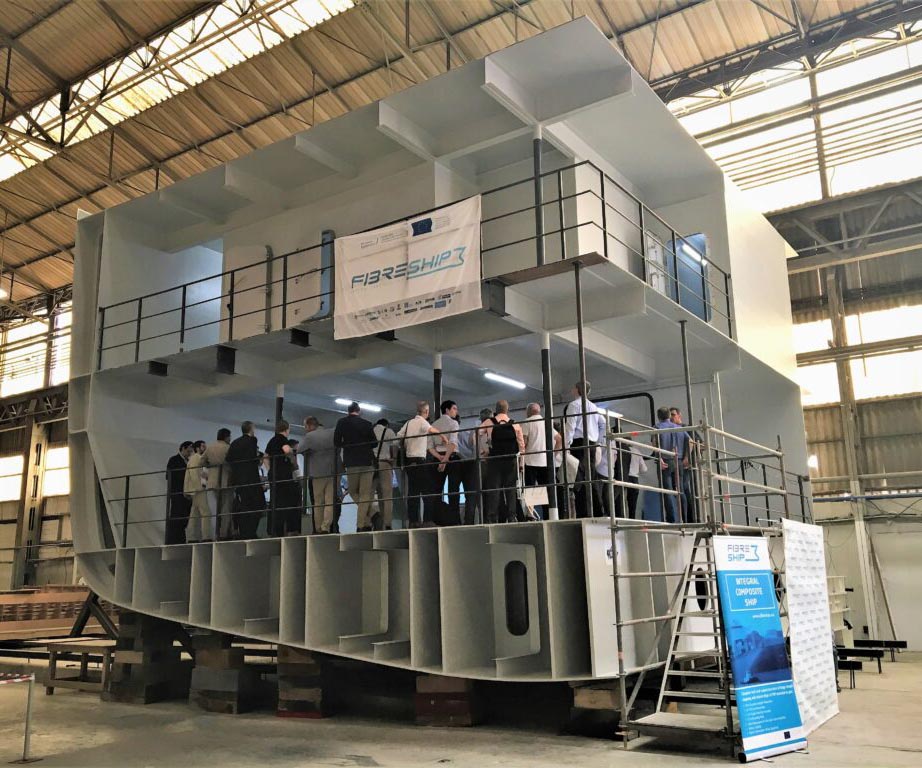
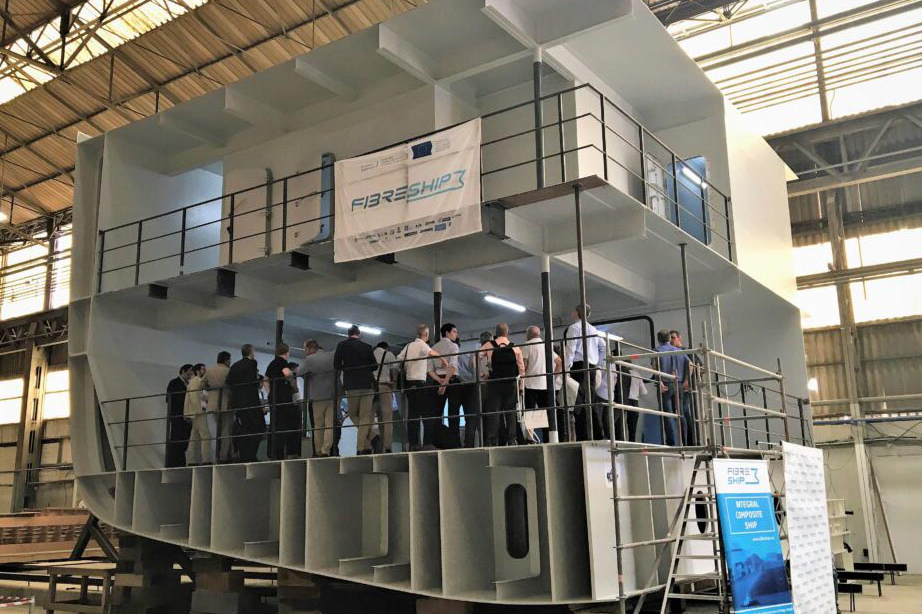
Compósitos de polímero reforçado com fibra de vidro e carbono (GFRP e CFRP) têm sido usados para construir embarcações marítimas por décadas, incluindo vários caçadores de minas de 40 a 60 metros e embarcações ainda maiores, incluindo o Visby Class Corvette de 72 metros de comprimento da Marinha sueca e o iate à vela de 75 metros de comprimento Mirabella V . O iate a motor de 141 metros Swift 141 (renomeado para Yas ) é uma fragata de aço holandesa reconstruída usando GFRP / CFRP em solas abaixo do convés e superestrutura de três conveses (consulte “De fragata a gigayacht de luxo”), incluindo uma junta de convés composto a aço.
E, no entanto, os compósitos raramente são usados na construção naval. Isso se deve principalmente aos regulamentos de Safety Of Life At Sea (SOLAS) emitidos pela Organização Marítima Internacional (IMO, Londres, Reino Unido), que exigiam que os navios comerciais fossem construídos em aço até o MSC / Circ. 1002 foi emitido em 2002 permitindo projetos alternativos.
“O regulamento exige a realização de uma análise de risco, mostrando que o projeto e construção alternativos são equivalentes ao aço”, explica Stéphane Paboeuf, chefe da Seção de Materiais Compósitos da sociedade classificadora Bureau Veritas (BV, Nantes, França). “Este processo é longo, caro e a decisão final ainda pode ser negativa.” Assim, embora os compostos ofereçam muitas vantagens para a construção naval, os desafios de segurança contra incêndio e as regulamentações impõem barreiras ao uso.
Enquanto isso, armadores, operadores e construtores estão buscando soluções para melhorar a sustentabilidade, incluindo peso mais leve para reduzir o uso de combustível, emissões de gases de efeito estufa e calado de embarcações - este último para vias navegáveis interiores rasas. A resistência à corrosão inerente dos compósitos para reduzir a manutenção também é atraente.
