Entrevista com especialista:Engenheiro-chefe da Oerlikon para AM, Matthew Donovan, sobre impressão 3D para a indústria aeroespacial
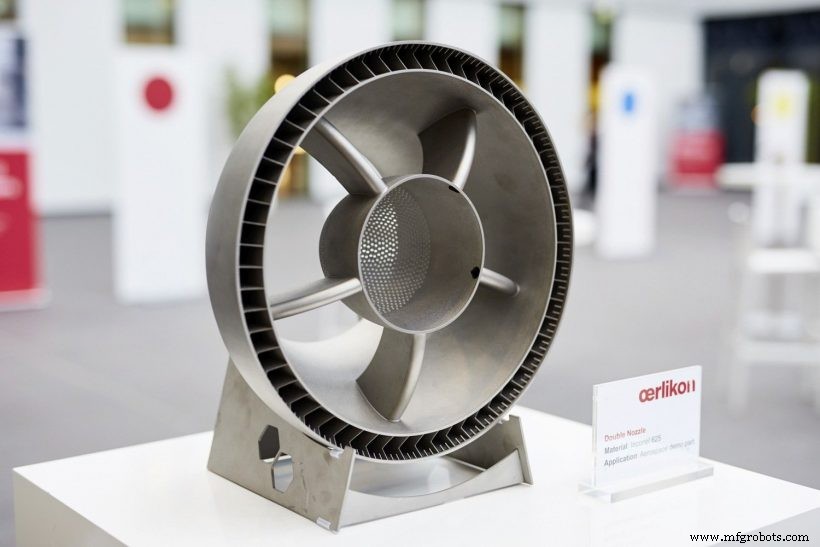
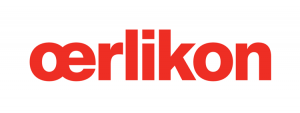
Na Entrevista com Especialistas desta semana, nos sentamos com Matthew Donovan, Engenheiro Principal de Fabricação de Aditivos da Oerlikon, para discutir como ela continua a desenvolver uma instalação de produção AM de ponta a ponta, estimulantes tendências AM para esteja atento e porque os padrões são críticos para o futuro da indústria.
Você poderia me falar sobre a Oerlikon?
A Oerlikon é uma empresa global e líder em manufatura nos segmentos de Soluções de Superfície e Fibras Manufaturadas. Parte do segmento de Soluções de Superfície, a Oerlikon AM oferece soluções de manufatura aditiva, desde pós de metal até prototipagem e produção em série.
Como você se envolveu pela primeira vez na manufatura aditiva?
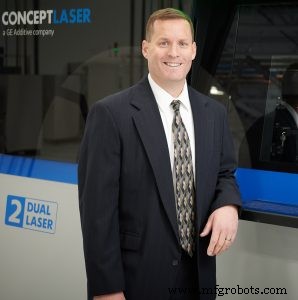
Minha formação é aeroespacial. Antes de vir para a Oerlikon, passei os últimos 20 anos trabalhando, principalmente, em motores de turbina a gás, componentes de seção quente e componentes de seção de combustão.
Tenho experiência em sistemas de distribuição de combustível, principalmente para motores de turbina a gás aeroespacial, mas também para turbinas a gás industriais e reformadores de células de combustível. Eu também trabalhei em vários esforços de P&D com a NASA e outras empresas. Então, tive experiência em trabalhar com materiais de alta resistência e alta temperatura para ambientes muito exigentes.
Comecei como engenheiro de manufatura, aprendendo os prós e contras de como fabricar e construir peças e gastei tempo como engenheiro de qualidade fazendo investigações de campo para esses mesmos componentes.
Comecei a trabalhar com manufatura avançada em 2006. Comecei a encontrar geometrias e componentes desafiadores que não poderíamos realmente fazer com a manufatura convencional.
Nessa altura, estava a trabalhar com a Morris Technologies em componentes metálicos impressos em 3D. Iniciamos o desenvolvimento de componentes para injetores de combustível por meio de manufatura aditiva.
Ao longo dos anos, desenvolvi alguns componentes usando manufatura aditiva. Trabalhei para a United Technologies, auxiliando toda a empresa no desenvolvimento e implementação de tecnologias AM, principalmente com foco em hardware de certificação de voo.
Enquanto estávamos trabalhando para implementar esses componentes, uma das principais lacunas que descobri foi que havia uma total falta de padrões sobre como fazer as peças e como certificá-las.
