Protótipos WMG Estrutura CFRP para veículo de demonstração Very Light Rail (VLR)
O Revolution VLR é um consórcio no Reino Unido - liderado pela Transport Design International Ltd (TDI, Stratford upon Avon) - que ganhou financiamento em 2013 para desenvolver um bogie ferroviário com alimentação própria com um sistema de propulsão híbrido integral. A TDI acredita que projetar veículos “light rail” mais leves - ou seja, very light rail (VLR) - é crucial para fornecer a próxima geração de transporte público sustentável. Na fase 2 do projeto VLR, um veículo demonstrador de bateria a diesel de 18 metros de comprimento estará disponível para teste em 2020.
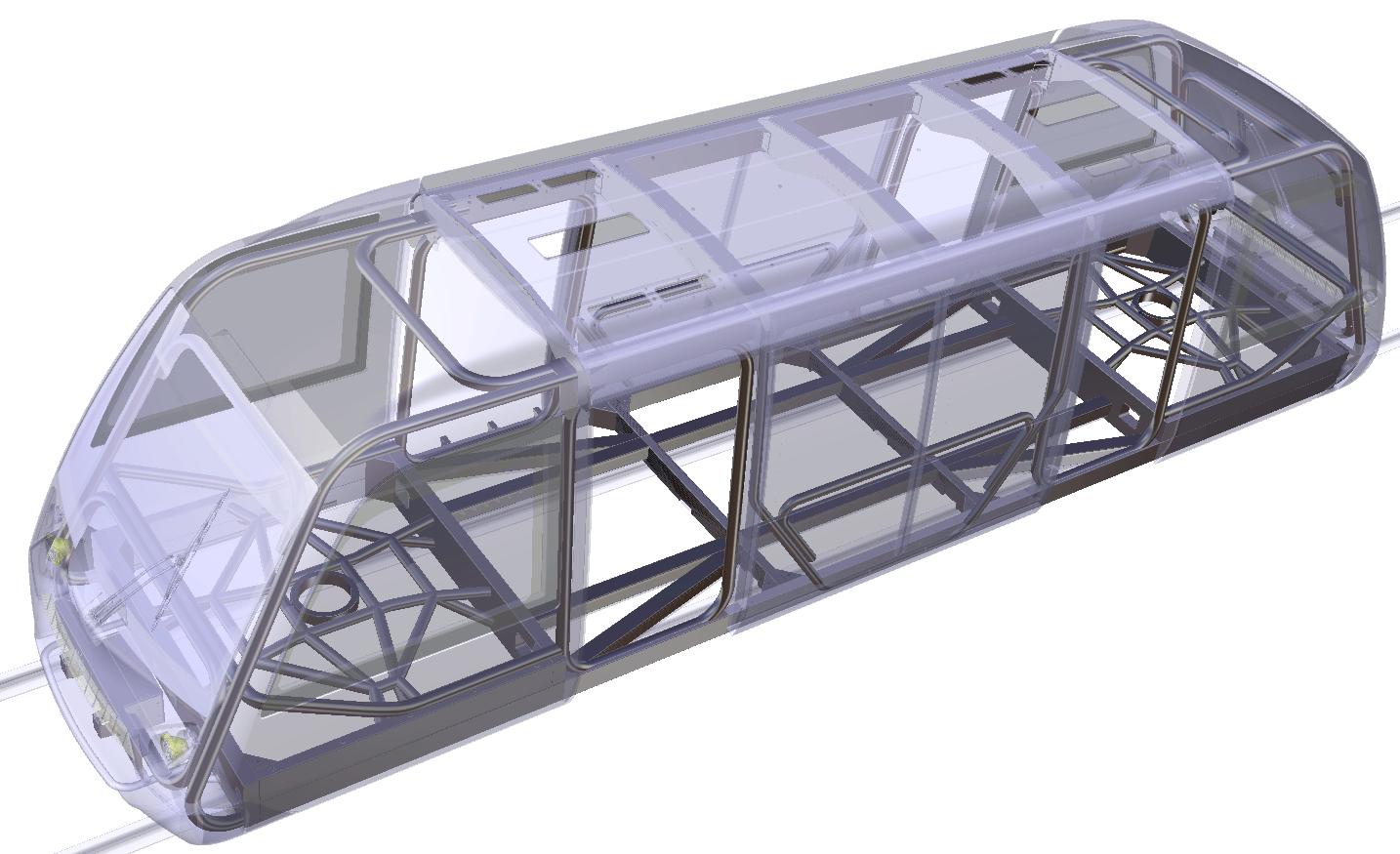
O demonstrador Very Light Rail (VLR) é um bogie de 18 metros de comprimento com sistema de propulsão híbrido de bateria diesel integrado e um chassi leve feito de tubos compostos trançados. FONTE | University of Warwick.