Em 2017, a IMO emitiu o MSC.1 / Circ., Um novo conjunto de diretrizes para o uso de compostos de FRP em navios comerciais. Conforme a avaliação da IMO dessas diretrizes em 2021 se aproxima, uma quantidade incrível de atividades está ocorrendo. Dois consórcios europeus, FIBRESHIP e RAMSSES, apoiados pela rede europeia de 378 membros para aplicações leves no mar (E-LASS), estão liderando esta onda de projetos de demonstração, que inclui decks compostos, lemes, cascos, cabines modulares e superestruturas, patch reparos em juntas soldadas de aço e composto de aço. Juntos, eles visam superar as barreiras para a construção de navios compostos leves, não apenas demonstrando o desempenho estrutural e ao fogo de grandes estruturas e embarcações inteiras, mas também desenvolvendo novas rotas para certificação e métodos de produção, novas tecnologias de união e ferramentas de design. Eles também estão compartilhando informações por meio de oficinas em andamento, repositórios de conhecimento e bancos de dados de materiais / design. Um novo mercado pode estar se abrindo para compósitos marinhos, mas quais soluções serão necessárias?
FIBRESHIP e RAMSSES
O FIBRESHIP e o RAMSSES foram iniciados em junho de 2017, financiados pelo programa Horizonte 2020 da União Europeia. FIBRESHIP tem 18 membros e funcionará até maio de 2020, enquanto RAMSSES tem 36 membros e termina em maio de 2021. Ambos incluem empresas de toda a cadeia de abastecimento que abrange centros de P&D, universidades, fornecedores de materiais e tecnologia, fabricantes de peças, arquitetura de navios e firmas de engenharia, estaleiros, armadores e sociedades de classificação. Estes últimos são responsáveis por desenvolver regras específicas para construções de navios individuais com base nas diretrizes gerais da IMO. Eles são autorizados pelos Estados de bandeira (cada navio tem a bandeira de um país) para auditar a construção do navio e garantir que essas regras sejam seguidas. “É importante que todas as partes interessadas e usuários finais estejam envolvidos”, diz Alfonso Jurado, chefe de P&D da Tecnicas y Servicios de Ingeniería (TSI, Madrid, Espanha) e coordenador do projeto FIBRESHIP.
“O principal objetivo do FIBRESHIP é desenvolver a capacidade de projeto e produção para grandes embarcações marítimas (mais de 50 metros de comprimento) com menos peso”, continua Jurado. “Esta é também a principal motivação da minha empresa.” O TSI está projetando a estrutura composta de um navio de pesquisa pesqueira (FRV) de 85 metros de comprimento total (LOA), que servirá como um demonstrador e, até agora, alcançou uma redução de quase 70% no peso estrutural em comparação ao navio de referência de aço. “Isso é incrível, oferece uma possibilidade real de ajuda para o setor marítimo”, afirma. Uma seção de 20 toneladas deste FRV, medindo 11 por 11 por 8,6 metros (veja a imagem de abertura), foi construída pelo estaleiro parceiro iXblue em La Ciotat, França, e exibida no segundo workshop público da FIBRESHIP em junho de 2019 (ver postagem de notícias com vídeo do demonstrador sendo fabricado).