Grande parte do custo associado à indústria aeroespacial não é necessariamente os componentes em si, mas a certificação. Devemos fornecer rastreabilidade completa para cada componente que fabricamos. Desenvolver os padrões de como fazemos isso e implementamos isso para aditivos foi um grande desafio.
Comecei a trabalhar nos padrões AM com ASTM F42 por volta de 2009. Eu ajudei a redigir alguns padrões e posteriormente servi em alguns comitês. Fui coautor do guia de design para fusão de leito de pó metálico a laser, ISO ASTM 52911, com ISO / TC 261 e ASTM F42.
Através desse trabalho com a United Technologies, trabalhando com muitas pessoas altamente talentosas e tendo acesso a uma série de recursos excelentes, fomos capazes de apresentar várias inovações e desenvolver alguns produtos realmente de ponta para AM cama de pó de metal.
O que sua função na Oerlikon envolve?
Comecei na Oerlikon em 2017 e minha função, agora, é Engenheira Principal para AM. Minha função tem se concentrado fortemente na implementação e desenvolvimento de tecnologias de metal AM prontas para a produção.
Começamos como uma divisão inicial do Surface Solutions Group. Construímos uma nova instalação em Huntersville, Carolina do Norte, para a qual nos mudamos há pouco menos de um ano.
É uma instalação de 120.000 pés quadrados que atualmente opera 18 sistemas de leito de pó metálico. No local, temos HIP (Hot Isostatic Pressing) e recursos de forno a vácuo, bem como recursos de pós-processamento, manuseio de pó e inspeção.
O objetivo é estabelecer esta instalação como um verdadeiro fluxo de trabalho de produção AM de ponta a ponta, com controle de todos os aspectos da cadeia de abastecimento, para que possamos fornecer rastreabilidade aos nossos clientes.
Meu papel nisso tem sido, principalmente, na certificação de máquinas. Eu trabalho em estreita colaboração com os OEMs de máquinas na instalação e qualificação de nossas máquinas e, em seguida, obtendo a certificação de sua capacidade e capacidade cruzada para componentes em máquinas diferentes.
Somos então capazes de compreender as capacidades da máquina, a tolerância e a precisão de uma máquina individual para produzir a tolerância geométrica de um componente AM e as diferenças entre nossas máquinas e, em seguida, ajustá-los para que possamos entregar o mesmo produto em várias máquinas.
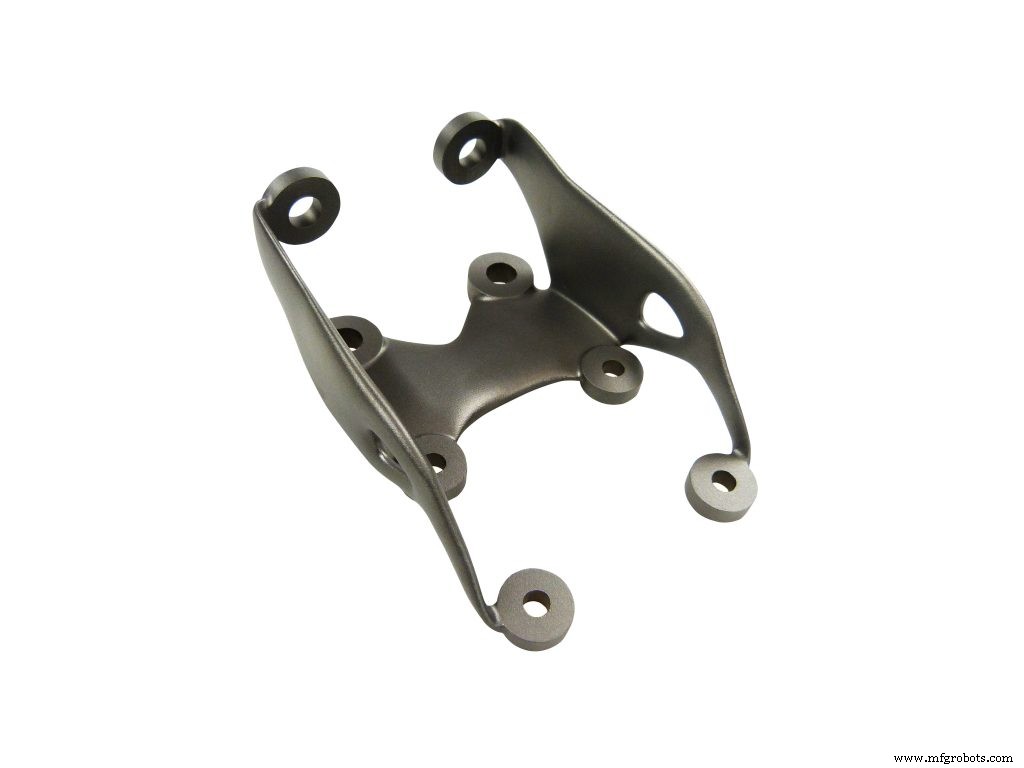
A padronização tem sido um grande ponto de discussão, especialmente para setores como o aeroespacial. Como as coisas se desenvolveram ao longo do tempo em que você está envolvido no setor e qual é o status atual da padronização de AM?
