Superando a divisão da transformação digital com análises avançadas de manufatura
Engenharia de Manufatura: O monitoramento e a análise de máquinas tornaram-se mais críticos do que nunca na era da manufatura digital/Indústria 4.0. O que há de novo nas últimas ofertas da Sight Machine?
Jon Sobel: Nossas ofertas mais recentes são projetadas para uma gama muito maior de fabricantes. Embora a maioria dos fabricantes tenha pelo menos iniciado suas jornadas de transformação digital, encontramos um amplo espectro de níveis de prontidão entre eles. Muitas empresas estão ansiosas para usar dados de IoT [Internet das Coisas] para obter melhor visibilidade de suas operações de fabricação, mas não estão prontas para análises avançadas. Eles podem não ter a experiência interna, o suporte organizacional ou isso representa um salto muito grande para dar em uma etapa. Introduzimos um novo nível de nossa plataforma de fabricação digital:Enterprise Manufacturing Visibility [EMV], que oferece uma entrada rápida na fabricação digital. O EMV permite que as empresas obtenham rapidamente visibilidade em tempo real do desempenho de suas operações de fabricação em todas as suas fábricas. Ele oferece configuração de autoatendimento, permitindo que os fabricantes obtenham rapidamente todos os tipos de dados de produção do chão de fábrica e monitorem esses dados por meio de visibilidade baseada em navegador.
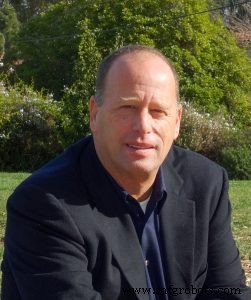
O Enterprise Manufacturing Analytics [EMA] da Sight Machine, nosso nível avançado, oferece um conjunto completo de ferramentas analíticas, como controle estatístico de processos, mapas de calor de correlação, detecção de anomalias e análise de gargalos. Ele aplica análises avançadas para obter benefícios como maior produção, tempos de ciclo reduzidos e taxas de refugo reduzidas. Esses insights baseados em análises são a base necessária para as empresas transformarem seus modelos de negócios e seus relacionamentos com fornecedores e clientes.
EU: Como sua nova estrutura em camadas pode ajudar os fabricantes a iniciarem na fabricação digital sem fazer análises completas?
Sobel: Até agora, tínhamos uma única oferta que oferecia visibilidade e análise. Agora, dividimos nossas ferramentas de visibilidade em um produto independente. O EMV fornece uma entrada direta, de autoatendimento e facilmente escalável na fabricação digital, com ferramentas automatizadas para ingerir os dados, limpá-los e contextualizá-los e modelar o processo de produção.
O EMV permite que as empresas monitorem a produção, a disponibilidade e o tempo de inatividade por instalação, tipo de máquina e máquina por meio de aplicativos que incluem Global Operations View, KPI Dashboard e Streaming Data Visualization. A visibilidade é em tempo real e histórica.
Os recursos do EMV incluem o Digital Twin Builder, nossa ferramenta baseada em navegador para criar modelos de dados de instalações, máquinas e tipos de máquinas. Ele também inclui o FactoryTX, nosso software de ponta que prepara dados de máquina e fábrica para streaming para a nuvem.
EU: Quão difícil é para as empresas começarem com monitoramento/análise e o que sua metodologia do Índice de Prontidão Digital introduzida recentemente diz a elas?
Sobel: Descobrimos que a chave para uma transformação digital bem-sucedida é escolher projetos adequados ao nível de prontidão de uma empresa ou planta. A prontidão inclui não apenas fatores técnicos, como conectividade e acessibilidade de dados, bem como estratégia de nuvem e segurança, mas também fatores organizacionais. Descobrimos em nossos seis anos trabalhando com fabricantes do G500 que os fatores organizacionais são pelo menos tão importantes quanto os fatores técnicos. Eles incluem o nível de comprometimento e adesão tanto no nível da fábrica quanto no nível executivo, e a existência de estratégias de nuvem e segurança.