Membro original da Revolution VLR, a WMG da University of Warwick desenvolveu uma estrutura de plástico reforçado com fibra de carbono (CFRP) para este veículo VLR de demonstração. A WMG apoia há muito tempo os compósitos, com iniciativas como o National Automotive Innovation Center, o Materials Engineering Center e o International Institute for Nanocomposites Manufacturing. Os parceiros da WMG para este projeto “BRAINSTORM VLR” incluem a TDI, a Innovate UK do governo do Reino Unido (que financia compósitos), desenvolvedora de componentes de compósitos estruturais leves Far Composites e Composite Braiding. A estrutura é feita de uma série de tubos compostos termoplásticos trançados que são facilmente montados por colagem e soldagem simples.
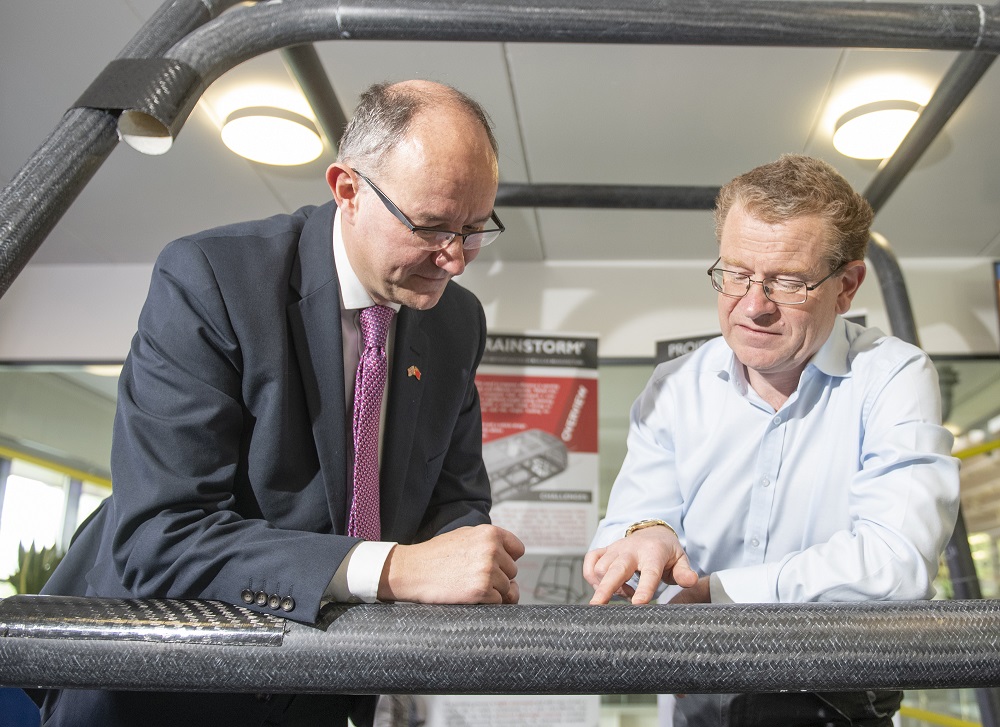
O veículo protótipo / demonstrador VLR usará um chassi spaceframe feito de tubos compostos termoplásticos reforçados com fibra de carbono trançada que são facilmente montados por colagem e soldagem simples. FONTE | University of Warwick.