Houve alguns desenvolvimentos muito bons.
Precisamos de padrões, especialmente na indústria aeroespacial, mas também em outras áreas críticas para a segurança, como médica, nuclear e energética. O principal aspecto dos padrões é que eles permitem que todos falem a mesma língua e entendam do que um produto é capaz.
Com a ausência de padrões, todos estavam efetivamente construindo peças e realizando seu trabalho de maneiras muito semelhantes, mas não da mesma maneira. Eles não estavam falando a mesma língua. É muito comum que as pessoas se refiram a termos diferentes para significar o mesmo processo ou se referem ao mesmo termo e significam processos radicalmente diferentes.
O desenvolvimento de padrões permite que você fale na mesma língua e compreenda o que você quer dizer quando se refere a, digamos, uma construção de qualificação, matéria-prima ou nível de qualificação da máquina.
Na indústria aeroespacial, se você não tem um padrão pelo qual possa certificar uma peça ou, normalmente, vários padrões para identificar a peça que você está fabricando, suas propriedades mecânicas, desempenho e tolerâncias e para ser capaz de rastreá-lo até o lote original de onde veio, até a composição química dos elementos que o compõem, então você não pode colocá-lo em uma plataforma aeroespacial.
Podemos fazer geometrias incrivelmente complexas e fazer peças com AM que não são fisicamente possíveis de outra maneira. Podemos economizar muito peso, tempo, material e custo fabricando peças por meio do AM.
A liberdade de design e fabricação que a AM nos oferece é clara. Mas a desvantagem é que é ótimo se você pode fazer a parte, mas se você não pode provar que é uma parte boa, não faz bem a ninguém.
Os padrões são o que nos leva a atravessar essa linha para ser capaz de fabricar e vender peças e ser capaz de usá-los na produção para a indústria aeroespacial.
Portanto, os padrões aeroespaciais são uma das peças-chave do quebra-cabeça antes que você possa fazer as peças.
Há várias organizações de desenvolvimento que trabalham arduamente nesta área há muito tempo. Trabalho como voluntário nos padrões ASTM há cerca de 10 anos e tenho visto os benefícios do que fazemos.
Como mencionei, eu contribuí para o padrão original de titânio para fusão em pó. Aquele primeiro levou eu (e várias outras pessoas), pouco mais de dois anos para validar o primeiro. Posteriormente, conseguimos transformar outros adicionais em cerca de metade desse tempo.
As coisas estão realmente começando a acelerar agora. A ASTM lançou recentemente seu Centro de Excelência com sede em Auburn, Alabama, em conjunto com a Auburn University.
A intenção por trás disso era aplicar fundos e esforços de pesquisa e desenvolvimento direcionados por meio de parceiros de colaboração para atingir mais padrões rapidamente. Tem havido muita colaboração da indústria e de órgãos governamentais para identificar as lacunas e os padrões que percebemos na indústria, que é o que precisamos para seguir em frente.
Você deve ter ouvido falar sobre o roteiro ANSI. É um documento muito bom para o qual alguns de nós da indústria contribuíram, a fim de identificar quais são as nossas lacunas principais, que precisamos preencher para alcançar a produção real para manufatura aditiva.
Na última versão desse roteiro, acredito que foram identificadas 91 lacunas, principalmente em áreas de padrões, e algumas delas são de alta prioridade. O Centro de Excelência ASTM é um veículo que está sendo usado para aplicar P&D para fechar essas lacunas nos padrões.
Em outra área, a SAE International possui sua Especificação de Materiais Aeroespaciais (AMS). Os primeiros para fusão de leito de pó aditivo foram AMS 7000, 7001, 7002 e 7003 para liga de níquel 625, que foi lançada recentemente.
São excelentes trabalhos que vão render muitos resultados. Muitos de nós já estamos usando esses padrões para desenvolver peças de produção.