Jurado explica que o FRV é o primeiro de três gabinetes de navios compostos gerais que a FIBRESHIP está desenvolvendo. Os próximos dois são navios porta-contêineres LOA de 260 metros e ROPAX de 204 metros, este último combinando a capacidade de carga de um navio roll-on / roll-off com as instalações de passageiros de uma balsa. “O FRV foi escolhido como demonstrador por ser menor com uma estrutura marítima mais convencional e, portanto, o mais viável de ser construído em um futuro próximo”, afirma. “Os armadores também demonstraram um interesse real em tal embarcação.” Enquanto isso, RAMSSES tem 13 demonstradores em andamento, 10 dos quais incluem compostos, e também está perseguindo uma embarcação totalmente composta.
Jurado observa que as empresas que participam desses projetos veem o potencial de tais designs inovadores e novos produtos leves para fornecer uma vantagem competitiva para seus negócios, bem como para a indústria de transporte de cada país. Mas o progresso não será garantido apenas por grandes manifestantes. “Devemos contar também com o apoio das autoridades reguladoras”, acrescenta. “Um primeiro passo é envolver a IMO e adaptar o regulamento SOLAS atual aos novos requisitos e demandas da indústria naval. Sem isso, não podemos avançar porque as seguradoras não subscreverão os navios de compósitos reforçados com fibra se eles não cumprirem os requisitos mínimos e a certificação de segurança, por exemplo. ”
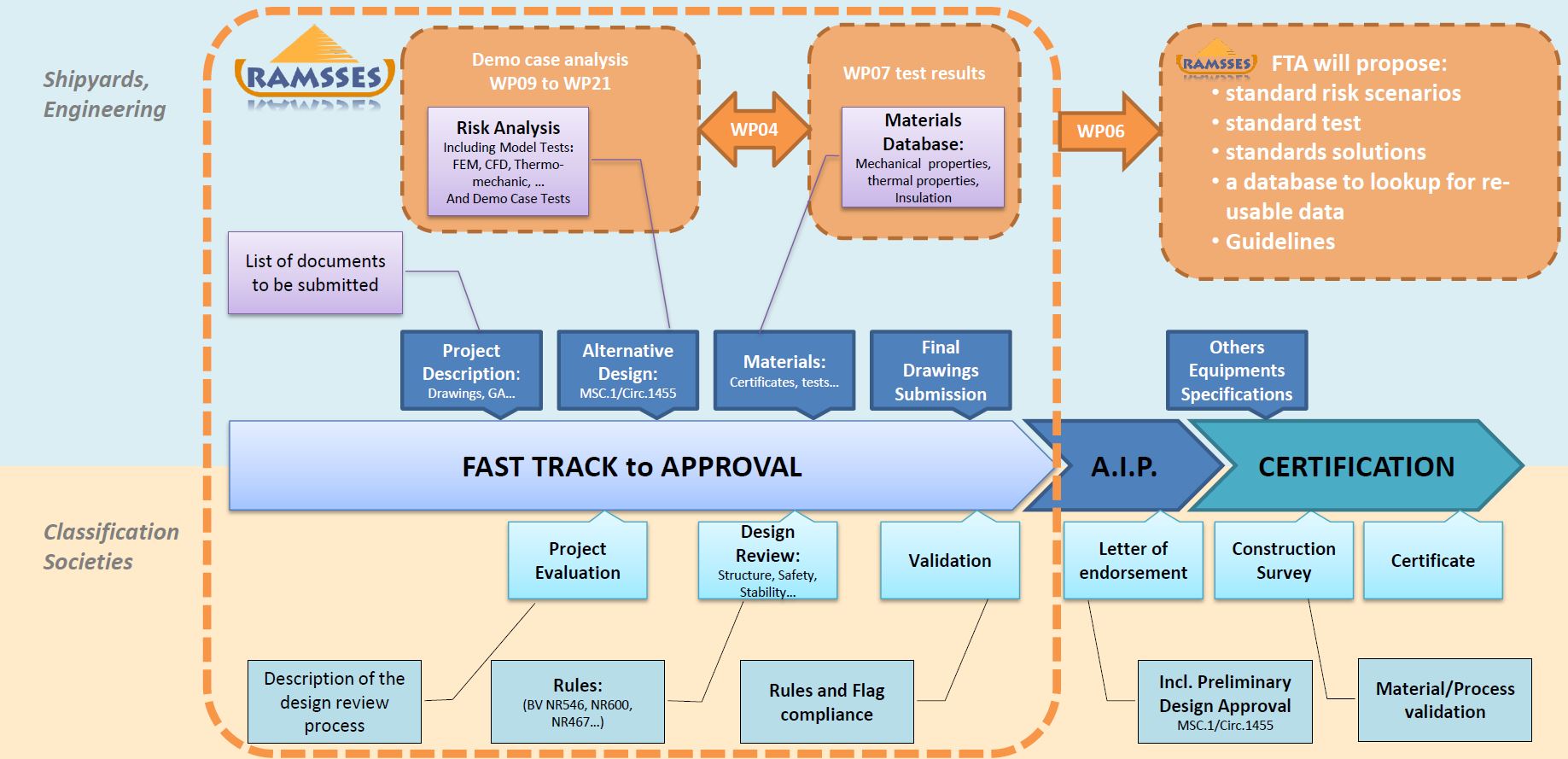
Proposta de abordagem Fast Track to Approval (FTA) para certificação de compósitos em navios comerciais em desenvolvimento no projeto RAMSSES, apresentada durante o Seminário E-LASS de junho de 2019 (Vigo, Espanha). Fonte | RAMSSES e Stephane Paboeuf, Bureau Veritas
“FIBRESHIP está buscando uma abordagem de longo prazo desenvolvendo novas regras, enquanto RAMSSES está desenvolvendo uma abordagem de curto prazo usando regras e métodos existentes”, explica Paboeuf no BV, que é o único parceiro da sociedade de classificação em RAMSSES, e um dos três em FIBRESHIP ao lado de Lloyd's Register (Londres, Reino Unido) e RINA (Gênova, Itália). “No RAMSSES, estamos desenvolvendo um procedimento Fast Track to Approval (FTA) com base na reutilização de dados do projeto para padronizar os testes e fornecer orientação para o projeto e a aprovação.” Este procedimento deve ser simples e facilmente legível por estaleiros, arquitetos navais e fornecedores. A aceleração versus o processo atual virá por meio de suportes sendo desenvolvidos em projetos de demonstração RAMSSES, incluindo:
- um banco de dados de soluções pré-aprovadas e resultados de testes de materiais para evitar testes repetitivos,
- cenários de risco de incêndio cobrindo uma gama de aplicações semelhantes para limitar o número e a extensão das avaliações de risco, e
- ferramentas de análise e modelagem, incluindo modelos numéricos ou estatísticos que podem substituir os testes físicos no futuro.
“No FIBRESHIP, estamos trabalhando com o Lloyd’s Register e o RINA para desenvolver um conjunto de regras prescritivas especificamente para grandes embarcações construídas com materiais compostos”, continua Paboeuf. “Para o desempenho estrutural, estamos definindo novos coeficientes de segurança para cargas locais e globais.” RAMSSES e FIBRESHIP também propõem substituir os níveis de classificação de fogo atuais, como A60, B30 e B15 por uma nova convenção REIxx, onde R especifica a resistência ao fogo (capacidade de carga no fogo), E designa integridade (a prevenção de fumaça e propagação de chamas ) e I define o isolamento contra incêndio. “O objetivo é alinhar melhor as classificações estruturais de incêndio com os materiais compósitos usados”, explica Paboeuf.