A Sight Machine desenvolveu uma metodologia chamada Índice de Prontidão Digital [DRI] para avaliar a prontidão técnica e organizacional de uma empresa para projetos de fabricação digital e identificar projetos apropriados - aqueles com maior probabilidade de sucesso com base na prontidão atual. Usamos um questionário padronizado para mapear cada empresa em uma das cinco Zonas de Prontidão Digital:Conexão, Visibilidade, Eficiência, Análise Avançada e Transformação. Cada Zona de Prontidão Digital mapeia exemplos de projetos que podem ser alcançados para esse nível de prontidão.

EU: Neste ponto, quão longe está o setor de manufatura na adoção de análises avançadas de fábrica?
Sobel: Todos os principais fabricantes com quem falamos começaram pelo menos a jornada de transformação digital. Encontramos uma grande variação não apenas entre as empresas, mas dentro das fábricas individuais das empresas.
Você pode pensar nisso em termos destas etapas:acesso a dados; visibilidade; e insights. É bastante comum que as empresas coletem e armazenem seus dados digitais. Muitos construíram painéis simples que lhes permitem monitorar as diferentes linhas ou máquinas dentro de fábricas individuais.
Relativamente poucos fabricantes ganharam visibilidade em suas fábricas. Acreditamos que a Sight Machine oferece a única solução escalável no mercado para obter rapidamente visibilidade entre empresas.
Para análises avançadas, deixando de lado as empresas com as quais trabalhamos, na maioria das vezes vemos projetos de ciência de dados sob medida. As empresas que enfrentam um problema de desempenho ou qualidade encarregarão seus cientistas de dados de resolver o problema conhecido. Eles normalmente desenvolverão uma solução única, pegando todos os dados que puderem, jogando-os no Excel ou em um programa estatístico e procurando correlações.
O problema é que esses projetos não são escaláveis nem aplicáveis a outros problemas. A extração e modelagem de dados é feita de forma a criar silos de aplicativos e dados. Do ponto de vista de um vice-presidente de operações ou CIO, eles ficam com uma proliferação de aplicativos personalizados que não podem ser integrados de maneira a entender as operações da empresa de manufatura como um todo.
O Digital Twin da Sight Machine é um modelo de dados ativo e funcional do processo de produção. Um único aplicativo que pode ser expandido rapidamente adicionando novas máquinas e processos, nosso Digital Twin fornece uma única fonte de verdade que pode ser consultada para obter qualquer problema operacional.
EU: O que a análise avançada pode oferecer aos fabricantes que mergulham profundamente nessa tecnologia?
Sobel: A revolução digital transformou setor após setor – publicidade, varejo, investimento, ciência, política – desencadeando não apenas grandes melhorias na eficiência, mas também transformando e criando novos modelos de negócios. Os fabricantes estão apenas começando a aproveitar o poder de seus dados e estão vendo resultados reais.
Quando você extrai mais produtividade de suas plantas e máquinas existentes, ou reduz refugos e defeitos, isso afeta diretamente seus resultados. Mas a maioria dos fabricantes líderes escolheu todos os frutos mais fáceis há muito tempo de disciplinas como Seis Sigma e Lean. Os próximos grandes saltos virão da obtenção de visibilidade real das operações corporativas de um fabricante, em todas as fábricas, e da aplicação das técnicas analíticas aprimoradas ao longo de mais de uma década com as transformações digitais em outros setores.
EU: Como a inteligência artificial [IA] na plataforma da Sight Machine impulsiona a análise de fábrica ainda mais do que em ofertas anteriores ou concorrentes?
Sobel: O AI Data Pipeline da Sight Machine é uma tecnologia com patente pendente que transforma dados brutos em dados contextualizados aos quais a análise pode ser aplicada com sucesso. Com nossa plataforma, o AI Data Pipeline faz o trabalho pesado de coletar dados brutos de sensores, PLCs, historiadores de dados etc. e, em seguida, prepará-los para análise por meio de limpeza, marcação e combinação.