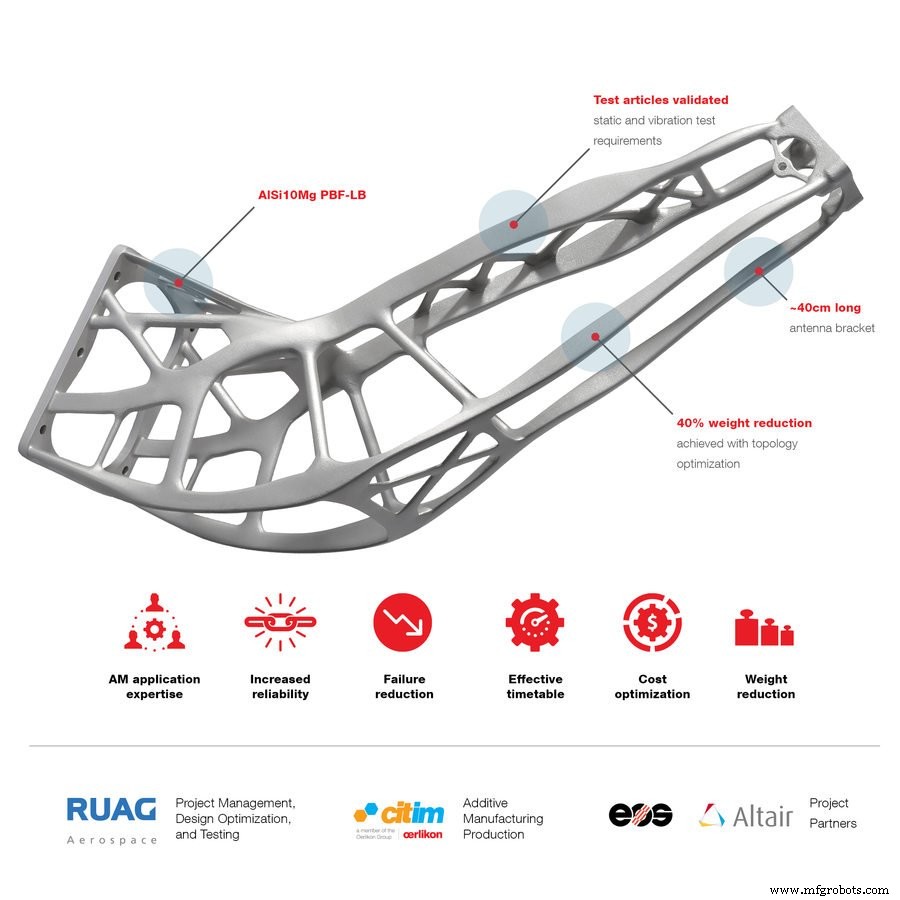
Com sua experiência de adoção de AM, quais foram alguns dos desafios para integrar a tecnologia internamente e como você navegou nesse processo?
A Oerlikon AM tem como objetivo fornecer soluções AM que atendam aos requisitos das indústrias mais exigentes, como aeroespacial e médica, entre outras.
Em nossas várias instalações, temos os sistemas de qualidade adequados, como o AS9100 para aeroespacial e ISO 13485 para médicos. Mas em relação a integrar todos os sistemas necessários para chegar lá, isso tem sido um desafio, embora existam algumas soluções por aí que fornecem peças do quebra-cabeça.
Eu diria que não existe uma solução que cubra todos os aspectos do que precisamos, de ponta a ponta. Mas existem muitas ferramentas boas que cobrem partes de toda a cadeia de abastecimento de ponta a ponta.
Portanto, um dos nossos desafios é identificar as soluções que cobrem diferentes aspectos de nossa cadeia de abastecimento, trazer incorporar aqueles que cobrem os aspectos de que precisamos e integrá-los.
Por exemplo, algumas soluções lidam muito bem com finanças e estoque, mas não funcionam muito bem para fluxos de trabalho de manufatura. Outros lidam bem com fluxos de trabalho de manufatura e planejamento de produção, mas não lidam, digamos, com estimativa de tempo de construção, problemas de revisão de materiais ou problemas de componentes geométricos, como projetos e modelos 3D.
Portanto, há muitos de diferentes aspectos, e nosso desafio é integrar todas essas peças diferentes para ter uma solução ponta a ponta perfeita. Atualmente, é um processo bastante manual, mas estamos trabalhando para torná-lo muito mais automatizado à medida que avançamos.