Além disso, os dois projetos também estão lidando com avaliações de risco devido à propagação de chamas, produção de fumaça e risco de incêndio no espaço de origem, mas também no nível de segurança global do navio. “Para o desempenho de incêndio, estamos desenvolvendo uma abordagem de equivalência local, que trata da segurança contra incêndio em nível local com base nas classificações de incêndio das anteparas e outras divisões estruturais em cada espaço da embarcação”, diz Paboeuf. “A segunda abordagem, a equivalência global, lida com o fogo no nível da embarcação, levando em consideração todos os sistemas (proteção contra incêndio ativa e passiva, detecção, evacuação, etc.) que impactam a segurança contra incêndio da embarcação como um todo, não apenas cada espaço dividido. ”
“A adoção mais ampla de compósitos na construção naval será passo a passo”, diz ele. “Começará com pequenas peças, como conveses e superestrutura, ou equipamentos como linhas de poços e hélices, antes de avançar para a construção de embarcações inteiras, que a princípio serão em sua maioria embarcações para fins especiais, como embarcações de pesquisa e teste sísmico e de alta velocidade nave de patrulha. ”

Fig. 1 embarcação composta de 80 metros RAMSSES
O Estaleiro Damen (DSNS) está desenvolvendo uma embarcação do tipo patrulha offshore totalmente composta no projeto RAMSSES. Seu demonstrador de seção de casco em escala real de 6 por 6 por 3 metros será construído em 2020 usando infusão de resina em colaboração com a InfraCore Company (ICC) e a Airborne International (AIR). Fonte | Estaleiro Damen e RAMSSES
Demonstradores de embarcações totalmente compostas
Além do FRV de 85 metros demonstrado pelo FIBRESHIP, um navio do tipo patrulha offshore de 80 metros de comprimento está sendo desenvolvido no RAMSSES para ser o primeiro navio SOLAS totalmente composto. Liderado pelo Damen Shipyard Group (Gorinchem, Holanda), este trabalho leva adiante os resultados de seu projeto Bluenose iniciado em 2014. Dentro do pacote de trabalho 17 do RAMSSES, a Damen está liderando a demonstração de um seção de casco composta em escala desta embarcação feita com infusão a vácuo, explica Matthias Krause, engenheiro de P&D do Centro de Tecnologias Marítimas (CMT, Hamburgo, Alemanha) e co-coordenador do projeto RAMSSES junto com a CETENA (Gênova, Itália). “A Evonik desenvolveu uma nova resina para esta seção de casco de demonstração e ferramentas de 6 metros de altura foram fabricadas. Damen também está trabalhando com a Airborne International (Haia, Holanda), um fornecedor da indústria de aeronaves que também construiu grandes estruturas infundidas. ” A Evonik (Essen, Alemanha) explicou seu papel em melhorar a resistência ao impacto e o comportamento à fadiga do casco infundido com fibra de vidro / vinil éster.
Outro parceiro neste demonstrador é a InfraCore Co. (Rotterdam, Holanda), que está desenvolvendo novas aplicações para a tecnologia InfraCore usada pela empresa irmã FiberCore Europe (Rotterdam) em mais de 1.000 pontes compostas e comportas em todo o mundo. “Originalmente, nos juntamos à Damen neste projeto para construir um heliponto de 12 a 14 toneladas”, explica o gerente de operações da InfraCore, Laurent Morel. “Agora estamos trabalhando com eles para construir os conveses, anteparas e estrutura do casco. Usaremos infusão horizontal e vertical para produzir a seção do casco de uma vez. Até agora, temos infundido a uma altura de 9,8 metros. ” Depois de concluído, este demonstrador será testado para desempenho estrutural e de incêndio, com resultados e lições aprendidas alimentadas nos novos módulos FTA do RAMSSES.
decks leves
Os compostos já foram demonstrados na primeira transportadora de automóveis roll-on / roll-off a usar um convés de carga composto, projetado e construído pelo Uljanik Group (Pula, Croácia) como parte do pacote de trabalho 14 RAMSSES (consulte “Baixo peso no alto mares ”), bem como um deck leve para um navio de cruzeiro fluvial de 110 metros de comprimento (consulte“ Convés composto reduz o calado do navio ”) e um convés de interpolação composto para um navio de carga geral de 200 metros de comprimento. “Um convés de interpolação é um convés removível que você pode instalar para dividir o porão de carga para facilitar diferentes tipos de carga”, explica Arnt Frode Brevik, gerente da Compocean (Sandvika, Noruega), um fornecedor de soluções compostas que surgiram do petróleo e gás indústria.
“Temos trabalhado com a Oshima Shipbuilding (Nagasaki, Japão) e DNV GL por vários anos para desenvolver um convés de interpolação leve com o objetivo de reduzir o peso em 50% em relação ao aço”, disse Brevik. Isso resultou em um protótipo GRP de 9 por 2 metros que foi testado para impacto e cargas máximas e, em seguida, exibido na NOR-Shipping 2017.
A Compocean agora estendeu este desenvolvimento a um novo projeto com Oshima, DNV GL e o armador Masterbulk Pte Ltd. (Cingapura) para construir um protótipo de convés de interpolação composto de 27 por 12 metros em escala real, que será instalado no próximo ano e testado até o final de 2021.
“Oshima buscava otimizar itens para reduzir os custos de combustível e manuseio”, diz Brevik. “Embora não haja muitos conveses entre os navios por navio, é uma parte fácil de começar ao introduzir novos materiais porque não faz parte da estrutura primária do navio.” O design é baseado em uma placa de fibra de vidro com infusão de resina de poliéster com reforços de chapéu embaixo. “Usamos uma mistura de layup de ± 45 graus, 0 graus e 0 graus / 90 graus para todas as peças, mas em diferentes proporções. A estrutura do convés também precisa integrar muitos pontos de amarração para proteger a carga. ” A placa será colada aos reforçadores do chapéu usando um adesivo estrutural, enquanto o aparafusamento será usado em combinação com o sistema de amarração. Um suporte de extremidade de aço aparafusado unirá o composto à estrutura de aço do navio. “Também buscaremos um projeto com juntas puramente adesivas no futuro”, acrescenta Brevik.