Os dados então vão para nossa outra tecnologia com patente pendente, o Plant Digital Twin, que modela os processos de produção da fábrica. Ele pega os dados do AI Data Pipeline e os monta em um modelo do sistema, traduzindo milhares de pontos de dados de centenas de fontes em uma representação de peças ou lotes que passam pela produção. O Plant Digital Twin reflete o estado da máquina em cada ponto do processo de produção, para cada peça ou lote, e também registra a matéria-prima usada para essa peça ou lote, fatores ambientais como umidade e temperatura, as identidades dos operadores da máquina e o que for. dados adicionais estão disponíveis.
Com ofertas concorrentes, como iniciativas analíticas internas, os cientistas de dados passam a maior parte do tempo selecionando, limpando e combinando dados manualmente, não analisando dados para encontrar insights de negócios acionáveis. Por outro lado, nossas tecnologias AI Data Pipeline e Plant Digital Twin criam automaticamente uma representação digital dos processos de produção em tempo real, deixando cientistas de dados, operadores de linha e gerentes de fábrica livres para responder proativamente a problemas operacionais, em vez de investigá-los retroativamente.
EU: Dê-me um exemplo de um fabricante fazendo um trabalho exemplar com sua plataforma de análise de manufatura.
Sobel: Fomos contratados por um fabricante de produtos de saúde para ajudar a resolver um problema que outros fornecedores de tecnologia não conseguiam resolver – uma alta taxa de sucata em sua planta mais lucrativa. A plataforma Sight Machine realizou análise de causa raiz que combinou processamento de linguagem natural, análise de sequência, análise de cluster e regressões.
A plataforma Sight Machine identificou e priorizou as múltiplas causas de sucata, levando a um aumento na Eficácia Geral do Equipamento de cerca de 3%. Isso se traduz em economias potenciais de mais de US$ 20 milhões por ano apenas para esta planta.
Aquisições
Software PLM da Siemens (Plano, TX) concordou em adquirir a Solido Design Automation Inc. (Saskatoon, SK), desenvolvedora de software de caracterização e design com reconhecimento de variação para empresas de semicondutores.
Os termos da transação não foram divulgados. A Siemens disse que espera fechar a transação no início de dezembro de 2017. Os produtos baseados em aprendizado de máquina da Solido são atualmente usados em produção em mais de 40 grandes empresas, permitindo que elas projetem, verifiquem e fabriquem produtos mais competitivos.
A aquisição ainda mais expande o portfólio de verificação analógico/sinal misto (AMS) da Mentor Graphics (adquirida pela Siemens em março de 2017), permitindo que ela enfrente os crescentes desafios de projeto e verificação de IC para automóveis, comunicações, computação de data center, redes, dispositivos móveis, e aplicativos de IoT.
A Solido ajuda seus clientes a lidar com o impacto da variabilidade para melhorar o desempenho, potência, área e rendimento do IC, disse Amit Gupta, fundador, presidente e CEO da Solido Design Automation. “Combinar nosso portfólio de tecnologia com os recursos de IC e alcance de mercado da Mentor nos permitirá fornecer soluções para a indústria de semicondutores em uma escala ainda maior”, disse Gupta. “Estamos entusiasmados em contribuir para a estratégia de digitalização mais ampla da Siemens com nosso aprendizado de máquina aplicado para portfólio e experiência em tecnologia de engenharia.”