Você pode compartilhar alguma história de sucesso sobre como usou o AM na produção?
Embora eu não possa me referir especificamente a esses clientes sem obter sua autorização, temos vários componentes que estão ativamente em produção. Alguns que consigo pensar, de início, são os componentes aeroespaciais e relacionados à defesa.
Portanto, um é um componente de vôo que faz parte de um sistema de missão em um helicóptero militar. Estamos em produção para esse componente há dois anos e já entregamos com sucesso mais de 200 unidades até o momento.
Também fazemos outro componente que é usado para um sensor de solo, onde você tem um sistema integrado de 80 componentes individuais diferentes em uma peça monolítica. Esse também está em produção há quase dois anos.
Temos uma série de outros componentes de produção que fabricamos — para petróleo e gás e áreas de exploração submarina, que estão em produção ativa para robótica submarina — para outro de nossos clientes que estamos fabricando peças para, que são ativamente usados em petróleo e gás, perfuração e exploração e robótica submarina.
Como você vê a evolução da manufatura aditiva nos próximos cinco anos, tanto em termos de tecnologia quanto da indústria em geral?
Nos próximos cinco anos, vejo a tecnologia evoluindo com mais sistemas multi-laser, o que permitirá que as peças sejam produzidas com mais rapidez, reduzindo assim o custo dos componentes. Isso impulsionará ainda mais a implementação de peças AM.
O custo das peças é um fator chave e o tempo do laser é o principal fator para o custo de um componente AM. Então, se você puder espremer mais lasers em uma peça e ser capaz de certificar os componentes, usando esses sistemas multi-laser, você será capaz de construir a mesma peça mais rápido e, portanto, mais barato.
A outra evolução é que teremos melhores sistemas de monitoramento em processo. Existem alguns diferentes atualmente disponíveis por diferentes fabricantes, mas minha impressão é que embora muitos deles sejam bons sistemas, eles ainda não estão no nível de capacidade que os usuários, como eu, precisariam para implementá-los a uma taxa de produção real.
Minha esperança é que em breve tenhamos um verdadeiro monitoramento em processo, para que possamos monitorar o que está acontecendo na máquina durante o processo e sermos capazes de identificar problemas com um componente antes que ele deixe o máquina.
O cenário ideal seria ter um software inteligente que pudesse identificar problemas e potencialmente fazer correções com suporte de engenharia em tempo real. Claro, melhor ainda seria ter máquinas verdadeiramente robustas que não tenham nenhum problema e funcionem 24 horas por dia, 7 dias por semana.
Há alguma tendência com a qual você está animado?
Estou animado com vários desenvolvimentos, com sistemas de monitoramento em processo, como mencionei, sendo um deles.
Existem também alguns novos materiais que estão sendo desenvolvidos e lançados. Estamos desenvolvendo alguns materiais diferentes que permitem que alguns de nossos clientes façam alguns componentes muito revolucionários.
Outra coisa que me entusiasma é que há muito mais diversificação de fabricantes em todo o mundo. No início, a maioria das máquinas AM era produzida em alguns países da Europa. Agora, existem novos fabricantes e vários países que estão aplicando abordagens diferentes e inovadoras para a construção de máquinas.
Eles estão reduzindo o custo das máquinas e estão aprendendo, com seu uso em toda a indústria, a torná-las mais intuitivas para os operadores.
Minha experiência nos primeiros anos com essas máquinas, foi que elas são muito exigentes e requerem muita atenção e “babá”. E, francamente, muito do design da máquina não era muito amigável para a fabricação.
Vejo muita facilidade de uso sendo incorporada às máquinas agora, à medida que os fabricantes obtêm feedback de seus usuários.
Mas também, o aumento da competição de diferentes fabricantes em todo o planeta está, eu acho, ajudando a impulsionar a inovação nos sistemas, reduzir os custos e aumentar a usabilidade dos sistemas da máquina.