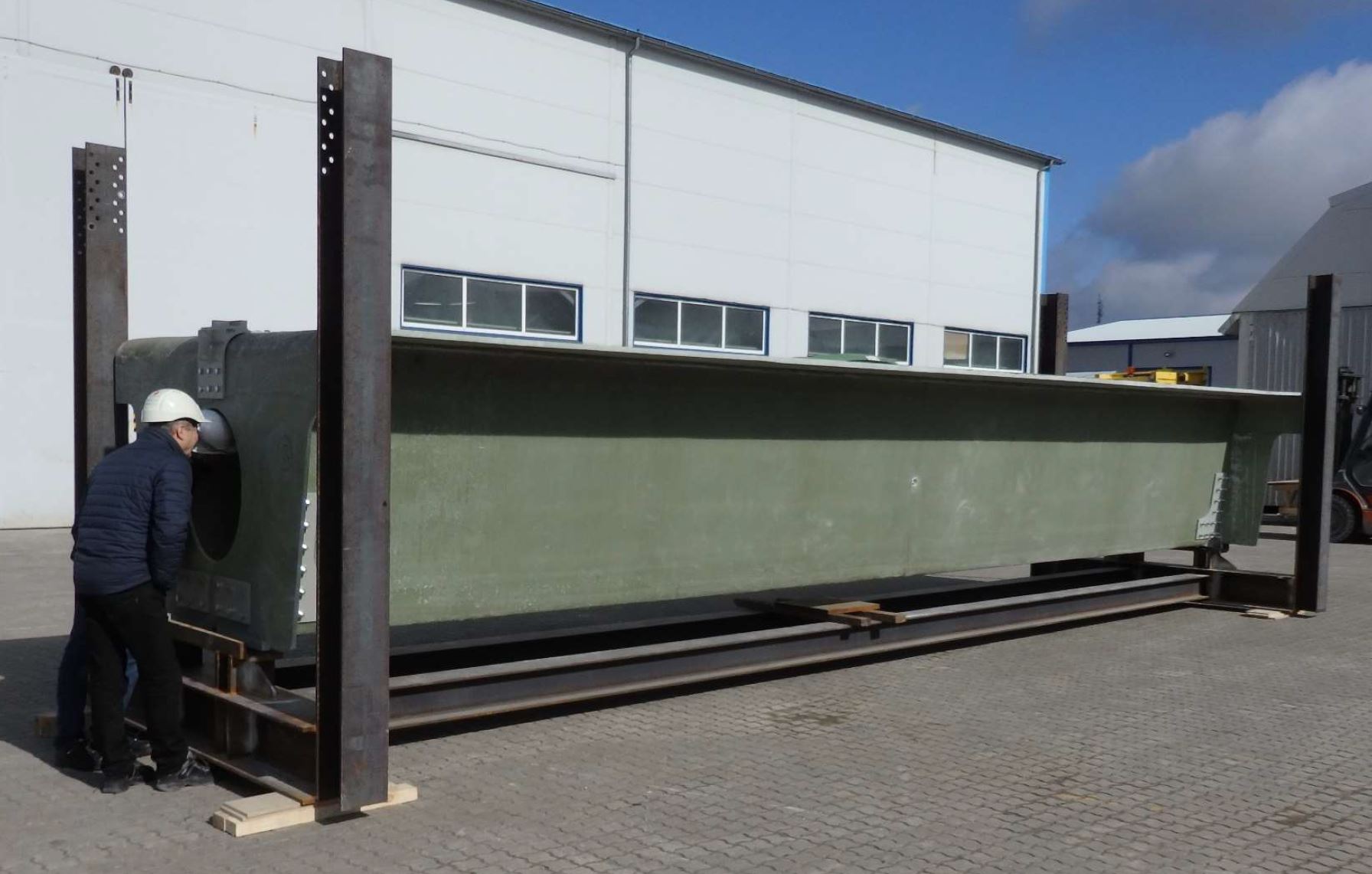
Fig. 2 deck de interpolação composto
O novo design de transportador de carga geral de 65k open-hatch da Oshima Shipbuilding usará o protótipo de convés composto de interpolação da Compocean, que economiza 50% do peso em relação ao aço e será composto de vários reforçadores de chapéu de FRP infundidos (inseridos) ligados a uma placa superior de FRP com conexões aparafusadas de o composto para a estrutura do navio de aço. Fonte | Compocean e DNV GL
Tendo recebido a aprovação final da DNV GL para o projeto de convés em escala real, a Compocean produziu os moldes e iniciou os testes de fabricação. “O deck composto em escala real será construído por um parceiro na Malásia, que o transportará por meio de barcaça até o navio”, disse Brevik. A próxima etapa é buscar uma redução de peso muito maior, por exemplo, escotilhas compostas no topo das aberturas de carga (placas planas no topo das “caixas” verdes na representação do navio acima). “Existem sete grandes tampas de incubação neste tipo de transportador”, observa ele. “Conseguir que eles sejam aprovados pela DNV GL apresentará alguns novos desafios, mas o sucesso com o convés de interpolação ajudará.”
Superestrutura leve, cabines modulares
RAMSSES tem seis pacotes de trabalho focados em superestruturas compostas e componentes usados acima do convés principal, a maioria com demonstradores e resultados de testes a serem apresentados em 2020. O pacote de trabalho 16, liderado pelo Naval Group (Paris, França), está demonstrando um módulo de superestrutura composta leve unido a uma plataforma de aço. O demonstrador em terra representa um bloco padrão para uma embarcação do tipo patrulha offshore. “A construção naval em materiais metálicos é baseada na construção em blocos para diminuir o tempo e os custos”, explica Jurado. “Construir tais blocos usando compostos apresenta problemas com a necessidade de grandes moldes, bem como técnicas de junção e requisitos de segurança de junta. A Fibreship estudou isso e desenvolveu algumas recomendações sobre a união de blocos à base de compósitos, incluindo a sequência de montagem. ” Em RAMSSES, o Naval Group investigou três tipos de estruturas em sanduíche, incluindo GF / poliéster / núcleo de balsa, núcleo de espuma de epóxi FR / PET e núcleo de espuma reforçada com fibra de GF / poliéster / 3D. Também está desenvolvendo um sistema de monitoramento de integridade estrutural (SHM) dentro da junta e dos painéis compostos.
O pacote de trabalho 18, liderado por Chantiers de l’Atlantique (Saint Nazaire, França) está desenvolvendo uma solução modularizada para cabines de passageiros. “Eles normalmente vêm sem piso porque são soldados no convés de aço do navio”, diz Krause. “A ideia é fabricá-los a partir de compósitos, pré-equipados com todos os sistemas auxiliares, como aquecimento e ar, elétrico, etc. Ao incluir um piso composto, eles podem ser inseridos em uma estrutura de aço (como uma gaveta) versus soldagem em um deck de aço sólido, economizando muito peso. ” Embora o projeto esteja avaliando compósitos para reduzir o tempo de produção e montagem de paredes, tetos e banheiros, porque a substituição do deck de aço economizaria cerca de 125 quilos por metro quadrado, os pisos de compósitos são o foco principal. Hutchinson (Paris, França) propôs o uso de sua espuma composta reforçada com fibra mineral ZALTEX, que resiste a temperaturas de -190 ° C a 1.000 ° C.