Novos lançamentos
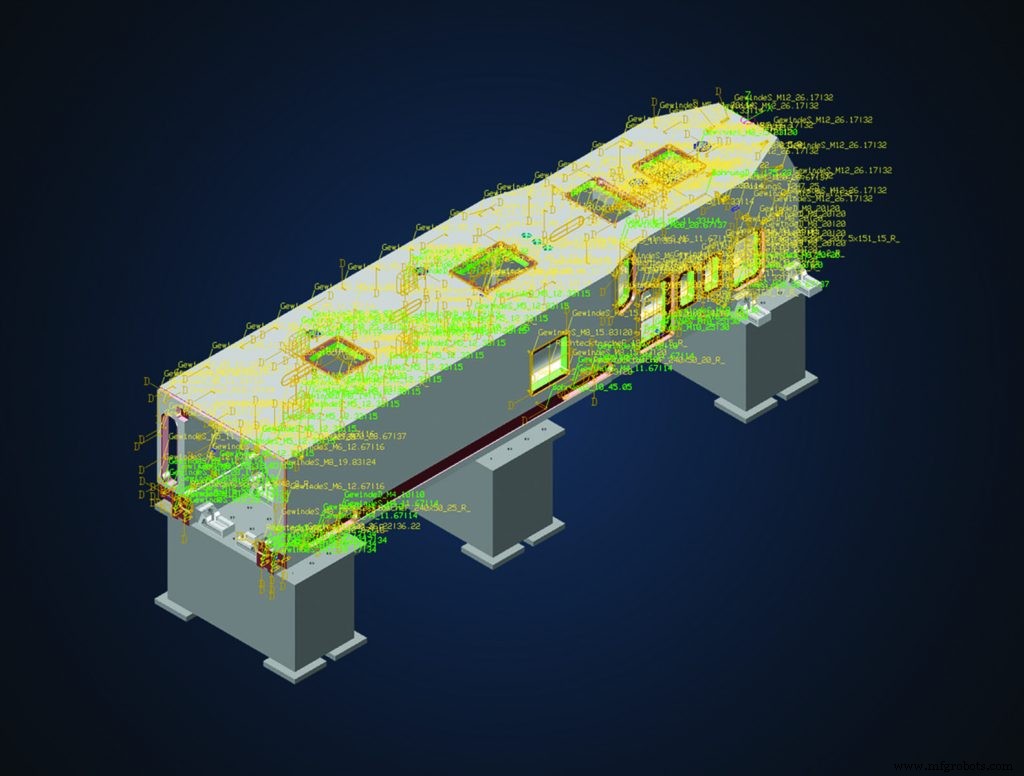
Tebis América (Troy, MI) anunciou a versão 5 de seu software CAD/CAM Versão 4.0 com desempenho otimizado que ajuda os usuários a acelerar seus processos.
As atualizações nesta versão permitem que os usuários agilizem os processos sem restrições funcionais com melhorias na simulação de máquinas, trabalhando com conjuntos de ferramentas, procurando ferramentas na usinagem de recursos ou trocando ferramentas no Job Manager.
Com esta nova versão, a programação NC agora é amplamente automatizada com base em modelos com bibliotecas de processos que permitem procedimentos e processos rápidos e confiáveis. Os usuários também podem editar peças grandes e complexas com o software. Tebis identified the heaviest loads that occur in specific processes, helping alleviate bottlenecks that can result in long waiting times as well as heavy use of resources and conflicts. Tebis developers adapted the system to optimize the use of available memory, and multicore technology relying on parallel processing was integrated at the same time. The extended parallel processing saves significant time, especially in the calculation of NC programs for re-roughing. Parts can be loaded, shaded and saved with time optimization.
Manufacturing execution systems (MES) developer 42Q (San Jose, CA) has released its new Digital Factory Starter Kit, a solution with key capabilities that accelerate digital factory transformation.
The Digital Factory Starter Kit includes shop floor and quality functions, traceability capability and business intelligence (BI) reporting. Part of 42Q’s cloud solution, this kit enables manufacturers to realize value from digital factory transformation using 42Q in a few weeks.
“The costs and complexity of deploying a conventional on-premise MES platform can result in a time-to-value of between 9–18 months for basic functionality,” said Srivats Ramaswami, CTO of 42Q. “Manufacturers beginning their digital transformation should not have to wait that long. We designed the Digital Factory Starter Kit to include the core features necessary for digital transformation, and get companies up and running in a few weeks with no interruption to business processes or customer deliveries.”