Os diâmetros externos do tubo são mantidos iguais, com diferentes requisitos de carga e fixação atendidos pela variação da espessura da parede. Isso mantém os custos de ferramentas baixos e significa que as junções podem ser padronizadas. A trança permite um processo de fabricação altamente automatizado - taxas para o reforço sozinho podem exceder 1 milha / dia - bem como um conjunto de materiais sob medida, incluindo outras fibras (por exemplo, vidro, aramida, termoplástico) e materiais de matriz termoplástica de polipropileno de baixo custo à polieteretercetona de ponta (PEEK). Enquanto isso, a WMG demonstrou um ciclo de moldagem completo que pode ser reduzido para menos de cinco minutos, destacando o potencial desse processo acessível para aplicações de alto volume.
Os termoplásticos também oferecem reciclabilidade, de acordo com David Goodwin, gerente de engenharia da Far-UK. “Com os compósitos você pode economizar muito peso, o que obviamente é atraente para a operação do vagão [ferroviário]”, ele começa, “mas com os compósitos tradicionais, no final da vida do carro ele é simplesmente colocado em aterro sanitário, que não é ideal. Com este [projeto], existe um caminho para reciclar a carroceria do carro quando eventualmente ficar fora de serviço, ou, alternativamente, se sofrer um impacto e parte dela tiver que ser reparada e substituída ”.
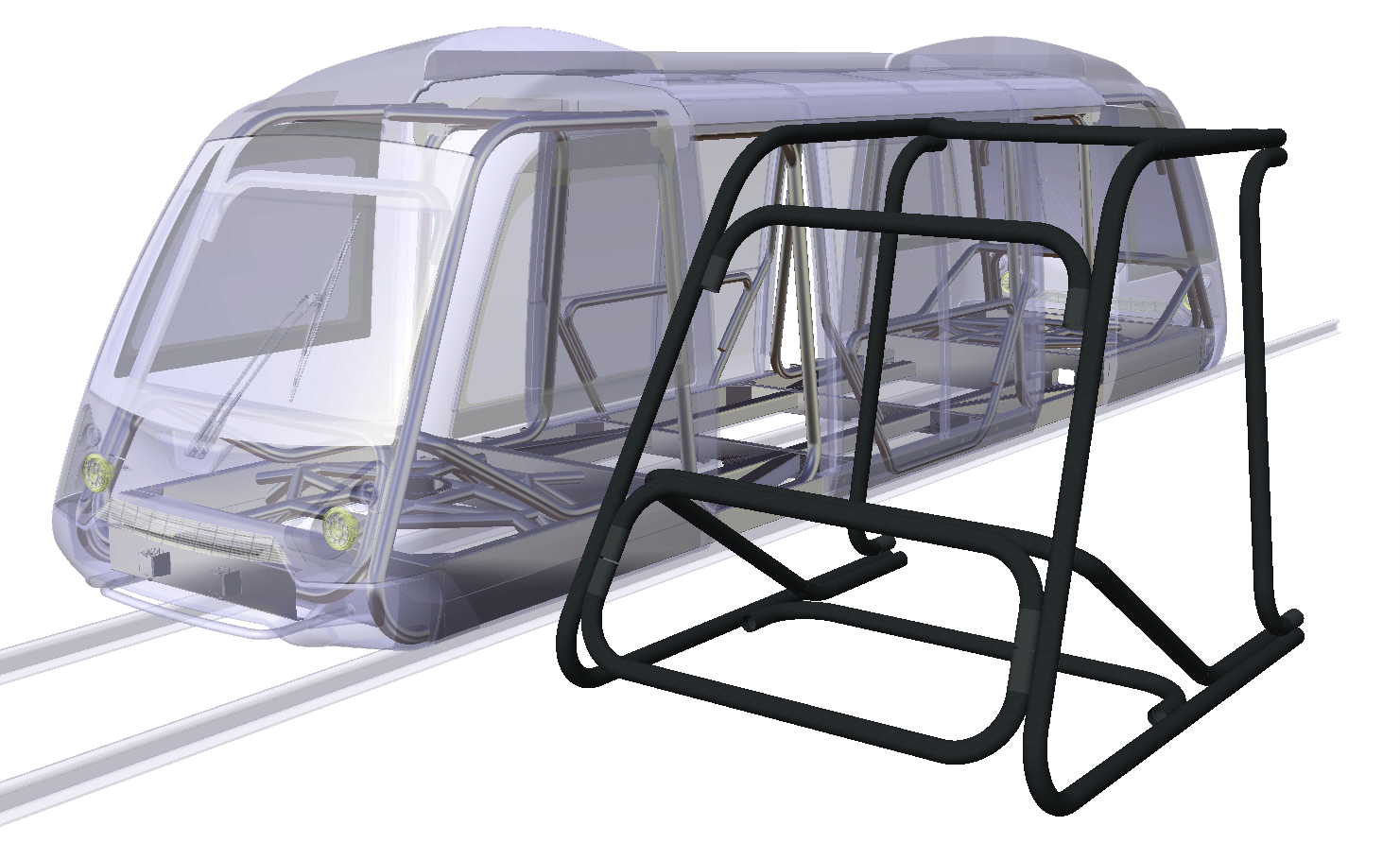
Universidade de Warwick
O projeto do chassi tubular do spaceframe também ajuda nessa abordagem, permitindo que quaisquer tubos danificados sejam simplesmente removidos e substituídos por um novo ou reparado. “Nossa parceria de pesquisa BRAINSTORM VLR conseguiu uma redução significativa de peso, permitindo que os serviços de VLR acomodassem mais passageiros, ao