O pacote de trabalho 13, liderado pelo construtor de navios de cruzeiro Meyer Werft (Papenburg, Alemanha), também visa processos eficientes de montagem, mas visando anteparas. . O objetivo é construir dois demonstradores - um em terra e um em alto mar (teste marítimo) - onde paredes mistas serão unidas a estruturas de aço e depois submetidas a 80 testes mecânicos. O parceiro do projeto InfraCore realizou análises para definir os requisitos de isolamento térmico e acústico, frequência própria (vibração), deformação e largura e altura máximas para paredes compostas. “Fomos solicitados a desenvolver paredes internas e externas multifuncionais”, explica Morel, da InfraCore. “Para economizar tempo, custo e peso, devemos integrar o isolamento e um bom acabamento interno com o painel estrutural leve. Existem até 6.800 metros quadrados dessas paredes em cada navio de cruzeiro. Temos uma oportunidade para colocá-los a bordo de um navio de cruzeiro em meados de 2020, o que poderia ser as primeiras paredes compostas aprovadas pela SOLAS em um navio de cruzeiro em todo o mundo. ”
No pacote de trabalho 10, Podcomp (Öjebyn, Suécia) está desenvolvendo um painel alternativo interno / externo usando base biológica compósitos que devem ser retardadores de fogo e com preços competitivos. Foram examinados três conceitos de sanduíche baseados em GF / álcool polifurfurílico (PFA) pré-impregnado da Composites Evolution (Chesterfield, Reino Unido) e diferentes materiais de núcleo. Apenas um conceito passou no calorímetro de cone e em outros testes de fogo realizados pelos Institutos de Pesquisa RISE da Suécia (Borås). Agora está sendo otimizado para peso e custo.
Depois de experimentar a soldagem de alumínio e fricção, a Baltic Workboats (Nasva, Estônia) está agora avançando com compósitos para desenvolver painéis reforçados e pré-ajustados para a casa do convés / superestrutura de barcos de trabalho de alumínio (pacote de trabalho 15). O projeto do painel, a conexão com outros painéis e com o resto da estrutura da casa de convés, procedimentos de análise estrutural e solução de isolamento serão demonstrados, bem como técnicas de instalação a bordo.
Outra solução para superestrutura leve está sendo desenvolvida pela BaltiCo (Hohen Luckow, Alemanha), uma produtora de equipamentos navais que tem uma nova startup para construir barcos completos usando fibra de carbono colocada por robô enrolada em uma estrutura de treliça. “Você constrói o esqueleto da estrutura que deseja produzir, colocando estruturas cruzadas ou nervuras GFRP a cada meio metro e, em seguida, um robô enrola fibra de carbono em torno dela”, explica Krause. O objetivo é um sistema modular ultraleve usando um processo altamente automatizado. A demonstração incluirá a produção e montagem de dois módulos autoportantes de casco e convés em um catamarã leve não SOLAS movido a energia solar.
Juntas de aço FRP soldadas
“Acreditamos que o futuro da construção naval está na combinação de compósitos FRP, aço e outros materiais em estruturas híbridas”, disse o Dr. Lars Molter, um veterano de 10 anos na CMT. “Analisamos a colagem, mas não há um projeto de junta padronizado que possa ser usado em todos os navios e não há regras gerais sobre como aplicar a colagem adesiva em embarcações SOLAS. Além disso, você deve controlar o ambiente e o processo de vinculação. ” Ele observa que isso é difícil em meio à soldagem e ao corte que normalmente dominam a construção de estaleiros. “Perguntamos à DNV GL o que eles aprovariam para juntas de materiais diferentes”, disse Molter. “Eles disseram que a estrutura primária normalmente requer uma fixação mecânica; a ligação pura não seria certificada facilmente sem fixadores redundantes. ”
Molter e CMT responderam com o projeto FAUSST (Fibra e Padrão de Aço), financiado pela Alemanha, que desenvolveu um tecido de malha híbrido que faz a transição de 100% fibras de vidro para 100% fibras de aço. Este último é soldado a um conector de aço (por exemplo, placa plana, perfil retangular, etc.), que pode então ser facilmente soldado na estrutura de aço de um navio (Fig. 3). A extremidade da fibra de vidro é unida à estrutura do compósito por meio de infusão de resina. “Este projeto de junta oferece inspeção 100% NDT porque você pode usar UT (ultrassom) ou raio-X na solda”, diz Molter. A FAUSST realizou testes mecânicos, ambientais e de fadiga neste tipo de junta e também obteve a aprovação de princípio das sociedades de classificação, mas ainda havia muito trabalho a ser feito para transformar a tecnologia em um produto comercial. Assim, Molter deixou a CMT e fundou a HYCONNECT GmbH (Hamburgo, Alemanha) em 2018.