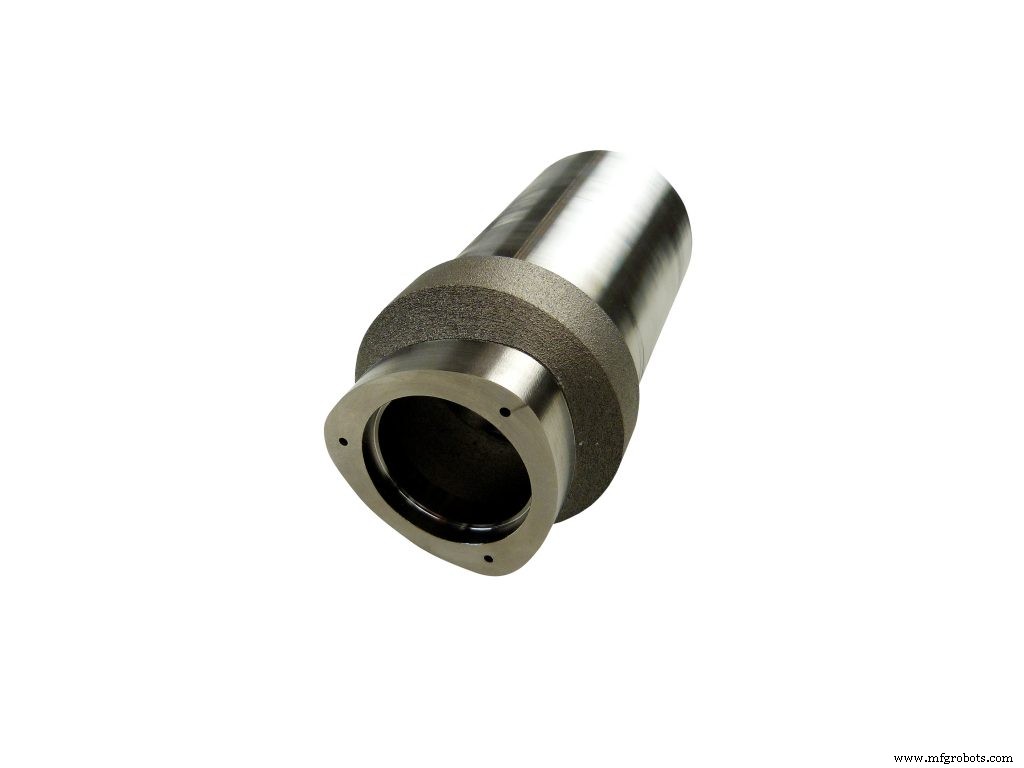
O que vem por aí para a Oerlikon, especialmente para a instalação que você está ajudando a supervisionar e administrar?
Nossa meta de curto prazo para esta instalação é que todos os equipamentos que adquirimos sejam instalados e certificados. Portanto, temos 18 sistemas de leito de pó de metal online e operacionais atualmente, e estamos produzindo hardware em muitos desses sistemas.
Nosso próximo passo para aqueles, é completar as propriedades dos materiais para todos os nossos sistemas de materiais em todas as nossas máquinas e os conjuntos de dados para eles. Mas isso consome muito tempo e é caro.
Felizmente, temos muitas pessoas muito talentosas aqui com muitos materiais, metalurgia e experiência em engenharia, e estou muito orgulhoso de fazer parte dessa equipe.
O outro objetivo é erguer todos os outros equipamentos para alcançar essa verdadeira instalação de produção de ponta a ponta.
Recentemente colocamos nosso forno HIP e forno a vácuo online e estamos trabalhando para obter a certificação deles.
Também trouxemos alguns equipamentos CNC e temos um número substancial de fornos adicionais e equipamentos CNC para pós-processamento. Assim, o objetivo é que todos esses equipamentos sejam instalados, certificados e operacionalmente integrados para criar um sistema de fabricação completo e coeso.
Para saber mais sobre a Oerlikon, visite: https://www.oerlikon.com/en/
impressao 3D
- Entrevista com um especialista:Professor Neil Hopkinson, Diretor de Impressão 3D da Xaar
- Entrevista com um especialista:Philip Cotton, fundador do 3Dfilemarket.com
- Entrevista com um especialista:Spencer Wright de pencerw.com e nTopology
- Entrevista com um especialista:Dr. Alvaro Goyanes da FabRx
- Entrevista com especialista:Nanoe CEO Guillaume de Calan sobre o futuro da impressão 3D em cerâmica
- Entrevista com especialista:Ultimaker Presidente John Kawola sobre o futuro da impressão 3D
- Como a Ford Motor Company está inovando a impressão 3D para a indústria automotiva:Entrevista de especialista com Harold Sears
- Entrevista com especialista:Nano Dimension Co-Fundador Simon Fried sobre a ascensão da impressão 3D para eletrônicos
- Entrevista com especialista:Brian Alexander da Solvay sobre o desenvolvimento de polímeros de alto desempenho para impressão 3D
- Entrevista com especialista:Uma olhada nas impressoras 3D SLA de nível industrial ultrarrápidas da Nexa3D