mesmo tempo que reduzia a energia necessária para impulsionar o veículo e o peso que ele colocaria nos trilhos e na superfície da estrada”, explica o Dr. Darren Hughes, professor associado de Materiais e Manufatura na WMG University of Warwick. “A tecnologia também garante que o veículo seja resistente para uma vida longa em serviço, facilmente reparável em caso de acidentes e forte o suficiente para proteger os passageiros a bordo.”
“O Projeto BRAINSTORM parece um verdadeiro passo à frente para a equipe da Far Composites”, disse o diretor e gerente geral da Far-UK, Lyndon Sanders. “Foi ótimo poder aproveitar a experiência da indústria de TDI para aprimorar o princípio de um novo tipo de estrutura corporal para aplicações de transporte de massa. Adicione a isso o trabalho colaborativo com Composites Braiding e WMG para transformar esse pensamento em um demonstrador físico para mostrar como seria na prática foi realmente poderoso. Agora é mais do que uma boa ideia, é uma revelação para os participantes da indústria que podem ver, tocar e até mesmo pegar. ”
Resina
- Compósitos TPE ultraleves para calçados
- Projeto para fabricação automatizada de compósitos de aeroestruturas de baixo volume
- Resinas epóxi reprocessáveis, reparáveis e recicláveis para compósitos
- Combinação de medições dielétricas AC e DC para monitoramento de cura de compósitos
- Perseverance rover dá um passo para composições em Marte
- RS Electric Boats seleciona Norco para a fabricação de compostos
- Termopar de alta temperatura PEEKSense para cura de compósitos PEEK
- Compostos Solvay selecionados para catamarã de corrida
- Porta termoplástica a primeira para compósitos automotivos
- A Ashland faz parceria com a Velox para distribuição de compostos na França