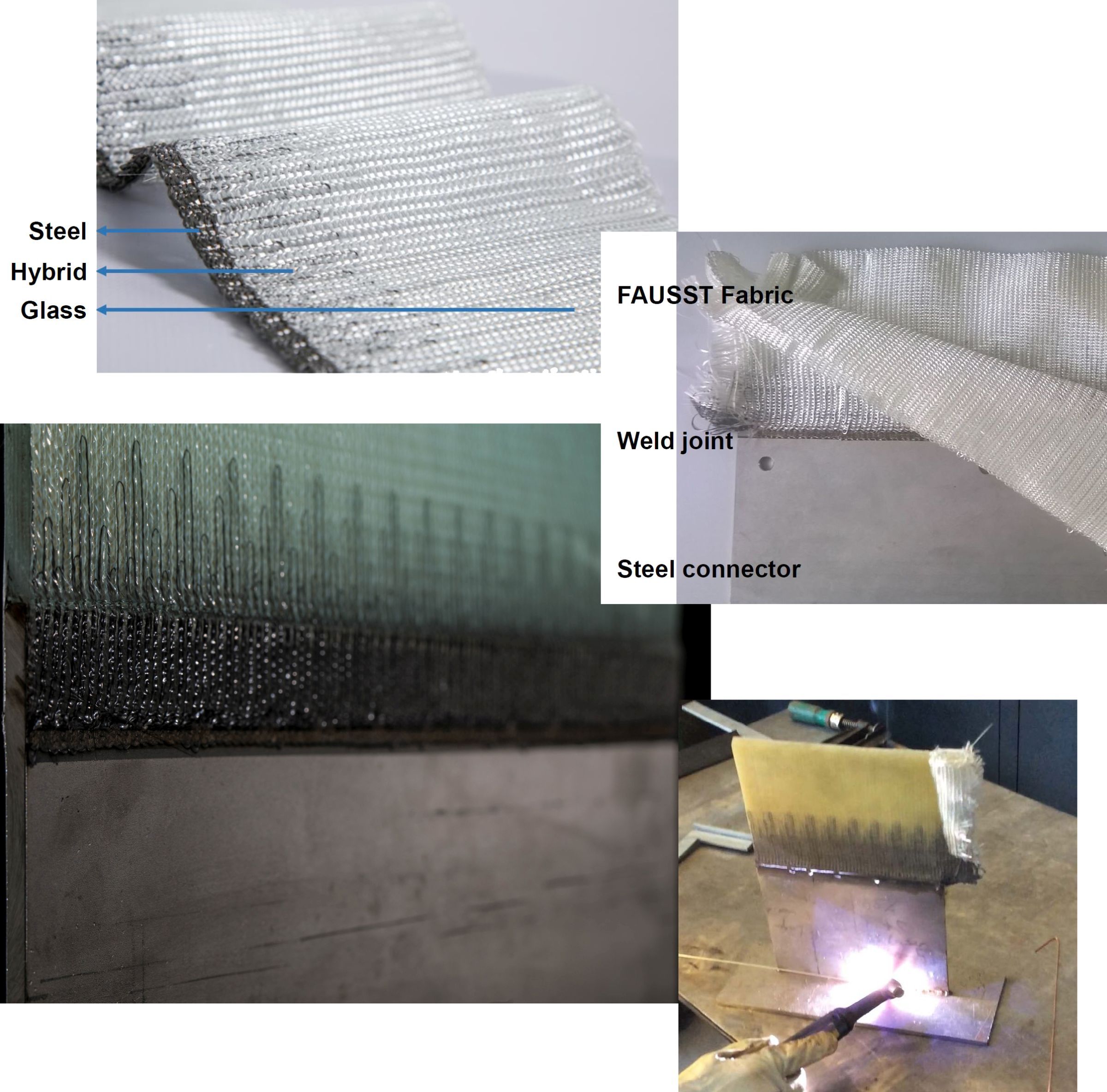
Fig. 3 Junta de aço-FRP soldada HYCONNECT
Tecido de fibra de vidro híbrido FAUSST (canto superior esquerdo) é soldada por prensagem a uma placa de aço ou outro conector (canto superior direito) e pode então ser integrado a uma estrutura composta por meio de infusão de resina (canto inferior esquerdo) . Essas estruturas compostas híbridas são então facilmente soldadas em estruturas de navios de aço (canto inferior direito) .
Fonte | HYCONNECT
“Reunimo-nos com estaleiros, DNV GL e BV e estamos desenvolvendo um produto que pode ser certificado”, diz Molter. “Você simplesmente pede suas peças compostas com este sistema de junta e, em seguida, pode soldá-las em seu navio. Essa é a nossa visão. Projetamos a junta de compósito para aço e, em seguida, entregamos um produto com tecido soldado a um conector de aço (placa, perfil, etc.). ”
Ele explica que o design da junta e o tecido serão certificados em um sistema gradual:“Ao aplicar mais camadas de tecido FAUSST, há um aumento linear na capacidade de transporte de carga.” Por exemplo, o produto base poderia ser quatro camadas de FAUSST com uma barra plana de 1 metro soldada a ela, classificada para uma determinada carga de tração e flexão. Então, haveria alguns produtos disponíveis para a esquerda (por exemplo, duas ou três camadas no total para uma classificação de carga mais baixa) e direita (por exemplo, seis camadas no total para uma classificação de carga mais alta). “Ainda estamos finalizando esses detalhes, mas o objetivo é um sistema padronizado e fácil de usar”, observa Molter.
HYCONNECT has adapted the fabric technology to handle the difference in stiffness and coefficient of thermal expansion (CTE) between steel and composites; the use of knitted fibers for mechanical interlocking with unidirectional fibers for carrying load through the joint; and the technique required for high-quality press welding of the steel fibers to the steel connector (see "Connecting composites to steel”). “This solution is based on continuous testing,” says Molter. “Because FAUSST consists of standardized ready-made sub-products, it can be supplied quickly, within days.” Prototypes are currently being produced for selected customers, and HYCONNECT will begin full production in 2020.
Composite rudders
Ship rudders are also being developed as FRP-steel hybrids. As part of RAMSSES work package 12, Becker Marine Systems (BMS, Hamburg, Germany) is demonstrating a lightweight composite flap for a steel rudder designed for large container ships. Such rudders typically weigh more than 200 tons, says Jörg Mehldau, head of R&D at BMS. “By adding a hinged aft flap, you can significantly reduce the rudder area.” BMS pioneered this flap rudder, which dramatically reduces ship turning radius and improves course-keeping and maneuverability, enabling berthing without tugboat assistance. A composite flap not only reduces weight but also enables more functional shapes as well as more hydrodynamically- and load-optimized designs.