Key capabilities of the Digital Factory Starter Kit include electronic travelers, cycle time management, shop order management and process.
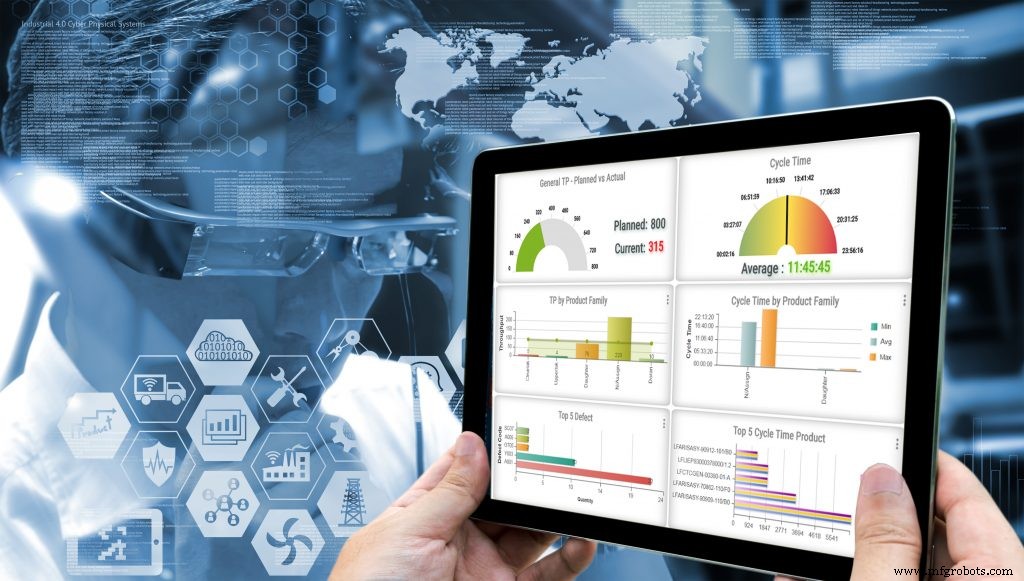
routing control. Functionality for quality management is fully integrated, including employee verification and electronic work instructions, traceability, product genealogy, labeling and control plans. The Digital Factory Starter Kit also includes 42Q’s Business Intelligence module, which provides tools for real time alerts from manufacturing operations along with data visualization.
The solution enables companies to manage quality and operations, monitor yields, WIP, and throughput in real time. “This solution is proven and already deployed in many manufacturing facilities in highly regulated industries, including medical, aerospace and automotive manufacturing,” Ramaswami said.
Computerized maintenance management software (CMMS) developer EZmaintain (Cleveland) has introduced its cloud-based CMMS package for integrating IoT sensors to measure temperature and vibration levels of equipment such as motors, gear boxes and generators.
Users can run the web-based CMMS independently to manage failure or preventive maintenance activities. Adding these smart IoT sensors allows users to capture real-time data for condition monitoring with alerts viewed directly via a CMMS dashboard.
EZmaintain CMMS works across different devices, from desktops to mobile devices. Users can add or configure Temperature/Vibration sensors via the dashboard, and can mount IoT sensors on various assets that need monitoring using screw-type mounting designs. With these low-cost, easy-to-setup sensors, the software can be used in various industrial or commercial applications.
Sistema de controle de automação
- Otimizando a transformação digital na manufatura de CPG
- Transformação digital na manufatura - Os aceleradores e o roteiro para os fabricantes
- IoT e educação:Reduzindo a divisão digital
- Como a tecnologia dupla digital está preenchendo a lacuna de talentos na fabricação
- O que é transformação digital na manufatura?
- Desafios da Transformação Digital na Manufatura
- Melhore a tomada de decisões na fabricação avançada com análises
- Superando os gargalos:o poder da análise na fabricação
- Censornet:garantindo o futuro da indústria manufatureira
- GE Digital:transformando a manufatura com o Smart MES