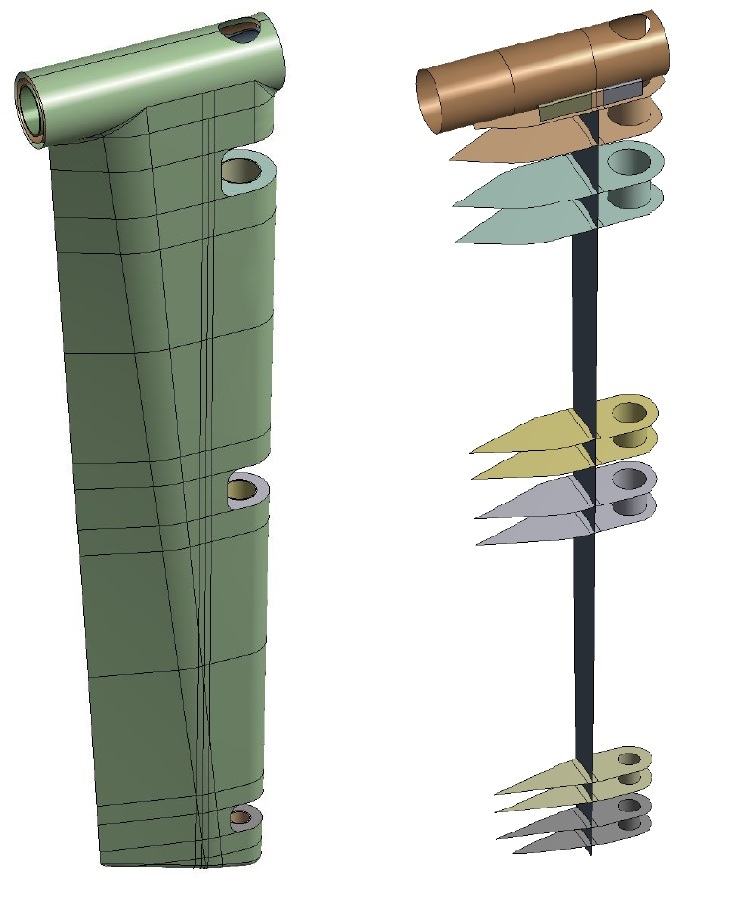
Fig. 4 Composite rudder flap
Becker Marine Systems is working with InfraCore to develop a lightweight, resin-infused rudder flap for the largest container ships. Measuring 11.8 meters long and 0.9 meter wide with a 2.9 meter chord, the full-scale flap must withstand 100 tons/m 2 of load. A 2-meter high demo will be tested 2Q 2020. Source| Becker Marine Systems
“The composite flap we are developing was inspired by the aviation industry,” notes Mehldau. For RAMSSES, the full-scale test case is aimed at one of the largest container ships (≈400 meters long), a flap measuring 11.8 longmeters and 0.9 meters wide with a chord of 2.9 meters (see Fig. 4). “We calculated the forces on this rudder and flap using formulas based on DNV GL rules for this ship’s type, weight and maximum speed,” says Mehldau. BMS then conducted preliminary design and engineering analysis, as well as trade studies for manufacturability and cost. “We first favored filament winding but it was too expensive,” he notes. “For each new ship hull, the rudder is a single design.” Thus, resin infusion was chosen, as was an alternative design from InfraCore. “It was the best for production flexibility, cost and structural performance combined,” Mehldau explains.
“To me, this was a natural fit for InfraCore because the composite lock gates we have built are very similar,” says Morel. He notes container ship rudders must withstand loads of roughly 100 tons per square meter with a surface area of 150 square meters. This matches well with InfraCore’s infusion-based technology used in bridge decks spanning up to 142 meters. Instead of bonding a high-density structural core to faceskins, InfraCore uses a low-density foam core only as a permanent formwork for multiple Z-shaped, two-flanged web structures. These are overlapped, faced with multiaxial fabrics and co-infused to form a robust construction. InfraCore will build a 1:6 scale demonstrator, using glass fiber and polyester resin materials already certified by DNV GL to keep costs low.
Morel notes that the reduced-weight InfraCore composite flap is cost-competitive, “because steel ship rudders are quite complicated to manufacture.” Mehldau agrees, “together with less maintenance and operational cost advantages, we see a successful business case.” The 2-meter -high demonstrator will be finished by 2Q 2020, followed by testing.
“We will test this using a lab test bench and air cushions, which can apply up to 8 bar of pressure equal to at least 80 Mpa of load,” says Mehldau. “We will measure strains and deflections to verify our simulations and perform a break load test.” A lab-scale demonstrator will also be tested via sea trials on a research ship in the Elbe River by CETENA (Genoa, Italy) which serves as project coordinator for RAMSSES along with CMT.
Forward momentum
“The outlook for composites in ships is good because many of the marine sector stakeholders have shown interest in FIBRESHIP, RAMSSES and other projects,” says Jurado. “The largest challenges are the need for new regulations, fire safety aspects, bonding techniques and reduction of shipbuilding costs.” For the latter, he cites automated manufacturing in shipyards as a key issue as well as mold construction and composite materials sourcing and storage. “Composites are already growing in ships,” says Krause at CMT, “but we started this work 20 years ago, so it is a slow process. However, we now have this critical mass and the industry is more connected via E-LASS.”
Jörg Bünker, head of R&D, application service for SAERTEX LEO FR products at SAERTEX (Saerbeck, Germany), agrees:“The drivers to reduce weight are strengthening. Within the next five to seven years, more composite materials will be sold into ships. This is the right time for more projects because IMO needs to see this interest and effort from the industry. Suppliers must show new solutions and shipyards must show where composites can be used, but no one can do it alone.”
Resina
- Envie em uma garrafa
- Reciclagem:Compósitos termoplásticos reforçados com fibra contínua com policarbonato reciclado
- Como a tecnologia móvel está removendo barreiras para viajar
- TxV Aero Composites está em conformidade com os padrões AS9100
- Mikrosam automatiza compósitos termoplásticos com sistema de colocação multi-robô sem ferramentas
- Hexcel faz parceria com Lavoisier Composites, Arkema
- Fabricação contínua de fibra (CFM) com compostos moi
- Cúpula de peso leve:visando oportunidades de trens de força automáticos compostos
- A Ashland faz parceria com a Velox para distribuição de compostos na França
- Compósitos para impressão 3D com fibra contínua